钢铁料消耗计算
我的钢铁成本计算公式

我的钢铁成本计算公式
1、T=1.6X+0.5Y+Z-S其中:T为生铁成本X为铁矿石价格,Y为焦炭价格,Z为添加剂与高炉折旧总费用(300-350元/吨),S为水渣、废气回收的节约费用(100元/吨)。
更加详细的计算公式:1.55吨铁矿石+焦炭340kg+喷吹煤粉130kg+烧结矿煤焦50kg+加工费(人工、折旧、财务成本)
2、生铁→钢水(400-500元/吨,其中50-60度电和耐材消耗)→小钢坯(200元/吨,铁合金、浇铸、辅助材料)
3、小钢坯→螺纹(300元/吨退火、电耗、轧制三项费用)
4、小钢坯→热轧(500-600元/吨,退火、回火、电耗、轧制)
5、热轧→酸洗(100元/吨)→轧硬(400元/吨,包括轧辊损耗,400是大钢厂指标)
6、轧硬→退火(200元/吨)250罩退贵100
7、轧硬→(退火50元/吨加热+锌层成本,按照50克锌层计算每平方米的)
8、镀锌→彩涂(按每平米计算成本)。
粗钢生产工序能耗计算

粗钢生产工序能耗计算引言能耗计算是工业生产过程中的一个重要环节,通过对不同工序的能耗进行准确计算,可以帮助企业找出能耗较高的环节,进而采取相应的节能措施,提高生产效率,降低成本。
本文将针对粗钢生产过程中的不同工序进行能耗计算,以帮助企业更好地控制和优化能源消耗。
粗钢生产工序简介粗钢是指通过冶炼过程制得的未经初步加工的钢材,具有较高的含碳量和较低的纯度。
粗钢生产工序一般包括:原料准备、熔炼冶炼、钢水处理、连铸、初轧和粗轧等环节。
原料准备能耗计算原料准备环节主要包括铁矿石的破碎、磨矿、混合和配料等过程。
根据实际产量和生产数据,可以计算出原料准备环节的能耗。
原料准备能耗 = 原料准备消耗能量 / 产量熔炼冶炼能耗计算熔炼冶炼环节是将铁矿石和其他辅助材料经高温熔炼,得到钢水的过程。
熔炼冶炼能耗可以通过以下公式计算:熔炼冶炼能耗 = 燃料消耗能量 + 电能消耗能量 + 冷却水消耗能量 / 产量钢水处理能耗计算钢水处理环节是将熔炼冶炼出来的钢水经过脱硫、脱氧等处理,提高钢水的纯度和质量。
钢水处理能耗可以通过以下公式计算:钢水处理能耗 = 电能消耗能量 + 冷却水消耗能量 / 产量连铸能耗计算连铸是将钢水浇铸成连续铸坯的过程,连铸能耗可以通过以下公式计算:连铸能耗 = 电能消耗能量 + 冷却水消耗能量 + 氧气消耗能量 / 产量初轧能耗计算初轧环节是将连铸坯经过初轧机轧制成规定尺寸的厚板,并进行质量控制。
初轧能耗可以通过以下公式计算:初轧能耗 = 电能消耗能量 + 冷却水消耗能量 / 产量粗轧能耗计算粗轧环节是将初轧后的厚板不断轧制,降低其厚度,最终得到要求尺寸的薄板。
粗轧能耗可以通过以下公式计算:粗轧能耗 = 电能消耗能量 + 冷却水消耗能量 / 产量结论通过对粗钢生产工序的能耗计算,可以帮助企业找出能源消耗较高的环节,并针对性地采取节能措施,提高能源利用效率,降低生产成本。
在实际应用中,还应考虑到设备能效、操作参数等因素对能耗的影响,以实现更精确和全面的能耗计算和优化。
6钢铁企业吨钢可比能耗计算方法

