3组主要气化工艺及8种典型气化炉图文详解
煤制天然气工艺流程图

煤制天然气工艺流程图煤制天然气是一种通过煤炭转化为天然气的工艺,其工艺流程可以分为煤气化、气体净化和气体转化三个主要步骤。
下面将对煤制天然气的工艺流程进行详细介绍。
第一步:煤气化煤气化是将煤炭通过高温和压力作用下转化为气体的过程。
首先,将煤炭破碎成适当大小的颗粒,然后进入煤气化炉。
在煤气化炉内,煤炭与一定量的氧气和水蒸气反应,产生一种称为合成气的气体。
合成气主要由一氧化碳、二氧化碳、氢气和甲烷等成分组成。
第二步:气体净化合成气中含有一些固体和液体杂质,需要进行净化处理。
首先,合成气经过除尘器去除其中的灰尘颗粒。
然后,经过吸收塔进行酸性气体的吸收,从而去除二氧化硫等物质。
接下来,通过变换器进行催化转化,将一氧化碳和二氧化碳转化为二氧化碳和甲烷。
最后,合成气经过低温除硫,去除其中的硫化物。
第三步:气体转化经过净化的气体进一步进行转化,产生天然气。
首先,将气体送入转化炉中,通过触媒的作用,使甲烷含量增加。
然后,将转化后的气体经过冷凝器冷却,将其中的液体分离出来,得到液态天然气。
最后,将气体通过压缩机进行压缩,得到压缩天然气。
煤制天然气工艺流程图如下:1. 煤炭破碎2. 煤气化炉3. 合成气4. 除尘器5. 吸收塔6. 变换器7. 低温除硫8. 转化炉9. 冷凝器10. 液态天然气11. 压缩机12. 压缩天然气以上是煤制天然气的工艺流程。
通过煤气化、气体净化和气体转化等步骤,煤炭可以被高效地转化为天然气,提供给人们使用。
这种工艺不仅可以减少对传统天然气资源的依赖,还可以促进煤炭资源的利用,实现能源的可持续发展。
气化炉设计简图及说明

生物质焦油催化裂解原理与石油的催化裂解相似,所以关于催化剂的选用可从石油工业中得到启发。
但是由于焦油催化裂解的附加值小,其成本要求很低才有实际意义。
所以人们除了利用石油工业的催化剂外,还大量研究了低成本的材料,如石灰石,石英砂和白云石等天然产物。
大量的实验表明,很多材料对焦油裂解都有催化作用,其中效果较好又有应用前景的典型材料主要有三种,即木炭,白云石,镍基催化剂,主要性能如下图示:从上面三种典型催化结果比较可知,镍基催化剂的效果最好,在750℃时既有很高的催化裂解率,而其他的材料在750℃裂解的效果还不理想,但由于镍基催化剂较昂贵,成本较高,一般生物质气化技术难以应用,所以只能在气体需要精制或合成汽油的工艺中使用。
木炭的催化作用实际上在下吸式气化炉中既有明显的效果,但由于木炭在催化裂解焦油的同时参与反应,所以消耗很大(在1000℃时达0.1kg/m³)对大型生物质气化来说木炭作催化剂不现实,但木炭的催化作用对气化炉的设计及小型气化炉有一定的指导意义。
白云石(dolomite)是目前为止研究的最多和最成功的催化剂,虽然各地白云石的成分略有变化,但都有催化效果一般当白云石中的CaCO3/MgCO3在1-1.5时效果较好。
白云石作为焦油裂解催化剂的主要优点是催化效率高,成本低,所以具有很好的使用价值。
