喷头及氧枪设计计算
喷嘴设计

喷嘴设计计算一、已知数据CH4、O2都按照理想气体计算,并且氧气中只含有O2,天然气进料中只含有甲烷。
a)进料Q O2=10L/minQ CH4=20L/min(室温下,20o C,0.2MPa)b)温度、压力进料温度,从室温预热至500o C,压力按照理想气体计算得到c)进料速度根据气体燃料喷头的设计取得O2进料速度设定为u1=40m/sCH4进料速度设定为u1=150m/sd)符号Q——体积流量,L/min;u1、u2分别为O2的进料、出口速度,m/s;u1、u2分别为CH4的进料、出口速度,m/s;Di、Do、D*分别是O2进口、出口、喉、口直径,mm;di、do分别是CH4的进口、出口直径,mm;L1、L2——喷嘴喉、口前后两端的长度,mm;α——喷头的锥度二、主流道的尺寸计算O2由室温条件预热到500 o C,体积膨胀,体积流量变大,由理想状态方程,得①假设气体压力保持不变,则得出Q O2=26.4L/min由气体流量计算Q=Su以及圆面积公式③得出Di=3.7mm 可以约等于Di=4mm修正进料速度u1=35m/s由切割喷嘴的参考经验,入口直径Di=(2)D*,取2 D*,则D*=2mm由声速④得声速c=95m/s其中——气体绝热指数,O 2为1.4R——气体常数,取8.314,J/〔mol·K〕T——绝对温度,K马赫数⑤计算得Ma=0.37*5.12651D M M D o ⎪⎪⎭⎫ ⎝⎛+= ⑥ 得Do=2.5mm ,喷嘴入口收缩长度L1=(0.8)Di ,L1=4mm喷嘴出口超音速长度L2大于2Do ,取4Do=10mm 喷嘴的喉口段长度可以用短的直线段(长度为2mm )加上两端过渡到两个圆锥相切的圆弧来形成。
三、副流道核算由文献可知,一般情况下,主流道与副流道的压力比为4,所以副流道的压力是0.05Mpa ,由①式得,Q CH4=211L/min再由 ③式算出di=5.46mm ,取di=5.5mm还可以由另外一种方法得出,预热氧气与天然气进口面积之比是1:2,则di=Di=5.5mm ,两者结果一致设计时。
转炉吹氧相关计算

转炉吹氧相关计算一、120t转炉熔池深度的计算:(以1#转炉为例)1、熔池体积:V池=G/ρ式中,G-公称容量,取125t;ρ-钢水密度,取7.8t/m3。
