第三章催化裂化催化剂 1什么是催化裂化 催化裂化是指石油的高
催化裂化

类型
移动床催化裂化用的是小球硅酸铝催化剂。流化床催化裂化用的是微球硅酸铝催化剂。现代提升管催化裂化 用的是微球分子筛催化裂化催化剂。控制短的接触时间可以减少缩合反应,减少焦炭的生成。所用原料为减压馏 分油、焦化蜡油、脱沥青油等馏分油者,称馏分油催化裂化;所用原料为常压渣油、减压渣油或馏分油中掺入渣 油,都称渣油催化裂化。
沿革
催化裂化催化裂化技术由法国E.J.胡德利研究成功,于1936年由美国索康尼真空油公司和太阳石油公司合作 实现工业化,当时采用固定床反应器,反应和催化剂再生交替进行。由于高压缩比的汽油发动机需要较高辛烷值 汽油,催化裂化向移动床(反应和催化剂再生在移动床反应器中进行)和流化床(反应和催化剂再生在流化床反 应器中进行)两个方向发展。移动床催化裂化因设备复杂逐渐被淘汰;流化床催化裂化设备较简单、处理能力大、 较易操作,得到较大发展。60年代,出现分子筛催化剂,因其活性高,裂化反应改在一个管式反应器(提升管反 应器)中进行,称为提升管催化裂化。中国1958年在兰州建成移动床催化裂化装置,1965年在抚顺建成流化床催 化裂化装置,1974年在玉门建成提升管催化裂化装置。1984年,中国催化裂化装置共39套,占原油加工能力23%。
高低并列式特点是反应时间短,减少了二次反应;催化剂循环采用滑阀控制,比较灵活。
同轴式装置形式特点是:①反应器和再生器之间的催化剂输送采用塞阀控制;②采用垂直提升管和90°耐磨 蚀的弯头;③原料用多个喷嘴喷入提升管。
工艺流程
催化裂化的流程主要包括三个部分:①原料油催化裂化;②催化剂再生;③产物分离。原料喷入提升管反应 器下部,在此处与高温催化剂混合、气化并发生反应。反应温度480~530℃,压力0.14~0.2MPa(表压)。反应 油气与催化剂在沉降器和旋风分离器(简称旋分器),分离后,进入分馏塔分出汽油、柴油和重质回炼油。裂化气 经压缩后去气体分离系统。结焦的催化剂在再生器用空气烧去焦炭后循环使用,再生温度为60称分布物料喷嘴进入提升管,并喷入燃油加热,上升过程中开始在高温和催 化剂的作用下反应分解,进入沉降器下段的气提段,经汽提蒸汽提升进入沉降器上段反应分解后反应油气和催化 剂的混合物进入沉降器顶部的旋风分离器(一般为多组),经两级分离后,油气进入集气室,并经油气管道输送 至分馏塔底部进行分馏,分离出的催化剂则从旋分底部的翼阀排出,到达沉降器底部经待生斜管进入再生器底部 的烧焦罐。
催化裂化
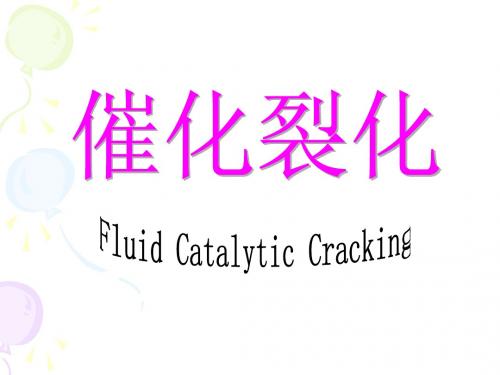
胜利
0.23 0.29 <0.02 0.2~0.4 4.7 8.5 4.8 39.2
2.以重油为裂化原料时会遇到以下技术困难: ①焦炭产率高 原因是:
重油的H/C比较低,含稠环芳烃多,胶质沥青质含量高;
重金属污染催化剂 引起一系列的问题,主要有: 再生器烧焦负荷大 焦炭产率过高,会大大破坏装置的热平衡 装置能耗增大
