轴类检验标准
数控轴线的定位精度和重复定位精度的确定

数控轴线的定位精度和重复定位精度的确定1 范围本部分规定了通过直接测量机床的单个轴线来检验和评定数控机床的定位精度和重复定位精度的方法。
这种方法对线性轴线和回转轴线(直线运动和回转运动)同样适用。
本部分适用于机床的型式检验、验收检验、比较检验、定期检验。
也可用于机床的补偿调整检验。
本部分不适用于需同时检验几个轴线的机床。
检验方法涉及每个位置上的重复测量。
本部分给出了与检验有关的参数的定义和计算方法。
ISO/TR 230-9:2005的附录C[2]中描述了不确定度的估算方法。
附录A提供了估算测量不确定度的方法。
附录B叙述了可供选择应用的阶梯循环。
这一循环的结果既不用在与本部分有关的技术文献中,也不用于验收,除非供方/制造厂与机床用户之间签订有特殊的书面协议。
出于机床验收目的考虑,使用本部分的标准检验循环始终是正确的选择。
2 定义与符号下列定义和符号适用于本文件:2.1轴线行程axis travel在数字控制下运动部件沿轴线移动的最大直线行程或绕轴线回转的最大行程。
注当运动部件绕轴线回转超过360°时,可能无法清晰地定义行程最大长度。
2.2测量行程 measurement travel用于采集数据的部分轴线行程。
选择测量行程时应保证可以双向趋近第一个和最后一个目标位置(见图1)。
2.3目标位置P i(i=1至m) target position P i(i=1 to m)运动部件编程要达到的位置。
注下标i表示沿轴线或绕轴线选择的目标位置中的特定位置。
2.4实际位置P ij(i=1至m ;j=1至n) actual position P ij( i=1 to m; j=1 to n)运动部件第j次向第i个目标位置趋近时实际测得的到达位置。
1位置偏差 X ij deviation of position; positional deviation X ij运动部件到达的实际位置减去目标位置之差。
检验通则

检验通则一、目的:为了规范指导检验员正确的作业程序和检验方法,特制定本检验通则。
二、范围:检验员对自制产品、外购外协件、入库原材料的检验均适用本检验通则。
三、引用标准和技术要求:1、立、卧式加工中心普通级适用型号:VC600\ TVCL600\VMC600\VMCL600\VMCL850\VMC1100B(C)\VMC1300A\ VMC1650A\VMC1800A\VGC500\VGC1500\VGC2000\ MCH50\H50\MCH63B① GB/T 18400.1-2010加工中心检验条件第1部分:卧式和带附加主轴头机床几何精度检验(水平Z轴)② GB/T 18400.2-2010加工中心检验条件第2部分:立式或带垂直主回转轴的万能主轴头机床几何精度检验(垂直Z轴)③ GB/T 18400.4-2010加工中心检验条件第4部分:线性和回转轴线的定位精度和重复定位精度检验④ GB/T 18400.5-2010加工中心检验条件第5部分:工件夹持托板的定位精度和重复定位精度检验⑤ GB/T 18400.7-2010加工中心检验条件第7部分:精加工试件精度检验⑥ JB/T 8801-1998 加工中心技术条件⑦ GB 18568-2001 加工中心安全防护技术条件⑧ GB 5226.1-2008 机械电气安全机械电气设备第1部分:通用技术条件⑨ GB 15760-2004 金属切削机床安全防护通用技术条件2、立、卧式加工中心精密级适用型号:VCL850\VCL1100\MCH630\VP1050(精密级内控)① GB/T 