大型球墨铸铁件铸造工艺的优化设计[1]
大中型厚壁球铁箱体零件的铸造工艺及数值模拟分析

大中型厚壁球铁箱体零件的铸造工艺及数值模拟分析摘要:厚大球铁铸件在铸造时,常应用无冒口铸造工艺与冷铁配合的方法,能够有效提高冒口补缩能力,消除缩孔、缩松和铁豆等铸造缺陷,保证铸件质量,并且还使树脂砂用量减少,提高了工艺出品率。
而为了提高铸造的合格率,常在进行无冒口铸造时添加较小的补偿冒口。
并基于pro/e与procast对铸造工艺进行改进数值模拟,根据模拟结果对工艺进行改进。
关键词:无冒口;球铁铸件;冷铁1 铸件结构特点箱体结构,内部中空,由多个隔板分隔,上下为两个大平板,上板较大,使用时承载其上的部件,板上有螺纹孔和油槽用于固定和润滑,下板通过螺纹孔与下部固定。
侧壁倾斜并内凹。
在上平板上有四个对称分布,呈工字型的油槽,用于将重物放于其上时的润滑,防止该移动板与其他重物接触时因力量过大而产生磨损。
隔板与外壁相交处散热较难,易产生热节,产生缩松,在工艺设计时应注意应用冷铁等措施改进这些部位的散热。
最大壁厚50mm,最小壁厚30mm,该铸件为大型厚壁铸件,壁厚较均匀且与铸件尺寸相适应。
生产经验表明:具有较大平板的铸件,如机床床身等,会因为结构的刚度差,或由于铸件各表面冷却条件的差别产生的内应力,产生翘曲变形。
该件内腔多处为隔板,能够起到拉肋的作用,因此在一定程度上避免了翘曲变形。
2 无冒口铸造工艺原理球墨铸铁中的碳以球形石墨的形态存在,流动性和线收缩与灰铸铁相近,体收缩及形成内应力倾向较大,易产生缩松和裂纹。
在铁水凝固过程中,具有石墨化膨胀的特点,适宜采用均衡凝固方式,要求砂型的刚度较高,在铸件膨胀时约束铸件,对其产生反作用力,形成自补缩。
自补缩不足的部分可以利用冒口进行补缩,冒口的补缩量和补缩时间均较小,可以有效提高铸件的工艺出品率。
本件为厚大球铁件,适用于无冒口铸造的工艺。
3 铸造工艺设计3.1 分型面与浇注位置的选择采用卧浇卧冷,使合型位置、浇注位置、冷却位置相同。
将零件上部的大平板置于铸型下部。
固溶强化球墨铸铁生产工艺

固溶强化球墨铸铁生产工艺固溶强化是一种常用的球墨铸铁生产工艺,通过对球墨铸铁进行固溶处理,可以显著提高其力学性能和耐磨性能。
本文将详细介绍固溶强化球墨铸铁的生产工艺及其优点。
一、固溶强化球墨铸铁的生产工艺1. 原料准备:选择高品质的生铁和合适的合金元素作为原料,确保球墨铸铁的化学成分符合要求。
2. 熔炼:将生铁和合金元素放入高炉或电炉中进行熔炼,控制好熔炼温度和时间,使合金元素充分溶解于铁液中。
3. 铸造:将熔炼好的铁液倒入球墨铸铁模具中,通过冷却凝固形成球墨铸铁件。
4. 固溶处理:将球墨铸铁件放入固溶炉中,加热至一定温度进行固溶处理。
固溶温度一般为球墨铸铁材料的临界温度,不同的合金元素有不同的固溶温度。
