陶瓷生产工艺设计
陶瓷的制造工艺流程
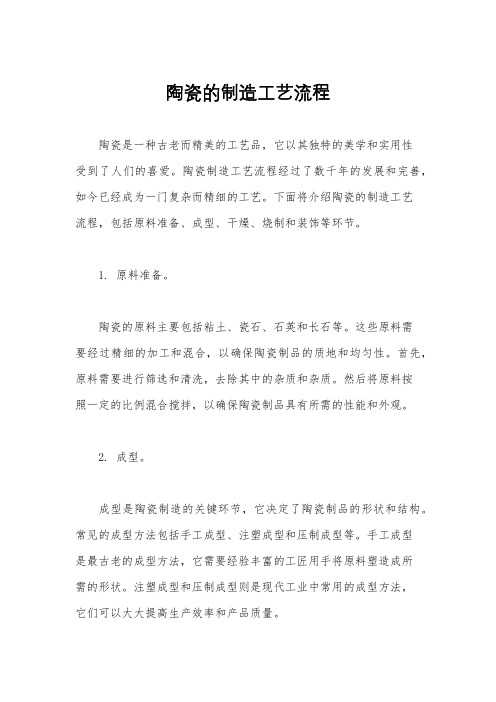
陶瓷的制造工艺流程陶瓷是一种古老而精美的工艺品,它以其独特的美学和实用性受到了人们的喜爱。
陶瓷制造工艺流程经过了数千年的发展和完善,如今已经成为一门复杂而精细的工艺。
下面将介绍陶瓷的制造工艺流程,包括原料准备、成型、干燥、烧制和装饰等环节。
1. 原料准备。
陶瓷的原料主要包括粘土、瓷石、石英和长石等。
这些原料需要经过精细的加工和混合,以确保陶瓷制品的质地和均匀性。
首先,原料需要进行筛选和清洗,去除其中的杂质和杂质。
然后将原料按照一定的比例混合搅拌,以确保陶瓷制品具有所需的性能和外观。
2. 成型。
成型是陶瓷制造的关键环节,它决定了陶瓷制品的形状和结构。
常见的成型方法包括手工成型、注塑成型和压制成型等。
手工成型是最古老的成型方法,它需要经验丰富的工匠用手将原料塑造成所需的形状。
注塑成型和压制成型则是现代工业中常用的成型方法,它们可以大大提高生产效率和产品质量。
3. 干燥。
成型后的陶瓷制品需要经过干燥过程,以去除其中的水分。
干燥是一个至关重要的环节,它直接影响着陶瓷制品的质量和稳定性。
通常情况下,陶瓷制品会在室温下自然干燥一段时间,然后再进行加热干燥,以确保其内部完全干燥。
4. 烧制。
烧制是陶瓷制造的核心环节,它将成型干燥后的陶瓷制品转化为坚硬的陶瓷制品。
烧制的温度和时间是关键因素,它们直接影响着陶瓷制品的质地和色泽。
通常情况下,陶瓷制品会被放入窑炉中进行烧制,温度和时间会根据不同的陶瓷制品和要求进行调整。
5. 装饰。
装饰是陶瓷制品的点睛之笔,它可以赋予陶瓷制品更加丰富的艺术和文化内涵。
常见的装饰方法包括釉上彩、刻画、贴花和镶嵌等。
这些装饰方法需要经过精细的设计和施工,以确保陶瓷制品具有独特的美感和表现力。
综上所述,陶瓷的制造工艺流程经过了数千年的发展和完善,它包括原料准备、成型、干燥、烧制和装饰等环节。
每一个环节都需要经验丰富的工匠和精湛的技艺,以确保陶瓷制品具有高质量和独特的艺术价值。
希望通过对陶瓷制造工艺流程的介绍,能够让更多的人了解和欣赏这一古老而精美的工艺品。
陶瓷翻模工艺介绍

陶瓷翻模工艺介绍
陶瓷翻模工艺是一种将陶瓷原型制作成模具的技术。
翻模工艺分为模型制作、制模和制品制作三个步骤。
第一步是模型制作。
在陶瓷翻模工艺中,常用的模型制作材料有泥、蜡和树脂等。
首先,将设计师设计好的陶瓷原型用这些材料制作成三维模型。
这个过程需要非常细致的手工操作来保证模型的精确性和细节的展现。
第二步是制模。
在制模过程中,将模型制作成可用于翻模的硅胶模具或石膏模具。
首先,将模型放置在一个容器中,然后用特制的硅胶或石膏材料倒入容器中,等材料凝固后,将容器打开,取出硅胶模具或石膏模具。
硅胶模具具有高弹性和耐高温的特点,石膏模具则相对便宜,但耐用度较低。
第三步是制品制作。
在这个步骤中,使用制作好的模具来制作陶瓷制品。