V池=G/ρ=125/7.8=16.03 m32、熔池深度h:根据测厚仪测出1#转炉的熔池直径D=6570mm,熔池体积V池和熔池直径D及熔池深度h有如下关系:V池=0.665hD2-0.033D3所以h=V池+0.033D30.665D2=16.03+0.033×6.5730.665×6.572=884mm二、氧枪氧气射流冲击深度L的计算:通常冲击深度L与熔池深度h之比选取L/h≈0.4~0.6为宜。
操作实际证明,当L/h<0.3时,即冲击深度过浅,则脱碳速度和氧的利用率会大大降低,还会导致出现终点成分及温度不均匀的现象;当L/h>0.7时,即冲击深度过深,有可能损害炉底并喷溅严重。
1、枪位不变H0(基本枪位1.6m),选取1#转炉氧气压力0.43Mpa,0.60Mpa,计算冲击深度L。
当氧压p0=0.43Mpa时,氧气流量Q=13868m3/h,根据冲击深度L 的经验公式:L=34×p0×D喉/√H0+3.8式中,D喉—氧枪喷头喉口直径,取35.6mm;P0-氧气喷嘴压力,取0.43Mpa;H0—枪位,取基本枪位160cm;则L=34×0.43×35.6/√160+3.8=44.95cm对于五孔喷头取修正系数0.85,则修正后的冲击深度L=44.95×0.85=38.20cm,冲击深度L与熔池深度h的笔直L修/h=382/884=0.43。
当氧气压力位0.6Mpa时,氧气流量Q=19085 m3/h冲深度L=34×0.6×35.6/√160+3.8=61.21cm,修正后的冲击深度为61.21×0.85=52.03cm,冲击深度L与熔池深度h的比值L修/h=0.59。
喷嘴设计及计算
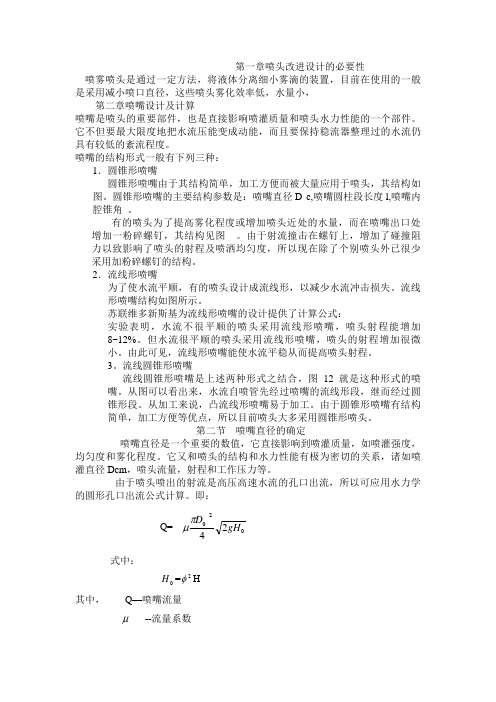
流线圆锥形喷嘴是上述两种形式之结合,图12就是这种形式的喷嘴。从图可以看出来,水流自喷管先经过喷嘴的流线形段,继而经过圆锥形段。从加工来说,凸流线形喷嘴易于加工。由于圆锥形喷嘴有结构简单,加工方便等优点,所以目前喷头大多采用圆锥形喷头。
第二节喷嘴直径的确定
喷嘴直径是一个重要的数值,它直接影响到喷灌质量,如喷灌强度,均匀度和雾化程度。它又和喷头的结构和水力性能有极为密切的关系,诸如喷灌直径Dcm,喷头流量,射程和工作压力等。
提供各种雾化效果最佳选择:
压力值一般为0.2-0.7Mpa左右
而当管口直径为2~3毫米时,H/Dc值选3000,压力值选0.7Mpa左右,喷嘴仰角在40度到45度左右,
光洁度在 。
四改变喷头喷洒轨迹的力学途径
