鼓风炉熔炼再生铜(5)
再生铜冶炼工艺(一)

再生铜冶炼工艺(一)再生铜铸造工艺介绍什么是再生铜工艺?再生铜工艺是指将废弃铜制品进行回收利用,重新铸造成新的铜制品,并且保证与原铜制品一样的化学成分和物理性质。
再生铜工艺的使用可以减少对自然资源的耗费,具有环保与经济双重效益。
再生铜冶炼的技术流程再生铜冶炼的技术流程包括以下几个步骤:1.冶炼废弃铜制品首先要被压碎成小块,然后投入冶炼炉中进行熔化。
在高温和高压的环境中,铜制品中的杂质会沉淀到底部,铜液则上浮到炉口。
2.气体处理通过将炉内的气体进行处理,可以去除铜液中残留的氧化物、硫酸盐等杂质。
可以使用氧气和氮气来实现这一步骤。
3.精炼在精炼炉中,将铜液进一步加热,在同时通入空气的情况下,溶解其中的氧化物杂质,然后再次用冷却的气体或水进行冷却,将杂质沉淀下去。
4.熔铸经过冷却后的铜液可以进行熔铸,将其倾倒入模具中,等待其冷却凝固后,即可得到新的再生铜制品。
再生铜工艺的优势1.节约资源再生铜工艺可以充分利用已经生产的铜制品,可以避免对自然环境的破坏和耗费资源的浪费。
2.地球环保再生铜冶炼不需要新开采铜矿,减少了对大自然的破坏,同时减少了不必要的岩石开采、水资源消耗等行为。
3.有利于社会经济发展再生铜工艺的使用不仅可以节约能源和原材料,而且可以创造非常多的就业机会,形成一个良性的循环。
4.节约原材料再生铜的冶炼不仅能够节约自然资源,同时单位能耗也大幅降低。
总之,再生铜工艺是一种环保、经济、资源节约的铸造方式,对于保护地球的环境和社会经济的可持续发展具有重要意义。
再生铜工艺的发展在过去的几十年中,再生铜工艺的发展比较迅速。
从最初的手工加工、回收到现在的自动化、智能化加工。
随着技术和设备的提升,再生铜工艺的加工质量、效率、自动化程度等方面都有了很大的提高。
同时,再生铜工艺的应用范围也不断扩大。
除了传统的家电、电器类产品,现在再生铜工艺已经开始应用于航空、汽车、通讯等高科技领域以及建筑、农业、船舶等传统行业。
鼓风炉富氧熔炼炼铜

鼓风炉富氧熔炼炼铜简介****公司位于**市,海拔约1700m,空气含氧量约16%(海平面空气氧浓约21%,每升高350m,氧浓约降1%),现有5.8m2、4.1m2鼓风炉两台,日处理鼓风炉炼铜是一种古老的炼铜方法。
铜炉料与熔剂、焦炭在鼓风炉内熔炼产出铜锍(或粗铜)和炉渣的铜熔炼方法。
铜炉料可以是混捏铜精矿、铜精矿烧结块或其他含铜块料。
密闭鼓风炉一般处理经混捏的铜精矿料,而敞开式鼓风炉只能处理经过制团或烧结的块料。
根据炉内不同的气相成分,鼓风炉炼铜可分为氧化炼铜和还原炼铜。
氧化炼铜用于处理硫化矿,还原炼铜用于处理氧化矿或再生铜料。
这种熔炼工艺简单,床能力大,热效率高,渣含铜低,投资省,建设快;在20世纪30年代以前一直是世界上主要的炼铜方法。
在中国,20世纪50年代以前,这种方法几乎是矿铜生产的唯一方法。
传统的铜锍熔炼鼓风炉的炉顶是敞开式的,只能处理烧结矿或块矿,所产烟气含二氧化硫浓度低,仅0.5%左右,难以回收,造成烟害。
为了克服传统鼓风炉的这种弊病,人们曾试图通过制团的途径,使铜精矿中的硫保留下来,以集中到鼓风炉中进行氧化,再加上炉顶采取密闭措施,使鼓风炉烟气中的SO2浓度达到能经济而有效地回收的程度。
在工业实践中,团矿偶然自燃后,出现块状硫化物以及鼓风炉炉壁结块中也有硫化物等现象表明,铜精矿可在加压和加热条件下发生固结作用。
20世纪50年代初,日本四阪岛冶炼厂开发了料封式密闭鼓风炉熔炼法即百田法,铜精矿只需加水混捏后即可直接加入炉内,在炉气加热和料柱的压力作用下,固结成块,使熔炼得以顺利进行。
