柔性夹具与计算机辅助夹具设计技术的进展
柔性制造系统FMS

柔性制造系统(FMS)1.概述柔性制造系统的发展1967年,英国莫林斯公司首次根据威廉森提出的FMS基本概念,研制了“系统24”。
其主要设备是六台模块化结构的多工序数控机床,目标是在无人看管条件下,实现昼夜24小时连续加工,但最终由于经济和技术上的困难而未全部建成。
同年,美国的怀特·森斯特兰公司建成Omniline I系统,它由八台加工中心和两台多轴钻床组成,工件被装在托盘上的夹具中,按固定顺序以一定节拍在各机床间传送和进行加工。
这种柔性自动化设备适于在少品种、大批量生产中使用,在形式上与传统的自动生产线相似,所以也叫柔性自动线。
日本、前苏联、德国等也都在60年代末至70年代初,先后开展了FMS的研制工作。
,1976年,日本发那科公司展出了由加工中心和工业机器人组成的柔性制造单元(简称FMC),为发展FMS提供了重要的设备形式。
柔性制造单元(FMC)一般由1~2台数控机床与物料传送装置组成,有独立的工件储存站和单元控制系统,能在机床上自动装卸工件,甚至自动检测工件,可实现有限工序的连续生产,适于多品种小批量生产应用。
70年代末期,柔性制造系统在技术上和数量上都有较大发展,80年代初期已进入实用阶段,其中以由3~5台设备组成的柔性制造系统为最多,但也有规模更庞大的系统投入使用。
1982年,日本发那科公司建成自动化电机加工车间,由60个柔性制造单元(包括50个工业机器人)和一个立体仓库组成,另有两台自动引导台车传送毛坯和工件,此外还有一个无人化电机装配车间,它们都能连续24小时运转。
这种自动化和无人化车间,是向实现计算机集成的自动化工厂迈出的重要一步。
与此同时,还出现了若干仅具有柔性制造系统的基本特征,但自动化程度不很完善的经济型柔性制造系统FMS,使柔性制造系统FMS的设计思想和技术成果得到普及应用。
迄今为止,全世界有大量的柔性制造系统投入了应用,仅在日本就有175套完整的柔性制造系统。
第五讲柔性夹具

安徽机电职业技术学院
柔性模块化夹具使用实例
南京信息职业技术学院
二、柔性夹具类型
2. 柔性组合夹具
槽系
基础件
支承件
安定徽位机件电职业技术学院
导向件
夹紧件
其它件
紧固件
合件
南京信息职业技术学院
槽系组合夹具
二、柔性夹具类型
2. 柔性组合夹具
槽系
基础件
支承件
主要用作
夹具体
安定徽位机件电职业技术学院
南京信息职业技术学院
一、柔性夹具概述
1. 柔性夹具特性
柔性夹紧(膨胀销孔定位)
毛坯 上夹具
车床
更换 底座
翻身车
更换 底座
安徽机电职业技术学院
传统加工工艺
线切割 电火花
毛坯 上夹具
车床
下夹具 换夹具
线切割
电火花
下夹具 翻身 换夹具
翻身车
南京信息职业技术学院
一、柔性夹具概述
1. 柔性夹具特性
柔性夹紧(膨胀销孔定位)
导向件
夹紧件
其它件
紧固件
合件
南京信息职业技术学院
二、柔性夹具类型
2. 柔性组合夹具
槽系
基础件
支承件
用做钻 套、钻模
安定徽位机件电职业技板术学院
导向件
夹紧件
其它件
紧固件
合件
南京信息职业技术学院
二、柔性夹具类型
2. 柔性组合夹具
槽系
基础件
支承件
用做夹
紧工件
安定徽位机件电职业技术学院
导向件
夹紧件
其它件
安徽机电职业技术学院
南京信息职业技术学院
柔性夹具应用技术之解析
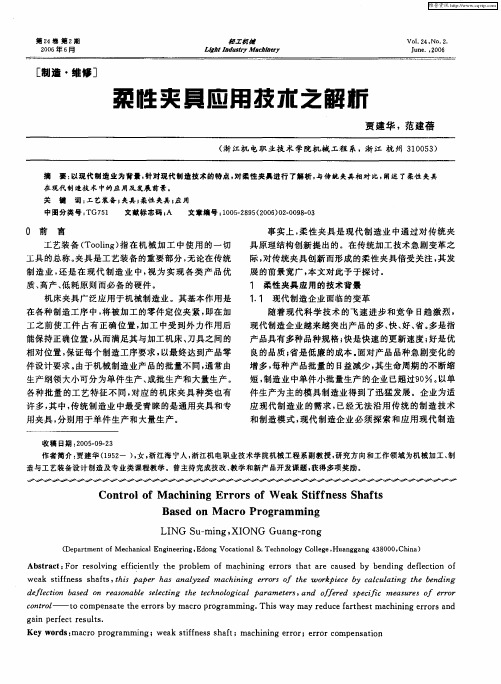
第2 4卷 第 2期 20 0 6年 6 月
轻 I 祝 摄
LI htZ u 1 y M a h n r R nd ¥ r c i e y
Vo . 4, 1 2 No. 2
J n . 2 0 u e ,0 6
[ 制造 ・ 维修 ]
柔 性 夹 具 应 用 技 之 翩 析
