太钢高炉降低铁水硅含量的实践
提高3200m3高炉生铁硅含量合格率实践

3 调 整造渣制度
1 炉 渣 碱 度 。碱 度高 , 利 于减 少 SO气体 的 ) 有 i 挥 发 , 是 碱度 过高会 使 炉渣 的熔 化 温度 升高 , 高 但 提 炉 缸温 度 , 进 SO气体 的挥 发 , 而抵 消高 碱度 减 促 i 从 少 SO 气 体 挥 发 的 作 用 。 提 高 炉 渣 的 二 元 碱 度 i
2 控 制 合 适 的理 论 燃 烧 温 度
理论燃 烧 温度 (f是反 映 炉缸 热状态 的重要参 T) 数 , 于确定 的炉 料 及 高 炉 , 最 佳 的 T 值 是 一 定 对 其 f
上 限炉温较多 , 不利于高炉炼铁降低成本 。
1 改善原燃料质量
1 1 提 高烧 结矿低 温 还原 粉化 指数 .
次数 , 同时控制筛分速度 , 杜绝空仓 , 半仓打料等措 施, 使高炉的人炉含粉率低于 l %。 13 监控 焦炭 质 量 .
供 320 m 高炉焦炭采用 7 、 炉干熄焦 , 0 8焦
虽然质量 比其他焦炉高 , 但是仍然存在质量 、 性能不 稳定的问题 , 造成高炉被动调剂频繁, 焦炭负荷变化 大, 不利于炉缸工作。通过与焦化厂及时沟通 , 了解
煤气拥有更多的热量传递给炉料 , 有利于炉料的加 热 分解 和促 进 还原过 程 的进 行 。 因此 , 高 的 T 会 较 f
增 加 SO i 的还 原 和 SO 气体 的挥发 , 过低 的理论 i 而 燃 烧 温度 又使 炉缸 热 量 不 足 , 因此 确 定 适 宜 的理 论 燃 烧 温度 为 210~ 5 : 更 有利 于稳 定 生铁 硅 5 220c , I
莱钢 科技
21 0 1年 1 2月
利 于 提高 炉渣 的稳 定 性 , 当 A 含 量 继 续 升 高 但 1 0
降低转炉铁水单耗实践

降低转炉铁水单耗实践随着国家环保政策不断升级,钢铁行业的污染排放问题越来越引人关注。
其中,转炉钢铁生产过程中产生的废气和废水被认为是主要污染源之一。
为此,我们采取一系列措施,降低转炉铁水单耗,减少污染排放。
1. 优化炉渣配比在转炉炼铁生产过程中,炉渣的形成率比较高。
过多的炉渣不仅增加了能耗和原材料消耗,而且会增加转炉钢铁生产中的废气和废水排放量。
因此,我们对炉渣配比进行了优化,减少了炉渣的形成量,同时又保证了铁水的质量。
经过实践证明,炉渣配比的优化可以有效地降低转炉铁水单耗。
2. 采用高炉矿渣代替部分石灰石在转炉钢铁生产中,大量使用石灰石作为反应物。
但是,石灰石的开采和利用也会对环境造成一定的影响。
为了减少这种影响,我们开始采用高炉矿渣代替部分石灰石。
高炉矿渣是高炉生产过程中产生的废渣,如果不合理利用将对环境造成污染。
采用高炉矿渣代替部分石灰石不仅可以减少石灰石的使用量,还可以充分利用高炉矿渣这种废弃资源。
3. 强化废气处理转炉钢铁生产过程中,废气的排放量相当大。
为了减少废气的排放,我们采用了一系列措施强化废气处理。
首先,对主要污染物进行了分析,找出了污染排放的毒害物质,然后针对性地选用了相应的废气处理设备进行处理。
同时,我们还对设备的运行状况进行了监测,及时进行维修和保养,确保了废气处理的效果。
4. 加强员工环保意识教育环保工作是一个长期的过程,不能单靠一些设备和措施来解决。
员工的环保意识也是至关重要的。
因此,我们加强了员工的环保意识教育,讲解环保政策和环境保护法律法规,让员工充分了解环保的重要性,并为员工提供各种环保知识,鼓励员工在日常工作和生活中节约能源和减少污染物排放。
总之,转炉钢铁生产过程中的污染问题需要每一个钢铁企业的积极参与。
