渗氮技术中的气体渗氮控制
渗氮材料使用温度
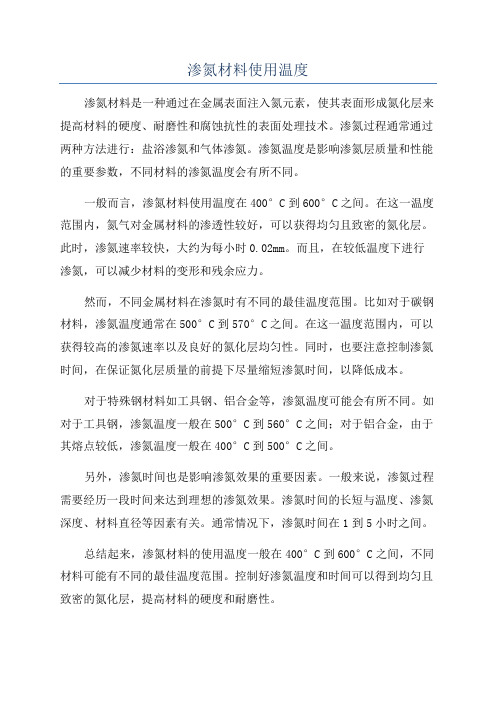
渗氮材料使用温度渗氮材料是一种通过在金属表面注入氮元素,使其表面形成氮化层来提高材料的硬度、耐磨性和腐蚀抗性的表面处理技术。
渗氮过程通常通过两种方法进行:盐浴渗氮和气体渗氮。
渗氮温度是影响渗氮层质量和性能的重要参数,不同材料的渗氮温度会有所不同。
一般而言,渗氮材料使用温度在400°C到600°C之间。
在这一温度范围内,氮气对金属材料的渗透性较好,可以获得均匀且致密的氮化层。
此时,渗氮速率较快,大约为每小时0.02mm。
而且,在较低温度下进行渗氮,可以减少材料的变形和残余应力。
然而,不同金属材料在渗氮时有不同的最佳温度范围。
比如对于碳钢材料,渗氮温度通常在500°C到570°C之间。
在这一温度范围内,可以获得较高的渗氮速率以及良好的氮化层均匀性。
同时,也要注意控制渗氮时间,在保证氮化层质量的前提下尽量缩短渗氮时间,以降低成本。
对于特殊钢材料如工具钢、铝合金等,渗氮温度可能会有所不同。
如对于工具钢,渗氮温度一般在500°C到560°C之间;对于铝合金,由于其熔点较低,渗氮温度一般在400°C到500°C之间。
另外,渗氮时间也是影响渗氮效果的重要因素。
一般来说,渗氮过程需要经历一段时间来达到理想的渗氮效果。
渗氮时间的长短与温度、渗氮深度、材料直径等因素有关。
通常情况下,渗氮时间在1到5小时之间。
总结起来,渗氮材料的使用温度一般在400°C到600°C之间,不同材料可能有不同的最佳温度范围。
控制好渗氮温度和时间可以得到均匀且致密的氮化层,提高材料的硬度和耐磨性。
气体渗氮作业指导书

气体渗氮作业指导书1.概述渗氮俗称氮化,通常是指把已经预备热处理(如调质)的工件放入含氮介质的密闭容器中,在一定温度和一定压力下保持适当时间,使含氮介质通过工件表面的触媒作用发生化学反应,分解为活性氮原子,然后又工件表面渗入,并通过扩散而形成一定深度的渗层的汉为机械化学热处理方法。
与渗碳不同的是:渗氮虽然也包括吸收、分解和扩散几个过程,但它的扩散是一种反应扩散,即氮原子由工件表面吸收后,经一系列化学反应和转化、传递向内部扩散。
2.施工过程2.1 清洗及防渗处理由于渗氮对工件表面的清洁程度要求非常高,因此工件必须进行严格的清洗,操作者清洗工件前,必须先洗净并擦干双手,然后用煤油或普通汽油附之以毛刷清洗工件。
工件清洗前应无锈迹,清洗后汉为机械不得沾染任何油腻和污渍,炉具、炉架均应进行刷洗或擦拭;困扎工件用的铁丝应事先去锌(高温烧掉或酸浸后清洗烘干),以免污染炉罐,影响炉内气氛。
根据图纸要求,对工件防渗区域进行防渗处理。
1、涂料的配制:粉料:粘结剂=10:2~3,充分搅拌,调成一定稠度的浆液。
2、涂料的覆盖:涂层厚度一般为0.2mm,若氮化时间超过60h,则为0.3-0.5mm。
涂层应在第一遍干后再刷第二遍。
