焦化厂焦炉煤气脱硫工段的设计
焦化厂焦炉煤气二级加氢转化、二级脱硫工艺分析与设计技术实施方案

焦化厂焦炉煤气二级加氢转化、二级脱硫工艺分析与设计技术实施方案1.二级加氢转化:二级加氢转化器负责将经一级脱硫后焦炉煤气中剩余的少量的有机硫尤其是较难加氢转化的部分有机硫进一步加氢转化生成硫化氢。
设计上选用的催化剂是镍钼加氢转化催化剂,其作用机理与铁钼系列催化剂相同。
实际运行中由于到二级加氢转化器人口时气体温度相对较高,且催化剂床层温升大,常常导致二级加氢转化器出口及二级脱硫槽超温。
有的厂家为解决二级加氢转化器的超温现象,在其催化剂床层增加了冷激线,然而在实际生产中此冷激线不易开的过大,否则会导致脱硫负荷后移,影响脱硫工艺的整体经济运行。
因此控制二级加氢转化器的入口温度和催化剂床层温升才是优先调节手段。
然而控制入口温度又限制了一级加氢转化器床层及出口温度的提升而影响催化剂活性的充分发挥,尤其在后期需要提温增强活性时。
另外镍钼加氢转化催化剂的生产成本也较高,是铁钼系列的2~3倍。
鉴于此,一种新型钛系有机硫加氢转化催化剂(主要成分为二氧化钛):温升小,且其使用前不必硫化,用在二级加氢转化器的位置,可以适当提高一级加氢转化器的床层温度,而不用担心后系统超温。
但在使用过程也出现了新问题:由于其发热量低,床层温升偏小又导致二级脱硫槽及工段出口温度偏低,这对于预加氢转化器入口的焦炉气用高温转化气换热提温的工艺来说,脱硫工段出口温度的偏低导致与其换热的焦炉气预热器出口的转化气温度(亦即焦炉气初预热器入口的转化气温度)降低,从而进一步影响焦炉气初预热器出口的焦炉气温度(亦即预加氢转化器的入口温度)的提升,尤其是在预加氢转化器及一级加氢转化器使用后期,催化剂床层温升减小后,此影响更加明显,系统的热量平衡受到影响。
以上分析可知二级加氢转化器催化剂床层的温升对整个脱硫系统温度与热量平衡有很大的影响,因此对于其催化剂的选择要满足两点:一是具有少量的有机硫加氢转化作用,二是催化剂床层具有合适的发热量、温升,确保系统的热量平衡。
焦炉煤气制合成气的脱硫及净化工艺技术_汪家铭
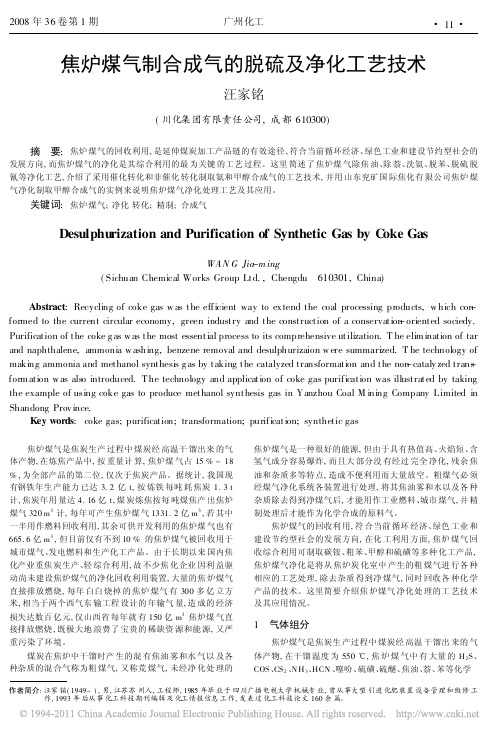
各种组分名称
含量
焦油雾
65~ 125
水气 氮化合物
硫化合物
氧化合物 氯化合物 碳氢化合物
煤中水分的 水气 化合水的水气 氨( NH3 ) 氰化氢( HCN ) 吡啶( C5 H5 N) 氧化氮( N O) 硫 化氢( H2S) 二硫化碳( CS2 ) 硫氧化碳( COS) 噻吩( C4 H4S) 硫醇( CnH2n+ 2 S) 二氧化硫( SO2 ) 酚及同系 物
Key words: coke gas; purificat ion; transformation; purif icat ion; synthet ic gas
焦炉煤气是焦炭生产 过程中 煤炭经 高温干 馏出来 的气 体产物, 在炼焦产品中, 按 重量计 算, 焦炉煤 气占 15 % ~ 18 % , 为全部产品的第二位, 仅次于焦炭产品。据统计, 我国现 有钢铁年生 产能力 已达 3. 2 亿 t, 按 炼铁 每吨 耗 焦炭 1. 3 t 计, 焦炭年用 量达 4. 16 亿 t, 煤 炭炼焦按每 吨煤焦产 出焦炉 煤气 320 m3 计, 每年可产生焦炉煤 气 1331. 2 亿 m3 , 若 其中 一半用作燃料回收利用, 其余可供开发利用的焦炉煤 气也有 665. 6 亿 m3 , 但目前仅有不到 10 % 的焦炉煤气被回 收用于 城市煤气、发电燃料和生产化工产品。由于长期以来 国内焦
0. 02
0. 06
0. 01~ 0. 05
0. 05
0. 1
0. 1
0. 05
0. 03~ 0. 01
0. 02
0. 01~ 0. 02
( g m3) 萘 0. 3 0. 2
年产70万吨焦炭焦化厂毕业设计

焦化厂是炼焦行业的主要生产设施,主要用于将煤炭加热至高温下进行热解,产生焦炭、焦炉煤气和焦油等副产品。
本文将对一个年产70万吨焦炭的焦化厂进行毕业设计,包括以下内容:厂区设计、工艺流程、设备选型、环境保护等。