首先,在模具内涂上一层薄薄的脱模剂。
然后,将陶瓷浆料倒入模具中,等待一定时间,使浆料凝固。
最后,将模具分开,取出制成的陶瓷制品。
制品制作的质量取决于模具的制作精度和陶瓷浆料的质量。
陶瓷翻模工艺广泛应用于陶瓷制品的生产中,可以大批量制作出形状相同、细节丰富的陶瓷制品。
这种工艺的特点是制作周期较短,重复性好。
但是,翻模工艺也存在一些局限性,例如对于特殊形状的陶瓷制品,需要重新设计模具,增加了制作的复杂性。
陶瓷的制造工艺流程

陶瓷的制造工艺流程
《陶瓷制造工艺流程》
陶瓷制造是一个复杂而精细的工艺过程,经历了数千年的发展和创新。
从原料的准备到成品的烧制,每个环节都需要精心的设计和操作。
以下是一个典型的陶瓷制造工艺流程:
1. 原料准备:陶瓷的主要原料包括粘土、石英、长石和石膏等。
这些原料需要经过精细的筛选和混合,确保其成分和质量达到要求。
2. 成型:原料在经过混合后,需要进行成型。
成型的方法有手工成型、机械成型和注塑成型等。
通过成型,原料可以被制成各种形状的陶瓷坯体。
3. 干燥:成型后的陶瓷坯体需要进行干燥,以去除其中的水分。
这一步骤非常关键,因为如果水分未能充分去除,会在烧制过程中导致产品变形或开裂。
4. 装饰:一些陶瓷制品需要进行装饰,可以使用绘画、贴花、贴金或刻字等手法。
这些装饰可以增加产品的美观度和附加值。
5. 烧制:烧制是陶瓷制造中最重要的环节。
陶瓷坯体需要放入窑中进行高温烧制,以将其变成坚硬的陶瓷制品。
烧制的温度和时间会根据不同的产品要求和原料特性有所不同。
6. 磨光和包装:烧制后的陶瓷制品需要进行磨光处理,以去除
表面的毛刺和不平整。
随后进行包装,以保护产品在运输和销售过程中的完整性。
以上便是陶瓷制造的典型工艺流程,虽然每一步骤都显得简单,但实际操作中需要经验丰富的专业人员进行严格控制和监督。
只有不断地改进和创新,才能生产出更加优质的陶瓷产品。
陶瓷瓦生产工艺流程解读

陶瓷瓦生产工艺流程解读陶瓷瓦是一种常见的建筑材料,广泛应用于屋顶的覆盖。
本文将介绍陶瓷瓦的生产工艺流程,从原料选择到成品制作的各个环节,以及其中所涉及的技术和工艺。
1. 原料准备陶瓷瓦的主要原料包括粘土、矽质材料和颜料等。
首先,根据瓦型和设计要求,选择合适的粘土和矽质材料。
粘土应具备一定的粘结性和可塑性,而矽质材料用于增加陶瓷瓦的硬度和耐久性。
此外,根据需要,可以添加一些颜料进行调色。
2. 原料处理将采购回来的粘土和矽质材料进行混合处理。
这一步骤主要是为了确保原料的均匀性和稳定性。
一般情况下,原料会被送入一个混合设备中,在适当的温度和湿度下进行搅拌,以确保各种原料充分混合均匀。
3. 制胚制胚是陶瓷瓦生产的关键环节之一。
在制胚过程中,原料经过压制、切割和成型等工艺加工,完成瓦坯的制造。
通常情况下,会使用专用的陶瓷瓦制胚机进行加工,以确保制造出一致的瓦坯尺寸和形状。
4. 干燥制胚完成后,瓦坯需要进行充分的干燥。
这是为了去除瓦坯中的水分,防止在烧制过程中出现开裂等问题。
