铝合金铸件的铸造工艺分析
铝合金的铸造方法
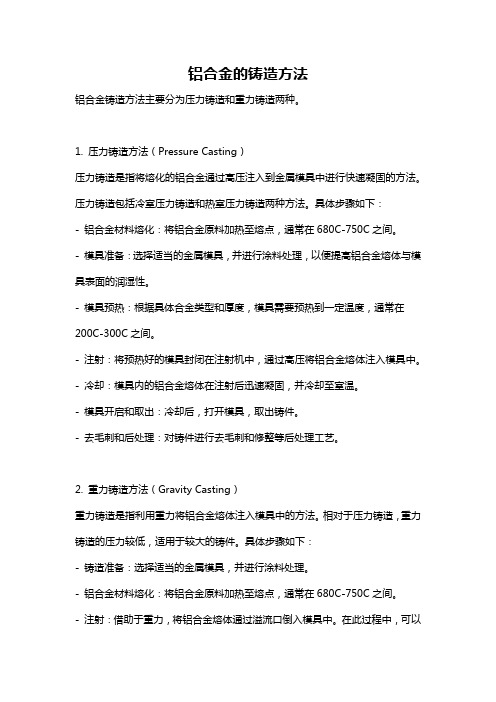
铝合金的铸造方法铝合金铸造方法主要分为压力铸造和重力铸造两种。
1. 压力铸造方法(Pressure Casting)压力铸造是指将熔化的铝合金通过高压注入到金属模具中进行快速凝固的方法。
压力铸造包括冷室压力铸造和热室压力铸造两种方法。
具体步骤如下:- 铝合金材料熔化:将铝合金原料加热至熔点,通常在680C-750C之间。
- 模具准备:选择适当的金属模具,并进行涂料处理,以便提高铝合金熔体与模具表面的润湿性。
- 模具预热:根据具体合金类型和厚度,模具需要预热到一定温度,通常在200C-300C之间。
- 注射:将预热好的模具封闭在注射机中,通过高压将铝合金熔体注入模具中。
- 冷却:模具内的铝合金熔体在注射后迅速凝固,并冷却至室温。
- 模具开启和取出:冷却后,打开模具,取出铸件。
- 去毛刺和后处理:对铸件进行去毛刺和修整等后处理工艺。
2. 重力铸造方法(Gravity Casting)重力铸造是指利用重力将铝合金熔体注入模具中的方法。
相对于压力铸造,重力铸造的压力较低,适用于较大的铸件。
具体步骤如下:- 铸造准备:选择适当的金属模具,并进行涂料处理。
- 铝合金材料熔化:将铝合金原料加热至熔点,通常在680C-750C之间。
- 注射:借助于重力,将铝合金熔体通过溢流口倒入模具中。
在此过程中,可以通过控制溢流口的大小和位置来控制铸件的形状和尺寸。
- 冷却:待铝合金熔体在模具中凝固,冷却至室温。
- 模具开启和取出:冷却后,打开模具,取出铸件。
- 去毛刺和后处理:对铸件进行去毛刺和修整等后处理工艺。
值得注意的是,上述方法仅列举了最常用和基本的铝合金铸造方法,实际生产中还有其他特殊的铸造方法,如砂芯铸造、低压铸造等。
具体方法的选择会根据铸件形状、尺寸和要求等因素进行灵活确定。
铝合金零件压铸关键技术的分析 林满湛
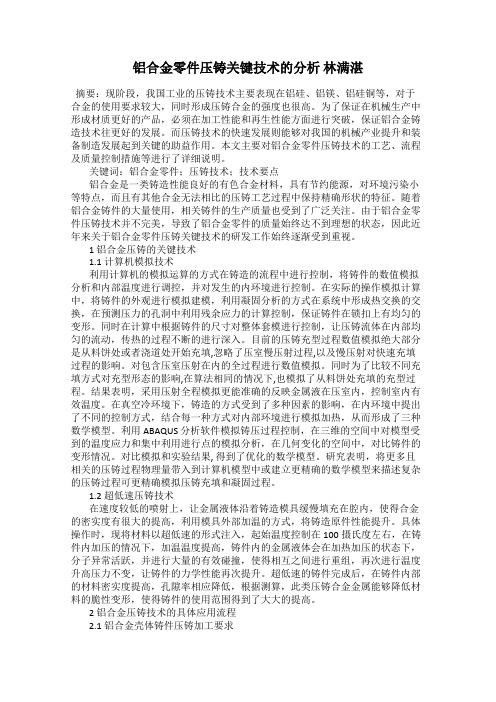
铝合金零件压铸关键技术的分析林满湛摘要:现阶段,我国工业的压铸技术主要表现在铝硅、铝镁、铝硅铜等,对于合金的使用要求较大,同时形成压铸合金的强度也很高。
为了保证在机械生产中形成材质更好的产品,必须在加工性能和再生性能方面进行突破,保证铝合金铸造技术往更好的发展。
而压铸技术的快速发展则能够对我国的机械产业提升和装备制造发展起到关键的助益作用。
本文主要对铝合金零件压铸技术的工艺、流程及质量控制措施等进行了详细说明。
关键词:铝合金零件;压铸技术;技术要点铝合金是一类铸造性能良好的有色合金材料,具有节约能源,对环境污染小等特点,而且有其他合金无法相比的压铸工艺过程中保持精确形状的特征。