气化炉简图其中还原区中放置炽热焦炭以促进焦油、二氧化碳的还原反应,焦油在热分解区裂解温度大约为1000℃左右,而吹入的空气与物料混合燃烧,这一区域叫做氧化区,温度约为900——1200℃,产生的热量用于支持热裂解区裂解反应和还原区的还原反应的进行;氧化区的上部为裂解区,温度约为300——700℃,在这一区域,生物质中的挥发分(裂解气,焦油以及水分)被分离出来;热解区的上部为干燥区,物料在这一区域被预热;氧化区的下部为还原区,氧化区产生的二氧化碳、炭和水蒸气在这一区域进行还原反应,同时残余的焦油在此区域发生裂解反应,产生以一氧化碳、氢气为主的产出气,这一区域的温度约为700——900℃来自热解区富含焦油的气体必须经过高温氧化区和以炽热焦炭为主的还原区,其中焦油在高温下被裂解,从而使产出气中的焦油含量大为减少。
气化炉工艺流程课件教材
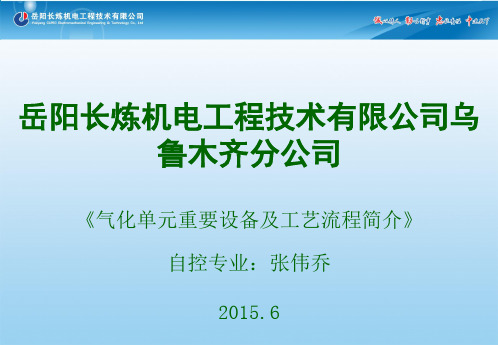
பைடு நூலகம்渣系统
•
来自气化炉激冷室的的渣水流入锁斗。从锁斗上部引出相对干净的水,用锁斗循 环泵将其送至气化炉激冷室底部,通过这股水的循环,将激冷室底部的渣和其它固体 冲至锁斗。 在一个预设的时间周期(通常约30分钟)之后,自动计时器启动一次锁 斗卸料循环。在卸料循环过程中,气化炉与锁斗之间的切断阀关闭,锁斗循环泵连接 锁斗的正常吸入口切断,锁斗循环泵至气化炉的循环水以最小流量送至泵自身的入口 。锁斗通过与锁斗冲洗水罐相连的管道卸压。卸压后,向卸压管线中通入灰水冲洗固 体颗粒。然后打开锁斗出口阀将渣和水送至渣池内的捞渣机上。在打开锁斗出口阀前 ,暂时关闭渣池隔离阀,使带有捞渣机的这部分渣池与另一部分隔离开,便于渣的沉 淀和送出。 在卸料期间,打开锁斗冲洗水罐底部出口阀,用较干净的灰水置换锁斗 中的水和渣。在到达设定时间后或锁斗冲洗水罐到达低液位时将锁斗出口阀关闭,这 样可以确保锁斗中仍充满水。当锁斗放空达到高限液位或灰水泵开始向锁斗冲洗罐中 注入灰水时,将锁斗冲洗水罐出口阀关闭。用高压冷凝液或来自高压灰水泵的除氧水 给锁斗充压。当锁斗与气化炉之间的压差小于给定值时,重新打开锁斗入口阀。同时 ,打开锁斗至锁斗循环泵的阀门,关闭锁斗循环泵回流阀。整个卸料循环(降压、卸 料、水置换、充压)用时约2 分钟。 大约5 分钟后重新打开渣池隔离阀,碳渣水流 入。渣池泵将渣池干净侧的渣水送至黑水闪蒸系统的第一真空闪蒸罐。 如果需要, 可将一股临时灰水注入渣池干净的一侧以稀释渣水的固体含量。 在气化炉预热循环 阶段,激冷室中的水排入渣池。预热水泵将预热水送回激冷环。
三、锁斗 锁斗(位号:2220-V-1001~8001)是供气化炉工作时储存经激冷之后的熔渣、黑 水及气化炉在连接操作的情况下向外排渣和黑水之用的设备,是气化关键设备之一。 根据锁斗功能的特点,本装置的锁斗承压在 0~6.68Mpa 的交替循环压力荷 载工况下工作。锁斗需按应力分析方法进行疲劳设计,要求应力循环次数为:2 次/小时,16000 次/年,锁斗设计寿命 20 年,总循环次数为 320000 次。 操作压力:0~6.58(max:6.78)MPa 操作温度:59(max:122)℃ 设计压力:7.46/-0.1Mpa 设计温度:278℃ 排渣次数:2 次/小时 设备规格:D×H=2000x6300 设备材质:Q345R+S31603(堆焊) 腐蚀裕量:0mm
生物质气化发电 气化反应器
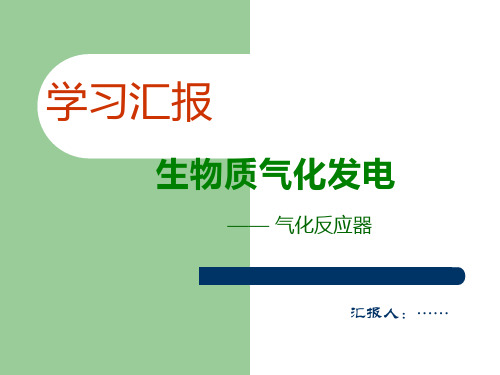
下吸式气化炉的结构原理图
