ANSYS结构拓扑优化设计
拓扑优化简介及在ansys软件中的实现

件中的实现
ANSYS TRAINING
主要内容
1
2 3
拓扑优化概述 ANSYS中拓扑优化过程 实例讲解
ANSYS TRAINING
拓扑优化概述
ANSYS TRAINING
拓扑优化概述
工程结构优化
尺寸优化:以几何尺寸为设 计变量,而材料的性质,结构
的拓扑和几何形状保持不变
ANSYS TRAINING
实例讲解
实例二 力热载荷综合作用下的拓扑优化
3.3KN
换热系数 (Wm-2K)
在实例一中的模型上施加热边界条件如下:
位置 温度(K)
长×宽=160 ×120
1 2 3
1358.37 293 363
1092.36 105.3 13433
6.5MPa
ANSYS TRAINING
• GUI操作对应命令流的输出
– 单步查看 – 最终整体输出
Help is very helpful!
ANSYS TRAINING
实例讲解
实例一 力载荷下的拓扑优化
对一长正方形平板零件,底边中部受到均匀的压力6.5MPa,顶部两
侧受到集中载荷3.3KN。本问题的目标是在体积减少70%的条件下,
结构的柔顺度最小。 3.3KN
实例讲解
热-结构耦合分析
耦合方法
采用顺序耦合分析的方法,即首先进行整机温度场分析,然 后利用热分析结果即节点温度作为“体载荷”施加到随后的 结构分析中。
分析流程
温度场 边界条件 清除 物理环境 转换 单元 保存温度场 物理环境 转换 材料属性 温度场 计算 转换 接触算法 设置 参考温度 设置 边界条件
–PLNSOL,TOPO –or General Postproc > Plot Results > Nodal Solution… –红色表示要保留的材料 (pseudo-density 1.0); –蓝色表示可以去掉的材料 (pseudo-density 0.0)。
基于ANSYS的空间桁架结构拓扑优化设计

( 4) 在 得 到的 拓 扑优 化 结 果基 础 上, 利 用 APDL 命令提取和输出节点的坐标, 得出各节杆的 节距, 可以实现在满足一 定强度条件下杆的截 面 尺寸优化。
2 建模
AN SY S 拓扑 优化 功能 可以 用 于求 得 最 优结 构 , 以获得最大刚度、最小体积或最大 自振频率。拓 扑优化的原理是在满足结构体积减小量的条件 下 使结构的柔度极小化, 极 小化的结构柔度实际 就 是要求结构的刚度最大化, 优化过程是通过自 动 改变设计变量, 即单元伪密度 ( ) 来实现的。单 元伪密度 = 0的材料为可以删除的部分, 单元伪 密度 = 1的材料为保留的部分 [ 1, 2] 。
作 者: 魏文儒 地 址: 大连理工大学机械工程学院 邮 编: 116023
四连杆式带式制动器的结构与计算
中船重工集团第七 & 四研究所 姚化利 上海吴泾化工设计院 刘朝阳
带式制动器有多种结构形式, 本文介绍基本 式四连杆式带式制动器, 其结构原理源于普通 带 式制动器, 另外给出了具有代表 性的 2种动力 配 置结构形式: 螺杆动力式和两段螺 杆式。分析 了 其结构、功能特点和计算方法。
4 汪希萱, 曾胜 电磁式在线自动平衡系统及其动平衡方 法研究 热能动力工程, 2003, 18 ( 103): 53# 57
5 ISO 1925, Ba lanc ing - V ocabu lary, 1981
作 者: 程 峰 地 址: 山西太原中北大学机电工程学院航空宇航工程系 邮 编: 030051
