关于硅烷法制备多晶硅工艺研究
国内硅烷法制备电子级区熔用多晶硅的进展分析

国内硅烷法制备电子级区熔用多晶硅的进展分析半导体材料中用量最大和用途最广的是半导体硅,半导体级多晶硅广泛应用于微电子、晶体管及集成电路、半导体器件等半导体工业中。
电子级多晶硅是半导体器件、集成电路、大功率电力电子器件的基础性材料。
电子级多晶硅作为半导体行业、信息行业发展的基础,必将成为全球第三次工业革命的焦点。
据统计,2013年全球电子级多晶硅产量将近2万t,中国国内的需求量约为3 000 t .在单晶硅的拉制工艺上,目前中国直拉工艺比较成熟,但是大部分原料仍然依赖进口。
由于区熔单晶硅生长技术门槛高,全球区熔单晶硅制造商比直拉单晶硅制造商数量少很多,全球有5家公司垄断了全部产量的95.5%以上。
中国生产区熔单晶硅的多晶硅原料主要依赖进口,瓦克是国内主要的进口厂商。
中国的电子级多晶硅生产技术、产品品质函待提高。
因此,研究制备高纯、超高纯的多晶硅,即电子级、区熔级多晶硅的技术对中国半导体产业的发展极为重要。
1电子级多晶硅生产工艺概述当前主流的电子级多晶硅生产技术主要有三氯氢硅法、硅烷法等。
流化床反应器法所生产的多晶硅为颗粒状,纯度也不及三氯氢硅法和硅烷法生产的纯度,主要应用于太阳能产业,也可作为拉制大直径单晶硅时的原料,连续加料,但不能直接提供区熔使用。
三氯氢硅法生产电子级多晶硅具有一定的优势,其沉积速率较快,可达8-10m/min,安全性相对较好,多晶硅纯度可以满足直拉和区熔的要求叫。
但是中国国内三氯氢硅法生产的大部分多晶硅产品为太阳能级,即使电子级产品,无论是质量上还是产量上都与国外的先进技术有一定差距,面区熔级的多晶硅产品更为少见。
硅烷法是利用硅烷热分解的方法制备多晶硅,反应温度低,原料气体硅烷易提纯,杂质含量可以得到严格控制。
硅烷法所生产的多晶棒结晶致密,结晶粒径也远小于三氯氢硅工艺,被用于区熔法生产硅单晶可一次成晶,是生产区熔单晶硅的最佳原料。
另外,硅烷及热分解产物都没有腐蚀性,从面避免了对设备的腐蚀以及硅受腐蚀面被沾污的现象,具有广阔的发展前景。
关于硅烷法制备多晶硅工艺研究

关于硅烷法制备多晶硅工艺研究硅烷法是一种常用的制备多晶硅的工艺方法,也被称为化学气相沉积法。
它是一种将硅材料从气相转化为固相的化学反应过程,通过控制温度、压力和反应气氛等参数,可以制备高纯度、大尺寸、低杂质的多晶硅材料。
硅烷法制备多晶硅的工艺流程包括硅烷气相制备、反应槽气氛控制、沉积反应和多晶硅生长等步骤。
首先是硅烷气相制备。
硅烷是一种有机硅化合物,由硅和氢原子组成。
制备硅烷的方法有很多种,常用的有热分解法、三硅烷氧化法等。
硅烷气相制备的关键是要保证产生高纯度的硅烷气体,避免杂质的影响。
接下来是反应槽气氛控制。
反应槽是硅烷法制备多晶硅的关键设备,其气氛控制对产品质量起着重要作用。
通常采用惰性气体(如氩气)和氢气混合的气氛,控制反应槽内的气氛成分和流速,以调控反应过程中的温度和压力。
然后是沉积反应。
在控制好反应槽内气氛后,将硅烷气体输送到反应槽中,与基片表面发生化学反应,使硅烷气体分解,产生游离的硅原子沉积在基片上,形成硅层。
反应条件的选择对硅层的沉积速率、均匀性和晶体结构有着重要的影响。
