汽车刹车盘铸件生产工艺
刹车盘铸造工艺规程
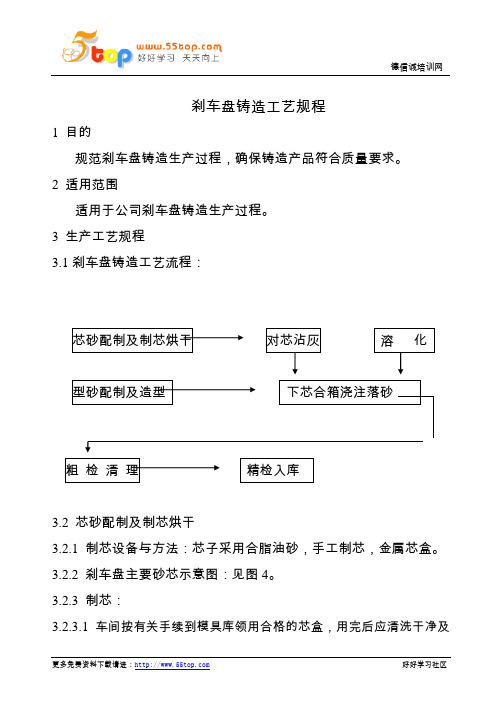
刹车盘铸造工艺规程1 目的规范刹车盘铸造生产过程,确保铸造产品符合质量要求。
2 适用范围适用于公司刹车盘铸造生产过程。
3 生产工艺规程3.1刹车盘铸造工艺流程:3.2 芯砂配制及制芯烘干3.2.1 制芯设备与方法:芯子采用合脂油砂,手工制芯,金属芯盒。
3.2.2 刹车盘主要砂芯示意图:见图4。
3.2.3 制芯:3.2.3.1 车间按有关手续到模具库领用合格的芯盒,用完后应清洗干净及时送回。
3.2.3.2 油砂混制时,严格按比例混制(芯砂与合脂油按100:3比例混制)。
使用过程中出现争议时,取样送实验室测试其强度和透气性。
3.2.3.3 打芯时,芯盒的筋片不得有刮砂、粘砂现象。
3.2.3.4 刹车盘砂芯上的字要清晰完整,刮出面要用工具刮了压光。
3.2.3.5 砂芯应尽量轻轻在专用工作台上均匀敲出或磕出芯盒。
3.1.3.6 芯头用Φ8mm气孔锥扎透。
(芯盒带有透气锥的除外)3.1.3.7 检验砂芯,大平面度不得大于0.3mm,厚度尺寸不小于芯盒磨损极限尺寸。
3.1.4 砂芯质量要求:尺寸准确、形状完整、紧实光洁、无有松动、气眼要畅、砂芯不得有掉砂、粘砂、裂纹的现象。
3.1.5 烘干(烤芯)3.1.5.1 严格控制芯窑温度和时间。
(芯窑温度和时间的控制温度见下图)T(降温50 50t小时(t小时)芯室温度6小时8小时3.1.5.2 烘芯最高温度为210℃~240℃。
3.2 对芯粘灰(采用组合芯时,涉及该项内容)3.2.1 当粘合小芯时,该砂芯没留有研磨量,所以只能用手工在平板上稍微研磨,粘合剂为糊精。
3.2.2 两小芯必须对正,不允许偏差,对缝需抹平,粘合后刷涂料。
3.2.3 刷涂后必须晾干后方可使用。
3.2.4 涂料配比:黑铅粉97%,膨润3%,两料混合后,用水调匀即可,涂料存放期为夏不超过两昼夜,冬不超过三昼夜,每两周要彻底清理一次。
3.3 型砂配制,砂型制造。
3.3.1 型砂配制。
3.3.1.1 刹车盘造型用砂分:面砂、背砂(石英面砂、煤粉面砂)。
制动盘加工工艺

制动盘加工工艺一、制动盘加工工艺概述制动盘是汽车制动系统中重要的零部件之一,其性能直接影响到车辆的安全性和行驶舒适性。
制动盘的加工工艺是制动盘生产过程中的核心环节,它包括多个步骤和工序,通过一系列的加工工艺使得原材料逐渐转变为具备一定形状、尺寸和质量要求的制动盘。
二、制动盘加工工艺步骤1. 原材料准备制动盘的原材料通常是一种特殊的铸铁材料,其力学性能和耐磨性能较好。
在加工工艺开始之前,需要对原材料进行质检,确保其符合制动盘的要求。
2. 切割原料切割是将原材料切割成适当的尺寸和形状的关键步骤。
常用的切割方法有火焰切割和等离子切割,通过切割将原材料切割成制动盘需要的圆形或其他形状。
3. 粗加工粗加工是制动盘加工的第一道工序,主要是对原材料进行初步的成型和修整。