生产 纲领大 小 可分 为单 件 生产 、 成批 生产和 大量 生产 。 各 种 批 量 的工 艺 特征 不 同 , 对应 的 机 床夹 具 种 类 也 有 许多 , 中, 其 传统 制 造业 中最受 青 睐的是 通用 夹具 和 专
用 夹具 , 别用 于单 件 生 产和 大量 生产 。 分
贾 建 华 ,范 建 蓓
( 江机 电职 业技 术 学院机械 工程 系,浙 江 杭 州 3 0 5 ) 浙 1 0 3
摘
关
要: 以现代 制造业 为背景 , 针对 现代制造 技术的特点 , 对乖性 夹具进行 了解 析 , 与传统 央具 相对 比, 阐述 了秉性 央具
键 词 ; 艺装 备 ; 工 央具 ; 性 央具 } 用 秉 应
Ab ta t F r r s l ig efce t h r be o c i ig er r h ta e c u e y b n i g d fe to f sr c : o e ovn fiin l t e p o lm f ma h n n ro s t a r a s d b e dn e lc in o y
Co r i0 a h ni r r f W e k Stf ne sSh f s nt o f M c i ng Er o s0 a if s a t Ba e n M a r o r m m i sdo c o Pr g a ng
柔性制造技术FMS

主要内容:
• 柔性制造技术概述 • 柔性制造技术的加工系统 • FMS的物料运储系统 • FMS刀具管理系统 • FMS的控制系统
2022/2/28
现代制造技术
2-1
第1节 柔性制造技术概述
1. 柔性制造技术与柔性制造系统
柔性制造技术(FMT——Flexible Manufacturing Technology) 是集数控技术、计算机技术、机器人技术、现代管理技术为一体的 现代制造技术,主要用于多品种小批量或变批量生产。
柔性制造系统 (FMS)是数控机床或设备自动化的延伸,FMS 的一般定义可以用以下三方面来概括;FMS是一个计算机控制的生 产系统;系统采用半独立的NC机床;这些机床通过物料输送系统联 成一体。其中,数控机床提供灵活的加工工艺,物料输送系统将数 控机床互相联系起来,计算机则不断对设备的动作进行监控、检测, 同时提供控制指令并进行工程记录,还可通过仿真来预示系统各部 件的行为。
加工中心,数控组合机床和托盘交换器等构成;用于加工回转 体类工件的FMS由数控车床,车削中心,数控组合机床和上下料 机械手或机器人及棒料输送装置等构成。
2022/2/28
现代制造技术
2-14
(2)机床配置形式: 1) 互替式(并联)
2) 互补式(串联)
当所选定零件组的全部工序可以被一 种机床独立完成时,FMS可以只配置数 量足够的相同型号机床,这些机床之 间是可以相互代替的。
3) 混合式(并串联)
当所选定零件组的全部工序不能被 一种机床独立完成时,FMS需要配置 几种不同型号的机床,各自完成特定 的工作,这些机床之间是互相补充的, 不能相互替代。
2022/2/28
现代制造技术
柔性制造系统FMS

柔性制造系统FMS70年代末80年代初,随着计算机辅助治理、物料自动搬运、刀具治理和计算机网络、数据库的进展以及CAD/CAM技术、成组技术(GT)、工业机器人等技术的成熟,更加系统化、规模化的柔性制造系统(FMS)就出现了。
所谓FMS,是一组数控机床和其他自动化的工艺设备,由计算机信息操纵系统和物料自动储运系统有机结合的整体,能适合加工对象变换的自动化机械制造系统(FlexibleManufacturingSystem)。
下面就柔性制造系统的组成、分类、优势及进展趋势实行阐述。
