防腐蚀涂层的测试
涂层附着力测试规范标准

划格法测试涂层附着力的操作方法及评价标准1.先在试片涂层上切割6道或11道相互平行的、间距相等�可分为1m m或2m m�的切痕�然后再垂直切割与前者切割道数及间距相同的切痕。
当涂层厚度小于或等于60μm时�选用划格刀片间距1m m的刀具�当涂层厚度大于60μm时�选用划格刀片间距2m m的刀具2.采用手工切割时�用力要均匀�速度要平稳无颤抖�以便使刃口在切割中正好能穿透涂层而触及基底。
用力过大或不均可能影响测试结果。
3.切割后�在试板上将出现25个或100个方格�用软毛刷沿方格的两对角线方向轻轻刷掉切屑�然后检查并评价涂层附着涂层附着力划格法测试的评定标准�G B/T9286-88�分级说明脱落表现0切割边缘完全平滑�无一格脱落1在切口交叉处涂层有少许薄片分离�但划格区受影响明显不大于5%2切口边缘或交叉处涂层明显脱落大于5%�但受影响明显不大于15%3涂层沿切割边缘�部分或全部以大碎片脱落�或在格子不同部位上�部分或全部脱落�明显大于15%�但受影响明显不大于35%4涂层沿切割边缘�大碎片剥落�或一些方格部分或全部脱落�明显大于35%�但受影响明显不大于65%5大于4级的严重剥落涂层附着力的现场检测摘要�介绍了防腐蚀涂料涂层附着力的机理�并对附着力检测的标准划格法、划X法以及拉开法的测试方法和程序�作了详细说明。
关键词�涂层、附着力、划格法、拉开法1�涂层附着力涂装工程中�对于防腐蚀涂料的涂层附着力检测是涂层保护性能相当重要的指标�越来越被业主和监理所重视。
除了在试验室内的检测外�防腐蚀涂料的选用过程中�对涂料产品进行的样板附着力测试�以及施工过程中现场附着力的检测�也越来越普遍。
有机涂层与金属基底间的附着力�与涂层对金属的保护有着密切的关系�它主要是由附着力与有机涂层下金属的腐蚀过程所决定的。
有机涂层下金属的腐蚀主要是由相界面的电化学腐蚀引起的�附着力的好坏对电化学腐蚀有明显的影响。
良好的附着力能有效地阻挡外界电解质溶液对基体的渗透�推迟界面腐蚀电池的形成�牢固的界面附着力可以极大地阻止腐蚀产物——金属阳离子经相间侧面向阴极区域的扩散�这些阳离子扩散是为了平衡阴极反应所生成的带负电荷的氢氧根离子�这虽然是一个相当缓慢的过程�但是一旦附着力降低�阳离子从相间侧面向阴极扩散的扩散则容易得多。
防腐蚀涂层保护层厚度及间距检测实施细则

防腐蚀涂层保护层厚度及间距检测实施细则1.引言本文档旨在规范防腐蚀涂层保护层厚度及间距的检测实施细则。
防腐蚀涂层保护层是用于保护金属结构免受环境侵蚀的重要措施。
通过合适的层厚度及间距检测,可以确保涂层的质量和性能符合要求,从而提高金属结构的耐腐蚀能力。
2.涂层保护层厚度检测要求为保证涂层的防腐蚀性能,必须对涂层的厚度进行定期检测。
具体要求如下:使用合适的测量设备和技术,准确测量涂层的厚度。
涂层厚度应符合设计规范或合同要求,并保证厚度的均匀性。
检测应覆盖涂层表面的不同区域,并确保取样的代表性。
检测结果应记录并保存,以备将来参考。
3.涂层保护层间距检测要求涂层保护层之间的间距也是确保防腐蚀效果的重要因素。
以下是涂层保护层间距的检测要求:使用合适的测量方法和工具,测量涂层保护层之间的间距。
间距应符合设计规范或合同要求,并保证其均匀性。
检测应涵盖涂层表面的多个位置,并确保取样的代表性。
间距检测结果应记录并保存,并与设计规范或合同要求进行比对。
4.检测频率为保证防腐蚀涂层保护层的质量和性能,对于已施工的涂层,应定期进行厚度和间距的检测。
具体检测频率应根据涂层类型、使用环境和设计要求等因素进行确定。
在检测频率方面,以下原则应被考虑:初次检测:在涂层施工完毕后的一段时间内进行首次检测。
定期检测:根据设计规范或合同要求,制定定期检测计划,并在规定的时间间隔内进行检测。