规模以上工业统计报表制度 —1—6.钢铁企业吨钢可比能耗计算方法工序 部位工序单位能耗 吨标准煤/吨产品(1)钢比或铁比 吨产品/吨钢(铁)(2)可比能耗的组成 吨标准煤/吨钢 (1)×(2)备 注焦化Aa =(烧结、球团、炼铁)耗焦量/全铁折合产量A ·aa b c 为折算铁比系数,只适用于能耗指标计算烧结 Bb =烧结矿消耗量/全铁折合产量B ·b球团 Cc =球团矿消耗量/全铁折合产量C ·c炼铁D =炼铁工序能耗/全铁折合产量D 1=炼铁工序能耗/全铁产量E = A ·a+ B ·b+ C ·c+ De :吨钢耗生铁量 E ·eD :炼铁工序折合全铁单位能耗;D 1:炼铁工序全铁单位能耗;E :企业吨铁单位能耗;转炉 电炉 其他炉 连铸F 1 F 2 F 3 F 4f 1转炉钢率 f 2电炉钢率 f 3其他炉钢率 f 4连铸钢率 (f 1+ f 2+ f 3=1)F= F 1·f 1+ F 2·f 2 + F 3·f 3+ F 4·f 4连铸能耗属炼钢工序开坯G :初轧单位能耗g ·[1— (连铸坯量+直接成材耗锭量)/ (初轧耗锭量+连铸坯量+直接成材耗锭量)]M=初轧开坯累计耗能量/(初轧耗锭量+连铸坯量+直接成材耗锭量)1.式中连铸坯量系企业直接成材消耗的连铸坯量;2.在特钢企业用钢锭成材时,生产的锻钢件(材)可按直接成材处理;3.M=G ·g ·[1— (连铸坯量+直接成材耗锭量)/ (初轧耗锭量+连铸坯量+直接成材耗锭量)]g.初轧钢坯成坯率轧材H=轧材耗能量/企业最终钢材产量h: 企业由钢到材的综合成材率 H ·h机车I=运输能耗量/企业钢产量燃气加工与输送J=燃气加工与输送耗量/企业钢产量 企业能源亏损K=企业能源亏损量/企业钢产量 企业吨钢可比能耗L=E ·e+F+M+ H ·h +I+J+K。
关于50吨转炉钢铁料消耗测算及影响因素分析

攀成钢50吨转炉钢铁料消耗测算及影响因素分析杨文明刘志军易良刚攀钢集团成都钢钒有限公司攀成钢50吨转炉2008年钢铁料消耗为1133.91kg/t,随后逐年降低,至2010年降低至1114.539kg/t,而在2011年1-8月钢铁料消耗达到1118.819kg/t。
通过对2011年1-8月钢铁料测算与2010年同期比较,掌握钢铁料各工序消耗状况,分析原因,并提出改进措施。
0 前言钢铁料消耗是炼钢厂的重要经济技术指标,其成本约占炼钢成本的80%左右,降低其消耗是炼钢厂降低成本、提高竞争力的主要手段之一,也是操作水平和综合管理水平的体现。
从某种意义上说炼钢企业降低了钢铁消耗量就意味着增加了企业收入,因此,炼钢企业不断优化钢铁料消耗指标,对提高企业经济效益和产品竞争力具有十分重要的意义。
1、钢铁料消耗的定义按照中国钢铁工业协会制定的《中国钢铁工业生产统计指标体系》的规定[1],钢铁料=生铁量+废钢铁量,钢铁料消耗=钢铁料量÷合格钢产量。
废钢铁包括各种废钢、废铁等。
在计算废钢铁消耗指标时, 除轻薄废钢、渣钢、优质钢丝、各类铁、钢屑按规定的折合标准进行折合外, 其它废钢均按实物量计算。
计算钢铁料消耗应按每投一次料就算一次消耗。