20957.1-2007精密加工中心检验条件第1部分:卧式和带附加主轴头机床几何精度检验(水平Z轴)② GB/T 20957.2-2007精密加工中心检验条件第2部分:立式或带垂直主回转轴的万能主轴头机床几何精度检验(垂直Z轴)③ GB/T 20957.4-2007精密加工中心检验条件第4部分:线性和回转轴线的定位精度和重复定位精度检验④ GB/T 20957.5-2007精密加工中心检验条件第5部分:工件夹持托板的定位精度和重复定位精度检验⑤ GB/T 20957.7-2007精密加工中心检验条件第7部分:精加工试件精度检验⑥ GB/T 20012-2007 精密加工中心技术条件⑦ GB 18568-2001 加工中心安全防护技术条件⑧ GB 5226.1-2008 机械电气安全机械电气设备第1部分:通用技术条件⑨ GB 15760-2004 金属切削机床安全防护通用技术条件⑩ Q/TKNK002-2012精密加工中心几何、位置、工作精度检验(VP1050使用)3、五轴联动立式加工中心、适用型号:5DGBC28\5DGBC50\5DGBC63① JB/T 10792.1-2007五轴联动立式加工中心第1部分:精度检验② JB/T 10792.2-2007五轴联动立式加工中心第2部分:技术条件③ GB 18568-2001 加工中心安全防护技术条件④ GB 5226.1-2008 机械电气安全机械电气设备第1部分:通用技术条件⑤ GB 15760-2004 金属切削机床安全防护通用技术条件4、五轴联动精密卧式加工中心适用型号:5DMCH63① Q/320601AN09.1-2010五轴联动精密卧式加工中心第1部分:精度检验② Q/320601AN09.2-2010五轴联动精密卧式加工中心第2部分:技术条件③ GB 18568-2001 加工中心安全防护技术条件④ GB 5226.1-2008 机械电气安全机械电气设备第1部分:通用技术条件⑤ GB 15760-2004 金属切削机床安全防护通用技术条件5、数控卧式车床适用型号:SL50\SLL50\TC50\LG24① GB/T 16462.1-2007数控车床和车削中心检验条件第1部分:卧式机床几何精度检验② GB/T 16462.4-2007数控车床和车削中心检验条件第4部分:线性和回转轴线的定位精度和重复定位精度检验③ GB/T 16462-1996 数控卧式车床精度检验④ JB/T 4368.2-1996数控卧式车床参数⑤ JB/T 4368.3-1996数控卧式车床技术条件⑥ JB/T 4368.4-1996数控卧式车床性能试验规范⑦ GB 22997-2008 机床安全小规格数控车床与车削中心⑧ GB 22998-2008 机床安全大规格数控车床与车削中心⑨ GB 5226.1-2008 机械电气安全机械电气设备第1部分:通用技术条件⑩ GB 15760-2004 金属切削机床安全防护通用技术条件6、数控龙门镗铣床适用型号:GM(C)1340\ GM(C)1360\ GM(C)1380\ GM(C)1640\ GM(C)2040\ G M(C)2060\G M(C)2560\G M(C)2580\G M(C)20100\ GDMC3080-5M\GMMC30120\5GF2580\GF25100\THS1460\THS2060/160① GB/T 19362.1-2003龙门铣床检验条件精度检验第1部分:固定式龙门铣床② JB/T 6600-2006 数控龙门镗铣床技术条件③ GB/T 