5. 淬火处理:固溶处理后的球墨铸铁件需要进行淬火处理,以获得良好的力学性能。
淬火温度和时间需要根据具体材料和要求来确定。
6. 机械加工:经过固溶强化处理的球墨铸铁件可以进行机械加工,如铣削、车削、磨削等,以达到所需的形状和尺寸。
二、固溶强化球墨铸铁的优点1. 提高强度和硬度:固溶处理可以使球墨铸铁中的合金元素均匀溶解,形成固溶体,从而提高材料的强度和硬度。
2. 提高耐磨性:固溶强化处理可以使球墨铸铁中形成更细小、更均匀的碳化物,从而提高材料的耐磨性和抗磨损能力。
3. 改善抗拉强度和韧性:固溶强化可以改善球墨铸铁的抗拉强度和韧性,使其在受力时更加稳定和可靠。
4. 提高抗疲劳性能:经过固溶强化处理的球墨铸铁具有较好的抗疲劳性能,能够在长期受到循环载荷时不易发生断裂和损伤。
5. 优化加工性能:固溶处理可以消除球墨铸铁中的残余应力,减少加工变形和裂纹的产生,提高材料的加工性能。
固溶强化是一种能够显著提高球墨铸铁性能的生产工艺。
通过固溶处理和淬火处理,可以使球墨铸铁具有更好的强度、硬度、耐磨性和韧性,适用于各种机械零部件和工程结构的制造。
球墨铸铁的球化与孕育处理工艺
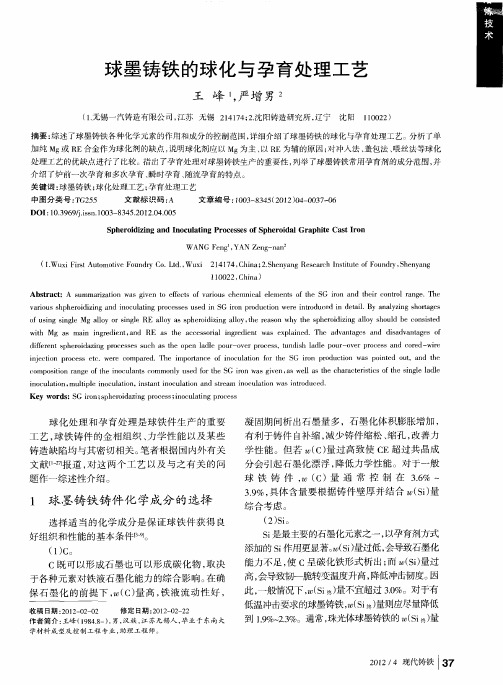
( )。 5 S
c 强烈促进形成碳化物, r 稳定珠光体 。 r c 的 加 入能提 高强 度 和硬 度 , 加 入量 以不 出现 游离 但
碳 化物 为 限 , 于高 韧性铁 素 体球 墨铸 铁要 严 格 对
限 制 ( r 量 。对 于珠 光 体 球 墨 铸 铁 , C) 当加 入 ( r量 02 03 C ) .%~ . %时 , 即可起 到 显 著 的稳 定 珠
10 2 ) 10 2
摘要 : 综述 了球墨铸铁各种化学元素的作 用和成分 的控制范 围, 细介绍 了球墨铸铁 的球化与孕育处理工艺 。 详 分析 了单 加 纯 Mg R 或 E合金作为球化剂的缺点 , 明球化剂应 以 Mg为主 、 R 说 以 E为辅 的原 因 ; 对冲入法 、 盖包法 、 喂丝法等球化 处理工 艺的优缺点进行 了比较 。 出了孕育处理对球墨铸铁生产的重要性 , 指 列举 了球墨铸铁 常用孕育剂的成分范围, 并 介绍 了炉前一次孕育和多次孕育 、 瞬时孕育 、 随流孕育的特点 。 关键词 : 球墨铸铁 ; 球化处理工艺 ; 孕育处理工艺 中图分类号 :G 5 T 25 文献标 识码 : A 文章编号 :0 3 84 (0 2 0 — 0 7 0 10 — 3 5 2 1 )4 0 3 — 6
往需要 进行脱 S处理 ;感 应 电炉熔 炼 由于不用焦 炭, 原铁液 州 S量一般在 0 1% ̄ . %。 () . 5 0 3 不需要进 0 0
R E元 素 中和 , 则会 引起球 化不 良。 E与 s 否 R b并
用 还可 以改 善大 断面件 的球 化 。