5~10
6~8
二:催化裂化的发展过程
分解等反应生成气体、汽油等小分子产物
催化裂化反应
缩合反应生成焦炭
反应:吸热过程
催化裂化 再生:放热过程
催化裂化的发展可以分成以下几个阶段:
1.天然白土和固定床催化裂化 2.合成硅铝催化剂和移动床催化裂化
①移动床催化裂化
②流化床催化裂化
3.分子筛催化剂和提升管催化裂化
次反应
二次反应并非对我 们的生产都有利,应 适当加以控制
为了获得较高轻质油收率,不追求反应深度过大,而是在
适当反应深度的基础上对未反应原料进行回炼 “未反应原料”是指反应产物中沸点范围与原料相当的那 一部分,称回炼油或循环油 目前我国的催化裂化装置采用的反应温度一般比国外低
三:渣油催化裂化
芳香基原料油、催化裂化循环油或油浆(其中含有较多的稠
环芳烃)较难裂化,要选择合适的反应条件或者先通过预处理
来减少其中的稠环芳烃而使其成为优质的裂化原料,如循环 油可作如下处理: 加氢→含环烷烃较多→优质裂化原料 溶剂抽提分理出芳烃(化工原料)→裂化
2.复杂的平行—顺序反应
重质石油馏分
中间馏分
烷烃
烯烃
①反应速度比烷烃快得多; ②氢转移显著,产物中烯烃、尤其 是二烯烃较少。
①反应速度与异构烷烃相似; ②氢转移显著,同时生成芳烃。 ①反应速度比烷烃快得多; ②在烷基侧链与苯环连接的键上断 裂。
催化裂化催化剂主要成分
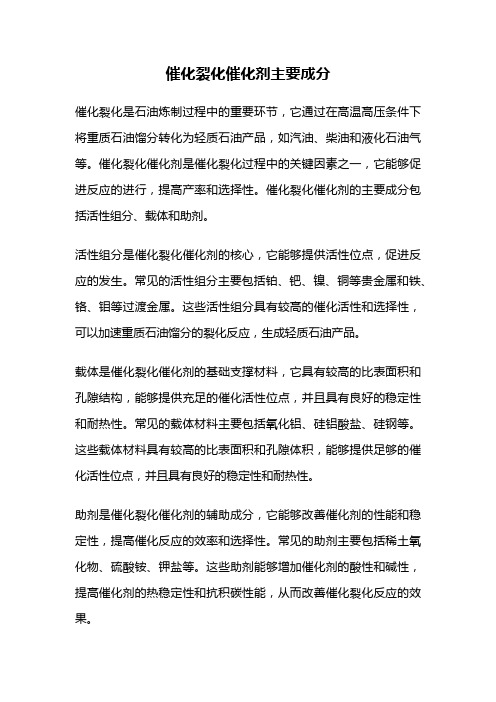
催化裂化催化剂主要成分催化裂化是石油炼制过程中的重要环节,它通过在高温高压条件下将重质石油馏分转化为轻质石油产品,如汽油、柴油和液化石油气等。
催化裂化催化剂是催化裂化过程中的关键因素之一,它能够促进反应的进行,提高产率和选择性。
催化裂化催化剂的主要成分包括活性组分、载体和助剂。
活性组分是催化裂化催化剂的核心,它能够提供活性位点,促进反应的发生。
常见的活性组分主要包括铂、钯、镍、铜等贵金属和铁、铬、钼等过渡金属。
这些活性组分具有较高的催化活性和选择性,可以加速重质石油馏分的裂化反应,生成轻质石油产品。
载体是催化裂化催化剂的基础支撑材料,它具有较高的比表面积和孔隙结构,能够提供充足的催化活性位点,并且具有良好的稳定性和耐热性。
常见的载体材料主要包括氧化铝、硅铝酸盐、硅钢等。
这些载体材料具有较高的比表面积和孔隙体积,能够提供足够的催化活性位点,并且具有良好的稳定性和耐热性。
助剂是催化裂化催化剂的辅助成分,它能够改善催化剂的性能和稳定性,提高催化反应的效率和选择性。
常见的助剂主要包括稀土氧化物、硫酸铵、钾盐等。
这些助剂能够增加催化剂的酸性和碱性,提高催化剂的热稳定性和抗积碳性能,从而改善催化裂化反应的效果。
催化裂化催化剂的制备过程通常包括活性组分的负载、载体的制备和助剂的添加。
活性组分的负载是将活性组分与载体进行物理或化学吸附,使其均匀分散在载体的表面,增加催化剂的活性位点。
载体的制备是通过合成和煅烧等工艺,将原料转化为具有良好孔隙结构和稳定性的载体材料。