25661.1-2010高架横梁移动龙门加工中心第1部分:精度检验④ GB/T 25661.2-2010高架横梁移动龙门加工中心第2部分:技术条件⑤ ISO8636-2:2007龙门铣床检验条件精度检验第2部分:移动式龙门铣床⑥ GB/T 5289.3-2006卧式铣镗床检验条件精度检验第3部分:带分离式工件夹持固定工作台的落地式机床⑦ JB/T 8490-2008 落地镗、落地铣镗床技术条件⑧ GB 5226.1-2008 机械电气安全机械电气设备第1部分:通用技术条件⑨ GB 15760-2004 金属切削机床安全防护通用技术条件7、各类技术文件①产品各型号的图纸和技术要求②产品各型号零部件的加工工艺和专项通则工艺③产品各型号整机的装配工艺和专项通则工艺④产品各型号的检验规范⑤产品订单和技术协议⑥相关产品质量会议的纪要四、检验步骤:4.1对照图纸要求,图号是否与实物一致。
JBZQ 6105--2017大型曲轴锻件的磁粉检验

JB/ZQ 6105--84大型曲轴锻件的磁粉检验机械工业部重型矿山机械工业局企业标准JB/ZQ6105--84大型曲轴锻件的磁粉检验----------------------------------------------------------------------------本标准适用于直径在200mm以上的锻钢曲轴主支承轴颈或曲柄轴颈的磁粉检验。
本标准等效采用ASTM A456-83《大型曲轴锻件的磁粉检验标准》。
1与本标准有关的标准JB/ZQ 6101《锻钢件的磁粉检验方法》JB/ZQ 6136《液体渗透检验方法》2订贷依据在合同中应写明曲轴按本标准进行验收。
3方法3.1磁粉探伤应按JB/ZQ 6101规定的方法执行。
3.2渗透探伤应按JB/ZQ 6136规定的方法执行,曲轴的渗透探伤仅作为磁粉探伤的辅助手段。
4检验范围4.1关键部位4.1.1任一曲柄轴轴颈的关键部位,都应当是以曲柄轴轴颈轴心到六点钟位置连线为基线划的正负60°夹角内的凸台并外延10mm区域(图1),以及大致从轴颈表面同圆角相切处沿曲柄方向延伸16mm的区域(图2)图 1 曲柄轴颈和主支承轴轴颈表面关键位置1--曲柄轴轴颈或主支承轴轴颈上的16mm区;2--圆角半径R;3--凸台;4--凸台外10mm环区.图 2 计算用的参考尺寸4.1.2任一主支承轴轴颈的主要关键部位,都应当是:以轴颈十二点钟位置为基线划的正负60°夹角内的凸台并外延10mm的区域(图1),以及大致由轴颈表面同圆角相切处沿轴颈方向延伸16mm的区域(图2)。
4.1.3任何曲柄轴轴颈或主支承轴轴颈的关键部位,还包括过渡圆角区与油孔的穿颈面交接处6mm以内的表面区域。
4.2非关键部位非关键部位包括所有的加工圆角、凸台和未规定为关键部位的各支承面。
5缺陷分类5.1曲轴表面上的磁粉痕迹显示的缺陷,按性质可分为如下类别:a. 开口裂纹、白点或缩管;b. 纵向非金属夹杂物;c. 常发生在同轴颈中心连线成45--70°角区域内的扭曲裂纹或非金属夹杂物。
轴类监造方案

(3)对关键部位进行无损检测,如磁粉探伤、超声波探伤等;
(4)对不合格品进行追溯、分析,制定改进措施,防止再次发生。
4.成品验收与交付
(1)对成品进行最终检验,确保产品质量符合客户要求;
(2)提供完整的产品质量证明文件,如检验报告、合格证等;
(3)按照约定时间完成产品交付,确保客户利益。
四、监造内容
1.原材料采购及检验:
a)确保采购的原材料符合国家和行业标准要求;
b)对进厂原材料进行严格检验,包括尺寸、外观、材质等;
c)对不合格原材料及时退货或处理,确保原材料质量。
