第8讲汽车典型零件制造工艺
汽车及其零件制造中常用制造工艺
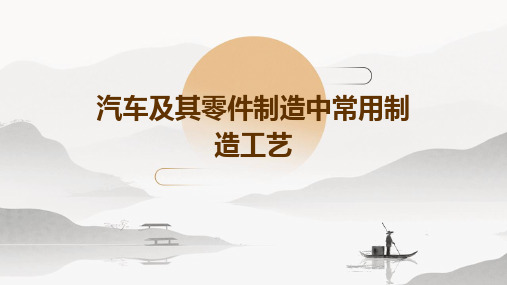
熔模铸造
总结词
精度高,表面质量好
详细描述
熔模铸造是一种精密铸造方法,通过使用易熔材料制作出与最终铸件形状相同的 模型,然后将其熔化,再倒入金属熔液中。由于其高精度和良好的表面质量,熔 模铸造广泛应用于制造高精度、高质量的铸件。
金属型铸造
总结词
生产效率高,强度高
详细描述
金属型铸造是一种使用金属模具进行铸造的方法,与砂型铸造相比,金属型铸造的铸件具有更高的强度和更长的 使用寿命。同时,由于金属型模具的快速冷却效果,金属型铸造的生产效率也较高,适用于大规模生产。
VS
详细描述
气体保护焊具有焊接速度快、质量稳定、 变形小等优点,广泛应用于汽车制造业中 。常用的保护气体包括二氧化碳、氩气等 。该工艺适用于各种金属材料的焊接,如 碳钢、不锈钢、铝等。
激光焊接
总结词
详细描述
激光焊接是一种高精度、高质量的焊接工艺, 通过高能激光束聚焦在材料表面,实现快速 熔化与连接。
铣削加工
总结词
铣削加工是一种利用铣刀对工件进行切削加 工的方法,主要用于加工平面、沟槽、齿形 等复杂形状。
详细描述
铣削加工通过高速旋转的铣刀对工件进行切 削,能够加工出高精度、高效率的复杂零件 。在汽车制造中,铣削加工广泛应用于发动
机缸体、曲轴等关键部件的制造。
磨削加工
总结词
磨削加工是一种利用磨料对工件进行研磨和抛光的工 艺,主要用于提高工件的表面质量和精度。
要点二
详细描述
电镀广泛应用于汽车制造中,主要用于镀锌、镀铬、镀镍 等。电镀能够提高零件的耐腐蚀性和耐磨性,延长使用寿 命。同时,电镀还可以增加零件的美观度,提升汽车的整 体质感。
喷涂
总结词
汽车及其零件制造工艺基础讲课文档
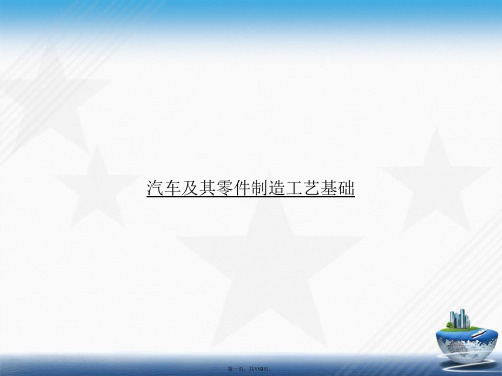
C:3.30~3.50, Si:1.80~2.00, Mn:0.6~0.8, Cr:0.2~0.4 C:3.30~3.60, Si:1.40~1.90, Mn:0.6~0.9, P<0.2, S<0.2 C:3.30~3.50, Si:1.80~2.00, Mn:0.6~0.8, Cr:0.1~0.3 C:3.65~3.80, Si:2.40~2.60, Mn:0.2~0.3, Mg:0.04~0.05
第十五页,共119页。
二、砂型铸造的造型工艺
砂型铸造工艺过程
第十六页,共119页。
二、砂型铸造的造型工艺
(二)造型材料和造型方法 造型材料 :制造铸型用的材料,型砂和芯砂 1.对型砂和芯砂性能的要求
(1) 可塑性。 (2) 强度。
(3) 耐火性。 (4) 透气性。 (5) 退让性。
第十七页,共119页。
(二)造型材料和造型方法
造型方法
1.造型
造型就是用型砂和模型制造铸型的过程。造型 方法分手工造型和机器造型两大类。
手工造型主要用于单件和小批生产,也用于形状复 杂和大型铸件的生产。在大量生产时,主要采用机器 造型。
机器造型是指用机器完成全部或至少完成紧砂 操作的造型过程。
第二十一页,共119页。
(二)造型材料和造型方法
第十页,共119页。
1 铸造工艺概要
合金的铸造性能
3.偏析及吸气性:在铸件中出现成分不匀的现象为偏析,合金在熔炼和浇
注时吸收气体的性 能称为合金的吸气性
偏析使铸件性能不均匀,严重时会使铸件报废。在合金 液冷凝过程中,随着温度降低会析出过饱和气体。若这些气 体来不及从合金液中逸出,将在铸件中形成气孔、针孔或非 金属夹杂物,从而降低了铸件的力学性能和致密性。