1.厂区设计:焦化厂的厂区面积应足够大,以容纳煤炭储存、炼焦、气体处理和产品运输等各个生产区域。
厂区应具有良好的硬质道路、供水、供电和卫生设施等基础设施,以确保生产的正常进行。
2.工艺流程:焦化厂的工艺流程主要包括煤炭破碎、除尘、焦炉炼焦、气体处理和产品收集等环节。
(1)煤炭破碎:使用煤炭破碎机将大块煤炭破碎成适合炼焦的小颗粒。
(2)除尘:煤炭破碎和炼焦过程中会产生大量的粉尘,需要通过除尘设备进行处理,以减少对环境的影响。
(3)焦炉炼焦:将破碎后的煤炭投入焦炉进行热解,同时通过燃烧热能产生焦炉煤气。
(4)气体处理:将焦炉煤气进行脱硫、脱氰等处理,以减少对环境和人体的污染。
(5)产品收集:从焦炉煤气中提取焦油和其他有价值的副产品。
3.设备选型:对于年产70万吨焦炭的焦化厂,需要选择适合规模的设备。
(1)煤炭破碎机:根据煤炭的硬度和颗粒度要求,选择适合的煤炭破碎机。
(2)除尘设备:根据排放标准,选择适合的除尘设备,如电除尘器或袋式除尘器。
(3)焦炉:选择适宜规模和效率的焦炉,以提高焦炉产出和降低能耗。
(4)气体处理设备:选择适合的脱硫、脱氰设备,如干法处理或湿法处理等。
(5)产品收集设备:选择适宜的焦油分离装置和其他副产品的收集设备。
4.环境保护:焦化厂是重要的污染源之一,为了减少环境污染,需要采取相应的措施。
(1)安装除尘设备和脱硫设备,减少粉尘和气体污染物的排放。
(2)合理规划厂区,将生产区域与居民区、水源保护区等分开,降低对周边环境的影响。
(3)定期进行环境监测,确保排放符合国家标准。
(4)建立完善的废物处理体系,对废弃物进行合理处置,避免对土壤和水体的污染。
综上所述,本文对年产70万吨焦炭的焦化厂进行了毕业设计,包括厂区设计、工艺流程、设备选型和环境保护等方面。
焦化厂烟气脱硝脱硫一体化解决方案1

110万吨/年焦炉烟气脱硝脱硫一体化技术方案110万吨/年焦炉烟道气与脱硝脱硫一体化设计方案廊坊市晋盛节能技术服务有限公司目录1. 项目概述 (2)1.1. 项目概况 (2)2. 设计依据 (2)2.1. 设计原则 (2)2.2. 设计标准 (3)2.3. 设计原始参数 (3)2.3.1 烟气参数 (3)2.3.2 气候条件 (4)2.4. 设计要求 (4)2.5. 工程范围 (4)3. 烟气脱硫脱硝一体化工艺 (5)3.1. 总工艺流程 (5)3.2. 脱硝工艺 (5)3.3. 脱硫工艺 (7)4. 烟气脱硫脱硝一体化技术说明 (8)4.1. 脱硝技术 (8)4.1.1脱硝系统的构成 (8)4.1.2脱硝系统主要设备 (9)4.2. 脱硫技术 (11)4.2.1脱硫工艺描述 (11)4.2.2脱硫主要设备 (11)5. 经济及环境效益分析 (13)5.1脱硫脱硝环境效益及节约费用 (13)5.2脱硫脱硝运行费用 (13)5.3脱硫脱硝投资费用 (14)5.4设备清单 (13)1.项目概述1.1.项目概况焦化厂是专门从事冶金焦炭生产及冶炼焦化产品、加工、回收的专业工厂。
焦、NOx及烟尘炉烟囱排放的大气污染物为焦炉煤气燃烧后产生的废气,主要有SO2等,污染物呈有组织高架点源连续性排放,是污染最为严重的行业之一。
2012年6月,环境保护部及国家质量监督检验检疫局联合发布了《炼焦化学工业污染物排放标准》,明确规定了焦化工业的大气污染物排放标准。
廊坊市晋盛节能技术服务有限公司一体化烟气治理技术,就是将烟气烟气除尘技术,烟气脱硫、脱硝技术捆绑在一起,形成一套集成创新的装置,这套装置既能除尘、脱硫、脱硝,从而达到烟气资源化利用的目的。
从此改变烟气治理只有投入,没有产出的困境。
2.设计依据2.1.设计原则2.1.1脱硫脱硝➢对尾气同时进行脱硝及脱硫治理。
➢采用高效、先进、运行稳定、管理方便的治理工艺及技术,保证废气的达标排放;➢烟气净化治理不影响焦化厂生产工艺的正常运行。
脱硫工段—脱硫工段生产流程与设备(焦炉煤气净化技术课件)
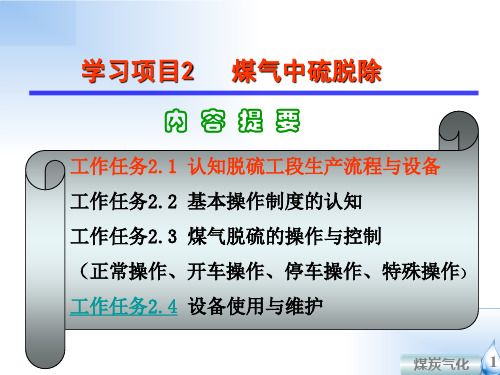