助剂的添加是在载体上加入一定量的助剂,通过改变催化剂的酸碱性质和热稳定性,提高催化剂的性能和稳定性。
催化裂化催化剂的性能主要取决于活性组分的选择和负载量、载体的比表面积和孔隙结构、助剂的种类和添加量等因素。
合理选择催化剂的成分和制备工艺,可以提高催化裂化反应的效率和选择性,降低能耗和环境污染。
因此,催化裂化催化剂的研究和开发对于石油工业的发展具有重要意义。
催化裂化的工艺特点及基本原理

教案叶蔚君5.1催化裂化的工艺特点及基本原理[引入]:先提问复习,再从我国催化裂化汽油产量所占汽油总量的比例引入本章内容。
[板书]:催化裂化一、概述1、催化裂化的定义、反应原料、反应产物、生产目的[讲述]:1.催化裂化的定义(重质油在酸性催化剂存在下,在470~530O C的温度和0.1~0.3MPa的条件下,发生一系列化学反应,转化成气体、汽油、柴油等轻质产品和焦炭的过程。
)、反应原料:重质油;(轻质油、气体和焦炭)、(轻质油);[板书]2.催化裂化在炼油厂申的地位和作用:[讲述]以汽油为例,据1988年统计,全世界每年汽油总消费量约为6.5亿吨以上,我国汽油总产量为1750万吨,从质量上看,目前各国普通级汽油一般为90-92RON、优质汽油为96-98RON,我国1988年颁布车用汽油指标有两个牌号,其研究法辛烷值分别为不低于90和97。
但是,轻质油品的来源只靠直接从原油中蒸馏取得是远远不够的。
一般原油经常减压蒸馏所提供的汽油、煤油和柴油等轻质油品仅有10-40%,如果要得到更多的轻质产品以解决供需矛盾,就必须对其余的生质馏分以及残渣油进行二次加工。
而且,直馏汽油的辛烷值太低,一般只有40-60MON,必须与二次加工汽油调合使用。
国内外常用的二次加工手段主要有热裂化、焦化、催化裂化和加氢裂化等。
而热裂化由于技术落后很少发展,而且正逐渐被淘汰,焦化只适用于加工减压渣油,加氢裂化虽然技术上先进、产品收率高、质量好、灵活性大,但设备复杂,而且需大量氢气,因此,技术经济上受到一定限制,所以,使得催化裂化在石油的二次加工过程中占居着重要地位(在各个主要二次加工工艺中居于首位)。
特别是在我国,车用汽油的组成最主要的是催化裂化汽油,约占近80%。
因此,要改善汽油质量提高辛烷值,首先需要把催化裂化汽油辛烷值提上去。
目前我国催化裂化汽油辛烷值RON偏低,必须采取措施改进工艺操作,提高催化剂质量,迅速赶上国际先进水平。
催化裂化催化剂的发展历程及研究进展

催化裂化催化剂的发展历程及研究进展催化裂化是一种重要的石油加工技术,通过将石油分子在催化剂的作用下进行裂解,得到高附加值的产品,如汽油和石脂油。
催化裂化催化剂的发展历程可以追溯到20世纪初,经过了多个阶段的演进和改进。
本文将详细介绍催化裂化催化剂的发展历程及研究进展。
20世纪初,催化裂化催化剂主要采用天然矿物催化剂,如石英、蛭石等。
这些催化剂具有一定的催化活性,但缺乏稳定性和选择性,难以应对复杂的原料和严苛的工业操作条件。