如何采用ansys workbench对结构进行拓扑优化分析
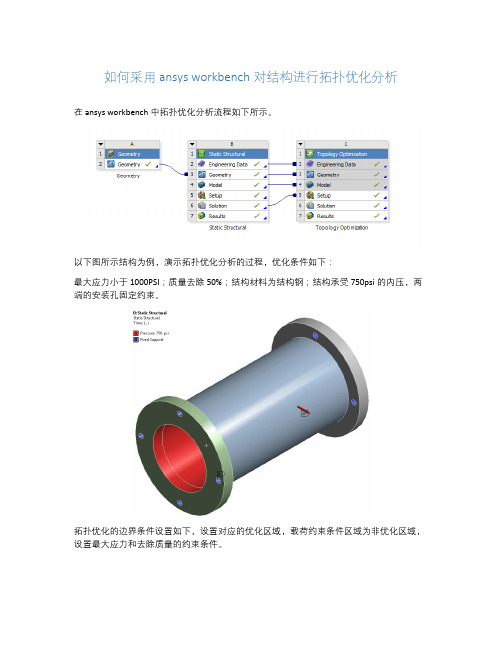
如何采用ansys workbench对结构进行拓扑优化分析
在ansys workbench中拓扑优化分析流程如下所示。
以下图所示结构为例,演示拓扑优化分析的过程,优化条件如下:
最大应力小于1000PSI;质量去除50%;结构材料为结构钢;结构承受750psi的内压,两端的安装孔固定约束。
拓扑优化的边界条件设置如下,设置对应的优化区域,载荷约束条件区域为非优化区域,设置最大应力和去除质量的约束条件。
优化前后的结果对比,优化后材料质量取出来42%
基于SCDM模块,对优化后的片面模型进行几何处理,并将模型一键转为为实体模型,进行优化后模型的验证分析。
验证分析的流程如下所示,通过workbench的一键传递,自动生成验证分析的静力学模块,按照上图所示的几何模型,完成几何处理,最后进行验证分析。
验证前后的结果对比如下所示,初始模型的变形为0.00032in,优化后模型的变形为
0.00061,初始模型的最大应力为8208psi,优化后模型的最大应力为9636psi,满足优化要求。
《Ansys拓扑优化》课件

REPORTING
• 拓扑优化概述 • ANSYS拓扑优化的基本原理 • ANSYS拓扑优化的操作流程 • 拓扑优化案例分析 • 结论与展望
目录
PART 01
拓扑优化概述
REPORTING
拓扑优化的定义
拓扑优化是在给定设计空间、载荷和约束条件下,通过求解数学优化问题,确定 最优的材料分布方案,以达到结构轻量化、刚度最大化或柔度最小化的目的。
PART 05
结论与展望
REPORTING
拓扑优化在工程设计中的重要性
01
02
03
提高结构效率
通过优化材料的分布,减 少不必要的材料,降低重 量并提高结构的刚度和稳 定性。
降低制造成本
减少材料使用意味着减少 生产成本和资源消耗,同 时优化设计可降低加工难 度。
创新设计
拓扑优化能够发现传统设 计方法无法达到的全新设 计方案,为工程师提供更 多创新选择。
熟悉ANSYS软件
深入了解ANSYS拓扑优化的基本原理、操作 流程和参数设置。
建立合理的模型
根据实际工程问题,建立准确的数学模型, 并选择合适的优化算法。
迭代与调整
在优化过程中,根据收敛情况和结果反馈, 不断调整优化参数和方法。
结果验证与评估
对优化后的设计方案进行实验验证,确保其 在实际应用中的可行性和可靠性。
迭代与收敛
在优化过程中,迭代计算并检查收敛性,直 至达到预设的收敛准则或迭代次数。
结果后处理和评估
评估与验证
根据优化结果,评估设计的可行性和有效性 ,如有需要可进行实验验证。
结果后处理
查看拓扑优化结果,如等效应力、应变分布 等。
设计优化建议
基于ANSYS和MATLAB数据接口的结构拓扑优化设计平台
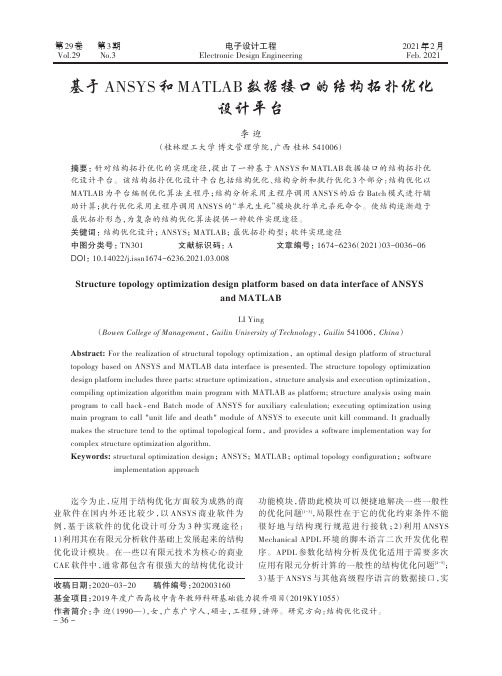
的各单元适应值进行大小排序。
④达到的效果:为下一步将排序在后的若干单
元进行遗传算子的操作提供了依据。
3)主程序读取 txt 文件适应值排序结果,调用自
定义函数完成选择、变异、杂交遗传算子的命令。
①技术原理:渐进遗传新型优化算法,将初始结
构有限元离散成的单元映射为遗传算法种群中的个
体,每个单元映射一个 n 位二进制串,用以代表单元
第 29 卷
Vol.29
第3期