1.1 对钢铁料消耗定义的理解《中国钢铁工业生产统计指标体系》的规定,钢铁料=生铁量+废钢铁量,钢铁料消耗=钢铁料量÷合格钢产量。
根据该原则,钢铁料消耗中的几个问题需要做出如下解释。
1)合金吸收量是否应该扣除在生产过程中几乎每炉钢都要加入合金(如硅铁、锰铁等),加入的合金是没有在钢铁料量中扣除的。
而一些钢铁企业(如酒钢)是将合金吸收量进行了扣除,这样钢铁料消耗就降低。
根据“规定”我们认为加入的合金不应该计入钢铁料消耗。
2)中间包余水及切头切尾量在回炉时是否计入“废钢铁料量”。
50吨转炉主要生产高品质的管坯钢,连浇炉数少,中间包余水及切头切尾量大,我们认为这部分废钢属于自产废钢,不应计入消耗。
炼钢工-计算题

6.出钢量为150t ,钢水中氧含量700ppm ,计算钢水全脱氧需要加多少铝?(小数点后保留一位有效数字,Al 的相对原子质量是27,氧的相对原子质量是16) (1)反应式是2Al+3[O]=(Al2O3)(2)钢水含0.07%(700ppm)[O],150t 中总氧含量: 150×1000×0.07%=105(Kg)(3)计算铝加入量,设铝的加入量为x : 2Al+3[O]=(Al2O3)105163272⨯=⨯x(2×27)/x=(3×16)/105 x=(2×27×105)/(3×16) x=118.1(Kg) 答:钢水全脱氧需要加入铝118.1Kg 7.冶炼某钢种,其成分是C0.12~0.18%、Mn1.0~1.5%、Si0.2~0.6%。
采用Mn-Fe 合金化,其含Mn68.5%,Mn 的收得率85%,冶炼终点钢水残锰0.15%。
出钢量为120吨。
求该炉钢Mn-Fe 合金的加入量是多少? 答案:Mn-Fe 合金加入量 答:Mn-Fe 合金加入量是2267Kg 。
10.设渣量为装入量的10%,炉衬侵蚀量为装入量的1%,炉衬MgO 量为40%;铁水成分Si =0.6%、P =0.09%、S=0.04%; 石灰成分:CaO=88%、MgO=1.7%、SiO2=0.4%; 白云石成分:CaO =40%、MgO =35%、SiO2=3%; 终渣要求(MgO)=10%,碱度为4.0。
求需要加入的石灰与白云石量。
答案:1)白云石应加入量: W 白=10%×10%×1000/35%=28.6kg/t 2)炉衬侵蚀进入渣中MgO 折算白云石量: W 衬=1%×40%×1000/35%=11.4kg/t 3)石灰带入MgO 折算白云石量: W 石=2.14×0.6%×3.5×1000×1.7%/[35%×(88%-4×0.4%)]=2.5kg/t 4)实际白云石加入量: W 白’=28.6-11.4-2.5=14.7kg/t 5)白云石带入渣中CaO 折算石灰量: 14.7×(40%-4×3%)/(88%-4×0.4%)=4.8kg/t 6)实际应加石灰量: W 石’=2.14×0.6%×4×1000/(88%-4×0.4%)-4.8=54.6kg/t 答:实际加入的白云石量为14.7kg/t 、石灰量54.6kg/t 。
影响钢铁料消耗的主要因素分析