干燥的时间和温度需要严格控制,以确保瓦坯完全干燥而不引起变形或开裂。
5. 烧制瓦坯干燥后,将进入烧制环节。
烧制是将瓦坯加热到高温并进行化学变化从而成为陶瓷瓦的过程。
烧制的温度和时间会根据具体的陶瓷瓦类型和要求而有所不同。
烧制的过程中,瓦坯会逐渐固化并形成坚硬的陶瓷结构。
6. 表面处理烧制完成后,瓦坯会进行表面处理。
这包括修整、涂釉和装饰等工艺。
修整是为了去除表面的瑕疵和不规则部分,使瓦面光滑平整。
涂釉是为了增加陶瓷瓦的耐候性和美观度,通常通过喷涂或浸涂的方式进行。
装饰工艺方面,可以根据设计要求进行彩绘、贴花等装饰,以增加陶瓷瓦的装饰效果。
7. 终检和包装最后一步是对成品进行终检和包装。
终检是为了确保陶瓷瓦的质量符合要求,检查瓦面的光洁度、尺寸的准确性以及颜色的一致性等。
合格的陶瓷瓦会被打包和包装,以便储存和运输。
通过以上的工艺流程,陶瓷瓦从原料的准备到成品的制作,经历了多个环节和工艺技术的应用。
卫生瓷陶瓷厂工艺设计 最终版

年产63万件卫生瓷陶瓷厂工艺设计1厂址的选择论证1.1建厂地区的选择厂址选在唐山市丰南沿海陶瓷产业创新示范园区1.1.1地理环境丰南沿海陶瓷产业创新示范园区位于唐山南部沿海、渤海湾中心地带,交通便利,生态环境良好,基础设施一应俱全,投资环境优越。
丰南沿海陶瓷产业创新示范园区地处环渤海中心地带、唐山南部,距唐山市中心区80千米,距离秦皇岛170千米,毗邻京津两大城市,距离北京220千米,距离天津120千米,是“一带一路”和京津冀协同发展的重要连接点。
它南临渤海,与青岛、大连、上海以及日本、韩国隔海相望,港口条件得天独厚,概括为水深、港阔、地广,具有临港产业低成本聚集的先天优势。
曹妃甸是正在崛起的国家级开发区,丰南沿海陶瓷产业创新示范园区属曹妃甸区,在不久的将来,曹妃甸将会成为东北亚区域合作的窗口、环渤海地区的新型工业化基地、首都经济圈的重要支点。
依托华北理工大学和唐山学院,为企业用工开展免费、定单式培训,为企业量身打造专门人才。
1.1.2自然气候丰南沿海陶瓷产业创新示范园区属东部季风区温带半湿润地区,大陆性季风特征显著,年均气温11℃,年降水量636毫米,四季分明;曹妃甸还有一大宝贵的自然资源—湿地,空气中负氧离子含量很高,是城市居民梦寐以求的天然氧吧。
因此曹妃甸适于发展教育科研、文化创意、高新技术、总部经济等高端服务业。
1.1.3自然资源(1)土地资源优势,曹妃甸工业区现有建设用地310平方公里,可为城市开发建设提供充足的用地,且具有国内其他同级开发区不具备的价格优势(2)石油天然气资源优势,区内冀东油田蕴藏着丰富的石油、天然气资源,液化天然气项目的建成使曹妃甸新区有了充足的燃气资源(3)水资源优势,曹妃甸拥有丰富的深水岸线,供水能力达到2亿吨每年,具备了向工业区供水的能力。
1.1.4交通运输(1)唐山市是全国性的综合交通枢纽城市之一。