直接处理铜精矿,烟气含二氧化硫浓度达4%~6%,可用以制取硫酸,减轻了烟气对环境的污染。
60年代,苏联成功地采取了处理团矿或块矿的料钟式密闭鼓风炉富氧自热熔炼工艺。
同期,波兰有2座料钟式密闭富氧熔炼鼓风炉投产。
60年代中期,中国成功地进行了料封式密闭鼓风炉工业试验后,相继用以改造敞开式鼓风炉,解决烟害问题。
毕业设计_30万吨年电铜的铜电解精炼车间工艺设计

30万吨/年电铜的铜电解精炼车间工艺设计设计总说明铜电解精炼过程,主要是在直流电的作用下,铜在阳极上失去电子后以铜离子的形态溶解,而铜离子在阴极上得到电子以金属铜的形态析出的过程。
目前世界铜冶炼厂使用的主要熔炼工艺为闪速熔炼和熔池熔炼,其中熔池熔炼包括诺兰达连续炼铜法、艾萨熔炼法、瓦纽科夫法。
本设计为年产30万吨电铜的铜电解精炼车间,铜的电解精炼是以火法精炼产出的精铜为阳极,以电解产出的薄铜(始极片)作阴极,以硫酸铜和硫酸的水溶液作电解液。
在直流电的作用下,阳极铜进行电化学溶解,纯铜在阴极中沉积,杂质则进入阳极泥和电解液中,从而实现了铜与杂质的分离,确定了铜电解过程中的主要技术经济指标。
本设计还进行了物料平衡、热平衡、水平衡、主要设备及辅助设备的计算与选择。
进一步提高铜电解精炼的技术水平,从而达到对铜电解精炼技术有更深刻了解的目的。
关键字:铜;电解精炼;平衡计算;设计The Process Design of Electrolytic Refining Workshop with Annual Output 300,000 Tons Electrolytic CopperSpecialty:Metallurgical engineeringName:Zhu langtaoTutor:Zhang qiuliDesign DescriptionThe copper electrolysis fining process is mainly under the direct current function,copper loses the electron after the anode by cupric ion shape dissolution,but the cupric ion obtains the electron on the negative pole by the metal copper shape separation process.At present the world copper refinery use main smelting craft to dodge the fast smelting and the molten bath smelts,the molten bath smelts including the Landa continual copper smelting,Isa smelts,Niu Shinao smelts.Originally designed to produce per 300,000 the first electrolytic copper refine the work shop,refining the precise copper produced electrolytically and concisely as the positive pole with fire law of copper,take copper sulfic acid and aqueous solution of the sulfuric acid as the electrolytic liquid very much with the