石材切削力与切削刀具研究
切削速度和切削力的关系

切削速度和切削力的关系
切削速度和切削力是数控加工中两个十分重要的参数。
切削速度是切削刀具在单位时间内切削的长度,一般用米/分钟表示;而切削力则是切削刀具在切削时受到的力的大小,一般用牛顿表示。
这两个参数之间存在着一定的关系。
在数控加工中,切削速度越快,切削力也会随之增大。
这是因为切削速度越快,刀具进给时与工件接触的时间越短,每个接触时间内需要切削更多的材料,因此需要更大的力来进行切削。
另外,当切削速度过高时,还会加剧切削刀具的磨损,从而降低切削质量。
因此,在确定切削速度时,需要综合考虑切削质量和切削效率之间的平衡。
除了切削速度,切削力还受到其他因素的影响,如切削深度、切削角度、刀具形状等。
因此,在进行数控加工时,需要根据具体工件的要求和材料特性,选择合适的切削参数,以确保切削质量和效率的最优化。
- 1 -。
PCD刀具的性能特点

PCD刀具的性能特点金刚石刀具具有硬度高、抗压强度高、导热性及耐磨性好等特性,可在高速切削中获得很高的加工精度和加工效率。
金刚石刀具的上述特性是由金刚石晶体状态决定的。
在金刚石晶体中,碳原子的四个价电子按四面体结构成键,每个碳原子与四个相邻原子形成共价键,进而组成金刚石结构,该结构的结合力和方向性很强,从而使金刚石具有极高硬度。
由于聚晶金刚石(PCD)的结构是取向不一的细晶粒金刚石烧结体,虽然加入了结合剂,其硬度及耐磨性仍低于单晶金刚石。
但由于PCD烧结体表现为各向同性,因此不易沿单一解理面裂开。
PCD刀具材料的主要性能指标①PCD的硬度可达8000HV,为硬质合金的8~12倍;②PCD的导热系数为700W/mK,为硬质合金的1.5~9倍,甚至高于PCBN 和铜,因此PCD刀具热量传递迅速;③PCD的摩擦系数一般仅为0.1~0.3(硬质合金的摩擦系数为0.4~1),因此PCD刀具可显著减小切削力;④PCD的热膨胀系数仅为0.9×10^-6~1.18×10^-6,仅相当于硬质合金的1/5,因此PCD刀具热变形小,加工精度高;⑤PCD刀具与有色金属和非金属材料间的亲和力很小,在加工过程中切屑不易粘结在刀尖上形成积屑瘤。
PCD刀具的应用工业发达国家对PCD刀具的研究开展较早,其应用已比较成熟。
自1953年在瑞典首次合成人造金刚石以来,对PCD刀具切削性能的研究获得了大量成果,PCD刀具的应用范围及使用量迅速扩大。
目前,国际上著名的人造金刚石复合片生产商主要有英国DeBeers公司、美国GE公司、日本住友电工株式会社等。
据报道,1995年一季度仅日本的PCD刀具产量即达10.7万把。
PCD刀具的应用范围已由初期的车削加工向钻削、铣削加工扩展。
由日本一家组织进行的关于超硬刀具的调查表明:人们选用PCD刀具的主要考虑因素是基于PCD刀具加工后的表面精度、尺寸精度及刀具寿命等优势。
金刚石复合片合成技术也得到了较大发展,DeBeers公司已推出了直径74mm、层厚0.3mm的聚晶金刚石复合片。
切削理论

切削功率
• 切削功率消耗在切削过程中的功率称为切削功率 Pm • 切削功率为切削力Fc和进给力Ff所消耗功率之和, 因背向力Fp没有位移,所以不消耗功率。于是切 削功率为 • Pm =10-3( Fc*vc + Ff*vf/1000) • Fc----切削力(N) • Vc----切削速度(m/s) • Ff----进给力(N) • Vf----进给速度(mm/s)
切屑形态