丰南沿海陶瓷产业创新示范园区境内的唐曹高速公路、沿海高速公路与京沈、唐津、唐港高速、唐承高速互通,唐遵、卑水、汉南、滦港4条国铁支线南北相连,正在建设和谋划的铁路有蒙曹铁路、唐曹城际铁路、京唐曹城际铁路、曹黄铁路、曹秦铁路、迁曹铁路。
制作陶瓷的工艺流程
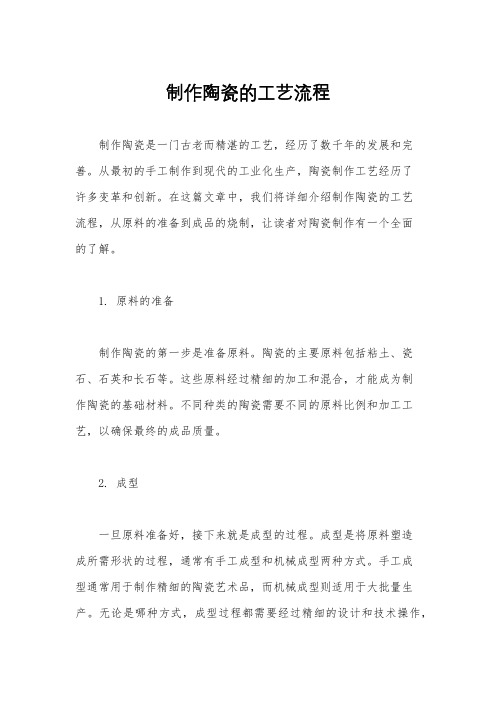
制作陶瓷的工艺流程制作陶瓷是一门古老而精湛的工艺,经历了数千年的发展和完善。
从最初的手工制作到现代的工业化生产,陶瓷制作工艺经历了许多变革和创新。
在这篇文章中,我们将详细介绍制作陶瓷的工艺流程,从原料的准备到成品的烧制,让读者对陶瓷制作有一个全面的了解。
1. 原料的准备制作陶瓷的第一步是准备原料。
陶瓷的主要原料包括粘土、瓷石、石英和长石等。
这些原料经过精细的加工和混合,才能成为制作陶瓷的基础材料。
不同种类的陶瓷需要不同的原料比例和加工工艺,以确保最终的成品质量。
2. 成型一旦原料准备好,接下来就是成型的过程。
成型是将原料塑造成所需形状的过程,通常有手工成型和机械成型两种方式。
手工成型通常用于制作精细的陶瓷艺术品,而机械成型则适用于大批量生产。
无论是哪种方式,成型过程都需要经过精细的设计和技术操作,以确保成品的质量和形状的准确度。
3. 干燥成型完成后,陶瓷制品需要进行干燥。
干燥的目的是去除原料中的水分,使制品变得坚硬和稳定。
通常会有自然干燥和人工干燥两种方式。
自然干燥需要在通风干燥室或者户外进行,而人工干燥则需要利用干燥设备进行加速干燥。
干燥的时间和温度需要根据原料的性质和制品的大小来进行调整,以确保制品的质量和稳定性。
4. 装饰装饰是陶瓷制品的重要环节,可以通过刻画、绘画、贴花等方式进行。
装饰不仅可以美化陶瓷制品,还可以增加其艺术价值和观赏性。
不同的装饰方式需要不同的技术和工艺,通常需要经过多道工序和精细的操作才能完成。
5. 烧制烧制是制作陶瓷的最后一道工序,也是最关键的一道工序。
烧制的目的是将原料中的无机物质转化为玻璃状物质,使制品变得坚硬和耐用。
烧制的温度和时间是影响陶瓷制品质量的关键因素,需要根据原料的性质和制品的要求来进行精确控制。
烧制过程中还需要注意防止制品变形、开裂和变色等问题的发生。
6. 包装最后,制作好的陶瓷制品需要进行包装。
包装的目的是保护制品不受损坏,并便于运输和销售。
不同种类的陶瓷制品需要不同的包装方式,通常会使用泡沫箱、纸盒、木箱等材料进行包装。
卫浴陶瓷生产工艺流程

卫浴陶瓷生产工艺流程
《卫浴陶瓷生产工艺流程》
卫浴陶瓷是指在卫生间使用的陶瓷制品,包括洗手盆、马桶、浴缸等。
其生产工艺流程是经过多道工序制作的,下面将介绍一下其生产工艺流程。
首先是原料准备。
卫浴陶瓷的主要原料是粘土和瓷石,进入生产车间后要经过搅拌、干燥等处理,将原料制成坯料。
然后是成型。
坯料经过挤压、注塑等工艺加工成型,常见的有旋转成型、注塑成型和冲压成型。
接着是烧制。
成型后的卫浴陶瓷要经过高温烧制,一般烧制温度在1200℃以上。
这个过程是非常关键的,烧制的温度和时
间都会直接影响产品的质量。
