全国大学生数学建模竞赛2018年B题智能RG的动态调度策略及优秀论文精选
智能RGV的动态调度策略

智能 RGV 的动态调度策略摘要:针对智能 RGV 系统一道工序的物料加工作业情况,首先,RGV根据距离就近原则选择下一操作的CNC。
在 RGV 对所有 CNC 完成一次上料操作后,不断进行上下料、清洗作业的循环操作。
考虑到物料加工时间,我们选择离 RGV 最近的 CNC 作为下一个上料对象。
模型反复按顺序进行操作,直到时间达到 8 小时。
代入各组数据计算,得到相应的RGV动态调度模型和相应的求解算法。
关键词:RGV动态调度全局搜索工作时间均衡度一、背景介绍一个智能加工系统的示意,由 8 台计算机数控机床、1 辆轨道式自动引导车、1 条 RGV 直线轨道、1 条上料传送带、1 条下料传送带等附属设备组成。
RGV 是一种无人驾驶、能在固定轨道上自由运行的智能车。
它根据指令能自动控制移动方向和距离,并自带一个机械手臂、两只机械手爪和物料清洗槽,能够完成上下料及清洗物料等作业任务。
1.任务复述与情况分析任务复述:对一般问题进行研究,给出 RGV 动态调度模型和相应的求解算法。
情况分析:要求对只加工一道工序的情况进行一般性研究。
以 8 小时内加工出最多物料为目标,我们给出了以下一道工序 RGV 动态调度模型。
考虑到RGV 移动的时间远小于物料加工时间,我们选择离 RGV 最近的 CNC 作为下一个上料对象。
模型中反复按顺序进行以下操作,直到时间达到 8 小时:1.等待直到 RGV 空闲且至少一个 CNC 空闲2.使 RGV 移动到距 RGV 当前位置最近的空闲 CNC 处3.对该 CNC 进行上下料操作,若有熟料则还需进行清洗作业三、问题求解针对于智能加工系统来说每班次工作共存在两种状态:启动阶段和稳定阶段。
启动阶段:即开始有 CNC 处于空闲状态的阶段,当所有 CNC 都有处于加工过程时,这一阶段结束,在这一阶段,RGV 不存在等待和清洗操作,CNC 只有空闲和正在加工中两个状态。
稳定阶段:即所有 CNC 都开始工作后的情况,在这一阶段 CNC 有正在加工中,成熟等待,正在上下料三个状态;RGV 有等待、移动、上下料、清洗作业四种状态。
【全国大学生数学建模竞赛获奖优秀论文作品学习借鉴】全国大学生数学建模竞赛2009年赛题B题

2009高教社杯全国大学生数学建模竞赛题目(请先阅读“全国大学生数学建模竞赛论文格式规范”)B题眼科病床的合理安排医院就医排队是大家都非常熟悉的现象,它以这样或那样的形式出现在我们面前,例如,患者到门诊就诊、到收费处划价、到药房取药、到注射室打针、等待住院等,往往需要排队等待接受某种服务。
我们考虑某医院眼科病床的合理安排的数学建模问题。
该医院眼科门诊每天开放,住院部共有病床79张。
该医院眼科手术主要分四大类:白内障、视网膜疾病、青光眼和外伤。
附录中给出了2008年7月13日至2008年9月11日这段时间里各类病人的情况。
白内障手术较简单,而且没有急症。
目前该院是每周一、三做白内障手术,此类病人的术前准备时间只需1、2天。
做两只眼的病人比做一只眼的要多一些,大约占到60%。
如果要做双眼是周一先做一只,周三再做另一只。
外伤疾病通常属于急症,病床有空时立即安排住院,住院后第二天便会安排手术。
其他眼科疾病比较复杂,有各种不同情况,但大致住院以后2-3天内就可以接受手术,主要是术后的观察时间较长。
这类疾病手术时间可根据需要安排,一般不安排在周一、周三。
由于急症数量较少,建模时这些眼科疾病可不考虑急症。
该医院眼科手术条件比较充分,在考虑病床安排时可不考虑手术条件的限制,但考虑到手术医生的安排问题,通常情况下白内障手术与其他眼科手术(急症除外)不安排在同一天做。
当前该住院部对全体非急症病人是按照FCFS(First come, First serve)规则安排住院,但等待住院病人队列却越来越长,医院方面希望你们能通过数学建模来帮助解决该住院部的病床合理安排问题,以提高对医院资源的有效利用。
