环氧树脂耐磨防腐涂层腐蚀性能研究
水性环氧防腐涂料的研究与制备
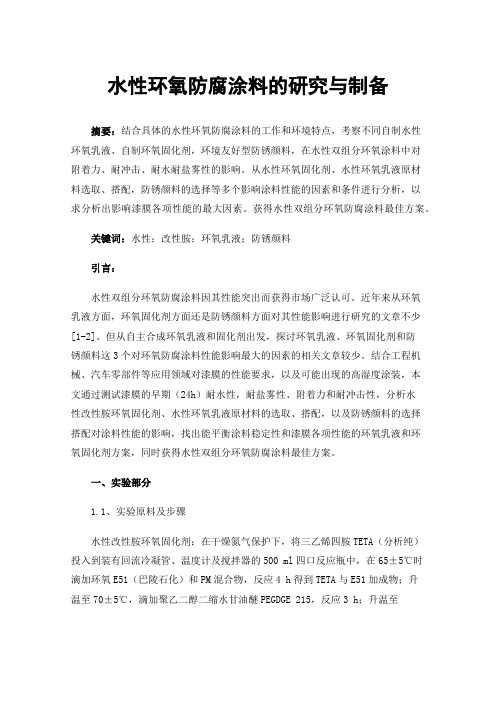
水性环氧防腐涂料的研究与制备摘要:结合具体的水性环氧防腐涂料的工作和环境特点,考察不同自制水性环氧乳液、自制环氧固化剂,环境友好型防锈颜料,在水性双组分环氧涂料中对附着力、耐冲击、耐水耐盐雾性的影响。
从水性环氧固化剂、水性环氧乳液原材料选取、搭配,防锈颜料的选择等多个影响涂料性能的因素和条件进行分析,以求分析出影响漆膜各项性能的最大因素。
获得水性双组分环氧防腐涂料最佳方案。
关键词:水性;改性胺;环氧乳液;防锈颜料引言:水性双组分环氧防腐涂料因其性能突出而获得市场广泛认可。
近年来从环氧乳液方面,环氧固化剂方面还是防锈颜料方面对其性能影响进行研究的文章不少[1-2]。
但从自主合成环氧乳液和固化剂出发,探讨环氧乳液、环氧固化剂和防锈颜料这3个对环氧防腐涂料性能影响最大的因素的相关文章较少。
结合工程机械、汽车零部件等应用领域对漆膜的性能要求,以及可能出现的高湿度涂装,本文通过测试漆膜的早期(24h)耐水性,耐盐雾性、附着力和耐冲击性,分析水性改性胺环氧固化剂、水性环氧乳液原材料的选取、搭配,以及防锈颜料的选择搭配对涂料性能的影响,找出能平衡涂料稳定性和漆膜各项性能的环氧乳液和环氧固化剂方案,同时获得水性双组分环氧防腐涂料最佳方案。
一、实验部分1.1、实验原料及步骤水性改性胺环氧固化剂:在干燥氮气保护下,将三乙烯四胺TETA(分析纯)投入到装有回流冷凝管、温度计及搅拌器的500 ml四口反应瓶中,在65±5℃时滴加环氧E51(巴陵石化)和PM混合物,反应4 h得到TETA与E51加成物;升温至70±5℃,滴加聚乙二醇二缩水甘油醚PEGDGE 215,反应3 h;升温至75±5℃,滴加单环氧化合物BEG(江苏森菲达)封端,反应至活泼氢当量为(120±10),最后加入去离子水稀释到60%固含。
环氧乳液:将E20溶于PM中,加入用PEG-8000、PEG4000(陶氏)自制的反应型乳化剂,在65-75℃,高速分散(2000-3000/min)下缓慢加入去离子水直至相转换,稀释至所需的固含和粘度。
环氧树脂纳米涂料在医疗器械防腐蚀中的应用研究
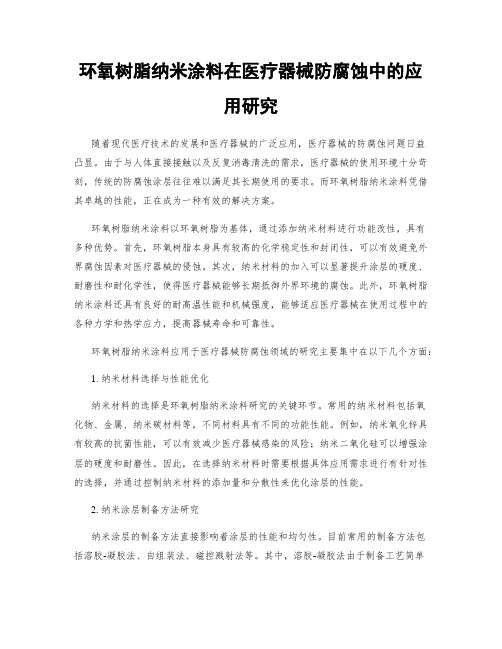
环氧树脂纳米涂料在医疗器械防腐蚀中的应用研究随着现代医疗技术的发展和医疗器械的广泛应用,医疗器械的防腐蚀问题日益凸显。
由于与人体直接接触以及反复消毒清洗的需求,医疗器械的使用环境十分苛刻,传统的防腐蚀涂层往往难以满足其长期使用的要求。
而环氧树脂纳米涂料凭借其卓越的性能,正在成为一种有效的解决方案。
环氧树脂纳米涂料以环氧树脂为基体,通过添加纳米材料进行功能改性,具有多种优势。
首先,环氧树脂本身具有较高的化学稳定性和封闭性,可以有效避免外界腐蚀因素对医疗器械的侵蚀。
其次,纳米材料的加入可以显著提升涂层的硬度、耐磨性和耐化学性,使得医疗器械能够长期抵御外界环境的腐蚀。
此外,环氧树脂纳米涂料还具有良好的耐高温性能和机械强度,能够适应医疗器械在使用过程中的各种力学和热学应力,提高器械寿命和可靠性。
环氧树脂纳米涂料应用于医疗器械防腐蚀领域的研究主要集中在以下几个方面:1. 纳米材料选择与性能优化纳米材料的选择是环氧树脂纳米涂料研究的关键环节。
常用的纳米材料包括氧化物、金属、纳米碳材料等,不同材料具有不同的功能性能。
例如,纳米氧化锌具有较高的抗菌性能,可以有效减少医疗器械感染的风险;纳米二氧化硅可以增强涂层的硬度和耐磨性。