汽车典型零件制造技术
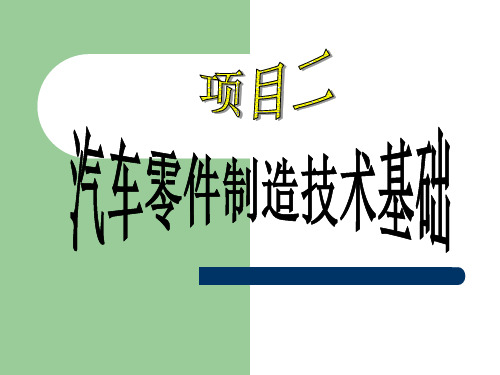
7
粗车-半精车一粗磨-精磨超精加工
IT5
0.12-0.l
主要用于 淬火钢,也 可用于未 淬火钢,但 不宜加工 有色金属
Hale Waihona Puke 主要用于8粗车-半精车-精车-精细车 (金刚石车)
IT6~7
0. 025~0.4
要求较高 的有色金
属加工
9
粗车-半精车-粗磨-精磨超精磨(或镜面磨)
IT5以上
0.006~0.025
极高精度
12.5~50
2 粗车一半精车
IT8~IT10
3 粗车一半精车—精车
4
粗车-半精车-精车-滚 压(或抛光)
IT7~IT8 IT7~IT8
3.2~6.3 0.8~1.6 0.025~0.2
适用于淬 火钢以外 的各种金
属
5 粗车一半精车-磨削
IT7~IT8 0.4~0.8
6 粗车一半精车-粗磨-精磨 IT6~IT7 0.1~0.4
工艺尺寸链的特征
尺寸链由一个自然形成的尺寸与若干个直接得到的尺寸所组成。 尺寸链一定是封闭的,且各尺寸按一定的顺序首尾相接。
尺寸链的组成
组成尺寸链的各个尺寸称为尺寸链的环
分为封闭环和组成环 封闭环 在加工(或测量)过程中最后自然形成的环称为封闭环 每个尺寸链必须有且仅能有一个封闭环。 组成环 在加工(或测量)过程中直接得到的环称为组成环。 按其对封闭环的影响,可分为增环和减环
大批大量生产的产品,可采用专用设各和工艺装备,如多刀、多轴机床或自动机 床等,将工序集中,也可将工序分散后组织流水线生产。但对一些结构简单 的产品,如轴承和刚性较差、精度较高的精密零件,则工序应适当分散。
设备与工装选择
机床的选择
汽车零部件制造工艺优化指南

汽车零部件制造工艺优化指南第1章汽车零部件制造工艺概述 (4)1.1 汽车零部件分类与工艺特点 (4)1.2 汽车零部件制造工艺发展现状与趋势 (4)第2章零部件铸造工艺优化 (5)2.1 砂型铸造工艺优化 (5)2.1.1 砂型材料选择与配比 (5)2.1.2 砂型制备工艺 (5)2.1.3 熔炼与浇注工艺 (5)2.1.4 铸件冷却与收缩控制 (5)2.2 低压铸造工艺优化 (5)2.2.1 低压铸造参数设定 (5)2.2.2 模具设计与优化 (5)2.2.3 浇注系统设计 (6)2.2.4 铸件后处理 (6)2.3 高压铸造工艺优化 (6)2.3.1 高压铸造参数优化 (6)2.3.2 模具设计与维护 (6)2.3.3 充型与冷却控制 (6)2.3.4 铸件缺陷预防与控制 (6)第3章零部件锻造工艺优化 (6)3.1 热模锻工艺优化 (6)3.1.1 锻造温度控制 (6)3.1.2 模具设计优化 (6)3.1.3 锻造参数优化 (7)3.1.4 锻造缺陷控制 (7)3.2 冷模锻工艺优化 (7)3.2.1 材料选择与预处理 (7)3.2.2 锻造工艺参数优化 (7)3.2.3 模具设计及冷却 (7)3.2.4 缺陷控制与检测 (7)3.3 精密锻造工艺优化 (7)3.3.1 锻造工艺参数设置 (7)3.3.2 模具设计与制造 (8)3.3.3 生产过程控制 (8)3.3.4 优化后处理工艺 (8)第4章零部件焊接工艺优化 (8)4.1 气体保护焊工艺优化 (8)4.1.1 焊接参数选择 (8)4.1.2 焊接材料选用 (8)4.1.3 焊接过程控制 (8)4.2 激光焊接工艺优化 (8)4.2.2 激光焊接设备选择与维护 (8)4.2.3 激光焊接过程监控与调整 (8)4.3 焊接质量检测与控制 (9)4.3.1 焊接缺陷检测 (9)4.3.2 焊接接头功能检测 (9)4.3.3 焊接过程质量控制 (9)4.3.4 焊接质量改进 (9)第5章零部件机加工工艺优化 (9)5.1 车削工艺优化 (9)5.1.1 选择合适的切削速度 (9)5.1.2 优化刀具参数 (9)5.1.3 选用合适的切削液 (9)5.1.4 优化加工路径 (9)5.2 铣削工艺优化 (9)5.2.1 选择合适的铣削方式 (10)5.2.2 优化铣削参数 (10)5.2.3 选用高品质刀具 (10)5.2.4 优化切削液应用 (10)5.3 钻削工艺优化 (10)5.3.1 钻头选择与优化 (10)5.3.2 优化钻削参数 (10)5.3.3 钻削顺序及路径优化 (10)5.3.4 预防钻头断裂 (10)5.4 加工中心工艺优化 (10)5.4.1 优化编程策略 (10)5.4.2 优化装夹方式 (10)5.4.3 多工序集成 (10)5.4.4 选用高精度刀具 (11)第6章零部件热处理工艺优化 (11)6.1 淬火工艺优化 (11)6.1.1 淬火介质选择 (11)6.1.2 淬火温度控制 (11)6.1.3 淬火速率优化 (11)6.2 回火工艺优化 (11)6.2.1 回火温度选择 (11)6.2.2 回火时间控制 (11)6.2.3 多次回火工艺应用 (11)6.3 渗碳工艺优化 (11)6.3.1 渗碳介质选择 (11)6.3.2 渗碳温度和时间控制 (11)6.3.3 渗碳后处理工艺 (12)6.3.4 渗碳工艺参数优化 (12)第7章零部件表面处理工艺优化 (12)7.1.1 喷涂材料选择 (12)7.1.2 喷涂设备与参数设置 (12)7.1.3 喷涂环境控制 (12)7.2 电镀工艺优化 (12)7.2.1 电镀液配方优化 (12)7.2.2 电镀工艺参数优化 (12)7.2.3 电镀设备与辅助系统优化 (13)7.3 热喷涂工艺优化 (13)7.3.1 热喷涂材料选择 (13)7.3.2 热喷涂工艺参数优化 (13)7.3.3 热喷涂设备与工艺流程优化 (13)第8章零部件装配工艺优化 (13)8.1 装配工艺流程优化 (13)8.1.1 流程分析与改进 (13)8.1.2 精简装配工序 (13)8.1.3 优化装配顺序 (13)8.1.4 搭建标准化作业指导体系 (13)8.2 自动化装配工艺优化 (14)8.2.1 自动化装配设备选型与布局 (14)8.2.2 应用与编程 (14)8.2.3 智能化装配系统 (14)8.2.4 信息化管理 (14)8.3 装配质量检测与控制 (14)8.3.1 质量检测方法 (14)8.3.2 检测数据统计分析 (14)8.3.3 质量控制策略 (14)8.3.4 持续改进 (14)第9章零部件制造过程质量控制 (14)9.1 质量管理体系建立与实施 (14)9.1.1 质量手册与程序文件编制 (14)9.1.2 质量管理体系文件管理 (15)9.1.3 内部审核与管控行动 (15)9.1.4 持续改进 (15)9.2 制造过程质量控制方法 (15)9.2.1 过程控制参数优化 (15)9.2.2 检验与测试 (15)9.2.3 SPC技术应用 (15)9.2.4 防错技术应用 (15)9.3 质量问题分析与改进 (15)9.3.1 质量问题识别与追溯 (15)9.3.2 原因分析与纠正措施 (15)9.3.3 预防措施制定与实施 (15)9.3.4 改进效果评估 (16)第10章零部件制造工艺发展趋势与展望 (16)10.1 绿色制造工艺发展 (16)10.2 智能制造工艺发展 (16)10.3 高功能材料在零部件制造中的应用前景 (16)10.4 跨界融合创新工艺摸索与实践 (17)第1章汽车零部件制造工艺概述1.1 汽车零部件分类与工艺特点汽车零部件作为汽车制造的核心组成部分,其质量与功能直接关系到整车的质量和功能。