• 硬脆非金属材料主要有工程陶瓷、玻璃及石材等被切削陶瓷在刀刃挤 压作用下,在刀刃附近产生裂纹,裂纹先向前下方扩展,深度超过切 削深度,而后一边前进一边向上方扩展,最后穿过工件上部的自由表 面,此时形成较大的薄片状切屑,并在切削表面上留下凹痕,这种情 况称之为大规模挤裂。如果从这种状态下继续切削,实际切除的只是 崩碎后的残留部分,这时发生小规模挤裂,生成切削表面上较平滑的 部分。 • 小规模挤裂是在切削深度较小时发生的,工件材料以粒状或粉末状的 切屑被切除。此时发生破碎和不发生破碎的交界线,与刀具前刀面前 方材料的最大切应力面的位置相一致,因此,可以认为此时的破碎是 由于切应力引起的。大规模挤裂是在切削深度大的情况下发生的,崩 碎切屑的脱落是由于所受应力超过材料的抗拉强度。因此,硬脆材料 的切除过程是以断裂破坏为主的过程,这与一般金属材料的切除过程 有很大不同。 • 崩碎切屑形成过程中力的波动很大,因此,加工硬脆材料时,宜选用 韧性好的刀具材料,采用负前角刀具,并以小的切削深度进行。
切削力影响因素
• 刃倾角: • 在很大的范围(从-40°——40°)内变化时,对,Fc没有 什么影响,但λs减小时,Fp增大,Ff减小 • 刀尖半径: • 刀尖半径对Fc的影响不大。刀尖半径增大时,Fp将增大。 • 刀具材料 • 刀具与被加工材料间的摩擦因数,直接影响着切削力的大 小。在同样切削条件下,高速钢刀具的切削力最大,硬质 合金次之,陶瓷刀具最小刀具后刀面磨损后,接触摩擦增 大,因而切削力增大;刀具前刀面上因磨损而形成月牙洼 时,由于增大了前角,因此切削力减小 • 切削液和刀具状况
金属切削原理中切削力效果的仿真模拟研究

金属切削原理中切削力效果的仿真模拟研究随着工业技术的快速发展,金属切削加工在各个领域中都扮演着重要的角色。
而在金属切削加工过程中,切削力效果的研究对于提高切削加工的效率和质量具有重要的影响。
本文将以金属切削原理中切削力效果的仿真模拟研究为题,探讨金属切削过程中切削力的影响因素以及仿真模拟的方法。
首先,我们需要了解金属切削加工中切削力的概念和作用。
切削力是指在金属切削过程中刀具对工件产生的力。
它是通过与工件表面接触形成的摩擦力和切削力的合力,用于克服金属材料的强度和硬度,从而将金属材料切削成预定形状和尺寸的零件。
切削力直接影响着切削加工的效率、切削工具的寿命以及加工表面质量等方面。
在金属切削过程中,切削力的大小和方向受到多种因素的影响。
首先是刀具的几何形状和刀具材料的选择。
刀具的刃角、刃宽以及刀具材料的硬度和耐磨性等因素都会直接影响切削力的大小。
其次是被切削材料的性质。
材料的硬度、塑性和热导率等特性都会对切削力产生影响。
此外,切削速度、进给量和切削深度等工艺参数也会对切削力产生影响。
因此,研究这些影响因素对切削力的影响是非常必要的。
为了研究金属切削过程中切削力效果,研究人员常常采用仿真模拟的方法。
仿真模拟可以通过建立切削力的数学模型和计算机模拟技术,准确预测切削过程中的切削力大小和方向,并分析各种影响因素对切削力的影响。
其中,有限元法是一种常用的仿真模拟方法。
有限元法是一种数值计算方法,广泛应用于工程领域中的结构力学和材料力学问题。
在金属切削过程中,有限元法可以通过将切削区域划分成许多小块,建立小块上的切削力模型,并通过求解数学方程组来计算切削力的大小和方向。
通过调整模型中的参数,如刀具几何形状、工件材料特性、切削速度等,可以得到不同情况下的切削力效果。