常用的粗加工方法有车削、铣削和钻削等,通过这些工艺将原材料加工成初步形状。
4. 热处理热处理是为了提高制动盘的力学性能和硬度,常见的热处理方法有正火、淬火和回火等。
通过这些热处理工艺可以使制动盘达到所需的硬度和韧性,提高其抗磨性和抗疲劳性能。
5. 精加工精加工是对制动盘进行最终成型和表面处理的工序,其目的是使制动盘具备更好的表面光洁度和平整度。
常见的精加工方法有砂轮修整、磨削和抛光等,通过这些工艺将制动盘的表面修整得更光滑、更平整。
6. 检测和质检制动盘加工完成后,需要进行检测和质检,以保证制动盘的尺寸和质量符合要求。
常见的检测方法包括超声波检测、磁粉检测和硬度检测等,通过这些检测手段来排除制动盘存在的缺陷和隐患。
三、制动盘加工工艺的优化制动盘加工工艺的优化可以提高生产效率、降低生产成本,同时还能改善制动盘的性能和质量。
1. 工艺参数优化通过优化制动盘加工工艺的参数,如切削速度、进给量和刀具材料等,可以提高加工效率和加工质量。
合理选择刀具和切削材料,降低切削力和摩擦力,减少刀具磨损,延长使用寿命。
2. 设备改进和自动化引进先进的加工设备和自动化系统,能够提高生产效率和生产质量。
汽车制动卡钳的铸造工艺研究
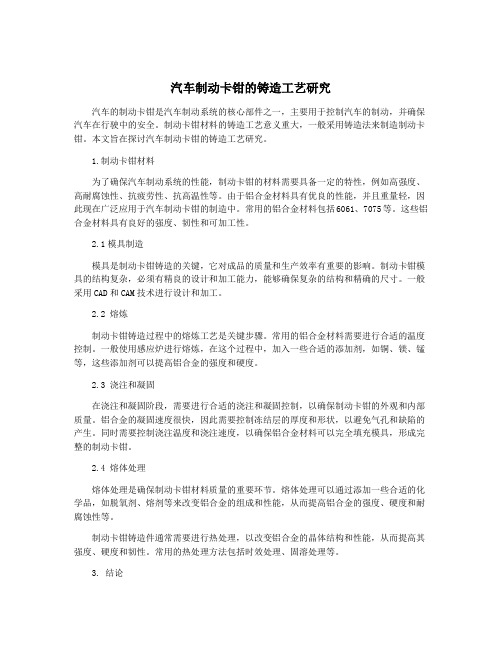
汽车制动卡钳的铸造工艺研究汽车的制动卡钳是汽车制动系统的核心部件之一,主要用于控制汽车的制动,并确保汽车在行驶中的安全。
制动卡钳材料的铸造工艺意义重大,一般采用铸造法来制造制动卡钳。
本文旨在探讨汽车制动卡钳的铸造工艺研究。
1.制动卡钳材料为了确保汽车制动系统的性能,制动卡钳的材料需要具备一定的特性,例如高强度、高耐腐蚀性、抗疲劳性、抗高温性等。
由于铝合金材料具有优良的性能,并且重量轻,因此现在广泛应用于汽车制动卡钳的制造中。
常用的铝合金材料包括6061、7075等。
这些铝合金材料具有良好的强度、韧性和可加工性。
2.1模具制造模具是制动卡钳铸造的关键,它对成品的质量和生产效率有重要的影响。
制动卡钳模具的结构复杂,必须有精良的设计和加工能力,能够确保复杂的结构和精确的尺寸。
一般采用CAD和CAM技术进行设计和加工。
2.2 熔炼制动卡钳铸造过程中的熔炼工艺是关键步骤。
常用的铝合金材料需要进行合适的温度控制。
一般使用感应炉进行熔炼,在这个过程中,加入一些合适的添加剂,如铜、镁、锰等,这些添加剂可以提高铝合金的强度和硬度。
2.3 浇注和凝固在浇注和凝固阶段,需要进行合适的浇注和凝固控制,以确保制动卡钳的外观和内部质量。
铝合金的凝固速度很快,因此需要控制冻结层的厚度和形状,以避免气孔和缺陷的产生。
同时需要控制浇注温度和浇注速度,以确保铝合金材料可以完全填充模具,形成完整的制动卡钳。
2.4 熔体处理熔体处理是确保制动卡钳材料质量的重要环节。
熔体处理可以通过添加一些合适的化学品,如脱氧剂、熔剂等来改变铝合金的组成和性能,从而提高铝合金的强度、硬度和耐腐蚀性等。