很多喷头采用的是喷洒轨迹为弧形的喷洒喷头,很浪费水源,面对多种喷洒的要求,本研究采用弧形轨迹改为方形轨迹为研究对象,依据流体力学原理,提出改变喷头喷洒轨迹的力学方法及途径。
喷嘴光洁度
流量系数
0.86
1.84
三设计喷头最优参数选择
由以上应选取45度内锥角,流量系数为0。86。光洁度(表面光洁度)应为 。考虑影响射程和水滴直径H/Dc值,H/Dc对喷头有高度影响,比值H/Dc在一定程度上反映雾化程度,即喷洒雨滴的直径,所以大家把它称为雾化指标。当H/Dc=3000时有最远射程。喷头工作压力和喷头直径的比值H/Dc是随其增加,水滴直径将减小,对于不同的喷嘴,,在相同的H/Dc下,随着喷嘴直径的增加而水滴直径将减小。
综上所述,由于喷嘴直径的大小影响到喷头的喷洒量,功率消耗,射程和水底大小,,所以喷嘴止直径的确定,应以式
喷头直径Dc(毫米)
适宜的H/Dc值
2~4
2喷淋计算(给排水专业)
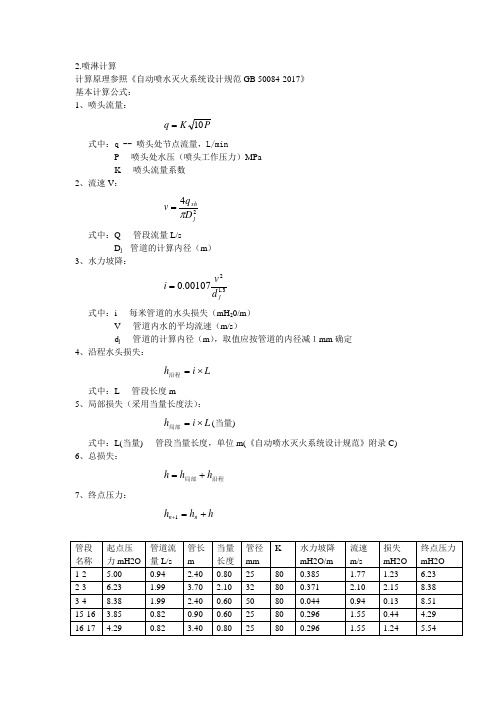
2.喷淋计算
计算原理参照《自动喷水灭火系统设计规范GB 50084-2017》 基本计算公式: 1、喷头流量:
P K q 10=
式中:q -- 喷头处节点流量,L/min
P -- 喷头处水压(喷头工作压力)MPa K -- 喷头流量系数 2、流速V :
2
4j
xh
D q v π=
式中:Q -- 管段流量L/s
D j --管道的计算内径(m ) 3、水力坡降:
3.12
00107.0j
d v i =
式中:i -- 每米管道的水头损失(mH 20/m ) V -- 管道内水的平均流速(m/s ) d j -- 管道的计算内径(m ),取值应按管道的内径减1mm 确定 4、沿程水头损失:
L i h ⨯=沿程 式中:L -- 管段长度m
5、局部损失(采用当量长度法): L i h ⨯=局部(当量)
式中:L(当量) -- 管段当量长度,单位m(《自动喷水灭火系统设计规范》附录C) 6、总损失:
沿程局部h h h += 7、终点压力:
h h h n n +=+1
计算结果:
所选作用面积:162.7平方米
总流量:23.97 L/s
平均喷水强度:9.21 L/min.平方米
本层入口压力:26.62 +2+48=76.62米水柱。
发电机房水喷雾设计计算书
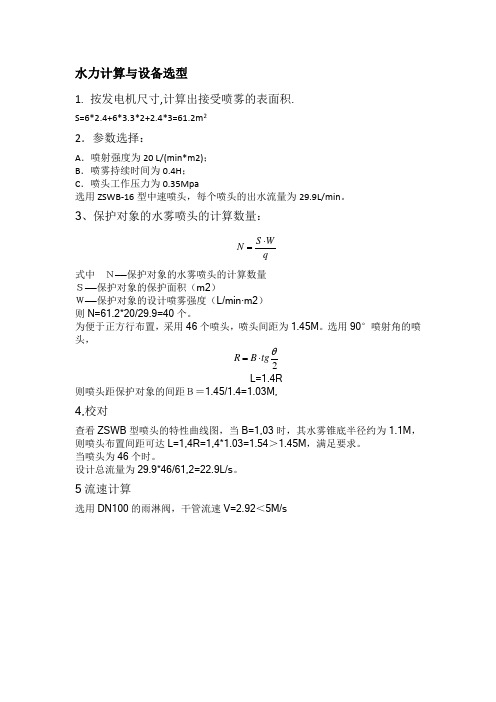
水力计算与设备选型
1. 按发电机尺寸,计算出接受喷雾的表面积.
