连杆设计的详细计算
连杆计算
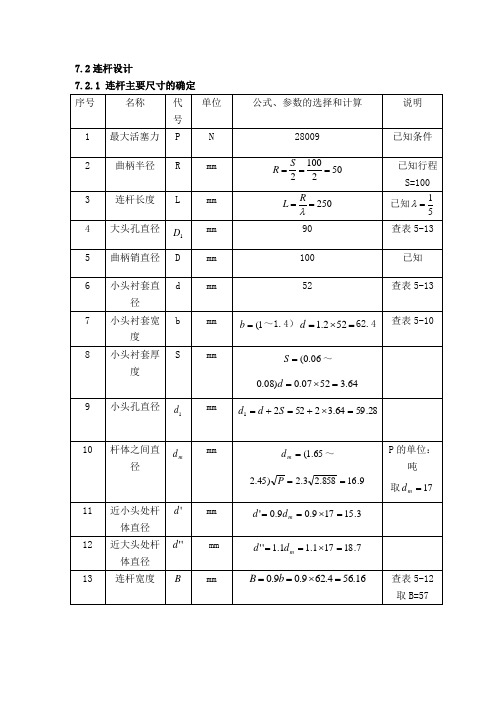
惯性矩
7
连杆摆动平面纵弯应力
8
杆体的长度
mm
9
惯性矩
10
垂直于连杆摆动平面纵弯应力
11
在连杆摆动平面总应力
12
垂直于连杆摆动平面总应力
13
大头盖截面 处抗弯截面模数
14
截面A-A弯曲应力
15
小头处截面C-C抗弯截面模数
16
小头侧壁中心距
mm
17
截面C-C弯曲应力
7.2连杆设计
7.2.1连杆主要尺寸的确定
序号
名称
代号
单位
公式、参数的选择和计算
说明
1
最大活塞力
P
N
28009
已知条件
2
曲柄半径
R
mm
已知行程
S=100
3
连杆长度
L
mm
已知
4
大头孔直径
mm
90
查表5-13
5
曲柄销直径
D
mm
100
已知
6
小头衬套直径
d
mm
52
查表5-13
7
小头衬套宽度
b
mm
~1.4) 62.4
~
20
截面C-C的厚度mm取 Nhomakorabea21
连杆螺栓直径
mm
~
P的单位:吨
22
两螺栓间距离
mm
120
查表5-13
23
螺栓在大头体内长度
mm
~
24
螺栓在大头盖内长度
mm
~
7.2.2连杆的计算
序号
名称
代号
单位
概念设计阶段连杆强度计算规范

CAE 规范第1部分:概念设计阶段连杆强度计算1 范围本部分规定了连杆强度的校核方法。
本部分适用于概念设计阶段连杆强度的校核,以安全系数表示连杆在发动机产品生命周期内的安全裕度。
对船用发动机,需同时采用船检规范进行校核。
2 名称、符号图1 连杆杆身最小截面模型示意图表-1 连杆强度计算参数序号 名称 符号单位 1连杆质量rod m kg2 活塞组质量 pst mkg 3 连杆长度 Lmm 4 缸套内径 D mm 5连杆大头轴瓦宽度ps Lmm6 连杆主轴瓦宽度js Lmm7 杆身最小截面积 A2mm 8 极惯性矩(z 轴) z I 4mm 9极惯性矩(y 轴)y I4mmσMPa10 材料的屈服极限sL mm11 连杆大小头孔中心距y12 连杆杆身长z L mm13 材料的抗拉强度bσMPaσMPa13 材料的疲劳极限1-14 转速n rpm15 最大爆压g p MPa 3 计算流程图2 流程图4 计算原理连杆的设计基于对高应力区域的疲劳安全进行评估。
本规范中的计算基于以下假定:●连杆小头内侧、杆身过渡圆角处、大头盖螺栓台阶面是高应力区域;●活塞组往复惯性力以轴向抛物线、径向120°余弦分布作用在小头衬套和连杆轴瓦上;●爆发压力以轴向抛物线、径向120°余弦分布作用在小头衬套和连杆轴瓦上;●活塞组往复惯性力、爆发压力是引起连杆破坏的主要因素,连杆旋转惯性力产生的影响很小,可以忽略不计。
5 计算工况对长期稳定工作于额定转速的发动机,以全负荷工况为计算工况;对在大转速范围内工作的发动机,以额定转速为计算工况;对船用发动机,以超负荷(110%负荷)工况为计算工况。
通常,一个工作周期内,由燃气压力和惯性力引起的作用在连杆上的径向载荷对所有曲柄位置都应计算。
简单起见,径向力可以采用简化计算,并只计算一个工作周期内的最大受拉和最大受压两种状态。
6 连杆载荷6.1 压杆稳定时连杆载荷连杆属于细长杆件类的柴油机零件,在承受较大爆发压力的工况下须做杆件的稳定性校核:临界载荷由Rankine Gordan 公式计算:p zz F pn = py yF p n =6.2 连杆受到惯性载荷连杆载荷以大小头孔轴向抛物线、径向120°余弦分布的分布力作用在衬套和连杆轴瓦上,作用范围为连杆大头轴瓦宽度(见图3-b ),其大小按以下公式计算:θθ23cos )41(25),(22psps p p p L x L D F x q -⋅=p F :作用在衬套和连杆轴瓦上的径向载荷,N ;对于连杆小头p F 可按曲柄连杆动力学或多体动力学计算得到,对V 型机,p F 应考虑不同的相位和连杆设计(分叉连杆、连接连杆、并列连杆等)分别计算与合成。