最后是多晶硅的生长。
沉积的硅层并非是完全结晶的,需进行后续的热处理或控制晶体生长条件,使其逐渐形成多晶结构。
常用的方法有热退火、区域熔融和液相外延等。
这些方法能够消除硅层中的晶粒界面,促进晶体生长,提高多晶硅的结晶质量。
硅烷法制备多晶硅具有优点明显,例如制备过程可扩展性强、成本相对较低、能够制备大尺寸的硅片等。
然而,也面临一些挑战,例如反应槽的设计和优化、硅烷气氛的控制、多晶硅层的均匀性和控制等。
因此,需要进一步的研究和探索,以提高多晶硅的质量和降低制备成本。
总之,硅烷法是制备多晶硅的重要方法之一,通过合理控制制备工艺和条件,可以得到高质量的多晶硅材料。
未来随着技术的不断发展,硅烷法在半导体材料制备领域将会发挥更大的作用。
多晶硅的生产工艺及研究
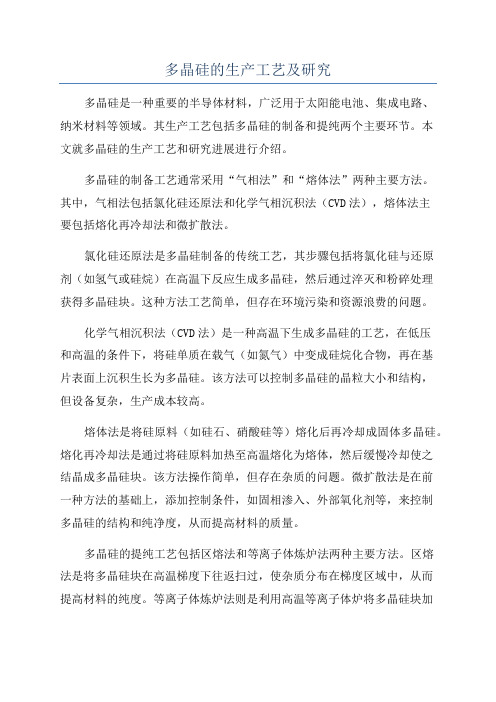
多晶硅的生产工艺及研究多晶硅是一种重要的半导体材料,广泛用于太阳能电池、集成电路、纳米材料等领域。
其生产工艺包括多晶硅的制备和提纯两个主要环节。
本文就多晶硅的生产工艺和研究进展进行介绍。
多晶硅的制备工艺通常采用“气相法”和“熔体法”两种主要方法。
其中,气相法包括氯化硅还原法和化学气相沉积法(CVD法),熔体法主要包括熔化再冷却法和微扩散法。
氯化硅还原法是多晶硅制备的传统工艺,其步骤包括将氯化硅与还原剂(如氢气或硅烷)在高温下反应生成多晶硅,然后通过淬灭和粉碎处理获得多晶硅块。
这种方法工艺简单,但存在环境污染和资源浪费的问题。
化学气相沉积法(CVD法)是一种高温下生成多晶硅的工艺,在低压和高温的条件下,将硅单质在载气(如氮气)中变成硅烷化合物,再在基片表面上沉积生长为多晶硅。
该方法可以控制多晶硅的晶粒大小和结构,但设备复杂,生产成本较高。
熔体法是将硅原料(如硅石、硝酸硅等)熔化后再冷却成固体多晶硅。
熔化再冷却法是通过将硅原料加热至高温熔化为熔体,然后缓慢冷却使之结晶成多晶硅块。
该方法操作简单,但存在杂质的问题。
微扩散法是在前一种方法的基础上,添加控制条件,如固相渗入、外部氧化剂等,来控制多晶硅的结构和纯净度,从而提高材料的质量。
多晶硅的提纯工艺包括区熔法和等离子体炼炉法两种主要方法。
区熔法是将多晶硅块在高温梯度下往返扫过,使杂质分布在梯度区域中,从而提高材料的纯度。
等离子体炼炉法则是利用高温等离子体炉将多晶硅块加热至高温,利用等离子体液体交互作用力使杂质从多晶硅中析出,从而提高材料的纯度。
多晶硅的研究主要集中在杂质控制、晶粒控制和能效提高等方面。
杂质控制是多晶硅研究的重点之一,因为杂质对多晶硅电子性能的影响十分显著。
目前的研究主要集中在减少杂质含量、改善杂质分布和控制杂质降解等方面。
晶粒控制是另一个重要的研究方向,因为晶粒尺寸对多晶硅的导电性能和光学性能有着重要的影响。
研究目标主要是通过改变制备工艺和添加控制条件来控制晶粒尺寸。
硅烷流化床法制备颗粒多晶硅

流化床颗粒多晶硅技术介绍Steve Chu, Ph.D.Sunnyside Technologies, Inc2010 Hennepin Ave E, Minneapolis, MN 55114steve.chu@多晶硅生产关键技术多晶硅生产实际上都分成两大步,第一步是将工业硅(纯度为98-99%)进行气化,经多级提纯得到气体如三氯氢硅(SiHCl3)、二氯二氢硅、或硅烷(SiH4)。
