鼓风炉富氧熔炼炼铜
多枪顶吹连续吹炼炉高浓度富氧炼铜生产工艺

多枪顶吹连续吹炼炉高浓度富氧炼铜生产工艺
多枪顶吹连续吹炼炉高浓度富氧炼铜生产工艺是一种现代化的铜矿冶炼工艺,主要包括以下步骤:
1. 矿石破碎和浸出:将铜矿石经过破碎和浸出处理,将铜含量较高的矿石得到提取出来。
2. 富氧化:将得到的矿石放入多枪顶吹连续吹炼炉中,通过高浓度富氧对矿石进行氧化处理,将铜矿石中的硫化铜转化为氧化铜。
3. 炉内反应:在炼炉内进行高温反应,将氧化铜和其他杂质分离出来,得到纯净的铜水。
4. 熔炼和精炼:将得到的铜水进行进一步的熔炼和精炼处理,以提高铜的纯度。
5. 铜的成品生产:最终得到的纯净铜液可用于生产各种铜制品,如铜管、铜板等。
这种工艺具有高效、节能、环保等优点,被广泛应用于现代铜矿冶炼生产中。
鼓风炉富氧熔炼炼铜

鼓风炉富氧熔炼炼铜简介****公司位于**市,海拔约1700m,空气含氧量约16%(海平面空气氧浓约21%,每升高350m,氧浓约降1%),现有5.8m2、4.1m2鼓风炉两台,日处理鼓风炉炼铜是一种古老的炼铜方法。
铜炉料与熔剂、焦炭在鼓风炉内熔炼产出铜锍(或粗铜)和炉渣的铜熔炼方法。
铜炉料可以是混捏铜精矿、铜精矿烧结块或其他含铜块料。
密闭鼓风炉一般处理经混捏的铜精矿料,而敞开式鼓风炉只能处理经过制团或烧结的块料。
根据炉内不同的气相成分,鼓风炉炼铜可分为氧化炼铜和还原炼铜。
氧化炼铜用于处理硫化矿,还原炼铜用于处理氧化矿或再生铜料。
这种熔炼工艺简单,床能力大,热效率高,渣含铜低,投资省,建设快;在20世纪30年代以前一直是世界上主要的炼铜方法。
在中国,20世纪50年代以前,这种方法几乎是矿铜生产的唯一方法。
传统的铜锍熔炼鼓风炉的炉顶是敞开式的,只能处理烧结矿或块矿,所产烟气含二氧化硫浓度低,仅0.5%左右,难以回收,造成烟害。
为了克服传统鼓风炉的这种弊病,人们曾试图通过制团的途径,使铜精矿中的硫保留下来,以集中到鼓风炉中进行氧化,再加上炉顶采取密闭措施,使鼓风炉烟气中的SO2浓度达到能经济而有效地回收的程度。
在工业实践中,团矿偶然自燃后,出现块状硫化物以及鼓风炉炉壁结块中也有硫化物等现象表明,铜精矿可在加压和加热条件下发生固结作用。
20世纪50年代初,日本四阪岛冶炼厂开发了料封式密闭鼓风炉熔炼法即百田法,铜精矿只需加水混捏后即可直接加入炉内,在炉气加热和料柱的压力作用下,固结成块,使熔炼得以顺利进行。
直接处理铜精矿,烟气含二氧化硫浓度达4%~6%,可用以制取硫酸,减轻了烟气对环境的污染。
60年代,苏联成功地采取了处理团矿或块矿的料钟式密闭鼓风炉富氧自热熔炼工艺。
同期,波兰有2座料钟式密闭富氧熔炼鼓风炉投产。
60年代中期,中国成功地进行了料封式密闭鼓风炉工业试验后,相继用以改造敞开式鼓风炉,解决烟害问题。
一冶的铜是这样炼出来的