之后是喷釉。
烧制后的卫浴陶瓷表面会进行喷釉处理,这个过程可以增加产品的光泽度和防水性能,同时也可以增强产品的美观性。
最后是包装。
经过一系列工序后的卫浴陶瓷产品需要进行包装,这个过程包括产品检验、包装设计和标识标牌添加等。
以上就是卫浴陶瓷的生产工艺流程,这个过程非常繁琐,需要经验丰富的工人来进行操作。
只有经过精心设计和严格管理,才能生产出高质量的卫浴陶瓷产品。
建筑陶瓷生产工艺流程
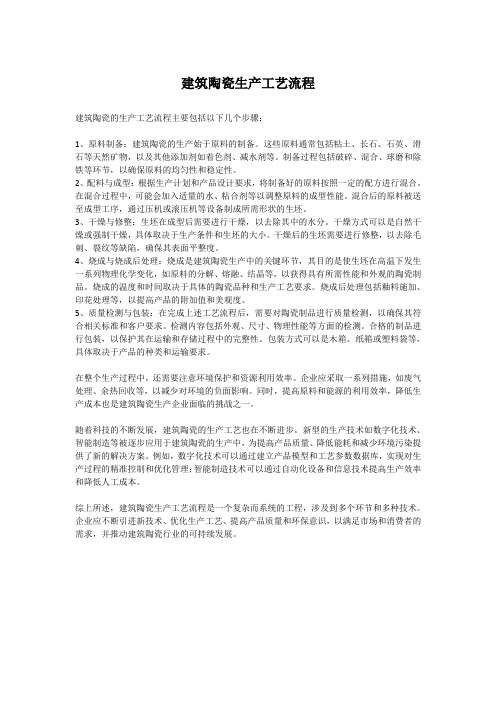
建筑陶瓷生产工艺流程建筑陶瓷的生产工艺流程主要包括以下几个步骤:1、原料制备:建筑陶瓷的生产始于原料的制备。
这些原料通常包括粘土、长石、石英、滑石等天然矿物,以及其他添加剂如着色剂、减水剂等。
制备过程包括破碎、混合、球磨和除铁等环节,以确保原料的均匀性和稳定性。
2、配料与成型:根据生产计划和产品设计要求,将制备好的原料按照一定的配方进行混合。
在混合过程中,可能会加入适量的水、粘合剂等以调整原料的成型性能。
混合后的原料被送至成型工序,通过压机或滚压机等设备制成所需形状的生坯。
3、干燥与修整:生坯在成型后需要进行干燥,以去除其中的水分。
干燥方式可以是自然干燥或强制干燥,具体取决于生产条件和生坯的大小。
干燥后的生坯需要进行修整,以去除毛刺、裂纹等缺陷,确保其表面平整度。
4、烧成与烧成后处理:烧成是建筑陶瓷生产中的关键环节,其目的是使生坯在高温下发生一系列物理化学变化,如原料的分解、熔融、结晶等,以获得具有所需性能和外观的陶瓷制品。
烧成的温度和时间取决于具体的陶瓷品种和生产工艺要求。
烧成后处理包括釉料施加、印花处理等,以提高产品的附加值和美观度。
5、质量检测与包装:在完成上述工艺流程后,需要对陶瓷制品进行质量检测,以确保其符合相关标准和客户要求。
检测内容包括外观、尺寸、物理性能等方面的检测。
合格的制品进行包装,以保护其在运输和存储过程中的完整性。
包装方式可以是木箱、纸箱或塑料袋等,具体取决于产品的种类和运输要求。
在整个生产过程中,还需要注意环境保护和资源利用效率。
企业应采取一系列措施,如废气处理、余热回收等,以减少对环境的负面影响。
同时,提高原料和能源的利用效率,降低生产成本也是建筑陶瓷生产企业面临的挑战之一。
随着科技的不断发展,建筑陶瓷的生产工艺也在不断进步。
新型的生产技术如数字化技术、智能制造等被逐步应用于建筑陶瓷的生产中,为提高产品质量、降低能耗和减少环境污染提供了新的解决方案。
例如,数字化技术可以通过建立产品模型和工艺参数数据库,实现对生产过程的精准控制和优化管理;智能制造技术可以通过自动化设备和信息技术提高生产效率和降低人工成本。
- 1、下载文档前请自行甄别文档内容的完整性,平台不提供额外的编辑、内容补充、找答案等附加服务。
- 2、"仅部分预览"的文档,不可在线预览部分如存在完整性等问题,可反馈申请退款(可完整预览的文档不适用该条件!)。