2.加工过程监控:
a)制定合理的加工工艺,确保加工过程符合技术要求;
b)对加工设备进行定期维护和校准,保证设备精度;
c)对加工过程中的关键工序进行重点监控,确保产品质量;
5.采购部门:负责原材料的采购及供应商管理。
六、监造流程
1.制定监造计划:明确监造范围、内容、时间等;
2.开展监造工作:按照计划进行原材料采购、加工过程监控、质量检验等;
3.问题反馈与处理:对发现的问题及时反馈,制定改进措施,督促整改;
4.成品验收:对成品进行最终检验,确保产品质量;
5.监造总结:对监造过程进行总结,持续改进。
一、引言
为确保轴类零件的制造质量,满足设备运行性能和安全性要求,本方案旨在提供一套详细的轴类监造方案。本方案遵循国家相关法律法规,结合企业实际,旨在提高产品质量,降低成本,增强企业市场竞争力。
二、监造目标
1.确保轴类零件制造过程符合国家法律法规及行业标准;
2.提高轴类零件的产品质量,降低废品率;
3.提升企业生产效率,优化资源配置;
第六章 孔、轴检测与量规设计基础
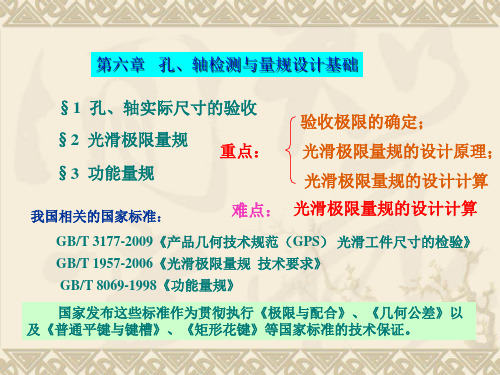
§1 孔、轴实际尺寸的验收
§2 光滑极限量规 §3 功能量规
重点:
验收极限的确定; 光滑极限量规的设计原理; 光滑极限量规的设计计算
我国相关的国家标准:
难点: 光滑极限量规的设计计算
GB/T 3177-2009《产品几何技术规范(GPS) 光滑工件尺寸的检验》 GB/T 1957-2006《光滑极限量规 技术要求》 GB/T 8069-1998《功能量规》
规
规
孔
轴
适用场所不同
工 验校 作 收对 量 量量 规 规规
生
检
计
产
验
量
车
部
部
间
门
门
二、光滑极限量规的设计原理——泰勒原则
设计光滑极限量规时,应遵守泰勒原则(极限尺寸判断原则)的规定。
Dfe dfe
图7-7 孔、轴体外作用尺寸 Dfe、 dfe与实际尺寸 Da、 da
1—实际被测孔;2—最大的外接理想轴
(2)不内缩方式验收极限
不内缩方式的验收极限是以图样上规定的
上极限尺寸和下极限尺寸分别作为上、下 验收极限,即取安全裕度为零(A=0), 因此
KS
L; max
Ki Lmin
图7-2 工件尺寸公差带及验收极限
y
2、验收极限方式的选择
① 对于遵循包容要求的尺寸和标准公差等 级高的尺寸,其验收极限按双向内缩方式 确定。
轴用量规——环规或卡规
孔用量规——塞规
光滑极限量规有通规和止规,应成对使用。
常见量规的结构形式
◆量规按用途分类:
(1)工作量规——指在零件制造过程中操作者所使用的量 规。 分为通规“T”和止规“Z”。
五金原材来料检验标准
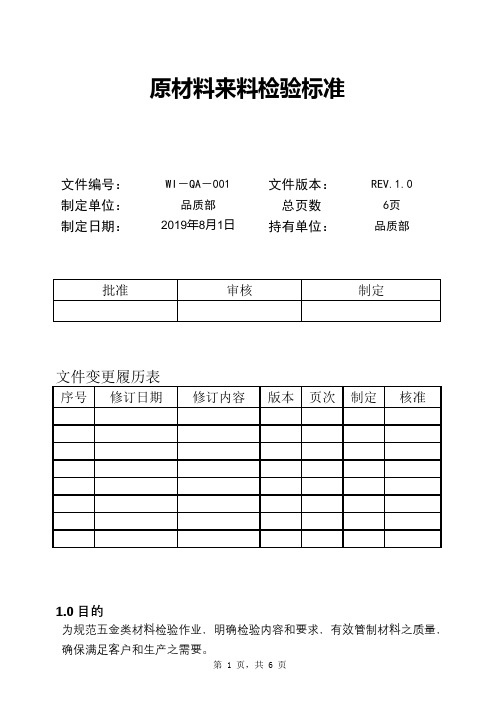
序号版本页次制定核准原材料来料检验标准确保满足客户和生产之需要。
1.0 目的为规范五金类材料检验作业,明确检验内容和要求,有效管制材料之质量,文件变更履历表修订日期修订内容制定日期:2019年8月1日持有单位:品质部批准审核制定文件编号:WI-QA-001文件版本:REV.1.0制定单位:品质部总页数6页2.0 范围适用于本公司所有产品的五金类材料的进料检验。
3.0 引用标准MIL-STD-105E正常检验单次抽样II类检验水平(适用于连续批的检查)。
项目分类及允收质量水平:MA ----- 主要项目:AQL=0.65;MI----- 次要项目:AQL=1.5。
测试项目采用特殊检验S-2水平:AQL=1.5,取0/1。
