硅酸盐水泥熟料的煅烧和生产过程
水泥生产工艺流程
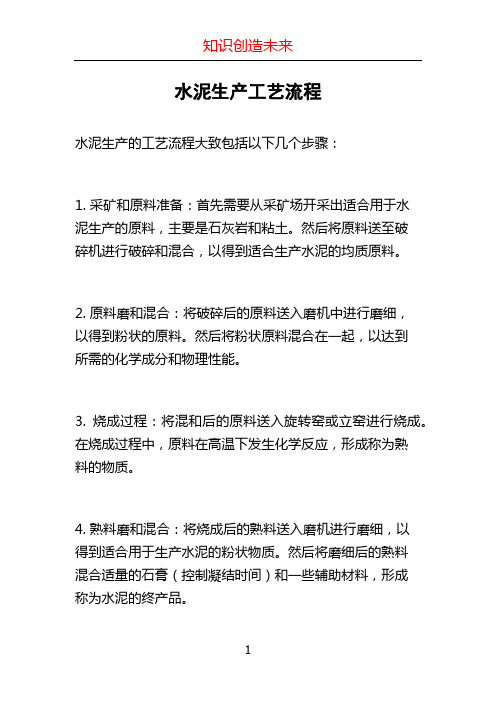
水泥生产工艺流程
水泥生产的工艺流程大致包括以下几个步骤:
1. 采矿和原料准备:首先需要从采矿场开采出适合用于水
泥生产的原料,主要是石灰岩和粘土。
然后将原料送至破
碎机进行破碎和混合,以得到适合生产水泥的均质原料。
2. 原料磨和混合:将破碎后的原料送入磨机中进行磨细,
以得到粉状的原料。
然后将粉状原料混合在一起,以达到
所需的化学成分和物理性能。
3. 烧成过程:将混和后的原料送入旋转窑或立窑进行烧成。
在烧成过程中,原料在高温下发生化学反应,形成称为熟
料的物质。
4. 熟料磨和混合:将烧成后的熟料送入磨机进行磨细,以
得到适合用于生产水泥的粉状物质。
然后将磨细后的熟料
混合适量的石膏(控制凝结时间)和一些辅助材料,形成
称为水泥的终产品。
5. 煅烧和制备:将水泥熟料送入煅烧窑中进行煅烧,将水泥熟料在高温下煅烧,使其结晶、熔融、冷却和固化,形成硅酸盐水泥。
6. 筛分和包装:将煅烧后的水泥进行筛分,去除不合格的颗粒。
然后将合格的水泥通过自动包装机进行包装,最常见的是将水泥装入袋中。
上述是水泥生产的主要工艺流程,不同的水泥生产厂家可能会有一些细微的差异。
同时,为了提高生产效率和降低能耗,还可以采用一些先进的技术和设备,如干法生产工艺、回转窑技术等。
水泥生产工艺及水泥熟料的形成
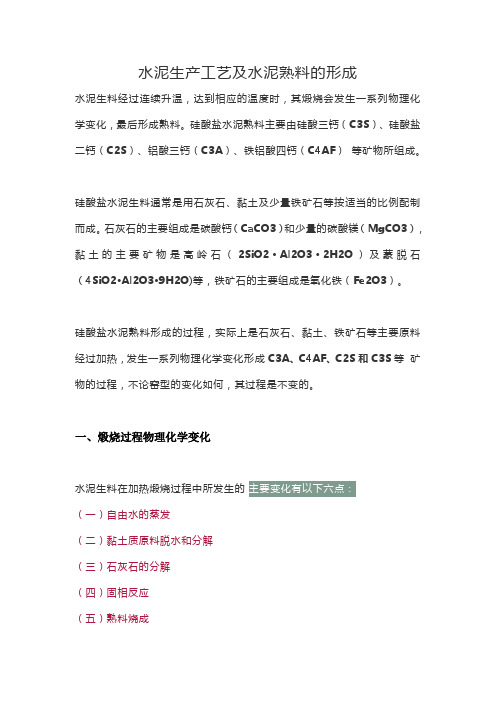
水泥生产工艺及水泥熟料的形成水泥生料经过连续升温,达到相应的温度时,其煅烧会发生一系列物理化学变化,最后形成熟料。
硅酸盐水泥熟料主要由硅酸三钙(C3S)、硅酸盐二钙(C2S)、铝酸三钙(C3A)、铁铝酸四钙(C4AF)等矿物所组成。
硅酸盐水泥生料通常是用石灰石、黏土及少量铁矿石等按适当的比例配制而成。
石灰石的主要组成是碳酸钙(CaCO3)和少量的碳酸镁(MgCO3),黏土的主要矿物是高岭石(2SiO2·Al2O3·2H2O)及蒙脱石(4SiO2·Al2O3·9H2O)等,铁矿石的主要组成是氧化铁(Fe2O3)。
硅酸盐水泥熟料形成的过程,实际上是石灰石、黏土、铁矿石等主要原料经过加热,发生一系列物理化学变化形成C3A、C4AF、C2S和C3S等矿物的过程,不论窑型的变化如何,其过程是不变的。
一、煅烧过程物理化学变化水泥生料在加热煅烧过程中所发生的(一)自由水的蒸发(二)黏土质原料脱水和分解(三)石灰石的分解(四)固相反应(五)熟料烧成(六)熟料的冷却(一)自由水的蒸发无论是干法生产还是湿法生产,入窑生料都带有一定量的自由水分,由于加热,物料温度逐渐升高,物料中的水分首先蒸发,物料逐渐被烘干,其温度逐渐上升,温度升到100~150℃时,生料自由水分全部被排除,这一过程也称为干燥过程。
(二)黏土质原料脱水和分解黏土主要由含水硅酸铝所组成,其中二氧化硅和氧化铝的比例波动于2:1~4:1之间。