《平面连杆传动机构作业设计方案-2023-2024学年高中通用技术地质版2019》

《平面连杆传动机构》作业设计方案一、设计要求1. 设计一个平面连杆传动机构,实现输入轴的旋转运动转换为输出轴的直线往来运动。
2. 输出轴的往来运动幅度为20mm,速度为20mm/s。
3. 设计要思量传动效率、结构稳定性和工作可靠性。
4. 设计要求符合机械设计原理和相关标准规范。
二、设计方案1. 选择机构类型:平面连杆传动机构2. 确定输入轴和输出轴位置:输入轴为旋转轴,输出轴为直线往来轴。
3. 确定连杆长度:根据输出轴的往来运动幅度确定连杆长度。
4. 确定连杆位置:根据输入轴和输出轴位置确定连杆位置,保证连杆在运动过程中不会发生干涉。
5. 确定连杆角度:根据输入轴和输出轴位置确定连杆角度,保证连杆在运动过程中不会发生过大的角度变化。
6. 确定传动比:根据输出轴的速度要求确定传动比,选择合适的齿轮传动或皮带传动。
7. 确定传动方式:根据传动效率要求选择合适的传动方式,保证传动效率高。
8. 确定传动元件:选择合适的齿轮、链条或皮带等传动元件,保证工作可靠性和结构稳定性。
9. 进行动力学分析:进行连杆传动机构的动力学分析,验证设计方案的合理性和可行性。
10. 进行结构优化:根据动力学分析结果进行结构优化,提高传动效率和工作可靠性。
三、设计计算1. 连杆长度计算:根据输出轴的往来运动幅度确定连杆长度。
2. 传动比计算:根据输出轴的速度要求确定传动比。
3. 传动效率计算:根据传动方式确定传动效率。
4. 动力学分析:进行连杆传动机构的动力学分析,验证设计方案的合理性和可行性。
5. 结构优化:根据动力学分析结果进行结构优化,提高传动效率和工作可靠性。
四、设计方案优势1. 结构简单:采用平面连杆传动机构,结构简单,易于制造和维护。
2. 传动效率高:通过传动方式和结构优化,传动效率高。
3. 工作可靠性高:通过结构优化,保证机构工作可靠性。
4. 运动稳定性好:通过连杆角度和位置的确定,保证机构运动稳定性。
五、结论本设计方案基于平面连杆传动机构,实现了输入轴的旋转运动转换为输出轴的直线往来运动,满足了设计要求。
连杆传动关联速度计算公式
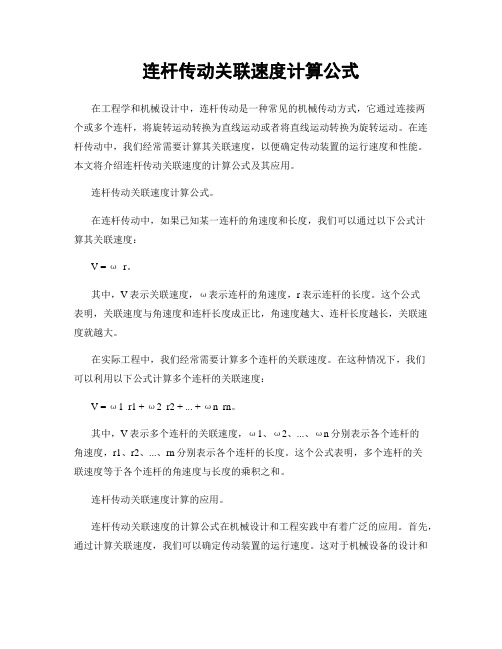
连杆传动关联速度计算公式在工程学和机械设计中,连杆传动是一种常见的机械传动方式,它通过连接两个或多个连杆,将旋转运动转换为直线运动或者将直线运动转换为旋转运动。
在连杆传动中,我们经常需要计算其关联速度,以便确定传动装置的运行速度和性能。
本文将介绍连杆传动关联速度的计算公式及其应用。
连杆传动关联速度计算公式。
在连杆传动中,如果已知某一连杆的角速度和长度,我们可以通过以下公式计算其关联速度:V = ω r。
其中,V表示关联速度,ω表示连杆的角速度,r表示连杆的长度。
这个公式表明,关联速度与角速度和连杆长度成正比,角速度越大、连杆长度越长,关联速度就越大。
在实际工程中,我们经常需要计算多个连杆的关联速度。
在这种情况下,我们可以利用以下公式计算多个连杆的关联速度:V = ω1 r1 + ω2 r2 + ... + ωn rn。
其中,V表示多个连杆的关联速度,ω1、ω2、...、ωn分别表示各个连杆的角速度,r1、r2、...、rn分别表示各个连杆的长度。