重点检测:对于特殊环境下的涂层,或者涂层质量有疑问的情况下,应加大检测频率。
5.检测记录与控制为确保涂层保护层的厚度和间距检测工作顺利进行,并实现有效的质量控制,以下措施应被采取:检测人员应具备相关专业知识和技能,并经过培训合格。
检测记录应包括检测日期、位置、涂层厚度或间距数值,并由相关人员签字确认。
检测结果应进行及时反馈和汇总分析,以便及早发现问题并采取纠正措施。
如发现涂层厚度或间距不符合要求,应立即采取措施进行修复或重新施工。
6.结论通过本文档所述的防腐蚀涂层保护层厚度及间距的检测实施细则,可以确保涂层的质量和性能符合要求,提高金属结构的耐腐蚀能力。
防腐蚀质量检验

三、涂层附着力检验
检验方法:划格法 拉开法 (注意:由于附着力检验为破坏性试验,宜做抽样或 是带样试验)
1)划格法
当涂膜厚度>250μm时,应用划叉法检验,在涂膜上划 两条夹角为60°的切割线并划透至基底,用透明胶带粘牢划 口部分,快速撕起,涂层应无剥落。
当涂膜厚度≯250μm时,应按照GB/T9286中的规定用划
一致,如有变更应经设计方书面认可,并加以记 录。
牺牲阳极的布置和安装应依据设计文件并满足 一下要求: 1. 牺牲阳极的工作表面不应粘有油漆和油污。 2. 牺牲阳极的布置和安装方式应不影响金属结构 的正常运行,并能满足金属结构各处的保护电 位均能符合相关要求. 3. 牺牲阳极与金属的链接位置应除去涂层并露出 金属基底,其面积宜为1d㎡左右。 4. 牺牲阳极应通过钢芯与金属结构短路连接,宜 优先采用焊接方法,也可以采用电缆连接或机 械连接。
第二节 涂料保护质量检验(掌握)
防腐蚀涂层系统有底漆、中间漆和面漆构成。 底漆:具有良好的附着能力和防腐蚀性能 中间漆:具有屏蔽性能且与底、面漆结合良好; 面漆: 具有耐候性或耐水性。
注意事项: 1、进行涂装施工时,环境空气相对湿度低于85%或基体金属表面温度 不低于大气露点以上3度。 2、涂装前应进行表面预处理,预处理与涂装之间的时间尽可能短,在潮 湿或工业大气等环境下,应在2h内涂装完毕,晴天或湿度不大的条件下 不超过8h。 3、涂装前,对不涂装或是暂时不涂装的部位进行遮蔽。 4、涂装过程中,应进行湿膜外观检查,不应有漏涂、流挂等缺陷,宜用 湿膜测厚仪估测湿膜厚度 5、涂层系统各层之间的覆涂时间应按涂料厂的规定执行,若超过 时间,则需要打毛之后再涂装,保证涂层之间的结合力。
能,切割后,采用双方协商认可的交代,借助于一 个辊子或用手指施以5N的荷载将胶带压紧在被切 割的涂层上,然后垂直于涂层方向快速将胶带拉开 。如不能用此方,则双方协商后确定检测方法。
3)聚氨酯三防漆测试标准
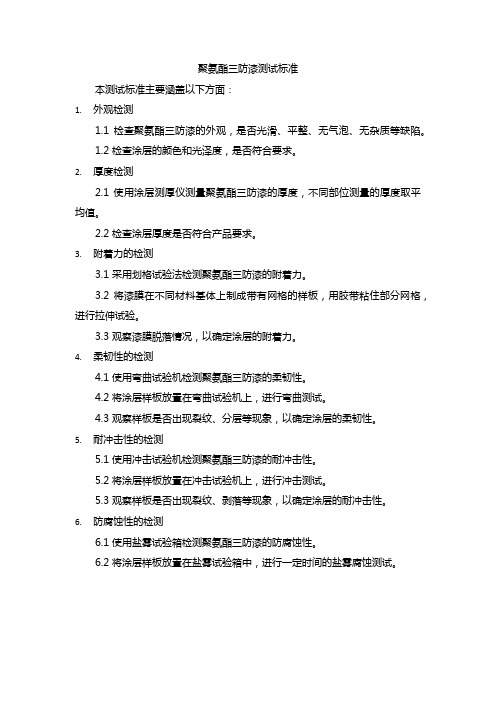
聚氨酯三防漆测试标准
本测试标准主要涵盖以下方面:
1.外观检测
1.1 检查聚氨酯三防漆的外观,是否光滑、平整、无气泡、无杂质等缺陷。
1.2 检查涂层的颜色和光泽度,是否符合要求。
2.厚度检测
2.1 使用涂层测厚仪测量聚氨酯三防漆的厚度,不同部位测量的厚度取平均值。
2.2 检查涂层厚度是否符合产品要求。
3.附着力的检测
3.1 采用划格试验法检测聚氨酯三防漆的附着力。
3.2 将漆膜在不同材料基体上制成带有网格的样板,用胶带粘住部分网格,进行拉伸试验。
3.3 观察漆膜脱落情况,以确定涂层的附着力。
4.柔韧性的检测
4.1 使用弯曲试验机检测聚氨酯三防漆的柔韧性。
4.2 将涂层样板放置在弯曲试验机上,进行弯曲测试。
4.3 观察样板是否出现裂纹、分层等现象,以确定涂层的柔韧性。
5.耐冲击性的检测
5.1 使用冲击试验机检测聚氨酯三防漆的耐冲击性。
5.2 将涂层样板放置在冲击试验机上,进行冲击测试。