一冶的铜是这样炼出来的□刘英刚一冶,系铜陵有色公司第一冶炼厂的简称,是新中国的第一个冶炼厂。
第一冶炼厂(原名铜官山冶炼厂)建于新中国成立初期。
当时国家的经济建设即将开始,朝鲜战争已经打响,所有这些,都需要铜,而建厂的条件极不成熟:机械设备制造能力极低,设计机构还未组建,资金短缺等等。
1950年华东工业部组建铜官山工程处,并抽调以喇华佩为首的几位工程技术人员,于1951年5月1日开始,借助一本外文炼铜教科书进行设计。
根据铜矿资源少,资金又困难等情况,采用烧结机——鼓风炉——转炉生产流程。
实践证明,这些冶炼设备能够较好地适应提高生产能力的需要。
鼓风炉可以沿长度增加水套,扩大炉床面积,烧结机和转炉都可延长或增加台数。
在一冶投产后的三十多年中,随着铜山、狮子山、凤凰山等矿山的陆续投产,铜原料不断增多,鼓风炉纵向水套的块数由最初的4块逐步增加至6块、7块、10块,而炉床面积则由原来的3.6平方米逐步加大至5.4平方米、6.4平方米及10.5平方米。
烧结机由最初的一台8.5平方米增加至两台16平方米。
转炉的公称能力也经历过5吨、8吨、15吨,而且其台数由2台增加至5台。
对一冶的建设,铜官山工程处采用三自(自行设计、自行制造设备、自行施工)、三边(边设计、边施工、边生产)的措施,缩短建设周期。
第一冶炼厂自1951年5月1日开始设计,投入330万元,仅用两年的时间便获得最终产品,于1953年5月1日产出第一炉粗铜。
不可否认,由于建设期间条件较差,装备水平低,机械化程度不高,因而劳动强度比较高,劳动条件也很差。
烧结机的生产是人工抬料、拌料、进料、布料,烧结块的运输全部是人夹手推,工人在火花四溅、硫烟滚滚的烧结机尾部将装满火红冒烟烧结块的元宝车推到堆场,再用大铁钳将火红的烧结块夹下来成堆(因烧结机在鼓风炉开炉前几个月便开车生产)。
为了改变这种恶劣条件,一年后,国家批准《改善烟害工程》,建一个地下大矿仓,烧结块的运输实行了机械化,但劳动条件没有改善,烟、尘依旧。
密闭鼓风炉富氧熔炼

新 疆 有 色 金 属
1 3 7
密闭鼓风炉富氧熔炼
吴 建 军
( 新疆众鑫矿业股份有限责任公 司 哈密 8 3 9 0 0 0 )
摘 要 关 键 词 本 文介绍了众鑫镍冶炼厂密闭鼓风炉 富氧熔炼前后 炉况 出现的变化和渣型的调整。 密 闭鼓 风炉 富氧熔炼 床能率 本床 精矿 渣 型 金 属回收率
项目 N i C u F e
工艺依据质检部 的各家精矿化验单数据 , 进行 分析 、 对 比。根据众鑫鼓风炉的特性进行配料 , 把易 熔 和难熔精矿 以一定 比例 , 进行混合 , 调配处适合众 鑫矿业鼓风炉的混合精矿 。表 2 为混合后精矿化验 结果。
表 2 混合后精矿化验结果表
合亚克斯采、 选厂, 收购周边选厂的镍精矿产品, 为 型的目的, 就是尽量降低渣含金属, 提高金属回收
卧式转炉吹炼 , 产品为水淬金属化高冰镍。众鑫 2 生产原料