生物质从气化炉的上部加入,新生物质落在物质最上层,处在干燥 区内,在这里由于受内胆的热辐射,生物质内的水分吸收热量被蒸发, 变成干物料。之后随着下部物料的氧化消耗向下移动到热分解区,热分 解区的温度高到可以让热分解反应发生干生物质开始发生热分解反应生 成炭、气体和焦油等。生成的炭随着物料的消耗而继续向下落入氧化区 。作为气化剂的空气,一般在氧化区加入。在该区,由热分解区生成的 炭与气化剂中的氧进行燃烧反应生成一氧化碳、二氧化碳,并放出大量 的热能,这是生物质气化全过程的保证。没有反应的炭继续下落进入还 原区。在还原区内二氧化碳被还原成一氧化碳;炭还与水蒸气反应生成 氢气和一氧化碳,灰渣则排入灰室中。生成的可燃气流过炉栅进入外腔 后被导出。炉体中温度分布大致为:干燥区温度为100~300,裂解区温度 为500~700,氧化区温度达1000~1200,还原区的温度为700~900。 在干燥区和热分解区生成的一氧化碳、二氧化碳、氢气、焦油等产 物一起通过下面的氧化和还原区。由于氧化区温度高,焦油在通过该区 时发生裂解,变为可燃气体,因而下吸式气化炉产出的可燃气热值相对 较高,而焦油含量相对较低。
6.5.2.5增压流化床气化炉
增压循环流化床气化炉的炉膛压力可以 高达0.5~2MPa。与常压循环流化床气化炉相 比,增压循环流化床气化炉的炉腔截面热强 度可提高10倍左右,在炉容量相同时,增压 循环硫化床炉的尺寸课显著减小,产生的高 压可燃气体无需升压可直接进入燃汽轮机发 电。
固定床气化炉结构特征是有一个容纳原料的炉膛和一个 承托反应料层的炉栅。根据气化炉内气流运动的方向,固定 床气化炉又可分为下吸式气化炉、上吸式气化炉、横吸式气 化炉及开心式气化炉四种类型。
6.5.1.1 下吸式气化炉
上下吸式生物质燃气炉技术图纸讲解

这是一款秸杆气化炉简图.优点:目前各种品牌秸杆气化炉商们宣扬的优点我的小炉都具备;二、秸杆气化炉(简图)说明炉体1;炉体高100厘米;直径40厘米;三毫米厚铁板焊成。
出气口3;出气口是1寸管短接头,焊接在水封槽7下方.捅料杆4;用8毫米x 70厘米钢筋做成T字型。
保温层5; 用保温材料做5厘米厚’30厘米高的保温层,如无保温材料,用普通泥土做也行, 我就是用普通泥土做的.进风口6;是一段13厘米长的1寸管,焊在离炉底5厘米的地方,伸进炉壁内8厘米,炉壁外留5厘米.水封槽7;在炉体上口内环做5厘米深,3厘米宽的槽,使用时里面装满水.落灰坑8;在炉底下方做一个15厘米直径,5厘米深的坑。
出灰口9;是一段5厘米粗的管子.三、制作要点:1;因炉内压力不大炉盖用水密封,这样开启方便,密封也好,(类似南方广大农村淹菜用水密封的坛子口,三木.飞马。
火距。
小康等产品也都是这样用水密封的。
)2;设捅料杆的作用,因炉内底料烧空后上部燃料不会自动落下,这时用捅料杆捅一下让上部燃料落下不至于终断制气.(很多集中供气的大型秸杆气化炉也存再燃烧驾空问题,也是用人工捅才能落料.)3;进风口6应装在离炉底10厘米以下的地方,若离炉底过高则产气不好或不产气.(也就是说炉内不能装炉篦子和留专门灰渣层).4;做一个落灰坑8,可以降低出灰口的加工工艺,不需要加工丝扣,随便扣个盖就行,使用起来方便。
5; 安装时进风口6和鼓风机之间应装一个阀门,停止工作时先关闭阀门再关闭鼓风机。
这样可以防止回火.这点很重要。
注》1:炉具不需装炉篦子;2:进风口6应装在离炉底10厘米以下的地方,若离炉底过高则产气不好或不产气,进风口是一段13厘米长的1寸铁管;3:落灰坑就是个凹下去的坑,大小要求不严,有无不引响产气;4: 不必用喷嘴,以前三木炉子早期产品有使用,现在也不用了,缺点是易堵塞,需要经长更换。