随着铝合金铸件的大量使用,相关铸件的生产质量也受到了广泛关注。
由于铝合金零件压铸技术并不完美,导致了铝合金零件的质量始终达不到理想的状态,因此近年来关于铝合金零件压铸关键技术的研发工作始终逐渐受到重视。
1 铝合金压铸的关键技术1.1 计算机模拟技术利用计算机的模拟运算的方式在铸造的流程中进行控制,将铸件的数值模拟分析和内部温度进行调控,并对发生的内环境进行控制。
在实际的操作模拟计算中,将铸件的外观进行模拟建模,利用凝固分析的方式在系统中形成热交换的交换,在预测压力的孔洞中利用残余应力的计算控制,保证铸件在锁扣上有均匀的变形。
同时在计算中根据铸件的尺寸对整体套模进行控制,让压铸流体在内部均匀的流动,传热的过程不断的进行深入。
目前的压铸充型过程数值模拟绝大部分是从料饼处或者浇道处开始充填,忽略了压室慢压射过程,以及慢压射对快速充填过程的影响。
对包含压室压射在内的全过程进行数值模拟。
同时为了比较不同充填方式对充型形态的影响,在算法相同的情况下,也模拟了从料饼处充填的充型过程。
结果表明,采用压射全程模拟更能准确的反映金属液在压室内,控制室内有效温度。
在真空冷环境下,铸造的方式受到了多种因素的影响,在内环境中提出了不同的控制方式,结合每一种方式对内部环境进行模拟加热,从而形成了三种数学模型。
铸造铝合金的熔炼工艺
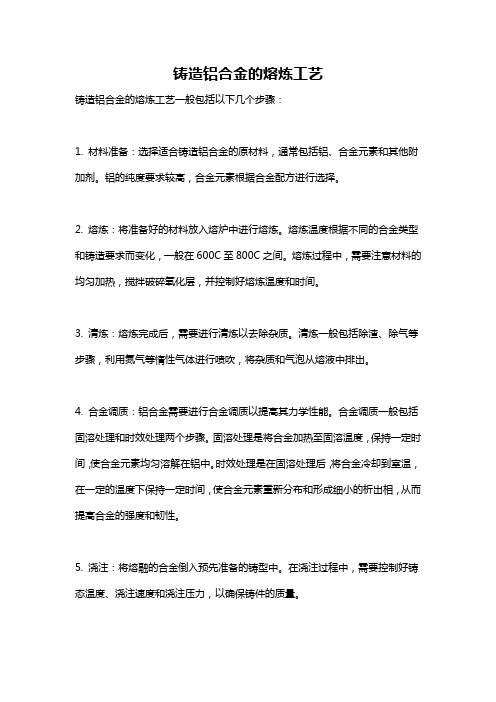
铸造铝合金的熔炼工艺
铸造铝合金的熔炼工艺一般包括以下几个步骤:
1. 材料准备:选择适合铸造铝合金的原材料,通常包括铝、合金元素和其他附加剂。
铝的纯度要求较高,合金元素根据合金配方进行选择。
2. 熔炼:将准备好的材料放入熔炉中进行熔炼。
熔炼温度根据不同的合金类型和铸造要求而变化,一般在600C至800C之间。
熔炼过程中,需要注意材料的均匀加热,搅拌破碎氧化层,并控制好熔炼温度和时间。
3. 清炼:熔炼完成后,需要进行清炼以去除杂质。
清炼一般包括除渣、除气等步骤,利用氮气等惰性气体进行喷吹,将杂质和气泡从熔液中排出。
4. 合金调质:铝合金需要进行合金调质以提高其力学性能。
合金调质一般包括固溶处理和时效处理两个步骤。
固溶处理是将合金加热至固溶温度,保持一定时间,使合金元素均匀溶解在铝中。
时效处理是在固溶处理后,将合金冷却到室温,在一定的温度下保持一定时间,使合金元素重新分布和形成细小的析出相,从而提高合金的强度和韧性。
5. 浇注:将熔融的合金倒入预先准备的铸型中。
在浇注过程中,需要控制好铸态温度、浇注速度和浇注压力,以确保铸件的质量。
6. 冷却:浇注后,铸件需要进行冷却。