S=6*2.4+6*3.3*2+2.4*3=61.2m 2
2.参数选择:
A .喷射强度为20 L/(min*m2);
B .喷雾持续时间为0.4H ;
C .喷头工作压力为0.35Mpa
选用ZSWB-16型中速喷头,每个喷头的出水流量为29.9L/min 。
3、保护对象的水雾喷头的计算数量:
S W N q
⋅= 式中 N——保护对象的水雾喷头的计算数量
S——保护对象的保护面积(m2)
W——保护对象的设计喷雾强度(L/min·m2)
则N=61.2*20/29.9=40个。
为便于正方行布置,采用46个喷头,喷头间距为1.45M 。
选用90°喷射角的喷头,
2
R B tg θ=⋅ L=1.4R
则喷头距保护对象的间距B=1.45/1.4=1.03M,
4,校对
查看ZSWB 型喷头的特性曲线图,当B=1,03时,其水雾锥底半径约为1.1M ,则喷头布置间距可达L=1,4R=1,4*1.03=1.54>1.45M ,满足要求。
当喷头为46个时。
设计总流量为29.9*46/61,2=22.9L/s 。
5流速计算
选用DN100的雨淋阀,干管流速V=2.92<5M/s。
喷嘴压力等计算公式之欧阳学创编

有关计算公式
时间:2021.03.03 创作:欧阳学
1、泵压力、流量→求电机功率
: 泵额定压力MPa,: 泵流量L/min, :电机功率kW.
泵压力、流量→求发动机功率
: MPa, : L/min, : kW.
2、喷嘴直径计算及喷嘴选择
(1)
式中, 为喷嘴直径,mm;为喷射压力,bar;
为喷射流量,L/min;为喷嘴个数.
为喷嘴效率系数,对喷枪喷嘴0,对柔性喷杆
(2)
式中, Nozzle#为喷嘴索引号;q: 流量, GPM (gal/min);p: 压力, psi(lb/inch2)
3、管路压力损失计算
高压硬管压力损失:,雷诺数:
高压软管压力损失:,雷诺数:
式中:∆p为压力损失,MPa/m;为流量,L/min; D 为钢管(软管)内径,mm.
4、高压水射流反作用力计算
:反作用力,N;:有效流量,L/min; :工作压力,MPa
:反作用力,N;:有效流量,L/min; :工作压力,bar
:反作用力,lb;:有效流量,L/min;
:工作压力,psi
时间:2021.03.03 创作:欧阳学。
转炉设计(2)
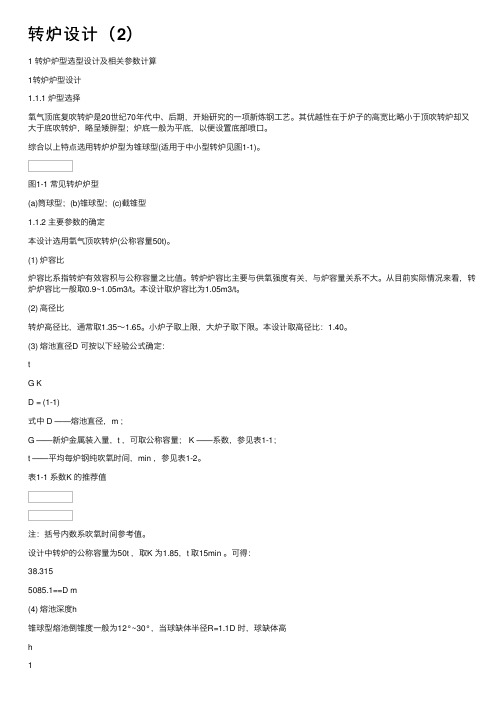
转炉设计(2)1 转炉炉型选型设计及相关参数计算1转炉炉型设计1.1.1 炉型选择氧⽓顶底复吹转炉是20世纪70年代中、后期,开始研究的⼀项新炼钢⼯艺。
其优越性在于炉⼦的⾼宽⽐略⼩于顶吹转炉却⼜⼤于底吹转炉,略呈矮胖型;炉底⼀般为平底,以便设置底部喷⼝。
综合以上特点选⽤转炉炉型为锥球型(适⽤于中⼩型转炉见图1-1)。
图1-1 常见转炉炉型(a)筒球型;(b)锥球型;(c)截锥型1.1.2 主要参数的确定本设计选⽤氧⽓顶吹转炉(公称容量50t)。
(1) 炉容⽐炉容⽐系指转炉有效容积与公称容量之⽐值。
转炉炉容⽐主要与供氧强度有关,与炉容量关系不⼤。
从⽬前实际情况来看,转炉炉容⽐⼀般取0.9~1.05m3/t。
本设计取炉容⽐为1.05m3/t。
(2) ⾼径⽐转炉⾼径⽐,通常取1.35~1.65。
⼩炉⼦取上限,⼤炉⼦取下限。
本设计取⾼径⽐:1.40。