问题一:试分析确定合理的评价指标体系,用以评价该问题的病床安排模型的优劣。
问题二:试就该住院部当前的情况,建立合理的病床安排模型,以根据已知的第二天拟出院病人数来确定第二天应该安排哪些病人住院。
并对你们的模型利用问题一中的指标体系作出评价。
数学建模2018年-基于 0-1 规划的单 RGV 动态调度模型

s s s 个 个
(������)
������修������
(������)
������ (������) (������) ������������������ ������������
������ (������) ������������
(������)
������(������������ )
四、符号及变量说明
符号 ������ ������
(������)
������������
������
������(������)
������
������ (������) ������������
(������)
表示含义 上料轮数,������ = 0,1,2 … 当������ = 0时,表示此时在第一轮上料之前 ������ = 1,2, … ,8 依次表示 CNC1#,CNC2#,…, CNC8# 第������轮上料 RGV 是否前往第������ 台 CNC 0, 第������轮上料不前往第������台 CNC (������) ������������ = { 1, 第������轮上料前往第������台 CNC ������ = 1,2,3,4,表示 RGV 移动的起点位置 ������ = 1表示 CNC1#与 CNC2#之间; ������ = 2表示 CNC3#与 CNC4#之间; ������ = 3表示 CNC5#与 CNC6#之间; ������ = 4表示 CNC7#与 CNC8#之间。 表示第������轮上料 RGV 移动的起点位置 ������ = 1,2,3,4,表示 RGV 移动的终点位置 ������ = 1表示 CNC1#与 CNC2#之间; ������ = 2表示 CNC3#与 CNC4#之间; ������ = 3表示 CNC5#与 CNC6#之间; ������ = 4表示 CNC7#与 CNC8#之间; 表示第������轮上料 RGV 移动的终点位置 RGV 前往第������ 台 CNC 完成第������轮上料所用时间 第������轮从位置������(������) 移动到位置������ (������) 所花的时间 第������ 轮上料后第������ 台 CNC 上物料剩余加工完成的时间 在第������ 台 CNC 的处第������轮上料时间 在第������ 台 CNC 的处第������轮洗料时间 第������轮上料后第������ 台 CNC 的加工时间
2018年高教社杯全国大学生数学建模竞赛题目-B-Chinese-Appendix1

附件1:智能加工系统的组成与作业流程1.系统的场景及实物图说明在附图1中,中间设备是自带清洗槽和机械手的轨道式自动引导车RGV,清洗槽每次只能清洗1个物料,机械手臂前端有2个手爪,通过旋转可以先后各抓取1个物料,完成上下料作业。
两边排列的是CNC,每台CNC前方各安装有一段物料传送带。
右侧为上料传送带,负责为CNC输送生料(未加工的物料);左边为下料传送带,负责将成料(加工并清洗完成的物料)送出系统。
其他为保证系统正常运行的辅助设备。
附图1:RGV—CNC车间布局图附图2:带机械手臂和清洗槽的RGV实物图附图2是RGV的实物图,包括车体、机械臂、机械手爪和物料清洗槽等。
附图3:RGV机械手臂前端的2个手爪实物图在附图3左图中,机械臂前端上方手爪抓有1个生料A,CNC加工台上有1个熟料B。
RGV机械臂移动到CNC加工台上方,机械臂下方空置的手爪准备抓取熟料B,在抓取了熟料B后即完成下料作业。
在附图3右图中,RGV机械臂下方手爪已抓取了CNC加工台上的熟料B抬高手臂,并旋转手爪,将生料A对准加工位置,安放到CNC加工台上,即完成上料作业。