制动卡钳铸造件通常需要进行热处理,以改变铝合金的晶体结构和性能,从而提高其强度、硬度和韧性。
常用的热处理方法包括时效处理、固溶处理等。
3. 结论汽车制动卡钳是汽车制动系统中重要的部件,其制造过程需要采用合适的材料和工艺。
铸造工艺是制动卡钳铸造的关键,涉及到模具制作、熔炼、浇注和凝固、熔体处理和热处理等步骤。
汽车制动卡钳的铸造工艺研究
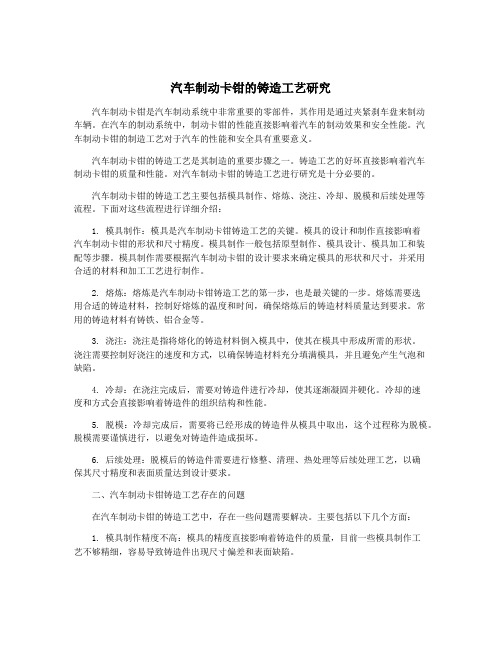
汽车制动卡钳的铸造工艺研究汽车制动卡钳是汽车制动系统中非常重要的零部件,其作用是通过夹紧刹车盘来制动车辆。
在汽车的制动系统中,制动卡钳的性能直接影响着汽车的制动效果和安全性能。
汽车制动卡钳的制造工艺对于汽车的性能和安全具有重要意义。
汽车制动卡钳的铸造工艺是其制造的重要步骤之一。
铸造工艺的好坏直接影响着汽车制动卡钳的质量和性能。
对汽车制动卡钳的铸造工艺进行研究是十分必要的。
汽车制动卡钳的铸造工艺主要包括模具制作、熔炼、浇注、冷却、脱模和后续处理等流程。
下面对这些流程进行详细介绍:1. 模具制作:模具是汽车制动卡钳铸造工艺的关键。
模具的设计和制作直接影响着汽车制动卡钳的形状和尺寸精度。
模具制作一般包括原型制作、模具设计、模具加工和装配等步骤。
模具制作需要根据汽车制动卡钳的设计要求来确定模具的形状和尺寸,并采用合适的材料和加工工艺进行制作。
2. 熔炼:熔炼是汽车制动卡钳铸造工艺的第一步,也是最关键的一步。
熔炼需要选用合适的铸造材料,控制好熔炼的温度和时间,确保熔炼后的铸造材料质量达到要求。
常用的铸造材料有铸铁、铝合金等。
3. 浇注:浇注是指将熔化的铸造材料倒入模具中,使其在模具中形成所需的形状。
浇注需要控制好浇注的速度和方式,以确保铸造材料充分填满模具,并且避免产生气泡和缺陷。
4. 冷却:在浇注完成后,需要对铸造件进行冷却,使其逐渐凝固并硬化。
冷却的速度和方式会直接影响着铸造件的组织结构和性能。
5. 脱模:冷却完成后,需要将已经形成的铸造件从模具中取出,这个过程称为脱模。
脱模需要谨慎进行,以避免对铸造件造成损坏。
6. 后续处理:脱模后的铸造件需要进行修整、清理、热处理等后续处理工艺,以确保其尺寸精度和表面质量达到设计要求。
二、汽车制动卡钳铸造工艺存在的问题在汽车制动卡钳的铸造工艺中,存在一些问题需要解决。
主要包括以下几个方面:1. 模具制作精度不高:模具的精度直接影响着铸造件的质量,目前一些模具制作工艺不够精细,容易导致铸造件出现尺寸偏差和表面缺陷。
新东线生产YH3216刹车盘的铸造工艺优化

新东线生产YH3216刹车盘的铸造工艺优化曹玉亭,李振,韩海全(烟台胜地汽车零部件制造有限公司,山东烟台264006)摘要:介绍了YH3216刹车盘的铸件结构及技术要求,针对原生产工艺出现的砂眼、气孔等缺陷问题,采取了以下改进措施:将过滤网设置在横浇道上,并将阻流截面变成二次搭接来挡渣;利用缓流式浇,阻,降低流速,流;采用环形横浇道,将内浇道适当分散,使砂;适当铸砂的气。