冶炼厂于 2 0 0 7 年5 月投产 , 当年 投 产 即打 通 生 产 工
艺, 产 出合 格产品 。当时鼓风炉是空气熔炼 。空气 熔炼造成鼓风炉床能率低下 , 前、 本床温度低 。金属 产 品 产 量 偏 低 。随 着 周 边 选 厂 的增 加 和 扩产 , 镍精 矿产 品供应量大于众鑫熔炼要求 。在这种情况下公
和鑫
镜儿泉
5 . 2 9
O . 8 3 0 . 2 4 9 4 2 . 0 2 2 8 . 1 2 6 . 8 2
1 . 3 8
4 . 1 9
2 。 3 原料的物理特性 这五家精矿 , 都是 细粉状 矿 , 色泽 灰 、 黑。其 中 四家含水分一般都 在 1 3 %~ 1 4 . 5 %之 间 , 只有详论精 矿最湿 , 含水分 2 4 . 7 %。 2 . 4 精 矿 配料 和调 配后 的精 矿成 分
铜氧化矿的鼓风炉还原熔炼

銅氧化礦的鼓風爐還原熔煉Smelting Reduction of Copper Oxide Ore Blast Furnace文/邊瑞民 申殿邦 劉俊江東營方圓有色金屬有限公司摘要:本文系統介紹了銅氧化礦採用鼓風爐還原熔煉的基本原理、生產過程、常見故障及其處理方法、合理渣型的探討與建議等。
銅氧化礦還原熔煉工藝原是一項老技術,而現代銅冶煉工藝幾乎都將處理硫化礦生產技術作為研究重點。
因而銅氧化礦的鼓風爐還原熔煉有數十年無人研究與應用,很少有相關資料。
近年來,由於非洲礦產的開發,處理銅氧化礦問題又提上新的議事日程。
為此,東營方圓有色金屬有限公司(以下簡稱方圓公司)於2006年建設了依台處理銅氧化礦的舉行全水套鼓風爐(見圖1),爐體分別有上下水套組成,底部設有固定式本床。
爐料經計量後有加料小車通過提升機運送到加料平台人工上料,打鋼釬或燒氧間斷放渣放銅,爐渣經水碎後出售。
冷卻水循環使用,採用羅茨鼓風機供風。
煙氣依次經沉降冷卻室、漩渦收塵器、U型管冷卻器,使煙氣溫度降低到100℃以下,並使用其中的粗塵分離,再通過離心式引風機進入布袋室收塵後達標排空,其工藝流程(見圖2)。
爐子系負壓操作,車兼內外基本無煙塵,清潔環保,勞動環境優越。
圖1 銅氧化礦還原熔煉鼓風爐圖2 銅氧化礦還原熔煉流程圖方圓公司當時尚未建設銅的粗煉系統,而陽極爐產生的精煉渣無適當的設備進行處理,只能廉價出售。
銅氧化礦還原熔煉鼓風爐建成投產後,將精煉渣以適當的比例配入氧化礦中處理,效果很好。
該鼓風爐的原料主要有兩種,從南非等地進口的銅氧化礦以及自產的銅陽極爐精煉渣,屬連續作業,年開爐時間330天,處理料量50,000噸,其中銅氧化礦40,000噸,銅精煉渣10,000噸,生產粗銅10,000噸。
經多年的反覆生產實踐,技術條件不斷優化,工藝操作日趨成熟。
目前,爐子生產運行穩定,並實現了連續生產,大幅提升了爐子的作業率及處理能力,有效降低了生產成本。