5.3 观察样板是否出现裂纹、剥落等现象,以确定涂层的耐冲击性。
6.防腐蚀性的检测
6.1 使用盐雾试验箱检测聚氨酯三防漆的防腐蚀性。
6.2 将涂层样板放置在盐雾试验箱中,进行一定时间的盐雾腐蚀测试。
锌镍涂层盐雾试验要求

锌镍涂层盐雾试验要求
【原创版】
目录
1.锌镍涂层的介绍
2.盐雾试验的定义和目的
3.锌镍涂层盐雾试验的具体要求
4.锌镍涂层盐雾试验的注意事项
5.锌镍涂层盐雾试验的结论和影响
正文
锌镍涂层是一种防腐蚀涂层,广泛应用于各种金属制品的表面处理,以保护金属制品不被腐蚀。
盐雾试验是一种测试材料抗腐蚀性能的试验,通过模拟海洋、工业大气和自然气候等环境,测试材料在盐雾环境下的耐蚀性。
锌镍涂层盐雾试验是测试锌镍涂层在盐雾环境下的耐蚀性能,其目的是为了确保锌镍涂层在实际应用中能够有效地保护金属制品,防止腐蚀。
具体要求如下:
首先,试验样品需要经过锌镍涂层的处理,涂层的厚度需要均匀,涂层的附着力需要达到一定的标准。
其次,试验环境需要模拟盐雾环境,盐雾的浓度、温度和湿度等参数需要符合标准。
最后,试验时间需要足够长,以确保能够准确地评估锌镍涂层的耐蚀性能。
在试验过程中,需要注意以下几点:
一是试验样品的处理,需要确保样品的表面清洁、无油脂,以保证涂
层的附着力。
二是试验环境的控制,需要确保盐雾的浓度、温度和湿度等参数符合标准,以保证试验的准确性。
三是试验时间的控制,需要确保试验时间足够长,以确保能够准确地评估锌镍涂层的耐蚀性能。
锌镍涂层盐雾试验的结论和影响主要取决于试验结果,如果试验结果显示锌镍涂层在盐雾环境下的耐蚀性能良好,那么可以得出锌镍涂层具有较好的防腐蚀性能的结论。
防腐涂层相关质量检测
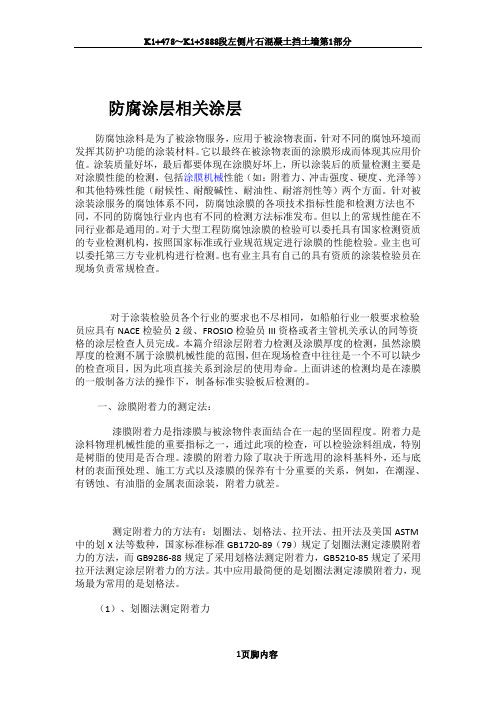
防腐涂层相关涂层防腐蚀涂料是为了被涂物服务,应用于被涂物表面,针对不同的腐蚀环境而发挥其防护功能的涂装材料。
它以最终在被涂物表面的涂膜形成而体现其应用价值。
涂装质量好坏,最后都要体现在涂膜好坏上,所以涂装后的质量检测主要是对涂膜性能的检测,包括涂膜机械性能(如:附着力、冲击强度、硬度、光泽等)和其他特殊性能(耐候性、耐酸碱性、耐油性、耐溶剂性等)两个方面。
针对被涂装涂服务的腐蚀体系不同,防腐蚀涂膜的各项技术指标性能和检测方法也不同,不同的防腐蚀行业内也有不同的检测方法标准发布。
但以上的常规性能在不同行业都是通用的。
对于大型工程防腐蚀涂膜的检验可以委托具有国家检测资质的专业检测机构,按照国家标准或行业规范规定进行涂膜的性能检验。
业主也可以委托第三方专业机构进行检测。
也有业主具有自己的具有资质的涂装检验员在现场负责常规检查。
对于涂装检验员各个行业的要求也不尽相同,如船舶行业一般要求检验员应具有NACE检验员2级、FROSIO检验员III资格或者主管机关承认的同等资格的涂层检查人员完成。
本篇介绍涂层附着力检测及涂膜厚度的检测,虽然涂膜厚度的检测不属于涂膜机械性能的范围,但在现场检查中往往是一个不可以缺少的检查项目,因为此项直接关系到涂层的使用寿命。
上面讲述的检测均是在漆膜的一般制备方法的操作下,制备标准实验板后检测的。
一、涂膜附着力的测定法:漆膜附着力是指漆膜与被涂物件表面结合在一起的坚固程度。
附着力是涂料物理机械性能的重要指标之一,通过此项的检查,可以检验涂料组成,特别是树脂的使用是否合理。
漆膜的附着力除了取决于所选用的涂料基料外,还与底材的表面预处理、施工方式以及漆膜的保养有十分重要的关系,例如,在潮湿、有锈蚀、有油脂的金属表面涂装,附着力就差。
测定附着力的方法有:划圈法、划格法、拉开法、扭开法及美国ASTM 中的划X法等数种,国家标准标准GB1720-89(79)规定了划圈法测定漆膜附着力的方法,而GB9286-88规定了采用划格法测定附着力,GB5210-85规定了采用拉开法测定涂层附着力的方法。