一、柔性制造系统(FMS)的组成1.加工系统柔性制造系统采纳的设备由待加工工件的类别决定,主要有加工中心、车削中心或计算机数控(CNC)车、铣、磨及齿轮加工机床等,用以自动地完成多种工序的加工。
2.物料系统物料系统用以实现工件及工装夹具的自动供给和装卸,以及完成工序间的自动传送、调运和存贮工作,包括各种传送带、自动导引小车、工业机器人及专用起吊运送机等。
3.计算机操纵系统计算机操纵系统用以处理柔性制造系统的各种信息,输出操纵CNC机床和物料系统等自动操作所需的信息。
通常采纳三级(设备级、工作站级、单元级)分布式计算机操纵系统,其中单元级操纵系统(单元操纵器)是柔性制造系统的核心。
4.系统软件系统软件用以确保柔性制造系统有效地适合中小批量多品种生产的治理、操纵及优化工作,包括设计规划软件、生产过程分析软件、生产过程调度软件、系统治理和监控软件。
二、柔性制造系统的分类1.柔性制造单元(FMC)FMC由单台带多托盘系统的加工中心或3台以下的CNC机床组成,具有适合加工多品种产品的灵活性。
FMC的柔性最高。
2.柔性制造线(FML)柔性制造线FML是处于非柔性自动线和FMS之间的生产线,对物料系统的柔性要求低于FMS,但生产效率更高。
3.柔性制造系统(FMS)FMS通常包括3台以上的CNC机床(或加工中心),由集中的操纵系统及物料系统连接起来,可在不停机情况下实现多品种、中小批量的加工治理。
CNC机床加工中的夹具设计与应用

CNC机床加工中的夹具设计与应用CNC机床加工在现代制造业中扮演着重要的角色,它能够以高精度、高效率完成各种复杂零部件的加工任务。
而夹具作为CNC机床加工过程中不可或缺的辅助工具,对于确保工件的位置、固定和刚性等方面起着至关重要的作用。
本文将探讨CNC机床加工中夹具设计与应用的相关问题。
一、夹具的定义与分类夹具是指在加工过程中将工件固定在CNC机床上的一种装置。
它的主要作用是保证工件的准确定位、稳定固定,从而确保加工质量和效率。
根据不同的应用需求,夹具可以分为以下几类:1. 机床夹具:用于将工件固定在机床上进行加工。
常见的机床夹具包括平口夹具、机床铣削用刀具夹具、分度头夹具等。
2. 刀具夹具:主要用于固定和夹持刀具,保证刀具在加工过程中的稳定性和刚性。
刀具夹具的设计应考虑到刀具的类型、尺寸以及加工要求。
3. 工件夹具:将工件固定在机床上进行加工的夹具,能够确保工件的稳定固定和准确定位。
根据工件的形状和尺寸不同,工件夹具可分为平口夹具、螺纹夹具、气动夹具等。
二、夹具设计的重要性在CNC机床加工中,夹具设计的合理与否直接影响到加工效果和质量。
一方面,夹具设计需要根据具体工件的特点和加工要求进行合理选择,以确保工件在加工过程中的稳定性和精度;另一方面,夹具设计还需要考虑材料的选择、结构的合理优化,以提高夹具的刚性和耐用性。
三、夹具设计的基本原则夹具设计应遵循一定的原则,以保证夹具的可靠性和稳定性:1. 合理选择夹具类型:根据工件的形状、尺寸和加工要求,选择适当的夹具类型,并确保夹具能够提供足够的固定力和刚性。
2. 准确定位和定位:夹具设计中需要确保工件在加工过程中的准确定位和定位,避免加工误差和产生不良影响。
3. 确保夹具刚性:夹具的刚性直接影响加工过程中的稳定性和加工精度。
因此,在夹具的设计中,需要合理选择夹具材料和结构,提高夹具的整体刚性。
4. 简化夹具结构:夹具的结构应简洁、紧凑,减少不必要的部件和连接点。
柔性制造系统
柔性制造系统随着机电一体化技术的发展,传统的机械技术与新兴的微电子技术相结合,出现了很多现代化的加工设备和手段,特别是数控机床和加工中心的迅速普及和多功能化,为改变中小批量生产的落后状况提供了可能。
柔性制造系统(FMS)便是在这样的背景下产生和发展起来的。