20世纪30年代,随着石油需求的增加和技术的进步,人们开始研发新型催化剂。
那时,主要采用的是氧化物催化剂,如铝、硅等。
这些催化剂的活性和稳定性有了一定的提升,但仍然存在一些问题,如选择性不高、催化剂寿命短等。
20世纪50年代,人们开始尝试使用酸性功能组分的催化剂,如酸化铁、硫酸等。
这些催化剂具有较高的催化活性和选择性,但具有腐蚀性,容易造成催化剂失效和设备损坏。
20世纪60年代,人们将焦油催化裂化硅铝酸催化剂推向了催化裂化工业化生产的舞台。
这种催化剂具有良好的热稳定性和选择性,能够实现高效的催化裂化反应。
焦油催化裂化硅铝酸催化剂的应用推动了石油工业的发展,成为当时催化裂化的主流技术。
近年来,催化裂化催化剂的研究进展主要集中在以下几个方面:1.催化剂结构设计:通过调控催化剂的孔径分布、酸中心密度和酸强度等结构参数,以提高其活性、选择性和稳定性。
常见的结构设计方法包括合金化、钾的添加、微介孔化等。
2.催化剂负载材料研究:将催化剂负载在合适的载体上,可以提高催化剂的分散性和稳定性。
常用的载体材料包括Al2O3、SiO2、TiO2等。
3.催化剂表面改性:通过表面改性的方法,如纳米粒子修饰、溶胶-凝胶法制备等,可以改变催化剂的活性中心和表面酸性,以提高其催化效果。
4.新型催化剂开发:人们正在探索使用新型催化剂,如纳米材料、金属有机骨架材料(MOFs)等,以提高催化裂化过程的效率和选择性。
催化裂化知识

催化裂化知识催化裂化是一种重要的炼油工艺,通过催化剂的作用将重质石油馏分转化为轻质产品。
在催化裂化过程中,石油馏分经过加热后与催化剂接触,发生裂化反应,生成较轻质的烃类化合物。
催化裂化技术广泛应用于石油炼制行业,使得石油资源得以充分利用。
催化裂化的原理是通过催化剂的作用降低反应的活化能,加快反应速率。
催化剂是一种能够提供活性位点的物质,它能够吸附反应物分子并改变其化学键,从而促进反应的进行。
常用的催化剂有酸性催化剂、碱性催化剂和金属催化剂等。
在催化裂化过程中,石油馏分首先被预热至适宜的温度,然后进入催化剂床层。
在催化剂的作用下,石油馏分中的大分子化合物发生裂化反应,生成烃类产品。
裂化反应主要包括裂解、重排和异构化等过程。
裂解是指将长链烃分子裂解为短链烃分子,重排是指短链烃分子发生位置变化,异构化是指短链烃分子发生结构变化。
催化裂化的反应条件主要包括温度、压力和催化剂的选择等。
温度是影响催化裂化反应速率和产物分布的重要因素。
适宜的温度能够提高反应速率,但过高的温度会导致生成焦炭等副产物。
压力对催化裂化反应的影响相对较小,一般较低的压力即可满足反应的需求。
催化剂的选择对反应的效果有着重要影响,不同的催化剂对产品分布、产率和选择性有不同的影响。
催化裂化技术的应用使得石油炼制过程更加灵活多样,能够根据市场需求灵活调整产品结构。
通过合理的催化剂设计和反应条件控制,可以实现不同产品的选择性裂化。
催化裂化不仅能够提高汽油产率,还能够产生重要的石化原料,如乙烯、丙烯等。