这个公式表明,多个连杆的关联速度等于各个连杆的角速度与长度的乘积之和。
连杆传动关联速度计算的应用。
连杆传动关联速度的计算公式在机械设计和工程实践中有着广泛的应用。
首先,通过计算关联速度,我们可以确定传动装置的运行速度。
这对于机械设备的设计和优化非常重要,可以帮助工程师确定传动装置的工作性能和运行参数,从而确保设备的正常运行。
其次,通过计算关联速度,我们可以评估传动系统的稳定性和可靠性。
传动系统的稳定性和可靠性与关联速度密切相关,通过计算关联速度,我们可以评估传动系统的工作状态和性能,从而及时发现和解决潜在的问题,确保传动系统的安全运行。
此外,通过计算关联速度,我们还可以进行传动系统的优化设计。
在传动系统的设计过程中,我们可以通过调整连杆的长度和角速度,来实现传动系统的性能优化,提高传动效率和能量利用率,从而降低能源消耗和成本。
总之,连杆传动关联速度的计算公式在机械设计和工程实践中有着重要的应用。
对心曲柄滑块连杆长度计算

对心曲柄滑块连杆长度计算摘要:1.引言2.曲柄滑块机构的概念与组成3.曲柄长度与滑块行程、偏置距离的关系4.连杆长度的计算方法5.举例说明6.结论正文:1.引言曲柄滑块机构是一种常见的机械传动机构,它由曲柄、滑块和连杆组成。
在工程中,如何合理地设计曲柄滑块机构的尺寸,以达到最佳的传动效果,是一个十分重要的问题。
其中,曲柄长度和连杆长度的计算是机构设计的关键环节。
本文将对心曲柄滑块连杆长度的计算方法进行详细阐述。
2.曲柄滑块机构的概念与组成曲柄滑块机构是由曲柄、滑块和连杆组成的一种传动机构。
其中,曲柄和连杆之间通过轴承连接,滑块则可以在曲柄的带动下沿着连杆做往复运动。
在曲柄滑块机构中,根据滑块运动轨迹的不同,可以分为直线运动和曲线运动两种类型。
对心曲柄滑块机构是其中一种典型的直线运动机构。
3.曲柄长度与滑块行程、偏置距离的关系在曲柄滑块机构中,曲柄长度与滑块的行程和偏置距离有密切的关系。
具体来说,曲柄长度决定了滑块在连杆上的运动范围,即滑块的行程。
同时,曲柄长度还与滑块的偏置距离有关。
偏置距离是指滑块在连杆上的运动轨迹与连杆的轴线之间的距离。
当偏置距离较大时,滑块的运动速度会受到影响,因此,曲柄长度需要根据实际需求进行合理设计。
4.连杆长度的计算方法在曲柄滑块机构中,连杆长度的计算是一个重要的环节。
通常情况下,连杆长度的计算需要考虑以下因素:滑块的行程、曲柄的长度和偏置距离。
根据这些因素,可以采用以下公式来计算连杆长度:连杆长度= 滑块行程^2 / (2 * 曲柄长度* cos(偏置距离角))其中,滑块行程、曲柄长度和偏置距离角需要根据实际需求进行测量或设定。
5.举例说明假设一个对心曲柄滑块机构的滑块行程为300mm,曲柄长度为200mm,偏置距离为45°,需要求解连杆长度。
根据上述公式,代入已知参数,可得:连杆长度= 300^2 / (2 * 200 * cos(45°)) ≈ 231.97mm因此,在这个对心曲柄滑块机构中,连杆长度约为231.97mm。
断桥窗平开窗连杆计算公式
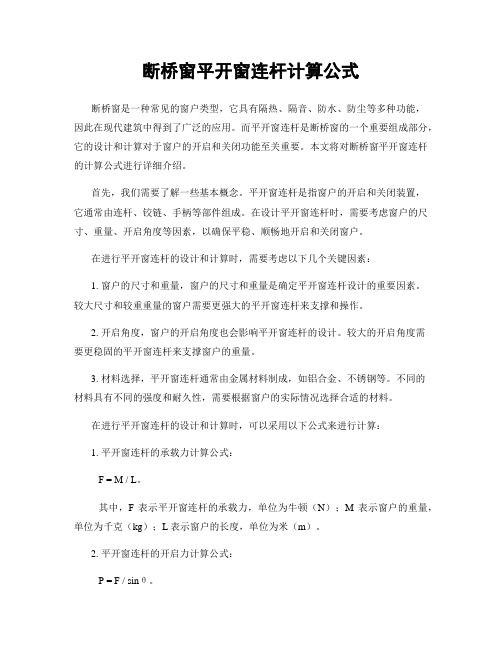
断桥窗平开窗连杆计算公式断桥窗是一种常见的窗户类型,它具有隔热、隔音、防水、防尘等多种功能,因此在现代建筑中得到了广泛的应用。
而平开窗连杆是断桥窗的一个重要组成部分,它的设计和计算对于窗户的开启和关闭功能至关重要。
本文将对断桥窗平开窗连杆的计算公式进行详细介绍。
首先,我们需要了解一些基本概念。
平开窗连杆是指窗户的开启和关闭装置,它通常由连杆、铰链、手柄等部件组成。
在设计平开窗连杆时,需要考虑窗户的尺寸、重量、开启角度等因素,以确保平稳、顺畅地开启和关闭窗户。