所谓柔性制造系统是利用计算机控制系统和物料输送系统,把若干台设备联系起来,形成没有固定加工顺序和节拍的自动化制造系统。
它在加工完一定批量的某种工件后,能在不停机调整的情况下,自动地向另一种工件转换。
它的主要特点是包括以下几方面。
(1)高柔性。
能在不停机调整的情况下,实现多种不同工艺要求的零件加工。
(2)高效率。
能采用合理的切削用量实现高效加工,同时使辅助时间和准备终结时间减小到最低程度。
(3)高度自动化。
自动更换工件、刀具、夹具,实现自动装夹和输送,自动监测加工过程,有很强的系统软件功能。
柔性制造系统的组成柔性制造系统由加工系统、物流系统、信息流系统三部分组成。
1.加工系统加工系统的功能是以任意顺序自动加工各种工件,并能自动地更换工件和刀具。
通常由若干台加工零件的CNC机床或CNC板材加工设备以及操纵这种机床要使用的刀具所构成。
在加工较复杂零件的FMS加工系统中,由于机床上机载刀库能提供的刀具数目有限,除尽可能使产品设计标准化,以便使用通用刀具和减少专用刀具的数量外,必要时还需要在加工系统中设置机外自动刀库以补充机载刀库容量的不足。
2.物流系统FMS中的物流系统与传统的自动线或流水线有很大的差别,整个工件输送系统的工作状态是可以进行随机调度的,而且都设置有储料库以调节各工位上加工时间的差异。
物流系统包含工件的输送和储存两个方面。
工件输送包括工件从系统外部送入系统和工件在系统内部的传送两部分,目前,大多数工件送入系统和夹具上装夹工件仍由人工操作,系统中设置装卸工位,较重的工件可用各种起重设备或机器人搬运。
工件输送系统按所用运输工具可分成为自动输送车、轨道传送系统、带式传送系统和机器人传送系统四类。
槽系组合夹具计算机辅助拼装系统的研究
・
现代设 计 与先进 制造 技术 ・
许 晓呖
顾
铭
槽 系组 合夹 具计算 机辅 助拼 装 系统 的研究
3 3
槽 系组 合 夹 具 计 算 机 辅 助拼 装 系统 的研 究
许晓呖, 顾 铭
1 ( 成都 电子 机械 高等专 科学 校 机械 系 , 四川 成都
辅助 人工 进 行 夹 具 设 计 并 进 行 虚 拟 拼装 的 系 统 。
收 稿 日期 :o 6一O 2o 9一O 8
行修改设计。若进行全新设计 , 则首先选择工件的
定 位 面 、 紧面 , 行夹 具 的 定位 机构 , 紧机构 , 夹 进 夹 刀具 导 向 、 刀 机 构 的 设计 , 完 成装 配 设 计 。 对 并 设
可节 约 夹 具 设 计 工 时 和 材 料 , 为 与 加 工 中心 、 成
1 系统 总体 结构
系统的总体框架如图 1 所示。信息输入模块 主要完成工件几何形状信息、 工艺信息 、 加工表面 信息的输入及处理 ; 构设计模块则完成定位机 结
构 , 紧机 构 , 向 、 夹 导 对刀机 构 和辅助机 构 的设计工 作; 定位 、 紧 、 向 、 刀及 辅 助机 构 的零 部 件 之 夹 导 对 间的装配 则 由装配设 计模 块来 完成 ; 构设 计和 装 结 配 设计过 程 中的零 部 件 参 数修 改 、 调用 、 除 等 操 删 作 在编辑 修改 模块 中进行 ; 具组合 体 的精度校 核 夹 及 干涉检 查在 结构设 计 校核模 块 中完成 ; 组合夹 具
可根 据用 户要 求 , 索相 似夹具 结构 或进行 全新设 检 计 。若检 索 出相似结 构 的夹具 , 可在此基 础上 进 则
汽车零部件制造中柔性组合夹具的运用探究
内燃机与配件0引言人们生活质量的提高,对于汽车需求日渐增大,对于汽车制造行业来说不仅仅是一次机遇更是一种发展挑战。
要提高各部件制造系统的柔性,就需要重点关注组合夹具的创新,实现柔性组合夹具的高效运用,从而提高汽车制造的良率,为社会提供更多高质量汽车种类。