第二步,将上述高纯气体还原成高纯硅(多晶硅)。
图1多晶硅还原技术路线还原过程是多晶硅生产中的核心步骤,直接影响多晶硅的质量与成本,也反映了一个国家在此领域的综合技术水平。
目前国际上多晶硅生产主要工艺有:1.利用钟罩式还原炉制成棒状多晶硅,即改良西门子工艺,生产的多晶硅约占世界总产能的85%以上。
2.利用流化床反应器制成颗粒状多晶硅,流化床还原技术以其节能高效等优势已占越来越多的份额。
棒状多晶硅还不是最终产品,需要破碎成块状供单晶硅生产商使用。
而粒状多晶硅由于可以实现连续投料,单晶硅的成本得到降低,因此粒状多晶硅是单晶硅制造商的最终选择。
3.由于现行大多制气和还原工艺产生大量四氯氢硅,而四氯氢硅必须经过氢化反应生成三氯氢硅之后才能更为有效的利用。
目前多晶硅生产厂商特别是中国国内厂商面临大量四氯氢硅库存,有待氢化的问题,因而高效低成本四氯氢硅氢化也是重要技术壁垒之一。
西门子方法生产多晶硅的一个主要问题就是投资大能耗高,每生产一公斤多晶硅需耗电几十到两百度,与之相比,流化床还原生产颗粒多晶硅具有转换效率高、耗电少等特点。
另外,颗粒多晶硅也是电子与太阳能产业中新的应用所必需的原料,如在拉制大直径单晶硅时连续加料以及生产太阳能电池所用硅薄带和连续铸锭都需用颗粒多晶硅。
发明西门子法的西门子公司甚至还将自己工艺生产的棒状硅熔化成滴生成颗粒硅(美国专利: 4,532,090),可见很早人们就意识到颗粒硅的重要性。
氢化技术目前有两类, 即热氢化和冷氢化。
硅烷法多晶硅生产工艺

硅烷法多晶硅生产工艺硅烷法多晶硅生产工艺,这个听上去是不是有点复杂?其实它就像是做一道大菜,虽然步骤多,但只要掌握了诀窍,就能轻松搞定。
大家都知道,硅是我们日常生活中不可或缺的元素,尤其在电子和太阳能行业,简直是个明星。
说到硅,硅烷就是它的好朋友,硅烷可不是什么新鲜玩意儿,简单来说,它就是硅的化合物,气体状态的那种,哎呀,听上去是不是有点儿科幻?但其实它在我们的生活中可用得上,甚至能帮我们制造出高纯度的多晶硅,咱们可要好好聊聊这个。
准备工作是关键。
想象一下,厨师在下厨之前,得把食材准备好。
硅烷法就是把硅烷气体送入一个大箱子,咱们把它叫做反应器。
这个反应器就像是个巨大的烤箱,里面得保持合适的温度和压力。
硅烷在高温下就会分解,硅的颗粒会慢慢沉淀在反应器的底部,形成多晶硅。
就像是做糖一样,慢慢加热,糖分融化后就能凝结成一块块的糖。
反应过程中,得控制温度。
太高了,硅烷可能会跑掉;太低了,反应又不彻底。
这个过程得监控得死死的,咱们可是不能让这小家伙溜走。
想象一下,调温就像调节火候,火候掌握得好,出来的菜才会好吃。
这样,经过一段时间的反应,沉淀下来的硅就变成了一块块闪闪发光的晶体,想想都让人开心。
说到这里,有趣的是,硅烷法的经济性也很高。
很多人可能会想,生产多晶硅那么复杂,成本一定不低吧?其实不然,硅烷的来源可广泛得很,价格也相对实惠。
它的纯度高,后续加工也比较简单。
这就像是用高质量的食材做出好菜,省下来的钱可真不少,没准还能省出点儿零花钱呢。