①迅速关闭真空泵酸气入口阀门,并打开交通阀; ②待出口压力减小,逐渐关闭出口阀门; ③同时关闭各泵出入口阀门,并停泵; ④若短时间停电,则做好开泵准备;若长时间停电,按停工操 作,并放空、清扫。
学习单元2.5.3 真空碳酸钠法脱硫操作制度
以含邯钢焦化厂老区真空碳酸钾法工艺为例
三、应急预案和特殊操作
一、脱硫塔技术指标和技术规定
1、硫塔煤气温度:25—27℃,压力:10—13KPa
2、出脱硫塔煤气温度:≤35℃, 压力:8—11KPa 3、脱硫塔阻力≤2000Pa 4、脱硫塔上段液位≤380mm 5、脱硫塔底液位:1000—1600mm 6、上段贫液喷洒量:160m3/h,喷洒压力:0.7MPa 7、下段贫液喷洒量:160m3/h,喷洒压力:0.7MPa 8、冷却器后贫液温度:30—35℃ 9、外排贫液流量:0—0.3m3/h 10、脱硫塔NaOH喷洒液位:≤500mm
3、工区停水:
①停循环水,增加低温水量。 ②停低温水,增加循环水量。
工作任务2.5 真空碳酸钠法脱硫
思考题:
真空碳酸钠法脱硫原理 真空碳酸钠法脱硫 工艺流程 真空碳酸钠法脱硫操作制度
工作任务2.5 真空碳酸钠法脱硫
学习单元2.5.1 真空碳酸钠法脱硫原理 学习单元2.5.2 真空碳酸钠法脱硫工艺流程 学习单元2.5.3 真空碳酸钠法脱硫操作制度 学习单元2.5.4 再生塔尾气制硫磺 学习单元2.5.5 再生塔尾气制硫酸
学习单元2.5.3 真空碳酸钠法脱硫操作制度
以含邯钢焦化厂老区真空碳酸钾法工艺为例
二、再生塔技术指标和技术规定
1、再生塔顶部温度:55℃ 2、入再生塔富液温度:45—50℃ 3、再生塔顶压力:-85— -80KPa 4、再生塔上段液位:180—360mm 5、再生塔塔底液位:800—1200mm 6、入再生塔富液流量:180m3/h
焦化厂焦炉煤气精脱硫工艺分析与设计技术实施方案
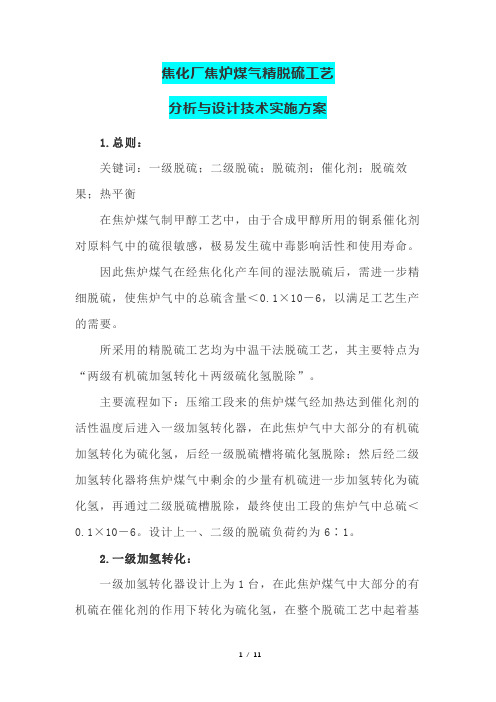
焦化厂焦炉煤气精脱硫工艺分析与设计技术实施方案1.总则:关键词:一级脱硫;二级脱硫;脱硫剂;催化剂;脱硫效果;热平衡在焦炉煤气制甲醇工艺中,由于合成甲醇所用的铜系催化剂对原料气中的硫很敏感,极易发生硫中毒影响活性和使用寿命。
因此焦炉煤气在经焦化化产车间的湿法脱硫后,需进一步精细脱硫,使焦炉气中的总硫含量<0.1×10-6,以满足工艺生产的需要。
所采用的精脱硫工艺均为中温干法脱硫工艺,其主要特点为“两级有机硫加氢转化+两级硫化氢脱除”。
主要流程如下:压缩工段来的焦炉煤气经加热达到催化剂的活性温度后进入一级加氢转化器,在此焦炉气中大部分的有机硫加氢转化为硫化氢,后经一级脱硫槽将硫化氢脱除;然后经二级加氢转化器将焦炉煤气中剩余的少量有机硫进一步加氢转化为硫化氢,再通过二级脱硫槽脱除,最终使出工段的焦炉气中总硫<0.1×10-6。
设计上一、二级的脱硫负荷约为6∶1。
2.一级加氢转化:一级加氢转化器设计上为1台,在此焦炉煤气中大部分的有机硫在催化剂的作用下转化为硫化氢,在整个脱硫工艺中起着基础性作用。
设计上一级加氢转化器选用的催化剂是铁钼加氢转化催化剂,其活性成分是氧化钼和少量的氧化铁,使用前需预先进行升温硫化才能有较好的催化活性。
实际运行表明,只要对催化剂硫化充分,生产中温度控制合适,一级加氢转化器即能够将焦炉煤气中大部分的有机硫进行加氢转化生成硫化氢,满足生产需要。
目前存在的主要问题是,大部分的甲醇生产厂家都反映催化剂的使用寿命不够理想:好的状况下可使用2年,一般的在使用1年后催化剂活性就会大大削弱,有机硫加氢转化能力降低甚至会消失,即使提高催化剂床层的运行温度也不会有大的改观。
如此增加了催化剂的更换频率和脱硫成本。
理论上催化剂的活性是不会下降或消失的,造成这种现象有多方面原因。
催化剂的生产厂家认为是催化剂在使用前硫化不彻底所致,但这并非主要原因:因为催化剂在使用过程中始终是处在一个多硫和强还原性的氛围中,即使在投用前预硫化不十分彻底,但在使用过程中也会不断地有硫化反应发生,直至硫化彻底。
年产100万吨焦炭焦化厂硫铵工段初步设计
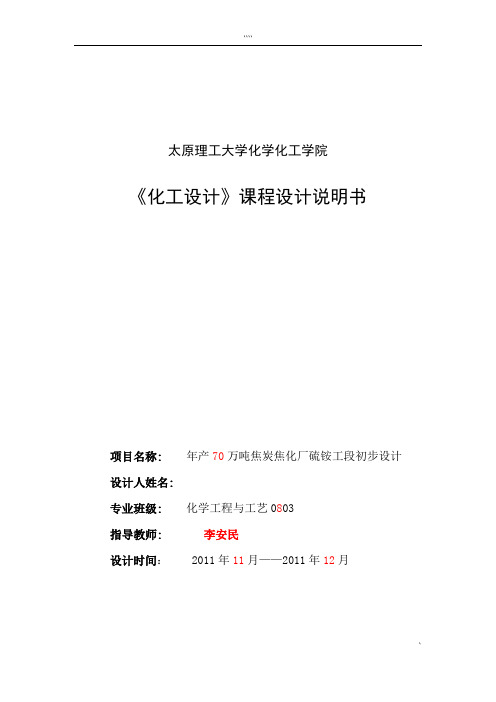