electrolytic thin copper beginning that produces.Under the funcition of the direct current,positive pole copper carries on electrochemistry to dissolve,pure copper is deposited in the negative pole,the impurity is entered in positive pole mud and electrolytic liquid,thus realized the separation of the copper and impurity,have confirmed the main technical and economic index in the electrolytic course of copper.Have originally designed and also carried on supplies equilibrating,calculation and choice of the thermal balance,horizontal weighing apparatus,capital equipment and auxiliary equipment. Further improve the standard of the electrolytic refining and reached for the refinement of the electrolytic technology is a profound understanding of purpose. Keywords:Copper;Electro refining;balanced computing;design目录1 文献综述 (6)1.1铜的简介 (6)1.2铜生产技术 (7)1.2.1传统炼铜技术 (7)1.2.2现代炼铜技术 (7)1.2.3冰铜吹炼 (7)1.2.4铜的精炼 (7)1.2.5湿法炼铜 (8)1.3铜的电解精炼 (9)1.3.1铜电解精炼现状 (9)1.3.2铜电解精炼的基本原理 (9)1.3.3铜电解精炼中杂质的主要行为 (11)2 设计原则及要求 (14)2.1设计原则 (14)2.2设计要求 (14)2.3主要设备及辅助设备的计算与选择 (14)2.4冶金计算 (15)2.5制图内容和要求 (15)3 主要设备的计算与选择 (16)3.1电解槽 (16)3.1.1电解槽的材质 (16)3.1.2电解槽的构造 (16)3.1.3电解槽衬里的材质 (17)3.1.4电解槽的安装 (17)3.1.5阳极 (18)3.1.6阴极 (19)3.1.7种板 (19)3.2电解槽各有关设备选择和计算 (20)3.3整流器的选材及计算 (22)3.4车间运输设备的选择与计算 (22)3.5车间及跨的选择 (23)3.6极板作业机组 (23)4 主要技术经济指标的论证与选择 (25)4.1主要技术条件 (25)4.1.2添加剂 (26)4.1.3电解液温度 (26)4.1.4电解液循环 (27)4.1.5电流密度 (27)4.1.6同极中心距 (27)4.1.7阳极寿命和阴极周期 (27)4.2主要经济指标 (28)4.2.1电流效率 (28)4.2.2残极率 (29)4.2.3铜电解回收率 (29)4.2.4槽电压 (29)4.2.5直流电能单位消耗 (30)4.2.6硫酸单位消耗 (30)4.2.7蒸汽单位消耗 (30)5 冶金计算 (31)5.1铜电解精炼物料平衡计算 (31)5.1.1阳极泥率和阳极泥成分计算 (31)5.1.2电解精炼物料计算 (32)5.2铜电解精炼热平衡计算 (34)5.2.1计算电解槽液面水蒸发热损失 (35)5.2.2电解槽液面的辐射与对流的热损失 (35)5.2.3电解槽壁的辐射与对流热损失 (36)5.2.4管道内溶液热损失 (36)5.2.5电流通过电解液所产生的热量 (36)5.2.6全车间需要补充热量 (37)5.3电解液净化及硫酸盐生产冶金计算 (37)5.3.1净液量计算 (37)5.3.2硫酸铜的物料平衡计算 (38)5.3.3脱铜电解物料平衡计算 (40)5.3.4粗硫酸镍生产计算 (41)5.4电解循环系统设备及管道计算 (43)5.4.1循环贮槽材质及容积确定 (43)5.4.2高位槽 (43)5.4.3阳极泥贮槽 (43)5.4.4电解液循环泵 (43)5.4.5电解液加热器 (44)6 厂址选择 (46)7 环保与安全 (48)7.1环境保护 (48)7.2安全生产 (48)致谢 (50)参考文献 (51)附:专题 (52)1 文献综述1.1铜的简介铜是人类最早发现和应用的金属之一,据考证,西亚地区是世界上最早应用铜并掌握炼铜技术的地区。
鼓风炉富氧熔炼炼铜

再生金属冶金考试试题

课程名称再生金属冶金(A)卷 06 年上期命题人王宇菲适用班级冶金0232 考试方法(闭)卷一、填空(每空1分,共30分)1、有色金属废料和废件______,所产出的________叫做再生金属或再生有色金属合金,有时也将有色金属废料、废件统称为__________。
2、废旧原料的预处理主要有:______、解体、捆扎、______、压块、破碎、______、分选等工序,其中解体的目的是_______________,解体的主要方法有________和_________。
3、铜的熔点为____________,由于其具有良好的______和_______,因而铜广泛用于_____工业、______工业和______工业。
4、目前铜废料主要有三种再生利用途径:________、_________和__________。
5、再生粗铜电解精炼时用的阳极是________,阴极由厚为______的铜片做成,而电解槽是由_______制成并内衬防腐材料的长方形槽子。
6、粗铜中的锌在火法精炼过程中可以以______形式进入炉气;也可以以_____和_________形式进入炉渣;而铁则通过______以________形式进入炉渣中。
7、我国主要含铜废料有_________、__________、_________和___________。
二、简答题(10×5= 50分)1、再生有色金属废料的特点有哪些?2、电解精炼的原理是什么?请写出电解过程中的电极反应。
3、黑铜吹炼的目的是什么?请简述黑铜吹炼的生产实践。
4、什么是黑铜?请写出铜废料鼓风炉熔炼时物料在炉内各区域中发生的反应。
5、粗铜火法精炼的基本原理是什么?请简述反射炉精炼的生产过程三、论述题(20分)1、结合所学专业知识,谈谈我国发展再生金属生产的意义和现状。
铜密闭鼓风炉熔炼技术经济指标

邵武厂
铜陵二冶
富冶
(新厂)
试生产期
生产期
精矿成分
Cu
S
富氧浓度,O2
16~22
25~28
24
17.7~22.4
26.5~32.5
27~30
21~24
28~30
27
10~15
25~30
22~24
块料率
焦率
铜硫品位
脱硫率
42.4
6.80
30~33
46.0
35~40
6.5~7.0
34.3~41.5
53.5~57.2
