切削力计算公式
机加工计算公式
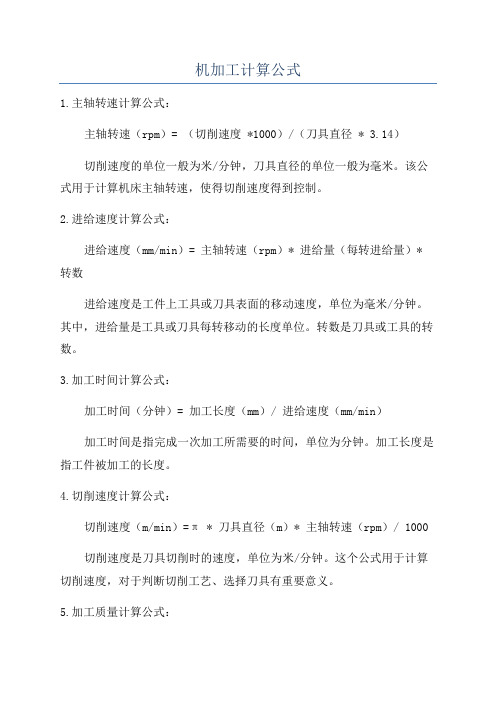
机加工计算公式1.主轴转速计算公式:主轴转速(rpm)= (切削速度 *1000)/(刀具直径 * 3.14)切削速度的单位一般为米/分钟,刀具直径的单位一般为毫米。
该公式用于计算机床主轴转速,使得切削速度得到控制。
2.进给速度计算公式:进给速度(mm/min)= 主轴转速(rpm)* 进给量(每转进给量)* 转数进给速度是工件上工具或刀具表面的移动速度,单位为毫米/分钟。
其中,进给量是工具或刀具每转移动的长度单位。
转数是刀具或工具的转数。
3.加工时间计算公式:加工时间(分钟)= 加工长度(mm)/ 进给速度(mm/min)加工时间是指完成一次加工所需要的时间,单位为分钟。
加工长度是指工件被加工的长度。
4.切削速度计算公式:切削速度(m/min)=π * 刀具直径(m)* 主轴转速(rpm)/ 1000切削速度是刀具切削时的速度,单位为米/分钟。
这个公式用于计算切削速度,对于判断切削工艺、选择刀具有重要意义。
5.加工质量计算公式:切削力(N)= 切削速度(m/min) * 切削厚度(m)* 切削宽度(m)* 切削力系数加工质量是指在机加工过程中,加工时所产生的力的大小。
切削厚度是指切削时每刀具进给的厚度单位。
切削宽度是刀具切削宽度。
6.切削宽度计算公式:切削宽度(m)=刀具直径(m)-余量(m)切削宽度是刀具在切削过程中,与工件接触的宽度。
余量是机加工过程中工件与刀具接触的部分。
7.余量计算公式:余量(m)=公差(m)+刀具磨损量(m)余量是机加工中为了保证工件尺寸大小和形状准确性而保留的部分。
公差是表明尺寸允许偏差的尺寸测量指标。
刀具磨损量是指刀具由于使用而磨损的长度。
以上是一些常用的机加工计算公式,通过这些公式,我们可以确定机床的主轴转速、进给速度、加工时间等参数,从而保证机加工的质量和效率。
当然,根据不同的机加工过程和需要,还可以根据实际情况建立适用的机加工计算公式。
切削参数和计算公式参考
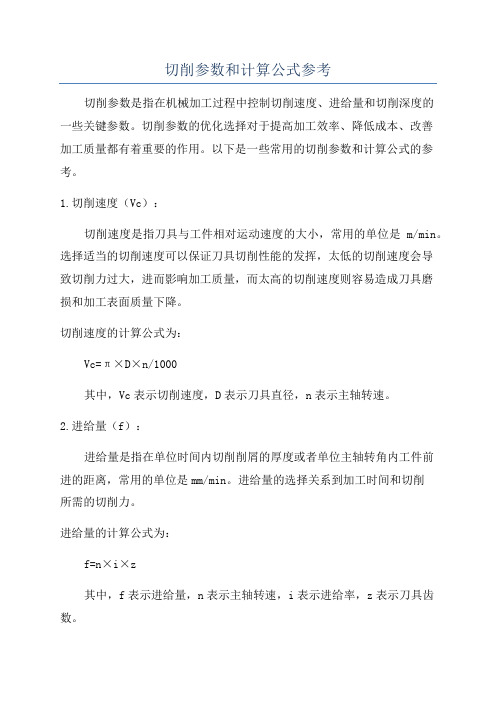
切削参数和计算公式参考切削参数是指在机械加工过程中控制切削速度、进给量和切削深度的一些关键参数。
切削参数的优化选择对于提高加工效率、降低成本、改善加工质量都有着重要的作用。
以下是一些常用的切削参数和计算公式的参考。
1.切削速度(Vc):切削速度是指刀具与工件相对运动速度的大小,常用的单位是m/min。
选择适当的切削速度可以保证刀具切削性能的发挥,太低的切削速度会导致切削力过大,进而影响加工质量,而太高的切削速度则容易造成刀具磨损和加工表面质量下降。
切削速度的计算公式为:Vc=π×D×n/1000其中,Vc表示切削速度,D表示刀具直径,n表示主轴转速。
2.进给量(f):进给量是指在单位时间内切削削屑的厚度或者单位主轴转角内工件前进的距离,常用的单位是mm/min。
进给量的选择关系到加工时间和切削所需的切削力。
进给量的计算公式为:f=n×i×z其中,f表示进给量,n表示主轴转速,i表示进给率,z表示刀具齿数。
3. 切削深度(ap):切削深度是指切削层厚度的大小,即刀具和工件之间的垂直距离。
切削深度的选择应根据工件材料和刀具性能来进行合理的安排。
4.切削力(Fc,Fr):切削力是指刀具对工件施加的力,也是切削参数的重要指标之一、切削力的大小与切削材料的性质、切削速度、进给量和切削深度等因素有关。