1汽车制造中组合夹具运用的特点汽车生产制造中,涉及到的零部件种类较多,在实际组装制造中对于组合夹具的使用必不可少。
结合当前实际生产情况,从组合夹具的结构形式入手,可以将其大致划分为三个种类:一是槽系组合夹具;二是孔系组合夹具;三是组合冲模。
三种不同的组合夹具类型需要根据实际制造标准合理选择,不可盲目,例如槽系组合夹具就包含有12mm 、16mm 等。
1.1经济性特点相对于过去的夹具使用来说,组合夹具的运用更具有高效性和经济性,通过对各种夹具的组合使用可以满足不同零部件的安装,之后再将其进行拆卸,还可以使用到其它元件中,这样就避免了库存问题出现,也满足了节约资源的客观要求。
从制造的时效性来看,它的经济性还可以最大程度的压缩成本,缩短制造夹具所需要的时间,有效减轻了人力劳动的强度,得到了普遍采纳。
1.2通用性特点一般来说,汽车零部件制造中对于组合夹具的运用并不是随意盲目的,首要的运用出发点就是提高制造的标准化和精密化,从此角度就可以看出组合夹具是具有很明显的通用性的,并且也可以实现多次循环利用。
实际运用中的组合夹具具有很高的几何精度和尺寸精度,这是人工所难以达到的,而且它的耐磨性和硬度也可以满足大多数零部件的生产加工需要[1]。
除此之外,元件之间还具有相互交换的特性,如果在零部件制造中运用,能够按照实际需要将各元件进行针对性拼接,最后形成多种不同的结构型式满足多种类加工要求。
1.3适用性特点现代汽车行业为了满足使用的多样性,其内部功能设计越来越多样化,这就为零部件制造提出了更高的标准。
在进行实际生产制造中,组合夹具就体现出了很明显的适用性,可以在各个部位中运用,例如汽车制造中的钻、铣、刨、磨等制造工艺,不仅仅是这些工艺,在汽车的装配、检验以及焊接等环节也有很好的运用效果,这是传统夹具所不具备的。
2018-2019-夹具设计实验报告-精选word文档 (10页)
本文部分内容来自网络整理,本司不为其真实性负责,如有异议或侵权请及时联系,本司将立即删除!== 本文为word格式,下载后可方便编辑和修改! ==夹具设计实验报告篇一:夹具设计实训报告夹具设计实训研修报告专业:机电一体化学号:12025904 班级:机电12302班姓名:李新目录设计任务书????????????????????????3 前言???????????????????????????4 设计思想?????????????????????????8 1、钻床夹具设计过程???????????????????91.1 工件本工序的加工要求分析?????????????10 1.2 确定夹具的类型??????????????????11 1.3 拟定夹具的定位方案和选择定位元件?????????11 1.4 确定夹具的夹紧方案????????????????12 1.5 确定夹具引导元件?????????????????12 1.6 夹具的精度分析与计算???????????????13 1.7夹紧机构设计与夹紧计算??????????????14 1.7.1夹紧机构设计???????????????141.7.2夹紧计算????????????????15 1.8 夹具操作过程明??????????????16 2、绘制夹具总图?????????????????????16 3、绘制夹具零件图????????????????????17 4、小结?????????????????????????17 5、设计心得体会?????????????????????18 6、参考文献???????????????????????21附图钻床夹具三维装配图钻床夹具课程设计任务书题目:设计“挡环”零件的钻床夹具设计内容:1、挡环零件图 1张2、钻床夹具装配图1张3、钻床夹具零件图3张4、钻床夹具三维图3张 5、课程设计说明书 1份201X年12月 25日前言1、主要技术指标1)保证工件的加工精度专用夹具应有合理的定位方案、合适的尺寸、公差和技术要求,并进行必要的精度分析,确保夹具能满足工件的加工精度要求。