因此,在选择纳米材料时需要根据具体应用需求进行有针对性的选择,并通过控制纳米材料的添加量和分散性来优化涂层的性能。
2. 纳米涂层制备方法研究纳米涂层的制备方法直接影响着涂层的性能和均匀性。
目前常用的制备方法包括溶胶-凝胶法、自组装法、磁控溅射法等。
其中,溶胶-凝胶法由于制备工艺简单且成本低廉,在医疗器械防腐蚀领域得到了广泛应用。
此外,通过调控涂层的制备工艺,可以实现涂层的厚度和组织结构的控制,提高涂层的附着力和防腐蚀性能。
3. 环氧树脂纳米涂层的性能评价对环氧树脂纳米涂层的性能评价主要包括涂层的耐腐蚀性能、机械性能、表面粘附性和溶剂耐受性等。
耐腐蚀性能是衡量涂层抗腐蚀性能的重要指标,可以通过模拟医疗器械使用环境的盐雾试验、浸泡试验等方法进行评价。
一、环氧系列防腐涂料

一、环氧系列防腐涂料一、简介随着现代工业的发展,一批新兴工业领域的出现和许多现代工程的兴建,对防腐涂料承受环境的能力和使用寿命提出了更高的要求。
常用的防腐涂料已不能满足这些需要。
人们提出的“重防腐涂料(Heavy Duty Coating)”的概念,一般指在苛刻的腐蚀环境使用,包括底漆和面漆的配套涂料。
简单地说:重防腐涂料就是使用寿命更长,可适应更苛刻的使用环境的涂料称为重防腐涂料。
在化工大气和海洋环境里重防腐涂料一般可使用10年或15年以上,在酸、碱、盐和溶剂介质里,并在一定温度的腐蚀条件下,一般应能使用5年以上。
重防腐涂料的应用涉及现代化各个领域,大型的工矿企业:化工、石油化工、钢铁及大型矿山冶炼的管道、贮槽、设备等;重要的能源工业:天然气、油管、油罐、输变电、核电设备及煤矿矿井等;现代化的交通运输:桥梁、船舶、集装箱、火车和汽车等;新兴的海洋工程:海上设施、海岸及海湾构造物及海上石油钻井平台等。
环氧树脂是由环氧氯丙烷和双酚A在碱催化下缩合而成的聚合物,随分子量的不同,可分为液体和固体环氧树脂。
以环氧树脂为主要成膜物质的涂料称为环氧涂料。
每年世界上约有40%以上的环氧树脂用于制造环氧涂料,其中大部分用于防腐领域。
环氧防腐涂料是目前世界上用得最为广泛、最为重要的重防腐涂料之一。
环氧树脂类防腐蚀涂料种类很多,大致可分为:胺固化环氧涂料、聚酰胺固化环氧涂料、胺加成物固化环氧涂料、环氧粉末涂料、环氧改性涂料。
二、环氧系列防腐涂料性能特点环氧系列涂料产品具有涂膜坚韧、耐磨、附着力好、耐化学腐蚀、耐强碱、耐水、耐溶剂、耐油等性能优异的特性,并有良好的绝缘性。
主要体现在以下几个方面:1、极好的附着力环氧树脂结构中含有不易水解的脂肪基(-C-)和醚键(-C-O-C-),能够产生电磁引力。
另外,在固化过程中活泼的环氧基和介质表面上的游离键起反应而形成牢固的化学键,从而使环氧树脂涂层获得极好的附着力。
2、优异的防腐蚀性能环氧树脂固化涂层,含有稳定的苯环、醚键等,结构致密,耐酸、耐碱、耐有机溶剂、耐水。
环氧树脂地面涂层特性、施工方法及注意事项

环氧树脂地面涂层特性、施工方法及注意事项环氧树脂地面涂层特性、施工方法及注意事项1 、范围用于环氧树脂为主要原材料的底层涂料、自流平地面涂层材料,薄涂型环氧树脂地面涂层材料。
执行标准JC/T 1015-2006.2 、术语与定义环氧树脂底层涂料epoxy resin flooring primer由环氧树脂、固化剂、稀释剂及其他助剂等组成,在环氧树脂地面涂层材料涂装时,直接涂到地面基体上,起到封闭和粘结作用的涂料。