切削力的计算公式为:Fc = k × ap × f其中,Fc表示切削力,k表示切削力系数。
5.切削功率(P):切削功率是指切削过程中单位时间内切削所需要的能量,常用单位为W。
切削功率的计算可以帮助选取合适的切削参数,保证切削过程的稳定性和高效性。
切削功率的计算公式为:P=Fc×Vc/6000其中,P表示切削功率,Fc表示切削力,Vc表示切削速度。
综上所述,切削参数的选择是一项复杂的任务,需要结合实际加工情况、刀具性能和工件要求等多方面因素进行综合考虑。
数控车床编程教学计算公式

数控车床编程教学计算公式数控车床是一种通过预先编写的程序来控制刀具和工件之间的相对运动,从而实现对工件进行加工的机床。
数控车床编程是数控加工技术中的重要环节,它涉及到各种计算公式的运用。
本文将介绍数控车床编程中常用的计算公式,并对其进行详细解析。
1. 切削速度(Vc)的计算公式。
切削速度是指刀具在加工过程中与工件接触的线速度,它是数控车床加工过程中的重要参数。
切削速度的计算公式为:Vc = π D n。
其中,Vc为切削速度,π为圆周率(取3.14),D为刀具直径,n为主轴转速。
2. 进给速度(F)的计算公式。
进给速度是指刀具在加工过程中沿着工件表面的运动速度,它也是数控车床加工的重要参数。
进给速度的计算公式为:F = f n z。
其中,F为进给速度,f为进给量,n为主轴转速,z为刀具的刃数。
3. 主轴转速(n)的计算公式。
主轴转速是指主轴每分钟的转动次数,它是数控车床加工中的另一个重要参数。
主轴转速的计算公式为:n = (1000 Vc) / (π D)。
其中,n为主轴转速,Vc为切削速度,π为圆周率,D为刀具直径。
4. 切削力(Fc)的计算公式。
切削力是指刀具在加工过程中对工件施加的力,它是衡量刀具加工性能的重要指标。
切削力的计算公式为:Fc = k ap ae。
其中,Fc为切削力,k为切削力系数,ap为切削深度,ae为切削宽度。
5. 切削功率(Pc)的计算公式。
切削功率是指刀具在加工过程中消耗的功率,它是衡量刀具加工效率的重要指标。
切削功率的计算公式为:Pc = Fc Vc。
其中,Pc为切削功率,Fc为切削力,Vc为切削速度。
以上是数控车床编程中常用的计算公式,这些公式在数控车床编程中起着至关重要的作用。
掌握这些计算公式,能够帮助工程师更好地进行数控车床编程,并且能够更加准确地控制加工过程,提高加工效率,降低加工成本。
除了以上介绍的计算公式外,数控车床编程还涉及到其他一些参数的计算,比如切削时间、切削深度、切削宽度等。
加工参数计算公式

加工参数计算公式
加工参数计算公式是指在机械加工中,根据不同的加工要求,计算出需要使用的各种加工参数的公式。
这些参数包括切削速度、进给量、切削深度等,它们直接影响着加工的效率、质量和安全性。
1. 切削速度计算公式:
Vc=π×D×n/1000
其中,Vc为切削速度,D为刀具直径,n为主轴转速。
单位为m/min。
2. 进给量计算公式:
f=Z×n×fz
其中,f为进给量,Z为齿数,n为主轴转速,fz为每齿进给量。
单位为mm/min。
3. 切削深度计算公式:
ae=Kt×fz×Z
其中,ae为切削深度,Kt为切削力系数,fz为每齿进给量,Z 为齿数。
单位为mm。
4. 切削宽度计算公式:
ap=ae×tanα
其中,ap为切削宽度,ae为切削深度,α为刀具前角。
单位为mm。
以上是常用的加工参数计算公式,不同的加工过程和材料会有所不同,需要根据具体情况进行调整和计算。