冷却速度会影响铸件的晶粒大小和组织结构,因此需要根据不同的合金性能要求,选择合适的冷却方式。
7. 修磨和表面处理:冷却后的铸件需要进行去毛刺、修磨和表面处理等工艺,以提高铸件的表面质量和精度。
以上是铸造铝合金的一般熔炼工艺流程,具体操作步骤和参数设置会根据不同的铝合金材料和铸造要求而有所差异。
铸铝件工艺流程
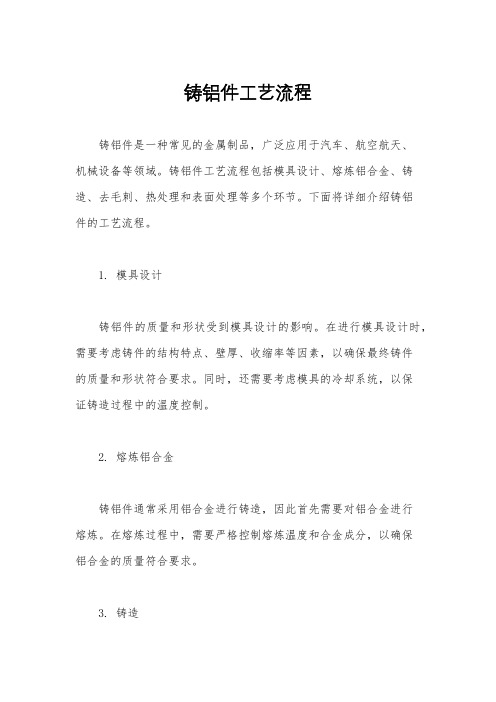
铸铝件工艺流程铸铝件是一种常见的金属制品,广泛应用于汽车、航空航天、机械设备等领域。
铸铝件工艺流程包括模具设计、熔炼铝合金、铸造、去毛刺、热处理和表面处理等多个环节。
下面将详细介绍铸铝件的工艺流程。
1. 模具设计铸铝件的质量和形状受到模具设计的影响。
在进行模具设计时,需要考虑铸件的结构特点、壁厚、收缩率等因素,以确保最终铸件的质量和形状符合要求。
同时,还需要考虑模具的冷却系统,以保证铸造过程中的温度控制。
2. 熔炼铝合金铸铝件通常采用铝合金进行铸造,因此首先需要对铝合金进行熔炼。
在熔炼过程中,需要严格控制熔炼温度和合金成分,以确保铝合金的质量符合要求。
3. 铸造铸造是铸铝件工艺流程中的关键环节。
在铸造过程中,需要将熔化的铝合金倒入预先设计好的模具中,然后等待铸件冷却凝固。
在此过程中,需要注意控制浇注速度、温度和压力,以避免产生气孔、夹杂等缺陷。
4. 去毛刺铸造完成后,铸件表面通常会留有一些毛刺和氧化皮。
因此,需要对铸件进行去毛刺处理,以提高表面质量和加工性能。
5. 热处理铸铝件通常需要进行热处理,以消除残余应力、改善组织结构和提高硬度。
常见的热处理工艺包括时效处理、固溶处理和淬火处理等。
6. 表面处理最后,铸铝件还需要进行表面处理,以提高其耐腐蚀性和装饰性。
常见的表面处理工艺包括阳极氧化、喷涂、电镀等。
总结铸铝件工艺流程包括模具设计、熔炼铝合金、铸造、去毛刺、热处理和表面处理等多个环节。
每个环节都对最终铸铝件的质量和性能有着重要影响。
因此,在生产过程中需要严格控制每个环节,以确保铸铝件的质量符合要求。
铝合金铸件的铸造工艺分析

铝合金铸件的铸造工艺分析摘要:本文作者结合工作经验,对铸造工艺设计的几个控制要点、铸造工艺设计以及零件的浇注系统设计进行重点分析。
以期参考交流。
关键词:铝合金;筒体;铸造;中图分类号:ts912+.3文献标识码: a 文章编号:1、铸件的基本信息筒体铸件最大轮廓尺寸为准900 mm×850 mm,最大壁厚137 mm,铸件净重约650 kg,属于典型厚壁件,铸件表面全部加工,铸件结构如图1。