影响钢铁料消耗的主要因素分析1前言钢铁料消耗指标是炼钢厂重要的经济技术指标,一般占生产成本的80~85%,对炼钢厂的成本有重要的意义。
钢铁料消耗国家规定的统计标准:转炉钢铁料消耗(kg/t钢)=[铁水+生铁+废钢铁量(kg)]/转炉合格产出量(t),其中:生铁包括高炉铁块、还原铁;废钢铁包括各种废钢、废铁等。
(行业惯例目前都以合格铸坯量代替转炉合格产出量)以下对影响钢铁料的主要因素进行梳理,由于涉及的因素较多,以定性分析为主。
2影响钢铁料消耗的主要因素2.1铁水预处理铁水脱硫处理的钢铁料损失主要发生在处理前后的扒渣带铁和处理过程中的喷溅及铁水倒运铁损失等。
扒渣带铁与铁水自带的高炉渣和脱硫渣量成正比,其中脱硫渣量的大小与采用的脱硫剂有关。
如复合喷吹脱硫工艺,脱硫剂消耗为4 kg/t铁,渣量为4.64kg/t铁,扒渣铁损为2.09 kg/t铁。
2.2转炉冶炼转炉的钢铁料损失主要由冶炼的烟尘、钢渣及喷溅等因素引起,占本工序损失量的98%,回炉、钢水出不尽等占一部分。
烟尘损失:通常情况下占转炉工序损失量的55%,其中碳氧化损耗约占44%、金属烧损约占11%,这部分损失量主要取决于钢铁料中碳含量。
钢渣中金属损失量:通常情况下占损失量的37 %,其中硅、锰氧化损失约占7.5%,铁氧化损失约占22.5%,渣中钢粒约占7%。
喷溅损失:通常情况下约占6%。
回炉、钢水出不尽等:通常情况下约占2%。
转炉冶炼是一个氧化过程,减少氧化损失是减少钢铁料损失的关键。
氧化损失中,一类为必要损失,无法避免,如碳、硅、锰等元素氧化,以获得化学热,这部分损失为必要损失。
另一类氧化损失是可以避免或减少的,如转炉后吹。
2.3 连铸连铸的钢铁料损失主要包括氧化铁皮、切割损失、切头切尾、中包注余、大包注余、漏钢、废品、清理损失等。
其中中包注余、切头切尾、切割损失等因素,占连铸工序钢铁料损失量的80%。
中包注余:通常约占连铸工序损失量的40%。
炼钢部分各种计算公式汇总
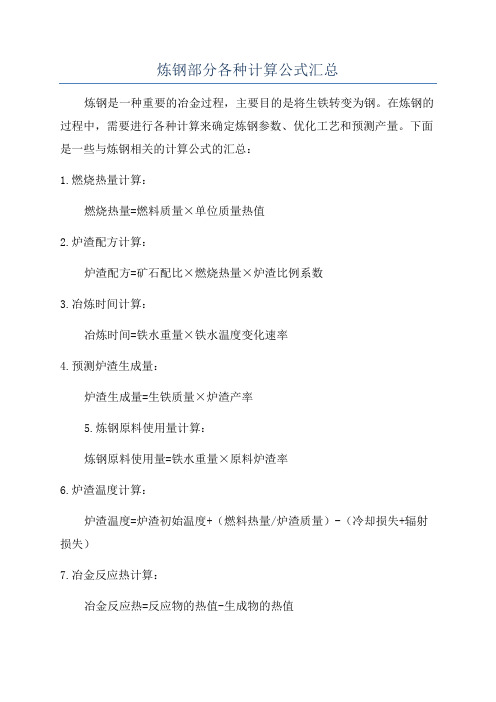
炼钢部分各种计算公式汇总炼钢是一种重要的冶金过程,主要目的是将生铁转变为钢。
在炼钢的过程中,需要进行各种计算来确定炼钢参数、优化工艺和预测产量。
下面是一些与炼钢相关的计算公式的汇总:1.燃烧热量计算:燃烧热量=燃料质量×单位质量热值2.炉渣配方计算:炉渣配方=矿石配比×燃烧热量×炉渣比例系数3.冶炼时间计算:冶炼时间=铁水重量×铁水温度变化速率4.预测炉渣生成量:炉渣生成量=生铁质量×炉渣产率5.炼钢原料使用量计算:炼钢原料使用量=铁水重量×原料炉渣率6.炉渣温度计算:炉渣温度=炉渣初始温度+(燃料热量/炉渣质量)-(冷却损失+辐射损失)7.冶金反应热计算:冶金反应热=反应物的热值-生成物的热值8.炉温控制计算:炉温控制=炉温目标值-炉温测量值9.耗氧量计算:耗氧量=氧气流量×氧浓度×燃烧公式系数10.炉渣替代率计算:炉渣替代率=炉渣替代量/炉渣生成量11.冷却水量计算:冷却水量=冷却热量/剪切热12.制氧气量计算:制氧气量=铁水含氧量×铁水重量×(氧气纯度/100)13.吹氧流量计算:吹氧流量=制氧气量/铁水供氧时间14.坩埚温度计算:坩埚温度=铁水温度+气氛温度15.炉水质量计算:炉水质量=炉水比例×矿石质量以上是一些与炼钢相关的计算公式的汇总。