不过,生产多晶硅可不仅仅是反应这么简单。
大家都知道,任何事情都有两面性,这个过程也不是没风险。
硅烷虽然听上去温和,但它是一种易燃气体,稍不注意就可能引发火灾。
这就像咱们在厨房炒菜,油烟太多,火苗一不小心就上来了。
所以,安全措施一定要到位,得装上监控设备,随时监测气体浓度,确保整个过程平稳进行。
再说了,反应结束后,咱们还得对这些多晶硅进行清洗和处理。
这一步可不能省,毕竟,谁都不想吃到脏东西,对吧?所以,把沉淀下来的硅清洗干净,再经过一系列加工,才能真正变成高纯度的多晶硅,送到电子产品或者太阳能电池的生产线上。
硅烷法制备多晶硅分析报告

硅烷法制备多晶硅分析报告四川永祥股份有限公司新材料项目组易正义张兵周炯文旭明王凤丽目录第一章项目背景 (1)1.1 多晶硅行业背景 (1)1.2 颗粒料多晶硅行业产销状况 (1)1.3 电子级多晶硅的行业产销状况 (2)1.3.1 半导体多晶硅的市场需求 (2)1.3.2 高端电子级多晶硅的市场需求 (2)第二章制备电子级多晶硅工艺技术 (3)2.1 制备高纯硅烷工艺 (3)2.1.1 固定床工艺 (3)2.1.2单步反应精馏法制备硅烷工艺 (4)2.2 硅烷制备电子级多晶硅工艺--气相沉积法 (4)第三章电子级多晶硅生产厂家 (4)3.1 厂家采用的工艺及产品等级 (4)3.2 技术提供厂商工艺包 (5)第四章,投资估算 (5)4.1 CVD炉生产区熔料、流化床建设成本及经济效益分析表.. 54.2 附录 (6)硅烷法制备多晶硅分析报告第一章项目背景1.1 多晶硅行业背景近年来,多晶硅行业历经2009-2012年的低谷后,产能过剩、国内市场开发不足等种种矛盾和困境,为我国光伏产业的健康发展布下了阴霾。
2013年,伴随着中欧贸易争端的解决和国内一系列利好政策的出台,我国光伏产业迎来了新一轮发展的曙光。
但国内技术水平仍无法满足产业发展需求,企业生产成本倒挂,行业进入微利时代。
欧美多晶硅企业,在政府政策扶持及高价长单捆绑中国下游客户的背景下,大幅低价倾销中国市场,给刚刚兴起的中国多晶硅产业致命的打击,使我国多晶硅行业艰难前行。
严酷的市场洗礼淘汰了大部分无规模效应的企业,目前我国80%多晶硅企业停产超过一年,能够提供有效产能的企业数量约3—8家,产能不足3万吨。
其中:2012年中国产能利用率仅三分之一;2013年一季度全国产量不足1万吨,产能利用率不足25%。
内忧外患导致我国多晶硅的产业安全度降低,多晶硅企业步履艰辛。
目前,国际上多晶硅产品等级主要分为两类:太阳能级和电子级。
太阳能级主要应用于光伏行业及太阳能电池;电子级广泛应用到集成电路、半导体、高性能动力装备及绿色能源领域。
创新型改良深低温硅烷法生产技术开发多晶硅高新产品项目可行性研究报告

创新型改良深低温硅烷法生产技术开发多晶硅高新产品项目可行性研究报告一、前言深低温硅烷法是生产多晶硅高新产品的先进工艺,其生产效率高,品质稳定,被广泛应用于光电子、太阳能、半导体等领域。
本文通过可行性研究报告,探究了开发多晶硅高新产品项目的可行性,并提出了改良深低温硅烷法生产技术的创新型措施。