- 3、如文档侵犯您的权益,请联系客服反馈,我们会尽快为您处理(人工客服工作时间:9:00-18:30)。
椭圆滚压成形机 解决了非圆形回转体产品滚压成形 难的难题,主要用于陶瓷厂生产椭 圆扁平制品-鱼盘和具有一定深度 的椭圆形锅类制品,可取代注浆成 形和旋压成形。
2.1.3 挤出、车坯
工艺特点:适用于管件、棒件、板件及砖 瓦,在电瓷、无线电陶瓷及砖瓦等行业中 广泛应用。
一般套管、棒形、支柱类电瓷产品:用低 水分泥段在横式或立式车床上车修成型;
成型车间的基本要求
3)采暖通风 安装热风管、热风机和通风设备。 车间内不允许存在不均匀的气流,对北方地区
应考虑冬春季节的保温和防风措施。 卫生陶瓷成型车间温度一般为20~28℃,相对
湿度60%左右;采暖高度0.4~1.2米。 大面积厂房中可在注浆台下设置蒸汽排管,排
管的设置高度应低于注浆台面100~150毫米。
旋坯机的选择
单刀旋坯机:适用于各种迥转器形, 生产能力同产品最大直径有关。对日 用瓷,一般60~300件/时,大直径产 品取低值;
双刀旋坯机:适合碗、盘、杯和碟的 成型,生产效率高于单刀旋坯机,当 产品最大直径为250毫米时,生产能 力为420~540件/h;
鱼盘旋坯机:生产能力800~1600件/ 班;
旋壶机:生产能力900件/班。
2.1.2 滚压
工艺特点:机械化半自动化成型,坯件产量高、质 量好;可取代旋坯成型,目前国内日用瓷厂普遍采 用;
滚压成型机:固定式、转盘式和往复式。 生产能力:一般盘、碗、碟为480~1000件/班,因
产品而异 。
滚压成型机
滚头转向滑板式异形产品滚压成型机 采用滚头转向、滑板移位和自动夹摸装置,能滚压成 形腹部或底部直径大于口部直径的陶瓷制品,并解决 了大件产品模型取放的难题
成型车间的基本要求
2)采光
利用天窗、侧窗并辅以局部照明。 各种制品Байду номын сангаас成型、检验、上釉及卫生陶瓷注型、修粘
打磨等部分的采光,一般不低于三级;对釉面砖半成 品检验部分在条件可能时应提高采光要求。 采用大跨度的连跨或单跨度的建筑厂房,可利用锯齿 形结构的天窗来满足采光的要求。 成型车间对采光的要求较高,车间方位对采光影响较 大,应特别予以注意。
二、成型工艺的选择
2.1可塑成型 2.2注浆成型 2.3压制成型 注射成型 挤出成型 轧膜成型 流延成型 凝胶注模成型 直接凝固注模成型
2.1可塑成型
可塑成型工艺:旋坯、滚压、挤坯、 拉坯,车坯和湿压等。
适用产品:大部分日用瓷、电瓷产品。
2.1.1 旋坯
工艺特点:半机械化成型,适合各种规格的回旋对称 型器皿; 如碗、盘、杯、碟和悬式、针式绝缘子等。在不 同模型的配合下,能使器皿产生浮雕、花纹、图案条 棱的效果。改变模型、调整型刀还可用于口径大的壶 类及鱼盘等制品;
空心和中孔大小不等的坯件:采用立式多 刀湿车,内径为直筒形的多采用横式湿车; 对于大套管,可以采用湿坯接、瓷接和整 体车修等三种方法。
滚压成型机
滚头臂转向滑板式异形产品滚压成型机 采用滚头臂转向、滑板移位和自动夹摸装置,能滚压成形腹部或底