太原理工大学化学化工学院《化工设计》课程设计说明书项目名称: 年产70万吨焦炭焦化厂硫铵工段初步设计设计人姓名:专业班级: 化学工程与工艺0803****: ***设计时间: 2011年11月——2011年12月目录第一章概述1设计依据--------------------------------------------------------------------3 2硫铵生产方法的确定----------------------------------------------------------5 第二章饱和器法硫铵生产工艺1工艺流程图及流程叙述--------------------------------------------------------7 2硫铵工段的正常操作制度------------------------------------------------------8 3硫铵工段的工艺操作参数------------------------------------------------------9 4车间工艺布置---------------------------------------------------------------10 第三章化工计算1计算原始数据---------------------------------------------------------------12 2小时生产能力计算 ----------------------------------------------------------13 3氨平衡计算-----------------------------------------------------------------134 水平衡的计算---------------------------------------------------------------145 热平衡计算-----------------------------------------------------------------15 第四章设备选型1饱和器基本尺寸-------------------------------------------------------------20 2旋风式除酸器的基本尺寸-----------------------------------------------------22 第五章设备结构图叙述及附表1设备结构图叙述-------------------------------------------------------------23 2 工艺设备一览表-------------------------------------------------------------26 致谢-----------------------------------------------------------------------27参考文献--------------------------------------------------------------------28第一章、概 述1设计依据(1) 设计项目名称:年产70万吨焦炭焦化厂硫铵工段初步设计(2) 生产能力:年产干硫铵2.7万吨(3) 生产方法:饱和器法(外部除酸式),又称半直接法(4) 硫铵主要质量标准:硫铵的主要质量标准名称指标 一级品 二级品 三级品 颜色白色或微带颜色的结晶 氮含量(以干基计)≥21 ≥20.8 ≥20.6 水分%≤0.3 ≤1.0 ≤2.0 游离酸()% ≤0.05≤0.2 ≤0.3 粒度(60目筛余量)≥75 (5) 硫铵的物理化学性质:硫铵的分子式为,分子量为132.16。
PDS法焦炉煤气脱硫工艺分析

返回
工艺原理:
总反应方程式 2H2S + O2 → 2S + 2H2O 这方程式是整个脱硫的目的和整体过程,也是经常被大多数人忽略的一个反应方程 式,总方程式决定了总体思维模式。 3.2脱硫原理 对于无机硫: H2S+Na2CO3 → NaHS + NaHCO3 这是典型的复分解反应,也是酸碱中和反应,无须任何催化剂,即使加入催化剂, 也不能影响到反应平衡。 对于有机硫: RSH + Na2CO3 → RSNa + NaHCO3 虽然有机硫的平衡常数比无机硫小,但酸碱中和的推动力,能够使反应进行的深度 也很高。 3.3再生原理 对于无机硫: NaHS + 1/2 O2 → S + NaOH 对于有机硫: 2RSNa + 1/2 O2+ H2O → RSSR + 2NaOH
返回
工艺流程图:
返回
工艺分析:
PDS脱硫工艺是以酞菁钴磺酸盐系化合物的混合物为催化 剂的湿式氧化法脱硫工艺,其工艺过程与HPF工艺类同。 最初使用的PDS是双核酞菁钴六磺酸铵,后改进到二双核 酞菁钴砜+磺酸铵,其活性比原PDS提高一倍。PDS法硫 容量可大于0.5g/L,不发生堵塞,副产品盐类增长速度缓 慢,脱硫率大于97%,脱氰率大于95%,有机硫的脱除率 大于40%,PDS结合栲胶法可以达到更好的脱硫效果,该 工艺的缺点是产生大量废液不好处理,目前独立焦化厂使 用此工艺的较多。
PDS法焦炉煤气脱硫工艺分析
应化3141 张斌
关键词:焦炉煤气;PDS脱硫
人机化 含含 体硫氢 有有 也。及 焦多 未 有不多 油种 经 较但种 气 净 大污结 萘体 化 毒染构 氰组 的 害空复 化分 焦 性气杂 氢, 炉 。,的 ,尤 煤 对有 硫其 气 中
- 1、下载文档前请自行甄别文档内容的完整性,平台不提供额外的编辑、内容补充、找答案等附加服务。
- 2、"仅部分预览"的文档,不可在线预览部分如存在完整性等问题,可反馈申请退款(可完整预览的文档不适用该条件!)。
- 3、如文档侵犯您的权益,请联系客服反馈,我们会尽快为您处理(人工客服工作时间:9:00-18:30)。
本科生毕业设计100万吨/年焦化厂焦炉煤气脱硫工段的设计摘要本设计为100万t/a焦化厂焦炉煤气脱硫工段的设计,采用的煤气脱硫方法为湿法脱硫的改良A.D.A.法。
本设计的主要任务是脱除焦炉煤气中的硫化氢,同时要使生产出来的煤气各项指标能满足要求,达到民用煤气的标准。
设计的主要内容包括:1、煤气脱硫方法的概述和意义;2、工艺流程的选择与论证,选用改良A.D.A法;3、主要设备的计算、选型和布置;4、保障生产正常进行所必须的非工艺部分,包括供水、供电、采暖、设备维修、仪表自动化等;5、经济核算,每生产一吨焦炭该设计工段亏损7.0元。
本设计的工艺部分包括煤气脱硫和脱硫液再生以及硫磺回收。
脱硫采用了脱硫塔,再生部分用再生塔,对于其基本原理,文中有着详细的论述,回收硫部分采用了真空过滤机。
在设计过程中,参考了焦化厂的焦炉煤气净化工艺,并在其基础上将国内外一些新的、成熟的工艺进行了比较、引用。
关键词:焦炉煤气;脱硫;改良A.D.A法AbstractThis is a design of 100 million t / a coking plant coke oven gas desulfurization section, the method for gas desulfurization is the improved ADA law. The main task of this design is the removal of hydrogen sulfide in coke oven gas, and the gas produced to make the indicators to meet the requirements, to civilian gas standards, at the same time.The main contents of the design are as follows:1, an overview of gas desulphurization and significance. 2, the process of selection and demonstration,select the improved of ADA Act. 3, the calculation, selection and arrangement of major equipment. 