此外,还可以使用商业仿真软件来进行金属切削过程中切削力效果的仿真模拟研究。
这些软件通过提供各种切削过程的模型和计算工具,能够更加方便地进行切削力的预测和分析。
坚德PCD

坚德PCD(人造聚晶金刚石)刀具的简介金刚石刀具具有硬度高、抗压强度高、导热性及耐磨性好等特性,可在高速切削中获得很高的加工精度和加工效率。
坚德金刚石刀具的上述特性是由金刚石晶体状态决定的。
在金刚石晶体中,碳原子的四个价电子按四面体结构成键,每个碳原子与四个相邻原子形成共价键,进而组成金刚石结构,该结构的结合力和方向性很强,从而使金刚石具有极高硬度。
由于聚晶金刚石(PCD)的结构是取向不一的细晶粒金刚石烧结体,虽然加入了结合剂,其硬度及耐磨性仍低于单晶金刚石。
但由于PCD烧结体表现为各向同性,因此不易沿单一解理面裂开。
坚德PCD刀具材料的主要性能指标:①PCD的硬度可达8000HV,为硬质合金的80~120倍;②PCD的导热系数为700W/mK,为硬质合金的1.5~9倍,甚至高于PCBN和铜,因此PCD刀具热量传递迅速;③PCD的摩擦系数一般仅为0.1~0.3(硬质合金的摩擦系数为0.4~1),因此PCD刀具可显著减小切削力;④PCD的热膨胀系数仅为0.9×10 -6~1.18×10 -6,仅相当于硬质合金的1/5,因此PCD刀具热变形小,加工精度高;⑤PCD刀具与有色金属和非金属材料间的亲和力很小,在加工过程中切屑不易粘结在刀尖上形成积屑瘤。
PCD刀具的应用工业发达国家对PCD刀具的研究开展较早,其应用已比较成熟。
自1953年在瑞典首次合成人造金刚石以来,对PCD刀具切削性能的研究获得了大量成果,PCD刀具的应用范围及使用量迅速扩大。
目前,国际上著名的人造金刚石复合片生产商主要有英国De Beers公司、美国GE公司、日本住友电工株式会社等。
据报道,1995年一季度仅日本的PCD刀具产量即达10.7万把。
PCD刀具的应用范围已由初期的车削加工向钻削、铣削加工扩展。
由日本一家组织进行的关于超硬刀具的调查表明:人们选用PCD刀具的主要考虑因素是基于PCD刀具加工后的表面精度、尺寸精度及刀具寿命等优势。
PCD刀具
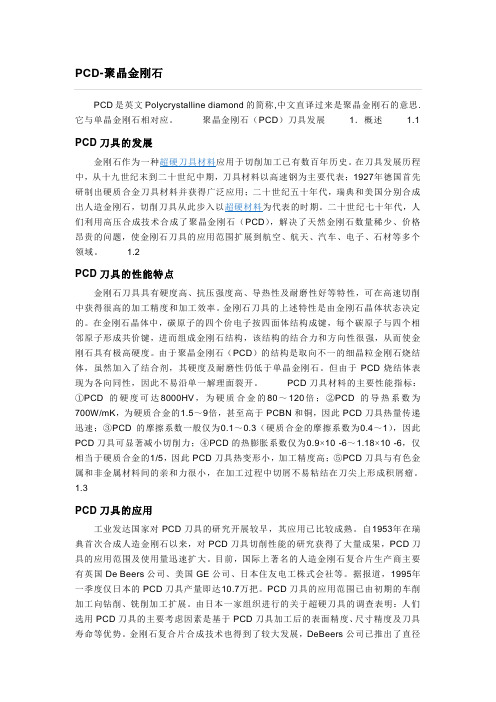
PCD-聚晶金刚石PCD是英文Polycrystalline diamond的简称,中文直译过来是聚晶金刚石的意思.它与单晶金刚石相对应。
聚晶金刚石(PCD)刀具发展1.概述 1.1PCD刀具的发展金刚石作为一种超硬刀具材料应用于切削加工已有数百年历史。
在刀具发展历程中,从十九世纪末到二十世纪中期,刀具材料以高速钢为主要代表;1927年德国首先研制出硬质合金刀具材料并获得广泛应用;二十世纪五十年代,瑞典和美国分别合成出人造金刚石,切削刀具从此步入以超硬材料为代表的时期。
二十世纪七十年代,人们利用高压合成技术合成了聚晶金刚石(PCD),解决了天然金刚石数量稀少、价格昂贵的问题,使金刚石刀具的应用范围扩展到航空、航天、汽车、电子、石材等多个领域。
1.2PCD刀具的性能特点金刚石刀具具有硬度高、抗压强度高、导热性及耐磨性好等特性,可在高速切削中获得很高的加工精度和加工效率。
金刚石刀具的上述特性是由金刚石晶体状态决定的。
在金刚石晶体中,碳原子的四个价电子按四面体结构成键,每个碳原子与四个相邻原子形成共价键,进而组成金刚石结构,该结构的结合力和方向性很强,从而使金刚石具有极高硬度。