GB1800-79 标准公差数值4.0 流程4.1 检验流程包装检验 → 尺寸检验 → 试装检验 → 外观检验 → 测试项目试验5.0 定义5.1 A面:指物料的正前面、上面(在使用过程能直接看到的表面);5.2 B面:指物料侧面(需将视线偏转45°~ 90°才能看到的四周边);5.3 C面:指物料背面及底面(正常使用时看不到的背面及底面)。
5.4 硬度:材料抵抗硬的物体压入自己表面的能力。
5.5 极限强度:材料抵抗外力破坏作用的最大能力。
5.6 可焊性:材料表面吸附焊锡的性能。
6.0 不良缺陷定义6.1 色差:产品表面颜色与标准样品颜色有差异。
6.2 光泽度:产品表面光泽与标准样品光泽有差异。
6.3 手印:产品表面出现的手指印。
6.4 硬划痕:硬物磨擦造成产品表面严重划痕(用指甲刮有明显感觉)。
6.5 软划伤:没有深度的划痕(无手感)。
6.6 毛丝:产品表面出现细小的尘丝。
直径(mm)长度(mm)深度(mm)宽度(mm)距离(mm)面积(mm 2)数目(个)DLHWDSSN9.0 代码对照表10.0 检验标准10.1 说明10.1.1 当缺陷直径D<0.30mm 且不连续时,可不作为缺陷,数量不计。
机械零部件检验标准规范
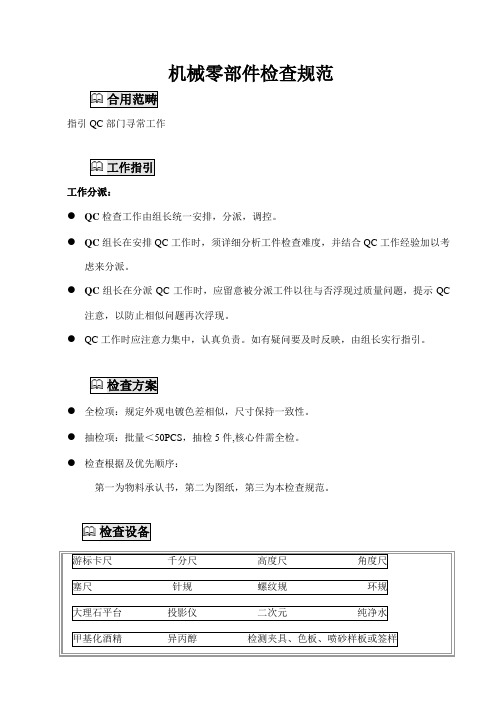
机械零部件检查规范指引QC部门寻常工作工作分派:●QC检查工作由组长统一安排,分派,调控。
●QC组长在安排QC工作时,须详细分析工件检查难度,并结合QC工作经验加以考虑来分派。
●QC组长在分派QC工作时,应留意被分派工件以往与否浮现过质量问题,提示QC注意,以防止相似问题再次浮现。
●QC工作时应注意力集中,认真负责。
如有疑问要及时反映,由组长实行指引。
●全检项:规定外观电镀色差相似,尺寸保持一致性。
●抽检项:批量<50PCS,抽检5件,核心件需全检。
●检查根据及优先顺序:第一为物料承认书,第二为图纸,第三为本检查规范。
1)对照图纸规定之版本,与否与实物一致。
2)清点图纸规定之数量,与否与实际相符3)辨认图纸规定之材料,与否与实物相符。
4)审查技术阐明。
留意:与否有对称件。
不同类型热解决、光洁度等对加工规定。
5)审核图纸尺寸、形位公差、外观规定、光洁度等,决定检查办法,合理选用量具,保证检测质量。
6)QC按顺序对工件进行检查,检完一种尺寸,作一种记号,不能漏检。
7)检出不良品,由组长或厂部确认与否返修,报废。
8)检查完毕订立检查记录,工件按规定进行清洗,清点包装,粘贴标记。
9)入库/出货。
1)审图时注意图纸与否模糊不清、与否漏盖工艺章。
2)图纸数量理论上只许多不能少。
3)审核所有材料,避免错料,混料。
4)检查与否有漏加工之处。
5)图纸规定热解决,氧化,关注与否除锈,留量,堵孔,氧化淬火前攻牙加工等。
6)留意零件与图纸其他不符之处,例如方向相反等。
1)外观检视条件——视力:校正视力1.0以上——目视距离:检查物距眼睛A级面40㎝,B、C距眼睛一臂远。
——目视角度:45度~90度(检查时产品应转动)——目视时间:A级面15秒/面,B、C面10秒/面——灯光:不不大于500LUX照明度2)术语和定义●柄,透镜,按键及键盘正面,探头整个表面等)。
●在使用过程中经常被客户看见某些(如:面壳左右侧面,底壳或后壳左右侧面及背面等)。
3立式光学计检测轴径
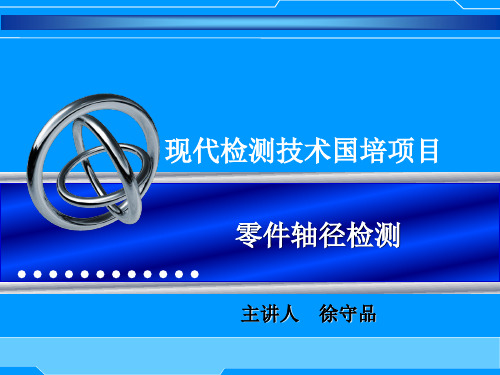
比较仪测量方法
零件轴径检测
1、立式光学计结构
一、立式光学计测量轴径
用量 块作长度 标准,在 立式光学 计上可进 行零件厚 度、球径 和轴径等 外尺寸测 量。
零件轴径检测