当生料烘干后,被继续加热,温度上升较快,当温度升到450℃时,黏土中的主要组成高岭土(Al2O3·2SiO2·2H2O)失去结构水,变为偏高岭石(2SiO2·Al2O3)。
高岭土进行脱水分解反应时,在失去化学结合水的同时,本身结构也受到破坏,变成游离的无定形的三氧化二铝和二氧化硅,其具有较高的化学活性,为下一步与氧化钙反应创造了有利条件。
在900-950℃,由无定形物质转变为晶体,同时放出热量。
硅酸盐水泥的标准

水泥比表面积测定GB8074-87
勃 氏 比 表 面 积 仪
四、试验方法(硅酸盐水泥)
序 号 项 目 指标 P· Ⅰ P· Ⅱ 检验方法 与依据
1
2 3 4 5 6
不溶物(%)
烧失量(%) 细度(比表面积)(m2/kg) 凝结时间(min)
≤0.75
≤3.0 ≥300 初凝≥45 终凝≤390
7
三氧化硫(%)
GB/T176-1996
GB/T176-1996 JC/T420 GB/T17671-1999 GB8074-87 GB1345-91
8 碱(Na2O+0.658Na2O)(%) 9 10 11 12 氯离子(%) 强度 比表面积 细度
五、检验规则
(1)编号与取样
年产120万吨以上不超过1200吨为一编号; 60万吨以上至120万吨,不超过1000吨为一编号; 30万吨以上至60万吨,不超过600吨为一编号; 10万吨以上至30万吨,不超过400吨为一编号; 10万吨以下,不超过200吨为一编号。
2.1 硅酸盐水泥的标准
类型:100多个水泥专业标准 强制性标准 国家标准(代号GB) 建材行业标准(代号JC) 推荐性标准 国家标准(代号GB/T) 建材行业标准(代号JC/T) 此外还有企业标准(代号:Q)
标准号表示方法: GB175-2007硅酸盐水泥 标准名称 制订或修订年份 标准编号 标准代号
-
-
-
复合硅酸盐 水≤50(e)
一、通用硅酸盐水泥的定义
※组分材料: ① 硅酸盐水泥熟料(clinker) ② 石膏 (gypsum ) ③ 混合材料(admixture) ④ 窑灰(kiln dust) ⑤ 助磨剂 窑灰:从回转窑窑尾气中收集下来的粉尘,品质指标应符合 JC/T742的规定。 助磨剂:水泥粉磨时允许加入主要起助磨作用而不损害水泥性 能的助磨剂,其加入量不得超过水泥质量的0.5%。 助磨剂应符合JC/T667的规定
3. 水泥

其中,硅酸三钙和硅酸二钙为强度组分,铝酸三钙和铁铝酸四钙为熔 剂组分。 其他还有少部分f-CaO、f-MgO及玻璃体等
三、硅酸盐水泥的主要技术性能
1. 密度
2. 细度(分散度) 3. 需水量 4. 泌水性和保水性 5. 凝结时间 6. 体积安定性 7. 强度等级 8. 水化热 9. 碱含量 10. 氯离子含量
抗折强度 3d 28d ≥3.5 ≥6.5 ≥4.0 ≥4.0 ≥7.0 ≥5.0 ≥5.0 ≥8.0 ≥5.5 ≥3.5 ≥6.5 ≥4.0 ≥4.0 ≥7.0 ≥5.0
品 种 矿渣硅酸盐水泥 火山灰硅酸盐水 泥 粉煤灰硅酸盐水 泥 复合硅酸盐水泥