自流平环氧树脂地面涂层材料self-leveling epoxy resin flooring coating由环氧树脂、稀释剂、固化剂及其他添加剂等组成,搅拌后具有流动性或稍加辅助性铺摊就能流动找平的地面用材料。
薄涂型环氧树脂地面涂层材料thin epoxy resin flooring coating由环氧树脂、稀释剂、固化剂及其他添加剂等组成,采用喷涂、滚涂或刷涂等施工方法,通常一遍施工干膜厚度在10μm 以下的地面涂层材料。
表 1 环氧树脂底层涂料的要求序号项目技术指标1 容器中的状态搅拌后无硬块,呈均匀状态2 固体含量/% ≥ 503 干燥时间/h 表干≤ 6 实干≤ 244 7d 拉伸粘强度 2.0表 2 自流平环氧树脂地面涂层材料的要求序号项目技术指标1 容器中的状态搅拌后无硬块,呈均匀状态2 涂膜外观平整,无折皱、针孔、气泡等缺陷3 固体含量/% ≥ 954 流动度/mm ≥ 1405 干燥时间/h 表干≤ 8 实干≤ 246 7d 抗压强度/MPa ≥ 607 7d 拉伸粘结强度/MPa ≥ 2.08 邵氏硬度(D 型)≥ 7.09 抗冲击性,ф 60mm ,1000g 的钢球涂膜无裂纹、无剥落10 耐磨性/g ≤ 0.1511 耐化学性15% 的NaOH 溶液涂膜完整,不起泡、不剥落,允许轻微变色10% 的HCl 溶液120# 溶剂汽油表 3 薄涂型环氧树脂地面涂层材料要求序号项目技术指标1 容器中的状态搅拌后无硬块,呈均匀状态2 涂膜外观平整、无刷痕、折皱、针孔、气泡等缺陷3 固体含量/% ≥ 604 干燥时间/h 表干≤ 6实干≤ 245 铅笔硬度/H ≥ 36 抗冲击性,ф 50mm ,500g 的钢球涂膜无裂纹、无剥落7 耐磨性/g ≤ 0.208 7d 拉伸粘强度/MPa 2.09 耐水性涂膜完整,不起泡,不剥落,允许轻微变色10 耐化学性15% 的NaOH 溶液涂膜完整,不起泡、不剥落,允许轻微变色10% 的HCl 溶液120# 溶剂汽油一、产品主要性能特点抗冲击优、硬度好、高负裁、耐磨损;无接缝、防尘、防潮、防腐、防霉;耐酸、碱、盐及其它化学溶剂性腐蚀,耐油污、耐化学品腐蚀、硬化收缩率小;色彩丰富,营造美丽清洁环境;施工方便,涂刷、喷刷、滚涂均可。
防腐涂料的研究 - 中国涂料在线

防腐涂料的研究由于防腐涂料具有性能优异、制造方便、价格低廉等一些其它材料无法比拟的优点,因此在选择防腐措施时成为优先考虑的对象。
随着防腐技术的成熟,防腐涂料也必将得到进一步发展。
其中高固体分涂料因其可挥发成分少、固化速度快、施工性能好必将成为发展的趋势。
研究和分析了环氧树脂、聚氨酯等金属防腐涂料的特点,介绍了它们的最新发展动向。
金属的腐蚀,是金属受环境介质的化学或电化学作用而被破坏的现象。
金属的腐蚀遍及国民经济各个领域,给国民经济带来了巨大的损失。
在工业发达的国家中,腐蚀造成的直接经济损失占国民经济总产值的1%~4%,每年腐蚀生锈的钢铁约占产量的20%,约有30%的设备因腐蚀而报废。
在中国,由于金属腐蚀造成的经济损失每年高达300亿元以上,占国民生产总值的4%。
长期以来,人们一直采用多种技术对金属加以保护,防止腐蚀的发生。
其中,金属设备防腐蚀最有效、最常用的方法之一是在金属表面涂敷防腐蚀涂层,以隔绝腐蚀介质与金属基体。
防腐涂料和其它涂料一样,其配方组成主要包括基料(树脂)、颜填料和溶剂。
基料树脂是成膜物质,是涂料中的主要成分,它的分子结构决定着涂料的主要性能;颜填料是用来辅助隔离腐蚀因素的,根据作用机理又可分为防锈颜料和片状填料;溶剂分为有机溶剂或水,用来溶解基料树脂,便于成膜。