No.3
电子设计工程
Electronic Design Engineering
2021 年 2 月
Feb. 2021
基于 ANSYS 和 MATLAB 数据接口的结构拓扑优化
设计平台
李迎
(桂林理工大学 博文管理学院,广西 桂林 541006)
摘要:针对结构拓扑优化的实现途径,提出了一种基于 ANSYS 和 MATLAB 数据接口的结构拓扑优
关键词:结构优化设计;ANSYS;MATLAB;最优拓扑构型;软件实现途径
中图分类号:TN301
文献标识码:A
文章编号:1674-6236(2021)03-0036-06
DOI:10.14022/j.issn1674-6236.2021.03.008
Structure topology optimization design platform based on data interface of ANSYS
化设计平台。该结构拓扑优化设计平台包括结构优化、结构分析和执行优化 3 个部分:结构优化以
MATLAB 为平台编制优化算法主程序;结构分析采用主程序调用 ANSYS 的后台 Batch 模式进行辅
助计算;执行优化采用主程序调用 ANSYS 的“单元生死”模块执行单元杀死命令。使结构逐渐趋于
ANSYS结构拓扑优化设计

三、客车车身有限元分析
车身骨架作为客车的关键总成,其结构必须有足够的强度和静刚度以保证其疲劳寿命、装配和使用的要求,同时还应有合理的动态特性以达到控制振动与噪声的目的。应用实践证明[5],用有限元法对车身结构进行分析,可在设计图纸变成产品前就对其刚度、强度、固有频率及振型等有充分认识,以了解车身的应力和变形情况,对不足之处及时改进,使产品在设计阶段就可保证满足使用要求,从而缩短设计试验周期,节省大量的试验和生产费用,它是提高产品可靠性既经济又适用的方法之一。
二、拓扑优化设计数学模型
2.1优化方法的选择
目前常用的连续体结构的拓扑优化方法有:变厚度法、变密度法及均匀化方法。变厚度法的数学模型简单,但优化对象受到很大的限制。变密度法是人为的建立一种材料密度与材料特性之间的关系,拓扑优化计算以后得到单元的密度值为0或1,拓扑优化结构比较清晰[2,3]。均匀化方法是最为流行的方法,拓扑优化后单元的密度值是介于0~1之间的连续值,得到的是一种比较模糊的拓扑结构。最优拓扑结构形式只考虑到结构的强度,结构的设计还需要满足制造工艺、装配关系等设计要求,人们需要在拓扑优化的基础上进行结构设计,模糊的拓扑结构提供的是一个取值范围,更利于后续设计。
ANSYS结构拓扑优化设计
潘震来源:e-works
关键字:客车车顶结构拓扑优化设计ansys
本文用ANSYS软件对某客车车身进行静态有限元分析。在此基础上,采用均匀化方法,以车架总柔度为目标函数,以体积作为约束条件,对几种工况下的车顶进行了拓扑优化设计。探讨了拓扑优化设计过程中,基本模型建立、优化区域选择、优化过程控制及优化结果分析与应用等问题。实现了拓扑优化在汽车结构的初始设计过程中的应用。
ANSYS拓扑优化设计理论
拓扑优化是指形状优化,有时也称为外型优化。
拓扑优化的目标是寻找承受单载荷或多载荷的物体的最佳材料分配方案。
这种方案在拓扑优化中表现为“最大刚度”设计。
与传统的优化设计不同的是,拓扑优化不需要给出参数和优化变量的定义。
目标函数、状态变量和设计变量(参见“优化设计”一章)都是预定义好的。
用户只需要给出结构的参数(材料特性、模型、载荷等)和要省去的材料百分比。