四、秸杆气化炉简图2(这是更详细秸杆气化炉简图)五、以下是上吸式小型秸秆气化炉照片外观图俯瞰图全用碎料时的燃烧效果图六、以下是某厂家生产的炉体的各主要部件,均由生铁铸造而成;上封盖水封槽储料桶底座环保气化炉结构图七、气化炉的燃料应用范围:秸杆、松树叶、玉米杆、玉米芯、高粱杆、豆杆、枯树叶、杂草、花生壳、锯沫、刨花等一切可燃植物。
煤气化工艺流程图及主要的工艺控制点
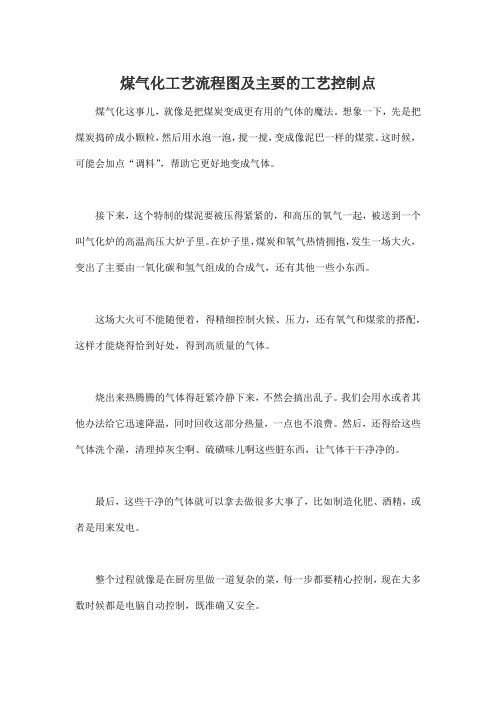
煤气化工艺流程图及主要的工艺控制点煤气化这事儿,就像是把煤炭变成更有用的气体的魔法。
想象一下,先是把煤炭捣碎成小颗粒,然后用水泡一泡,搅一搅,变成像泥巴一样的煤浆。
这时候,可能会加点“调料”,帮助它更好地变成气体。
接下来,这个特制的煤泥要被压得紧紧的,和高压的氧气一起,被送到一个叫气化炉的高温高压大炉子里。
在炉子里,煤炭和氧气热情拥抱,发生一场大火,变出了主要由一氧化碳和氢气组成的合成气,还有其他一些小东西。
这场大火可不能随便着,得精细控制火候、压力,还有氧气和煤浆的搭配,这样才能烧得恰到好处,得到高质量的气体。
烧出来热腾腾的气体得赶紧冷静下来,不然会搞出乱子。
我们会用水或者其他办法给它迅速降温,同时回收这部分热量,一点也不浪费。
然后,还得给这些气体洗个澡,清理掉灰尘啊、硫磺味儿啊这些脏东西,让气体干干净净的。
最后,这些干净的气体就可以拿去做很多大事了,比如制造化肥、酒精,或者是用来发电。
整个过程就像是在厨房里做一道复杂的菜,每一步都要精心控制,现在大多数时候都是电脑自动控制,既准确又安全。
煤炭气化方法—熔融床气化工艺(煤气化技术课件)
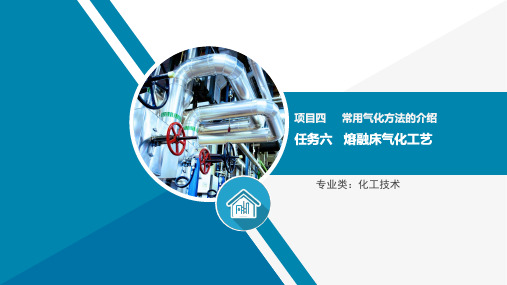
1
+
知识点
2
3
知识点1 鲁麦尔熔渣气化炉
熔渣黏度在这一气化方法中起着重要作用
• 一方面,它影响渣池内粉煤 和气化剂之间盼反应速度, 熔渣黏度越小,则流动性越 好,进入渣池内的反应物质 容易形成气泡,使反应面积 迅速增加,气化反应速度相 应加快。相反,渣的黏度大, 流动性差,气化物质形成气 泡的速度低,反应面积小, 反应速度相应降低。
熔渣池的深度约500mm,其中的三氧化二铁是一种廉价的有效助熔剂,大体上可维持灰的熔点在 1200℃以下,能够保证渣液的良好流动性。
知识点2 熔盐气化法
在单筒气化炉内分成气化区和燃烧区两部 分,两区的下部连通。气化压力约 2.79MPa , 熔 盐 池 的 温 度 为 950~1000℃ 。 粉煤和水蒸气混合后从气化炉的下部鼓泡 进入气化区,在此快速气化。没有气化完 的碳随熔盐由气化区循环进入燃烧区,在 燃烧区,残碳和空气(或氧气)进行燃烧反应, 放出的热量将熔盐加热。
另一方面,熔渣黏度决定了熔渣在渣池内流动时 具有一定的黏滞性,使得粉煤在渣池内的停留时间延 长,有利于提高煤的气化强度,使气化彻底。和前述 几种类型的气化过程相比,移动床气化时,气化强度 较低;流化床气化时,气化强度高但气化不彻底。因 而熔融床气化基本保留了两者的优点,克服了两者的 不足之处。
生成的混合气体逸出熔渣池时,将液面层上的末气化粉煤粒带走,在上升的过程中一部分继 续气化,一部分被气体带出气化炉,经过气固分离的粉煤粒可以返回炉内进一步气化,因而该法 的碳转化率可达99%左右。