本文拟对常用金属防腐涂料的最新研究进展作一综述。
环氧树脂涂料环氧树脂是平均每个分子含有两个或两个以上环氧基的热固性树脂。
环氧树脂以其易于加工成型、固化物性能优异等特点而被广泛应用,通过环氧结构改性、环氧合金化、填充无机填料、膨胀单体改性等高性能化后可以制成防腐涂料。
环氧树脂涂料有优良的物理机械性能,最突出的是它对金属的附着力强;它的耐化学药品性和耐油性也很好,特别是耐碱性非常好。
环氧树脂涂料的主要成分是环氧树脂及其固化剂,辅助成分有颜料、填料等。
不锈钢粉末是最近几年发展起来的金属颜料,由于其具有不活泼性,特别是在高温强蚀环境中的防护性极好,所以既可用来作为主要颜料,也可作为复合颜料的一部分,与粘合剂组成防护性涂料。
自修复环氧防腐涂层的研究进展

自修复环氧防腐涂层的研究进展目录1. 内容综述 (2)1.1 研究背景与意义 (3)1.2 国内外研究现状概述 (4)2. 自修复环氧防腐涂层材料的设计与制备 (5)2.1 材料选择与改进 (6)2.2 涂层制备方法与优化 (8)2.3 涂层性能评价标准建立 (8)3. 自修复环氧防腐涂层的机理研究 (9)3.1 自修复机制的探究 (10)3.2 防腐效果的评估方法 (12)3.3 涂层与基材的界面结合分析 (13)4. 自修复环氧防腐涂层在典型环境中的应用 (14)4.1 在金属腐蚀环境中的应用 (15)4.2 在化工环境污染环境中的应用 (17)4.3 在海洋工程防腐环境中的应用 (18)5. 自修复环氧防腐涂层的性能改进与优化 (18)5.1 提高耐磨性、耐腐蚀性和耐候性 (20)5.2 优化涂层结构与成分以提高整体性能 (21)5.3 涂层的多功能化与集成化研究 (22)6. 实际应用案例分析 (23)6.1 工程实例介绍 (25)6.2 应用效果与评价 (26)6.3 经验教训与发展建议 (27)7. 结论与展望 (28)7.1 研究成果总结 (29)7.2 存在问题与挑战 (31)7.3 未来发展方向与前景展望 (32)1. 内容综述随着科技的不断发展,自修复环氧防腐涂层作为一种新型环保型涂料,逐渐受到人们的关注和重视。
自修复环氧防腐涂层具有优异的耐磨、耐腐蚀、抗老化等性能,能够有效地延长物体的使用寿命,降低维修成本,减少对环境的污染。
国内外学者在自修复环氧防腐涂层的研究方面取得了一系列重要进展。
自修复环氧防腐涂层的制备工艺得到了不断的优化,研究人员通过采用不同的成膜基料、添加剂和分散剂等,成功地实现了不同类型自修复环氧防腐涂层的制备。
还研究了纳米颗粒、微米级颗粒等特殊功能填料在自修复环氧防腐涂层中的应用,进一步提高了涂层的性能。
自修复环氧防腐涂层的性能研究取得了显著成果,研究人员通过对不同种类的自修复环氧防腐涂层进行对比试验,发现其具有较高的抗划伤性、耐磨性和耐腐蚀性,能够有效抵抗各种恶劣环境的侵蚀。
环氧树脂防腐性能研究进展
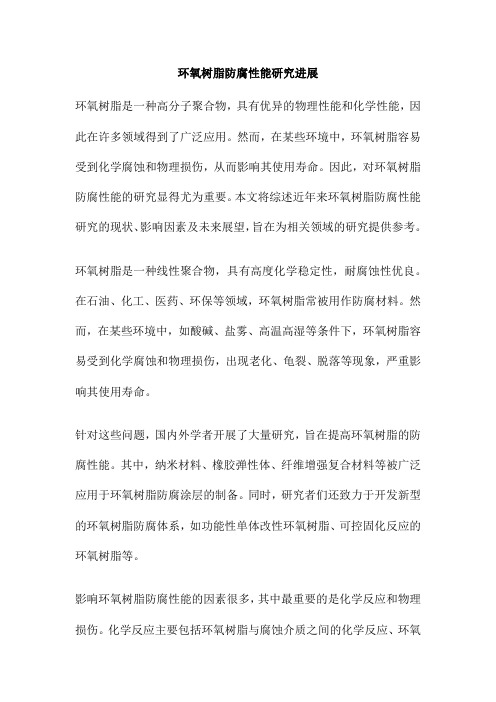
环氧树脂防腐性能研究进展环氧树脂是一种高分子聚合物,具有优异的物理性能和化学性能,因此在许多领域得到了广泛应用。
然而,在某些环境中,环氧树脂容易受到化学腐蚀和物理损伤,从而影响其使用寿命。
因此,对环氧树脂防腐性能的研究显得尤为重要。
本文将综述近年来环氧树脂防腐性能研究的现状、影响因素及未来展望,旨在为相关领域的研究提供参考。
环氧树脂是一种线性聚合物,具有高度化学稳定性,耐腐蚀性优良。
在石油、化工、医药、环保等领域,环氧树脂常被用作防腐材料。
