铁水硅含量的确定
铁水温度和硅含量的关系

铁水温度和硅含量的关系
铁水的温度和硅含量之间存在一定的关系,这种关系通常体现在铁水的凝固过程中。
在铸造工艺中,硅对铁水的凝固温度有着显著的影响。
一般来说,随着铁水中硅含量的增加,铁水的凝固温度会降低。
这是因为硅的存在会导致铁水的凝固点下降,使得铁水更容易凝固成型。
硅对铁水凝固温度的影响可以通过下面的两个方面解释:
1. 减小凝固点:硅的加入可以形成固溶体,使得铁水的凝固点降低。
这意味着相同温度下,含有更多硅的铁水会比含有较少硅的铁水更容易凝固。
2. 形成石墨:在铁水中,硅还有助于形成石墨,而石墨有利于降低铁水的凝固温度,提高铁水的流动性。
因此,一般情况下,当铁水中的硅含量增加时,铁水的凝固温度会相应降低。
铁水温度和硅含量之间的关系受多种因素影响,包括化学反应、冶炼条件等。
通过深入研究和分析这些因素,可以更准确地预测和控制铁水中的硅含量。
高炉铁水硅含量自组织预测中的模式量化

高炉铁水硅含量自组织预测中的模式量化
高炉铁水的硅含量是决定其品质的关键指标,因此掌握并准确预测高
炉铁水中硅含量变化趋势,对企业的生产过程有着不可忽视的作用。
传统的预测方法大多基于统计分析,其实践效果一般,此时引入模式
量化技术,可以有效提高预测精度。
模式量化可以有效获取复杂问题的解决方案,在高炉铁水硅含量预测
中也有着很好的应用。
基于供热方式、炉料品种和炉内特殊因素的不同,高炉硅含量发生的变化是复杂的,尤其是在高温通风过程中,硅
含量随气流动态变化较快,这要求我们把时变参数不断量化,并把量
化参数赋给高炉铁水量化模型,形成硅含量预测模型,然后通过数据
计算机模拟,就可以有效地预测高炉铁水中硅含量变化趋势。
模式量化是一种先进的方法,但也存在一定的困难,比如随着炉况参数、工艺参数变化而变化的模型参数传递,模型参数求解的及时性以
及模型的精度等问题,影响着模式量化的收敛性。
因此,我们在进行
模式量化自组织预测时,应该更加注重参数的采集和数据分析,在数
据量足够大的基础上,更好地优化模型参数,以确保预测的准确性。
总之,模式量化自组织预测技术在高炉铁水硅含量的预测中的应用,
能够有效地解决传统预测方法的缺陷,提升预测精度,提高生产效率,有利于企业的可持续发展。
炉前铁水碳硅含量的测定

炉前铁水碳硅含量的测定一般来说,在碳硅分析仪实际测定钢铁合金时,碳、硫的连续测定中,难点是硫。
其3个原因。
原因如下:一、铁中硫的含量比碳低得多,含量越低,测定越困难;二、钢铁中的硫化物(MnS、FeS)比相应的碳化物的燃烧反应比相应的碳化物要困难得多,三、比较燃烧后的产物,二氧化硫有有副反应发生,在一定的条件下易转化成三氧化硫,而二氧化碳无此现象。
由于这些原因硫的测定比碳困难得多,而且测定的准确度也有效期。
这种情况后来我们工程师经过多方认证在电弧炉使用添加剂,添加剂在电弧炉中的作用除助熔剂外还有引弧、稳燃、改性,供热等性能,一般添加剂是锡粒、硅粉、三氧化钼的混合物。
更多碳硅分析仪连续测定钢铁合金时的注意事项的资料,可咨询南京诺金高速分析仪器厂技术部。