拓扑优化的目标——目标函数——是在满足结构的约束(V)情况下减少结构的变形能。
减小结构的变形能相当于提高结构的刚度。
这个技术通过使用设计变量(hi)给每个有限元的单元赋予内部伪密度来实现。
这些伪密度用PLNSOL,TOPO命令来绘出。
例如,给定V=60表示在给定载荷并满足最大刚度准则要求的情况下省去60%的材料。
图2-1表示满足约束和载荷要求的拓扑优化结果。
图2-1a表示载荷和边界条件,图2-2b表示以密度云图形式绘制的拓扑结果。
图2-1 体积减少60%的拓扑优化示例如何做拓扑优化拓扑优化包括如下主要步骤:1.定义拓扑优化问题。
2.选择单元类型。
3.指定要优化和不优化的区域。
4.定义和控制载荷工况。
5.定义和控制优化过程。
6.查看结果。
拓扑优化的细节在下面给出。
关于批处理方式和图形菜单方式不同的做法也同样提及。
定义拓扑优化问题定义拓扑优化问题同定义其他线性,弹性结构问题做法一样。
用户需要定义材料特性(杨氏模量和泊松比),选择合适的单元类型生成有限元模型,施加载荷和边界条件做单载荷步或多载荷步分析。
参见“ANSYS Analysis Procedures Guides”第一、二章。
选择单元类型拓扑优化功能可以使用二维平面单元,三维块单元和壳单元。
要使用这个功能,模型中只能有下列单元类型:二维实体单元:SOLID2和SOLID82三维实体单元:SOLID92和SOLID95壳单元:SHELL93二维单元用于平面应力问题。
指定要优化和不优化的区域只有单元类型号为1的单元才能做拓扑优化。
ansys结构参数优化和拓扑优化专题
响应面优化
Kriging (克里格法 ): 多项式F(x)与Z(X)的组合。Z(x)为对平均值为零,方差和非 零方差的正态分布高斯 由于克里格法通过所有设计点拟合响应面,因此拟合优度指 标总是好的 变量变化剧烈,或非线xing时,结果优于标准响应面拟合方 法
响应面优化
Kriging (克里格法 )修正设计点,会出现曲线振荡 可以通过在响应面上插入Refinement Point(改进点) 来修正响应面
拓扑优化
结构材料不同,设计方案不同,优化结果也不同 结构质量分布一致时,质量和体积的优化结果一样
拓扑优化
其余约束条件: 全局等效应力约束
对优化区域的zui da等效应力进行约束,可以对单个或所有工况
位移约束
对所选几何、节点的三个方向的zui da位移进行约束
局部等效应力约束
对所选的几何(面,线或体)、网格的zui da等效应力进行约束
Excel表格数据优化
添加Microsoft Office Excel模块,导入做好参数定 义的Excel表格,定义输入、输出参数
Excel表格数据优化
在Excel表格,输出参数可以定义为输入参数的函数表达式,添加DOE模块 在DOE中生成输入设计点,WB会根据Excel表格中定义的函数表达式求解出对应的输出参数
拓扑优化
挤出(extrusion): 类似于扫略
Without With
NLPQL (二次拉格朗日非线xing规划)
支持单目标,多约束,要求参数保持连续,适合于局部优化
MISQP(混合整数序列二次规划)
支持连续或离散的输入参数 只支持单目标,只生成一个最优解,适合局部优化
Excel表格数据优化
基于DX可以对Excel表格中的数据进行优化分析 在Excel中做好参数定义
ansys的几种优化方法_命令流