由于聚晶金刚石(PCD)的结构是取向不一的细晶粒金刚石烧结体,虽然加入了结合剂,其硬度及耐磨性仍低于单晶金刚石。
但由于PCD烧结体表现为各向同性,因此不易沿单一解理面裂开。
PCD刀具材料的主要性能指标:①PCD的硬度可达8000HV,为硬质合金的80~120倍;②PCD的导热系数为700W/mK,为硬质合金的1.5~9倍,甚至高于PCBN和铜,因此PCD刀具热量传递迅速;③PCD的摩擦系数一般仅为0.1~0.3(硬质合金的摩擦系数为0.4~1),因此PCD刀具可显著减小切削力;④PCD的热膨胀系数仅为0.9×10 -6~1.18×10 -6,仅相当于硬质合金的1/5,因此PCD刀具热变形小,加工精度高;⑤PCD刀具与有色金属和非金属材料间的亲和力很小,在加工过程中切屑不易粘结在刀尖上形成积屑瘤。
石材背切角度如何计算公式

石材背切角度如何计算公式石材背切角度计算公式。
石材背切角度是在石材加工过程中非常重要的一个参数,它直接影响到石材的加工质量和效率。
正确的背切角度可以确保石材切割的平整度和精度,同时也可以减少切割时的损耗和浪费。
因此,石材背切角度的计算是石材加工过程中必不可少的一部分。
石材背切角度的计算公式可以通过几何学的原理来推导。
在石材加工中,为了使得切割后的石材表面平整,通常会采用背切的方式,即在切割时将刀具倾斜一定角度。
这个角度就是背切角度。
背切角度的大小不仅取决于石材的硬度和材质,还与刀具的类型和切割速度有关。
因此,在实际应用中,需要根据具体情况来确定背切角度的大小。
在石材加工中,背切角度的计算公式可以通过以下几个步骤来推导。
首先,我们需要确定石材的硬度和材质。
石材的硬度和材质直接影响到切割时产生的切削力和切削热。
一般来说,硬度较大的石材需要更大的背切角度,而硬度较小的石材则需要较小的背切角度。
其次,我们需要确定刀具的类型和切割速度。
不同类型的刀具在切割时产生的切削力和切削热也不同,因此需要根据刀具的类型和切割速度来确定背切角度的大小。
最后,根据石材的硬度和材质以及刀具的类型和切割速度,可以通过以下公式来计算背切角度:背切角度 = arctan(切削力 / 切削热)。
其中,arctan表示反正切函数,切削力和切削热是根据实际情况测量得到的。
通过这个公式,我们可以根据具体的情况来确定石材的背切角度,从而确保石材加工的质量和效率。
需要注意的是,以上公式只是一个简化的计算方法,实际应用中可能还需要考虑更多的因素,比如刀具的磨损、切割时的冷却方式等。
因此,在实际应用中,可能还需要根据具体情况来进行调整和修正。
总之,石材背切角度的计算是石材加工过程中非常重要的一部分。
通过合理的背切角度计算,可以确保石材加工的质量和效率,减少浪费和损耗,提高加工的经济效益。
因此,在石材加工过程中,需要根据具体情况来确定合适的背切角度,从而实现最佳的加工效果。
55°菱形刀片参数

55°菱形刀片参数一、刀片介绍菱形刀片是一种常用的切削工具,其刀片角度为55°。
该刀片具有许多特点,包括尖端锋利、切削力小、切削效率高等优点。
在各类加工领域中广泛应用,如金属加工、木材加工、塑料加工、石材加工等。
为了更好地了解和应用55°菱形刀片,有必要对其参数进行详细的讨论。
二、刀片参数刀片参数是指影响刀片性能的各项参数,包括刀片材质、刃角、刃口宽度等。
1. 刀片材质菱形刀片通常采用硬质合金或高速钢制造。