汽车零件加工工艺
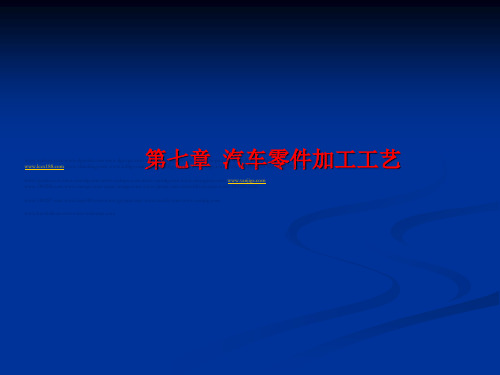
锤上模锻是将上模固定在模锻锤头上,下模紧固在模座 上,通过上模对置于下模的坯料施以直接打击来获得锻件 的模锻方法。图7-14为连杆的模锻过程。
图7-14 连杆的模锻
(二)胎模锻造 在自由锻设备上使用可移动胎模具成形制得模锻件的方 法,称为胎模锻造。
Hale Waihona Puke 7.2.4 板料冲压图7-15 冲压件
7.1 铸造
铸造是指将液体金属浇注到具有与零件形状相应的铸型 型腔内,待其冷却凝固后获得铸件的方法,其实质是利 用熔融金属的流动性能实现材料成形。一般情况下,铸 件通常是毛坯,需经过切削加工才能成为零件,但对要 求不高或精密铸造方法生产出来的铸件,也可以不经切 削加工而直接使用。
7.1.1 铸造合金的性能特点
7.2.2 自由锻造
a)冲一面 b) 冲另一面 c) 冲孔完成 图7-7 双面冲孔示意图
a) 准备冲孔 b) 冲孔完成 图7-8 单面冲空示意图
a)完全镦粗b)端面镦粗c)中间镦粗d)水压机 用球面板镦粗 图7-9 镦粗
a) 用大锤打弯b) 用吊车打弯c) 板料弯曲d) 角尺弯曲 图7-10 弯曲
7.1.4 铸造在汽车制造中的应用
在汽车制造过程中,采用铸铁制成毛坯的零件很多,约 占全车重量10%左右,如气缸体、变速器箱体、转向器 壳体、后桥壳体、制动鼓、各种支架等。制造铸铁件通 常采用砂型。砂型的原料以砂子为主,并与粘结剂、水 等混合而成。砂型材料必须具有一定的粘合强度,以便 被塑成所需的形状并能抵御高温铁水的冲刷而不会崩塌。 为了在砂型内塑成与铸件形状相符的空腔,必须先用木 材制成模型,称为木模。炽热的铁水冷却后体积会缩小, 因此,木模的尺寸需要在铸件原尺寸的基础上按收缩率 加大,需要切削加工的表面相应加厚。空心的铸件需要 制成砂芯子和相应的芯子木模(芯盒)。有了木模,就可 以翻制空腔砂型(铸造也称为“翻砂”)。在制造砂型时, 要考虑上下砂箱怎样分开才能把木模取出,还要考虑铁 水从什么地方流入,怎样灌满空腔以便得到优质的铸件。 砂型制成后,就可以浇注,也就是将铁水灌入砂型的空 腔中。浇注时,铁水温度在1250—1350℃,熔炼时温度 更高。
典型的汽车零件的加工工艺流程

铸造
铸造是将熔化的金属浇灌入铸型空腔中,冷却凝固后而获得产品的生产方法.在汽车制造过程中,采用铸铁制成毛坯的零件很多,约占全车重量10%左右,如气缸体、变速器箱体、转向器壳体、后桥壳体、制动鼓、各种支架等。制造铸铁件通常采用砂型.砂型的原料以砂子为主,并与粘结剂、水等混合而成。砂型材料必须具有一定的粘合强度,以便被塑成所需的形状并能抵御高温铁水的冲刷而不会崩塌。为了在砂型内塑成与铸件形状相符的空腔,必须先用木材制成模型,称为木模。炽热的铁水冷却后体积会缩小,因此,木模的尺寸需要在铸件原尺寸的基础上按收缩率加大,需要切削加工的表面相应加厚。空心的铸件需要制成砂芯子和相应的芯子木模(芯盒).有了木模,就可以翻制空腔砂型(铸造也称为“翻砂”)。在制造砂型时,要考虑上下砂箱怎样分开才能把木模取出,还要考虑铁水从什么地方流入,怎样灌满空腔以便得到优质的铸件。砂型制成后,就可以浇注,也就是将铁水灌入砂型的空腔中。浇注时,铁水温度在1250—1350度,熔炼时温度更高.