二、市场调研本项目的主要市场是太阳能、半导体领域,由于近年来环保意识提高,太阳能产品市场不断扩大,同时半导体行业也需大量需要多晶硅高新产品,市场需求量十分庞大。
与此同时,国家对清洁能源的政策倾斜也为本项目带来了更多的机会。
三、技术可行性分析目前,深低温硅烷法已经被广泛应用于多晶硅高新产品的生产,石墨炉、氯化法也相继出现并应用于相关产业。
但是,本项目还需要在改善深低温硅烷法的生产质量和效率等方面作出创新,具体措施如下:1.优化前驱体制备过程:采用湿法氧化工艺制备硅粉,大大降低了后续工序中的杂质含量,提高了产品的质量和纯度。
2.手性富勒烯助剂的引入:通过手性富勒烯助剂的引入,实现了对多晶硅晶体生长方向的控制,提高了晶体质量。
3.多晶硅晶体生长中加入金属催化剂:通过金属催化剂的加入,可以促进多晶硅晶体生长速度的提高,达到快速生长的效果。
以上改良措施在实际生产中不仅可以提高生产质量和效率,同时还可以降低原材料和能源消耗等成本。
四、财务可行性分析本项目的生产周期为两年,预计生产多晶硅高新产品100吨,单价为30万元/吨,总收入为3000万元。
同时,预估占地3000平方米,投资成本为5000万元,预计两年内累计支出4000万元,期初净现值为500万元,总资产收益率达到10%以上。
五、风险分析本项目的生产周期较长,市场竞争也十分激烈,在申请相关执照和证书时需要满足严格的要求,而且原材料、人力成本和管理等风险也必须得到有效控制。
六、结论在多晶硅高新产品项目可行性研究报告中,我们探究了开发多晶硅高新产品项目的可行性,并提出了改良深低温硅烷法生产技术的创新型措施。
硅烷法多晶硅生产技术详解
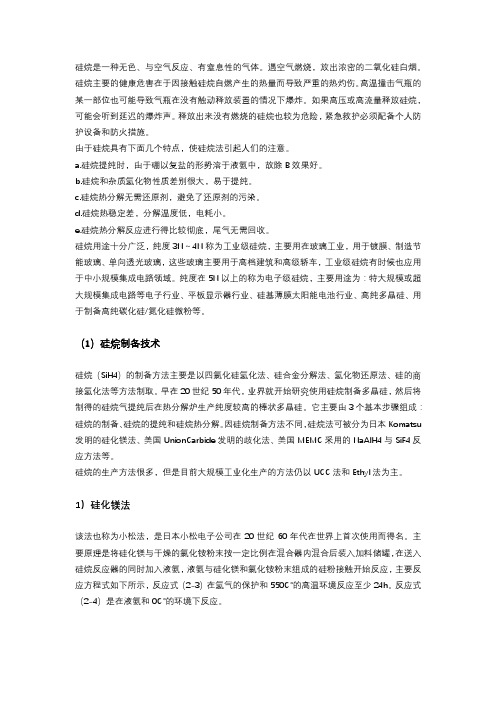
硅烷是一种无色、与空气反应、有窒息性的气体。
遇空气燃烧,放出浓密的二氧化硅白烟。
硅烷主要的健康危害在于因接触硅烷自燃产生的热量而导致严重的热灼伤。
高温撞击气瓶的某一部位也可能导致气瓶在没有触动释放装置的情况下爆炸。
如果高压或高流量释放硅烷,可能会听到延迟的爆炸声。
释放出来没有燃烧的硅烷也较为危险,紧急救护必须配备个人防护设备和防火措施。
由于硅烷具有下面几个特点,使硅烷法引起人们的注意。
a.硅烷提纯时,由于硼以复盐的形势溶于液氨中,故除B效果好。
b.硅烷和杂质氢化物性质差别很大,易于提纯。
c.硅烷热分解无需还原剂,避免了还原剂的污染。
d.硅烷热稳定差,分解温度低,电耗小。
e.硅烷热分解反应进行得比较彻底,尾气无需回收。
硅烷用途十分广泛,纯度3N~4N称为工业级硅烷,主要用在玻璃工业,用于镀膜、制造节能玻璃、单向透光玻璃,这些玻璃主要用于高档建筑和高级轿车,工业级硅烷有时候也应用于中小规模集成电路领域。
纯度在5N以上的称为电子级硅烷,主要用途为:特大规模或超大规模集成电路等电子行业、平板显示器行业、硅基薄膜太阳能电池行业、高纯多晶硅、用于制备高纯碳化硅/氮化硅微粉等。
(1)硅烷制备技术硅烷(SiH4)的制备方法主要是以四氯化硅氢化法、硅合金分解法、氢化物还原法、硅的商接氢化法等方法制取。
早在20世纪50年代,业界就开始研究使用硅烷制备多晶硅,然后将制得的硅烷气提纯后在热分解炉生产纯度较高的棒状多晶硅。
它主要由3个基本步骤组成:硅烷的制备、硅烷的提纯和硅烷热分解。