铜密闭鼓风炉熔炼技术操作条件
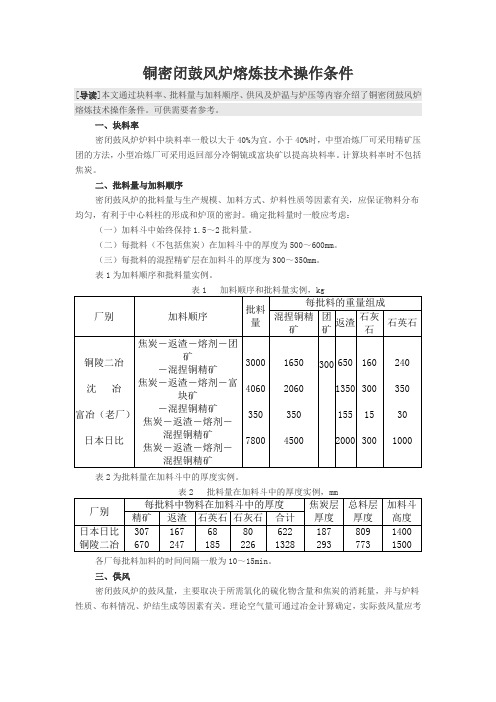
密闭鼓风炉的批料量与生产规模、加料方式、炉料性质等因素有关,应保证物料分布均匀,有利于中心料柱的形成和炉顶的密封。确定批料量时一般应考虑:
(一)加料斗中始终保持1.5~2批料量。
(二)每批料(不包括焦炭)在加料斗中的厚度为500~600mm。
(三)每批料的混捏精矿层在加料斗的厚度为300~350mm。
铜密闭鼓风炉熔炼技术操作条件
[导读]本文通过块料率、批料量与加料顺序、供风及炉温与炉压等内容介绍了铜密闭鼓风炉熔炼技术操作条件。可供需要者参考。
一、块料率
密闭鼓风炉炉料中块料率一般以大于40%为宜。小于40%时,中型冶炼厂可采用精矿压团的方法,小型冶炼厂可采用返回部分冷铜锍或富块矿以提高块料率。计算块料率时不包括焦炭。
340
420
470
烟气单体硫含量,g/m³0.78
0.35
密闭鼓风炉炉顶负压过高,漏入空气量增加,降低了烟气中二氧化硫浓度。但负压过低又会造成炉顶操作条件恶化,一般控制在50~100Pa为宜。表11为炉顶负压与烟气二氧化硫浓度的测定值。
表11 炉顶负压与烟气二氧化硫浓度的测定值
㎡
t/(㎡·d)
m³/min
%
m³/(㎡·d)
m³/t
10.5
38~45
390~400
21
30~38
~1400
10
40~45
330~400
21
33~40
~1240
2
40~45
75~80
21
38~40
~1320
1.5
45~50
50~55
21
33~37
~1060
2、风压 密闭鼓风炉的鼓风压力主要取决于炉内阻力,在一定范围内增加风压对熔炼过程有利。但风压过高会增加烟尘率和料层穿孔而跑空风。目前各厂的鼓风压力一般控制在8~10kPa。表4为鼓风压力实例。
3鼓风炉熔炼

二、密闭鼓风炉熔炼的基本原理
1、密闭鼓风炉的热工特性 、 铜精矿密闭鼓风炉熔炼属于半自热氧化熔炼, 铜精矿密闭鼓风炉熔炼属于半自热氧化熔炼,炉气 中含有较多的游离氧,炉内为氧化性气氛。 中含有较多的游离氧,炉内为氧化性气氛。冶炼过程所 需的热量由焦炭燃烧和冶炼过程本身的放热反应供给。 需的热量由焦炭燃烧和冶炼过程本身的放热反应供给。 密闭鼓风炉的炉料由混捏铜精矿、 密闭鼓风炉的炉料由混捏铜精矿、熔剂和固体转炉 渣。块料的容积比应在50%左右。 块料的容积比应在 %左右。
9
(3)本床区 ) 本床区位于焦点区下部,是汇集熔体和最后调整熔 本床区位于焦点区下部,是汇集熔体和最后调整熔 体成分的区域 在调整熔体成分的过程中, 的区域。 体成分的区域。在调整熔体成分的过程中,最主要的反 应是溶于炉渣中的少量Cu O被冰铜中的 被冰铜中的FeS再硫化 再硫化。 应是溶于炉渣中的少量Cu2O被冰铜中的FeS再硫化。 调整后的熔体经咽喉口流入前床。 调整后的熔体经咽喉口流入前床。