通过优化炉渣配比、采用高炉矿渣代替部分石灰石、强化废气处理和加强员工的环保意识教育等措施的实施,我们成功地降低了转炉铁水单耗并减少了污染物的排放。
这从一个侧面说明,在生产中注重环保是可以提高经济效益和企业形象的,也是企业应尽的社会责任。
炼钢冶炼低硅工艺操作措施-概述说明以及解释
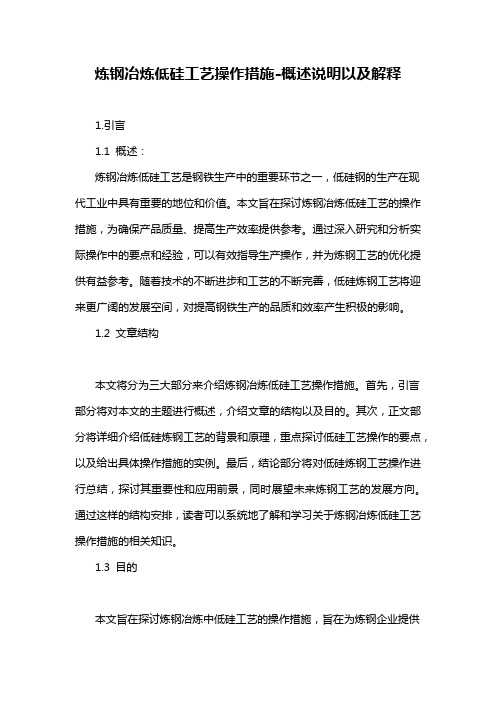
炼钢冶炼低硅工艺操作措施-概述说明以及解释1.引言1.1 概述:炼钢冶炼低硅工艺是钢铁生产中的重要环节之一,低硅钢的生产在现代工业中具有重要的地位和价值。
本文旨在探讨炼钢冶炼低硅工艺的操作措施,为确保产品质量、提高生产效率提供参考。
通过深入研究和分析实际操作中的要点和经验,可以有效指导生产操作,并为炼钢工艺的优化提供有益参考。
随着技术的不断进步和工艺的不断完善,低硅炼钢工艺将迎来更广阔的发展空间,对提高钢铁生产的品质和效率产生积极的影响。
1.2 文章结构本文将分为三大部分来介绍炼钢冶炼低硅工艺操作措施。
首先,引言部分将对本文的主题进行概述,介绍文章的结构以及目的。
其次,正文部分将详细介绍低硅炼钢工艺的背景和原理,重点探讨低硅工艺操作的要点,以及给出具体操作措施的实例。
最后,结论部分将对低硅炼钢工艺操作进行总结,探讨其重要性和应用前景,同时展望未来炼钢工艺的发展方向。
通过这样的结构安排,读者可以系统地了解和学习关于炼钢冶炼低硅工艺操作措施的相关知识。
1.3 目的本文旨在探讨炼钢冶炼中低硅工艺的操作措施,旨在为炼钢企业提供明确的操作指导,帮助其在低硅炼钢过程中减少能耗、提高生产效率、优化产品质量,从而提升企业的竞争力。
通过深入分析低硅炼钢工艺的特点和存在的问题,总结出一套科学合理的操作措施,为提高炼钢工艺的稳定性和可控性提供参考,推动炼钢行业的技术进步和发展。
分的内容2.正文2.1 低硅炼钢工艺介绍低硅炼钢工艺是指在钢铁冶炼过程中,控制炉料中硅含量低于一定标准的工艺。
硅是钢铁中的杂质元素,其含量过高会对钢铁的性能产生不利影响,降低钢的强度和可焊性。
因此,通过优化低硅炼钢工艺,可以提高钢材的质量和机械性能。
低硅炼钢工艺的主要特点包括:1. 控制炉料成分:在炉料中添加足量的硅剂,使其与熔融金属中的硅相结合,降低金属浆和硅含量。
2. 保持一定的炉温:适当控制炉温,促使硅剂和熔融金属充分反应,确保低硅工艺的有效实施。
高炉低硅冶炼技术
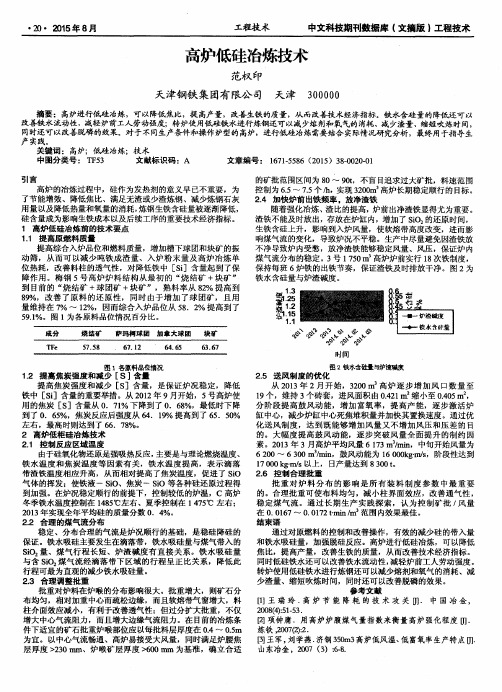
工程技术
中文科 技期 刊数 据库 ( 文摘 版 l 工程技术
高炉低硅冶炼技术
范 杈 印
天津钢铁 集 团有 限公 司 天津
3 0 0 0 0 0
摘要 :高炉进行低硅冶炼 ,可以降低 焦比,提 高产量 ,改善生铁 的质量 ,从而改善技术经济指标 。铁水含硅量 的降低还可 以 改善铁水 流动性 ,减轻炉前 工人 劳动 强度;转炉使用低硅 铁水进行 炼钢还可 以减少熔剂和氧气的消耗 、减 少渣量 、缩短 吹炼时间, 同时还可 以改善脱磷的效果。对 于不同生产条件和操作炉型的 高炉,进行循硅 冶炼需要结合 实际情况研 究分析 ,最终用于指导生 产 实践。 关键 词 :高炉;低硅冶炼;技术 中图分类号 :T F 5 3 文献标识码 :A 文章编号 : 1 6 7 1 . 5 5 8 6( 2 0 1 5 )3 8 . 0 0 2 0达 到 了 6 6 。7 8 %。
2 高炉低柜硅 冶炼技术
2 . 1 控 制 反 应 区 域 温 度 由于硅氧 化物 还原是强吸热反应 , 主要 是与理论燃烧温度 、 铁 水温 度和焦 炭温度 等 因素 有关 ,铁 水温度 提高 ,表 示滴 落 带渣铁温度相应升高 ,从而相对提高 了焦炭温度 ,促进 了 S i O
臻
I 十 铰 康 翕 许 鬣
时问