在进行平开窗连杆的设计和计算时,需要考虑以下几个关键因素:1. 窗户的尺寸和重量,窗户的尺寸和重量是确定平开窗连杆设计的重要因素。
较大尺寸和较重重量的窗户需要更强大的平开窗连杆来支撑和操作。
2. 开启角度,窗户的开启角度也会影响平开窗连杆的设计。
较大的开启角度需要更稳固的平开窗连杆来支撑窗户的重量。
3. 材料选择,平开窗连杆通常由金属材料制成,如铝合金、不锈钢等。
不同的材料具有不同的强度和耐久性,需要根据窗户的实际情况选择合适的材料。
在进行平开窗连杆的设计和计算时,可以采用以下公式来进行计算:1. 平开窗连杆的承载力计算公式:F = M / L。
其中,F表示平开窗连杆的承载力,单位为牛顿(N);M表示窗户的重量,单位为千克(kg);L表示窗户的长度,单位为米(m)。
2. 平开窗连杆的开启力计算公式:P = F / sinθ。
其中,P表示平开窗连杆的开启力,单位为牛顿(N);F表示平开窗连杆的承载力,单位为牛顿(N);θ表示窗户的开启角度。
通过以上公式的计算,可以得到平开窗连杆的承载力和开启力,从而确定合适的平开窗连杆设计方案。
在实际应用中,还需要考虑平开窗连杆的安装方式、固定方式、防盗性能等因素,以确保窗户的安全和稳定性。
总之,平开窗连杆的设计和计算是窗户设计中的重要环节,它直接影响窗户的开启和关闭功能。
通过合理的设计和计算,可以确保窗户的平稳、顺畅地开启和关闭,提高窗户的使用效果和安全性。
曲柄连杆的计算
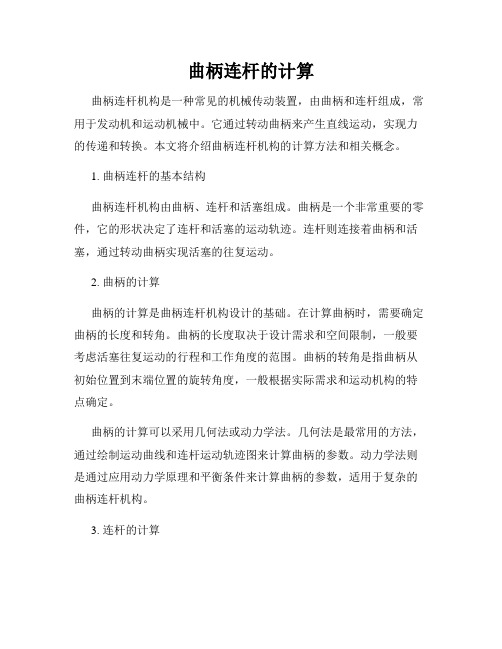
曲柄连杆的计算曲柄连杆机构是一种常见的机械传动装置,由曲柄和连杆组成,常用于发动机和运动机械中。
它通过转动曲柄来产生直线运动,实现力的传递和转换。
本文将介绍曲柄连杆机构的计算方法和相关概念。
1. 曲柄连杆的基本结构曲柄连杆机构由曲柄、连杆和活塞组成。
曲柄是一个非常重要的零件,它的形状决定了连杆和活塞的运动轨迹。
连杆则连接着曲柄和活塞,通过转动曲柄实现活塞的往复运动。
2. 曲柄的计算曲柄的计算是曲柄连杆机构设计的基础。
在计算曲柄时,需要确定曲柄的长度和转角。
曲柄的长度取决于设计需求和空间限制,一般要考虑活塞往复运动的行程和工作角度的范围。
曲柄的转角是指曲柄从初始位置到末端位置的旋转角度,一般根据实际需求和运动机构的特点确定。
曲柄的计算可以采用几何法或动力学法。
几何法是最常用的方法,通过绘制运动曲线和连杆运动轨迹图来计算曲柄的参数。
动力学法则是通过应用动力学原理和平衡条件来计算曲柄的参数,适用于复杂的曲柄连杆机构。
3. 连杆的计算连杆是曲柄连杆机构中起关键作用的零件,它将曲柄的旋转运动转换为活塞的往复运动。
连杆的计算需要确定连杆长度和连杆角度。
连杆长度一般根据工作行程和曲柄长度来确定。
连杆角度是指连杆与曲柄和活塞的夹角,一般根据设计需求和活塞运动的要求来确定。
连杆的计算可以采用解析法或图解法。
解析法主要是通过应用三角函数和几何关系求解连杆的参数,适用于简单的连杆机构。
图解法则是通过绘制连杆运动轨迹图和使用平行四边形法则来计算连杆的参数,适用于复杂的连杆机构。
4. 活塞的计算活塞是曲柄连杆机构中的另一个重要零件,它接受曲柄的动力传递,实现往复运动。
活塞的计算主要涉及活塞直径和活塞往复行程的确定。
活塞直径一般根据发动机功率和气缸内径来选择。
活塞往复行程一般根据发动机排量和气缸数来确定。
活塞的计算可以通过运动学方法和动力学方法进行。
运动学方法主要是通过几何关系和运动规律来计算活塞的参数,适用于简单的活塞机构。
02平面连杆机构的设计计算