硬质合金刀片具有硬度高、耐磨性好的特点,适用于加工硬材料;而高速钢刀片则具有韧性好、断裂率低的特点,适用于加工大批量的工作。
2. 刃角刃角是指刀片刃口与刀具轴线之间的夹角。
对于55°菱形刀片来说,刃角一般为55°,这样的刃角可以使刀片具有较大的进刀角度范围,适用于多种加工情况。
3. 刃口宽度刃口宽度是指刀片刃口的有效切削长度。
刃口宽度的选择与加工材料的硬度有关,一般来说,刃口宽度越大,切削效率越高,但是也会引入较大的切削力。
三、刀片选择与使用在实际使用中,正确选择和使用菱形刀片是保证加工质量和效率的关键。
以下是一些刀片选择与使用的注意事项:1. 根据加工材料选择刀片不同材料的加工需要选择不同材质和参数的刀片。
硬质合金刀片适用于加工较硬的材料,而高速钢刀片适用于加工较软的材料。
刀片的刃角和刃口宽度也应根据加工材料的硬度和尺寸进行选择。
2. 控制切削速度和进给量刀片的切削速度和进给量是影响切削效果的重要因素。
切削速度过高易导致刀片磨损加剧,刀片寿命缩短;进给量过大则容易导致刀片断裂。
因此,在使用菱形刀片时,要根据具体情况合理控制切削速度和进给量。
3. 刀片的定期检查和更换刀片在长时间的使用过程中会出现磨损和断裂的情况,这时需要及时检查并更换刀片。
定期检查刀片的状态,及时更换磨损严重的刀片可以保证加工质量和效率。
4. 刀片的保养和润滑刀片在使用过程中需要进行必要的保养和润滑工作。
- 1、下载文档前请自行甄别文档内容的完整性,平台不提供额外的编辑、内容补充、找答案等附加服务。
- 2、"仅部分预览"的文档,不可在线预览部分如存在完整性等问题,可反馈申请退款(可完整预览的文档不适用该条件!)。
- 3、如文档侵犯您的权益,请联系客服反馈,我们会尽快为您处理(人工客服工作时间:9:00-18:30)。
石材切削力与切削刀具研究 广东工学院 王成勇 大连理工大学 刘培德 胡荣生
提要 本文对石材的切削力和切削刀具进行了研究,给出了若干切削力经验公式,优选了刀具材辩及其几何参数 和切削参数.井培出了刨槽刀具的最佳形状
天然石材的切削加工法包括刨削、铣 削 钻孔和车削等工艺,既便是金钢石结块 锯的锯切加工以及磨削加工,也是通过刀具 上无数刀刃切削工件的。本文对石材的切削 力和切削刀具进行了实验研究。 实验方法 (一)切削力洲试实验采用QB一05 型铣削测力仪,YD一15型动态应变仪和Sc 16型光线示波器,测量切削力的最大 值、波动幅值和平均值。每一实验点测试两 次,取其平均值为测试结果。工件材料为辉 绿岩 花岗岩和大理石(肖氏硬度分别为 79、101和58)。刀具材料为YG8。刀具前 角Y=一10 ̄30。 后角a=8~8。,切削深 t=0·04~0.8毫米,切削宽W=3.4~6毫 米,切削速度v=7.59 ̄30.99米/分。实验 采用干式刨削法. 略 5 面 矗 (二)切削刀具性能实验采用YG8和 YDl5两种材料的刀具。测量后刀面砉损量 VB值,观察、测试刀具前后刀面的磨损和破 损、 削噪声、切槽宽和刨槽蜊表面质量。 工件材料为黑云母花岗岩和细粒花岗岩(石 英含量分剐为>25%秆3 )。实验采用逐层 创削法加工淘槽,每刨削l米对刀具的冲击 (切入切出)为10次。刀具前角T=5~一lO 、 后角口:5~8。、副偏角1。30 、刀刃宽W: 6.5毫米 水冷却,刨削刀片型号C306 二石材切削力经验公式 (一)t口 条件对切烈力的影响 囝 1~6给出在刨削实验过程中,切削的深度t、 宽度W、速度v和刀具前角Y及工件材料种 类等与最大水平切削力FH…、最大垂直切 削力Fv…、平均切酎力FH、FV以及切削 力波动幅值DFH,DFV的关系曲线。