圈 l各原料 晶位情况
瞪 2铁琦 、 舍链量与炉渣碱度
2 . 5 送风制度的优化 1 . 2 提高焦炭 强度和减少 [ S]含量 提 高焦炭强度和 减少 [ s l含量 ,是 保证炉况 稳定 ,降低 从 2 0 1 3年 2月开 始,3 2 0 0 I I l 3 高 炉逐 步增 加 风 口数量 至 铁中 [ s i ]含量 的重要举措 。从 2 0 1 2年 9月开始,5号 高炉使 1 9 个 ,维持 3个砖套 ,进风面积 由0 . 4 2 1 缩小至 0 . 4 0 5 1 l l 2 , 用 的焦炭 [ S ]含量从 0 .7 1 % 下 降到 了 0 .6 8 %,最低 时下 降 分 阶段 提高鼓 风动 能,增加 富氧率 ,提 高产 能,逐步激 活炉 到了0 .6 5 %,焦炭反应后强度从 6 4 .1 9 % 提高到 了 6 5 .5 0 % 缸 中心 ,减少炉缸 中心死焦堆积量并加快其 置换速度 。通过优
高炉低硅冶炼知识
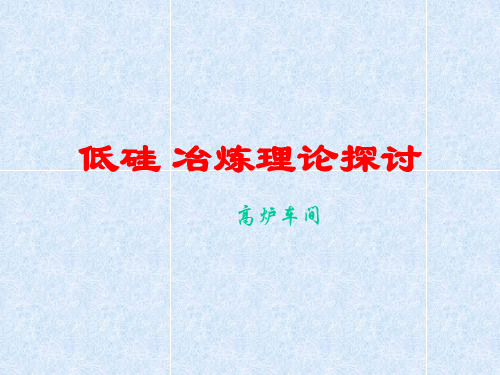
根据杭钢300m3级高炉低硅冶炼研究结果,铁 水中含[Si]在风口水平达到最高,故可以这样 来划分,在风口线水平以上,主要是硅的还 原,铁水中含[Si]不断升高的过程(增硅), 因此称为硅的还原区,铁水吸硅区又叫做增 硅区;在风口水平线以下,由于各种氧化作 用的结果,铁水含[Si]不断减少,形成一个脱 硅过程,因此可以叫做硅的氧化区,铁水脱 硅区又叫降硅区。该结论与日本各类高炉解 剖后的变化、分布规律相似,与前苏联高炉 取样研究的结果也是一致的,因此是可信的。
三、最佳硅含量的选择
• 铁水含硅不一定越低越好,要综合考虑 冶炼效果。特别是在炉况不正常、原料 条件大幅度波动或炉役后期,很难做到 维持铁水含[Si]不波动,同时考虑到原料 准备等诸方面付出的代价和操作人员精 神紧张程度,倒不如采取低硅冶炼与炉 外处理相结合更为合理。
我国精料水平近年来虽然有大幅度提高, 但原料条件差,炉容不大,顶压也较低,热 损失大,铁水温度也比日本低,要实现生铁 含硅量在0.25%左右困难太大,而且硅含量 在0.25%左右时经济效益也不一定就好。 就我国目前情况而言,铁水含[Si]普遍 偏高,就现阶段来看,铁水含[Si]可能在 0.3~0.4%左右为宜。
SiO是一种气体,随炉内煤气或炉渣中二氧化硅 的活度(αSi02)与温度(主要是风口前煤气理论燃 烧温度t理)的增加,都将是SiO量增加,硅的迁移量 增加,使Si的还原量增加,导致铁水吸硅量增加,使 高炉冶炼低硅生铁难度增加。后来的研究工作与生产 实践都充分表明这一论点是现代科学研究的进步,推 动了炼铁研究的生产的发展。
以上是高炉内硅的还原与氧化等的主 要反应式,如果以风口中心线(面) 为界,从以上反应特点可知,风口中 心线(面)以上为硅的还原区(吸硅、 增硅),风口中心线(面)以下为硅 的氧化区(脱硅、减硅)。以离子式 可以表达为: Si4++4e=Si(风口中心线以上)
降低转炉铁水单耗实践

降低转炉铁水单耗实践随着钢铁行业的不断发展,降低转炉铁水单耗已成为炼钢企业不断追求的目标之一。
通过实践和总结经验,在生产上积极采取措施,实现了较高的成果。
以下是详细的实践内容和成效。
一、改善炉况管理炉况管理是炼钢过程中非常重要的一环,直接影响着铁水的单耗和质量。
该企业在炉况管理方面采取了以下措施:1.加强炉冶设备日常巡检和维护,确保设备处于良好状态,减少补炉次数和熔炼时间,从而减少铁水单耗。
2.精细化的炉前配料管理,定期调整配料比例,提高了铁水品质的稳定性和一致性,同时减少了废钢的使用量。
3.绿色冶炼,通过技术创新来降低铁水单耗。