2.系统的构成及说明智能加工系统由8台CNC、1台带机械手和清洗槽的RGV、1条RGV直线轨道、1条上料传送带和1条下料传送带等附属设备构成。
(1)CNC:在上料传送带和下料传送带的两侧各安装4台CNC,等距排列,每台CNC同一时间只能安装1种刀具加工1个物料。
如果物料的加工过程需要两道工序,则需要有不同的CNC安装不同的刀具分别加工完成,在加工过程中不能更换刀具。
第一和第二道工序需要在不同的CNC上依次加工完成,完成时间也不同,每台CNC 只能完成其中的一道工序。
(2)RGV:RGV带有智能控制功能,能够接收和发送指令信号。
根据指令能在直线轨道上移动和停止等待,可连续移动1个单位(两台相邻CNC间的距离)、2个单位(三台相邻CNC间的距离)和3个单位(四台相邻CNC间的距离)。
智能RGV的动态调度策略

智能RGV的动态调度策略发表时间:2019-03-13T16:30:42.367Z 来源:《新材料·新装饰》2018年8月上作者:李道安1 陈哲2 梁拓1[导读] RGV有轨制导车辆系统是一种自动化,无人化的系统,被广泛用于现代化物流系统中,直线往复式RGV系统(1.华北理工大学电气工程学院,河北省唐山市 063210;2.华北理工大学理学院,河北省唐山市 063210)摘要:RGV有轨制导车辆系统是一种自动化,无人化的系统,被广泛用于现代化物流系统中,直线往复式RGV系统可以使用同样的刀具加工一道工序或由两台不同的CNC加工两道工序,但在加工过程可能会发生故障,因此RGV的动态调度是提高工作效率的基础。
本文对智能RGV的动态调度策略进行分析研究。
关键词:排队论;MMC模型;CNC引言智能加工系统由8台CNC、1台带机械手和清洗槽的RGV、1条RGV直线轨道、1条上料传送带和1条下料传送带等附属设备构成。
RGV在收到需求信号后运行至需要作业的CNC处,自行辨别CNC的上下料作业次序。
RGV在不移动的情况下用一只机械手抓取出清洗槽中的成料放入熟料到清洗槽中,然后转动机械臂,将成料放到下料传送带上送出系统。
1 RGV的动态调度模型1.1数据准备RGV的运行路径有两种方式,一种是从起始点到终止点一次完成上料,即对计算机数控机床1,计算机数控化机床2…依照顺序进行上下料和清洗处理,根据指令在直线轨道上移动一个单位所需时间为Rt1,所以完成一次上料后RGV停在1,2之间等候指令。
另一种是RGV 按CNC编号1,3,5,7,8,6,4,2,完成上料后RGV停在7,8之间等待指令。
我们将RGV看做服务台,将CNC看做被服务者,服务台相继到达被服务者的时间符合参数为λ的指数分布,符合排队论系统。
在调度决策的时候往往只有临近部分的任务是已知的,大多数任务是在传达决策后随机到达,因此在进行RGV对指令的接收和上下料及清洗工作时,需要考虑采用的调度方法是可以在一定时间内完成最多的任务。
基于寻优算法的智能RGV的动态调度问题

下料传送带RGVCZjl
I--------^>L_i1
上料传送带
CNC1#
■ 未DQ工生料
CNC3«
CNC5*
CNC7S
CZJB加工魚料 匚二I清洗后成料
图1智能加工系统示意图
轨道式自动引导车是一种无人驾驶、能在固定轨道上自 由运行,并自带一个机械手臂、两只机械手爪和物料清洗槽的 智能车,它能根据指令自动控制移动方向和距离来完成上下
2基于模拟退火算法的RGV调度模型的建立
一道工序的物料加工作业情况:每台CNC安装同样的刀 具,物料可以在任何一台CNC上加工完成。首先,RGV的动 态调度模型的好坏体现于整个系统在RGV动态调度模型下
的工作效率。釆用定性定量分析相结合的原则,以平均每台
CNC的工作时间与系统整体总的工作时间之比为评价系统工 作效率高低的标准,可以得到CNC加工台的总的工作时间越 长,则平均每一台CNC的工作时间越长,系统的工作效率就 越大,即CNC加工台的总的空闲时间越短,系统的工作效率