催化裂化技术的发展也为石油炼制行业的绿色转型提供了重要支持。
然而,催化裂化过程中也存在一些问题。
首先,催化剂的失活是一个严重的问题,随着反应的进行,催化剂会逐渐失去活性,需要定期更换。
其次,催化裂化反应的过程较复杂,需要综合考虑反应的热力学和动力学特性,以及催化剂的选择和反应条件的控制。
此外,催化裂化过程中还会产生大量的副产物,如焦炭和烟气,对环境造成一定的污染。
催化裂化

置里,由于催化剂老化减活及重金
属污染,催化剂活性下降,为了维 持系统内平衡催化剂活性,需要补
充新催化剂。在置换催化剂及停工
时要从系统内卸出催化剂。
反应器作用:进行催化裂化反应的场所,为反 应提供一定反应温度、反应时间和空间,是催
化裂化装置的核心设备。
沉降器作用:使来自提升管的反应油气和催化
剂分离,回收催化剂。
化剂,烟 气经集气室和双动滑阀排入烟囱。再生
烟气温度很高而且含有约5%~10% CO,为了利 用其热量,不少装置设有CO 锅炉,利用再生烟 气产生水蒸汽。对于操作压力较高的装置,常设 有烟气能量回收系统,利用再生烟气的热能和压
力作功,驱动主风机以节约电能。
装置内设有催化剂储罐的原因:
在生产中催化剂会损失,为 了维持反应再生系统内催化剂藏量, 需要定期地或经常补充新鲜催化剂。 在一些催化剂损耗很低的装
分子筛催化剂不能在床层反再系统应用的原因
分子筛催化剂活性很高,如果在流化床层中进行裂化反应,则 由于油气在床层中停留时间过长、反混严重、必然会引起过 多二次反应,结果使轻质油产率降低,焦炭产率增大。使用 分子筛催化剂时裂化反应时间只需1~4秒。采用提升管反应 器可以严格控制反应时间,而且气固混合物在提升管中高速 流动,减少反混,也减少了二次反应,充分发挥分子筛催化 剂高活性和高选择性的优点。 分子筛催化剂的提升管裂化的优越性 使用分子筛催化剂的提升管裂化比无定形硅酸铝的床层裂 化反应有明显优越性:轻质油收率高、焦炭产率低,柴油十
旋风分离器:使气固分离并回收催化剂
再生器作用:是烧去结焦催化剂上的焦炭以恢
复催化剂的活性,同时也提供裂化所需的热量。
②分馏系统 分馏系统的作用:是将反应再生系统的产物进 行分离,得到部分产品和半成品。
催化裂化催化剂
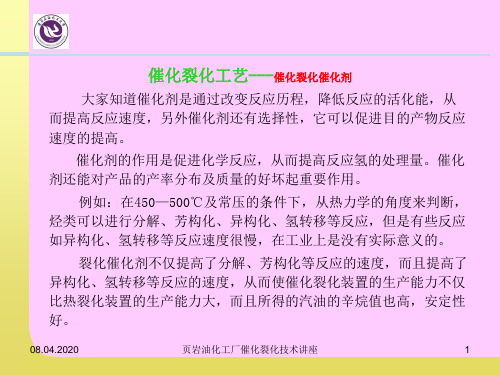
08.04.2020
页岩油化工厂催化裂化技术讲座
3
2、无定型硅酸铝催化剂 1958年我国开始生产小球状93-5毫米 合成硅酸铝催化剂,用于
移动床。 1965年开始生产微球状920-100微米 合成硅酸铝。 ①高铝低铝催化剂和合成方法 硅酸铝的主要成分是氧化硅和氧化铝,依铝含量的不同,合成硅
酸铝又分为低铝和高铝。 低铝硅酸铝含Al2O3 10-13% 高铝硅酸铝含Al2O3 25% 合成的方法是:由Na2SiO3 俗称水玻璃 Al2 (SO4)3,溶液按一定比例配 合生成凝胶,再经过水洗,过滤,成型,干燥,活化等步骤制成。
08.04.2020
页岩油化工厂催化裂化技术讲座
10