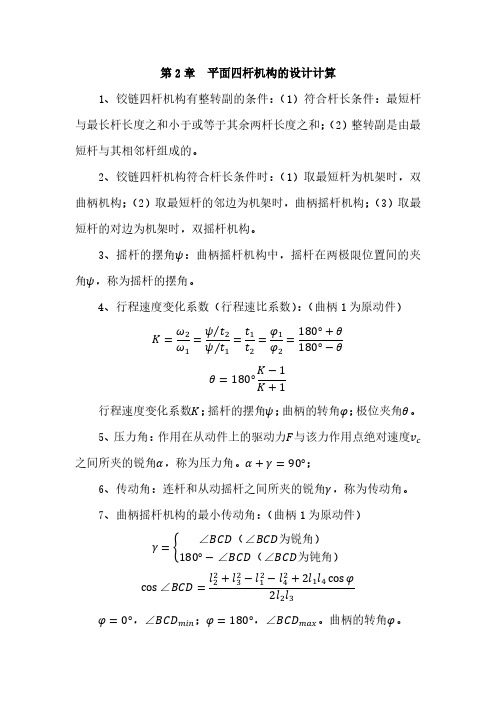
180°+
180°−
= 3.17 ;
摇杆摆角: = ∠ ′ − ∠ " = 90.07° 。
例 2-3 设计一曲柄摇杆机构。已知摇杆长度3 = 100,摆
角 = 30°,摇杆的行程速度变化系数 = 1.2。
(1)用图解法确定其
余三杆的尺寸;
(2)用式(2-6)和式(2-7)确定机构最小传动角(若
第2章
平面四杆机构的设计计算
1、铰链四杆机构有整转副的条件:(1)符合杆长条件:最短杆
与最长杆长度之和小于或等于其余两杆长度之和;
(2)整转副是由最
短杆与其相邻杆组成的。
2、铰链四杆机构符合杆长条件时:(1)取最短杆为机架时,双
曲柄机构;
(2)取最短杆的邻边为机架时,曲柄摇杆机构;
(3)取最
短杆的对边为机架时,双摇杆机构。
位置如题 2-13 图所示,
1 = 45°,
1 = 52°10′;2 = 90°,
2 = 82°10′;
3 = 135°,2 = 112°10′,机架长度 = 50 ,试用解析法求其
余三杆长度。
2-13 解:已知:
1 + 2 = 50 + 3
(b) 最短杆与最长杆长度之和= 45 + 120 = 165
其余两杆长度之和= 100 + 70 = 170
①满足杆长条件:最短杆与最长杆长度之和≤其余两杆长度之和;
②最短杆的邻边为机架;
所以此铰链四杆机构为曲柄摇杆机构。
(c) 最短杆与最长杆长度之和= 60 + 100 = 160
其余两杆长度之和= 70 + 62 = 132
- 1、下载文档前请自行甄别文档内容的完整性,平台不提供额外的编辑、内容补充、找答案等附加服务。
- 2、"仅部分预览"的文档,不可在线预览部分如存在完整性等问题,可反馈申请退款(可完整预览的文档不适用该条件!)。
- 3、如文档侵犯您的权益,请联系客服反馈,我们会尽快为您处理(人工客服工作时间:9:00-18:30)。
第四章典型零部件(连杆)的设计连杆是发动机最重要的零件之一,近代中小型高速柴油机,为使发动机结构紧凑,最合适的连杆长度应该是,在保证连杆及相关机件运动时不与其他机件相碰的情况下,选取小的连杆长度,而大缸径的中低速柴油机,为减少侧压力,可适当加长连杆。
连杆的结构并不复杂,且连杆大头、小头尺寸主要取决于曲轴及活塞组的设计。
在连杆的设计中,主要考虑的是连杆中心距以及大、小头的结构形式。
连杆的运动情况和受力状态都比较复杂。
在内燃机运转过程中,连杆小头中心与活塞一起作往复运动,承受活塞组产生的往复惯性力;大头中心与曲轴的连杆轴颈一起作往复运动,承受活塞连杆组往复惯性力和不包括连杆大头盖在内的连杆组旋转质量惯性力;杆身作复合平面运动,承受气体压力和往复惯性力所产生的拉伸.压缩交变应力,以及压缩载荷和本身摆动惯性力矩所产生的附加弯曲应力。
为了顺应内燃机高速化趋势,在发展连杆新材料、新工艺和新结构方面都必须既有利于提高刚度和疲劳强度,有能减轻质量,缩小尺寸。
对连杆的要求:1、结构简单,尺寸紧凑,可靠耐用;2、在保证具有足够强度和刚度的前提下,尽可能的减轻重量,以降低惯性力;3、尽量缩短长度,以降低发动机的总体尺寸和总重量;4、大小头轴承工作可靠,耐磨性好;5、连杆螺栓疲劳强度高,连接可靠。
但由于本设计是改型设计,故良好的继承性也是一个考虑的方面。
4.1连杆材料结合发动机工作特性,发动机连杆材料应当满足发动机正常工作所需要的要求。
应具有较高的疲劳强度和冲击韧性,一般选用中碳钢或中碳合金钢,如45、40Cr等,本设计中发动机为中小功率发动机,故选用一般的45钢材料基本可以满足使用要求。