3、涂料的干燥:阴干4-5h,即可进炉施工。
4、涂料的去除:用棉纱或刷子去除。
注:粘结剂尽量存放在10-40℃环境中,若有冻结,用50-60℃化冻。
2.2 装炉渗氮一般采用冷炉装料(按照工艺规程要求的装炉方式和装炉量装炉,以免工件变形和施渗不均),随炉升温。
在连续作业生产中,允许到温入炉(如出一炉,接着装一炉)。
炉盖密封后,应通氨(或氮气)排气30min,待炉内空气驱除殆尽,然后加压施渗。
2.3 设备操作1、根据《热处理氮化工艺卡片》调取程序号。
2、炉温升至100℃以前,开启冷却泵,保证循环冷却水畅通。
3、升温达到100℃以上,打开搅拌风扇。
装炉后温升至160-200℃时保持通入甲醇,滴量为40-60滴/分。
气体二段渗氮
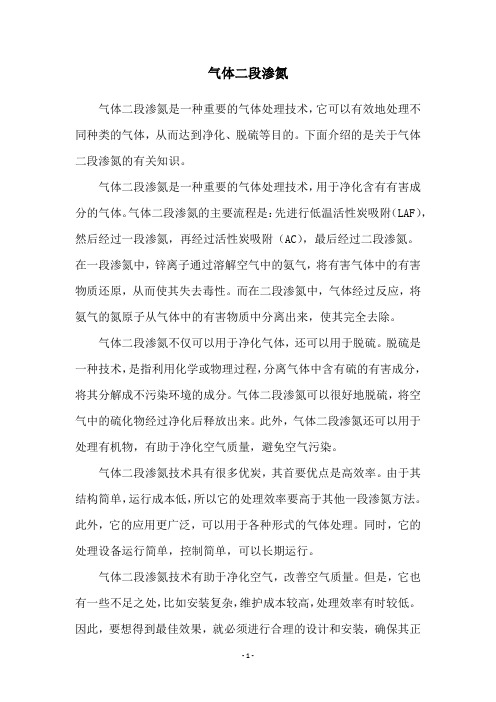
气体二段渗氮气体二段渗氮是一种重要的气体处理技术,它可以有效地处理不同种类的气体,从而达到净化、脱硫等目的。
下面介绍的是关于气体二段渗氮的有关知识。
气体二段渗氮是一种重要的气体处理技术,用于净化含有有害成分的气体。
气体二段渗氮的主要流程是:先进行低温活性炭吸附(LAF),然后经过一段渗氮,再经过活性炭吸附(AC),最后经过二段渗氮。
在一段渗氮中,锌离子通过溶解空气中的氨气,将有害气体中的有害物质还原,从而使其失去毒性。
而在二段渗氮中,气体经过反应,将氨气的氮原子从气体中的有害物质中分离出来,使其完全去除。
气体二段渗氮不仅可以用于净化气体,还可以用于脱硫。
脱硫是一种技术,是指利用化学或物理过程,分离气体中含有硫的有害成分,将其分解成不污染环境的成分。
气体二段渗氮可以很好地脱硫,将空气中的硫化物经过净化后释放出来。
此外,气体二段渗氮还可以用于处理有机物,有助于净化空气质量,避免空气污染。
气体二段渗氮技术具有很多优炭,其首要优点是高效率。
由于其结构简单,运行成本低,所以它的处理效率要高于其他一段渗氮方法。
此外,它的应用更广泛,可以用于各种形式的气体处理。
同时,它的处理设备运行简单,控制简单,可以长期运行。
气体二段渗氮技术有助于净化空气,改善空气质量。
但是,它也有一些不足之处,比如安装复杂,维护成本较高,处理效率有时较低。
因此,要想得到最佳效果,就必须进行合理的设计和安装,确保其正常运行。
综上所述,气体二段渗氮是一种重要的气体处理技术,可以有效地净化气体,脱硫,改善空气质量。
不仅具有高效率、低成本、安装简单的优点,而且能够产生更稳定、可靠的效果,使气体处理获得良好的效果。
然而,安装和维护需要特殊的专业技术,而且处理效率也不一定高。
因此,在应用气体二段渗氮技术前,应充分考虑各方面的因素,最后才能获得最佳的应用效果。
齿轮渗氮、氮碳共渗工艺及质量控制

齿轮渗氮、氮碳共渗工艺及质量控制
齿轮渗氮是一种提高齿轮表面硬度和耐磨性的表面处理方法,可以通过在齿轮表面注入氮气,使其在表面形成氮化层。