当然,实际的炼钢过程非常复杂,还需要考虑其他因素如温度、压力、流量等等。
这些公式只是提供了一些基本的计算方法,实际应用中还需要根据具体情况进行适当的调整和修正。
吨钢成本计算公式是什么
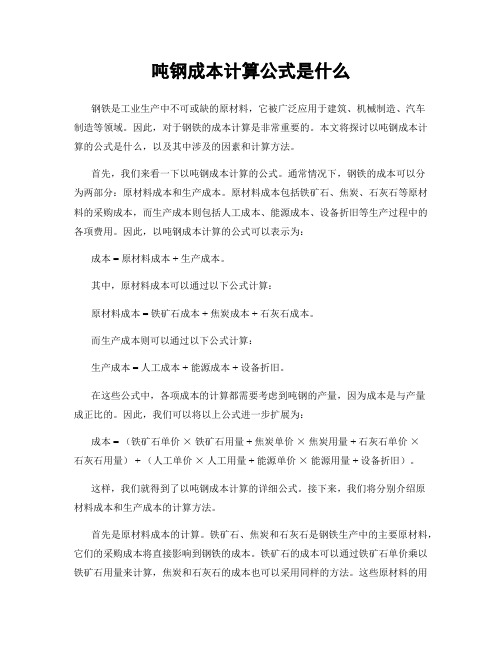
吨钢成本计算公式是什么钢铁是工业生产中不可或缺的原材料,它被广泛应用于建筑、机械制造、汽车制造等领域。
因此,对于钢铁的成本计算是非常重要的。
本文将探讨以吨钢成本计算的公式是什么,以及其中涉及的因素和计算方法。
首先,我们来看一下以吨钢成本计算的公式。
通常情况下,钢铁的成本可以分为两部分:原材料成本和生产成本。
原材料成本包括铁矿石、焦炭、石灰石等原材料的采购成本,而生产成本则包括人工成本、能源成本、设备折旧等生产过程中的各项费用。
因此,以吨钢成本计算的公式可以表示为:成本 = 原材料成本 + 生产成本。
其中,原材料成本可以通过以下公式计算:原材料成本 = 铁矿石成本 + 焦炭成本 + 石灰石成本。
而生产成本则可以通过以下公式计算:生产成本 = 人工成本 + 能源成本 + 设备折旧。
在这些公式中,各项成本的计算都需要考虑到吨钢的产量,因为成本是与产量成正比的。
因此,我们可以将以上公式进一步扩展为:成本 = (铁矿石单价×铁矿石用量 + 焦炭单价×焦炭用量 + 石灰石单价×石灰石用量) + (人工单价×人工用量 + 能源单价×能源用量 + 设备折旧)。
这样,我们就得到了以吨钢成本计算的详细公式。
接下来,我们将分别介绍原材料成本和生产成本的计算方法。
首先是原材料成本的计算。
铁矿石、焦炭和石灰石是钢铁生产中的主要原材料,它们的采购成本将直接影响到钢铁的成本。
铁矿石的成本可以通过铁矿石单价乘以铁矿石用量来计算,焦炭和石灰石的成本也可以采用同样的方法。
这些原材料的用量可以通过生产工艺和设备参数来确定,通常可以根据生产计划和实际生产情况进行调整。
其次是生产成本的计算。
人工成本、能源成本和设备折旧是生产过程中不可避免的费用,它们的计算方法也比较简单。
人工成本可以通过人工单价乘以人工用量来计算,能源成本和设备折旧也可以采用类似的方法。
这些成本的用量可以通过生产过程中的能耗数据和设备运行情况来确定,通常可以通过生产管理系统进行记录和分析。
- 1、下载文档前请自行甄别文档内容的完整性,平台不提供额外的编辑、内容补充、找答案等附加服务。
- 2、"仅部分预览"的文档,不可在线预览部分如存在完整性等问题,可反馈申请退款(可完整预览的文档不适用该条件!)。
- 3、如文档侵犯您的权益,请联系客服反馈,我们会尽快为您处理(人工客服工作时间:9:00-18:30)。
钢铁料耗计算知识
钢铁料耗是炼钢厂重要的经济技术指标,一般占转炉生产成本的80~85%,降低钢铁料耗成为一个炼钢厂降成本的主要手段,钢铁料耗指标即体现了炼钢厂技术水平,也体现了管理水平,对炼钢厂的成本有重要的意义。