( 1微量 干扰 元素 。 1) 球 墨铸 铁 中常存 在 一 些 非 特 意加 入 的微 量
qt600球墨铸铁铸造技术条件

qt600球墨铸铁铸造技术条件(最新版)目录1.QT600 球墨铸铁的概述2.QT600 球墨铸铁的技术要求3.QT600 球墨铸铁的铸造工艺4.QT600 球墨铸铁的应用领域5.结论正文一、QT600 球墨铸铁的概述QT600 球墨铸铁是一种高强度、高韧性的球墨铸铁材料,其抗拉强度达到 600MPa 以上,因此得名 QT600。
这种材料主要应用于各种重型机械、汽车、铁路、船舶等工业领域,尤其适用于高负荷、高强度的工作环境。
二、QT600 球墨铸铁的技术要求QT600 球墨铸铁的技术要求主要包括化学成分和物理性能两方面。
在化学成分方面,QT600 球墨铸铁的典型成分为:碳 (C)2.5-3.0%,硅(Si)2.3-2.7%,锰 (Mn)0.2-0.4%,硫 (S) 小于 0.02%,磷 (P) 小于0.08%,镁 (Mg) 小于 0.09%,铜 (Cu)0.35-0.40%。
在物理性能方面,QT600 球墨铸铁的抗拉强度需达到 600MPa 以上,硬度在 HRC38-45 之间。
三、QT600 球墨铸铁的铸造工艺QT600 球墨铸铁的铸造工艺主要包括以下几个步骤:1.熔炼:将球墨铸铁原材料(生铁、废钢等)加入熔炉中进行熔炼,调整成分,提高温度。
2.球化处理:在熔炼过程中,加入适量的球化剂(如镁、钙、稀土等),使铸铁中的石墨球化,提高铸铁的性能。
3.浇注:将熔炼好的球墨铸铁液倒入预先准备好的砂型或金属型中,进行浇注。
4.凝固:铸型中的球墨铸铁液在冷却过程中逐渐凝固,形成 QT600 球墨铸铁件。
5.清理:将凝固后的 QT600 球墨铸铁件从铸型中取出,进行清理、打磨,去除内外表面的砂粒、毛刺等。
四、QT600 球墨铸铁的应用领域QT600 球墨铸铁广泛应用于各种重型机械、汽车、铁路、船舶等工业领域,尤其适用于高负荷、高强度的工作环境。
例如,用于制造汽车发动机缸体、缸盖、轮毂等部件;船舶的螺旋桨、舵等部件;铁路车辆的车体、车轴等部件;以及各种工业设备的壳体、支架等部件。
基于anycasting的球墨铸铁汽车泵体铸造工艺优化
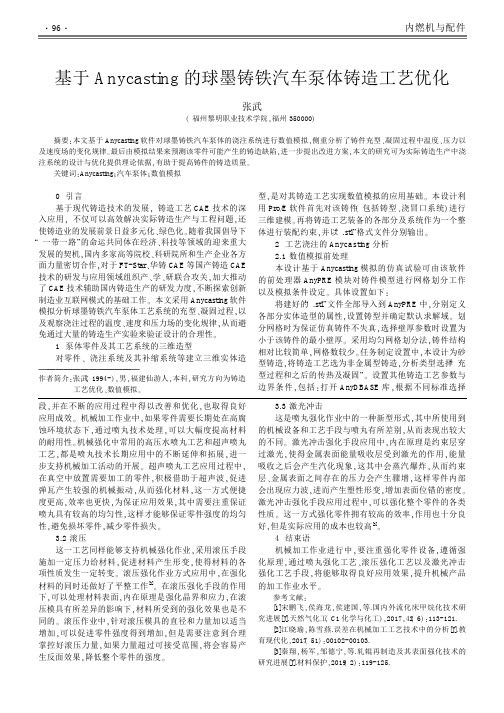
0引言基于现代铸造技术的发展,铸造工艺C A E 技术的深入应用,不仅可以高效解决实际铸造生产与工程问题,还使铸造业的发展前景日益多元化、绿色化。
随着我国倡导下“一带一路”的命运共同体在经济、科技等领域的迎来重大发展的契机,国内多家高等院校、科研院所和生产企业各方面力量密切合作,对于FT-St ar 、华铸C A E 等国产铸造C A E 技术的研发与应用领域组织产、学、研联合攻关,加大推动了C A E 技术辅助国内铸造生产的研发力度,不断探索创新制造业互联网模式的基础工作。