W 薄虞 {} 却划、 (a) (b) (C) 图1切剐深度t和刀具前角丫对切州力的影响 (大理石.V胃7.56米/分,w兰6毫米;囤由0l 一10。.△:Y=20。,x:Y鼻30。)
(1)切削深度t对切削力的影响:I主i图 1~3可知,切削力随切削深度的增加而大致 呈指数增加.在切削深度较JJ、时,切削力增
加幅度较大 在辉缘岩和大理岩切削深度大
5;
维普资讯 http://www.cqvip.com 于O.4毫米、花岗岩研 谭)芟大TO.2毫米 时,切削力随着切削深度增fJ口而增加的幅度 减小.就这三种岩石而. l刃削深度对水平
科 窘t奢}’ (a)
方向切 4力及其波动幅值的影响均大于对垂 直方向的影响。切削力Lt(FV/FH)则随着切 削深度的增加而下降,切削力比均小于1。
封暮囊 督 , (b) 蒯鬣蓝‘t和
(c) 图2切削深度t和刀具前角丫对切削力的影响 (侮绿岩.V 7.56米/分,w=6毫米;图巾C:Y=一10。.△:T-20。,x: ̄--30‘)
(a) (b) (C) 图3 切削深度t和刀具前角丫对切削力的影响 (花街岩,V工7.56米/分,w 5毫来;图南0:T葺O。I x:丫c一10。I●。y--lO·)
由于切削深度较大时,切削力随切自 深 度增加而增nⅡ的幅度较小, 印屑为大块断 屑,因此,在机珠性能和刀具强度许可范围 [^】,应尽量取较大的切削深度进行切削,以 提高切削效率。但对加工表面的质量有要求 H{,9llI应采用小深度切削。 (2)刀具前角Y对切削力的影响:由图 1~3可见,切削力随刀具前角的增大而呈减 小趋势,这种趋 大致随切削深度的增加而 加强,但刀具前角对垂直方向切削力的影响 程度较水平方向小 切削力波动幅值大致随 刀具前角的增大面藏小。显然,在保证刀具 有一定强度的前提下,刀具前角取较大值可 降低切削力。 54 (3)切削宽度W和切削速度v对切削 力的影响:切削力及其波动幅值,随切削宽 度的增加大致呈线性增加(图4)}切削力 随切削速度的增加呈波动状态。从整体上 看,在实际范围内,切削速度对切削力的影 响较小,可以忽略(图5)。 (4)工件材料种类对切削力的影响: 由图6可知,切削力及其波动l陌值,随工件 的肖氏硬度增加而增加。 (=)切削力经验公式在生产中,通 常需要估计最大切削力及其波动幅值,以便 设计加工机械、刀具和夹具,由于切削力主 要受卯削深度t、刀具前角T和工件材料种类 的影响,且加工过程中,一次切削深度通常
一 硅;;喜 ~/ 一 维普资讯 http://www.cqvip.com 小于2毫米,刀具前角 一般也在一1O‘左 右,因此,在切削速度对切削力的影响忽略 不计、切削力与切削宽度成正比的前提下, 麓可由图l~3获得在v=7.56米/分、T= 1O‘的条件下石材切削力的经验公式(表 1),以供生产应用。对于不同的石材种类, 还可参考图6,大致估算切削力值。
2 6。r l i ^/ ∞f i《垄兰=二
星 }睾I === : 州 口 ID 2。 ∞ 韧l4蔫燕t孙)
图5切脚速度对切削力的影响 C夫理岩,tl0 4鼍米 W尊6鼍米一7---10。)
三石材切削刀具研究 台理选择刀具材料致其几何参数和切削 参数等,对于提高切舰效率和加工件表面质 量,降低加工成本是极为重要的.下面仅就 其研究结果概述之.