强度等 级 32.5 32.5R 42.5 42.5R 52.5
度需水量。(水泥重量百分数)P.O水泥一般在25~28%
之间。
影响因素:
①细度; ②矿物组分:C3A>C3S>C4AF>C2S
4.泌水性与保水性
(water bleeding and water retentivity)
在拌制水泥浆以及砂浆、砼时,为保证必要的和易性, 往往加入比标准稠度用水量多的水。但是,水泥由于自重 的原因,有可能下沉,而余水则向上移动被析出,从而使 浆体分层,从而影响强度及耐久性等。(这一现象即称为 泌水性) 与之有关的是保水性:此时余水不会析出,但当在真空 抽吸时能析出,这种现象称为保水性。
1)碳酸的腐蚀 2)一般酸的腐蚀 3)镁盐的腐蚀 (3)膨胀性腐蚀 1)硫酸盐腐蚀 2)硫酸的腐蚀 (4)碱的腐蚀 (5)水泥石腐蚀的防止
八、水泥的储存与运输
储存条件:不得受潮,或混入杂物 存放期:不得超过3个月,超过3个月应重新检验强 度,以实测为准 运输
水泥 土木工程材料 复习资料 合工大

水泥防止水泥石腐蚀的措施有:(1)根据环境特点,合理选择水泥品种;(2)提高水泥石的密实度;(3)在水泥石的表面加做保护层。
1、硅酸盐水泥生产过程:用石灰石和粘土和铁矿粉按一定比例混合后磨细成生料,然后送入回转窑在1450摄氏度下煅烧,得到以硅酸钙为主要成分的水泥熟料,再与适量石膏共同磨细,最后得到硅酸盐水泥成品。
“两磨一烧”:磨细生料,磨细水泥,生料煅烧成熟料2、铝酸盐水泥(1)不能进行蒸汽养护,不能再高温季节施工(2)不能用于长期承重结构(3)不能与硅酸盐水泥或石灰等能析出氢氧化钙的物质混合,否则将产生瞬凝而无法施工。
3、水泥石腐蚀基本原因:(1)水泥石中含有氢氧化钙,水化氯酸钙等不耐腐蚀的水化产物。
(2)水泥石本身不密实,有很多毛细孔,腐蚀性介质容易通过毛细孔深入到水泥石内部,加速腐蚀的进程或引起盐类的循环结晶腐蚀。
4、防止水泥石腐蚀措施:(1)根据工程所处环境特点,选择合适的水泥品种(2)提高水泥石的密实程度(例如降低水灰比,掺加减水剂,改善施工方法)(3)表面防护处理(表面涂层或加保护层)5、影响水泥水化和凝结硬化的主要因素:(1)水泥细度(2)用水量(3)养护条件(4)养护龄期(5)石膏掺量6、试说明以下各条的原因:(1)生产通用硅酸盐水泥时必须掺入适量的石膏;(2)水泥必须具有一定的细度;(3)水泥体积安定性必须合格;(4)测定水泥凝结时间、体积安定性及强度等级,均须采用规定的加水量。
1、(1)生产通用硅酸盐水泥时掺入适量的石膏是为了调节水泥的凝结时间。
若不掺入石膏,由于水泥熟料矿物中的C3A急速水化生成水化铝酸四钙晶体,使水泥浆体产生瞬时凝结,以致无法施工。
当掺入石膏时,生成的水化铝酸四钙会立即与石膏反应,生成高硫型水化硫铝酸钙(即钙矾石),它是难溶于水的针状晶体,包围在熟料颗粒的周围,形成“保护膜”,延缓了水泥的水化。
但若石膏掺量过多,在水泥硬化后,它还会继续与固态的水化铝酸四钙反应生成钙矾石,体积约增大1.5倍,引起水泥石开裂,导致水泥安定性不良。