ansys的几种优化方法_命令流拓扑优化理论及在ANSYS软件中的实现拓扑优化理论及在ANSYS软件中的实现拓扑优化理论及在ANSYS软件中的实现一.拓扑优化概论:连续体结构的拓扑优化设计是继结构的尺寸优化设计和形状优化设计之后,在结构优化领域出现的一种富有挑战性的研究方向,它是一种比尺寸优化和形状优化更高层次的优化方法,也是结构优化问题中最为复杂的一类问题。
拓扑优化处于结构的概念设计阶段,其优化结果是一切后续设计的基础。
因而在初始设计阶段需要确定结构的最佳拓扑形式。
拓扑优化的目的是寻求结构的刚度在设计空间最佳的分布形式,或在设计域空间需求结构最佳的传力路线,以优化结构的某些性能或减轻结构的重量。
目前对于拓扑优化的研究主要集中在以下几个方面:结构拓扑描述方式和材料插值模型;拓扑优化中结构拓扑描述方式和材料的插值模型非常重要,是一切后续拓扑优化工作的基础。
常用的拓扑描述方式和材料插值模型有均匀化方法、密度法、变厚度法和拓扑函数描述法等。
拓扑优化求解数值算法,新型优化算法在拓扑优化中的应用;拓扑优化的数值计算方法主要包括有限元法和无网格法,基于成熟的有限元理论的拓扑优化格式简单,便于实现,但在优化过程中常因网格的重分和细化导致计算困难,结构中常出现中间密度材料、棋盘格现象和网格依赖性等问题。
无网格法是今年发展的一种新型数值求解技术,摆脱了有限元繁琐的网格生成过程,从理论上看比有限元法拥有更广阔的应用前景,但目前尚处于发展和完善中。
拓扑优化的特点是:设计变量多,计算规模大,目标函数和约束函数一般为设计变量的非线性、非单调函数。
目前应用于连续体结构拓扑优化计算的优化算法主要包括两类:优化准则法和序列凸规划法。
去除优化过程中数值计算不稳定的方法,优化结果的提取和重构;拓扑优化中经常出现的数值计算问题有:多孔材料、棋盘格现象、网格依赖性和局部极值问题。
优化结果的提取和应用主要考虑的是如何将优化的结果转化为可用的CAD模型问题,实现CAE和CAD之间的数据共享和交流。
ansys workbench拓扑优化实例
ansys workbench拓扑优化实例
拓扑优化(Topology Optimization)是一种结构优化的方法,通过在给定的设计空间内寻找最佳材料分布来实现结构的轻量化和性能优化。
在ANSYS Workbench 中,可以通过拓扑优化模块来进行这种优化分析。
以下是一个简单的ANSYS Workbench 拓扑优化实例的步骤:
1. 创建几何模型:首先,在ANSYS Workbench 中创建一个几何模型,可以是一个零件或者一个装配体。
2. 设定材料属性:为模型中的材料定义材料属性,包括弹性模量、泊松比等。
3. 设定加载和约束条件:定义模型的加载和约束条件,包括受力点、受力大小和方向,以及约束点和约束类型。
4. 添加拓扑优化模块:在Workbench 中选择拓扑优化模块,并将模型导入到拓扑优化模块中。
5. 设定优化目标和约束条件:定义优化的目标,比如最小化结构的重量或者最大化结构的刚度,同时设置一些约束条件,比如最大应力、最大变形等。
6. 设定优化参数:定义拓扑优化的参数,比如拓扑优化的迭代次数、网格分辨率等。
7. 运行优化分析:运行拓扑优化分析,软件会根据设定的优化目标和约束条件,在给定的设计空间内寻找最佳的材料分布。
8. 分析结果:分析优化结果,查看优化后的结构形态和性能指标,根据需要对设计进行进一步的调整和优化。
请注意,以上步骤是一个简化的示例,实际的拓扑优化分析可能涉及到更多的参数设定和分析步骤。