此法在操作时,将空气预热到600℃左右,从而 保证气化炉的温度。在炉内加入碳酸钙的目的是起助 熔剂的作用,同时还可以除去部分硫。但为了避免出 现熔渣含硫太高而使流动性变差,一般要求煤的含硫 量约4%~8%。
煤气化工艺
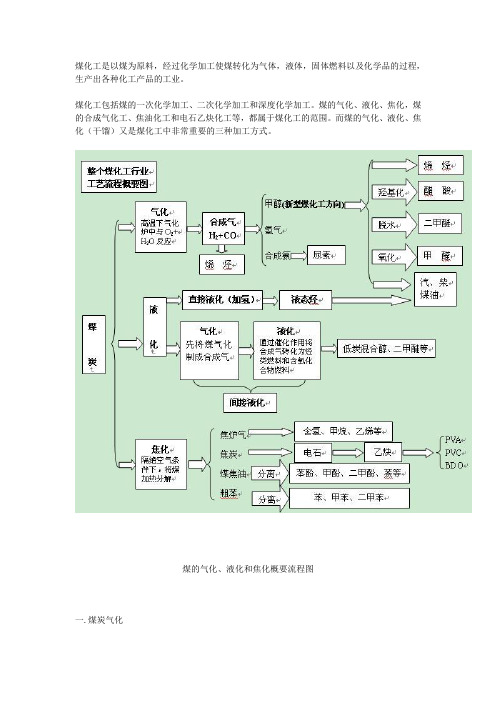
煤化工是以煤为原料,经过化学加工使煤转化为气体,液体,固体燃料以及化学品的过程,生产出各种化工产品的工业。
煤化工包括煤的一次化学加工、二次化学加工和深度化学加工。
煤的气化、液化、焦化,煤的合成气化工、焦油化工和电石乙炔化工等,都属于煤化工的范围。
而煤的气化、液化、焦化(干馏)又是煤化工中非常重要的三种加工方式。
煤的气化、液化和焦化概要流程图一.煤炭气化煤炭气化是指煤在特定的设备内,在一定温度及压力下使煤中有机质与气化剂(如蒸汽/空气或氧气等)发生一系列化学反应,将固体煤转化为含有CO、H2、CH4等可燃气体和CO2、N2等非可燃气体的过程。
煤的气化的一般流程图煤炭气化包含一系列物理、化学变化。
而化学变化是煤炭气化的主要方式,主要的化学反应有:1、水蒸气转化反应C+H2O=CO+H22、水煤气变换反应CO+ H2O =CO2+H23、部分氧化反应C+0.5 O2=CO4、完全氧化(燃烧)反应C+O2=CO25、甲烷化反应CO+2H2=CH46、Boudouard反应C+CO2=2CO其中1、6为放热反应,2、3、4、5为吸热反应。
煤炭气化时,必须具备三个条件,即气化炉、气化剂、供给热量,三者缺一不可。
煤炭气化按气化炉内煤料与气化剂的接触方式区分,主要有:1) 固定床气化:在气化过程中,煤由气化炉顶部加入,气化剂由气化炉底部加入,煤料与气化剂逆流接触,相对于气体的上升速度而言,煤料下降速度很慢,甚至可视为固定不动,因此称之为固定床气化;而实际上,煤料在气化过程中是以很慢的速度向下移动的,比较准确的称其为移动床气化。
2) 流化床气化:它是以粒度为0-10mm的小颗粒煤为气化原料,在气化炉内使其悬浮分散在垂直上升的气流中,煤粒在沸腾状态进行气化反应,从而使得煤料层内温度均一,易于控制,提高气化效率。
3) 气流床气化。
它是一种并流气化,用气化剂将粒度为100um以下的煤粉带入气化炉内,也可将煤粉先制成水煤浆,然后用泵打入气化炉内。
- 1、下载文档前请自行甄别文档内容的完整性,平台不提供额外的编辑、内容补充、找答案等附加服务。
- 2、"仅部分预览"的文档,不可在线预览部分如存在完整性等问题,可反馈申请退款(可完整预览的文档不适用该条件!)。
- 3、如文档侵犯您的权益,请联系客服反馈,我们会尽快为您处理(人工客服工作时间:9:00-18:30)。
3组主要气化工艺及8种典型气化炉图文详解!一、气化简介气化是指含碳固体或液体物质向主要成分为H2和CO的气体的转换。
所产生的气体可用作燃料或作为生产诸如NH3或甲醇类产品的化学原料。
气化的限定化学特性是使给料部分氧化;在燃烧中,给料完全氧化,而在热解中,给料在缺少O2的情况下经过热降解。
气化的氧化剂是O2或空气和,一般为蒸汽。
蒸汽有助于作为一种温度调节剂作用;因为蒸汽与给料中的碳的反应是吸热反应(即吸收热)。
空气或纯O2的选择依几个因素而定,如给料的反应性、所产生的气体用途和气化炉的类型。