生产:次制,砂眼、气孔缺陷;生产,铸件成87.1%上97%,效关键词:铸;刹车盘;铸造工艺;砂眼;气孔中图分类号:TG251文献标志码:B文章编号:1003-8345(2021)03-0047-04D01:10.3969/j.issn.1003-8345.2021.03.012Optimization of Foundry Process of YH3216Brake Disc Produced by Sinto LineCAO Yu-ting,LI Zhen,HAN Hai-quan(Yantai Winhere Auto-part Manufacturing Co.,Ltd.,Yantai264006,China)Abstract:The casting structure and technical requirements of YH3216brake disc were introduced.According to the defects such as sand holes and porosity in the original production process,the following improvement measures were taken:A filter was placed on the cross runner and the choke cross section was changed to overlap twice to block the slag.The slow-flow pouring system was used to increase the local resistance,reduce the flow rate,and prevent the turbulence of the molten iron. An annular cross-runner was used to disperse the inner runner appropriately to make the sand mold heated evenly.Increase the exhaust capacity of mold and sand core.The production results showed that after small batch trial production,the defects of sand holes and porosity defects were greatly reduced.After mass production,the comprehensive yield of castings gradually raised from the initial87.1%to97%,and the effect was remarkable.Key words:gray iron;brake disc;casting process;sand hole;porosity1铸件结构及技术要求1.1铸件结构YH3216刹车盘结构为轴承盘,直径338mm,铸件质量19.51kg,铸件95.66mm,材G3500。