理论脱硫率可根据精矿到化学组成用以下经验公式粗略计算(假定精矿中的硫化物主要为Cu2S、mFeS.nFeS2):
式中:
DS1-一次脱硫率(FeS2分解);
DS2-二次脱硫率(FeS氧化);
DST-总脱硫率(炉渣和烟尘中的硫除外),%;
(Fe)-精矿含铁,%;
(S)-精矿含硫,%;
(Cu)-精矿含铜,%;
55~60
7~8.5
① 铜陵二冶A为富氧空气工业试验数据;B为1986~1993年生产平均值;
② 富氧空气工业试验数据;
③ 富氧空气生产资料。
四、铜回收率
密闭鼓风炉由于流程简单,中间环节少,铜锍品位较低,炉渣含四氧化三铁较少,渣含铜较低,故铜回收率较高。但如果精矿混捏不好,烟尘率加大,可降低铜回收率。一般直收率可达94%~96.5%。铜总回收率可达98%~98.5%。
4.1~4.7
6.5~8.5
9.5
1.46
14.18
20.73
35.34
4.4~4.5
7~8
8.77
铜的回收与再生利用_废杂铜利用的途径.
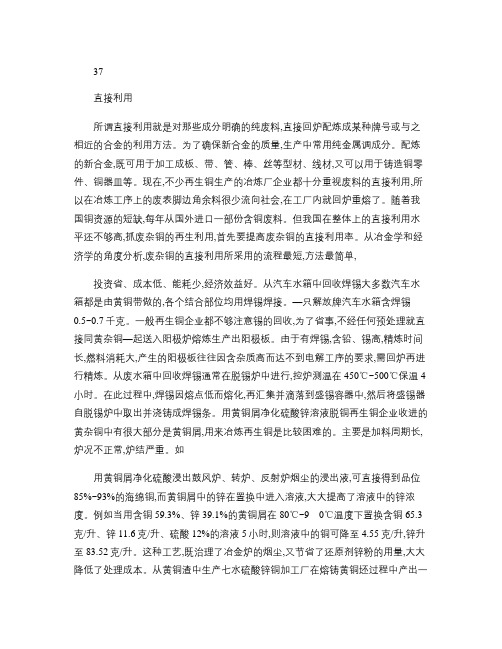
40~60千克/小时・米3,而普通
中和槽的溶铜能力仅为1~1.5千
克/小时・
米3。
用废杂铜
生产电解
铜
废杂铜一直作
为生产再生铜
的原料,由废
杂铜到电解
铜,—般经过
火法冶炼和电
解精炼两大工
序。在火法冶
炼中有一段
法、二段法和
三段法。
一段法冶
炼是物料只进
反射炉的冶
炼。炼铜反射
炉有烧块煤
金属铜粉 的氧化——浸出过程激
烈发生,反应生成的硫酸铜(夹带
未反应完全的铜粉 从塔的溢流口
流出,进入—铜粉分离器。从分离
器溢流口流出的硫酸铜溶液送带
式水冷结晶机,分离出的铜粉返
回鼓泡塔继续反应。
该反应器与传统的中和槽相
比。具有溶铜效率高,能连续生
产、操作简便等优点。对于筛板直
径600毫米,塔体有效高度2600
出了采用工频真空感应炉处理黄
杂铜的设想并进行研究。当黄杂
铜于电炉中在1200℃的高温熔化
用黄铜屑净化硫酸浸出鼓风炉、转炉、反射炉烟尘的浸出液,可直接得到品位85%~93%的海绵铜,而黄铜屑中的锌在置换中进入溶液,大大提高了溶液中的锌浓度。例如当用含铜59.3%、锌39.1%的黄铜屑在80℃~90℃温度下置换含铜65.3克/升、锌11.6克/升、硫酸12%的溶液5小时,则溶液中的铜可降至4.55克/升,锌升至83.52克/升。这种工艺,既治理了冶金炉的烟尘,又节省了还原剂锌粉的用量,大大降低了处理成本。从黄铜渣中生产七水硫酸锌铜加工厂在熔铸黄铜坯过程中产出一定量的黄铜渣,黄铜渣中含锌40%~60%、含铜30%~40%,锌大部分以氧化锌形态存在,少部分以铜锌合金形态存在。用此种渣生产硫酸锌、可综合回收锌和黄铜粒。生产工艺采用两段酸
铜密闭鼓风炉熔炼技术操作条件
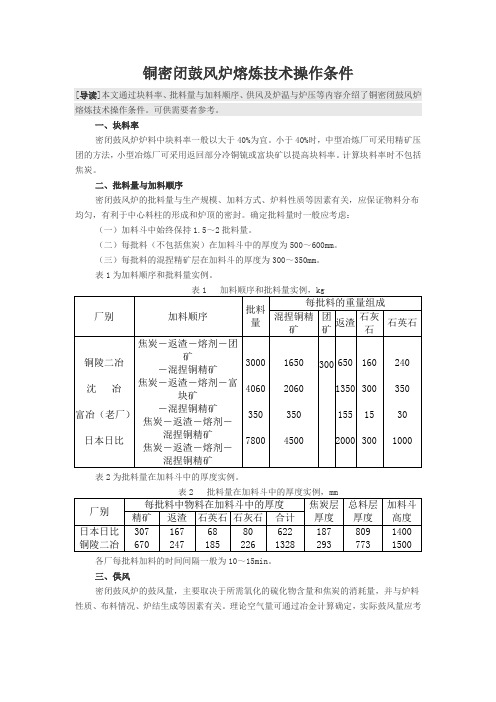
密闭鼓风炉的批料量与生产规模、加料方式、炉料性质等因素有关,应保证物料分布均匀,有利于中心料柱的形成和炉顶的密封。确定批料量时一般应考虑:
(一)加料斗中始终保持1.5~2批料量。
(二)每批料(不包括焦炭)在加料斗中的厚度为500~600mm。
(三)每批料的混捏精矿层在加料斗的厚度为300~350mm。
铜密闭鼓风炉熔炼技术操作条件
[导读]本文通过块料率、批料量与加料顺序、供风及炉温与炉压等内容介绍了铜密闭鼓风炉熔炼技术操作条件。可供需要者参考。
一、块料率
密闭鼓风炉炉料中块料率一般以大于40%为宜。小于40%时,中型冶炼厂可采用精矿压团的方法,小型冶炼厂可采用返回部分冷铜锍或富块矿以提高块料率。计算块料率时不包括焦炭。
340
420
470
烟气单体硫含量,g/m³0.78