(2)因为大、小头孔中心距的变化将会使气缸的压缩比发生变化,从而影响发动机的效率,因此要求两孔中心距公差等级为IT9。大、小头孔中心线在两个相互垂直方向上的平行度误差会使活塞在气缸中倾斜,致使气缸壁唐攒不均匀,缩短发动机的使用寿命,同时也使曲轴的连杆轴颈磨损加剧,因此也对其平行度公差提出了要求。
(3)连杆大头孔两端面对大头孔中心线的垂直度误差过大,将加剧连杆大头两端面与曲轴连杆轴颈两端面之间的磨损,甚至引起烧伤,所以必须对其提出要求.
《典型汽车零件的机械加工工艺》讲解教学课件
第五章
典型汽车零件的机械加工工艺
§5-1 齿轮制造工艺 §5-2 连杆制造工艺 §5-3 曲轴制造工艺
讲解教学课件
§5-1 齿轮制造工艺
一、齿轮的结构特点
汽车齿轮按照其结构特点分为五类: Ⅰ类 单联齿轮,孔的长径比L/D>1 。 Ⅱ类 多联齿轮,孔的长径比L/D>1 。
这两种齿轮亦称为筒形齿轮,内孔为光孔、键 槽孔或花键孔。
§5-1 齿轮制造工艺
三、齿轮的主要技术要求
(3)端面圆跳动。带孔 (4)齿轮齿顶圆公差。当
齿轮齿坯轮毂端面是切 齿轮齿顶圆作为加工、测
齿时的定位基准,端面 量的基准时,其尺寸公差
对内孔的跳动量对齿轮 要求比较严,一般为IT8。
的加工精度有很大影响。 不作为加工、测量的基准
对于6~7级精度的汽车齿 时,其公差一般为IT11。
讲解教学课件
§5-1 齿轮制造工艺 五、齿轮机械加工的定位基准
加工孔长径比L/D﹥1的单联或多联齿轮时,应以孔 作为主要定位基面。为了消除孔和心轴间的间隙的影 响,精车齿坯时,常用过盈心轴或小锥度心轴。
预加工齿面时,可采用能自动定心的可胀心轴或分 组的小间隙心轴装夹。
齿轮孔长径比L/D>1齿轮的定位
汽车第一速及倒档齿轮锻件毛坯图
模锻齿轮毛坯材料纤维排列
§5-1 齿轮制造工艺
四、齿轮的材料和毛坯
(3)齿轮热处理。 齿轮毛坯必须进行初步热处理,常采用正火或等
温退火,以消除内应力,改善切削加工性。 齿轮齿面热处理: 对中碳钢或中碳合金钢常采用高频淬火和低温回
火; 对低碳合金渗碳钢采用渗碳淬火热处理。
轮规定为0.011~0.022mm。 (5)齿轮的热处理要求。
汽车典型零件的制造工艺
(2)加工长径比L/D < 1 的齿圈或盘形齿轮 当齿轮孔的长径比L/D < 1 时,如图7-1-10a
所示,应以端面作为主要的定位基准,限制3 个自 由度,内孔限制2 个自由度。为使作为定位基准的 孔和端面具有较高的垂直度,在加工这两个表面时, 可装在三爪自定心卡盘内,在一次安装中车出,如 图7-1-10b 所示。
25 模 块 七 汽 车 典 型 零 件 的 制 造 工 艺
课题一 汽车齿轮的制造工艺
1.齿轮的切削加工 1)滚齿。滚齿是应用最广的齿轮
加工方法,可加工渐开线齿轮、圆弧齿 轮、摆线齿轮、链轮、棘轮、蜗轮和包 络蜗杆。滚齿加工的过程相当于一对交 错轴斜齿轮互相啮合运动的过程,如图 7-1-13 所示。
一、发动机连杆的结构特点 二、发动机连杆的结构工艺性分析 三、发动机连杆的机械加工工艺过程 四、发动机连杆主要表面的加工方法
37 模 块 七 汽 车 典 型 零 件 的 制 造 工 艺
课题二 发动机连杆的制造工艺
一、发动机连杆的结构特点
汽车发动机连杆结构简 图如图7-2-1 所示,连杆由 大头、小头和杆身等部分组 成。
3 模块七 汽车典型零件的制造工艺
课题一 汽车齿轮的制造工艺
4 模块七 汽车典型零件的制造工艺