- 1、下载文档前请自行甄别文档内容的完整性,平台不提供额外的编辑、内容补充、找答案等附加服务。
- 2、"仅部分预览"的文档,不可在线预览部分如存在完整性等问题,可反馈申请退款(可完整预览的文档不适用该条件!)。
- 3、如文档侵犯您的权益,请联系客服反馈,我们会尽快为您处理(人工客服工作时间:9:00-18:30)。
综 述柔性夹具与计算机辅助夹具设计技术的进展北京机械工业学院 朱耀祥 美国吴士脱工学院(WPI) 融亦鸣
本世纪制造业的主导生产模式是标准产品的大批大量生产,专用夹具在其中起过关键性的作用。自70年代以后,随着NC机床和加工中心在生产中的普遍使用,80年代柔性制造系统(FMS)的兴起,计算机集成制造系统(CIMS)的提出,多品种中小批生产日益受到重视。但早在80年代后期有的文献就谈到美国65%的FMS只能加工同族的2~10个品种,而其余1/3只能加工一种产品,主要原因之一就是仍沿用专用夹具,因而夹具就成为制造系统实现真正柔性的瓶颈。随着柔性已作为一个和质量、成本、生产率等量齐观考虑的问题,柔性夹具理所当然成为开发的重点。90年代以后制造业中的竞争空前加剧。能实现快速生产准备的计算机辅助夹具设计(CAFD)技术成为国际上竞相研究的热点,但由于其复杂和困难,至今只有我们研究的夹具规划和结构生成的Fix-Des孔系组合夹具设计系统已开发成为唯一的初步的商品化软件,并在美国工业中使用。1 夹具功能的演变 传统夹具以专用夹具为代表,主要有4种功能,即定位、夹紧、导向和对刀。由于NC系统的准确控制功能和精密机床传动中小摩擦零间隙的实现,以及传统转塔车床工艺中钻孔的方法,不用导向钻套,也得到了很高的孔位置精度。此外,加工中心还具备有触头和测量的功能。铣刀的对刀在编程中就能轻而易举地得到解决。可见,在NC机床、加工中心上使用的夹具,只需要具备定位和夹紧两种功能就能满足要求。“夹具”一词在英文中用“Jig”和“Fixture”两个词来表示,前者指钻模,现在已经用不到了,当前在夹具文献中也只看到“Fixture”或“Fixturing”一词了。夹具中取消了导向和对刀功能就使夹具种类减少,结构简化,这些都有利于CAFD系统的实现。由于加工中心在复杂零件加工中的广泛应用,机加工工艺过程中更多地采用工序集中而摒弃分散。大多数复杂的箱体或基体零件,在普通机床上完成基准加工后,不需超过3次安装就可在加工中心上完成高质量的加工,其中少数工序也可能仍要用到普通机床。因此普通机床和加工中心的混合使用和工序的高度集中将是当代机加工工艺的大势所趋。这也是CAPP和CAFD共同的工艺基础。
2 柔性夹具的研究与开发 一般说来,柔性夹具是指工件的形状和尺寸有一定变化后,夹具还能适应继续使用的应变能力。但是工件变化可以在小范围,即在相似的形状和尺寸变动不大的范围内,也可在大范围,即零件形状完全不同,尺寸变化也很大。所以,柔性夹具还是含糊的,没有明确的定义和界限。笼统地说,就是指与NC机床、加工中心配合使用的、具有夹持多种不同工件能力的夹具。自80年代后柔性夹具的研究开发主要沿以下两大方向发展。2.1 原理和结构均有创新的柔性夹具这类柔性夹具有三类:(1)相变和伪相变式柔性夹具。利用材料物理性质从液相到固相,再变回液相,相变的机制一般是效应或电感应。所用材料有铋基低熔点合金,聚丙烯腈类高分子聚合物等。相变机制必须易于控制,相变材料必须对工件和人无害。这类夹具通常都有一个充满相变材料的容器,当材料液相时将工件埋入液体中,然后改变条件(如升温或降温),在液相变成固相时,将零件夹持并固定,然后进行加工。加工结束后再将材料恢复成液相,就可将工件取出。由于升降温容易引起工件的热变形而影响精度。因此,现正研究用电场控制相变的高分子材料。图1为用叶片曲面定位加工叶片根部榫头的封装块式柔性夹具。图中先将叶片用相变材料在模具中安装并固化,然后从模具中取出工件封装块,将封装块安装在夹具中加工叶片根部榫头。最后再通过介质相变图1 封装块式相变材料夹具