然而,在某些环境中,如酸碱、盐雾、高温高湿等条件下,环氧树脂容易受到化学腐蚀和物理损伤,出现老化、龟裂、脱落等现象,严重影响其使用寿命。
针对这些问题,国内外学者开展了大量研究,旨在提高环氧树脂的防腐性能。
其中,纳米材料、橡胶弹性体、纤维增强复合材料等被广泛应用于环氧树脂防腐涂层的制备。
同时,研究者们还致力于开发新型的环氧树脂防腐体系,如功能性单体改性环氧树脂、可控固化反应的环氧树脂等。
影响环氧树脂防腐性能的因素很多,其中最重要的是化学反应和物理损伤。
化学反应主要包括环氧树脂与腐蚀介质之间的化学反应、环氧树脂本身的化学反应。
物理损伤主要包括环氧树脂的机械强度、耐磨性、抗冲击性等。
这些因素之间相互作用,共同影响着环氧树脂的防腐性能。
未来,环氧树脂防腐性能的研究将朝着多功能化、智能化、绿色化等方向发展。
具体来说,研究者们将致力于开发具有自修复能力、耐高温高湿、抗紫外老化等功能的环氧树脂防腐体系;利用智能材料和传感器技术,实现环氧树脂防腐涂层的智能监测和预警;还将在保证环氧树脂防腐性能的前提下,降低其生产和使用过程中的能耗和排放,实现绿色可持续发展。
环氧树脂防腐性能的研究对于提高其在各领域的应用效果具有重要意义。
通过深入探究影响环氧树脂防腐性能的因素及作用机制,合理设计并制备高性能的环氧树脂防腐材料,有助于解决环氧树脂在复杂环境下的腐蚀问题,延长其使用寿命。
随着科学技术的发展,环氧树脂防腐性能的研究将不断取得突破性进展,为相关领域的发展提供有力支持。
防腐涂料性能比较

防腐涂料性能比较近一、二十年研究、开发的新型高分子防腐涂料,具有非寻常高分子材料的优异性能,是当今高分子材料开发的热点之一,有高聚物"合金"的美誉。
对材料表面产生防腐保护和装饰作用。
防腐涂料具有高强度、高韧性、耐冲磨、耐老化、耐酸碱盐腐蚀,附着力强,耐水解、耐汽油、煤油等介质,无毒和不燃烧等优良性能。
因此用途广泛,不但适用于钢材防腐,在混凝土、木质等非金属构件也能应用。
其综合性能特点如下:1、产品为带锈防腐涂料,施工时允许金属表面留有薄锈,涂料成膜固化时可渗透到锈层中,将铁锈分隔包围,阻止金属进一步锈蚀,因此在钢铁等金属层上应用不需要前处理,可带锈施工,大大简化了防腐作业工序,施工简单方便;2、产品为弹性涂层,涂层伸长率为100%。
在各种基层材料的自由伸缩或机械伸缩下,涂层均能适应,保证不脱落,不开裂,确保了涂层的防腐质量和使用寿命;3、产品为高固体份涂料,清漆固体份60%,色漆更高,高于其它防腐涂料。
减少了施工道数,节约了涂料用量。
二、环氧防腐涂料系列环氧树脂涂料主要是由环氧树脂和屏蔽性高的防锈颜料、填料、触变剂、防锈添加剂、固化剂和混合溶剂等配制而成。
由于使用的环氧树脂分子量大小差异以及比例的不同,添加剂的各异,所得到的产品性能、用途也就各不相同。
环氧树脂涂料,具有独特优良的防腐蚀性能。
主要具有如下特性:1、优异的耐腐蚀性能。
由于环氧树脂成膜后的分子链上含有很稳定的碳-碳键和醚键和苯环,结构致密,屏蔽性好,经固化后抗渗透性能优异,具有耐水性、耐盐雾性、耐油性,还有优良的耐化学药品性;2、有良好的附着力。
因涂膜分子中含有的极性较大的羟基与相临界面产生引力,如与金属表面上的游离键起反应,而形成牢固的化学元素键,因而大大地加强了涂膜的附着力,扩大了对底材的适应性;3、具有较好的物理机械性。
成膜后分子结构中的苯环上羟基已被醚化,所以质量稳定,涂膜刚柔结合,耐磨性好,涂料固体含量高,一次成膜厚,同时在固化过程中没有小分子副产物的生成,不会产生气体,因此还具有体积收缩性小,热膨胀系数低等特点;涂层不但介电性和电绝缘性好,而且防潮防水性能优异,热老化性好,因此用于电器产品可作为绝缘涂层。