课题一 汽车齿轮的制造工艺
一、齿轮的结构特点 二、齿轮结构的工艺性分析 三、齿轮的机械加工工艺过程 四、齿轮的加工方法 五、汽车典型齿轮的机械加工工艺过程
5 模块七 汽车典型零件的制造工艺
课题一 汽车齿轮的制造工艺
一、齿轮的结构特点
汽车中的各种齿轮,按照结构工艺特点可分为五类,如图7-1-2 所 示。
1.单联齿轮:如图7-1-2a 所示,孔的长径比L/D > 1。 2.多联齿轮:如图7-1-2b 所示,孔的长径比L/D > 1。 3.盘形齿轮:如图7-1-2c 所示,具有轮毂,孔的长径比L/D < 1。 4.齿圈:如图7-1-2d 所示,具有轮毂,孔的长径比L/D < 1。 5.轴齿轮:如图7-1-2e 所示。
汽车上一些零件的加工工艺
汽车上一些零件的加工工艺
汽车上的零部件是汽车制造中至关重要的一环,它们的加工工艺直接影响着汽车的性能和品质。
以下是汽车上一些常见零部件的加工工艺:
1. 发动机缸体加工工艺:发动机缸体是发动机的重要组成部分,它需要经过多道工序才能完成加工。
首先是精密铸造,然后通过数控机床进行精细加工、车削、铣削等工序,最后进行喷漆等表面处理。
2. 制动系统盘片加工工艺:制动系统盘片的加工工艺主要包括冷却孔加工、车削、磨床磨削等工序。
这些工序可以提高盘片的散热性和耐磨性,并确保盘片的平整度和圆度。
3. 悬挂系统弹簧加工工艺:悬挂系统弹簧的加工工艺包括钢丝拉拔、成形、热处理等多道工序。
这些工序可以确保弹簧的强度、弹性以及稳定性。
4. 变速器齿轮加工工艺:变速器齿轮的加工工艺是一项复杂的工程,包括铸造、车削、磨削、齿轮加热处理等多个环节。
这些工序可以确保齿轮的强度、耐磨性等性能指标。
总之,汽车零部件的加工工艺涉及到多个工序和技术领域,需要高超的技术和严格的质量控制,以确保汽车的品质和性能。
- 1 -。
汽车零部件制造工艺
汽车零部件制造工艺专业名称:汽车制造与装配技术课程学分: 4 总学时: 72课程特性:专业核心课程一、课程定位为合理定位课程的内容,我们对广汽本田、广汽丰田、东风日产、东风本田发动机等整车制造企业和汽车零部件制造企业进行了调研,通过与一线工人、企业人事部门负责人、企业专家的访谈,分析了汽车制造与装配技术专业在相关企业的人才需求情况,对本专业在各类企业中的人才岗位及其相关岗位技能要求进行了归纳。
特别地,对于本课程在汽车制造与装配技术专业所涉及的汽车制造企业类型、岗位及其技能要求进行了总结(见表1),并确定了本课程的培养方向。
该课程主要围绕汽车零部件机械加工工艺规程的编制和汽车零部件制造专用夹具设计两方面内容,是汽车制造与装配技术专业的核心课程。
通过本课程的学习,培养学生具备中等复杂程度的汽车零部件的机械加工工艺规程的编制能力,使学生掌握机械加工工艺规程编制的基本知识和专用机床夹具设计的基本知识。
同时可以通过系统的专业基础和专业课的学习具备一定的基础理论,奠定持续发展基础,使得在实际工作中能够发现问题、分析问题、解决问题,同时具备团队协作与他人沟通交流能力和工作责任感。
表1 汽车制造与装配技术专业人才岗位技能要求本课程与前、后续课程密切相联,是对前期课程的深入、是后续课程的铺垫,体现了汽车零部件制造的基本生产过程。
二、课程教学设计理念和思路此部分请进一步提炼、精简课程教学设计以汽车零部件制造企业的生产准备技术人员和工艺人员的岗位技能为依托,结合本人在汽车零部件制造企业多年的实践,课程内容按理论实践一体化编排,设置两个最能体现生产准备技术人员和工艺人员的岗位技能的项目引领学生完成该岗位的典型任务,经历完整的工作过程。