0.35
密闭鼓风炉炉顶负压过高,漏入空气量增加,降低了烟气中二氧化硫浓度。但负压过低又会造成炉顶操作条件恶化,一般控制在50~100Pa为宜。表11为炉顶负压与烟气二氧化硫浓度的测定值。
表11 炉顶负压与烟气二氧化硫浓度的测定值
㎡
t/(㎡·d)
m³/min
%
m³/(㎡·d)
m³/t
10.5
38~45
390~400
21
30~38
~1400
10
40~45
330~400
21
33~40
~1240
2
40~45
75~80
21
38~40
~1320
1.5
45~50
50~55
21
33~37
~1060
2、风压 密闭鼓风炉的鼓风压力主要取决于炉内阻力,在一定范围内增加风压对熔炼过程有利。但风压过高会增加烟尘率和料层穿孔而跑空风。目前各厂的鼓风压力一般控制在8~10kPa。表4为鼓风压力实例。
- 1、下载文档前请自行甄别文档内容的完整性,平台不提供额外的编辑、内容补充、找答案等附加服务。
- 2、"仅部分预览"的文档,不可在线预览部分如存在完整性等问题,可反馈申请退款(可完整预览的文档不适用该条件!)。
- 3、如文档侵犯您的权益,请联系客服反馈,我们会尽快为您处理(人工客服工作时间:9:00-18:30)。
书山有路勤为径,学海无涯苦作舟
鼓风炉熔炼再生铜(5)
鼓风炉熔炼的配料计算鼓风炉熔炼时需根据原料性质计算出所加熔剂
量,常用的方法有两种。
一、有效熔剂法原料为含铜炉渣。
(1)已知条件a、含铜炉渣的化学成
分为SiO2 21.50%、CaO 2.20%、FeO 14.40%、其他61.90%。
b、石英石成分为SiO2 92.4%、CaO 1.2%、FeO 0.3%。
c、石灰石成分为SiO2 1.3%、CaO 54%、FeO 0.5%。
d、选择的渣型为SiO2 30%、CaO 28%、FeO 14%。
(2)配料计算以100kg 含铜炉渣为计算基础a、计算石英石和石灰石的有效溶剂
率100kg 石英石中含有1.2kg CaO,炉渣中CaO 与SiO2 之比是28:30 1.2kg CaO 造渣需1.2×30/28=1.2kg SiO2 100kg 石英石中游离的SiO2=92.4-1.29=91.11kg,即石英石的有效熔剂率为91.11%。
同样,100kg 石灰石中有
1.3kg SiO2,因此石灰石中有1.3×28/30=1.2kg CaO 与SiO2 造渣,故石灰石的
有效熔剂率为(54-1.2)÷100=52.8% b、计算炉渣量和各组成的量通过渣型
和铜炉渣中含FeO 量计算出渣量为14.4/14×100=103kg 渣型各组成的量如下SiO2=103×0.30=30.9kgCaO=103×0.28=28.84kgFeO=103×0.14=14.40kg c、计算补加的石英石和石灰石量除去原料中SiO2、CaO 的含量,炉渣中还缺的量为
SiO2=30.9-21.5=9.4kgCaO=28.8-2.2=26.64kg 需补加的石英石熔剂为9.4/91.11%=10.3kg 补加的石灰石熔剂为26.64/52.8%=10.3kg 故造渣率为103/ (100+10.3+50.5)×100%=64% 当熔剂质量稳定且加入量不大时,可近似取
石英石的有效熔剂率为92%,石灰石的有效熔剂率为53%。
此时可算出补加
的石英石为9.4/92%=10.21kg 补加的石灰石为26.64/53%=49.7kg[next] 二、代
数法通常用于计算黄杂铜、白杂铜熔炼时的配料。
(1)已知条件a、选择
炉渣成分为:SiO2 30%、CaO 32%、FeO 8%。
b、石英石成分为SiO2。