- 1、下载文档前请自行甄别文档内容的完整性,平台不提供额外的编辑、内容补充、找答案等附加服务。
- 2、"仅部分预览"的文档,不可在线预览部分如存在完整性等问题,可反馈申请退款(可完整预览的文档不适用该条件!)。
- 3、如文档侵犯您的权益,请联系客服反馈,我们会尽快为您处理(人工客服工作时间:9:00-18:30)。
环氧树脂耐磨防腐涂层腐蚀性能研究周晓谦(辽宁工程技术大学材料系,辽宁阜新123000)E-mail:zxq6558960@摘要:通过三种不同配方的环氧树脂涂层耐腐蚀性能测试,得到在五种不同介质条件下涂层的拉伸剪切强度数据。
由比较可知,通过插层复合的方法制备环氧树脂/纳米蒙脱土/203#PA耐磨防腐涂层的耐腐蚀性能最佳,确定了环氧树脂耐磨防腐涂层的最佳配方。
关键词:环氧树脂涂层,纳米蒙脱土,粉煤灰,腐蚀性能耐磨胶粘涂层是使用含有耐磨填料的胶粘剂涂敷在零件表面上所形成的一种新型抗磨复合材料,是以修复、防磨或减磨为主的新型涂层,主要用于密封、堵漏、抗腐蚀、抗冲蚀磨损及抗磨粒磨损等工况,在铸造、水泥、铁路、电子等多种行业有广泛应用。
耐磨胶粘涂层的种类和配方不同,但其基本成分可归纳为基体、固化剂、填料和辅助材料等四种组分。
以环氧树脂为胶粘剂的涂层在冲蚀磨损条件下,得到了一定程度的应用[1]。
环氧树脂耐磨涂层在实际应用过程中可能有腐蚀性介质存在,所以环氧树脂耐磨涂层腐蚀性能研究在理论和实际应用中都很有意义。
1 材料制备与实验方法1.1 原材料(1) 冲蚀试样长度为100mm,宽为25mm,厚为3mm的Q235钢片。
(2) 环氧树脂:E-44(沈阳正泰防腐材料有限公司生产)和E51(无锡树脂厂生产)。
(3) 固化剂:T-31(沈阳化工十厂生产)和203#PA(天津延安化工厂生产)。
(4) 增韧剂:DBP(郑州市化学试剂三厂)。
(5) 填料:粉煤灰(阜新热电厂粉磨后的成品)和纳米蒙脱土(中科院化学所)。
1.2 样品制备首先对Q235钢片进行机械磨平,除去其表面污物、氧化皮、锈斑、灰尘等,用丙酮擦洗脱脂后,再用砂纸打磨,将表面处理光滑后再用刀片粗糙钢片表面,严格按照配方称量药品,配胶时的加入顺序为:环氧树脂E-44、E-51、增韧剂、填料、固化剂。
采用刮涂法进行涂胶,使试样的五个面均涂上胶层且保持均匀平整,控制胶膜层的厚度为0.8-1.0mm为宜。
环氧树脂涂层配比见表1。
表1 环氧树脂涂层配比(质量份数)Tab. 1 The Mixture Ratio of Epoxy Anti-wear Coatings (Mass Ratio)配方E-44 E-51 DBP T-31 PA 粉煤灰纳米蒙脱土A 30 70 14 25 0 150 0B 30 70 0 0 80 200 0C 30 70 0 0 80 0 7* 固化条件为:20℃×24h+120℃×3 h+20℃×24h- 1 -1.3 涂层腐蚀性能测试首先根据表1的配方和固化条件制备环氧树脂涂层试样。
这些试样分别在自来水、机油、10%盐酸水溶液、10%氢氧化钠水溶液、3%氯化钠水溶液中进行耐腐蚀实验。
浸泡三天干燥后的试样,测试其拉伸剪切强度,并与对比试样比较。
2 实验结果被放入腐蚀介质中浸泡后的拉伸剪切强度及其下降率的数据见表2,其中τ表示涂层剪切强度,Δτ%表示剪切强度的下降率,数据中的“-”表示剪切强度的增加率。
进而比较三种涂层在腐蚀性介质中的耐腐蚀性能,选出较好的耐腐蚀配方。