⑶分子筛催化剂的结构
每个单元晶胞结构,每个单元晶胞由八个削角八面体构成,削角八面体 的每个顶端是Si或Al原子,其间由氧原子相连接。由八个削角八面体围成的 空洞称为“八面沸石笼”。它是催化反应进行的主要场所。其体积为820埃。
进入八面沸石笼的主要通道是由十二员环组成,其平均直径为0.8— 0.9nm。钠离子的位置有多处。
项目 新鲜催化剂 平衡催化剂
松动 0.40 0.63
沉降 0.44 0.69
密实 0.53 0.79
催化剂的堆积密度常用于计量催化剂的体积重量,催化剂的颗 粒密度对催化剂的流化性能有重要的影响。
08.04.、活性、稳定性
(1)活性:是指催化剂促进化学反应的能力。
由于AL:O键趋向正电荷较强 Si,使Al带有正电性,即为非质 子酸。
在有少量的水存在在时,由 于AL原子带正电性使水分子离解 为H+与OH-,其中OH-与带正电的 性的Al结合,而则H+在Al原子附 近呈游离状态,此即质子酸。 (如a)
- 1、下载文档前请自行甄别文档内容的完整性,平台不提供额外的编辑、内容补充、找答案等附加服务。
- 2、"仅部分预览"的文档,不可在线预览部分如存在完整性等问题,可反馈申请退款(可完整预览的文档不适用该条件!)。
- 3、如文档侵犯您的权益,请联系客服反馈,我们会尽快为您处理(人工客服工作时间:9:00-18:30)。
第三章催化裂化催化剂
1.什么是催化裂化?
催化裂化是指石油的高沸点馏份(重质油)在催化剂存在下裂化为汽油、柴油和裂化气的过程。
2.催化裂化装置主要由哪几部分组成的?
催化裂化装置主要是由反应-再生系统、分馏系统、吸收稳定系统和烟气能量回收系统四部分组成的。
3.催化裂化的特点是什么?
原料来源广泛,一般渣油、重质馏分油均可适用;产品产率高、质量好;装置操作弹性大,产品方案灵活;催化裂化装置均为标准设计,装置水平高、自动化程度及连续化程度高,因此,装置经济规模较大。
4.石油馏分催化裂化的特点是什么?
是一个复杂的平行-顺序反应;各类烃在催化剂表面上的吸附存在竞争。
5.对催化裂化催化剂的性能要求是什么?
裂化催化剂具有较理想的可流化性能和抗磨性能;催化裂化催化剂应当具备较高的活性、稳定性和选择性;催化裂化催化剂应具有较好的抗金属污染性能和再生性能;催化裂化催化剂应具有比较理想的表面结构。
普遍认为催化裂化催化剂应当具有大孔低比表面结构。
6.从发展历程看,催化裂化催化剂分为哪几类?
工业上所使用的催化剂,从催化剂的发展历程来看,归纳起来有三大类:天然白土催化剂、无定型合成催化剂和分子筛催化剂。
7.无定型合成催化剂分为哪几类?
全合成硅酸铝催化剂、半合成硅酸铝催化剂、合成硅酸镁催化剂。
8.分子筛化学组成是什么?常见的分子筛有哪些?
M x/n[(AlO2)x(SiO2)y]·ZH2O
常见的分子筛有A型、X型、Y型沸石和丝光沸石。
9.分子筛催化裂化催化剂的主要组成是什么?
分子筛催化裂化催化剂的主要组成是活性组分分子筛和基质。
10.基质的主要作用是什么?