5
(1)预备区 ) 预备区位于炉子上部,温度大致从 预备区位于炉子上部,温度大致从250~600℃到 ℃ 1000~1100 ℃。两侧料柱温度比中心料柱温度高。 两侧料柱温度比中心料柱温度高。 在这一区域上部主要进行炉料的干燥和预热。 在这一区域上部主要进行炉料的干燥和预热。中心料柱 上部主要进行炉料的干燥和预热 只在中下部位发生炉料的干燥和预热。 只在中下部位发生炉料的干燥和预热。侧料柱中部和下 部,铜和铁的高价硫化物将发生分解。 铜和铁的高价硫化物将发生分解。 预备区为氧化气氛,部分固态硫化物将发生氧化,中心 预备区为氧化气氛,部分固态硫化物将发生氧化, 氧化气氛 料柱的氧化过程只在预备区下部才大理进行。 料柱的氧化过主要技术经济指标 、 密闭鼓风炉的主要技术经济指标是床能率、 密闭鼓风炉的主要技术经济指标是床能率、焦率和 铜的回收率。 铜的回收率。 床能率是以一昼夜内, 床能率是以一昼夜内,在单位风口区面积床面上熔 炼的炉料量(包括铜精矿、熔剂和转炉渣)来表示。它 炼的炉料量(包括铜精矿、熔剂和转炉渣)来表示。 主要取决于入炉风量、炉料的透气性和炉渣成分。 主要取决于入炉风量、炉料的透气性和炉渣成分。 焦率是用焦炭量与干炉料总量之百分比来表示的。 焦率是用焦炭量与干炉料总量之百分比来表示的。 焦率过低或过高均影响冶炼指标, 焦率过低或过高均影响冶炼指标,应在保证热平衡的条 件下,尽力降低焦率。 件下,尽力降低焦率。 下表列出了某些工厂的主要技术经济指标。 下表列出了某些工厂的主要技术经济指标。
铜富氧顶吹熔池熔炼节能设计
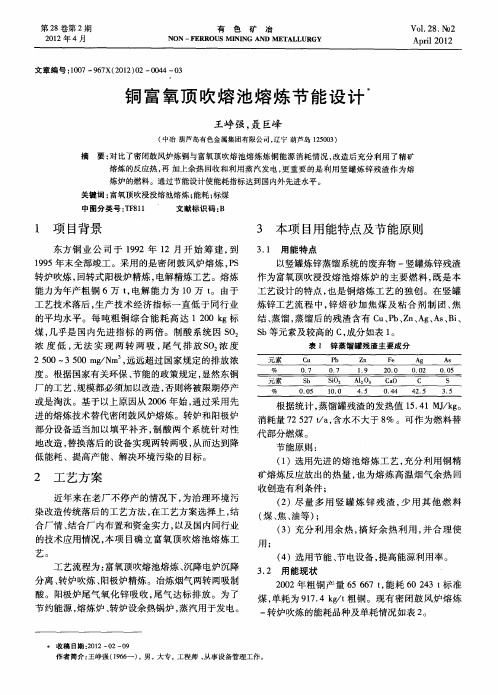
根据统计 , 蒸馏罐残渣的发热值 1 .1M / g 54 Jk 。
消耗 量 7 2 a含 水不 大于 8 。可作 为燃 料 替 257t , / % 代 部 分燃煤 。
节能 原则 :
( )选用 先进 的熔 池 熔 炼 工 艺 , 分利 用 铜 精 1 充 矿熔 炼反 应放 出 的热 量 , 为熔 炼 高 温 烟 气余 热 回 也 收创 造有 利条 件 ;
有
色
矿
冶
第2 8卷
( )使 用 较 高 的 铜 锍 品位 含 C 5 % 。铜 锍 品 4 u0 位 更高 时节 能效果 会 更 好 , 是 吹炼 工 序 热 平衡 不 但 易 掌握 , 会有 较多 冷料 , 返料 无法处 理 。
3 4 2 余 热 回收 ..
功损失 ;
( )采用节 能 型照 明灯具 ; 3 ( )电收尘 的高 温风 机采用 频调 速装 置 。 4
25 0— 0 / m , 远超 过 国家规 定 的排 放浓 0 35 0mg N 远
s 等元素及较高的 c 成分如表 1 b , 。
表 1 锌 蒸 馏 罐 残 渣 主 要成 分
室
; ; ;
! ! !