表2 三种涂层配方的拉伸剪切强度Tab. 2 The Tensile Strength of Three Epoxy Anti-wear Coatings配方A 配方B 配方C介质名称τΔτ% τΔτ % τΔτ%(MPa) (MPa)(MPa) (MPa) (MPa) (MPa)未被腐蚀试样14.70 0 16.37 0 18.99 0自来水15.74 -5.24 14.14 13.62 17.95 5.48机油13.08 11.02 14.95 8.67 17.77 6.42盐酸水溶液12.93 12.04 13.32 18.63 17.62 7.21氢氧化钠水溶液13.36 7.07 13.38 15.27 17.99 5.32氯化钠水溶液12.85 12.59 12.99 20.65 17.46 8.063 实验结果分析3.1水对环氧树脂涂层的腐蚀特性的影响配方A的涂层在水中浸泡后,测得的剪切强度与对照值增加了,而配方B和配方C涂层的剪切强度下降了,说明配方A的耐水性最好。
主要因为T-31是一种水下固化剂,耐水、耐潮性能良好,由于T-31脆性较大,胶层部分存在较多的微裂纹,水对胶层的物理增塑作用使微裂纹尖端钝化,同时材料的抗拉伸剪切性能对缺陷很敏感,所以在缺陷钝化后,以T-31为固化剂的环氧树脂涂层的拉伸剪切强度值增大[2]。
而203#PA具有较强的吸水性,因此总体看在水中由203#PA做固化剂的涂层,其拉伸剪切强度会降低些。
配方B是由微米级的粉煤灰作填料,它在一定程度上有吸水性,因此对水的腐蚀抵抗能力较弱,配方C则是用纳米蒙脱土作填料的,该蒙脱土由于经过有机化处理,由亲水性变为亲油性,从一定程度上削弱了水对它的腐蚀,因此配方C的耐水性比配方B强。
3.2机油对环氧树脂涂层的腐蚀特性影响三种配方的涂层在机油中浸泡后,测得的剪切强度与对照值相比均下降了,其中下降幅度最大的是配方A,下降幅度最小是配方C。
因为机油属于非极性有机介质,环氧树脂极性也较弱,根据相似相容原理可知,未交联的环氧树脂及其它有机小分子组分易溶于机油中而失去原有的性能,导致交联的环氧树脂的拉伸剪切强度下降[3]。
环氧树脂固化后分子长链生成,其最低分子量分级1是环氧树脂的低聚物,分级2是1mol环氧树脂与固化剂的加成产物,分级3是2mol- 2 -环氧树脂与2mol固化剂的加成产物,出现侧链,分级4是含有两个以上侧链的交联产物。
机油能溶解分级1和2产物,但很难溶解分级3和分级4的固化产物。
由实验数据可知配方A浸泡后的拉伸剪切强度降低得最大,下降了11.02%,说明固化产物中可溶于机油的分级1和分级2的产物较多,耐油性最差。
从配方B和配方C的数据比较可知:由于配方B采用的填料为粉煤灰,配方C采用的是纳米级的填料蒙脱土,填料的不同是影响这两个配方剪切强度下降的主要因素。
3.3 氢氧化钠水溶液对环氧树脂涂层的腐蚀特性影响三种配方的涂层在氢氧化钠溶液中浸泡后,测得的剪切强度与对照值均下降了,其中下降幅度最大是配方B,下降幅度最小是配方C。
在碱性环境下,涂层中的酯基容易发生水解,从而使环氧胶粘涂层的剪切强度下降,同时氢氧化钠分子电离出的Na+与水结合后形成了水合Na+,降低了水分子的活度,阻碍了水分子向胶粘涂层的扩散[4],另外根据水对三种不同胶粘涂层的腐蚀特性分析,可以看出氢氧化钠溶液对T-31固化产物的腐蚀程度较低,而对PA固化产物的腐蚀程度较重。
微米级的填料粉煤灰耐氢氧化钠溶液的腐蚀效果不十分明显,而纳米级的填料由于层间无限溶涨的特性,提高了胶粘剂的抗腐蚀特性,因而配方C表现为耐氢氧化钠溶液腐蚀性最强。