齿轮渗氮的主要工艺包括气体渗氮和盐浴渗氮两种方法。
1. 气体渗氮工艺:气体渗氮是将齿轮置于渗氮炉中,通过加热至高温状态,然后通过氨气或氮气等气体进行渗透处理,使氮原子渗入齿轮表面形成氮化层。
这种工艺具有操作简单、渗透深度可控、成本较低等优点。
2. 盐浴渗氮工艺:盐浴渗氮是将齿轮浸入温度较高的盐浴溶液中进行处理,使盐浴溶液中的氮原子渗透到齿轮表面形成氮化层。
这种工艺渗透速度较快,渗透深度大,但操作复杂,成本较高。
质量控制是齿轮渗氮过程中非常重要的环节,主要包括以下几个方面:
1. 温度控制:温度是齿轮渗氮过程中的重要参数,需要控制在合适的范围内,以保证渗透效果和避免过热损坏齿轮。
2. 渗氮时间控制:渗氮时间是影响氮化层深度和均匀性的重要因素,需要根据齿轮的具体要求和设计要求来确定。
3. 渗氮介质控制:选择合适的渗氮介质对于渗透效果和氮化层质量都有重要影
响,需要根据具体情况进行选择。
4. 清洗和处理后的质量检验:渗氮后需要对齿轮进行清洗和处理,以去除表面的残留物,然后进行质量检验,包括硬度测试、金相分析、氮化层厚度测量等。
通过合理的工艺选择和质量控制,可以确保齿轮渗氮的效果和质量,提高齿轮的使用寿命和性能。
气体氮化工艺的作用、特点和应用
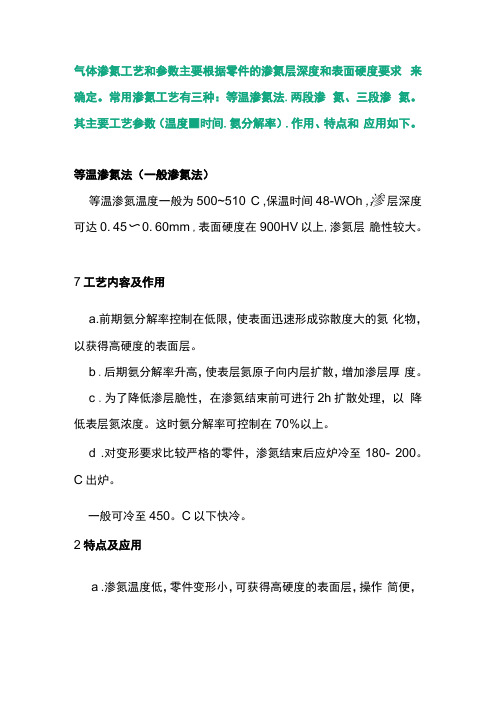
气体渗氮工艺和参数主要根据零件的渗氮层深度和表面硬度要求来确定。
常用渗氮工艺有三种:等温渗氮法.两段渗氮、三段渗氮。
其主要工艺参数(温度■时间.氨分解率).作用、特点和应用如下。
等温渗氮法(一般渗氮法)等温渗氮温度一般为500~510°C ,保温时间48-WOh ,渗层深度可达0. 45〜0. 60mm ,表面硬度在900HV以上,渗氮层脆性较大。
7工艺内容及作用a.前期氨分解率控制在低限,使表面迅速形成弥散度大的氮化物,以获得高硬度的表面层。
b .后期氨分解率升高,使表层氮原子向内层扩散,增加渗层厚度。
c .为了降低渗层脆性,在渗氮结束前可进行2h扩散处理,以降低表层氮浓度。
这时氨分解率可控制在70%以上。
d .对变形要求比较严格的零件,渗氮结束后应炉冷至180- 200。
C出炉。
一般可冷至450。
C以下快冷。
2特点及应用a .渗氮温度低,零件变形小,可获得高硬度的表面层,操作简便,但渗氮层浅,生产周期长。
b.表面易产生富氮脆化层,有时还会有疏松层。
c.适用于渗氮层变形要求严,硬度要求高的零件。
两段渗氮两段渗氮为先在510。
C渗氮,再升高至530 ~ 540。
C渗氮,两段的保温时间相等或后段略长,其渗氮时间比等温渗氮少1/3左右。
表面硬度低,为30~50HV01工艺内容及作用a.一段渗氮的分解率较低,使表面可形成颗粒细小、弥散度高的氮化物,得到较高的表面硬度。
b.二段渗氮的温度和氨分解率升高,加速了氮的扩散,增加了渗层深度,缩短了生产周期,硬度梯度变得平缓,同时亦可减薄脆性的白亮层。