在教学过程中,体现如下理念和思路:1.基于工作过程导向的课程设计对汽车零部件制造企业的生产技术准备技术人员和工艺人员岗位中所涉及的相关技能及工作过程进行分析,归纳出汽车拨叉零件的专用夹具设计、汽车齿轮零件的机械加工工艺规程的编制、活塞和活塞销的装配等典型工作任务和工作过程,以此作为课程的学习项目。
- 1、下载文档前请自行甄别文档内容的完整性,平台不提供额外的编辑、内容补充、找答案等附加服务。
- 2、"仅部分预览"的文档,不可在线预览部分如存在完整性等问题,可反馈申请退款(可完整预览的文档不适用该条件!)。
- 3、如文档侵犯您的权益,请联系客服反馈,我们会尽快为您处理(人工客服工作时间:9:00-18:30)。
第8讲汽车典型零件制造工艺
•第八讲 汽车典型零件制造工艺
•§1.制定工艺的基本知识
• 一、机械加工工艺规程
• 1. 机械加工工艺规程 • ◇ 概念 • 机械加工工艺规程是规定零件制造工艺过程 和操作方法 的工艺文件。 • 是指导工人操作和生产、工艺管理的各种技术规范。 • ◇ 主要的工艺文件 • a. 工艺过程卡片(也称工艺路线卡) • b. 工序卡片(也称工序卡) • c. 调整卡片 • d. 检验工序卡
PPT文档演模板
•另外,去毛刺、热处理、清洗和检验等工序在主要工序确 定之后,可根据需要在各阶段穿插进行。最后形成一个完整 的工艺路线。
第8讲汽车典型零件制造工艺
PPT文档演模板
•第八讲 汽车典型零件制造工艺
•六、检验工序安排的原则 • ◇ 在关键表面加工的工序之后; • ◇ 粗、精加工之间,检验工序尺寸和加工余量; • ◇ 特殊的检验项目:如焊接后的磁力探伤,动平衡、
•◆ 大批量生产:
• ⑴ 钻-拉-多刀方案
•
此种加工方法先加工好孔(常采用钻或扩、拉孔),
•
以孔定位加工外圆和端面。
第8讲汽车典型零件制造工艺
•第八讲 汽车典型零件制造工艺
• 3. 齿轮坯的加工
• ◇ 带孔齿轮的机械加工
• ◆ 单件小批生产
•
一般在普通车
•
床上进行。
• ◆ 产量较大时
•
在六角车床上
•
进行。(也称转塔
•
车床)
•
此方案生产效率
•
较低,适用中批量
•
以下。
PPT文档演模板
第8讲汽车典型零件制造工艺
•第八讲 汽车典型零件制造工艺
PPT文档演模板
第8讲汽车典型零件制造工艺
•第八讲汽车典型零件制造工艺
PPT文档演模板
第8讲汽车典型零件制造工艺
•第八讲 汽车典型零件制造工艺
PPT文档演模板
第8讲汽车典型零件制造工艺
•第八讲 汽车典型零件制造工艺
PPT文档演模板
第8讲汽车典型零件制造工艺
•第八讲 汽车典型零件制造工艺
•二、制订加工工艺规程时必须具备的原始资料 • 1. 零件图样和必要的产品或零部件(总成)装配图。
PPT文档演模板
第8讲汽车典型零件制造工艺
•第八讲 汽车典型零件制造工艺
•一、齿轮制造工艺
•1. 齿轮的结构特点及工艺性分析
• 汽车、拖拉机中常用的齿轮,按照结构的工艺特点可分为:
• ◇ 单联齿轮(长径比:L/D>1)
• ◇ 多联齿轮(长径比:L/D>1)
• ◇ 盘形齿轮 (具有轮毂,长径比:L/D < 1)
• ◇ 齿圈 (具有轮毂,长径比:L/D < 1)
• ◇ 轴齿轮
•
•
齿轮的结构直接影响齿面加工方法的选择,也影响加 工工艺
• 过程的安排。
PPT文档演模板
第8讲汽车典型零件制造工艺