・5・《制造技术与机床》 2000年第8期后,取出加工完毕的叶片。为了避免热致相变的负面效果,又研究出伪相变材料,这是用颗粒流态床来模拟相变材料的双相性质。其基本原理来自真空密封袋装咖啡。图2为流态床式夹具,床中布图2 流态床式夹具 满细小金属颗粒,床底有一多孔板,板下为进气口。床中放入标准夹具元件,元件埋在颗粒中,当关闭进气口时,由于重力颗粒形成块状图3 多叶适应性虎钳 固体并辅以液压板压紧有如夯实。将工件定位夹紧后就可加工工件,加工后打开进气口,压缩空气进入并松开液压板,颗粒恢复成松散状就可取出工件。此类夹具,目前只能用于曲面定位或加工力轻微的精加工等少数情况,许多问题尚待研究。(2)适应性夹具。所谓适应性夹具是指夹紧元件能自动适应工件形状的夹具,是一种被动式的装置,当夹紧时能改变形状以适应工件的变化。图3为带有多叶片的虎钳,一个钳口是固定的,另一个钳口由穿在转轴上的多叶片组成,当其他运动受限制时叶片可绕转轴自由转动以适应工件形状。(3)模块化程控式夹具。这类夹具实质上是将定位元件和夹紧元件装在双向可移动的导轨上,然后通过传动和程序控制作出多种不同布局。总之,近20多年来对柔性夹具国际上作过多种研究和探索,但尚没有找到结构上、经济上、实用性上能与传统夹具中已具柔性的一些夹具相匹敌的新型夹具。2.2 传统夹具的创新传统夹具中,可调整夹具可以适应小范围内的柔性,而组合夹具能符合大范围内柔性夹具的要求。可调整夹具由于受到成组生产组织形式和产品品种市场需求不确定性的约束,因而应用受到限制。传统的槽系组合夹具因材料贵、加工精度高、配套元件多、初置费用高而在市场上逐步受到冷落。自80年代以来,原理相同只是元件结构和组装方式不同的孔系组合夹具,因其材料价廉、加工方便、配套元件少、成本低、性能好而受到国内外市场的青睐,成为和加工中心、FMS配套的主要夹具,一跃成为当代柔性夹具的主流。图4为孔系组合夹具的结构和组装方式。孔系组合夹具的组装需要知识广博、经验丰富和技术熟练的人员,这正是当前工厂最缺少的,不仅我国如此,国外更稀缺。此外,在焊接生产中也在推广焊接组合夹具,坐标测量机需要测量组合夹具,新一代轻巧、灵活连接方便的夹具液压装置也已推出,说明传统夹具创新仍是现代柔性夹具的主流。
图4 孔系组合夹具(天津组合夹具厂制造)3 计算机辅助夹具设计(CAFD)系统和技术 CAFD以其本身的特点和其他部分的紧密连接是CAD/CAM系统中一个独立的部分,CAFD更广义地说是属于新兴的计算机辅助工艺装备CAT(ComputerAidedTooling)范畴。现在准确地说是CAPP和CAFD共同构成CAD和CAM间的接口,而CAPP和CAFD又是彼此相互提供信息和作出决策的两个独立系统。3.1 第三代CAFD系统与80年代初CAD软件的水平相配合,第一代CAFD系统是交互式设计系统(Ⅰ-CAFD)。设计人员简单应用CAD软件的图形功能,建立一个标准夹具元件数据库,用以在计算机屏幕上装配成夹具图。后来加上了定位方法选择,工件信息检索,元件选择,元件安装等模块,成为一个独立的系统。由于现代商品化CAD软件在屏幕上针对夹具几何图形的操作还是费时的,所以Ⅰ-CAFD在工业上应用还是有价值的。