4.2连杆主要尺寸 1、连杆长度l曲柄连杆比λ一般均大于0.3,这样可以使柴油机的机体高度降低,净质量减少,而且连杆长度减小后,其材料也相应减少,从而成本降低。
但是,过小的曲柄连杆比会引起活塞侧压力增加,从而导致柴油机摩擦损失的增加,加速活塞、活塞环、气缸套的磨损,影响可靠性。
《高速柴油机概念设计及实践》中指出:当曲柄连杆比31.0=λ左右时,对柴油机寿命及可靠性影响不大。
参照原机及总体布置,选择曲柄连杆比为:29.0260/65/,260≈===l r mm l λ。
2、连杆的结构尺寸小头主要尺寸为连杆衬套内径d 和小头宽度1b 。
《柴油机设计手册》中介绍的各个尺寸范围为:由 29.0260/65/≈==l r λ 查 《柴油机设计手册》36.0=Dd40=d 毫米 0625.0=dδ5.2=δ 毫米 小头内径4521=+=δd d 毫米36.112=d d 小头外径612=d 毫米 736.01=DD大头内径811=D 毫米 1.11=db 小头厚度 取 401=b 毫米 65.012=D b 大头厚度 取 532=b 毫米 113.1~2.1D l = 取981=l 毫米12.0=Dd M螺栓直径14=M d 毫米 327.0=D H 78.0=H B 17.0=Ht取36=H 毫米 28=B 毫米 6=t 毫米校核小头轴承的比压:bar db p q x5336251074.493104010401011010052.80⨯=⨯⨯⨯⨯⨯⨯⨯==--π 《柴油机设计手册》中给出,q 许用值为630bar,可见是在安全范围之内的。
注:式中 24,D p P P zz z π=---最高燃气作用力;;;衬套支承长度衬套内径------b d3、连杆杆身连杆杆身采用典型的工字形截面。
尺寸如图4-1所示。
4、连杆大头定位方式连杆大头定位方式为舌槽定位。
这种定位方式定位可靠,贴面紧密,抗剪切能力强尺寸紧凑。
但要注意舌槽部位要减小应力集中,以防疲劳损坏。
5、连杆大头、小头的结构形式连杆大头的剖面形式:从上面选取的参数70.0~65.069.0>=Dd,所以采用斜切口。
图4-2 衬套承压面段面图图4-1连杆杆身断面示意图连杆盖的定位方式:斜切口连杆盖一般采用止口定位、锯齿定位。
在本设计中采用止口定位 连杆小头的结构形式:由于活塞销的大小一般由活塞设计所决定,所以在连杆的设计中,应尽可能加大连杆小头衬套的承压面积以降低比压,结构设计如图4-2所示。
4.3连杆螺栓连杆螺栓将连杆盖和连杆大头连在一起,它在工作中承受很大的冲击力,如果折断或松脱,将造成严重事故。
因此,连杆螺栓为M14采用标准细牙螺纹,都采用优质合金钢40Cr 制造,并精加工和热处理特制而成。
安装连杆盖拧紧连杆螺栓螺母时,要用扭力板手分2~3次交替均匀地拧紧到规定的扭矩,拧紧后为了防止连杆螺栓松动,还应可靠的锁紧。
连杆螺栓损坏后绝不能用其它螺栓来代替。
连杆螺栓必须用中碳合金钢制造,经调质以保证高强度。
4.4连杆轴瓦为了减小摩擦阻力和曲轴连杆轴颈的磨损,连杆大头孔内装有瓦片式滑动轴承,简称连杆轴瓦。
轴瓦分上、下两个半片。
连杆轴瓦上制有定位凸键,供安装时嵌入连杆大头和连杆盖的定位槽中,以防轴瓦前后移动或转动,有的轴瓦上还制有油孔,安装时应与连杆上相应的油孔对齐。
目前多采用薄壁钢背轴瓦,在其内表面浇铸有耐磨合金层。
耐磨合金层具有质软,容易保持油膜,磨合性好,摩擦阻力小,不易磨损等特点。
连杆轴瓦的背面有很高的光洁度。
半个轴瓦在自由状态下不是半圆形,当它们装入连杆大头孔内时,又有过盈,故能均匀地紧贴在大头孔壁上,具有很好的承受载荷和导热的能力,并可以提高工作可靠性和延长使用寿命。
轴瓦厚度和宽度根据《柴油机设计手册》上提供的范围分别别取2.5mm 和38mm 。