油漆涂层附着力检测方法
油漆涂层附着力检测方法油漆涂层附着力检测方法————百格测试百格测试百格测试 含义及测试方法含义及测试方法含义:一般而言是测试对象在经过涂装之后测试其附着度的工具,按照日本工业标准(JIS),分为1~5级,级数越高,要求越严格,当客户规范当中要求是第5级时,表示完全不能有脱落。
参考标准:《GBT9286-1998 色漆和清漆 漆膜的划痕实验》测试方法:用百格刀在测试样本表面划10×10个(100个)1mm×1mm 小网格, 每一条划线应深及油漆的底层;用毛刷将测试区域的碎片刷干净;用3M600号胶纸或等同效力的胶纸牢牢粘住被测试小网格,并用橡皮擦用力擦拭胶带,以加大胶带与被测区域的接触面积及力度;用手抓住胶带一端,在垂直方向(90°)迅速扯下胶纸,同一位置进行2次相同试验。
实验条件及标准实验条件及标准规定利用3M600或610的胶带黏贴于百格中,快速拉起3M 胶带,其面漆或电度层被胶带黏起的数量依照百格的百分比:ISO 等级:0 =ASTM 等级:5B切口的边缘完全光滑,格子边缘没有任何剥落。
ISO 等级:1 =ASTM 等级:4B在切口的相交处有小片剥落,划格区内实际破损≤5% 。
ISO 等级:2 =ASTM 等级:3B切口的边缘和/或相交处有被剥落,其面积大于5%~15% 。
ISO 等级:3 =ASTM 等级:2B沿切口边缘有部分剥落或整大片剥落,或部分格子被整片剥落。
剥落的面积超过15%~35% 。
ISO 等级:4 =ASTM 等级:1B切口边缘大片剥落/或者一些方格部分或全部剥落,其面积大于划格区的35%~65% 。
ISO 等级:5 =ASTM 等级:0B在划线的边缘及交叉点处有成片的油漆脱落,且脱落总面积大于65%。
依照客户要求B 数测试是否通过百格实验,一般手机业界客户要求在4B 以上。
正式的话是使用百格刀,横向与纵向各划1刀及型成100各细小方格.如无百格刀利用美工刀也可以. 利用3M600或610的胶带黏贴于百格中,快速拉起3M 胶带,测试脱落数量。
涂层附着力测试规范标准
划格法测试涂层附着力的操作方法及评价标准1.先在试片涂层上切割6道或11道相互平行的、间距相等�可分为1m m或2m m�的切痕�然后再垂直切割与前者切割道数及间距相同的切痕。
当涂层厚度小于或等于60μm时�选用划格刀片间距1m m的刀具�当涂层厚度大于60μm时�选用划格刀片间距2m m的刀具2.采用手工切割时�用力要均匀�速度要平稳无颤抖�以便使刃口在切割中正好能穿透涂层而触及基底。
用力过大或不均可能影响测试结果。
3.切割后�在试板上将出现25个或100个方格�用软毛刷沿方格的两对角线方向轻轻刷掉切屑�然后检查并评价涂层附着涂层附着力划格法测试的评定标准�G B/T9286-88�分级说明脱落表现0切割边缘完全平滑�无一格脱落1在切口交叉处涂层有少许薄片分离�但划格区受影响明显不大于5%2切口边缘或交叉处涂层明显脱落大于5%�但受影响明显不大于15%3涂层沿切割边缘�部分或全部以大碎片脱落�或在格子不同部位上�部分或全部脱落�明显大于15%�但受影响明显不大于35%4涂层沿切割边缘�大碎片剥落�或一些方格部分或全部脱落�明显大于35%�但受影响明显不大于65%5大于4级的严重剥落涂层附着力的现场检测摘要�介绍了防腐蚀涂料涂层附着力的机理�并对附着力检测的标准划格法、划X法以及拉开法的测试方法和程序�作了详细说明。
关键词�涂层、附着力、划格法、拉开法1�涂层附着力涂装工程中�对于防腐蚀涂料的涂层附着力检测是涂层保护性能相当重要的指标�越来越被业主和监理所重视。