硅酸盐水泥生产工艺及其原料
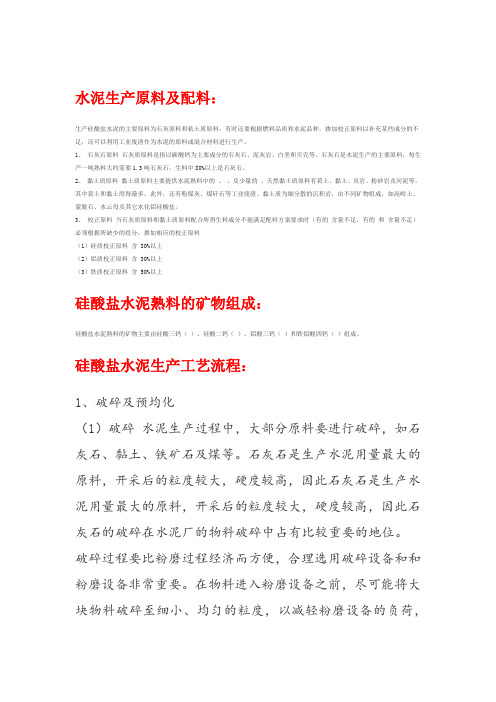
水泥生产原料及配料:生产硅酸盐水泥的主要原料为石灰原料和粘土质原料,有时还要根据燃料品质和水泥品种,掺加校正原料以补充某些成分的不足,还可以利用工业废渣作为水泥的原料或混合材料进行生产。
1、石灰石原料石灰质原料是指以碳酸钙为主要成分的石灰石、泥灰岩、白垩和贝壳等。
石灰石是水泥生产的主要原料,每生产一吨熟料大约需要1.3吨石灰石,生料中80%以上是石灰石。
2、黏土质原料黏土质原料主要提供水泥熟料中的、、及少量的。
天然黏土质原料有黄土、黏土、页岩、粉砂岩及河泥等。
其中黄土和黏土用得最多。
此外,还有粉煤灰、煤矸石等工业废渣。
黏土质为细分散的沉积岩,由不同矿物组成,如高岭土、蒙脱石、水云母及其它水化铝硅酸盐。
3、校正原料当石灰质原料和黏土质原料配合所得生料成分不能满足配料方案要求时(有的含量不足,有的和含量不足)必须根据所缺少的组分,掺加相应的校正原料(1)硅质校正原料含 80%以上(2)铝质校正原料含 30%以上(3)铁质校正原料含 50%以上硅酸盐水泥熟料的矿物组成:硅酸盐水泥熟料的矿物主要由硅酸三钙()、硅酸二钙()、铝酸三钙()和铁铝酸四钙()组成。
硅酸盐水泥生产工艺流程:1、破碎及预均化(1)破碎水泥生产过程中,大部分原料要进行破碎,如石灰石、黏土、铁矿石及煤等。
石灰石是生产水泥用量最大的原料,开采后的粒度较大,硬度较高,因此石灰石是生产水泥用量最大的原料,开采后的粒度较大,硬度较高,因此石灰石的破碎在水泥厂的物料破碎中占有比较重要的地位。
破碎过程要比粉磨过程经济而方便,合理选用破碎设备和和粉磨设备非常重要。
在物料进入粉磨设备之前,尽可能将大块物料破碎至细小、均匀的粒度,以减轻粉磨设备的负荷,提高黂机的产量。
物料破碎后,可减少在运输和贮存过程中不同粒度物料的分离现象,有得于制得成分均匀的生料,提高配料的准确性。
超细粉碎机(2)原料预均化预均化技术就是在原料的存、取过程中,运用科学的堆取料技术,实现原料的初步均化,使原料堆场同时具备贮存与均化的功能。
中热硅酸盐水泥熟料研发生产实践

中热硅酸盐水泥熟料研发生产实践摘要:针对市场要求及相关行业水泥质量要求,采用的新型干法烧窑,选用低碱原料,对生料组分、原料品种、熟料配方、水泥SO3、比表面积等进行了优化实验,得出了以石灰石、高硅砂岩、铝矿渣、白云石的最佳原料品种,其中热熟料三率值控制在KH0.870±0.02、SM2.50±0.10、IM0.80±0.10为佳,水泥比表面积控制目标为310+10m2/kg,SO3控制指标为2.2±0.3%,水泥比表面积控制目标为310+10m2/kg,SO3控制指标为2.2±0.3%,氧化镁含量控制为4.5±0.3%。
关键词:中热硅酸盐泥;低水化热;微膨胀;新型干法窑炉前言如果在大体积混凝土工程中使用放热温度较高的水化水泥,由于导热系数低,可能会导致混凝土内部温度升高,而内部温度高可能会增加混凝土内外温差,从而引起温度应力增加;如果大体积混凝土工程中的温度应力高于混凝土的抗拉强度,可能会导致混凝土开裂等问题。