气化最初的主要应用是将煤转化成燃料气,用于民用照明和供暖。
虽然在中国(及东欧)气化仍有上述用途,但在大多数地区,由于可利用天然气,这种应用已逐渐消亡。
最近几十年中,气化主要用于石化工业,将各种碳氢化合物流转换成"合成气",如为制造甲醇,为生产NH3提供H2或为石油流氢化脱硫或氢化裂解提供H2。
另外,气化更为专门的用途还包括煤转换为合成汽车燃料(在南非应用)和生产代用天然气(SNG)(至今未有商业化应用,但在70年代末和80年代初已受到重视)。
二、气化工艺的种类有多种不同的气化工艺。
这些工艺在某些方面差别很大,例如,技术设计、规模、参考经验和燃料处理。
最实用的分类方法是按流动方式分,即按燃料和氧化剂经气化炉的流动方式分类。
正像传统固体燃料锅炉可以划分成三种基本类型(称为粉煤燃烧、流化床和层燃),气化炉分为三组:气流床、流化床和移动床(有时被误称为固动床)。
流化床气化炉完全类似于流化床燃烧器;气流床气化炉的原理与粉煤燃烧类似,而移动床气化炉与层燃类似。
每种类型的特性比较见表1。
表1 各种气化炉比较* 如果在气化炉容器内有淬冷段,则温度将较低。
1.气流床气化炉在一台气流床气化炉内,粉煤或雾化油流与氧化剂(典型的氧化剂是氧)一起汇流。
气流床气化炉的主要特性是其温度非常高,且均匀(一般高于1000℃),气化炉内的燃料滞留时间非常短。
由于这一原因,给进气化炉的固体必须被细分并均化,就是说气流床气化炉不适于用生物质或废物等类原料,这类原料不易粉化。
气流床气化炉内的高温使煤中的灰溶解,并作为熔渣排出。
气流床气化炉也适于气化液体,如今这种气化炉主要在炼油厂应用,气化石油原料。
现在,运营中的或在建的几乎所有煤气化发电厂和所有油气化发电厂都已选择气流床气化炉。
气流床气化炉包括德士古气化炉、两种类型的谢尔气化炉(一种是以煤为原料,另一种以石油为原料)、Prenflo气化炉和Destec气化炉。
其中,德士古气化炉和谢尔油气化炉在全世界已有100部以上在运转。
2.流化床气化炉在一个流化床内,固体(如煤、灰)悬浮在一般向上流动的气流中。
在流化床气化炉内,气体流包含氧化介质(一般是空气而非O2)。
流化床气化炉的重要特点(像流化床燃烧器一样)是不能让燃料灰过热,以至熔化粘接在一起。
假如燃料颗粒粘在一起,则流化床的流态化作用将停滞。
空气作为氧化剂的作用是保持温度低于~1000℃。
这表示流化床气化炉最适合用比较易反应的燃料,如生物质燃料。
流化床气化炉的优点包括能接受宽范围的固体供料,包括家庭垃圾(经预先适当处理的)和生物质,如木柴,灰份非常高的煤也是受欢迎的供料,尤其是那些灰熔点高的煤,因为其他类型的气化炉(气流床和移动床)在熔化灰形成熔渣中损失大量能。
流化床气化炉包括高温温克勒(HTW),该气化炉由英国煤炭公司开发,目前由Mitsui Babcock能源有限公司(MBEL)销售,作为吹空气气化联合循环发电(ABGC)的一部分。
在运转的大型流化床气化炉相对较少。
流化床气化炉不适用液体供料。
3.移动床气化炉在移动动床气化炉里,氧化剂(蒸汽和O2)被吹入气化炉的底部。
产生的粗燃料气通过固体燃料床向上移动,随着床底部的供料消耗,固体原料逐渐下移。
因此移动床的限定特性是逆向流动。
在粗燃料气流经床层时,被进来的给料冷却,而给料被干燥和脱去挥发分。
因此在气化炉内上下温度显着不同,底部温度为1000℃或更高,顶部温度大约500℃。