在使用计算公式时,需要注意单位的换算,保证计算结果的准确性。
钻孔切削力和切削力矩计算

钻孔切削力和切削力矩计算
按照主轴转速 1000rpm ,进给速度 0.1mm/转,钻穿 1.8mm 约需要时间 1s 。
切削力 Ff
刀具材料:高速钢
加工方式:钻
公式:Ff=309*D*f^(0.8)*(Kp)
参数 :D = 8
参数 :f = 0.1
参数 :Kp = 0.75(按铜合金多相平均 HB>120)
计算结果 = 293.839
切削力矩 M
工件材料:灰铸铁 (HB190)
刀具材料:高速钢
加工方式:钻
公式:M=0.21*D^(2)*f^(0.8)*(Kp)
参数 :D = 8
参数 :f = 0.1
参数 :Kp = 0.75(按铜合金多相平均 HB>120)
计算结果 = 1.597
二、铣削切削力计算
铣削切削力计算类别:
工件材料:碳钢、青铜、铝合金、可锻铸铁等
刀具材料:高速钢
铣刀类型:端铣刀
公
式:F=(Cp)*(ap)^(1.1)*(fz)^(0.80)*D^(-1.1)*B^(0.95)*z*(Kp) 参数 :Cp = 294
参数 :ap = 1.8
参数 :fz = 0.5
参数 :D = 8
参数 :B = 8
参数 :z = 4
参数 :Kp = 0.75
计算结果 = 707.914。
铣削力计算表格

假设我们使用直径为100mm的铣刀进行铣削,刀具转速为500rpm,切削深度为2mm,进给速度为50mm/min。
首先,我们需要了解铣刀的切削面积,这可以通过以下公式计算:
切削面积= π × (刀具直径/2)^2 ×切削深度
将给定的值代入公式中,我们可以得到:
切削面积= 3.14 × (100/2)^2 × 2 = 31400 mm^2
接下来,我们需要了解切削力与切削面积的关系。
通常,切削力与切削面积成正比,所以我们可以使用以下公式来计算切削力:
切削力= 常数×切削面积
其中,常数是一个经验值,它取决于刀具的材料、切削条件和工件材料。
在实际应用中,这个常数需要通过实验来确定。
假设常数为10N/mm^2,代入公式中,我们可以得到:
切削力= 10 × 31400 = 314000 N
所以,对于给定的铣削条件,铣削力大约为314000N。
外圆磨削力计算公式

外圆磨削力计算公式
外圆磨削力是机械加工中的重要参数之一,它直接影响到加工质量和效率。
下面介绍外圆磨削力计算公式:
1. 线速度计算公式
外圆磨削力的计算需要用到外圆切割速度,其计算公式如下:v = π × D × n / 1000
其中,v为线速度,单位为m/min;D为工件直径,单位为mm;n为主轴转速,单位为r/min。
2. 切削深度计算公式
切削深度是指磨削刀具与工件接触的深度,它是磨削力计算的重要参数之一。
其计算公式如下:
ap = (D - d) / 2
其中,ap为切削深度,单位为mm;D为工件直径,单位为mm;d为刀具直径,单位为mm。
3. 磨削切削力计算公式
根据切削力公式,磨削切削力可以通过以下公式计算:
Fc = k × ap × b × vf
其中,Fc为磨削切削力,单位为N;k为材料特性系数;ap为切削深度,单位为mm;b为磨削刀具刃数;vf为磨削速度,单位为m/min。
以上是外圆磨削力计算公式的详细介绍,希望对大家有所帮助。
切削参数和计算公式

切削参数和计算公式切削参数是决定切削加工过程中各项切削条件的重要参数,包括切削速度、进给量、切削深度等。