因此,大多数大体积混凝土工程,特别是水电站工程,都采用含水量相对较低的中温硅酸盐水泥作为水泥材料,以减少碱性填料反应引起的混凝土开裂。
在水电工程中,需要使用中温、低碱的硅酸盐水泥和微膨胀水泥来减少因加碱反应引起的裂缝。
1.中热硅酸盐水泥熟料的指标要求中热水泥具有42.5的强度,是中国使用量最高的一种特殊水泥。
中热硅酸盐水泥熟料是一种专用于大型工程的水泥熟料,如大坝、水利等大型民生工程。
其具有强度高、碱度低、湿热适中等优势。
其性能指标:满足GB200-2003标准、水利建设(微膨胀)的特殊要求,对水泥、助剂的适应性、对回转窑锻烧的影响等。
2配料方案设计2.1配料设计中的原料选择根据以往数据低碱性硅酸盐水泥熟料生产的经验,经过对低碱性原材料的检查,除了石灰石、砂岩和铁矿石外,熟料中的碱度在0.6%~0.7%之间,通过对钢结构进行验证、计算,确定采用钢框架进行处理,对钢框架进行降解、循环再利用,以求提高对环境的保护作用。
水泥熟料的煅烧
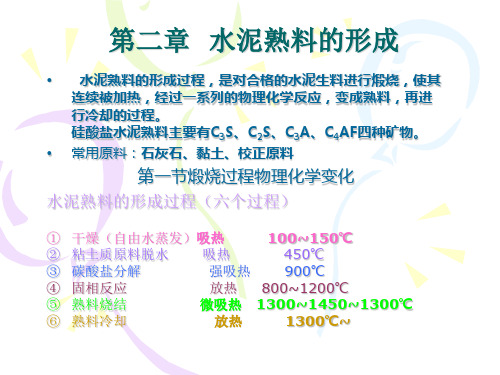
冷却目的: 冷却目的:
改善熟料质量与提高熟料的易磨性 降低熟料的温度,便于运输、储存、 和粉磨 回收热量,预热二次空气,降低热耗、提高热利用率。
冷却方式: 冷却方式:
按冷却速度的快慢分平衡冷却、独立结晶、淬冷(急 冷)。熟料冷却过程中对熟料质量影响较大的因素—冷却 速度 ,它影响固液相中的质点扩散速度、固液相的反应速 度等。 冷却制度 平衡冷却 淬 冷 C3S(%) 60 68 C2S(%) 13.5 C3A(%) 玻璃体(%) 26.5 32
4.二次风的作用 二次风是相对一次风而言,它来自冷却机内冷却 二次风 熟料并加热后入窑且参与煤粉燃烧的空气。温度 一般在400~800℃。
三、窑外分解技术
窑外分解技术是20世纪70年代发展起来也是迄今 为止水泥煅烧工艺的新技术,只是在悬浮预热器 和回转窑之间增设一个分解炉,使生料中的碳酸 钙在入回转窑之前分解,大大减轻了回转窑的热 负荷,窑的产量可比悬浮预热器窑提高1~2倍, 同时延长了耐火衬料的使用寿命,提高了窑的运 转率。其发展趋势是大型化、高产量,单位热耗 大幅下降。
3.一次风的作用 一次风-携带煤粉自喷煤管喷入窑内的用风。 一次风 作用- 作用-除对煤粉起输送作用外还供给煤的挥 发分燃烧所需的氧气。 一次风量- 一次风量-占总空气量的比例不宜过多,因 为一次风量的增加相应地就会使二次风比例 降低(总用风不变的情况),二次风的减少会 影响到熟料冷却,使熟料带走的热损失增加。 另外,一次风温度比二次风温度要低(为使煤 粉不致爆炸,一次风温度不能高于l20℃), 这样燃烧温度也要降低。
以上反应在进行时放出一定的热量, 因此,又称为放热反应 放热反应。 放热反应
固相反应总结
•反应特点: 反应特点: 反应特点
多级反应 放热反应