在实际应用中,建议根据具体的工程问题和软件版本进行详细的参数设定和分析。
- 1、下载文档前请自行甄别文档内容的完整性,平台不提供额外的编辑、内容补充、找答案等附加服务。
- 2、"仅部分预览"的文档,不可在线预览部分如存在完整性等问题,可反馈申请退款(可完整预览的文档不适用该条件!)。
- 3、如文档侵犯您的权益,请联系客服反馈,我们会尽快为您处理(人工客服工作时间:9:00-18:30)。
图4车顶载荷与边界条件处理
4.5定义和控制优化过程
拓扑优化过程包括四部分:定义优化函数,定义目标函数和约束条件,初始优化过程,以及执行拓扑优化。
4.5.1定义优化函数
ANSYS提供两种类型的拓扑优化,即以线性静力结构分析为基础的拓扑优化和以结构自振频率分析为基础的拓扑优化。本文所进行车身骨架顶棚结构的拓扑优化属于第一种类型,即以结构的柔顺度为拓扑优化函数。
在上述模型中,式(2)以结构的总柔顺性最小作为优化目标,以微结构的单胞尺寸a为优化设计变量;约束条件(3)根据虚功原理,以结构的静力平衡作为约束条件;约束条件(4)考虑到优化后的体积一定不大于初始体积,约束条件(5)假设了材料特性与密度的关系。
三、客车车身有限元分析
车身骨架作为客车的关键总成,其结构必须有足够的强度和静刚度以保证其疲劳寿命、装配和使用的要求,同时还应有合理的动态特性以达到控制振动与噪声的目的。应用实践证明[5],用有限元法对车身结构进行分析,可在设计图纸变成产品前就对其刚度、强度、固有频率及振型等有充分认识,以了解车身的应力和变形情况,对不足之处及时改进,使产品在设计阶段就可保证满足使用要求,从而缩短设计试验周期,节省大量的试验和生产费用,它是提高产品可靠性既经济又适用的方法之一。
v--节点的虚位移
εij(u)--由于节点位移u引起的应变
εkl(v)--由于节点虚位移v引起的虚应变
Eijkl(a)--假设的材料特性,与密度η及实际使用材料的材料特性E0有关
E0--实际使用材料的材料特性
α--待定系数
V--结构初始体积
Ω--表示在有体积力作用的体积域上积分
Г--表示在有面积力作用的边界域上进行积分
结构拓扑优化的基本思想是将寻求结构的最优拓扑问题转化为在给定的设计区域内寻求最优材料分布的问题。[1]通过拓扑优化分析,设计人员可以全面了解产品的结构和功能特征,可以有针对性地对总体结构和具体结构进行设计。特别在产品设计初期,仅凭经验和想象进行零部件的设计是不够的。只有在适当的约束条件下,充分利用拓扑优化技术进行分析,并结合丰富的设计经验,才能设计出满足最佳技术条件和工艺条件的产品。连续体结构拓扑优化的最大优点是能在不知道结构拓扑形状的前提下,根据已知边界条件和载荷条件确定出较合理的结构形式,它不涉及具体结构尺寸设计,但可以提出最佳设计方案。拓扑优化技术可以为设计人员提供全新的设计和最优的材料分布方案。拓扑优化基于概念设计的思想,作为结果的设计空间需要被反馈给设计人员并做出适当的修改。最优的设计往往比概念设计的方案结构更轻,而性能更佳。经过设计人员修改过的设计方案可以再经过形状和尺寸优化得到更好的方案。
4.2选择单元类型
通过对车身骨架及其顶棚结构以及受力特点分析,根据ANSYS对拓扑优化设计单元性质的设定来看,综合从计算机的计算容量、拓扑优化过程实际操作的方便性及优化结果的处理考虑,选用SHELL93 [6]单元来模拟车身骨架顶棚进行分析。
4.3基本结构