2特点及应用a.在保证表面得到高硬度的前提下可缩短生产周期,同时又可得到较深的渗氮层。
b.适用于渗氮层较深,要求表面较硬而结构简单的零件。
三段渗氮三段渗氮为510。
C渗氮,再升温至550 ~ 560。
C渗氮,然后降至520〜530。
C渗氮,保温时间大约各占1/3 ,渗速更快,表面硬度与两段渗氮相似,但变形略大一点。
漫谈二关于气体氮碳共渗软氮化表面白亮层的控制问题〖化学热处理〗热

漫谈二关于气体氮碳共渗软氮化表面白亮层的控制问题〖化学热处理〗热000000000000001,如果说渗氮的目标是希望表面获得少无白亮层又有足够深度的扩散层,同时要求保持心部调质状态的高强韧性--见漫谈(一);那么,氮碳共渗(含短时氮化)则希望表面获得一定厚度、性能优良的白亮层,至于氮碳共渗时产生的扩散层有多厚,以及对心部机械性能的要求上,除特殊要求(比如某些模具、高耐磨零件等)以外,一般不作明文规定。
这是这两种工艺方法在技术目标层面上最基本的区别。
2,氮碳共渗工艺覆盖的钢种很宽,几乎所有的钢牌号到铸铁都可以用得上。
氮碳共渗之所以应用如此广泛,是因为那一层厚度不大的白亮层,具有高硬度、高耐磨和有一定抗蚀能力,同时在钢表面形成压应力可以提高一些疲劳性能;其二,在价廉的碳素钢和低合金钢上,可以很容易获得较好的白亮层。
良好的性价比,使这种工艺技术在轻负荷零件、精密的机械零件以及某些大路货的耐大气腐蚀上得到设计师和厂商们的普遍赞誉和认可。
然而,必须指出,它不可能替代重负荷零件所需要的渗氮,就像目前的渗氮不能完全替代渗碳一样。
3,白亮层的控制主要有两个方面,一是厚度,二是相结构。
厚度要求取决于零件的服役条件,也受钢牌号和相结构的限制,最常见的要求是5~25μm范围内选择。
白亮层的相结构与脆性直接关联,获得性能比较良好的白亮层,应当以单相ε或单相γ,组织为上等,而不是现在大都是那种ε+γ,双相组织。
(参见.ge%3D2page=230楼'孤鸿踏雪'的帖子)。
由于形成γ,化合物的含氮量范围很窄,韧性较好的纯γ,的厚度只能很浅薄(有其特定用途),获得一定厚度的单相ε组织就成了热处理工作者氮碳共渗当前追寻的一个课题(参见)。
由于技术方法对限制,目前相关标准中检测白亮层脆性等级的尺度较大,难以判别脆性程度上的细微差别,也就是说,同样都是1级水平,由于相结构上的差别在使用性能上将有所区分,然而,并没有引起工程界的特别注意。
金属热处理中渗氮工艺常识

金属热处理中渗氮工艺常识金属热处理中的各种渗氮工艺使氮原子渗入钢铁工件表层内的化学热处理工艺;传统的气体渗氮是把工件放入密封容器中﹐通以流动的氨气并加热﹐保温较长时间后﹐氨气热分解產生活性氮原子﹐不断吸附到工件表面﹐并扩散渗入工件表层内﹐从而改变表层的化学成分和组织﹐获得优良的表面性能。
如果在渗氮过程中同时渗入碳以促进氮的扩散﹐则称为氮碳共渗。
钢铁渗氮的研究始於20世纪初﹐20年代以后获得工业应用。