料及清洗物料等作业任务。清洗槽每次只能清洗1个物料, 机械手臂前端有2个手爪,通过旋转可以先后各抓取1个物 料,完成上下料作业。智能加工系统的初始状态:RGV在 CNC1#和CNC2#正中间的初始位置,所有CNC都处于空闲状 态。RGV给偶数编号CNC2#,4#,6#,8#—次上下料所需时间 与给奇数编号CNC1#,3#,5#,7#—次上下料所需时间不同。
业的生产效率,从而提高企业的竞争力。本文运用模拟退火
算法和遗传算法找出较优的RGV调度模型。
1 RGV调度问题背景
智能加工系统由8台计算机数控机床(CNC)、1辆轨道 式自动引导车(RGV)、1条RGV直线轨道、1条上料传送带、1
智能RGV的动态调度策略
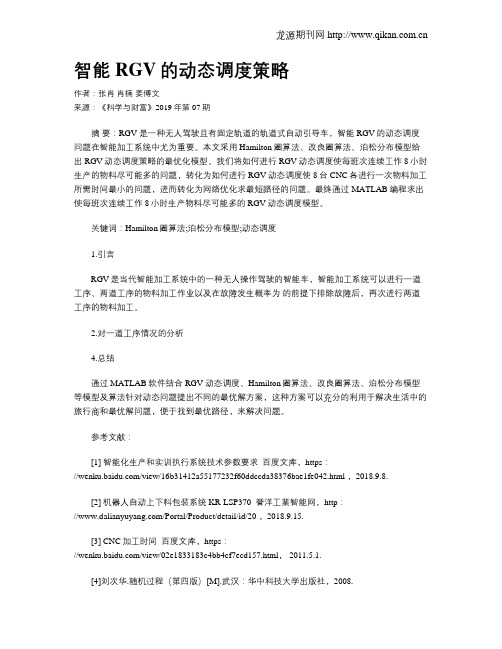
智能RGV的动态调度策略作者:张肖肖楠姜博文来源:《科学与财富》2019年第07期摘要:RGV 是一种无人驾驶且有固定轨道的轨道式自动引导车,智能RGV的动态调度问题在智能加工系统中尤为重要。
本文采用Hamilton圈算法、改良圈算法、泊松分布模型给出RGV动态调度策略的最优化模型。
我们将如何进行RGV动态调度使每班次连续工作8小时生产的物料尽可能多的问题,转化为如何进行RGV动态调度使8台CNC各进行一次物料加工所需时间最小的问题,进而转化为网络优化求最短路径的问题。
最终通过MATLAB编程求出使每班次连续工作8小时生产物料尽可能多的RGV动态调度模型。
关键词:Hamilton圈算法;泊松分布模型;动态调度1.引言RGV是当代智能加工系统中的一种无人操作驾驶的智能车,智能加工系统可以进行一道工序、两道工序的物料加工作业以及在故障发生概率为的前提下排除故障后,再次进行两道工序的物料加工。
2.对一道工序情况的分析4.总结通过MATLAB软件结合RGV 动态调度、Hamilton圈算法、改良圈算法、泊松分布模型等模型及算法针对动态问题提出不同的最优解方案,这种方案可以充分的利用于解决生活中的旅行商和最优解问题,便于找到最优路径,来解决问题。
参考文献:[1] 智能化生产和实训执行系统技术参数要求_百度文库,https:///view/16b31412a55177232f60ddccda38376bae1fe042.html ,2018.9.8.[2] 机器人自动上下料包装系统KR-LSP370_誉洋工業智能网,http:///Portal/Product/detail/id/20 ,2018.9.15.[3] CNC加工时间_百度文库,https:///view/02e1833183c4bb4cf7ecd157.html, 2011.5.1.[4]刘次华.随机过程(第四版)[M].武汉:华中科技大学出版社,2008.[5]汪晓银,周保平.数学建模与数学实验[M].北京:科学出版社,2013.[6]卓金武.MATLAB在数学建模中的应用[M].北京:北京航空航天大学出版社,2017.。
全国数学建模竞赛题目A,B

2018高教社杯全国大学生数学建模竞赛题目<请先阅读“全国大学生数学建模竞赛论文格式规范”)A题车道被占用对城市道路通行能力地影响车道被占用是指因交通事故、路边停车、占道施工等因素,导致车道或道路横断面通行能力在单位时间内降低地现象.因为城市道路具有交通流密度大、连续性强等特点,一条车道被占用,也可能降低路段所有车道地通行能力,即使时间短,也可能引起车辆排队,出现交通阻塞.如处理不当,甚至出现区域性拥堵.车道被占用地情况种类繁多、复杂,正确估算车道被占用对城市道路通行能力地影响程度,将为交通管理部门正确引导车辆行驶、审批占道施工、设计道路渠化方案、设置路边停车位和设置非港湾式公交车站等提供理论依据.视频1<附件1)和视频2<附件2)中地两个交通事故处于同一路段地同一横断面,且完全占用两条车道.请研究以下问题:1.根据视频1<附件1),描述视频中交通事故发生至撤离期间,事故所处横断面实际通行能力地变化过程.根据问题1所得结论,结合视频2<附件2),分析说明同一横断面交通事故所占车道不同对该横断面实际通行能力影响地差异.