制动盘铸造工艺设计

1.结合所学知识,查找相应资料,对所给零件或铸件原铸造工艺进行分析(工艺图设计,参数选取,砂芯设计,冒口设计,模板设计等)谈谈你的体会,及对教材、课堂教学的建议。
2.查资料,完成所指定锻件的生产过程,锻件图设计、相应的计算过程、下料、加热、锻造及热处理工艺进行分析。
3.结合汽车零件生产。
阐述埋弧焊原理、工艺特点、质量保证措施。
1 •结合所学知识,查找相应资料,对所给零件或铸件原铸造工艺进行分析(工艺图设计,参数选取,砂芯设计,冒口设计,模板设计等)。
1.1制动盘铸造要求及现状一、生产技术状况:制动盘种类繁多,特点是壁薄,盘片及中心处由砂芯形成。
不同种类制动盘,在盘径、盘片厚度及两片间隙尺寸上存在差异,盘毂的厚度和高度也各不相同。
单层盘片的制动盘结构比较简单。
铸件重量多为6~18kgo二、技术要求:铸件外轮廓全部加工,精加工后不得有任何缩松、气孔、砂眼等铸造缺陷。
金相组织为中等片状型,石墨型,组织均匀,断面敏感性小(特别是硬度差小)。
三、力学性能:(T b >250MPa , HB180-240,相当于国际HT250牌号。
四、有些外商对铸件的化学成分也作要求,本设计不作详细介绍。
1.2设计内容用金属型覆砂技术克服上述局限性,解决当前所遇到的铸造问题,保证工艺出品率。
即在金属型与铸件外形间覆薄砂层,形成砂型胶。
优点是同时具备金属型和砂型铸造的特点,金属型与熔体不直接接触,冷却速度和金相组织易于控制,同时提高金属型寿命,铸件形状可较复杂。
铸件可保证致密无气孔、缩孔、缩松等缺陷,工艺出口率咼。
2.1设计任务要求名称:制动盘材料:HT220类型:成批生产本铸件属于盘状薄壁件,盘面上的风道利于空气对流,达到散热的冃的。
如下图所示。
采用金属型覆砂工艺,需考虑金属型材料及芯砂材料。
2.2金属型材料选择根据以往金属型设计经验,选择常用的HT200作为金属型材料,参数如下:牌号:HT200标准:GB 9439-88特性:珠光体类型的灰铸铁。
用覆砂铁型铸造工艺生产球铁列车刹车盘

用覆砂铁型铸造工艺生产球铁列车刹车盘摘要:本文对各种铸造球铁刹车盘的工艺进行了介绍,并对覆砂铸铁工艺和粘土砂湿法铸造工艺进行了实验比较。
结果显示,粘土砂湿法铸件球有缩孔缺陷,但是球少、球化率低;覆砂铸铁件球化无缩松缺陷,特点是球多、球化率高,经过大量生产的覆砂铁型工艺,铸件质量稳定。
关键词:覆砂铁型;铸造工艺;球铁;列车刹车盘汽车底盘的重要安全部件是轮毂球墨铸铁铸件。