(3) 熔池直径D 可按以下经验公式确定:tG KD = (1-1)式中 D ——熔池直径,m ;G ——新炉⾦属装⼊量,t ,可取公称容量; K ——系数,参见表1-1;t ——平均每炉钢纯吹氧时间,min ,参见表1-2。
表1-1 系数K 的推荐值注:括号内数系吹氧时间参考值。
设计中转炉的公称容量为50t ,取K 为1.85,t 取15min 。
可得:38.3155085.1==D m(4) 熔池深度h锥球型熔池倒锥度⼀般为12°~30°,当球缺体半径R=1.1D 时,球缺体⾼h1=0.09D 的设计较多。
熔池体积和熔池直径D 及熔池深度h 有如下的关系:23665.0033.0DD V h +=池 (1-2)由池V G 1ρ=可得:09.705.7501===ρGV 池(m 3)将池V 代⼊式(7-2)得:98.038.3665.038.3033.009.7665.0033.02323=??+=+=DD V h 池(m)(5) 炉⾝⾼度⾝H转炉炉帽以下,熔池⾯以上的圆柱体部分称为炉⾝。
氧枪设计第四章

第四章氧气转炉供氧系统设计供氧系统工艺流程氧气转炉炼钢车间的供氧系统是由制氧机、加压机、中压储气罐、输氧管、操纵闸阀、测量仪器、氧枪等要紧设备组成。
图9 供氧系统工艺流程图1—制氧机2—低压储气柜3—压氧机4—桶形罐5—中压储气罐6—氧气站7—输氧总管8—总管氧压测定点9—减压阀10—减压阀后氧压测定点11—氧气流量测定点12—氧气温度测定点13—氧气流量调剂阀14—工作氧压测定点15—低压信号连锁16—快速切断阀17—手动切断阀18—转炉转炉炼钢车间需氧量计算(1)一座转炉吹炼时的小时耗氧量计算①平均小时耗氧量Q1(Nm3/h):947438512060T 60GW Q 11=⨯⨯==Nm 3/h (4-1) 式中: G —平均炉产钢水量,120t ;W —吨钢耗氧量,50m 3/t ,范围45~55m 3/t ; T 1—平均每炉钢水冶炼时刻,38min 。
② 顶峰小时耗氧量Q 2(m 3/h ):22500165012060T 60GW Q 22=⨯⨯==Nm 3/h (4-2) 式中:T 2—平均每炉纯吹氧时刻,16min 。
(2)车间小时耗氧量① 车间平均小时耗氧量Q 3(m 3/h ):Q 3=NQ 1=3×9474=28422m 3/h (4-3)式中:N —车间常常吹炼的炉座数。
② 车间顶峰小时耗氧量Q 4(m 3/h ):Q 4=N×Q 2=67500m 3/h (4-4)制氧性能力的选择关于专供氧气转炉炼钢利用的制氧机的生产能力必需依照转炉车间需氧选择。
制氧机的总容量依照炼钢车间小时平均耗氧(28422 m 3/h )量确信,通过在制氧机和转炉之间设置储气罐来知足车间顶峰用氧量。
在决定制氧机组的能力时,还需考虑制氧机国家标准系列。
目前我国可供氧气转炉车间选用的制氧机系列有:1000 3/m h 、15003/m h 、3200 3/m h 、6000 3/m h 、10000 3/m h 、20000 3/m h 、26000 3/m h 、35000 3/m h 等。
- 1、下载文档前请自行甄别文档内容的完整性,平台不提供额外的编辑、内容补充、找答案等附加服务。
- 2、"仅部分预览"的文档,不可在线预览部分如存在完整性等问题,可反馈申请退款(可完整预览的文档不适用该条件!)。
- 3、如文档侵犯您的权益,请联系客服反馈,我们会尽快为您处理(人工客服工作时间:9:00-18:30)。