- 1、下载文档前请自行甄别文档内容的完整性,平台不提供额外的编辑、内容补充、找答案等附加服务。
- 2、"仅部分预览"的文档,不可在线预览部分如存在完整性等问题,可反馈申请退款(可完整预览的文档不适用该条件!)。
- 3、如文档侵犯您的权益,请联系客服反馈,我们会尽快为您处理(人工客服工作时间:9:00-18:30)。
5.1.4 液相的形成与熟料的烧结
液相的形成 液相的组成:由氧化铁、氧化铝、 氧化钙、氧化镁和碱 及其他组分。
最低共熔温度:物料在加热过程中,两种或两种以上组 分开始出现液相的温度称为最低共熔温度。 其大小与组分的性质与数目有关。(见表1 -4-1)
硅酸三钙的形成: C 2SC aO 液 相 C 3S
物理化学变化过程:随着时间延长和温度升高,液相 量逐渐增加,氧化钙、硅酸二钙 不断溶解、扩散,硅酸三钙晶核 不断形成,小晶体逐渐发育长大, 最终形成几十微米大小、结晶良 好的阿利特晶体。
影响因素:物料的化学组成、煅烧方法、升温速率、 矿化剂与其他微量元素等。
800 ~ 900 ℃:开始形成12CaO•7Al2O3(C12A7); 900 ~ 1000 ℃: 2CaO• Al2O3•SiO2(C2AS)形成后又分解。
开始形成3CaO•Al2O3(C3A)和4CaO• Al2O3•Fe2O3(C4AF)。所有 碳酸盐均分解,游离氧化钙达到最高值。
1100 ~ 1200℃:大量形成C3A和C4AF,C2S含量达最大 值。
硅酸盐水泥熟料 的煅烧和生产过程
学习要点 本章主要介绍新型干法水泥生产过 程中的熟料煅烧技术以及煅烧过程 中的物理化学变化,以旋风筒—换 热管道—分解炉—回转窑—冷却机 为主线,着重介绍当代水泥工业发 展的主流和最先进的煅烧工艺及设 备、生产过程的控制调节等。
熟料的煅烧过程直接决定水泥的产量、质量、燃 料与衬料的消耗以及窑的安全运转。水泥窑有多种功 能:反应炉、熔炉、燃烧炉和传热设备、物料和气体 的输送设备。
液相的粘度:它直接影响硅酸三钙的形成速率及晶体发 育。其大小与液相的组分性质与温度有关。 温度越高,粘度越低;铝率越高,粘度越 大;多数微量元素可降低液相粘度。
液相的表面张力:其大小与组分性质、温度有关。它 影响着液相能润湿固相的程度,表 面张力越小,润湿性越好,有利于 C3S的形成。
熟料的烧结
(1)高岭石脱水
A l 2 O 3 2 S i O 2 2 H 2 O A l 2 O 3 2 S i O 2 2 H 2 O
(2)蒙脱石脱水 Al2O3.4SiO2.m H2O→Al2O3.4SiO2+m H2O (晶体结构—活性低)
(3)伊利石脱水 产物也是晶体结构,伴随体积膨胀
5.1.2碳酸盐分解 碳酸盐的分解主要为碳酸钙和碳酸镁的分解,其
影响固相反应的因素
生料的细度 生料愈细,比表面积越大,组分接触面越 大,同时表面质点的自由能越大,使扩散和反应 能力增强,因而反应速率加快;
生料的均化程度 生料的均匀混合,可增加各组分间接 触,也有利于加速反应;
压力 在固相反应中,增大压力可加速物质的传递过程. 但熟料烧结过程是多相共存、多反应同时进行的 过程.因此,提高压力有时并不表现出积极作用;