当前,大部分采用粘土砂湿法制造,这些部位的热接点分散,壁厚不均匀,而且容易出现缩孔倾向或是缩孔,采用覆砂铁型铸造工艺,对球化等级、铸件效益、粒度、密度等铸件显着改进提高了铸件的整体力学性能覆砂铁型生产线也提高了工人的劳动力、强度和工作环境,减少制造过程中的环境污染,提高生产效率,满足绿色铸造要求,取得明显的社会效益和经济效益。
一、覆砂铁型铸造工艺概念覆砂铁型工艺在模具与铁型(砂箱)内腔之间留有6-10m的缝网,在特定温度下注入覆膜砂并固化,将覆膜砂包覆在模具的内表面,获得模具型腔,并教导如何使用这种覆砂铁型铸件。
其最大特点是高速冷却,铰链式刚性强,可细化铸件晶粒,大幅度提高力学性能。
型腔去除极其刚性,铁型代替了传统的砂箱,在铸件的凝固过程中,可以利用石墨化膨胀阶段模具壁的高刚度来实现自补缩,一个过渡层是覆砂层,由于其厚度,可以通过来改变铸件的冷却速度,可以在适当的范围内调整。
提高冷却速度对缩短珠光体片距和细化晶粒有很大的作用。
二、铁型覆砂工艺特点首先,铁型(砂箱)顺应产品形状,中间圆周覆砂,厚度为6~10mm,成本低,用砂量少。
其次,废砂收集后,送专业厂家回收,完全再利用。
无需投资砂处理设备或场地,环保,成本低。
第三,覆膜砂强度高、致密、铸件尺寸精度高、铁型(铸铁)强度和柔韧性高、组织致密、重量轻、加工余量小、铸件自补缩强,工艺良率高,一般无需设置臂口供给。
第四,铁型导热快,薄砂涂层,铸件冷却快,粒度小,无需添加过多的贵重合金,易获得较高的力学性能。
刹车盘铸造工艺规程
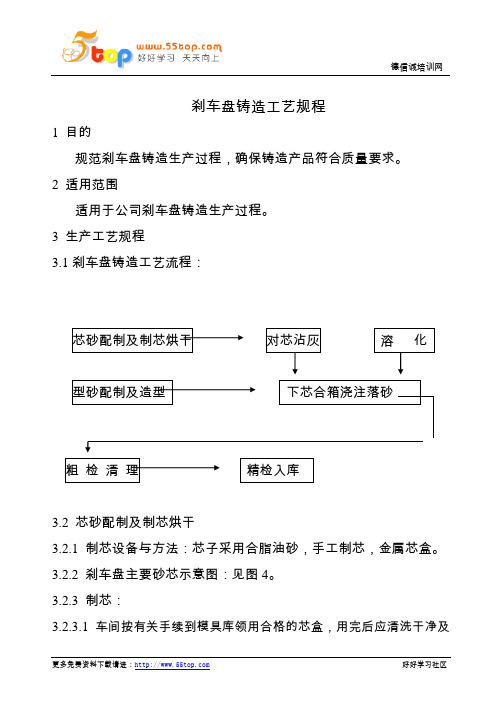
刹车盘铸造工艺规程
1 目的
规范刹车盘铸造生产过程,确保铸造产品符合质量要求。
2 适用范围
适用于公司刹车盘铸造生产过程。
3 生产工艺规程
3.1刹车盘铸造工艺流程:
3.2 芯砂配制及制芯烘干
3.2.1 制芯设备与方法:芯子采用合脂油砂,手工制芯,金属芯盒。
3.2.2 刹车盘主要砂芯示意图:见图4。
3.2.3 制芯:
3.2.3.1 车间按有关手续到模具库领用合格的芯盒,用完后应清洗干净及时送回。
3.2.3.2 油砂混制时,严格按比例混制(芯砂与合脂油按100:3比例混制)。
使用过程中出现争议时,取样送实验室测试其强度和透气性。
3.2.3.3 打芯时,芯盒的筋片不得有刮砂、粘砂现象。
3.2.3.4 刹车盘砂芯上的字要清晰完整,刮出面要用工具刮了压光。
3.2.3.5 砂芯应尽量轻轻在专用工作台上均匀敲出或磕出芯盒。
3.1.3.6 芯头用Φ8mm气孔锥扎透。
(芯盒带有透气锥的除外)
3.1.3.7 检验砂芯,大平面度不得大于0.3mm,厚度尺寸不小于芯盒磨损极限尺寸。
3.1.4 砂芯质量要求:
尺寸准确、形状完整、紧实光洁、无有松动、气眼要畅、砂芯不得有掉砂、粘砂、裂纹的现象。
3.1.5 烘干(烤芯)
3.1.5.1 严格控制芯窑温度和时间。
(芯窑温度和时间的控制温度见下图)
T(
降温
50 50。