本文采用A nycast i ng 软件模拟分析球墨铸铁汽车泵体工艺系统的充型、凝固过程,以及观察浇注过程的温度、速度和压力场的变化规律,从而避免通过大量的铸造生产实验来验证设计的合理性。
1泵体零件及其工艺系统的三维造型对零件、浇注系统及其补缩系统等建立三维实体造型,是对其铸造工艺实现数值模拟的应用基础。
本设计利用Pr o/E 软件首先对该铸件(包括铸型、浇冒口系统)进行三维建模。
再将铸造工艺装备的各部分及系统作为一个整体进行装配约束,并以“.st l ”格式文件分别输出。
2工艺浇注的A nycast i ng 分析2.1数值模拟前处理本设计基于A nycast i ng 模拟的仿真试验可由该软件的前处理器A nyPR E 模块对铸件模型进行网格划分工作以及模拟条件设定。
具体设置如下:将建好的“.st l ”文件全部导入到A nyPR E 中,分别定义各部分实体造型的属性,设置铸型并确定默认求解域。
划分网格时为保证仿真铸件不失真,选择壁厚参数时设置为小于该铸件的最小壁厚。
采用均匀网格划分法,铸件结构相对比较简单,网格数较少。
任务制定设置中,本设计为砂型铸造,将铸造工艺选为非金属型铸造,分析类型选择“充型过程和之后的传热及凝固”。
设置其他铸造工艺参数与边界条件,包括:打开A nyD B A SE 库,根据不同标准选择———————————————————————作者简介:张武(1994-),男,福建仙游人,本科,研究方向为铸造工艺优化、数值模拟。
汽车用球墨铸铁件生产技术要点
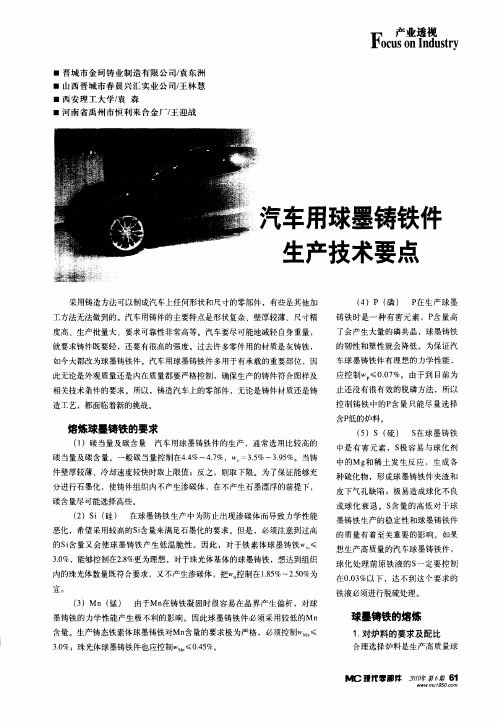
物 ,当然最好使用同种牌号的 回炉料 。
国钢 铁企业生产 的生铁 中都有干扰 球 化元素 ,只是 含量不 同而 已,主
要 的干扰元素是T 、Cr n b i 、S 、P 和 S 等。因此 ,选用含一定量稀土 元 b
炉料的配比是依生产球墨铸铁的牌号高低而定 ,通过准确计算炉料就可
以对碳当量和碳 、硅含量进行炉前控制 。球墨铸铁熔炼时比较 一致 的配料组
( )球 化处 理 工艺 2
球 化 处
倒包 ,这 样对原铁液 的出炉温度就 要有严格要 求 ,一般应该 控制在 17 ~ 40 10 5  ̄。铁液温 度过低 ,处理完浇注 的铸件很容易产生浇不足、冷 隔等铸造 0 缺陷 ;铁液温度太 高,球化 处理时Mg 的烧损严重 ,球化 不稳定 ,熔炼成本 也会增加 。另外 ,要求铁液在熔炼 中避 免过 度氧化 ,保证较低的含硫 ( ) S 量 ,必要时在炉 内加入 1 %左右的 电石粉等进 行脱硫 。还可以在球 化包内加 . 4 入苏打粉 ( 铁液量的0 %左右 )进 一步脱硫 ,虽然 该方法可能会 使铁液降 . 4
球墨铸铁的熔炼
1 对炉料的要求及配比 .