碳硅分析仪产品特点:1、碳硅分析仪测量结果数显直读,测量时间为2-3分钟,便于铸造工程师现场配料。
2、仪器测温范围:C%:2.8%-4.2%,Si%:0.9%-3.0%,CE%:3.2%-4.83%。
3、仪器操作简单,免维护,一般的炉工即可现场使用。
4、仪器可测量孕育前或孕育后的铁水,这是国内仪器无法做到的,这项技术填补了国内空白。
5、仪器能自动控制重要冶金参数。
它对灰白凝固铸铁自动进行测量,免去了人工操作。
可以连接大型远程显示器、信号灯、计算机、打印机。
碳硅分析仪测量原理:通过微处理器进行温度曲线的采集,通过铁水结晶法来测量计算碳硅成份及铁水品质,通过改进的求值方法进行工作,能自动控制重要的冶金参数,弥补“光谱"难以测准非金属元素(C、Si)之不足,以及常规分析仪器不能满足炉前快速分析的时间要求,满足铸造生产的质量控制要求。
南京诺金高速分析仪器厂2018年9月20日。
铁水一级品评判标准

铁水一级品评判标准
铁水是指在炼钢过程中,由高炉中的铁矿石还原而来的液态铁水。
铁水的质量直接影响到钢的质量和生产成本,因此铁水的评判非常重要。
以下是铁水一级品的评判标准:
1. 化学成分:铁水的主要成分是铁和碳,一级品的铁水应该保
持一定的化学成分。
其中,碳含量应该在2.5-4.0%之间,硅含量应
该在0.8-1.5%之间,磷含量应该在0.03%以下,硫含量应该在0.02%以下。
2. 氧化物含量:一级品的铁水应该保持较低的氧化物含量。
氧
化物会影响铁水的流动性和稳定性,同时也会影响钢的质量。
因此,一级品的铁水氧化物含量应该在1%以下。
3. 温度:一级品的铁水应该在适宜的温度范围内。
过高的温度
会增加钢的成分含量,同时也会增加钢的生产成本。
因此,一级品的铁水温度应该在1400℃左右。
4. 放流性:一级品的铁水应该有良好的放流性,即铁水应该能
够在炉子中流动自如,不产生结块或流动不畅的情况。
5. 外观:一级品的铁水应该没有杂质、气泡、夹渣等缺陷,表
面应该平整光滑,颜色均匀,没有变形或裂缝等缺陷。
以上是评判铁水一级品的主要标准,进行严格的铁水评判可以保证钢的质量和生产成本。
- 1 -。
(采用)高炉铁水硅含量
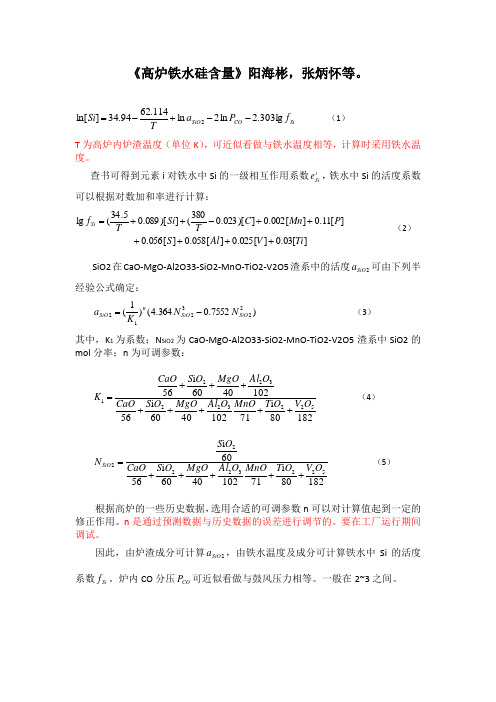
《高炉铁水硅含量》阳海彬,张炳怀等。
Si CO SiO f P a TSi lg 303.2ln 2ln 114.6294.34]ln[2--+-= (1)T 为高炉内炉渣温度(单位K ),可近似看做与铁水温度相等,计算时采用铁水温度。
查书可得到元素i 对铁水中Si 的一级相互作用系数iSi e ,铁水中Si 的活度系数可以根据对数加和率进行计算:][03.0][025.0][058.0][056.0][11.0][002.0])[023.0380(])[089.05.34(lg Ti V Al S P Mn C TSi Tf Si ++++++-++= (2)SiO2在CaO-MgO-Al2O33-SiO2-MnO-TiO2-V2O5渣系中的活度2SiO a 可由下列半经验公式确定:)7552.0364.4()1(223212SiO SiO nSiO