- 1、下载文档前请自行甄别文档内容的完整性,平台不提供额外的编辑、内容补充、找答案等附加服务。
- 2、"仅部分预览"的文档,不可在线预览部分如存在完整性等问题,可反馈申请退款(可完整预览的文档不适用该条件!)。
- 3、如文档侵犯您的权益,请联系客服反馈,我们会尽快为您处理(人工客服工作时间:9:00-18:30)。
汽车刹车盘铸件生产工艺、缺陷分析与对策
摘要:本文针对国内刹车盘铸件的生产工艺状况及刹车盘的结构特点,分析了常见铸造缺陷
如气孔、缩松、金相组织不达标等的形成机制,提出了防止的工艺措施和对策。
目前,国内汽车(主要是轿车)刹车盘的出口市场已经形成一定规模,仅就铸件来说,年产量
(出口量)估计在20万吨左右。由于刹车盘出口主要针对的是配件市场,外商定货品种繁杂,而
每个品种生产批量不大。另一方面,刹车盘铸件属薄壁小件,技术要求高,而国内生产出口刹车
盘的企业,大多采用手工造型,粘土砂湿型,冲天炉熔炼铁液,成分变化较大,给生产技术管理和
铸件质量控制带来一定难度,个别厂家铸件废品率居高不下,直接影响企业的经济效益和出口
业务。本文在对刹车盘铸造技术和常见缺陷进行分析的基础上,提出一些可供参考的工艺改
进对策。
1、刹车盘铸件生产技术状况
1、1 铸件结构
刹车盘种类繁多,图1 所示为双层盘片结构。特点是壁薄,盘片及中心处由砂芯形成。不
同种类刹车盘,在盘径、盘片厚度及两片间隙尺寸上存在差异,盘毂的厚度和高度也各不相同。
单层盘片的刹车盘结构比较简单。铸件重量多为6~18kg。
1、2 技术要求
(1)铸件外轮廓全部加工,精加工后不得有任何缩松、气孔、砂眼等铸造缺陷。
(2)金相组织为中等片状A型石墨,D、E型过冷石墨<15%,基体中珠光体>95%,碳化物量<1%,
组织均匀,断面敏感性小(特别是硬度差小)。
(3)力学性能:σb ≥250MPa,HB180~240,相当于国际HT250牌号。
(4)有些外商对铸件的化学成分也作要求。
1、3 生产工艺
。。。。。。
2、气孔的形成及防止
。。。。。。
3、缩松的形成及防止
。。。。。。
4、过冷石墨超标,组织不均匀
。。。。。。
5、砂眼缺陷及防止
个别厂家铸件砂眼缺陷较多,调研分析认为主要原因是型砂湿强度低。由于缺少型砂检测
仪器,凭经验掌握,粘土或膨润土、水等不定量,型砂的性能(水分、含泥量、透气性、湿强度、
紧实率等)不稳定或不能保证。而型砂的性能是控制刹车盘铸件的重要措施之一,这一点应该
引起生产厂家的重视并设法改进完善。在只混制面砂的情况下,控制混砂质量更为重要。另
外,采用手工模板造型时,浇注系统处的紧实度和均匀性也应得到保证,否则可能因冲砂、掉砂
而造成砂眼缺陷。
综上所述,针对不同铸造缺陷,采取相应工艺措施进行改进,有几点带有共性的地方:(1)大
流量低流速,高温快浇;(2)提高直浇道的充填流动和补缩压头;(3)铁液分散引入,既可避免局部
热量集中,又可缩短铁液流程,防止局部(流头对接处)温度过低;(4)小件应强调补缩。