第三部分喷头及氧枪设计计算(一)喷咀理论与设计一、有关公式[5]5371、缩放管公式(M2—1)错误!未找到引用源。
=错误!未找到引用源。
(3—1)讨论马赫数M=V/a (3—2)①M<1为亚音速,V<a,当断面缩小(dA=—),则流速增大(dv=+);②M=1为音速,V=a,喉口处面积不变(dA=0),为音速段(dV=0);③M>1为超音速,V>a,当断面放大(dA=+),则流速增大(dV=+)。
因此,当可压缩流在经过缩放喷咀后,流速可经亚音速,音速而得超音速,从而使氧气由压力能转化为超音速动能,用以搅拌熔池进行冶金反应。
2、三孔喷头在不同单位时的氧流量计算式[5]546错误!未找到引用源。
=3错误!未找到引用源。
0.4167P0A*/错误!未找到引用源。
[kg/S] (3—3)错误!未找到引用源。
=3错误!未找到引用源。
17.5P0A*/错误!未找到引用源。
[Nm3/min] (3—4)式中:A*——喉口面积[cm2]P0——设计氧压[kg/cm2]而KgO2=0.7[Nm3](参[2]628)3、用冷却水温度代氧滞止温度后的影响取氧气贮气罐滞止温度T0=15°C(288K),冷却水温度T水=20°C(293K),当用T水代T0上升5°C,对氧气流量地影响为:Wo2(288)/ Wo2(293)=错误!未找到引用源。
=错误!未找到引用源。
=1.0085即用T水代T0升温对氧气流的影响为0.0085<1%因此可用T水错误!未找到引用源。
T0(参[5]557)4、当确定出口马赫数后如提高供养压力,则出口压力,滞止温度和出口温度都相应提高。
错误!未找到引用源。
=(1+错误!未找到引用源。
)-7/2=错误!未找到引用源。
[5]546 (3—5)5、贮气罐的表压力可代喷头入口处的绝对氧压关系式为:错误!未找到引用源。
+(错误!未找到引用源。
—错误!未找到引用源。
)=错误!未找到引用源。
(3—6)式中:错误!未找到引用源。
贮气、表压力与喷咀入口氧压等错误!未找到引用源。
用于克服管道阻力损失,其值约1大气压,因此可认为近似地抵消了大气压力错误!未找到引用源。
错误!未找到引用源。
符号“0”指滞止状态,也即为设计氧压或供用氧压6、出口马赫数M=V/a=42.646错误!未找到引用源。
/19.07错误!未找到引用源。
[5]536 (3—7)=2.244错误!未找到引用源。
(3—8)P绝=P液+P大气(=P0=P设=P供)图3-1 转炉供氧各部压力示意图二、参数分析1、三孔喷头氧流量=(加废钢后每吨钢耗氧量)错误!未找到引用源。
(出钢量)/(吹氧量)[Nm3/min](3—9)或Qo2=3错误!未找到引用源。
17.5P0A*/错误!未找到引用源。
[Nm3/min] (3—10)①令后期炉膛扩大,为保持炉容比(V/T)和吹氧时间不变应同时提高出钢量和氧流量;②提高氧流量的方法有两种:提高氧压P0或换枪使用时增大喉口面积A*和出口面积A(由表3—1知出口马赫数可保持不变)。
表3—1 可压缩气体等熵流各参数的比值表M P/P0T/T0A/A*1.5 1.1761.95 1.6191.96 1.6331.97 1.6461.98 1.6601.99 1.6742.001.6882.011.7022.021.7162.031.7302.041.7452.051.7602.302.1932.502.6373.04.2352、供氧强度=加废钢后每吨钢耗氧量/吹氧时间[Nm 3/T 错误!未找到引用源。