4.5连杆小头的强度计算 4.5.1连杆小头承受的作用力1. 连杆小头在进气和排气冲程中承受活塞组往复惯性力jn P 的拉伸,在上止点附近之值为最大。
jn P =)1(2λω+-r m X =-2.05×0.065×162.12×(1+21065)=-4585.3 N式中:X m 为活塞组件的质量,其数值为2.05千克。
r 为曲柄半径,其值为65 毫米。
ω为曲柄半径与连杆长之比值31.0==Lrλ 2. 连杆小头在膨胀行程开始点所承受的压缩力 3.705403.458510110410)1052.80(625=-⨯⨯⨯⨯-=+=-πjn F ck P P P N式中:F P 为最高燃气作用力 3. 由于温度过盈和压配衬套而产生的力 (1) 温度过盈量小头衬套有青铜,也可用粉末冶金代之。
现以青铜衬套进行计算。
()()0492.015041101108.155=⨯⨯⨯-⨯=-=∆--dt T B αα 毫米式中: B α为青铜衬套材料的热膨胀系数B α=1.8×105-α为钢的小头材料热膨胀系数 5101-⨯=α t 为连杆小头的温升 推荐 C t ︒=200~100 取 C t ︒=150 d 为小头衬套的外径 d=41 毫米(2)衬套与小头配合面上由总过盈量所决定的单位压力PaB TMP E d d d d E d D d D d p 5.191017.13.05.38415.38411024.23.041604160410492.0068.05222252222212212222222=⎥⎥⎥⎥⎦⎤⎢⎢⎢⎢⎣⎡⨯-+++⨯+-+⨯+=⎥⎥⎥⎥⎥⎦⎤⎢⎢⎢⎢⎢⎣⎡--+++-+∆+∆=μμ 式中: D 2 小头外径 D 2=60 毫米D 小头内径 d=41 毫米 1d 衬套内径 1d =38.5 毫米 μ 泊桑系数 3.0=μE 连杆材料的抗拉弹性模数 E =2.24×105MP aB E 青铜衬套的抗拉弹性模数 B E =1.17×105MP a∆ 衬套装配过盈为 068.0~016.0毫米,可取 068.0=∆毫米。
4.5.2由于装配过盈与温度过盈所产生的应力 1、外表面的应力15.3441604125.1922222222=-⨯⨯=-=dD d p a σ MP a 2、内表面的应力65.53416041605.192222222222=-+⨯=-+=dD d D p i σ MP a 许用值[]a σ和[]i σ在150~100 MP a 故属安全。
4.5.3由活塞的惯性力在连杆小头中引起的拉应力 1、当活塞在上止点时27.24025.2523.458522=⨯⨯===Ar P FP cp jn jn p σ MP a式中:小头平均半径25.254416042=+=+=d D r cp 毫米 小头宽度 A=40 毫米[]58~29=p σ MP a 故安全 2、按小曲率曲杆公式计算弯矩和法向力 计算可作下述假定:① 曲杆固定于小头和杆身的衔接处。
即在连杆小头外圆和过度圆半径R 相切的位置; ② 连杆小头下部支承在刚性很大的杆身上,因而不变形;③ 小头沿连杆的纵向对称线切开,用弯矩0M 和反向力N 代替的小头右半部的作用。
小头Ⅲ—Ⅲ剖面弯矩M 和法向力N (图4-3)。
mN r P r N M M cp jn cp ⋅=⨯-⨯⨯⨯-⨯-⨯⨯+=---+=-︒︒-︒359.410)119cos 119(sin 25.253.45855.010)119cos 1(25.253.2186108.1)cos (sin 5.0)cos 1(3300φφφ式中: 0N 、0M 为当︒=0φ断面上的轴力和弯矩。