除了在试验室内的检测外�防腐蚀涂料的选用过程中�对涂料产品进行的样板附着力测试�以及施工过程中现场附着力的检测�也越来越普遍。
有机涂层与金属基底间的附着力�与涂层对金属的保护有着密切的关系�它主要是由附着力与有机涂层下金属的腐蚀过程所决定的。
有机涂层下金属的腐蚀主要是由相界面的电化学腐蚀引起的�附着力的好坏对电化学腐蚀有明显的影响。
良好的附着力能有效地阻挡外界电解质溶液对基体的渗透�推迟界面腐蚀电池的形成�牢固的界面附着力可以极大地阻止腐蚀产物——金属阳离子经相间侧面向阴极区域的扩散�这些阳离子扩散是为了平衡阴极反应所生成的带负电荷的氢氧根离子�这虽然是一个相当缓慢的过程�但是一旦附着力降低�阳离子从相间侧面向阴极扩散的扩散则容易得多。
防腐涂层耐盐雾性试验方法及相关标准
防腐涂层耐盐雾性试验方法及相关标准1.定义、目的及应用防腐涂层的耐盐雾性是指防腐涂层对盐雾侵蚀的抵抗能力。
由于沿海及近海地区的空气中富含呈弥散微小水滴状的盐雾,含盐雾空气除了相对湿度较高外,其比重也较空气大,容易沉降在各种物体上,而盐雾中的氯化物具有很强的腐蚀性,对金属材料及保护涂层具有强烈的腐蚀作用。
作为耐腐蚀试验之一的耐盐雾试验标准方法,包括中性盐雾试验、醋酸-盐雾试验、铜加速的醋酸-盐雾试验(CASS试验)以及湿(盐雾)/干燥/湿气—循环腐蚀环境试验。
特别中性盐雾试验被认为是评定与海洋气氛有密切关系的材料的有关性质的最有效的方法。
因为它可以模拟由湿度或温度,或者由两者共同引起的某些加速作用的基本条件。
可以讲耐盐雾性试验是各类防腐蚀涂料的加速性能试验中最经典、应用最广泛的检测项目,虽然对耐盐雾性试验与实际性能的相关性还是有很大的争论,但是实际应用还是非常普遍。
同时耐盐雾性试验方法也是金属材料耐腐蚀性能试验的主要方法之一。
所以广泛应用于评价和比较底材、前处理、涂层体系或它们的组合体的耐腐蚀情况,另外在许多工业生产、采矿、地下工程、国防工程以及鉴定程序中也成为非常有用的手段。
醋酸-盐雾试验和铜加速的醋酸-盐雾试验(CASS试验)的两种方法被认为更适于钢或锌基压铸件上的装饰性镀铬、镉以及化学处理的铝上的磷化或阳极化等。
而湿(盐雾)/干燥/湿气—循环腐蚀环境试验则主要用来模拟在室外侵蚀环境中发生的腐蚀过程,如海洋环境。
由于与天然老化之间有很好的相关性,所以一些标准的循环己成功用于汽车工业、建筑涂料和通用型防腐蚀涂料的评价中。
2.相关标准各国都有该试验方法的标准,内容基本相同,表1列出耐盐雾性试验方法的标准和试验参数的比较。
表1耐盐雾性试验方法,标准和相关参数标准应用提出单位试验参数GB/T 1771-1991 中国国标(35±2)℃ISO 7253 国际标准(35±2)℃ISO 11997-1:2005 国际标准(35±2)℃ASTM B117-1997 美国ASTM (35±2)℃ASTM B287-1997 美国ASTM (35±2)℃ASTM B368-1997 美国ASTM (35±2)℃3.试验设备和参数(1)盐雾试验箱基本组成和工作原理目前国内外普遍采用的试验没备是盐雾试验箱。
中国钢结构协会钢结构防腐蚀涂料产品认证标准
中国钢结构协会钢结构防腐蚀涂料产品认证质量评定标准1 总则本标准根据中国钢结构协会钢结构防腐蚀涂料产品认证需求,制订了产品质量评定标准,根据钢结构防腐涂装要求,规定防腐蚀涂料必需达到的主要技术指标,以及为此而规定的测试方法、检验规则。
2 制定原则对常用的钢结构防腐蚀涂料产品,优先采用国家标准、行业标准、地方标准;如无上述标准可采用的单一生产企业产品,确有优异产品性能及工程使用业绩的,亦可采用企业标准;较多生产企业产品,确有优异产品性能及工程使用业绩的,经协商,亦可采用行业内平均之上标准。