一、立式光学计测量轴径
1-投影灯 2-投影灯固定螺钉 3-支柱 4-零位微动螺钉 5-立柱 6-横臂固定螺钉 7-横臂 8-微动偏 心手轮 9-测帽提升器 10-工作台调整螺钉 11-工作台底盘 12-壳体 13-微动托圈 14-微动托圈 固定螺钉 15-光管定位螺钉 16-测量管固定螺钉 17-测量管 18-测帽 19-6V15W 变压器
现代检测技术国培项目 零件轴径检测
主讲人 徐守品
零件轴径检测
一、立式光学计测量轴径
主要 内容
二、万能测长仪测量轴径
三、万能工具显微镜测量轴径
零件轴径检测
当外部轮廓的长度尺寸大于直径尺寸的机械 零件均可称为轴类机械零件。
齿 轮 轴 台阶轴 轴类零件是机械产品中典型零件,其主要 作用是用于支承、传动、传递转矩。
零件轴径检测
2).工作台的选择
带筋工作台、平面工作台
一、立式光学计测量轴径
测量球径或轴径等具有圆弧表 面的零件时选用平面工作台, 测量量块或粗糙度数值小的平 行平面零件尺寸选用带筋工作台。
工作台的调整
零件轴径检测
3)、测量步骤
选用量块组合标准尺寸
一、立式光学计测量轴径
将研合好的量块和被测零件一起等温 调整仪器零位 确定被测尺寸
零件轴径检测
检测方法
1、生产车间常用: 通用量仪和量规来测量轴径 (1)游标卡尺 (2)外径千分尺 (3)量规
2、高精度轴径常用:用比较仪与量块进行比较测量 (1)机械式比较仪 杠杆齿轮比较仪、扭簧比较仪、百/千分表等 (2)光学比较仪 立式光学计、接触式干涉仪 (3)电动比较仪 电感测微仪 (4)气动比较仪 3、高精度且尺寸较大轴径常用:万能测长仪、测长机
- 1、下载文档前请自行甄别文档内容的完整性,平台不提供额外的编辑、内容补充、找答案等附加服务。
- 2、"仅部分预览"的文档,不可在线预览部分如存在完整性等问题,可反馈申请退款(可完整预览的文档不适用该条件!)。
- 3、如文档侵犯您的权益,请联系客服反馈,我们会尽快为您处理(人工客服工作时间:9:00-18:30)。
浙江赛安电气科技有限公司
1
轴类检验标准
编号:
1、外观检验
1.1 外观不可有锈斑、黑皮、变形、毛刺、缺损、划痕、碰伤; 1.2 有镀层或喷涂层的,镀层不可有剥落、起层、碰伤缺陷;
1.3 表面光洁度按照图纸要求,根据标准样板或标准粗糙度对比块进行对比; 1.4 螺纹不可有碰伤、毛刺、乱丝等缺陷;
1.5 当轴类零件为注塑镶件时,目测其止动结构应符合图纸要求。
2、尺寸检查
2.1、外径尺寸:
如果与轴承配合,使用标准轴承进行试装检测法进行检测;
如果同其它零件配合,使用相应的标准地封样零件进行试装检测; 也可以根据图纸尺寸,使用外径千分尺寸进行检测。
2.2、长度尺寸:
用游标卡尺进行检测。
2.3形位公差的检测
根据图纸的要求,对直线度、圆度、同轴度进行检测。
2.4 表面粗糙度 3、试装:
3.1检验工具:选择同轴配合的相关标准零件进行试装配,根据装配手感进行确定; 3.2、螺纹:用标准螺丝或螺母进行试装,同时检测螺纹的拧合顺滑性和攻丝深度。
4、材料检查
4.1可用简单的方法进行检测,譬如采用磁铁区分铁与不锈钢; 4.2 供方提供检测报告。
5、盐雾试验
5.1 温度35℃,盐水浓度5%,喷雾量1.6ml/80cm 2
/h ,相对湿度85%,空气桶温度47℃,8小时连续喷雾盐雾试验后,无明显生锈、白斑现象;测试数量:n>3pcs ;
6、检验规则 根据GB/T2828.1-2003,一般检验水平Ⅱ、正常检验一次抽样方案。
7、相关记录与表格 《进料检验报告》 FM/QP10-01
编制: 审核:。