部直径大于口部直径的陶瓷制品。
滚压成型机
椭圆滑板式异型产品滚压成型机 采用夹模自动装置解决了非圆形回转体 且腹部大于口部的锅类产品滚压成形难 的难题,主要用于陶瓷厂生产锅类、腹 部大于口部具有一定深度的椭圆形制品, 可取代注浆成形和旋压成形。
成型方法:多种多样;陶瓷产品种类繁多,形 状相差悬殊,坯料性能也不一致。
选择成型工艺的考虑因素:制品的形状、大小、 厚薄、产量、质量、泥料性质、技术与设备条 件、经济效果等。
一、 成型车间工艺特点与工艺设计原则
1.1 工艺特征 1)产品品种变动较大:除墙地砖外,多数陶瓷制品品
种多样,规格不一,且多属于小批量生产,因此成型 车间对产品品种的变动应具有较强的适应能力。 2)机械化、自动化程度较低:除墙地砖厂的成型车间 具有较高的机械化、自动化水平外,其它产品常为人 工操作。 3)运输量大:经常多品种同时加工,形成泥料运输、 坯件传递、废坯料、回坯料等复杂的物流与人流路线。 不同产品运输方式各异,为防止坯件碰损,应避免或 减少坯件的重复搬放,并尽可能采用机械化运输。 4)车间人员密度大:其中女工比例较大。
1.2 成型车间工艺设计的原则
1)尽可能选用切实可行的先进工艺和技术; 工艺简单、快捷、低耗、劳动条件好,尽
量减少工序、缩短生产周期,提高生产率,降 低原材料、燃料消耗,改善劳动条件。 2)成型生产工艺流程应力求单一化;
在满足制品加工要求的前提下,不同规格 或品种的产品尽可能采用相同的工艺流程,以 利于安排生产计划和生产调度。
1.3 成型车间的基本要求
1)土建要求 厂房:跨度一般12米、柱距6米,房架下弦的高度一般为
4.0~7.0米。考虑夏季通风,南方地区可取厂房高度的上限值。 车间交通:主要通道(车间与车间通道、车间内上下工序之
间的通道、主要人流通道)宽度一般在3米左右,干燥车单向 通道宽度一般1.5~1.7米,注浆件粘接工序操作通道净距一般 为0.6~0.8米。干燥室两端净空不得小于4米,以便车辆运转 和进出干燥室之用。 卫生:墙和地面应光滑,避免起尘且便于冲洗;门窗应有防 止室外尘土侵入的措施。 防护:卫生陶瓷成型车间的门窗应避免阳光直射和冷空气直 接侵袭坯体。
§4.2 陶瓷厂成型车间工艺设计
概述 成型车间工艺特点与工艺工艺设计原则 成型工艺的选择
可塑成型、 注浆成型、压制成型 干燥 修坯与粘接 施釉 成型车间生产流水线的组织
陶瓷厂成型车间工艺设计
成型车间的任务:将原料车间提供的可塑泥料、 浆料或粉料加工成坯体,并进行干燥、上釉, 为烧成车间提供质量合格的坯件。
成型车间工艺设计的原则
3)合理组织物流与人流; 避免交叉往返与不均衡现象;
4)按生产流水线布置设备和工位; 根据设备外形及基础尺寸要求,工艺相同
的产品,其成型设备宜集中布置在一条线上, 便于成型余泥和废坯采用皮带运输方式回收和 加工、干噪热风管道的布置。 5)成型、修坯、上釉等设备附近要留出空地 堆放模具,安置活动层架车或坯架。