比如采用高温烟气回收技术,有效减少了能源的消耗和二氧化碳的排放。
经过长期实践,对于炉况管理的概念和要求得到了更加深入的理解,通过认真贯彻这些措施,成功地提高了铁水品质和钢铁生产效率,有效地降低了铁水单耗。
二、加强工艺流程管理工艺流程管理是企业做好铁水单耗降低的基础。
该企业在工艺流程管理方面采取了以下措施:1.减少炉前物料的事故掉落和水分变化,保障高、稳的加料状况,避免对炉冶环境和铁水单耗的不良影响。
2.加强工艺流程的清晰化,制定工艺流程操作规范,规范化操作人员的技能和整个工艺流程的机械化水平,以达到更好的铁水质量和更低的单耗。
3.加强在线监控,根据实时数据对工艺流程进行调整和控制。
同时,及时分析异常原因和问题,做好对应措施和工艺调试。
通过落实这些措施,企业成功增强了工艺流程的规范性和稳定性,提高了铁水质量,降低了单耗。
三、优化设备优化设备是为了降低能耗,提高效率,同时确保铁水质量达到最好。
该企业在优化设备方面采取以下措施:1.炉后脱烟系统,采用了一种新型的高效脱烟系统,有效地减少了废气排放和热能损失,同时也改善了铁水质量。
2.采用新型的合金制造技术,通过科技创新提高了合金制造技术水平,减少了合金添加量和能源消耗。
3.控制铁水入炉前温度,严格控制铁水温度,确保其进入炉子时达到最佳状态,从而最大化降低单耗。
降低转炉铁水单耗实践

降低转炉铁水单耗实践降低转炉铁水单耗是炼钢企业提高生产效率、降低生产成本的重要措施之一。
转炉铁水单耗是指在转炉炼钢过程中,每吨钢水所消耗的生铁量。
降低转炉铁水单耗,可以提高钢水产量,减少炼钢时间,降低能耗和物料消耗,从而降低生产成本。
本文将从炼铁原料、冶炼工艺、操作管理及设备维护等方面介绍降低转炉铁水单耗的一些实践方法。
一、优化炼铁原料的配比炼铁原料的质量和配比对转炉炼钢过程影响很大。
合理调配原料配比可以提高冶炼质量,降低转炉操作难度,减少生铁耗损。
在原料配比上,应注意以下几点:1、合理选择炼铁矿石。
炼铁矿石质量的好坏直接影响到冶炼质量。
应选择具有良好还原性和脱硫性能的矿石,同时避免太多的矽、锰等偏高的元素。
2、合理低价使用废钢。
废钢是一种低价的原料,可以替代部分生铁,降低铁水单耗。
在使用废钢时,应注意选择质量良好的废钢,并控制废钢的含碳量、含杂质等指标。
3、控制沸石石量。
沸石石是降低炼铁矿石粉消耗的一种常用方法。
过多的沸石石添加会增加炉渣量,影响炉渣的流动性和炉渣碱度,应根据具体情况合理控制。
二、优化炼钢工艺炼钢工艺对转炉铁水单耗影响较大。
通过优化炼钢工艺,可以降低工艺损失、提高炉渣性能,从而降低转炉铁水单耗。
1、加强预处理工艺。
在转炉炼钢过程之前,应对生铁进行预处理。
如高铝生铁要进行脱磷处理,高磷生铁要进行返磷等。
通过预处理可以降低后续冶炼过程中的耗能和原料消耗。
2、提高炉渣性能。
炉渣是转炉冶炼过程中的重要组成部分,直接影响到钢水质量和转炉工艺的稳定性。
合理调整炉渣配比,提高炉渣碱度,增加炉渣粘度,可以降低炉渣量,减少冶炼时间,降低铁水单耗。
3、控制炼钢渣后的利用。
炼钢渣是转炉冶炼过程中的副产物,可以回收利用。
通过对炼钢渣的精炼和调整,可以将其中的有价值物质回收,减少资源浪费。
三、优化操作管理优化操作管理是降低转炉铁水单耗的关键。
良好的操作管理能够提高生产效率,降低杂质含量,减少浪费。
1、做好轧后处理。
高硅铁水转炉吹炼实践_王金辉

生产实践高硅铁水转炉吹炼实践王金辉,王军,魏春新,王富亮,刘文飞(鞍钢股份有限公司鲅鱼圈钢铁分公司,辽宁营口115007)摘要:介绍了鞍钢股份有限公司鲅鱼圈钢铁分公司在铁水预处理工序对高硅铁水进行脱硅处理,在转炉工序使用高硅铁水进行转炉生产的实践。