筒体铸件虽然我单位生产很多,但此铸件结构与常年生产的筒类铸件结构不同,不同之处在于:在准900 mm的平面上高出准280 mm×150 mm的圆柱体,正是由于高出的圆柱体给工艺设计和生产操作,带来很大的麻烦。
图1 筒体铸件结构图2、铸造工艺设计的几个控制要点2.1 铸件的补缩对于壁厚较大的铝合金铸件,在铸造工艺设计过程中合金的补缩是十分重要的,如果补缩的作用不够,铸件的最后凝固处易产生缩松,甚至可能产生集中缩孔,造成铸件报废。
在筒体铸件中,φ900 mm处壁厚137 mm (不包括加工量),φ450 mm内腔壁厚125 mm (不包括加工量),对于此类厚壁铸件,因浇注中型腔热容量大,凝固收缩比较缓慢,后期要求冒口提供的金属液补缩较大,故必须对整体采用强有力的补缩措施,以避免产生缩孔、缩松等铸造缺陷。
2.2 铸件的冷却因铸件使用过程中对气密性要求很高,故加大厚大铸件的凝固速度,以获得较细的金相组织,使其铸件表面有一层较细的致密层,是提高其气密性和力学性能重要技术措施。
故对于筒体铸件的内腔厚大部位,必须采用冷铁加强冷却。
2.3 准280 mm×150 mm圆柱体的成型及尺寸控制如果选择调整铸件壁厚形成准280 mm×150 mm的圆柱体,虽然工艺设计简单,但不可避免将产生以下缺点:1)为了适应铝合金顺序凝固原则,在准900 mm平面上必须增加很大的工艺补贴及加工量,给后续机加工带来很大麻烦。
铝铸件工艺
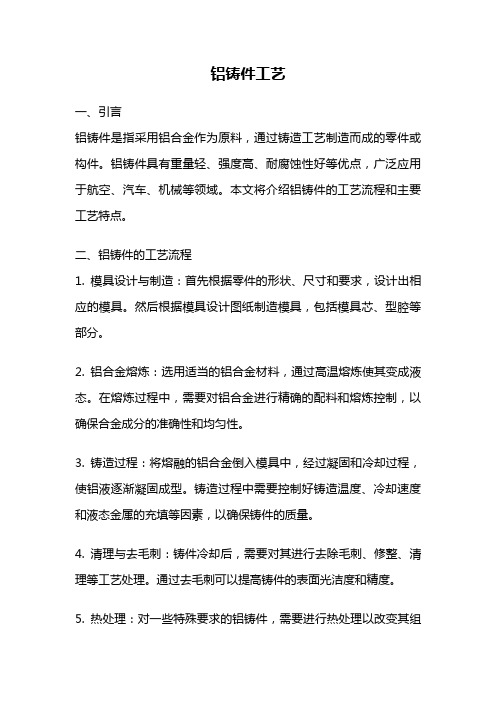
铝铸件工艺一、引言铝铸件是指采用铝合金作为原料,通过铸造工艺制造而成的零件或构件。
铝铸件具有重量轻、强度高、耐腐蚀性好等优点,广泛应用于航空、汽车、机械等领域。
本文将介绍铝铸件的工艺流程和主要工艺特点。
二、铝铸件的工艺流程1. 模具设计与制造:首先根据零件的形状、尺寸和要求,设计出相应的模具。
然后根据模具设计图纸制造模具,包括模具芯、型腔等部分。
2. 铝合金熔炼:选用适当的铝合金材料,通过高温熔炼使其变成液态。
在熔炼过程中,需要对铝合金进行精确的配料和熔炼控制,以确保合金成分的准确性和均匀性。
3. 铸造过程:将熔融的铝合金倒入模具中,经过凝固和冷却过程,使铝液逐渐凝固成型。
铸造过程中需要控制好铸造温度、冷却速度和液态金属的充填等因素,以确保铸件的质量。
4. 清理与去毛刺:铸件冷却后,需要对其进行去除毛刺、修整、清理等工艺处理。
通过去毛刺可以提高铸件的表面光洁度和精度。
5. 热处理:对一些特殊要求的铝铸件,需要进行热处理以改变其组织和性能。
常见的热处理方法包括时效处理、固溶处理等。
6. 机械加工:对于需要进行精密加工的铝铸件,如钻孔、铣削、车削等,需要进行相应的机械加工工艺。
7. 表面处理:根据产品要求和应用领域的不同,可以对铝铸件进行表面处理,如喷涂、阳极氧化、电镀等,以提高其防腐蚀性和美观度。