基质主要提供合理的孔分布、适宜的表面积和在水热条件下的结构稳定性,并要求有良好的汽提性能、再生烧焦性能,足够的机械强度和流化性能;同时基质给予催化剂一定的
物理形态和机械性能,如颗粒度、孔结构、堆积密度、抗磨性等,以保证催化剂的输送、流化和汽提性能。
此外它还有以下功能:
①在离子交换时,分子筛中的钠不可能完全被置换掉,而钠的存在会影响分子筛的稳定性,基质可以容纳分子筛中未除去的钠,从而提高了分子筛的稳定性。
②稀释和分散活性组分,使催化剂的活性适当;
③在再生和反应时,基质作为一个庞大的热载体,起到热量储存和传递的作用;
④重油催化裂化进料中的部分大分子难以直接进入分子筛的微孔中,如果基质具有适度的催化活性,则可以使这些大分子先在基质的表面上进行适度的裂化,生成的较小的分子再进入分子筛的微孔中进行进一步的反应;
⑤基质还能容纳进料中易生焦的物质如沥青质、重胶质等,抵抗杂质(如碱性氮、重金属等)对活性组分的污染破坏,保持催化剂良好的活性和选择性。
11.催化裂化催化剂的化学组成包括哪些?
通常包括:从AI2O3、SiO2、H2O、Na2O、Fe2O3、SO42-等,有时还包括RE2O3。
12.催化裂化催化剂的物理性质包括哪些?
物理性质表示催化剂的外形、宏观结构、密度、粒度等性能。
通常包括:比表面积、孔体积、密度、磨损指数、筛分组成5个主要项目。
13.催化裂化催化剂的抗磨损强度的评价指标是什么?
目前采用“磨损指数”来评价微球催化剂的耐磨损强度。
14.为了保证催化剂良好的流化状态,对筛分组成的要求是什么?
一般要求催化剂颗粒<40μm的不大于25%,40μm~80μm的不小于50 %,>80μm的不大于30%。
15.催化裂化催化剂的活性的测定方法是什么?
测定无定形硅铝裂化催化剂的活性,采用D+L法或CAT -A法;随着沸石裂化催化剂的应用,评定的方法也改进为微反活性法(MAT)。
工业平衡催化剂的活性,目前均用微反活性表示。
16.催化剂的平衡活性指的是什么?
在生产装置中,为使活性保持在一个稳定的水平上以及在补充生产中损失的催化剂,需补入一定量的新鲜催化剂,此时的活性称为平衡催化剂的活性。
17.催化裂化催化剂的选择性的表示方法有哪些?
以转化率为基准来表达的方式,如汽油/转化率,用焦炭/转化率的比值表示焦炭选择性;
另一种常用的方式是以焦炭产率为基准来表达的方式,如用汽油产率/焦炭产率之比表示催化剂生产汽油的选择性,也很直观。
另外,还用H2/CH4比值表示产氢的选择性,用iC4/n C4比值来表示异构化反应的选择性等。
18.怎样评价催化裂化催化剂的稳定性?
测定裂化催化剂的稳定性,通常是在一定条件下(分子筛催化剂是在常压800℃用水蒸气处理4h或17h,硅酸铝催化剂是在750℃通蒸汽6h)使催化剂老化,然后再测定其活性并与新鲜催化剂的活性(初活性)相比,由活性下降的情况来评价催化剂的稳定性。
老化后活性降低的越少说明催化剂的稳定性越好。
19.影响催化剂性能的重金属有哪些?
主要有铁、铜、镍、钒等。
20.重金属催化剂的污染程度用什么来表示?
用污染指数来表示;
污染指数=0.1(Fe + Cu + 14Ni + 4V)
式中:Fe、Cu、Ni、V分别为催化剂上铁、铜、镍、钒的含量,以10-6表示。
催化剂的污染程度还可以用生氢因素或裂化气中的H2/CH4比值来表示。
21.催化裂化催化剂失活的主要原因有哪些?
裂化催化剂失活的主要原因可分为三类:①水热失活;②结焦失活;③吸附毒物失活。
22.催化裂化催化剂助剂有哪些?
CO助燃剂、辛烷值助剂、金属钝化剂、钒捕集剂、硫转移添加剂(脱SO X剂)和降低催化裂化汽油烯烃助剂。