实践表明,在铁水预处理工序采用脱硅剂进行脱硅能有效降低铁水硅含量,在转炉工序通过调整操作制度,可以采用高硅铁水入转炉冶炼,实现了转炉和高炉生产同步。
关键词:铁水脱硅;转炉冶炼;装入制度;供氧制度;造渣制度中图分类号:T F72 文献标识码:A 文章编号:1006-4613(2009)04-0048-03C o n v e r t e r B l o w i n g O p e r a t i o n f o r H i g h S i l i c o n H o t M e t a lWa n g J i n h u i,Wa n g J u n,We i C h u n x i n,Wa n g F u l i a n g,L i u We n f e i(B a y u q u a n I r o n a n d S t e e l B r a n c h C o m p a n y o f A n g a n g S t e e l C o.,L t d.,Y i n g k o u115007,L i a o n i n g,C h i n a)A b s t r a c t:T h i s a r t i c l e p r e s e n t s t h e d e s i l i c o n i z i n g t r e a t m e n t f o r h i g h s i l i c o n h o t m e t a l i n h o t m e t-a l p r e t r e a t i n g p r o c e s s a n d t h eb l o w i n g o p e r a t i o n f o r h i g h s i l ic o n h o t m e t a l i n c o n v e r t e r i nB a y u q u a n I-r o na n d S t e e l B r a n c h C o m p a n y o f A n g a n g S t e e l C o.,L t d..A c t u a l o p e r a t i o n s s h o wt h a t s i l i c o nc o n-t e n t i nh o t m e t a l c a nb e s u f f i c i e n t l y r e d u c e d b y u s i n g d e s i l i c o n i z a t i o na g e n t i nh o t m e t a l p r e t r e a t m e n tp r o c e s s a n d t h e n h o t m e t a l w i t h h i g hs i l i c o n c a nb e b l o w n d i r e c t l y i n c o n v e r t e r b y a d j u s t i n g t h e o p e r-a t i n g p r o c e d u r e s o t h a t s t e e l m a k i n g i n c o n v e r t e r a n d i r o n m a k i n gb y B Fc a n b e o p e r a t ed s y n c h r o n o u s-l y.K e yw o r d s:h o t m e t a l d e s i l i c o n i z a t i o n;c o n v e r t e r b l o w i n g;c h a r g e s y s t e m;o x y g e n b l o w i n g s y s-t e m;s l a g m a k i n g s y s t e m 鞍钢股份有限公司鲅鱼圈钢铁分公司地处辽宁营口,远离鞍钢本部基地,开工初期能源动力、铁水等都不能相互调剂,开工难度远远大于鞍钢本部改、扩建工程。