所谓基本结构就是优化前的初始结构。基本结构应该即符合受力、支撑等特点,又便于优化计算。由于ANSYS程序的缺省规定,只有将单元号指定为1的单元才能做拓扑优化,可以运用此规则来控制模型中的优化与不优化部分。[8]例如车顶纵梁扇形管的布置位置是固定不能改变的;还有一些横梁是其主要承载截面焊接成一体的,因此也不能改变;此外,还有两根纵梁是顶棚的主要承载部件,不能参与优化。这些梁可以将其单元号指定为2或更大单元号,而需要通过拓扑优化计算来确定布置形式的区域就可以通过将其单元号指定为1来实现。为忠实于实际结构和功能,还应把一些实常数赋给单元,车身骨架所使用的材料均为各向同性材料16Mn,材料尺寸采用毫米,其它均采用Kg-mm-s单位制,见表2。建立的拓扑优化模型如图3所示,其中灰色为优化区域,黑色为不优化区域。
四、车顶拓扑优化
拓扑优化是指形状优化,也称为外形优化。拓扑优化的目的是寻找承受单载荷或多载荷的物体的最佳的材料分配方案。这种优化在拓扑优化中表现为"最大刚度"设计。与传统优化设计不同的是,拓扑优化不需要给出参数和优化变量的定义。目标函数、状态变量和设计变量都是预定义好的,用户只需给出结构的参数(材料特性、模型、载荷等)和要省去的材料百分比。[6]拓扑优化的目标函数是在满足结构约束的情况下减少结构的变形能,减少结构的变形能相当于提高结构的刚度。这个技术通过使用设计变量给每个有限元单元的伪密度得以实现。
4.5.4执行优化迭代
执行拓扑优化时,可以用两种方式进行:控制并执行每一次迭代,或自动进行多次迭代。
在本次优化计算中首先根据车身骨架的工况,将单工况下结构柔顺度定义为拓扑优化函数,函数参考名为F;将函数F指定为本次优化计算的目标函数,结构的名义总体积VOLUME指定为约束函数,经过多轮的优化计算结果的比较,选定将体积的去除量设定为75%;由于在第二步中将函数F定义为拓扑优化目标函数,函数VOLUME定义为约束条件时,按照ANSYS软件的原则要求,选用OC优化计算方法,优化迭代的收敛公差设定为0.0001(缺省值),优化迭代默认最大循环次数为30次。
4.5.2定义目标函数和约束条件
在优化前必须先定义拓扑优化的目标函数,再定义约束条件。ANSYS为用户缺省定义了一个拓扑函数"VOLUME"(表示总体积函数),这样加上我们自定义的函数F,就得到两个拓扑函数。
4.5.3优化过程初始化
在定义了优化问题之后,必须在拓扑优化之前对问题进行求解,否则可能在进行第一次优化迭代时出现错误信息。在明确优化问题和定义了拓扑优化函数之后,需要为优化计算过程选择合适的求解方法。ANSYS为用户提供了两种优化算法,即选择优化判据法(OC)或序贯凸函数寻优法(SCP)。选择方法的原则是:以体积作为约束问题的选择OC方法;SCP方法用于所有合法的目标函数和约束条件的组合。
2.2均匀化方法的数学模型
均匀化方法的基本思想是在组成拓扑结构的材料中引入微结构-单胞(图1),优化过程中以微结构的单胞尺寸为拓扑设计变量,建立材料密度与材料特性之间的关系,以单胞尺寸的消长实现微结构的增删,并产生由中间尺寸单胞构成的复合材料,以拓展设计空间,从而实现了结构拓扑优化模型与尺寸优化模型,具有严格的数学基础,是一种很好的方法。[4]
图1.微结构的单胞(单位细胞)
微结构单胞的密度为 (1)
均匀化方法的数
(4)
(5)
(6)
(7)
gs8(8)
式中:
η--微结构单胞的密度
l(u)--结构柔顺度
l(v)--结构所受到的等效体积力和边界载荷在虚位移v上所作的虚功
p、t--结构所受到的等效体积力和边界载荷