min] 当渣量少,炉容比大,喷空多均可提高供氧强度而缩短冶炼时间。
3、设计工况氧压(P 设=P 0)和出口马赫数M 的确定 取:冷却水温度代滞止氧温度T 0=17[°C]=290[K]炉内压力P=1大气压=1.034[kg/cm 2]可由式(3—5)、(3—6)和表3—1得表3—2及图3—2表3—2不同出口马赫数M 时所需的设计工况氧压(P 设)与各出口参数间的关系M T 0[K] a o [m/S] V 0[m/S] P 设=P 0[kg/cm 2]1.5 200.01 269.70 404.55 3.802.0 161.12 242.06 484.12 8.10 2.3 140.91 226.37 520.65 12.93 2.5 128.88 216.49 541.23 17.673.0103.56194.06582.2038.00① 由表3—2及图3—2可知 630 580 530 P 设=P 0[㎏/㎡]V 出[m/s]25 20 15 P 0V图 3—2 出口马赫数M 与P 设、V 出的关系图提高出口马赫数需相应提高设计工况氧压,但可得较大的出口速度取得较好的搅抖动能; ② 新炉取出口马赫数M=2时,由图或计算可知,设计工况氧压P 设=8.1[kg/cm 2]较低,但出口氧速V出=484[m/S]较高;③ 当M>2时,P 设上升快而V 出的上升曲线则变平,因此取M=2时比较经济合理,即设计氧压不高,但出口氧速大,搅拌好。
V 出的上升曲线在M>2后变平的原因可从表3一2中看出,原因是出口温度T 下降,和音速(a=19.07T)随之下降有关,这时P 设上升快而V 出上升慢(图3一2)。
气体动能分配估计: (参〔4〕16)搅拌. 克服浮力 非弹性碰撞 200% 5~1000 70~80%例1:取出口马赫数M=2,出口压力与炉内环境压力相等为P=1. 0348.1[kg/cm 2],并用冷却水温度代滞止氧气温度T 0=290[K],求喷头前供氧压力P o [kg/cm 2]绝对,以及出口氧流速V [m/S]和喷咀出口与喉口的直径比D/D*各为多少?解:由表3-1知,当M=2时可得等嫡流的参数比值如下: A/A*=1.688 ;两边开方得D/D* =1. 299 P/P 0=0.1278;或P o =1.034/0.1278=8.1[kg/cm 2] T/T 0=0.5556;或T=0. 5556 X 290=161.12[K]T=12. 7因此可得 V=Ma=2X19.07T=2X19.07X12.7=484[m/S] (见图3一2)也可由(3-7)式计算; V=42.6460T T-=42.646290161.12-=484[m/S]例2:如取出口马赫数M=2. 3,则设计氧压应提高为12. 98[kg/cm 2],Vm=520.65}[m/S](见表3一2)这里: 设计工况氧压提高12.938.18.1-=60%出口氧速仅提高520.65484484-=7.6%因此M=2时比较经济合理.如氧压许可,也可选用M>2 ,如M=2. 2~2. 3这对三孔喷 愉相应可提高枪位对枪令极为有利。
④生产炉不取M<2,因在低马赫数区,只要用较少的供氧压力%使可换取更大的出口氧速度%(见表3一3)。