因硅烷制备方法不同,硅烷法可被分为日本Komatsu 发明的硅化镁法、美国UnionCarbide发明的歧化法、美国MEMC采用的NaAlH4与SiF4反应方法等。
硅烷的生产方法很多,但是目前大规模工业化生产的方法仍以UCC法和Ethyl法为主。
1)硅化镁法该法也称为小松法,是日本小松电子公司在20世纪60年代在世界上首次使用而得名。
主要原理是将硅化镁与干燥的氯化铵粉末按一定比例在混合器内混合后装入加料储罐,在送入硅烷反应器的同时加入液氨,液氨与硅化镁和氯化铵粉末组成的硅粉接触开始反应,主要反应方程式如下所示,反应式(2-3)在氢气的保护和550℃的高温环境反应至少24h。
- 1、下载文档前请自行甄别文档内容的完整性,平台不提供额外的编辑、内容补充、找答案等附加服务。
- 2、"仅部分预览"的文档,不可在线预览部分如存在完整性等问题,可反馈申请退款(可完整预览的文档不适用该条件!)。
- 3、如文档侵犯您的权益,请联系客服反馈,我们会尽快为您处理(人工客服工作时间:9:00-18:30)。
关于硅烷法制备多晶硅工艺研究
作者:桑艳青
来源:《中国化工贸易·中旬刊》2019年第06期
摘要:太阳能是一种可以再生的清洁能源值得人们重视,开发太阳能的资源成为大趋势,太阳能的发电技术认为是目前世界上发展前景较广阔的新能源的新技术。
所以,作为太阳能的发电技术的核心,光伏产业也得到迅猛发展。
现在限制太阳能的发电技术不能快速的发展主要的原因是制作太阳能的发电设备材料--多晶硅生产的成本高,大约占到太阳能的发电成本的50%。
电子级别的多晶硅是半导体型器件,大功率的电力和电子器件,集成电路等的基础材料。
电子多晶硅是半导体业和信息业进行发展不可缺少的基础,定将变为全球性的第三次的工业革命焦点性产品。
中国电子多晶硅的生产技术其产品的品质有待提高,所以制做高纯和超高纯多晶硅的研究也就是电子区熔多晶硅技术对全国半导体的产业发展越来越重要。
关键词:硅烷法;多晶硅;制备;生产工艺
1 多晶硅的工艺概述
现有多晶硅的生产工艺,其技术主要包含:改良的西门子法,硅烷法,流化床法,氯硅烷还原法(其中包括Zn还原法、Na还原法、等离子的氢还原),重掺硅的废料制备的方法,冶金硅的精炼法(其中包括火法精炼、湿法精炼及定向凝固),还有其他的方法。
改良的西门子法一般是指在西门子法基础上发展得到的,用氯气与氢气来合成HC1,然后HC1與工业的硅粉在250到350摄氏度下合成SiHC13,再对SiHC13采取分离、精馏和提纯的操作,提纯后,SiHC13在氢的还原炉中进行反应,用化学气相沉积法得到高纯度的多晶硅。
硅烷法使硅烷进行热分解制备得到多晶硅。
反应的温度低,原料是气体硅烷容易提纯,杂质的含量可得到较好的控制。
硅烷法所制备的多晶硅棒,结晶的形状非常致密,结晶的粒径比三氯氢硅的工艺制备的小的多。
氯硅烷的还原法和冶金法等等新的工艺是光伏的产业迅速发展所形成的多晶硅的生产工艺,许多工艺条件还尚处于研究的阶段,投放市场还需一定时间。
2 硅烷法的工艺流程
2.1 Komatsu硅化镁法
这种方法的原料消耗量大,污染严重,投资的成本高,生产的危险性也高,也只有日本的Kommatsu用该法制备多晶硅。