一、钢铁料耗的统计方式。
1.理论基础
任何指标都要统一标准才好对比,钢铁料耗的理论基础是物质不灭定律,推广到具体的钢铁料耗方面为物料平衡,投入量与产出量之间的关系,为了统计方便,国家专门制订了钢铁料耗统计的相关规定。
2.国家规定的统计标准:
转炉钢铁料消耗(kg/t钢)=[生铁+废钢铁量(kg)]/转炉(电炉)合格产出量(t)
其中:生铁包括冷生铁、高炉铁水、还原铁;废钢铁包括各种废钢、废铁等。
凡分别管理、按类配用下列废钢铁的,在计算废钢铁消耗指标时,可按下列统一的折合标准折合计算:a. 轻薄料废钢,包括锈蚀的薄钢板以及相当于锈蚀薄板的其他轻薄废钢,按实物量×60%计算,其加工压块按实物量×60%计算;关于轻薄废钢,国家标准GB/T4223-1996中有明确规定;
b. 渣钢是指从炉渣中回收的带渣子的钢,按实物×70% 计算;经过砸碎加工(基本上去掉杂质)的渣钢,按实物量×90%计算;
c. 优质钢丝(即过去所称“钢丝”)、钢丝绳、普通钢钢丝(即过去所称“铁丝”)、铁屑以及钢锭扒皮车屑和机械加工的废钢屑(加工压块在内),按实物量×60%计算;
d. 钢坯切头切尾、汤道、中注管钢、桶底钢、冻包钢、重废钢等均按实物计算。
3某些厂家的统计方式
国家标准规定钢铁料消耗,是入炉料计算,实际企业计算时,炼钢厂内部回收的废钢都被扣除了.
二.钢铁料耗构成
1.投入的铁料量
由于考虑理论与实际投入的铁量之间的差异,实际生铁、废钢铁量,但是冶炼过程加入的含铁物质如烧结矿、生矿、合金等含铁物质对钢铁料耗的降低是有贡献,贡献的大小是可以计算的;
所以在条件允许下,可以多消化烧结矿、生矿等含铁物质,根据资料有关厂家吨钢消化生矿达到60kg,对钢铁料耗贡献大.
2. 生产的合格钢坯:
依据规定,参与计算的是转炉(电炉)生产合格钢坯量;
三.钢铁料耗影响:
1. 内部(工艺技术、管理等)影响因素
(1)转炉炉前吹损
转炉炉前吹损包括生铁和废钢的化学损失,烟尘损失,渣中氧化损失,渣中铁珠损失,喷溅损失,依据理论和首钢、武钢、马钢等公司转炉生产的实践经验转炉炉前吹损约为7.38~11.72%。
与炉料和操作水平有关.
(2)转炉厂内部管理因素
理论上的是认为各种称量系统都是准确的,实际情况并不是这样,这对钢铁料耗数值影响也很大。
如进厂铁水实际(真值)60吨,但过磅59吨,所以要加强这方面的管理工作;
渣钢回收的回收管理工作特别重要,由于转炉冶炼操作的控制波动较大。
渣中含有大块和小块钢以及铁颗粒的回收对降低钢铁料耗指标有重要的影响,影响多大体现了管理水平的高
低。
转炉厂钢水的流转工序管理,钢包的剩余钢水量、中包包底钢水量以及连浇炉数,连铸坯的定尺长度及割缝;生产事故和质量事故的金属损失等;
有些是转炉厂可以控制的如钢包的剩余钢水量、中包包底钢水量以及连浇炉数、连铸坯的割缝等,如连铸坯的定尺长度和钢种不能控制的,公司计划是什么就执行什么。
转炉厂钢坯出厂钢坯未计重量、支数的。
特别是出厂钢坯,若出厂时没有记数如10炉钢,有2支没记数,每支1.65吨
这对钢铁料耗的数值影响是很大的!