N N K a -= (3)其中,K 1为系数;N SiO2为CaO-MgO-Al2O33-SiO2-MnO-TiO2-V2O5渣系中SiO2的mol 分率;n 为可调参数:18280i 711024060i 561024060i 565223223221O V O T MnO O Al MgO O S CaOO Al MgOO S CaOK ++++++++=(4)18280i 711024060i 5660i 52232222O V O T MnO O Al MgO O S CaO O S N SiO +++++=(5)根据高炉的一些历史数据,选用合适的可调参数n 可以对计算值起到一定的修正作用。
n 是通过预测数据与历史数据的误差进行调节的。
要在工厂运行期间调试。
因此,由炉渣成分可计算2SiO a ,由铁水温度及成分可计算铁水中Si 的活度系数Si f 。
炉内CO 分压CO P 可近似看做与鼓风压力相等。
一般在2~3之间。
高炉铁水硅含量的预测模型
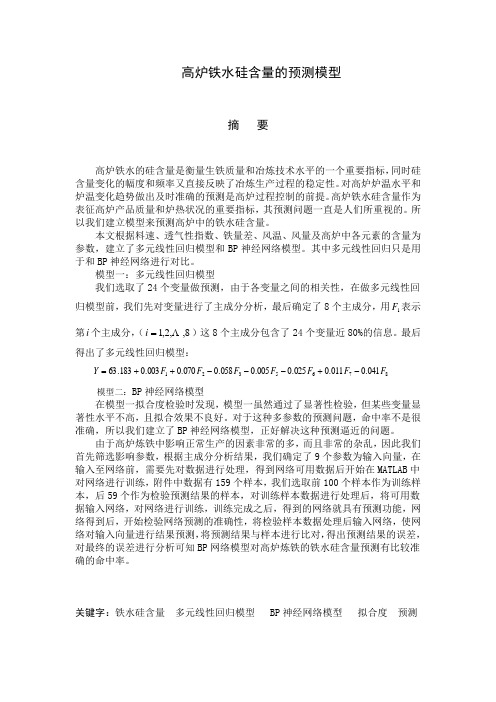
高炉铁水硅含量的预测模型摘 要高炉铁水的硅含量是衡量生铁质量和冶炼技术水平的一个重要指标,同时硅含量变化的幅度和频率又直接反映了冶炼生产过程的稳定性。
对高炉炉温水平和炉温变化趋势做出及时准确的预测是高炉过程控制的前提。
高炉铁水硅含量作为表征高炉产品质量和炉热状况的重要指标,其预测问题一直是人们所重视的。
所以我们建立模型来预测高炉中的铁水硅含量。
本文根据料速、透气性指数、铁量差、风温、风量及高炉中各元素的含量为参数,建立了多元线性回归模型和BP 神经网络模型。
其中多元线性回归只是用于和BP 神经网络进行对比。
模型一:多元线性回归模型我们选取了24个变量做预测,由于各变量之间的相关性,在做多元线性回归模型前,我们先对变量进行了主成分分析,最后确定了8个主成分,用i F 表示第i 个主成分,(8,,2,1 =i )这8个主成分包含了24个变量近80%的信息。
最后得出了多元线性回归模型:8765321041.0011.0025.0005.0058.0070.0003.0183.63F F F F F F F Y -+---++=模型二:BP 神经网络模型在模型一拟合度检验时发现,模型一虽然通过了显著性检验,但某些变量显著性水平不高,且拟合效果不良好。
对于这种多参数的预测问题,命中率不是很准确,所以我们建立了BP 神经网络模型,正好解决这种预测逼近的问题。
由于高炉炼铁中影响正常生产的因素非常的多,而且非常的杂乱,因此我们首先筛选影响参数,根据主成分分析结果,我们确定了9个参数为输入向量,在输入至网络前,需要先对数据进行处理,得到网络可用数据后开始在MATLAB 中对网络进行训练,附件中数据有159个样本,我们选取前100个样本作为训练样本,后59个作为检验预测结果的样本,对训练样本数据进行处理后,将可用数据输入网络,对网络进行训练,训练完成之后,得到的网络就具有预测功能,网络得到后,开始检验网络预测的准确性,将检验样本数据处理后输入网络,使网络对输入向量进行结果预测,将预测结果与样本进行比对,得出预测结果的误差,对最终的误差进行分析可知BP 网络模型对高炉炼铁的铁水硅含量预测有比较准确的命中率。