最初的气体渗氮﹐仅限於含铬﹑铝的钢﹐后来才扩大到其他钢种。
从70年{BANNED}始﹐渗氮从理论到工艺都得到迅速发展并日趋完善﹐适用的材料和工件也日益扩大﹐成为重要的化学热处理工艺之一。
渗入钢中的氮一方面由表及裡与铁形成不同含氮量的氮化铁﹐一方面与钢中的合金元素结合形成各种合金氮化物﹐特别是氮化铝﹑氮化铬。
这些氮化物具有很高的硬度﹑热稳定性和很高的弥散度﹐因而可使渗氮后的钢件得到高的表面硬度﹑耐磨性﹑疲劳强度﹑抗咬合性﹑抗大气和过热蒸汽腐蚀能力﹑抗回火软化能力﹐并降低缺口敏感性。
与渗碳工艺相比﹐渗氮温度比较低﹐因而畸变小﹐但由於心部硬度较低﹐渗层也较浅﹐一般只能满足承受轻﹑中等载荷的耐磨﹑耐疲劳要求﹐或有一定耐热﹑耐腐蚀要求的机器零件﹐以及各种切削刀具﹑冷作和热作模具等。
渗氮有多种方法﹐常用的是气体渗氮和离子渗氮。
气体渗氮:一般以提高金属的耐磨性为主要目的﹐因此需要获得高的表面硬度。
它适用於38CrMnAc等渗氮钢。
渗氮后工件表面硬度可达HV850~1200。
渗氮温度低﹐工件畸变小﹐可用於精度要求高﹑又有耐磨要求的零件﹐如鏜床鏜杆和主轴﹑磨床主轴﹑气缸套筒等。
但由於渗氮层较薄﹐不适於承受重载的耐磨零件。
气体参氮可採用一般渗氮法(即等温渗氮)或多段(二段﹑三段)渗氮法。
前者是在整个渗氮过程中渗氮温度和氨气分解率保持不变。
温度一般在480~520℃之间﹐氨气分解率为15~30%﹐保温时间近80小时。
这种工艺适用於渗层浅﹑畸变要求严﹑硬度要求高的零件﹐但处理时间过长。
气体渗氮工艺
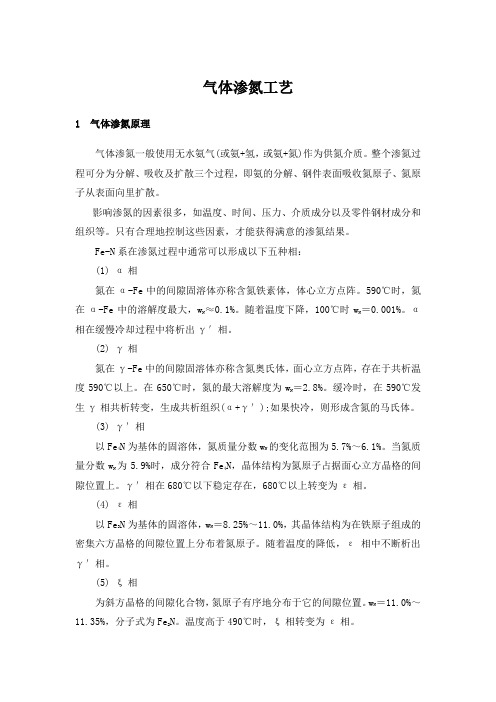
气体渗氮工艺1 气体渗氮原理气体渗氮一般使用无水氨气(或氨+氢,或氨+氮)作为供氮介质。
整个渗氮过程可分为分解、吸收及扩散三个过程,即氨的分解、钢件表面吸收氮原子、氮原子从表面向里扩散。
影响渗氮的因素很多,如温度、时间、压力、介质成分以及零件钢材成分和组织等。
只有合理地控制这些因素,才能获得满意的渗氮结果。
Fe-N系在渗氮过程中通常可以形成以下五种相:(1) α相氮在α-Fe中的间隙固溶体亦称含氮铁素体,体心立方点阵。
590℃时,氮在α-Fe中的溶解度最大,wN ≈0.1%。
随着温度下降,100℃时wN=0.001%。
α相在缓慢冷却过程中将析出γ′相。
(2) γ相氮在γ-Fe中的间隙固溶体亦称含氮奥氏体,面心立方点阵,存在于共析温度590℃以上。
在650℃时,氮的最大溶解度为wN=2.8%。
缓冷时,在590℃发生γ相共析转变,生成共析组织(α+γ′);如果快冷,则形成含氮的马氏体。
(3) γ′相以Fe4N为基体的固溶体,氮质量分数wN的变化范围为5.7%~6.1%。
当氮质量分数wN 为5.9%时,成分符合Fe4N,晶体结构为氮原子占据面心立方晶格的间隙位置上。
γ′相在680℃以下稳定存在,680℃以上转变为ε相。