5.1 生料煅烧过程中的物理、化学变化
尽管煅烧过程因窑型不同而有所差异,但物理、化 学变化过程基本相似.其过程可概括为:
干燥与脱水
碳酸盐分解
固相反应
熟料的冷却
液相和熟料的烧结
5.1.1 生料的干燥与脱水
干燥 自由水的蒸发。这一过程由于煅烧方式的不同
而有所差异。干法窑生料含水量一般不超过1.0%; 半干法立波尔窑和立窑为便于生料成球,通常含水 12-15%,半湿法立波尔窑过滤水分后的料块通常为 18-22%;湿法为保证料浆的可泵性则通常为30-40%。
自由水蒸发热耗:
100℃时,2257kJ/kgH2O(539kCal/kg)
✓ 脱水 指黏土矿物分解释放化学结合水。
粘土矿物的化合水存在形式: 层间水:以水分子形式吸附于晶层结构中。 配位水:以OH-状态存在于晶体结构中。
层间水在100℃左右即可排除, 而配位水则必须高达400~600℃以上 才能脱去。
(单个颗粒碳酸盐分解动力学方程)
窑系统的CO2分压 通风良好, CO2分压较低,有利 于碳酸盐分解;
生料细度和颗粒级配 生料细度细,颗粒均匀,粗粒 少,分解速率快;
生料悬浮程度 生料悬浮分散良好,相对减小颗粒 尺寸,增大了传热面积,提高了碳酸盐分解速率;
石灰石的种类和物理性质 结构致密,结晶粗大的 石灰石,分解速率慢;
目的:回收熟料带走的热量,预热二次空气,提高窑 的热效率;改善熟料质量与易磨性;便于熟料 运输、贮存与粉磨。
(4)分解出的CO2,穿过CaO层面向表面扩散的传质过 程;
(5)表面的CO2向周围介质气流扩散过程
✓影响碳酸盐分解速率的因素
温度 随温度升高,分解速率常数和压力倒数差相 应增大,分解速率和时间缩短;
t
d
(1—3 1—ε)
K(1 — 1 )
p P0
式中: t—分解时间;K—分解常数;
P—CO2的分压;ε—分解率 d—生料等效粒径;
生料中粘土质组分和性质 粘土质中的矿物组分 的活性依次按高岭土、蒙脱石、伊利石、石英降低.粘 土质原料活性越大,可加速碳酸盐的分解过程.
5.1.3固相反应
在碳酸盐分解的同时,石灰质与粘土质组分间进行固 相反应,其过程如下:
~800℃:CaO•Al2O3,CaO•Fe2O3与2CaO•SiO2开始 形成;
化学反应式为:
C aC O 3 C aO C O 21645Jg1(890C ) M gC O 3 M gO C O 21214Jg1(590C )
✓ 分解过程分五步进行:
CaCO3
(1)气流向颗粒表面的传热过程;
CaO
(2)热量由表面以热传导方式向分解面传递过程;
(3)碳酸盐在一定温度下吸收热量,进行分解并放出 CO2的化学过程;
液相量:液相量与组分的性质、含量、温度等因素有关 (一般为20~30%) 。对C-S-A-F四元系统, 在不同温度下的液相量(P)可按下式计算:
不同温度下,液相的计算公式:
1400℃ 1450℃ 1500℃
P=2.95A+2.20F P=3.00A+2.2分全部 进入液相。