合理选择炉料是生产高质量球
含量。生产铸态铁素体球墨铸铁对Mn 含量的要求极为严格 ,必须控制w ≤
3 %;珠光体球墨铸铁件也 应控制 ≤04 %。 . 0 .5
l C 瑗 代 墨 邪1 4 :
眸 劳 婀 6 1
www. c 9 0c m m 1 5 o
3 %,能够控制在2 %更为理想 。对于珠光体基体的球 墨铸铁 ,想达到组织 . O . 8 内的珠光体数量既符合要求,又不产生渗碳 体,把W控制在1 5 2 0 为 . %~ , % 8 5
球墨铸铁生产工艺控制

球墨铸铁生产工艺控制球墨铸铁是一种使用球墨铸铁母合金进行球化处理后浇铸而成的铸铁材料。
球墨铸铁具有良好的机械性能、高强度和耐磨性能,被广泛应用于汽车、机械、建筑和航空等领域。
在球墨铸铁生产工艺中,控制各个环节的参数和条件对于保证产品质量至关重要。
本文将重点探讨球墨铸铁生产工艺的控制。
首先,球墨铸铁生产工艺的控制从材料选择开始。
球墨铸铁的母合金应具有合适的成分和适宜的球化剂含量。
合金成分的选择应根据所需的性能要求和使用环境进行调整。
球化剂含量的控制则直接影响到球化效果。
过高或过低的球化剂含量都会导致球墨铸铁的性能下降。
因此,在材料选择阶段就需要有明确的控制要求。
其次,在球墨铸铁的熔炼过程中需要控制炉温和熔化时间等参数。
炉温过高会造成糊花的生成,破坏球化效果;炉温过低则会导致球墨形态不完整。
熔化时间过长会导致合金因在高温下持续存在而发生发热和烧损现象,降低了合金的性能。
因此,在熔炼过程中需要精确控制炉温和熔化时间,以达到优化的球化效果和合金质量。
再次,铸造工艺对球墨铸铁的性能和质量也有重要影响。
铸造温度和冷却速度是需要控制的关键参数。
铸造温度低于需求范围会导致铸件凝固不完全,造成缩松和孔洞等缺陷;铸造温度过高则会加剧合金的河流现象,使得铸件组织松散。
冷却速度过大或过小也会对铸件的显微组织和性能产生负面影响。
因此,在铸造过程中需要通过调整冷却剂和冷却方式来控制铸造温度和冷却速度,以达到理想的铸件质量。
此外,球墨铸铁的热处理过程也需要进行精确控制。
球化处理、淬火和回火等工艺参数的控制都会直接影响到球墨铸铁的硬度、强度和韧性等性能。
通过控制加热温度、保温时间和冷却速度等参数,可以使球墨铸铁获得最佳的组织结构和性能。
综上所述,球墨铸铁生产工艺控制涉及到整个生产过程中的多个环节和参数。
只有精确控制每个环节和参数,才能确保球墨铸铁的优良性能和高质量。
因此,科学、严谨的生产工艺控制是球墨铸铁生产过程中必不可少的重要环节。
风电球墨铸铁行星架铸造工艺研究

风电球墨铸铁行星架铸造工艺研究一、引言风电球墨铸铁行星架是风力发电机组的重要组成部分,其质量和性能对于整个风力发电系统的运行稳定性和经济效益具有重要影响。
因此,研究其铸造工艺具有重要的意义。
二、球墨铸铁行星架的概述球墨铸铁行星架是指采用球墨铸铁材料制造的风力发电机组主轴支撑结构,其主要功能是承受转子和风轮负荷,并传递到塔筒上。
该部件通常由两个半轮组成,通过螺栓连接在一起。
三、球墨铸铁材料的特点球墨铸铁材料具有高强度、高韧性、耐疲劳、耐腐蚀等优点,适用于制造大型机械零件。
同时,球墨铸铁材料也存在着一些缺陷,如气孔、夹渣等。
四、球墨铸铁行星架的设计球墨铸铁行星架的设计需要考虑多种因素,包括载荷条件、结构尺寸、材料选择等。
其中,载荷条件是设计的核心,需要考虑风轮的质量、旋转速度、风向变化等因素。
五、球墨铸铁行星架的铸造工艺球墨铸铁行星架的铸造工艺是影响其质量和性能的关键因素。
常用的球墨铸铁行星架铸造工艺包括砂型铸造、气体硬化模型(HWS)铸造、失重法(投资法)铸造等。
1. 砂型铸造砂型铸造是球墨铸铁行星架最常用的一种生产工艺。
该工艺具有成本低、适用范围广等优点,但存在着砂芯制作难度大、表面粗糙度高等缺点。
2. HWS 铸造HWS 铸造是一种新兴的球墨铸铁行星架生产工艺,其主要特点是采用气体硬化模型代替传统砂模。
该工艺具有制品尺寸精度高、表面质量好等优点,但成本较高。
3. 失重法(投资法)铸造失重法(投资法)铸造也是一种常用的球墨铸铁行星架生产工艺。
该工艺具有制品表面光洁度高、尺寸精度高等优点,但成本较高。
六、球墨铸铁行星架的质量控制球墨铸铁行星架的质量控制是保证其性能和寿命的重要环节。
常用的质量控制方法包括化学成分分析、金相组织检测、硬度测试、超声波探伤等。
七、结论风电球墨铸铁行星架作为风力发电机组的重要组成部分,其质量和性能对于整个风力发电系统的运行稳定性和经济效益具有重要影响。
因此,研究其铸造工艺及质量控制方法具有重要意义。