3 产品测试方法、检验规则的确立3.1 防腐蚀涂料产品的技术指标钢结构防腐蚀涂料产品体系的测试方法需符合GBT 30790.6-2014《色漆和清漆防护涂料体系对钢结构的防腐蚀保护第6部分实验室性能测试方法》。
钢结构防腐蚀涂料产品的技术指标测试方法、检验规则,优先采用国家标准、行业标准、地方标准;如采用上述标准以外的试验方法、检验规则,则在技术指标后,写明具体测试方法或检验规则。
3.2 防腐蚀涂料产品有害物质限量钢结构防腐蚀涂料产品的有害物质限量为强制性标准,按GB 30981-2014《建筑钢结构防腐涂料中有害物质限量》执行。
4 产品质量评定标准内容本评定标准分两部分:第一部分钢结构防腐蚀涂料认证标准;第二部分钢结构防腐蚀涂料测试方法。
5 本标准由中国钢结构协会《钢结构防腐蚀涂料产品认证评定委员会》制订,经中国钢结构协会批准执行。
第一部分钢结构防腐蚀涂料认证标准表1 认证钢结构防腐蚀涂料产品目录1.1富锌底漆1.1.1 富锌底漆采用标准HG/T 3668-2009《富锌底漆》。
1.1.2 富锌底漆技术要求和试验方法:表2 富锌底漆技术要求和试验方法1.2 低锌底漆1.2.1 低锌底漆采用标准HG/T 4844-2015《低锌底漆》。
1.2.2 低锌底漆技术要求和试验方法:表3 低锌底漆技术要求和试验方法1.3 环氧云铁中间漆1.3.2 环氧云铁中间漆采用标准HG/T 4340-2012《环氧云铁中间漆》。
- 1、下载文档前请自行甄别文档内容的完整性,平台不提供额外的编辑、内容补充、找答案等附加服务。
- 2、"仅部分预览"的文档,不可在线预览部分如存在完整性等问题,可反馈申请退款(可完整预览的文档不适用该条件!)。
- 3、如文档侵犯您的权益,请联系客服反馈,我们会尽快为您处理(人工客服工作时间:9:00-18:30)。
防腐蚀涂层的测试1、常规测试法防腐蚀涂层的测试法,在工业实践上,迄今仍以常规宏观的测试法为主。
各国均订阅了许多有关的测试标准,如美国的ASTM、ANSI、SSPC、NACE、MIL等均订有许多标准,国际标准化组织(ISO)、德国(DIN)、日本(JIS)、英国(BS)、法国(NF)、中国(G.B.)等都订有测试标准,逐年修订以测定涂层的防腐蚀性能。
兹将常用测试法简述如下:1.1 盐雾试验法此法是将涂漆的样板划伤后斜置于盐雾箱中,经一定时间后观察样板的锈蚀、蔓延和起泡程度。
这是一种实验室内的测试法,在国际上广泛采用,但它只能表征涂层在该规定条件下的耐腐蚀行为。
ISO3768-1976(E)中性盐雾试验(NSS)的序言中介绍,“抗盐雾性能和在其他介质中的抗蚀性之间很少有直接关系,因为有种种因素影响着腐蚀过程……试验所得结果不能被作为涂层在所有使用它的环境中抗蚀性的直接指南。
同样,试验中不同涂层的性能也不能直接指导这些涂层在服役中的相对耐蚀性”。
盐雾试验虽然采用颇多,但不少专家对它批评很多。
如Appleman和Campbell以及Hare均撰文批评。
事实上大多数研究表明:盐雾试验与实际暴露没有关联性,甚至在海洋环境中的结果与盐雾试验也少关联性。
而且用不同盐雾箱,或在不同时间,结果的重视性也缺乏证明。
T.Liu认为必须找出盐雾试验与实际暴露的关联性,因为涂料用户重视实际效果。
在许多盐雾试验结果中,也确实有些与实际应用的效果不符,例如油性红丹漆在一般大气中(尤其在未充分除锈的钢面上)具有良好的防腐蚀效果,但在盐雾试验中迅速破坏,因为油性基料不耐盐雾引起的阴极部位的皂化。
沿海盐雾中的氯化钠、氯化镁具吸潮而导电,氯离子腐蚀性强,所以盐雾试验比较接近船舶、近海采油平台、沿海港湾设施等。
盐雾试验迄今仍广泛采用,例如汽车的阴极电沉积底漆(CED)都规定必须通过700h的盐雾试验。
盐雾试验之所以广泛被采用,除了有一定的代表性外,是因为迄今尚无其它更广泛合适的测试法。