u--节点位移
3.2车身结构静态有限元载荷工况分析
客车运行时车身承受的载荷很多,就其载荷性质而言,车身所受到的主要载荷为弯曲、扭转、侧向载荷和纵向载荷等几种。其中弯曲载荷主要产生于车身、车载设备、乘客和行李等的质量;扭转载荷产生于路面不平度对车身造成的非对称支承,作为对比计算,可以用静态最大可能的扭矩,即模拟一个前轮悬空的极限状态;侧向载荷主要产生于转向时的离心作用;纵向载荷产生于加速、制动时的惯性力作用。为了能比较全面地了解车身骨架在实际工况下的应力分布情况,对水平弯曲工况(空载+满载)、极限扭转工况(左、右前轮悬空)、紧急转弯工况(左、右转弯)、紧急制动工况(满载)进行了有限元仿真计算来分析车身结构强度和刚度,为进一步进行优化设计提供参考依据。[6]
表1材料及其特性参数
4.4定义和控制载荷工况
由于拓扑优化没有考虑到蒙皮,为此需要将蒙皮转化为面载荷加在所有面上,此外车顶空调载荷处理成集中力施加在响应部位。顶棚作为全承载车身的一部分,其受力情况受车身结构工况影响很大,为此考虑五个载荷工况的情况,将车身静态分析各工况下的顶棚与侧围焊接点的位移作为初始约束加载各焊接点,进行拓扑优化求解,最终得到的载荷分布如图4所示。
ANSYS结构拓扑优化设计
潘震来源:e-works
关键字:客车车顶结构拓扑优化设计ansys
本文用ANSYS软件对某客车车身进行静态有限元分析。在此基础上,采用均匀化方法,以车架总柔度为目标函数,以体积作为约束条件,对几种工况下的车顶进行了拓扑优化设计。探讨了拓扑优化设计过程中,基本模型建立、优化区域选择、优化过程控制及优化结果分析与应用等问题。实现了拓扑优化在汽车结构的初始设计过程中的应用。
二、拓扑优化设计数学模型
2.1优化方法的选择
目前常用的连续体结构的拓扑优化方法有:变厚度法、变密度法及均匀化方法。变厚度法的数学模型简单,但优化对象受到很大的限制。变密度法是人为的建立一种材料密度与材料特性之间的关系,拓扑优化计算以后得到单元的密度值为0或1,拓扑优化结构比较清晰[2,3]。均匀化方法是最为流行的方法,拓扑优化后单元的密度值是介于0~1之间的连续值,得到的是一种比较模糊的拓扑结构。最优拓扑结构形式只考虑到结构的强度,结构的设计还需要满足制造工艺、装配关系等设计要求,人们需要在拓扑优化的基础上进行结构设计,模糊的拓扑结构提供的是一个取值范围,更利于后续设计。
对密度云图进行数字图像处理完全脱离图像上颜色所代表的实际意义,即不考虑密度值的问题,完全是针对图像进行处理。其原理是,先读出图像的各像素点的RGB值,然后通过一些数字图像处理函数对各像素点的颜色信息进行灰度处理、点运算、图像均衡、图像增强等一系列的处理,得到条例需要的结果图。
3.1有限元模型的生成
几何模型是有限元模型的基础。本文使用Unigraphics软件系统,根据车身骨架结构的AutoCAD二维设计图纸,建立其三维空间几何模型,用自行编制的接口程序将模型导入ANSYS。导入后的几何模型,还需要做一些必要的修改才能划分网格。为了对建成的有限元模型进行检查,将该模型在悬架装配部位的节点约束后,分别给三个坐标轴方向以一定加速度,检查梁之间的连接情况,并进行修改。最终建立的有限元模型如图2所示。模型的规模信息:关键点1288个、直线2150条、图2车身骨架有限元模型节点31216个、单元16044个。此模型车身骨架质量为4388.5kg,车载质量为5911.6kg,前轴承载3721.8kg,后轴承载6578.3kg。[6]