8. 检测与质量控制:通过各种检测方法对铝铸件进行质量检验,包括外观检查、尺寸测量、力学性能测试等。
确保铝铸件符合设计要求和使用要求。
三、铝铸件工艺的特点1. 模具成本低:与其他铸造工艺相比,铝铸件的模具成本较低,制造周期较短,能够快速满足不同产品的需求。
2. 产品形状复杂:铝铸件工艺适用于各种复杂形状的产品制造,可以生产出具有复杂内部结构和外观形状的零件。
3. 高材料利用率:铝铸件工艺具有较高的材料利用率,废料少,可以有效降低成本。
4. 材料性能优良:铝铸件具有优良的物理性能和机械性能,强度高、刚性好、耐腐蚀性强。
铝合金真空压铸技术

铝合金真空压铸技术铝合金真空压铸技术是一种高效、精密的铝合金铸造工艺,通过在真空环境中进行压铸,可以有效避免铸件表面氧化、气孔等缺陷,提高铸件的质量和性能。
以下是关于铝合金真空压铸技术的详细介绍,包括其工艺流程、优势、应用领域等方面。
一、铝合金真空压铸技术概述铝合金真空压铸技术是一种在真空环境下进行的高压铸造工艺。
其主要步骤包括:模具封闭,抽真空,充填铝液,施加高压,保压定型,冷却固化,开模取件。
整个过程在真空条件下进行,以确保铸件表面无气孔、氧化等缺陷,同时通过高压实现铝液的充分充填,提高铸件的密度和机械性能。
二、铝合金真空压铸技术的工艺流程模具设计和制造:根据产品的形状和尺寸,设计并制造合适的压铸模具,确保模具具有足够的强度和耐磨性。
模具封闭:将设计好的模具封闭,形成一个密封的腔室,以准备进行真空铸造。
真空抽气:在模腔封闭后,通过真空泵将模腔内的空气抽出,创造真空环境。
真空状态有助于减少铝液中气体的溶解,防止气孔的生成。
铝液充填:在真空状态下,将预热至一定温度的铝液注入模腔,确保铝液在模腔中均匀充填。
施加高压:在铝液充填后,施加高压,使铝液充分充填模腔,提高铸件的密度和机械性能。
保压定型:在高压作用下,保持一段时间,使铝液定型成型。
冷却固化:在定型后,通过冷却系统将模腔内的铝液迅速冷却,固化成为铝合金铸件。
开模取件:冷却固化后,打开模具,取出成型的铝合金铸件,进行后续的处理和加工。
三、铝合金真空压铸技术的优势减少氧化和气孔:在真空环境下进行铸造可以有效减少铸件表面的氧化,同时通过真空抽气减少气体的溶解,避免气孔的生成,提高铸件的表面质量。
提高密度和机械性能:高压充填和保压定型能够使铝液充分充填模腔,提高铝合金铸件的密度和机械性能。
精密铸造:铝合金真空压铸技术可以实现更精密的铸造,适用于复杂形状、高精度要求的铝合金零件生产。
高生产效率:由于真空压铸工艺的高压和高速度,可以实现较短的充填时间和较快的冷却速度,提高生产效率。