- 1、下载文档前请自行甄别文档内容的完整性,平台不提供额外的编辑、内容补充、找答案等附加服务。
- 2、"仅部分预览"的文档,不可在线预览部分如存在完整性等问题,可反馈申请退款(可完整预览的文档不适用该条件!)。
- 3、如文档侵犯您的权益,请联系客服反馈,我们会尽快为您处理(人工客服工作时间:9:00-18:30)。
太钢高炉降低铁水硅含量的实践1. 概况太钢不锈钢股份有限公司目前有三座高炉,炉容分别为3号炉1800m3、4号炉1650m3、5号炉4350m3。
1991年~1998年上半年,4号高炉第一代(1350m3)烧结矿配比只有55%~65%,大量使用了进口球团矿。
2002年底尖山铁矿提铁降硅工程投入使用,烧结矿品位提高到59%~60.3%,SiO2降低到4.5~5%,将烧结碱度提高到1.75~1.85%。
2003年一季度高炉入炉品位达到60.36%,之后高炉综合入炉品位长期保持在60%左右,渣铁比减少到270~290kg/t。
4号高炉第二代(1650m3)2000年11月扩容大修后投产,目前已到炉役后期。
5号高炉2006年10月份投产后利用系数、煤比和燃料比逐年进步,但铁水硅含量平均值高且稳定性差,2008年平均[Si]0.52%,σ[Si]达0.193%,个别月份高达0.247%。
3号高炉2007年7月扩容大修后投产,顺行状况相对最好,但使用的料种杂,成分、粒度及性能变化区间宽。
煤比提高到190kg/t以上时,干除尘灰碳含量增加,在高系数、高煤比、较低燃料比冶炼条件下,渣铁排放的负荷加重。
2008年下半年以来,钢铁产品出厂价格和使用的原燃料价格比以往发生了较大幅度的变化,炼铁系统降低生产成本提升EV A成为生产的主流。
许多降低铁水含硅量的措施与降成本提升EV A的方向是一致的,如多用烧结矿,少用球团矿,喷吹用煤多配烟煤,少配无烟煤。
为确保各高炉不同生产条件下,实现长周期炉况稳定顺行和低硅低硫高温铁水冶炼,太钢进行了较长时间的探索,并取得了一定的阶段成效。
2. 太钢高炉铁水硅含量长期偏高的原因分析2.1. 原燃料条件相对较差太钢三烧的烧结矿与宝钢比,同样碱度时转鼓强度低3%以上,酸性氧化球团矿SiO2含量比宝钢使用的酸性球团矿高0.9%。
2008年5号高炉综合含铁炉料的三元碱度(CaO+MgO)/SiO2平均为1.54,3号、4号高炉平均分别为1.52、1.58。
各高炉含铁炉料中峨口铁矿自产的酸性氧化球团配比较高,虽然综合入炉品位在60%左右,但软熔温度偏低,造成软融带位置高,软熔层厚,初渣过早形成,滴落行程长,铁水增硅过程长,初渣中FeO含量偏高,造成直接还原度高,炉缸热量相对不足。
过早软熔的球团粘附粉矿后堵塞煤气上升通道,造成高炉中部高温区透气性下降,是边缘局部气流过剩和产生管道的主要原因之一,而边缘局部气流过剩、管道及脱落发生时,渣铁热量急剧下滑,铁水含硫大幅度升高,处理不及时还引起炉芯死焦柱活性下降,炉底砖衬温度持续降低。
高炉日常操作中为防止炉温大幅度下滑造成炉凉,控制相对较高的铁水温度和硅含量,致使燃料比偏高。
2008年12月以前5号高炉球团矿配比20%~28%。
球团易滚动,开始软熔温度相对较低,布料偏析较大,混合矿在槽下至炉喉料面的运行过程中,球团矿容易在局部集中分布。
当5号高炉配比超过20%时,因偏析作用,边缘布料平台的宽度和各部位料层厚度波动范围宽,边缘局部球团分布多的区域气流稳定性不好,实际的料面形状和各部位料层厚度经常与布料矩阵设计不吻合,给布料控制造成很大的难度。