构建数学模型,分析视频1<附件1)中交通事故所影响地路段车辆排队长度与事故横断面实际通行能力、事故持续时间、路段上游车流量间地关系.假如视频1<附件1)中地交通事故所处横断面距离上游路口变为140M,路段下游方向需求不变,路段上游车流量为1500pcu/h,事故发生时车辆初始排队长度为零,且事故持续不撤离.请估算,从事故发生开始,经过多长时间,车辆排队长度将到达上游路口.附件1:视频1附件2:视频2附件3:视频1中交通事故位置示意图附件4:上游路口交通组织方案图附件5:上游路口信号配时方案图注:只考虑四轮及以上机动车、电瓶车地交通流量,且换算成标准车当量数.附件3视频1中交通事故位置示意图附件4附件5上游路口信号配时方案本题附件1、2地数据量较大,请竞赛开始后从竞赛合作网站“中国大学生在线”网站下载:试卷专题页面:试卷下载地址:2018高教社杯全国大学生数学建模竞赛题目<请先阅读“全国大学生数学建模竞赛论文格式规范”)B题碎纸片地拼接复原破碎文件地拼接在司法物证复原、历史文献修复以及军事情报获取等领域都有着重要地应用.传统上,拼接复原工作需由人工完成,准确率较高,但效率很低.特别是当碎片数量巨大,人工拼接很难在短时间内完成任务.随着计算机技术地发展,人们试图开发碎纸片地自动拼接技术,以提高拼接复原效率.请讨论以下问题:1. 对于给定地来自同一页印刷文字文件地碎纸机破碎纸片<仅纵切),建立碎纸片拼接复原模型和算法,并针对附件1、附件2给出地中、英文各一页文件地碎片数据进行拼接复原.如果复原过程需要人工干预,请写出干预方式及干预地时间节点.复原结果以图片形式及表格形式表达<见【结果表达格式说明】).2. 对于碎纸机既纵切又横切地情形,请设计碎纸片拼接复原模型和算法,并针对附件3、附件4给出地中、英文各一页文件地碎片数据进行拼接复原.如果复原过程需要人工干预,请写出干预方式及干预地时间节点.复原结果表达要求同上.3. 上述所给碎片数据均为单面打印文件,从现实情形出发,还可能有双面打印文件地碎纸片拼接复原问题需要解决.附件5给出地是一页英文印刷文字双面打印文件地碎片数据.请尝试设计相应地碎纸片拼接复原模型与算法,并就附件5地碎片数据给出拼接复原结果,结果表达要求同上.【数据文件说明】(1)每一附件为同一页纸地碎片数据.(2)附件1、附件2为纵切碎片数据,每页纸被切为19条碎片.(3)附件3、附件4为纵横切碎片数据,每页纸被切为11×19个碎片.附件5为纵横切碎片数据,每页纸被切为11×19个碎片,每个碎片有正反两面.该附件中每一碎片对应两个文件,共有2×11×19个文件,例如,第一个碎片地两面分别对应文件000a、000b.【结果表达格式说明】复原图片放入附录中,表格表达格式如下:(1)附件1、附件2地结果:将碎片序号按复原后顺序填入1×19地表格;(2)附件3、附件4地结果:将碎片序号按复原后顺序填入11×19地表格;(3)附件5地结果:将碎片序号按复原后顺序填入两个11×19地表格;(4)不能确定复原位置地碎片,可不填入上述表格,单独列表.。
- 1、下载文档前请自行甄别文档内容的完整性,平台不提供额外的编辑、内容补充、找答案等附加服务。
- 2、"仅部分预览"的文档,不可在线预览部分如存在完整性等问题,可反馈申请退款(可完整预览的文档不适用该条件!)。
- 3、如文档侵犯您的权益,请联系客服反馈,我们会尽快为您处理(人工客服工作时间:9:00-18:30)。
1. 问题的重述
现有一个智能加工系统,由 8 台 CNC、1 辆 RGV 以及其他附属设备组成。
RGV 能够根据指令与决策,在水平的轨道上自动控制移动的方向和距离,并通
过机械手爪、机械臂等部件完成“上下料”、“清洗作业”等诸多过程。
对于以下三种情况:
①加工过程包含 1 道工序且每台 CNC 都可以进行加工;
2018 年高教社杯全国大学生数学建模竞赛题目
(请先阅读“全国大学生数学建模竞赛论文格式规范”
)
问题 B
智能 RGV 的动态调度策略
图 1 是一个智能加工系统的示意图,由 8 台计算机数控机床(Computer Number Controller,CNC)、