盐雾试验法是1939年开发的,试验法中最广泛采用的是ASTM B-117-85,在其“范围”一节中认为:在抗盐雾和抗其它介质之间,很少存在直接的关系,因为反应的化学性质,包括膜的化学结构及其保护作用等常常是随所接触的条件而发生很大的变化。
ASTM B117盐雾试验中,盐溶液呈中性,其pH值在6.5~7.2范围中。
具体细节可参见该标准方法,该试验可用于涂层的质量验收,但不应将其看作是探索研究的最佳条件。
类似于B117中性盐雾试验的有:ISO 3768-1976中性盐雾试验(NSS)(划线刀刃角30°)日本JIS K5400 7.8(划线刀刃角22±2°)JIS Z2371德国 SS DIN 50021-1975DIN 53167欧洲ECCA T8(1985)欧洲卷材涂装协会标准GB 1771以上介绍的是中性盐雾试验,是各种盐雾试验法中最广泛采用以测定涂层的耐蚀性。
此外,为了加速腐蚀,尚有醋酸盐雾试验(ASS),是将前述的盐雾液中加入醋酸,使pH值达3.1~3.3。
例如:ANSI/ASTM B 287-74ESS DIN 50021ISO 3769~1976(E)本法适用于Cu+Ni+Cr或Ni+Cr的装饰性镀层,也适用于测定铝的阳极氧化层的耐蚀性。
此外尚有氯化铜加速的醋酸盐雾试验(CASS),因为含铜催化,比上述ASS试验更快速,箱内温度为50±2℃,如:ASTM B 368CASS DIN 50021因为此法快速,多数人喜欢采用于生产控制和产品验收。
但是ASS试验CASS试验均不及中性盐雾NSS广泛采用。
我国上海宝山钢铁总厂毛汉华等在“有机涂层钢板产品统一试验方法”研究报告中(1990年11月)对共20种涂层钢材按ASTM B117、ISO 7253、ECCA T8、JIS K5400 7.8、屯1771各种中性盐雾试验进行对比,发现划痕刀口角度对划伤处腐蚀蔓延距离有影响,刀口角度大则蔓延的距离也大,而且试样封边很重要,以免边部起泡,再蔓延到中部,影响结果的可靠性。
英国铁路局的Timmins开发了不连续而间歇喷雾的循环式盐雾试验箱,称之为Prohesion箱据说效果很好。
Skerry试用的结果认为此法比盐雾试验更接近实际腐蚀。
1.2 湿热试验湿热试验是将涂有漆膜的样板或实物置于湿热试验箱中,定时观察起泡、腐蚀及附着力下降等变化。
虽然湿热试验引起的腐蚀不及盐雾试验剧烈,但湿热试验也具有其现实重要性。
因为有许多涂了漆的物体是处在潮湿闷热的环境中,例如闷在大包装内的机电产品、或贮在洞窟、地下库房内的物体,周围通风不良,湿度很高,涂膜易破坏。
湿热试验与盐雾试验的主要区别是在湿热试验的雾滴中没有盐分而是蒸馏水。
虽然盐滴因其导率高、又含氯离子而腐蚀作用剧烈。
但对渗透压而言,蒸馏水因其导电率高、又含氯离子而腐蚀作用剧烈。
但对渗透压而言,蒸馏水的活度高,涂层是半透膜,蒸馏水渗入漆膜的能力比盐液强。
水分透入漆膜,在两层漆膜之间会降低层间附着力,在漆膜内会引起漆膜膨胀而产生内应力,透入漆膜与金属之间会降低附着力,最后导致漆膜起泡。
起泡后金属与漆膜脱离而开始腐蚀,从图1可见:漆膜吸水率在蒸馏水中比盐水中高。
各种湿热试验的具体方法略有不同,ASTM D 1735《有机涂层水雾试验标准方法》相似于B117盐雾试验的设备,温度为37.8±1.1℃,喷雾液为蒸馏水或去离子水。
ASTM D 2247-80《在100%相对湿度的样板表面始终存在冷凝水的情况下,温度保持38±1℃。
德国标标DIN 50017-1982也是有冷凝水的湿热试验,内中有恒定气氛(KK)和交变湿度和温度气氛(KFW)等试验方法。
以上三种标准测试的温度均为38℃左右。
在湿热试验中温度是重要参数,影响腐蚀和漆膜破坏。
温度越高则高分子链的热运动越活跃,分子间的自由体积增大,利于水汽的透入,但温度太高早与实际情况不符。