2.外部因素
(1)统计因素
根据国家规定的统计标准,a类、b类、c类在实践中比较难以区分,所以在选择折算系数时难以确定,对转炉的钢铁料耗也有较大的影响。
如一车60吨的小锣帽废钢,折算系数该怎么计。
(2)外部的称量系统因素
理论上称量系统是准确的,但在实际工作中不完全是这样的;若进入转炉的生铁、废钢铁量和出转炉的合格钢坯的称量系统出现系统误差,对钢铁料耗影响确实较大。
(3)原料因素
受高炉生产影响,铁水质量波动大如含Si 0.5%的铁水与Si 1.6%的铁水对转炉的钢铁料耗的影响是显著的;生铁块与废钢影响也是如此。
若有的钢厂铁水富余,全铁水炼钢,若含Si 0.5%的铁水与Si 1.6%的铁水,那钢铁料耗的数值影响5kg/t和16kg/t,可见钢铁料耗相差11kg/t。
(4)钢种的影响
由于合金在计算钢铁料耗时,投入项不计合金量的
而在计算合格产出量时,合金参与了合格产出量的计算,所以合金对钢铁料耗有影响,有时还特别大!!!
案例分析(为了分析便于的问题)
以某钢厂生产60Si2Mn和20MnSi钢的生产为例,进行钢铁料耗的分析。
炼钢终点控制一致,入炉原料基本相似。
1.基础数据
铁水65t,生铁10t,废钢5t,根据理论和实践经验转炉吹损8~12%,为计算选8.8%;60Si2Mn 的合金FeMnSi加入0.775t,FeSi加入1.580t,铸坯收得率99.75%;20MnSi的合金FeMnSi加入1.10t,FeSi加入0.12t, 铸坯收得率99.73%;合金全部加入钢水中它重量的回收经理论和生产实践92%计;
2.投入铁料量
铁水65t +生铁10t +废钢5t =80 t
3. 收得铁料量
60Si2Mn钢合格钢坯:[80×(1-8.8%)+(0.775+1.58)×92%]×99.75%=74.75t
20MnSi钢合格钢坯:[80×(1-8.8%)+(1.10+0.12)×92%]×99.73%=73.88t
4. 计算钢铁料耗(按国家规定公式)
60Si2Mn钢铁料耗=80/74.75×1000=1070.23kg/t
20MnSi钢铁料耗=80/73.88×1000=1082.8kg/t
生产60Si2Mn和20MnSi钢的案例对入炉金属料的废钢折算系数没有考虑,实际操作中是有废钢折算系数,考虑分析问题原因未考虑;
从上面可以看出转炉炉前对钢铁料耗影响约90kg/t,所以炉前的操作控制显得特别重要,减
少炉前的喷溅等事故。
有的恶性喷溅事故,金属料损失严重。
每喷溅一次损失金属料有的2t多(70t转炉)。
不同的钢种,由于合金加入量的不同,对钢铁料耗的贡献也不同,合金加入量大,对钢铁料耗的贡献也大,因此生产不同的钢种要考虑不同的钢铁料耗指标;铸坯收得率收得率钢包残钢量、连浇炉数、中包残钢量、铸坯定尺长度、铸坯割缝、头坯量和尾坯量等影响,
所以以上每个环节都要在满足质量的条件下严格控制,精细化管理;加大炼钢厂内部废钢的回收,对钢铁料耗有重大贡献。
如有侵权请联系告知删除,感谢你们的配合!。