正确选择切削参数可以提高工件的加工质量和加工效率,降低刀具的磨损和工时成本。
在进行切削参数的选择时,需要考虑材料的硬度、韧性、切削性能以及刀具的材料、形状和质量等因素,综合考虑才能确定最佳的切削参数。
一、切削参数的影响因素1. 切削速度:切削速度是指工件上切削过程中切削刀具进给的线速度,一般用V表示,单位是m/min。
切削速度的选择直接影响到切削加工的效率和切削表面质量。
通常情况下,切削速度越高,加工效率越高,但是也会导致刀具的磨损增加。
切削速度的选择要根据材料的硬度和切削性能来确定。
2. 进给量:进给量是指每分钟工件沿切削刀具的运动方向移动的距离,一般用f表示,单位是mm/rev。
进给量的选择影响到切削中切屑的形成和工件表面的光洁度。
进给量越大,切屑越容易破碎和排出,工件表面粗糙度越大,但是加工效率越高。
进给量的选择要根据切屑的形成和排出情况以及工件表面要求来确定。
3. 切削深度:切削深度是指切削刀具在一次切削过程中切入工件的深度,一般用a表示,单位是mm。
切削深度的选择直接影响到切削力和切屑的形成。
切削深度越大,切削力越大,切屑的形成和排出也更加困难。
切削深度的选择要根据工件的尺寸和形状以及切削刀具的刃数和形状来确定。
4.切削角度:切削角度是指切削刀具刀尖与工件表面之间的夹角,一般用α表示。
切削角度的选择影响到切削力和切屑的形成。
切削角度越小,切削力越小,但是刀具的强度也会减小。
切削角度的选择要根据工件材料的硬度和切削性能以及切削刀具的刃数和形状来确定。
二、切削参数的计算公式1.切削速度的计算公式:切削速度V=π×D×N/1000其中,V为切削速度,单位是m/min;D为刀具直径,单位是mm;N 为主轴转速,单位是r/min。
2.进给量的计算公式:进给量f=V×n其中,f为进给量,单位是mm/rev;V为切削速度,单位是m/min;n 为主轴转速,单位是r/min。
- 1、下载文档前请自行甄别文档内容的完整性,平台不提供额外的编辑、内容补充、找答案等附加服务。
- 2、"仅部分预览"的文档,不可在线预览部分如存在完整性等问题,可反馈申请退款(可完整预览的文档不适用该条件!)。
- 3、如文档侵犯您的权益,请联系客服反馈,我们会尽快为您处理(人工客服工作时间:9:00-18:30)。
一、钻孔切削力和切削力矩计算
按照主轴转速1000rpm,进给速度0.1mm/转,钻穿1.8mm约需要时间1s。
切削力Ff
刀具材料:高速钢
加工方式:钻
公式:Ff=309*D*f^(0.8)*(Kp)
参数:D = 8
参数:f = 0.1
参数:Kp = 0.75(按铜合金多相平均HB>120)
计算结果= 293.839
切削力矩M
工件材料:灰铸铁(HB190)
刀具材料:高速钢
加工方式:钻
公式:M=0.21*D^(2)*f^(0.8)*(Kp)
参数:D = 8
参数:f = 0.1
参数:Kp = 0.75(按铜合金多相平均HB>120)
计算结果= 1.597
二、铣削切削力计算
铣削切削力计算类别:
工件材料:碳钢、青铜、铝合金、可锻铸铁等
刀具材料:高速钢
铣刀类型:端铣刀
公式:F=(Cp)*(ap)^(1.1)*(fz)^(0.80)*D^(-1.1)*B^(0.95)*z*(Kp) 参数:Cp = 294
参数:ap = 1.8
参数:fz = 0.5
参数:D = 8
参数:B = 8
参数:z = 4
参数:Kp = 0.75
计算结果= 707.914。