3.4 10%盐酸水溶液、3%氯化钠水溶液对环氧树脂涂层的腐蚀特性研究三种配方的涂层在盐酸溶液中浸泡后,测得的剪切强度与对照值相比均下降了,其中下降幅度最大是配方B,下降幅度最小是配方C。
三种配方的涂层在盐酸溶液中浸泡后,测得的剪切强度与对照值均下降了,其中下降幅度最大是配方B,下降幅度最小是配方C。
由于环氧树脂在生产过程中闭环反应不完全,残留一定量的可水解氯,氯的存在会影响胶粘涂层的性能,因此生产时应当降低环氧树脂中氯的含量。
对于这两种介质的浸泡腐蚀,由于氯离子的浓度较高,导致胶粘涂层的强烈腐蚀,因此不论是以何种固化剂固化的环氧树脂涂层在这两种溶液中都腐蚀较重。
但可以看出,纳米蒙脱土增强的环氧树脂胶粘涂层抗这两种介质的腐蚀性能要优于其它两种,主要因为聚合物基体中存在着分散的纳米粘土层,这些高度分散的粘土层不能透过水分子,使得溶质要通过围绕粘土层弯曲的路径才能通过薄膜,再加上环氧树脂自身耐介质性能良好,因此渗透与扩散阻力增加,则耐介质性能有明显提高。
4 结论从三种配方在不同介质存在的条件下拉伸剪切强度的变化数据可知,除了涂层A的耐水性能最好外,涂层C在其它情况下的耐介质性能是最好的。
即使在水介质中涂层C的拉伸剪切强度依然高于涂层A。
显然涂层耐蚀性对在不同介质条件下发生的冲蚀磨损现象会有直接影响,提高涂层的耐蚀性也是提高抗冲蚀磨损能力的重要途径之一,由于以纳米蒙脱土为填料、203#PA为固化剂的配方C涂层的耐腐蚀性能最好,推荐用于耐腐蚀涂层的配方为E-44:E-51:203#PA:MMT=30:70:80:7(wt%),固化条件是室温预固化一天,高温固化温度为120℃,高温固化时间为3h,随后室温放置一天。
- 3 -参考文献[1]张向宇.胶接与胶补[M].武汉:湖南科学技术出版社.1994:58~70[2]陈正钧等.耐腐蚀非金属材料及应用[M].北京:化学工业出版社.1995:114~116[3]李京等.介质种类、浓度对环氧基复合涂膜传输的影响,材料保护[J],1997(10):13[4]杨学稳等.环氧树脂/蒙脱土纳米复合改性的研究,工程塑料[J],2002(4):5Study on Properties of anti-erosion wearing of EpoxyResin CoatingsZhou XiaoqianLiaoning Technical University(123000 China)AbstractBy testing three properties of anti-erosion wearing and corrosion resistance of epoxy resin coatings, it gained the data of tensile-shear strength of anti-erosion wearing under five media. Compared those data, it concluded Epoxy /nano-MMT/ 203#PA coatings prepared by means of intercalation is best of them and gave the best composition of anti-erosion wearing of epoxy resin coatings.Keywords:Epoxy resin coatings, nano-MMT, fly ash, corrosion resistance- 4 -。