0N 和0M 值有下列经验公式求得:3.2186)1190008.0572.0(3.4585)0008.0572.0(0=⨯-⨯=-=οφjn P N NmN r P M cp jn ⋅=⨯-⨯⨯⨯=-=-︒108.110)0297.011900033.0(25.253.4585)0297.000033.0(30φ式中:︒-︒-︒=+++=+++=11975307517cos 9022cos 90121R D RHφ25.25=cp r 毫米 41=d 毫米 602=D 毫米图4-3 连杆小头剖面图NP N N jn 6.2057)119cos 119(sin 3.45855.0119cos 3.2186)cos (sin 5.0cos 0=-⨯⨯+⨯=-+=︒︒︒φφφ(3)外侧纤维应力acp cp aj MP AhKN h r h h r M55.11105.9401]6.2057936.0)5.925.252(5.95.925.25610359.42[1])2(62[63=⨯⨯⨯⨯++⨯+⨯⨯⨯⨯=+++=σ 式中: h 为小头计算壁厚 5.92416022=-=-=d D h 毫米 系数936.0405.21017.140)4060(1024.240)4160(1024.255522=⨯⨯⨯+⨯-⨯⨯⨯-⨯⨯=⋅+⋅⋅=B B F E F E F E K (4)内侧纤维应力acp cp ij MP AhKN h r h h r M296.3105.9401]6.2057936.0)5.925.252(5.95.925.25610359.42[1])2(62[63-=⨯⨯⨯⨯+-⨯-⨯⨯⨯⨯-=+---=σ4.5.4由压缩力引起的应力计算假定载荷在连杆小头下部成正弦分布 1、Ⅲ-Ⅲ剖面上的弯矩和法向力)cos sin 2sin ()cos 1(00ππφφφφΦ----+=cp ck cp r P r N M M 式中0M 和0N 由曲线查得0012.00-=cpck r P M m N M ⋅-=⨯⨯⨯-=-14.21025.253.705400012.0300035.00=ckP N 9.2463.705400035.00=⨯=N N 弯矩)cos sin 2sin ()cos 1(00πφπφφφφ----+=cp ck cp r P r N M MmN ⋅-=-+-=--⨯⨯-⨯-⨯+-=︒︒︒--︒59.1971.2626.914.2)119cos 119sin 07.22119sin (1025.253.7054010)119cos 1(25.259.24614.233ππ法向力NN P N cK 1.1058)119cos 119sin 07.22119sin (3.70540cos )cos sin 2sin (0=--⨯=+--=︒︒︒ππφπφπφφφ 2、外侧纤维应力acp cp ac MP AhKN h r h h r M52.26105.9401]1.1058936.0)5.925.252(5.95.925.2561059.192[1])2(62[63-=⨯⨯⨯⨯++⨯+⨯⨯⨯⨯-=+++-=σ3、内侧纤维应力AhKN h r h h r Mcp cp ic 1])2(62[+--=σ aMP 195.40105.9401]1.1058936.0)5.925.252(5.95.925.2561059.192[63=⨯⨯⨯⨯+-⨯-⨯⨯⨯⨯=4.5.5连杆小头的安全系数)2(212a ac aj acaj n σσσψσσσσσ+++-=-连杆小头应力按不对称循环变化,在小头和杆身衔接处(即固定角R 处)的外侧纤维上安全系数最小。