燃料在气化过程中脱除挥发分意味着输出的燃料气含有大量煤焦油成分和甲烷。
故粗燃料气在出口处用水洗来除去焦油。
其结果是,燃料气不需要在合成气冷却器中来高温冷却,假如燃料气来自气流反应器,它就需冷却。
移动床气化炉为气化煤而设计,但它也能接受其他固体燃料,比如废物。
有两项主要的移动床气化炉技术。
20世纪30年代开发出早期的鲁尔干法排灰气化炉,已广泛应用于城市煤气的生产,在南非用于煤化学品生产。
在该气化炉内,床层底部温度保持在低于灰熔点,这样煤灰就可作为固体排出。
20世纪70年代,鲁尔公司,然后是英国煤气公司(现在的BG plc)开发了底部温度足以使灰熔化的液态排渣炉。
这种气化炉称为BGL (BG-Lurgi)气化炉。
目前,有几台BGL气化炉在电厂安装,用来气化固体废物和共同气化煤和废物。
三、典型气化炉以下按字母顺序介绍一些最重要的和众所周知的气化工艺。
1.BGL气化炉(移动床)BGL气化炉最初开发于20世纪70年代,用来提供一种高甲烷含量的合成气,为用煤生产代用天然气(SNG)提供一种有效方法。
这种气化炉15年以前由英国煤气公司在法夫的Westfield开发中心开发的,开始是为试验用该工艺生产SNG的适用性,后来用于IGCC。
(图1 BGL 气化炉)块煤和像石灰石这样的助熔剂送入一闸斗仓,定期往气化炉的顶部送料(见图1)。
一个缓慢旋转的分配器盘将煤均匀地分布在床的顶层。
对于粘结性煤给料,分配器被联接到一搅拌器,也维持床层均匀,和防止煤团聚。
当床层下降,煤料经过一些反应。
这些反应能在燃料床的不同高度分成三个层:上层煤被干燥和脱挥发分;中层被气化;低层被燃烧,产生的CO2作为中段的气化剂。
O2和蒸汽经床底部喷咀(喷口)加入。
产生的熔渣在气化炉底部形成熔渣池,定期排出。
气化炉容器有耐火材料衬里,以防止床层过多热量损失。
由于耐火材料被煤床本身与床层的最热部分(喷口的顶端)隔开,因此不经受高温。
气体在450-500℃的温度离开气化炉,气体中含有因煤脱挥发分而产生的焦油和油以及从床层淘析出的煤粉。
这由安装在气体出口的淬冷容器脱除。
气体同时由一水淬冷装置冷却和清洁。
然后气体通过一系列交换器,使气体在脱硫前冷却到室温。
气体中脱除的焦油和水转入一个分离器,焦油和煤尘从那里再循环到气化炉的喷咀(一部分可加在气化炉上部,用来抑制煤尘的扬析)。
BGL气化炉具有很高的冷气体效率,即,与其他气化炉比较,煤原有热值(CV)的大部分在气体中作为化学能出现,而非热能。
这样,BGL 气化炉不像其他气化炉中的谢尔和德士古系统那样要求有高温热交换器。
因此,气化区和CCGT装置很少紧密结合,因为气体冷却系统不直接与蒸气轮机循环结合。
BGL系统同气流床系统相比,燃气轮机产生的电力较多,蒸气轮机产生的电力较少。
BGL气化炉能处理给入气化炉顶部的块状供料里含的大量粉煤(即<6mm),取决于煤的粘结性,如匹兹堡No.8这样的高膨胀、高粘结性煤,其高达35%可作为粉煤给料。
但是,原煤一般按重量计含有40-50%的粉煤。
因此,气流床气化炉所有用煤要先经研磨,在BGL装置,煤要先经筛分。
BG实验了气化炉利用粉煤的多种方式,将粉煤送入风咀,或干法输送,或以煤浆形式,或用沥青作为粘结剂将它们压制成型煤。
目前,由法夫电厂再度交付使用的Westfield的现有的、备用的气化炉作为电厂的一部分将用煤和污泥发电120MWe。