铝合金重力浇铸与高压铸造
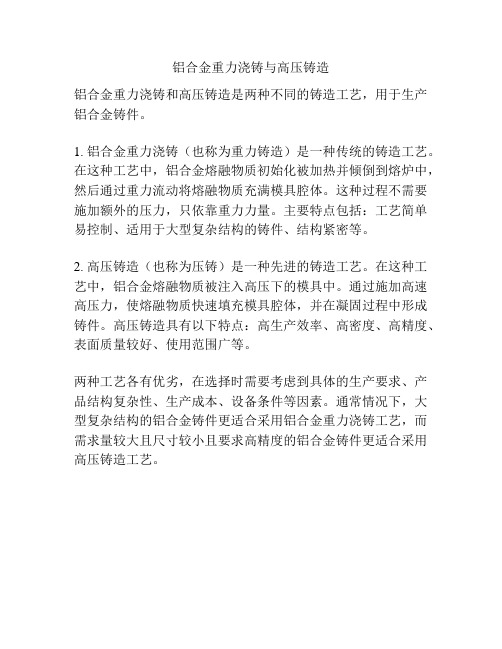
铝合金重力浇铸与高压铸造
铝合金重力浇铸和高压铸造是两种不同的铸造工艺,用于生产铝合金铸件。
1. 铝合金重力浇铸(也称为重力铸造)是一种传统的铸造工艺。
在这种工艺中,铝合金熔融物质初始化被加热并倾倒到熔炉中,然后通过重力流动将熔融物质充满模具腔体。
这种过程不需要施加额外的压力,只依靠重力力量。
主要特点包括:工艺简单易控制、适用于大型复杂结构的铸件、结构紧密等。
2. 高压铸造(也称为压铸)是一种先进的铸造工艺。
在这种工艺中,铝合金熔融物质被注入高压下的模具中。
通过施加高速高压力,使熔融物质快速填充模具腔体,并在凝固过程中形成铸件。
高压铸造具有以下特点:高生产效率、高密度、高精度、表面质量较好、使用范围广等。
两种工艺各有优劣,在选择时需要考虑到具体的生产要求、产品结构复杂性、生产成本、设备条件等因素。
通常情况下,大型复杂结构的铝合金铸件更适合采用铝合金重力浇铸工艺,而需求量较大且尺寸较小且要求高精度的铝合金铸件更适合采用高压铸造工艺。
- 1、下载文档前请自行甄别文档内容的完整性,平台不提供额外的编辑、内容补充、找答案等附加服务。
- 2、"仅部分预览"的文档,不可在线预览部分如存在完整性等问题,可反馈申请退款(可完整预览的文档不适用该条件!)。
- 3、如文档侵犯您的权益,请联系客服反馈,我们会尽快为您处理(人工客服工作时间:9:00-18:30)。
矿产资源开发利用方案编写内容要求及审查大纲
矿产资源开发利用方案编写内容要求及《矿产资源开发利用方案》审查大纲一、概述
㈠矿区位置、隶属关系和企业性质。
如为改扩建矿山, 应说明矿山现状、
特点及存在的主要问题。
㈡编制依据
(1简述项目前期工作进展情况及与有关方面对项目的意向性协议情况。
(2 列出开发利用方案编制所依据的主要基础性资料的名称。
如经储量管理部门认定的矿区地质勘探报告、选矿试验报告、加工利用试验报告、工程地质初评资料、矿区水文资料和供水资料等。
对改、扩建矿山应有生产实际资料, 如矿山总平面现状图、矿床开拓系统图、采场现状图和主要采选设备清单等。
二、矿产品需求现状和预测
㈠该矿产在国内需求情况和市场供应情况
1、矿产品现状及加工利用趋向。
2、国内近、远期的需求量及主要销向预测。
㈡产品价格分析
1、国内矿产品价格现状。
2、矿产品价格稳定性及变化趋势。
三、矿产资源概况
㈠矿区总体概况
1、矿区总体规划情况。
2、矿区矿产资源概况。
3、该设计与矿区总体开发的关系。
㈡该设计项目的资源概况
1、矿床地质及构造特征。
2、矿床开采技术条件及水文地质条件。