1 辆轨道式自动引导车(Rail Guide Vehicle,RGV)、1 条 RGV 直线轨道、1 条上料传送带、1 条下
于某个物料的加工,是否发生故障,故障发生的时间,以及故障排除时间这三个
随机变量。
本文拟构建一般性的规划,理清系统内部的机理关系。然后,通过提出不同
的原则,编写算法,解决该规划问题;并通过“基于蒙特卡洛的学习算法”,比
较、检验不同原则的优劣。
3. 模型的假设与符号的说明
3.1 模型的假设
(1)生料的供应是无限的。
这样的规划是一个 NP 问题,无法通过传统的方法求解,所以进而寻求模拟的方
法求得局部最优解。
本文选取了“就近原则”——构造时间代价函数,
“FIFO 原则”——考虑各
台 CNC 的等待时间,以及“HRRN 原则”——将时间代价与等待时间进行综合
考虑,分别对情况一进行了模拟。事实上,每种原则的结果相同:第一组数据加
RGV 为 CNC2#,4#,6#,8#进行一次上下料所需时间。
4
Step 2.
基于上述符号的定义,可以得到:
()
− ≥ 0 + 2 ,
�
= 0,
≤ 8 × 60 × 60 − 1
其他
(成时间在 8 小时终止以前,那么物料
的时刻,记为 .
此外,物料加工时间记为0 ,清洗时间记为1 ,第台机床“上下料”时间记
()
为2 .
()
2
⎧(1)
�2 ,
=
⎨ (2)
�2 ,
⎩
mod( ) ≠ 0
2
.
mod( ) = 0
2
(1)
(2)
其中,2 为 RGV 为 CNC1#,3#,5#,7#进行一次上下料所需时间,2 为
基于多原则比较和蒙特卡洛模拟的 RGV 动态调度模型
摘要
本文从规划模型、多原则求解的角度,综合了蒙特卡洛模拟与机器学习的思
想,研究了由 8 台 CNC、1 辆 RGV 以及其他附属设备组成的智能加工系统的动
态调度问题,并给出了不同工序情况下的具体调度方案。
针对情况一:单工序的作业流程较为简单。首先,利用规划的各个约束条件,
8. 考虑到机床安放的位置关系——偶数号码机床位于系统左侧,奇数号码机床
位于系统右侧——则 RGV 从机床移动到机床的时间为:
+ 1
+ 1
⎧ 0,
��
�−�
�� = 0
�
2
2
�
�
+ 1
+ 1
� ,
��
�−�
�� = 1
� 1
2
2
=
⎨
+ 1
+ 1
刻画了 RGV 在 CNC 之间的运动过程、单个物料的加工过程、
“上下料”时 RGV
手爪的旋转过程、清洗作业的过程、RGV 移动至下一个机床进行加工的过程等
等。此外,还刻画了物料加工与运送的“唯一性”,以及利用 0-1 变量构造的目
标函数。规划的目的是,在给定的时间内,使得加工出的物料数量最多。然而,
过程。
此外,双工序流程中各台 CNC 所负责的工序也是不确定的;因此,本文对
256 种工序布局方案,结合三种选取原则,进行了遍历。得到的结果是:第一组
数据的各台 CNC 最优工序分配为 1-2-1-2-1-2-1-2,三种原则结果一致,最终加工
出 253 件物料;第二组数据的各台 CNC 最优工序分配为 2-1-2-1-2-1-2-1,
(2)两个步骤,周而复始,直至 8 个小时
结束。
4.1.2 单工序的调度模型
考虑到模型的一般化问题,此处本文拟利用规划的方法,寻找并构建各台
CNC 以及生产物料的数量关系。
1. RGV 在 CNC 之间运动时间的刻画
不妨设,现有任意两台 CNC,分别记作,,其中 = 1, 2, …, 8; = 1, 2, …,
在情况(1)中,物料加工程序仅由一道工序组成。其中,每台 CNC 安装同
样的刀具,而物料可以在任意一台 CNC 上加工完成。
纵观整个单工序的加工过程,可以发现,当某台 CNC 完成加工,即完成“生
料→熟料”的过程时,便处于等待状态,并向 RGV 发出需求信号。当 RGV 移动
至该 CNC 正前方时,连续完成下述步骤:
统可加工完成的物料数量级为 102,所以准备 103 个生料一定足够。因此,参数
取值范围可以取为 = 1, 2, …, 1000.