o. 5 0 l o O. 4. 5 o4 .4
转炉吹炼 , 回转式阳极炉精炼 , 电解精炼工艺。熔炼
能 力为 年产粗 铜 6万 t电解 能 力 为 1 , O万 t 由 于 。
工艺技术落后 , 生产技术经济指标一直低于同行业 的平均 水平 。每 吨 粗 铜 综 合 能 耗 高 达 120k 0 g标 煤, 几乎是国内先进指标 的两倍。制酸系统 因 S O 浓 度 低 , 法 实 现 两 转 两 吸 , 气 排 放 S 度 无 尾 O浓
- 1、下载文档前请自行甄别文档内容的完整性,平台不提供额外的编辑、内容补充、找答案等附加服务。
- 2、"仅部分预览"的文档,不可在线预览部分如存在完整性等问题,可反馈申请退款(可完整预览的文档不适用该条件!)。
- 3、如文档侵犯您的权益,请联系客服反馈,我们会尽快为您处理(人工客服工作时间:9:00-18:30)。
精矿封顶。 鼓风炉熔炼工艺简单,渣含铜低,投资省,建设快。其缺点是床能 率、脱硫率、铜锍品位均低,增加吹炼作业的时间,且能耗较大,一般 适用于规模较小的炼铜厂。 设备选择 有鼓风炉和鼓风机等。 (1)鼓风炉。为竖式炉型,有敞开式鼓风炉,料封式密闭鼓风炉及料钟 式密闭鼓风炉几种,几种鼓风炉炉顶结构不同,炉身结构相同。规格均 以炉床面积,即炉身风口区断面积表示,计算式为: 式中Q为日处理炉料量,t;ɑ为鼓风炉床能率,t/(m2?d)。大型鼓风 炉断面为矩形,一般风口区的长度不大于9m,宽度为1~1.4m。小型炉 多采用圆形,一般炉身采用水套冷却。60年代末,中国的鼓风炉炉身水 套由水冷改为软化水汽化冷却,产出0.2~0.3MPa的低压蒸汽。汽包须 设水位计、压力表安全阀等,以确保安全运行。铜鼓风炉熔炼的产物一 般在前床沉淀。炉子前床容积可按日处理100t炉料需要4.5~6m3计算。 (2)鼓风机。要求风量稳定、风压可调。设计时风量可按冶金计算所需 风量乘以过剩系数1.1~1.3考虑或按炉床断面积鼓风强度25~40m3/ (m2?min)计算,风压为8~10kPa。 车间配置 为便于铜锍运输,鼓风炉与转炉垂直配置,鼓风炉前床与 转炉配置于同一跨度内。车间内须设事故安全坑和地面防水措施。汽化 冷却系统的汽包须设在鼓风炉上方,高出水套最高点6m以上。 改进成效 不论敞口鼓风炉炼铜法还是由它发展而来的密闭鼓风炉炼 铜法,由于其烟气SO2浓度低,不能经济地回收,能源消耗高,难以大 型化等,已陆续停止使用或被先进炼铜方法所取代。密闭鼓风炉其缺点 是床能率、脱硫率、铜锍品位均低,增加吹炼作业的时间,且能耗较 大,一般适用于规模较小的炼铜厂。 近年来,我国先后在铜冶炼的铜陵密闭鼓风炉和白银熔池炉采用了富 氧熔炼技术。中国铜陵有色金属公司第二冶炼厂于1986年在两座10m。 密闭鼓风炉进行富氧鼓风的生产性熔炼试验,取得了较好效果。当鼓风 含氧30.5%时,同空气鼓风熔炼相比,床能力和脱硫率分别由42.7t /(m?d)和46.8%,提高到62.4t/(m?d)和57.2%,而焦率则由10. 2%降到6.46%。 目前,我国有色冶金系统常用的熔炼炉配煤率为5%-7%,即100吨 矿粉进去,需配上5-7吨煤。即便国际上先进的日本三菱法、加拿大诺 兰达法等炼铜工艺,配煤率也要4.8%或3.4%。由此看来,如鼓风炉入炉