铁水预处理中的硅元素的流动
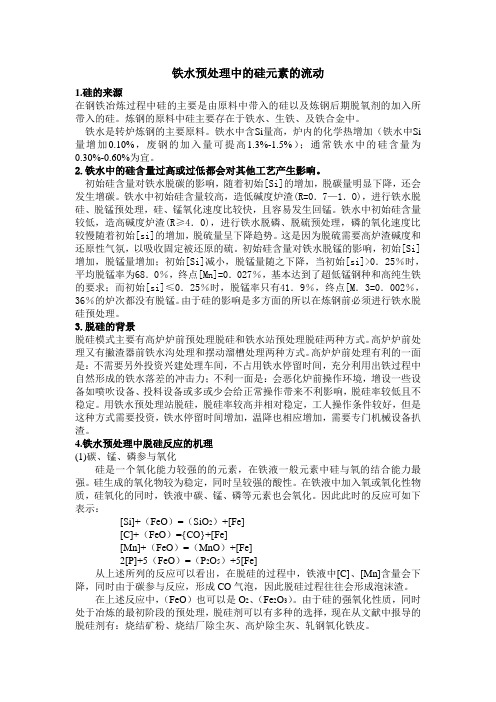
铁水预处理中的硅元素的流动1.硅的来源在钢铁冶炼过程中硅的主要是由原料中带入的硅以及炼钢后期脱氧剂的加入所带入的硅。
炼钢的原料中硅主要存在于铁水、生铁、及铁合金中。
铁水是转炉炼钢的主要原料。
铁水中含Si量高,炉内的化学热增加(铁水中Si 量增加0.10%,废钢的加入量可提高1.3%-1.5%);通常铁水中的硅含量为0.30%-0.60%为宜。
2.铁水中的硅含量过高或过低都会对其他工艺产生影响。
初始硅含量对铁水脱碳的影响,随着初始[Si]的增加,脱碳量明显下降,还会发生增碳。
铁水中初始硅含量较高,造低碱度炉渣(R=0.7—1.O),进行铁水脱硅、脱锰预处理,硅、锰氧化速度比较快,且容易发生回锰。
铁水中初始硅含量较低,造高碱度炉渣(R≥4.0),进行铁水脱磷、脱硫预处理,磷的氧化速度比较慢随着初始[si]的增加,脱硫量呈下降趋势。
这是因为脱硫需要高炉渣碱度和还原性气氛,以吸收固定被还原的硫。
初始硅含量对铁水脱锰的影响,初始[Si]增加,脱锰量增加;初始[Si]减小,脱锰量随之下降,当初始[si]>0.25%时,平均脱锰率为68.0%,终点[Mn]=0.027%,基本达到了超低锰钢种和高纯生铁的要求;而初始[si]≤0.25%时,脱锰率只有41.9%,终点[M.3=0.002%,36%的炉次都没有脱锰。
由于硅的影响是多方面的所以在炼钢前必须进行铁水脱硅预处理。
3.脱硅的背景脱硅模式主要有高炉炉前预处理脱硅和铁水站预处理脱硅两种方式。
高炉炉前处理又有撇渣器前铁水沟处理和摆动溜槽处理两种方式。
高炉炉前处理有利的一面是:不需要另外投资兴建处理车间,不占用铁水停留时间,充分利用出铁过程中自然形成的铁水落差的冲击力;不利一面是:会恶化炉前操作环境,增设一些设备如喷吹设备、投料设备或多或少会给正常操作带来不利影响,脱硅率较低且不稳定。
用铁水预处理站脱硅,脱硅率较高并相对稳定,工人操作条件较好,但是这种方式需要投资,铁水停留时间增加,温降也相应增加,需要专门机械设备扒渣。
入炉铁水对硅含量的要求

入炉铁水对硅含量的要求取决于具体的应用和钢铁生产流程。
以下是一些常见的硅含量要求:
1.高炉炼铁:在高炉炼铁过程中,通常要控制铁水的硅含量。
硅作为一种主要的杂质会影
响铁水的质量和后续钢铁生产工艺。
硅含量的要求通常在0.5%至2%之间,具体数值根据所需的钢种和工艺要求而定。
2.建筑钢、工程机械用钢:这些钢材通常要求硅含量较低,一般在0.15%至0.3%之间。
这
是因为较低的硅含量可以提高钢材的塑性、韧性和焊接性能。
3.不锈钢:不锈钢对硅的含量要求相对较高,通常在0.3%至1.0%之间。
适当的硅含量可
以提高不锈钢的耐蚀性和抗氧化性能。
需要注意的是,硅含量的要求可以根据具体的产品规范、市场需求以及铁水调整等因素而有所变化。
因此,在实际生产中,硅含量的控制需要根据具体情况进行调整和监测。