法夫电厂已申请建立第二座较大(400MWe)电厂,使用煤和城市固体废物(MSW)来发电。
2.Destec(气流床)Destec工艺是煤浆入料、加压、两段式工艺。
该工艺最初由Dow 化学公司于20世纪70年代开发。
随着中试规模和样机试验,1984年决定在Dow的普莱克明(路易斯安那)化学联合企业建立商业化装置,1987年该装置投入运营。
1989年,Dow将气化和其余电力从公司脱离出,另成立一公司,80%由Dow所有,称为Deslec 公司。
同时,该技术已被选来用于印第安纳州的沃巴什河的IGCC电厂增容项目。
气化炉(图3)由衬有未冷却的耐火材料的压力壳构成。
图3 Destec气化炉在气化炉的下(第一)段有两个气化燃烧器,在上段有煤的进一步喷入点。
煤制成约60%固体(按重量计)的浆状。
大约80%的煤浆同O2一起注入到下段的两个燃烧器中,在约1350-1400℃和大约30巴压力下不完全燃烧。
煤中的灰熔化,下落至容器并经排放口进入水冷却装置。
在第一段形成的燃料气向上流动到气化炉的第二段,剩余的20%煤浆在第二段注入和反应,经热解和气化,并将气体冷却到大约1050℃。
这两段工艺有增加合成气热值的作用。
然后粗合成气在一燃烧管合成气冷却器内冷却。
然后冷却的合成气用过滤器净化,去除大量灰分和半焦颗粒。
这些半焦可以再循环至气化炉。
唯一在运转的Destec气化炉在沃巴什河IGCC电厂,该电厂以烟煤作原料。
多年来,用次烟煤和石油焦作原料的进行了大量的试验。
3.高温温克勒(HTW)(流化床)HTW工艺是在原有温克勒流化床气化工艺的进一步发展。
原温克勒工艺最初于20世纪20年代开发和利用,是一项常压工艺。
HTW工艺由莱茵褐煤公司发明,莱茵褐煤公司拥有并经营德国鲁尔地区的几座褐煤煤矿。
HTW工艺最初是为生产铁矿石用的还原气而开发;后来兴趣转向生产合成气,再后来转向发电。
所有的应用是在褐煤气化基础上进行。
目前重点放在废塑料气化领域。
莱茵褐煤公司仍负责HTW工艺的开发,克鲁勃伍德公司从事销售和供应。
莱茵褐煤公司在弗雷兴建设一座中试厂,该厂从1978年至1995年运转。
额定工作压力10巴,每小时处理1.8t。
1985年在科隆附近Berrenrath建成一座示范装置。
该装置工作压力10巴,所产的合成气用管道输送至在Wesseling 附近的甲醇合成厂。
Berrenrath厂使用蒸气和O2作为气化介质。
1989年出于开发工艺用于发电目的,在Wesseling开始建工作压力25巴的中试厂。
那时,褐煤的气化,同在气化前预干褐煤的流化床工艺结合起来,被视为用莱茵褐煤以高效、洁净方式发电的最佳办法。
该项工作最终是设计吹气HTW气化炉为基础的IGCC电厂,名为KoBRA (Kombikraftwerk mit Lnlegrietier BRAunkohlvergasung褐煤气化联合循环)。
最初的KoBRA装置准备建在科隆附近的戈尔登堡电站,但是,出于经济问题的考虑,该项目现已中止。
现在,下一代褐煤电厂愿意采用高效传统Pf锅炉。
随着KoBRa IGCC项目的消亡,研究重点转向废物气化。
在Berrenrath 厂已就废塑料和污物的气化进行试验研究。
克鲁勃现已开发一种工艺,称之PreCon,在此工艺中,HTW气化炉与废料的预处理和灰的后处理结合生产化学品或发电用的合成气。