2.2. 炉身热负荷波动剧烈太钢以往没有4000m3级高炉操作经验,5号高炉在宝钢专家指导下开炉后,对气流调整进行了较长时间的摸索。
边缘和中心气流的分配,初期模仿宝钢高炉的W、Z值来调整布料。
一段时期尝试疏导边缘控制中心,逐渐加大矿批,矿批最大增加到138t,试图提高W值到0.7以上,将CCT 控制到750℃以下。
但炉身中上部热负荷剧烈波动的问题无法得到根除。
2008年有8个月煤比都在200kg/t以上运行,其中11月最高达到209kg/t,随着煤比提高,边缘气流有逐渐升高趋势,全炉热负荷与煤比同时升高。
2008年7月发生了一次较大的炉况失常,造成炉况失常的主要原因之一是,焦炭质量下降后,煤比未及时跟着往下退,炉芯焦粉量增加,透气透液性下降,中心气流通道受阻,边缘管道增加,导致频繁滑料和崩料,最终造成气流失常和炉凉。
恢复炉况期间控制了风量,炉况恢复后8~9月也控制煤比到190kg/t以下,但中心气流指数Z值仍然降低到6.5~7.5,炉底炭砖温度持续下降。
疏导边缘气流控制中心气流的操作模式,也使煤气利用率难以达到50%以上,热流比相对较低,与综合炉料软熔温度偏低叠加后,软融带根部位置靠上,软熔层较厚,块状带区域相对缩小,间接还原不足,直接还原度较高,燃料比长期在503kg/t以上运行。
在煤比200kg/t左右运行时,边缘局部经常出现气流过剩和管道,并伴随粘附和脱落发生,导致炉身热负荷大幅度波动,炉温波动剧烈,全炉热负荷经常在10000×10MJ/h~25000×10MJ/h之间波动,铜冷却板出水温度高峰时达到90℃左右,铁水硅含量由大于0.8%突然降低到0.1%左右。
铁水温度由1500℃,降低到1420℃。
2.3. 炉渣碱度偏低初渣出现位置较高2008年各高炉炉渣成分中MgO含量6.5%~8%,Al2O3含量12.8%~14.5%,二元碱度R2为1.10~1.15,三元碱度1.32~1.36。
终渣熔化温度比宝钢高炉渣低20~30℃,熔化性温度比宝钢高炉渣低50~60℃。
虽然应对炉温下行的能力较好,但也造成炉渣热焓低,炉缸热储备不足。
终渣二元和三元碱度控制偏低和熔化温度低,直接导致初渣出现位置较高,直接还原度高,炉缸渣铁热量不足,终渣的脱硫能力和稳定性较差。
2.4. 渣铁排放对炉况冲击较大2009年1月份以前,5号高炉使用的炮泥抗渣性不好,排放过程中铁口孔道容易越流越大,炉渣排出速度超过8t/min后,INBA冲渣能力达到饱和,必须被迫堵口,否则会造成冲渣喷溅,由此造成铁口先关后开现象,引起高炉憋风,炉温升高。
3. 降低铁水含硅量的措施及效果3.1. 降硅措施⑴提高烧结矿产量,增加高炉配料中烧结矿配比。
从2008年12月开始将旧烧碱度由1.7下调到1.65,逐步增加3号高炉和4号高炉的烧结矿配比,减少球团矿配比。
2009年2月份开始增加5号高炉烧结矿配比,各高炉烧结矿配比变化见图1。
⑵优化炉料结构,在提高烧结矿产量的基础上,提高烧结矿和块矿配比,减少球团矿配比。
高炉增加烧结矿和块矿配比,减少球团矿配比后,综合炉料的软熔性能改善。
经检测每减少1%球团比例,综合矿软化开始温度T10升高约2℃,T40-T10缩小约1.5℃。
2009年上半年全厂平均球团比例减少约4%,综合炉料软化开始温度平均提高约8℃。
软融带位置下移,软熔层变薄,扩大了块状带高度,间接还原比率提高,直接还原度降低,滴落路径缩短,气流稳定性改善,热负荷波动范围大幅度缩小。
减少球团矿比例4%,综合炉料软化开始温度虽然只提高约8℃,但随着球团入炉数量减少,滚动和偏析减少,球团在局部集中分布的概率减少。