•第八讲 汽车典型零件制造工艺
PPT文档演模板
•2. 齿轮的材料和毛坯
• ◇ 常用材料
•
汽车、拖拉机中的传动齿轮,常用的材料有:
•四、工序的集中与分散
•1. 工序集中:在一台机床上完成较多的表面加工。
•优点:
•减少装夹次数,便于保证位置精度;
•便于采用高效机床,极大地提高加工效率;
•减少了工序数量、设备数量、操作工人和工作场地。
•缺点:
•机床结构复杂,同时工作的刀具数增加,降低了工
作可靠性;
• 调整维修不便。
•应用:多轴钻孔、多轴镗孔。
• 2.选择毛坯 • 3.拟定工艺路线 • 4.确定各工序所采用的设备、工艺装备 • 5.确定各工序的加工余量,计算工序尺寸及其公差 • 6.确定各工序的切削用量和时间定额 • 7.确定各主要工序的技术检验要求及检验方法 • 8.填写工艺文件
PPT文档演模板
第8讲汽车典型零件制造工艺
•第八讲 汽车典型零件制造工艺
• 2. 工序分散:是和工序集中相对的。
PPT文档演模板
第8讲汽车典型零件制造工艺
•第八讲 汽车典型零件制造工艺
•五、工序顺序安排原则 • 1. 精基准面的加工:基准先行原则;
• 2. 主要表面粗加工(例:箱体孔、羊角孔等一般都要先 • 粗加工孔) • 3. 主要表面半精加工和次要表面加工(如槽、孔的加工) • 4. 精加工(保证精度和Ra值) • 5. 必要时光整加工(主要Ra↓值)
• 渗漏等,一般在精加工之前进行;
• ◇ 热处理之前; • ◇ 全部工序完成之后(完工检验、入库)。
• 按照质量管理的要求,检验方式规定:
• 首先自检,然后互检,最后检验人员终检。
第8讲汽车典型零件制造工艺
•第八讲 汽车典型零件制造工艺
•§2 汽车典型零件制造工艺
•一、齿轮制造工艺 •二、连杆制造工艺 •三、箱体制造工艺 •四、曲轴制造工艺 • 五、转向节制造工艺
• 20CrMnTi 20CrNiMo 20CrMo 20MnVB 40Cr 40MnB
• 45号钢等。
• ◇ 毛坯
• ◆ 中小批量生产时
•
在空气锤上采用胎模锻造。
• ◆ 大量生产时
•
一般均采用模锻。
• ◆ 当孔径大于25mm,长度不大于孔径的两倍时,也可锻
•
出(卧式锻造机上可锻造长径比大于5的深孔)。
• 2. 产品的生产纲领(即年产量及品种)。 • 3. 现有的生产条件等。 • 有了原始资料后,常常要依据生产任务,初步确定生 产类型、投产批量、工艺手段等,规定一个工艺原则, 供具体制定工艺的人员遵循和参考。
PPT文档演模板
第8讲汽车典型零件制造工艺
•第八讲 汽车典型零件制造工艺
•三、制订加工工艺规程的步骤 • 1.分析研究图纸
第8讲汽车典型零件制造工艺
•第八讲 汽车典型零件制造工艺
PPT文档演模板
•◆ 钢材经模锻后,内部纤维组织对称于轴线,可提高材料 • 的使用强度。 •◆ 为减小齿轮在渗碳和淬火时的热变形,要求毛坯的金相 • 组织和晶粒大小均匀。所以,锻件毛坯一定要经过初步 • 热处理(正火或退火),消除内应力并提高切削性能。 •◆ 精密锻造、粉末冶金锻造(即粉末冶金精密锻造)的齿 • 轮毛坯,在我国汽车、拖拉机工业中也得到了一定的应 • 用。因为齿面不需要机械加工,降低了生产成本、节约 • 了大量原材料,也大大提高了劳动生产率。 •◆ 粉末冶金锻造的齿轮,不需很多的机械加工,与原工艺 • 比较,生产率提高近三倍,材料利用率提高一倍以上。 • 但粉末材料成本高,设备投资大,推广应用受到限制。