图6工件材料种类对单位切州宽 度切削力的影响 (丫;10’,t‘O 2毫米,V正7.S6术,分) (一)刀具材料选择石材切削采用的 硬质台金材料主要有:YGcG,YG8、 YGIIC、YGIl和YG15等,新型硬质台金 材料YGRM(YD15)和610 已用于硬岩 切削加工.目前,广泛用于石材加工的金刚 石刀具,由于制作技术等原因,尚不能有效 地应甩于坚硬石材的加工。实验结果表明, 切削坚硬石材时,YD15刀片的耐磨性远远 大于YG8刀片,其一次刃磨有效切削长发可 达2O~3O米,这是目前较好的刀具材料。 (;)月具几何参数选择实验结果表 明,当刀具前角为5 和一5‘时,随着切削距 离的增加,前刀面均出现破损}当刀具前角 为一l0。时,在切削过程中刀具无破损现象, 并且后刀面磨损量最小;当刀具后角为8‘ 时,刀具磨损较小,无破损现象,并有良好 的切削性能。综上所述,刀具前,后角越
石材切刖力垣譬公式 囊l 切削力 1 FH… 1 Fv… FH FV DFH DFV 『…~————一—— 花 岩 2l4.It·…w j 67.8t w 126.5tI。·sW 34.2t●.● W 207.9t* I 9W 63.0t 0。, W
蜱绿岩 !l33.2t’ “w 24.5t。 3 aW 78.2t‘ ¨W “ gt0.3 W 102.7t●。,W 18.8t‘。¨W ^ 岩 “-5t。。。 w I 7·2t ‘’w 29.St·’- W 4t0‘‘W 64t*。tW 6 5t‘.·tW
往l刀刃觉w,切 4诨t的单位为毫米;切嘲力为牛蛾-
冬 ^ 一 ● ●q, 品薹 IJ p
维普资讯 http://www.cqvip.com 小,刀具磨损越大,越易破损,切削噪声和 振动越大。采用YDl5材质刀具切削坚硬石 材最佳刀具前角为一10。后角,为8。. (三)切削参数选择随着切削深度的 增加,后刀面磨损量减小,同时切削力也增 加I但刀具与石材的接触面积也增大,因而 切靓深度在一定范围内对刀具强度影响不 大。在加工质量要求许可时,采用0.6~0.8 毫米左右的切削深度,可获得较好的切削效 率,同时刀具磨搅 I旦较小一且无破损现象 发生。 虽然切削速度越高,切削效率也越高, 但对刀具的对I击和切削振动也越大。实验结 果表明,为避免刀具破损,采用低速度大切 深(切削速度8米/分左右、切深0.6~0.8毫 米)切削较台适。 (四)刨槽刀具几何彤状选择在生产 中,硬质板材锯切广泛地采用刨槽加工。在 甸槽过程中,工件在刀刃例面材料的影响 下,实际槽宽因便4面断裂而大于切削宽度。 只有当刨削深度增至一定值而侧裂纹不能扩 展至工件表面时,切削宽度始与刨槽宽相 等。倒槽侧面的裂纹不仅降低加工质量,且 易在工件的相邻刨槽问产生断裂。 从切削比能和咖削量来看,普通形状刨 刀的切削性能最好。因为脊形刀具等在切削 过程中有刨向分力作用;V形刀具虽然可使 切觏平稳,但因其前刀面作用力较大而刀尖 易破损,且还因其两切刃磨损不对称而易产 生侧向分力。在侧向分力作用下,不仅在相 邻槽间产生断裂,还易扎刀。因此,普通形 状刨槽刀是硬岩刨槽刀具的基本型式。 通常,板材锯切槽宽为8毫米,为此拟 采用两把刀具组合切削。第一把刀(A)主 刀刃宽6毫米,为增加刀尖强度,并防止切 屑堵槽造成崩刃和打刀,将A刀两铡刀尖磨 出1×45。的倒角(图7a)。在用来刨削花岗 岩并取切削深度为O.6~O.8毫米时,实际切 出的槽口宽约7毫米(图8).第二把刀(B) 应使槽宽最终达到8毫米,并形成台乎质量 要求的刨槽侧面。为此,要在刀尖磨出 O.5×45。的倒角。因B刀切靓量较小,切屑 堵塞不易产生,为使刨槽侧面质量较高,在 B刀L还磨有一小段侧修光刃(图7b)。这 种形状的刀具除使槽底宽达7毫米并起到修 光槽底作用外,当A刀再次以0.6~0.8毫 米的切深切槽时,侧裂纹仍可扩展到自由表 面而不会在刨槽侧面L产生断裂; 外,还 可保证^刀F一撒切削·幔利,避免因切槽过 深而产生扎刀 采用组合A、B刀的刨槽实验结果表 嘣,可 快速和高质量地刨削硬岩。
(a) (b) 圈7 A,B刀切刺I刃形厦几何参敷 (T一一19。,a-8。一刀片型号:A刀C396,B刀f:308 单位;毫米)
l 蒋E 穗 口 j睾踣
削jf莨承) 凰8 A刀切削槽口宽度与切削深度关系 (黑云母花崮岩.YDIS刀片;Y-一19’,a·8’, V一7.7米/分)
参考文献}(I)希禾,饰面石材开采与加工. 建筑工业 版汪,1986 ̄(2)棘^菏.采静,岩石破碎学. 煤炭工韭出版藏;(3)王应勇,如培德,陈培元,大理石 轮置嘲表面形成机理,州等料置县与置嘲》,疆2,1 7p
维普资讯 http://www.cqvip.com