实际上在高炉内对稳定软熔带和煤气流的作用,要远远大于检测的综合炉料平均软化开始温度升高值。
⑶采取控制边缘疏导中心的高热流比操作模式。
2009年2月份以后,5号炉球团配比逐步减少后,球团入炉后滚动和偏析减少,边缘布料平台宽度和各部位料层厚度稳定性好转,加宽边缘布料平台宽度的操作得以顺利实现。
气流调整以适当控制边缘、疏导中心为主,寻找合适的矿石批重。
矿石批重基本稳定在121~125t,W值控制到0.30~0.6,Z值9.0~12,CCT在700~800℃。
下部富氧率增大到4.5~5.5%,炉腹煤气量由8500~9500m3/min逐步提高到9800~10500m3/min,适当扩大送风面积,风速提高到270~280m/s,炉况顺行较好,热负荷波动区间明显缩小,炉顶平均温度下降约10~15℃。
6月中下旬煤比恢复到200kg/t以上后,热负荷波动区间又有增大趋势,但炉况稳定性仍比2008年好一些。
太钢5号高炉布料实践表明,高炉布料模式,必须与使用的炉料物理性能、粒度分布、堆角、冶金性能及煤气量和喷煤比相匹配。
在改善炉料物理和冶金性能的基础上,才有布料优化的物质基础,否则只能努力保顺行。
现阶段的炉料条件能够调整的范围还较小,只能在较小范围内减少峨口球团矿配比,增大烧结矿和块矿配比。
2010年660m2烧结机投产后,烧结矿总产能扩大,可以缓解目前三烧的生产压力。
届时可以减慢机速,以提高转鼓强度和改善冶金性能为主来组织生产。
5号高炉使用的烧结矿质量还有提高空间。
今后还需要进一步改善5号高炉使用的球团矿的冶金性能。
建议开发和使用MgO熔剂性球团矿,改善球团矿的高温软熔和还原性能,为5号高炉长期保持200kg/t以上煤比和冶炼含硅0.35%的低硅铁,创造精料条件。
⑷调整炮泥配方,改善抗渣性。
2009年2月在5号高炉开始使用新配方炮泥。
新配方炮泥增大了氮化硅配比,抗渣性改善。
出铁期间孔径变化很小,渣铁排出流速均匀,能够将炉渣排出速度控制到5~7.6t/min,基本消除了排渣速度超出INBA冲渣能力而被迫堵口的情况。
3月以后将5号高炉原配方炮泥用于3号高炉,也使3号高炉的铁口稳定性改善,渣铁排放均衡性提高。
⑸优化高炉渣型。
增加烧结矿配比的过程中,由烧结矿带入的MgO数量增加,炉渣MgO 含量也由6%~8%左右提高到8%~9.5%,二元碱度也小幅提高,三元碱度由1.32~1.36提高到1.35~1.39,炉渣粘度降低,也有利于低硅铁冶炼。
⑹细化高炉操作参数管理。
①针对以往气流波动较大的现象,制定了出铁温度的上下限和炉温偏离控制目标时的增减热调整制度,力争将炉温波动范围缩小,避免炉温下行破坏炉芯死焦柱的活性及炉温上行影响顺行;②将自产和外购焦炭质量划分成6~9种等级,结合各高炉外购焦配比,制定了各种焦炭质量状态的喷煤比上限。
焦炭质量变化时及时调整喷煤量和焦炭负荷,确保炉芯活性和料柱透气性在控制范围;③装料制度和送风制度依据原燃料质量状况及时调整,确保气流稳定;④对铁口深度、孔径、来渣时间、出铁时间、排出速度、出铁炉数等进行了细化规定。
⑺增大烟煤配比,降低混合煤灰分,磨煤新系统(5号高炉全部使用磨煤新系统煤粉,3号高炉35%左右使用新系统煤粉)烟煤配比逐步由30%提高到40%,混合煤灰分由10.2%降低到9.5%。
煤粉燃烧率提高,入炉SiO2负荷减少,减少了风口区SiO2的气化量,对降低铁水含硅量有一定效果。
3.2. 效果通过增加烧结矿配比、调整炉料分布、改进炮泥质量、优化渣型、增大烟煤配比等措施的应用,高炉稳定性好转,各项指标都有较大改善。
①气流稳定性好转,高炉炉身热负荷波动范围缩小,5号高炉炉体热负荷波动范围缩小,波动区间由12000×10MJ/h缩小到4000×10MJ/h以内。
②铁水硅含量稳定性提高,平均含硅量降低。