(4) ε相以Fe3N为基体的固溶体,wN=8.25%~11.0%,其晶体结构为在铁原子组成的密集六方晶格的间隙位置上分布着氮原子。
随着温度的降低,ε相中不断析出γ′相。
(5) ξ相为斜方晶格的间隙化合物,氮原子有序地分布于它的间隙位置。
wN=11.0%~11.35%,分子式为Fe2N。
温度高于490℃时,ξ相转变为ε相。
渗氮通常在共析温度(590℃)以下进行。
纯铁渗氮后,缓冷至室温,渗氮层达组织由表及里为ε→ε+γ′→γ′→γ′+α→α。
如果表面氮质量分数wN到11.0%左右,则ε相可能转变为ξ相。
因ε、γ′和ξ相抗蚀性很强,在金相显微镜下为一个白亮层,难以清晰区分。
当渗氮温度超过590℃时,纯铁在室温的渗氮层组织由表及里为ε→ε+γ′→γ′→(α+γ′)共析→α+γ′。
- 1、下载文档前请自行甄别文档内容的完整性,平台不提供额外的编辑、内容补充、找答案等附加服务。
- 2、"仅部分预览"的文档,不可在线预览部分如存在完整性等问题,可反馈申请退款(可完整预览的文档不适用该条件!)。
- 3、如文档侵犯您的权益,请联系客服反馈,我们会尽快为您处理(人工客服工作时间:9:00-18:30)。
渗氮技术中的气体渗氮控制
渗氮处理技术
零件的渗氮效果直接影响其工作效率,为此针对不同氮化要求,第一线的技术达人们探索出了不同的渗氮工艺,并在工业上广泛应用。
常用渗氮处理中的气体渗氮,因其理论简单、操作方便而得以广泛运用,但气体渗氮时间长,如果控制不好,易出现最外层氮化物质脆,在冲击载荷作用下易剥落,所以限制了应用范围。
随着生产上对于渗氮工艺的要求越来越高,相继出现了各类渗氮方法,如盐浴软氮化、气体软氮化、真空氮化等,这些技术的运用对缩短氮化时间,提高氮化氮层质量有着重要意义。
渗氮处理有哪些实用
经渗氮处理,零件能获得好的表面硬度(67-72HRC)、良好的耐磨性、耐腐蚀性、高温稳定和高疲劳强度。
这些优良的性能使渗氮钢广泛应用于制造各类重要零件,如燃油喷射系统中的精密件、发动机气缸、阀杆等。
渗氮处理与渗碳处理都是常用的表面强化方法,两者各有优势。
气体渗氮控制设备的进展
在今后,渗氮技术应逐渐向渗氮时间短、渗层深、能耗低、绿色经济的方向转变。
这就要求从生产工艺的角度、设备选择等方面进行改进和创新。
在气体渗氮或碳氮共渗气氛中,通常采用氨气或以氨气为主的气体作为原料气。
依据原理,炉气氮势与氨分解率有直接关系。
常规情况下,可以使用泡泡瓶、氢探头进行控制。
最新的研究发现,通入炉内的气氛除氨气之外,还通入了加快气氛冲刷速度的氮气、氧化及后氧化过程中所需的CO2、甲醇、水等其它气氛时,传统的测量会出现渗氮工艺偏差,甚至报废整炉工件的情况。
武汉华敏进行了深入研究,最新的热处理氮控系统的能够精确计算氢含量,相较于传统的铂比热导传感器,在测量精度、灵敏度,温度漂移小等方向有很大的提升。
并且在氢探头内置进口MEMS热导传感器,利用H2气体和其他气体热导率差异很大的特性对被测气氛中的氢含量进行测量。