有些湿热试验的条件规定有升温及降温的循环,降温时水汽在漆膜上凝露,增加水汽的透入。
所以湿热试验测试条件必须有明确规定,而且垂直悬挂样板之间必须间隔不碰。
Martin和Mcknight将丙烯酸和醇酸漆在潮湿箱中测试,其结果可以画出漆膜破坏程度与温度倒数(1/T)是呈Arrhenius线,并可估出活化能。
图1 漆膜在蒸馏水中与盐水中吸水率比较以上所述试验,整个样板温度是同一的。
另一种湿热试验法是采取温度梯度法,对涂层的考验也较为严酷,例如ISO 6270-1980(E)——耐湿性的测定(连续冷凝法),所用仪器实质上是一个加热器水浴,其顶盖上放置受试的样板,样板的表面(涂层)朝向水浴,水浴的水温保持在40±2℃,水浴上方的温度应在35~40℃之间。
而仪器应置在温度保持23±2℃、不通风环境中进行操作。
在此条件下,水浴的温热的(35~40℃)水蒸汽透入漆膜,蒸汽到达较冷的钢板底材时(23℃)会在涂层和钢板间冷凝,损伤漆膜的附着力而导致起泡。
见图2。
图2 耐湿性的测定图2 耐湿性的测定种试验在实际应用中,类似于有些贮槽的顶部和桥梁下部河面上钢架,在露天寒冷的夜间,钢板很冷,槽内尚温暖的蒸汽透过漆膜而在钢板的内表面上凝露。
水分透入漆膜开始是分散于漆膜中,达到饱和后再继续深入到漆膜与钢板间的界面,在钢面上形成连续水膜,导致腐蚀。
温度梯度法使水渗过漆膜,在其与钢板界面上冷凝成水膜,所以比常规湿热试验严酷。
类似的湿热试验有美国卷材涂装协会(NCCA)的标准Ⅲ-6,也以温度梯度来评定漆膜在潮湿条件下的附着力和抗起泡性。
试验箱中水蒸汽的温度为60±3℃[在距离样板0.0254m(1英寸处测量)]。
1.3 浸渍试验浸渍试验是将受试样板浸渍于液体介质中,这是最简便的测试法,不像上述盐雾试验或湿热试验需要专门的设备,所以在实验室中广泛应用,以测试涂层耐水、耐盐水、耐溶剂、耐酸、耐碱等腐蚀介质的情况。
一般是将试样的一部分浸入介质,一部分留在液面上,液体上面的漆膜要耐蒸气的侵蚀,液下部分的漆膜要耐介质的浸渍,尤其是在空气与液体的交界部位,液面的氧气浓度高,试样金属成为阴极而呈碱性,其下面部位的金属样板的氧气浓度低而形成阳极。
所以在浸渍试验中,试样漆膜在液面部位最易受碱性破坏而出现腐蚀。
浸渍试验中,浸水法有许多标准测试法。
(1)ISO 1521-1973(E)浸水法样板浸于40℃的去离水中并同时通入空气,试板长度的3/4浸渍在水中。
(2)ECCA T9-1985 耐浸水试验同上,水温为40±℃,试样长度的3/4浸入水中。
(3)NCCA Ⅲ-1 金属表面有机涂层浸水试验浸于37.8±1℃的水中。
(4)JIS K5400-19797.2 耐水性蒸馏水或去离子水,水浴保持到该涂料规定的温度。
7.3 耐沸水性7.6 耐盐水性浸入3%(W/V)氯化钠溶液,液温20℃左右,经96小时取出。
9.3 长期浸渍试验浸入液中,经30天之后,以及60天后取出观察检查。
(5)ASTM D870-880浸入蒸馏水,其温度为37.8±a℃(或供需双方都同意的温度),浸入样板长度的1/2~2/3。
浸渍试验一般都用样板进行,但对某些化学品腐蚀性溶液的浸渍试验,除样板外也有用钢棒,将其下端磨圆无棱角,涂上规定的漆膜,充分干透后浸入规定温度和浓度的腐蚀介质。
有关耐溶液浸渍的标准有:ISO 2812-1974(E)涂层耐液体介质的测定,除非另有规定,浸渍的温度为23±2℃。
DIN 53168-1982 抗化学介质稳定性评定。
JIS K5400 7.4 耐碱性7.5 耐酸性7.6 耐盐水浸渍(3%W/V)7.7 耐挥发性溶剂浸渍耐化学品腐蚀的测试法,除浸渍法外还有挂板法,将样板悬挂于化工厂现场,观察其对腐蚀气氛。