此公司出现过硅烷的爆炸事件。
国内有浙大、上海冶炼厂、复旦大学、上海合金厂曾经用硅化镁的液氨热分解来生产多晶硅。
因为同样原因,先后被迫停产。
2.2 碱金属的氢化物硅烷法
2.2.1 氯硅烷法
该工艺的基本过程如下:
MAlH4+SiCl4→SiH4+MCl+AlCl3 SiH4→Si+2H2
其中,M可以是Li、Na、K等碱性金属。
2.2.2 氟化硅法
Na2SiF6法又被称为DFD法,是由DFD公司提出新多晶硅的生产路线。
这种工艺是把磷肥的副产物Na2SiF6热解制备SiF4与NaF;再经过精制得到SiF4气体,和NaA1H4进行反应得SiH4与副产NaA1F4;硅烷进行精制纯化之后加入硅烷的热解炉当中制取多晶硅的产品。
副产物NaF与NaA1F4可用来制取冰晶石。
此工艺优点体现以下两方面:
①此工艺用廉价磷肥的副产品--氟硅酸钠作为原料,经过热分解来制取四氟化硅,再制取硅烷,降低生产的成本,解决磷肥业大量的Na2SiF6堆造成环境污染及资源浪费等问题;
②此工艺实现资源最优化的利用,实现氟资源综合的利用,解决含氟废料的处理难问题,充分利用了资源,还降低产品生产的成本,环境也得到保护。
2.2.3 NaAlH4法
以H2SO4、SiO2、Na、Al、H等为主要原辅材料来制备多晶硅的新工艺,主要包括五个环节:NaAlH4的制备、SiF4的制备与提纯、SiH4的制备与提纯和SiH4的热解。
其工艺流程如下:NaAlF4、H2SO4与SiO2在一定条件下制备得到SiF4气体;然后经精制后得SiF4与NaAlH4反应氢化得到SiH4和副产物NaAlF4,最后精制后的SiH4在流化床或固定床分解炉内进行分解来制备多晶硅,其中副产物氟化铝钠又可以作为制备SiF4气体的原料。
该工艺中涉及的主要化学反应如下:
NaALH4+SiF4→NaALF4+SiH4
2.2.4 歧化法
作为现在制取硅烷主要的方法,此方法以Union Carbide作为代表,优点是硅烷易提纯,硅量含较高(约87.5%);分解速率快,效率高(99%),温度低,生产的多晶硅能耗是40千瓦时每千克,而且纯度高。
缺点也明显,在制硅烷的时候,每一步转换效率都低,为充分利用原材料,需要多次循环使用,全过程需反复加热冷却,造成能耗高,而且用到易燃易爆物料--硅烷,安全管理要求更高,现在市场的占有率较低。
3 其他方法
除了上述几种方法之外,在硅烷法中还有下列几种方法可用于多晶硅的生产。
①H.E.Ulmer法,该法的主要反应式为:
4NaH+3SiF4→SiH4+Na2SiF6
②Jacubert法,该法的主要反应式为:
SiH4-xClx+xLiH→SiH4+LiCl
③Cadet电化学法,该方法利用Mg2Si的电解来制取SiH4,其反应式是:
Mg2Si+4H+→2Mg2++SiH4
4 结论
综上所述,我们可以看出,硅烷法制备多晶硅工艺多种多样,其中Na2SiF6法因成本较低,成为较合理路线,但该法也存在部分技术难题。
完善工艺路线,将成本与质量都有新突破,是我们现在的追求目标和努力方向。
参考文献:
[1]樊舜尧,师文林.多晶硅生产技术及发展现状[J].新材料产业,2013,5(10):22-26.。