表3—3 △M 相等氧压,出口速度相应增值比较表M 上升值相同△M△P%△V%M由1.5上升到2.0 0.5 8.1 3.83.8-=113%484404404-=20%M由2.0上升到2.5 0.5 17.678.18.1-=118%541484484-12%4、炉膛压力、出口氧压和供氧压力间的关系一般设计计算取喷头在炉内的环境压力为1个大气压,即P=P出口=P=1.034[㎏/C㎡]。
当取M=2时则P/P0=0.1278,由此可得新炉设计工况氧压P0 =1.034/0.1278=8.1[㎏/C㎡](参表3—1及3—2)。
①当喷头前氧压由Po=8. 1[kg/cm2」经缩放管达到出口断而处则下降到出口氧压P出=1.034[时压力能可全部转为超音速动能,且由于P出=P周因此可确保吹炼平稳。
②当氧枪和出口马赫数M=2已定,如提高操作氧压Po,则由式((3-5)将会相应提高出口氧压P并同时提高滞止氧和出口氧的温度T。
和T2换言之,出口音速与出口氧速也将同时提高(参式3-7)。
如假设T。
不变,则由式((3-8)可知T也不会改变。
因此可使出口氧速V也不变(参3-7)。
由上面分析可提出这样的结论:“在氧气的滞止温度为定值时,氧气流出速度是氧气喷孔出口断面积与临界断面积之比的函数,而与压力无关”(见[4]月13)。
否则出口氧速V与使用氧压有关(见[5]594)。
③如供氧压力低于8.1[kg/cmZ〕时,则由于P出口<P,会在喷孔出口处产生负压吸入金属熔滴和熔渣微粒发生喷头烧坏并使射流变形导致枪令下降。
④炉内实际环境压力由于泡沫上升和CO气体的排出,因此比1. 034[kg/cm2]稍大。
因此生产炉的实际使用氧压应稍大于8.1[kg/cma2],炉龄后期可提高供氧压力,但不大于P设的50%,一般后期为Po=12[kg/cm2]。
5、喷孔夹角和喷孔问距①三孔喷头的喷孔夹角一般为8°~12°(喷头与喷孔中心线夹角),可在正常枪位下达到(R冲/R熔}=0.1~0.2的范围而有利于化渣,防喷并提高枪令,当熔池较深时可取下限以提高搅拌强度,由于三股射流有相互吸引的作用,如喷孔夹角<7°。
则R冲/R熔<0. 1,会发生流股汇交类似于单孔喷头不利化渣,还易增大喷溅,如喷头夹角>12°,则高温氧流会冲刷炉壁,同时由于流股中心偏转较大使流速低对搅拌熔池不利,但随着喷头孔数的增加喷孔夹角也相应增大.。
表3一4推荐设计喷孔数和喷孔夹角的参数喷头孔数 3 4 5 >5 喷孔数增多喷空夹角9°~11°10°~11°13°~14°15°~17°喷空夹角增大②喷孔间距对射流产生的相互影响,间距过小,射流之间产生的吸引力会增大相互交汇的趋势,如增大喷孔间距,除可起增大喷孔夹角的效.果外,还不会降低射流中心的最大流速,这与增大喷孔夹角而降低中心最大流速是不同的,对三孔喷头取喷头中心与喷孔端面中心距为(0.8~1.0)d出时,可使氧流速的衰减变慢。
6、喷头端面形状为保证超音速氧流在出口时具有对称的边界条件而不影响流股的形态,喷孔的出口断面应为正口拉瓦尔型,即端面应设计成与喷孔中心线垂直的圆锥面,其圆锥角α与喷孔夹角相同,为改善端面顶部的冷却条件,也可设计成截头圆锥体。
7、喷孔缩放断面尺寸的确定收缩段为亚音速,马赫数M<0.2~1;喷头处为音速,故马赫数M=1;扩张段为超音速,因此M=1~2,尺寸表示如图3-3所示。
①半扩张角4°一6°(图3一3)过小一─扩张段长度增加而附面层增厚,除阻损增加外,由子减小了实际出口断面积并使出口氧速下降。