4, the security necessary for normal production of non-technology components, including water, electricity, heating, equipment maintenance, instrumentation and automation.5, the economic accounting, produce 1 ton of coke necessary to loss of 7.1442 yuan.Part of the design process including gas desulfurization and regeneration of the desulfurization solution and sulfur recovery. In zhe deign, part of desulfurization the desulfurization tower is used, recycled parts recycled tower is used. For the basic principles, the paper has a detailed discussion. Part of sulfur recovery the vacuum filter is used.In the design process, with reference to the coking plant in Xuzhou Universe coke oven gas purification process, and on its basis , compared the home and abroad new, mature technology, and references.Key words: coke oven gas; desulfurization; improved ADA Act目录1 总论................................................................................................................ 错误!未定义书签。
1.1 焦炉煤气脱硫的目的和意义 ................................................................. 错误!未定义书签。
1.2 硫化氢的性质......................................................................................... 错误!未定义书签。
1.3 设计的要求与说明 ................................................................................. 错误!未定义书签。
1.4 设计的任务............................................................................................. 错误!未定义书签。
1.5 厂址的选择............................................................................................. 错误!未定义书签。
1.5.1 地理条件.......................................................................................... 错误!未定义书签。
1.5.2 资源条件.......................................................................................... 错误!未定义书签。
1.5.3 供排水条件...................................................................................... 错误!未定义书签。
1.5.4 交通运输条件.................................................................................. 错误!未定义书签。
1.5.5 经济条件.......................................................................................... 错误!未定义书签。
1.5.6 气候条件.......................................................................................... 错误!未定义书签。
2 脱硫工艺论证及确定 .................................................................................... 错误!未定义书签。
2.1 脱硫方法概述......................................................................................... 错误!未定义书签。
2.1.1 干法脱硫.......................................................................................... 错误!未定义书签。
2.1.2 湿法脱硫.......................................................................................... 错误!未定义书签。
2.2 脱硫工艺的确定..................................................................................... 错误!未定义书签。
2.2.1 脱硫工艺的选择.............................................................................. 错误!未定义书签。
2.2.2 脱硫工艺的优化.............................................................................. 错误!未定义书签。
3 改良A.D.A法脱硫工艺流程及操作 ............................................................. 错误!未定义书签。
3.1 脱硫工艺流程......................................................................................... 错误!未定义书签。
3.2 影响碱液对硫化氢吸收速度的因素 ..................................................... 错误!未定义书签。
3.3 主要工艺参数......................................................................................... 错误!未定义书签。
3.4脱硫工艺操作要点 ................................................................................. 错误!未定义书签。