块率保持较高,焦率还可稍降,与目前国内水平相接近。 实践表明,富氧熔炼不仅增加了熔炼能力,提高了烟气的502浓度,更重 要的是降低了能耗,是实现自热熔炼的主要手段。据北京有色金属研究 总院郭先健建立的铜精矿自热熔炼动态热平衡数学模型为:dQ/dt= (762.7+2313/Rs-665.5/RsXs-610.5/Yo_2)V模型的计算及分析结果表明,精 矿含硫量的增加有利于熔炼过程的热平衡。若精矿含硫分数低于0.25,采 用富氧对过程的热平衡产生负效应。在脱硫率为0.60时,对于精矿含硫分 数分别为0.30、0.35和0.45,实现自热熔炼的富氧浓度分别为70%,45%和 30%。当精矿含硫分数低于0.29时,提高脱硫率有利于过程的热平衡,而高 于0.29时,则不利于过程的热平衡。 对比项目 烟气SO2浓度(%) 床能率(t/m2*d) 焦率(%) 渣含铜(%) 脱硫率(%) 富氧浓度(%) 空气鼓风 3-5 40-50 8-12 0.2-0.3 40-55 富氧鼓风 5-7 50-60 6-8 0.2-0.3 40-55 24-27 (某厂富氧后指标对比) 结语 由于鼓风炉的诸多缺点,加之面临国家、社会环保意识的大幅提 高,环境保护、低"碳"经济已成为政府倡导产业发展的新方向,为此强 化对鼓风炉富氧熔炼的研究,以低改造成本强化冶金过程、提高冶炼经
的铜精矿,受到两侧上升气流的间接加热以及料柱重力的压力作用,而 发生固结,变成具有一定强度的精矿块。 焦点区 此区温度最高,为1523~1573K,气氛属强氧化性,进行半自 热熔炼的主要反应。几乎所有的焦炭都是在焦点区依靠鼓风中的氧来燃 烧。在焦点区内,被氧化的硫化物主要是FeS,其氧化产物随即与炉料 中的SiO2造渣。此外,在SO2存在的条件下,入炉转炉渣中的Fe3O4和预 备区形成的Fe3O4成为FeS的固体氧化剂,对反应(1)而言,1molO2的热 效应为406kJ;而反应(2),1molO2的热效应为343kJ,即焦炭燃烧的热效 应大于FeS氧化造渣的热效应。从热力学观点看,在焦点区焦炭优先被 氧化。而且,焦炭是以灼热固体状态进入焦点区,在被烧尽以前始终保 持固态不变;而FeS则以熔体状态通过焦点区,迅速地向下流动。由于 液体硫化物在焦点区停留时间很短,从动力学观点看,在焦点区FeS争 夺鼓风中氧的能力远远不如焦炭。所以硫化物的氧化主要在预备区进 行,它在焦点区被氧化的程度,主要取决于该处的焦炭量,亦即取决于 焦率。在工厂的生产实践中,通过调整焦率,即可有效地调节熔炼过程 的脱硫率和铜锍品位。在熔炼热平衡允许的条件下,要力求降低焦率以 增加硫化物的氧化程度,达到提高烟气中SO2浓度和获得较高品位铜锍 的目的。 本床区 炉子的风口水平以下部分为本床区,温度达1473~1523K。熔 炼的熔炼产物汇集于此,并连续地通过咽喉口和流槽流入前床,在前床 进行熔炼产物的澄清分离。本床在完成熔炼产物汇集、澄清的同时,还 起调整熔体成分的作用。其中最主要的反应是熔解在炉渣中的Cu2O被 铜锍中的FeS再硫化。鼓风强度是影响鼓风炉熔炼的一个重要参数,密 闭鼓风炉的基本原料铜精矿是以混捏料的形式加入炉内,从而限制了鼓 风强度。炉料中块料的比例对熔炼的技术经济指标有着明显的影响 工艺过程 鼓风炉熔炼的炉料从炉顶加入,从炉身下部两侧鼓风,一 般进行半自热熔炼,即除炉料中硫化物氧化等放出的热外,还须补充冶 金焦炭为燃料,在炉内完成炉料的部分焙烧脱硫、熔化、造锍和造渣等 过程。