相对应地,将尚为生料的 被 RGV 放入号机床(“上料”过程完成)的时
刻,记为 ;将已加工为熟料的 被 RGV 取出号机床(“下料”过程完成)
378
500
182
RGV 为 CNC1#,3#,5#,7#一次上下料所需时间
28
30
27
RGV 为 CNC2#,4#,6#,8#一次上下料所需时间
31
35
32
RGV 完成一个物料的清洗作业所需时间
25
30
25
系统作业参数
注:每班次连续作业 8 小时。
附件 1:智能加工系统的组成与作业流程
附件 2:模型验证结果的 EXCEL 表(完整电子表作为附件放在支撑材料中提交)
2
(2)不考虑 RGV 转向的时间,即 RGV 从 CNC1#到 CNC2#,从 CNC3#到
CNC4#,从 CNC5#到 CNC6#,从 CNC7#到 CNC8#的时间全部为 0.
(3)上料传送带可以及时将生料运往需要的 CNC 正前方,下料传送带可以
及时将成料运出整个系统。
3.2 符号的说明
表 1
“FIFO
原则”和“HRRN 原则”更优,最终加工出 212 件物料;第三组数据的各台 CNC
最优工序分配为 1-1-2-1-2-1-1-2,
“就近原则”最优,最终加工出 241 件物料。此
外,所有的调度方案均呈现有规律的循环状态。
然后,利用“基于蒙特卡洛的学习算法”,在构造正反馈的前提下“随机”
地尝试以获得更优解。结果反映了,三种原则中的最优原则,已非常接近全局最
请你们团队完成下列两项任务:
任务 1:对一般问题进行研究,给出 RGV 动态调度模型和相应的求解算法;
任务 2:利用表 1 中系统作业参数的 3 组数据分别检验模型的实用性和算法的有效性,给出 RGV
的调度策略和系统的作业效率,并将具体的结果分别填入附件 2 的 EXCEL 表中。
表 1:智能加工系统作业参数的 3 组数据表
时间单位:秒
第1组
第2组
第3组
RGV 移动 1 个单位所需时间
20
23
18
RGV 移动 2 个单位所需时间
33
41
32
RGV 移动 3 个单位所需时间
46
59
46
CNC 加工完成一个一道工序的物料所需时间
560
580
545
CNC 加工完成一个两道工序物料的第一道工序所需时间
400
280
455
CNC 加工完成一个两道工序物料的第二道工序所需时间
符号的说明
符号
说明
单位
RGV 移动个单位所需时间
秒
RGV 从机床移动到机床的时间
秒
号机床所加工的第 个物料
件
0
物料加工时间
秒
1
物料清洗时间
秒
2
()
第台机床“上下料”时间
秒
生料 “上料”完成时刻
秒
生料经过 CNC 的加工成为熟料,而熟料经过 RGV 的清洗成为成料。从 RGV 的
作业过程来看,RGV 首先需要选取一台候选 CNC,然后移动至该 CNC,放入生
料,取出熟料,再将熟料进行清洗使之变为成料(包括送出系统)——最终 RGV
将进入下一轮选择 CNC 的阶段。
生料
熟料
图 1
成料
情况(1)物料的形态演化
工完成了 383 件物料,第二组数据加工完成了 360 件物料,第三组数据加工完成
了 393 件物料。并且,调度的方案全部为 1→2→…→8→1→… 此外,第三组数
据的系统效率最高,为 49.125 件/h.
针对情况二:双工序的作业流程十分复杂。首先,在情况一的基础上,对规
划的各个约束条件进行修正;并着重刻画了 RGV 移动至下一个机床进行加工的
料传送带等附属设备组成。RGV 是一种无人驾驶、能在固定轨道上自由运行的智能车。它根据指令
能自动控制移动方向和距离,并自带一个机械手臂、两只机械手爪和物料清洗槽,能够完成上下料
及清洗物料等作业任务(参见附件 1)
。
图 1:智能加工系统示意图
针对下面的三种具体情况:
(1)一道工序的物料加工作业情况,每台 CNC 安装同样的刀具,物料可以在任一台 CNC 上加