由于高温烟气的流动与炉料的运动呈对流形式,热效率高,生成 的铜锍和炉渣流入前床澄清分离。 料封式密闭鼓风炉熔炼直接处理铜精矿。要求铜精矿的硫铜比为1.1~ 1.5,二氧化硅含量不大于15%,氧化镁、三氧化二铝含量均不大于 5%。炉料的块料率占40%以上,通常加入熔剂、吹炼渣、含铜富块矿 等来作为块料,块料块度一般为30~80mm,铜精矿入炉前须经混捏, 混捏时加3%~5%的石灰粉,以增加铜精矿的粘结性,混捏后的铜精矿 含水14%~16%。加料顺序为:焦炭、吹炼渣、熔剂等,最后用混捏铜
焦炭从炉子上部加料口分批加入,靠其自身重力垂直向下移动,在高温 下,与从炉子下部两侧风口鼓入的空气或富氧空气相遇,发生各种反 应,而达到熔炼目的。熔炼产出的混合熔体进入炉底,通过本床咽喉流 入设于炉外的前床(见电热前床贫化)内进行铜锍与炉渣的澄清分离。炉 渣连续排放,铜锍按转炉吹炼的需要间断放出。产出的高温烟气,通过 炉内料柱的空隙上升,经炉顶排烟口进入排烟收尘装置。鼓风炉炼铜的 一般特征有四。(1)燃料在炉内燃烧,炉料与高温炉气成逆流运动,因而 热交换条件好,热利用率高达70%以上。(2)鼓风炉的最高温度带集中在 风口稍上的焦炭或硫化物激烈燃烧的所谓焦点区,焦点区最高温度可达 1723K。(3)焦点区的最高温度取决于炉渣的熔化温度和粘度等性质,以 及焦点区的热平衡;当炉渣成分一定时,强化燃料燃烧只能增加炉料的 熔炼量,而不能提高焦点区的温度。(4)在鼓风炉熔炼过程中,气相与炉 料之间的化学反应具有重要意义。 炼铜密闭鼓风炉 一种炉顶具有密封装置的鼓风炉。将传统敞开式鼓 风炉的烟罩取消,于加料台平面上安设一个加料斗把炉口封住,炉气由 加料台平面以下的排烟口进入排烟收尘系统。加料斗中经常保持有必要 数量的炉料,特别是致密性较好的混捏铜精矿,以保证炉口密闭。炉子 结构的其他部位,与传统敞开式鼓风炉大体相同。 密闭鼓风炉炼铜 铜精矿加水混捏(见铜精矿混捏)后,按规定比例配入 块状的熔剂、转炉渣和焦炭等,按焦炭-转炉渣-熔剂-混捏铜精矿,或转 炉渣与熔剂颠倒的顺序分批经由加料斗加入炉内。当炉料离开加料斗下 口时,块料自然地向两侧滚动,混捏精矿沿加料斗下口垂直下降到炉子 中心形成精矿料柱。于是炉子两侧便出现以块料为主而炉子中央则以混 捏精矿为主的状况,使炉内炉料分布不均匀。 由于炉料分布不均匀,炉气通过两侧较多,而流经中心的则很少。如 此,就导致炉子两侧温度比炉子中心高,越往上部,这种温差越大,在 接近风口水平时,这种温差变小。这种状况有利于混捏铜精矿在炉内发 生固结或烧结作用,为在鼓风炉内直接熔炼铜精矿创造了条件。但另一 方面,由于物料的偏析和炉气分布不均,使炉气与炉料之间以及炉料各 组分之间接触不良,削弱了硫化物氧化和造渣反应,这是密闭鼓风炉炼 铜床能力低[40~50t/(m2?d)]和铜锍含铜品位低的根本原因。 根据熔炼过程的特点,沿炉子高度可分为预备区,焦点区和本床区。 预备区 位于炉子上部,温度为523~873K至1273~1373K。在此区域 中进行炉料的干燥和预热,并发生铜和铁的高价硫化物离解及碳酸钙的 离解反应。预备区的气氛属于氧化性,部分硫化物被氧化。在预备区下 部,于温度较高的中央铜精矿柱的交界面上发生烧结作用。在料柱里面