80年代中期后,根据变异式和生成式两种不同的方法产生了基于成组技术(GT)和基于知识的两类CAFD系统,这是第二代CAFD。基于GT的CAFD有一个夹具设计信息的编码系统,系统中应包含零件几何形状的信息,零件装夹信息,即定位、夹紧等和工艺操作的信息等。由夹具编码系统在典型夹具图形库中检索出相似夹具,经手工修改成合乎需要的夹具。在我们研究开发的基于GT的CAFD中,由于装夹信息十分复杂,我们将这部分代码由线性码结构改成矩阵码结构,其次对如何评价夹具间相似性定义了相似系数,以便检索出库中最相似的夹具,作最少的修改。基于知识的CAFD,主要是搜集人类夹具专家的知识整理成知识库中的各种规则,然后通过专家系统推理机得到各种决策。这类系统主要解决定位、夹紧方法的选择,位置的确定。有的系统已经搜集和整理了上千条的规则,但
・6・《制造技术与机床》 2000年第8期因工件的多样性,夹具设计的复杂性也只能设计工件形状极简单的夹具。90年代后的第三代CAFD,总结经验认为夹具设计最终必须要得到夹具结构图,而过去的系统只是解决安装、定位、夹紧等问题或检索类似的结构,不能获得合乎工件实际应用的结构图。因此,必须开发出以产生夹具结构为目的,实际生产应用为导向的商品化夹具设计软件。为此我们研制了可用于FMS和CIMS的孔系组合夹具设计系统。此系统大体参考人工设计夹具的过程,同时照顾到计算机处理问题的特点。系统分成4个部分:(1)安装规划,(2)夹具规划,(3)夹具结构设计,(4)性能评价。安装规划的目的是决定需要的安装次数,每次安装中工件的方位和要求加工的表面。这部分也可以是CAPP的一个子集,也是CAFD和CAPP集成的交互接口。性能评价也是一个相对独立的软件,其目的是对已设计完成的夹具,按要求选项对有关性能进行评价和估算,如精度、刚度等。夹具规划主要用来决定工件上定位支撑的面和点,以及各夹紧点。夹具结构设计的任务是选择夹具元件并把它们装配成最终的夹具布局和结构。我们已开发出Fix-planning系统。此系统通过一个商品化CAD软件包和我们已开发成功的自动夹具结构设计系统Fix-Des集成。CAD作为平台提供夹具规划所需图5 Fix-Des系统输出的夹具三维视图信息,Fix-Des使用夹具规划的输出产生组合夹具结构。图5为由此系统输出的三维夹具结构图,由CAD软件的功能同样也能产生二维的三视图。3.2 系统中的关键技术(1)夹具规划的策略 夹具规划受到工件几何形状和公差,安装规划中的特征和刀具,每次安装中加工开始和终了的工件状态,能用的夹具元件的限制。夹具规划过程大体可分为5个阶段:输入、分析、规划、确认和输出。输入限制夹具规划的各种信息。分析是从候选的装夹特征中提取有关的精度和表面可及性信息。规划的任务是在当前安装步骤中自动决定主定位方向及选择理想的定位/夹紧表面和点。确认是验证规划的正确性。输出是指夹具规划的一种格式输出,用作Fix-Des的输入。图6为夹具规划的系统流程图。(2)夹具结构分析和元件装配关系推理 组合夹具结构能被分解成:功能单元、元件和功能表面等3个层次。应用集合论,夹具总体可分解为夹具元件的集合。通过对组合夹具应用实例的调查,各种夹具中有一些通用的基本结构,因此研究元件和提取元件基本组装结构单元是自动夹具结构设计的一条捷径。事实上组合夹具元件之间的装配关系并非任意自由,一种夹具元件只能用于一种或几图6 夹具规划流程图
种结构单元。确定定位方案和定位/夹紧表面后,通过这种装配关系之间的推理程序,选择元件组成单元,再将单元安装到基础板上就产生出夹具结构。图7为夹具结构自动生成流程图。
图7 自动夹具结构设计系统图(3)夹具功能检查和性能评价 不论是夹具规划还是结构生成部分,都需要检查某些功能。如夹具规划时,要检查刀具加工轨迹包络面是否和夹具元件产生干涉。此外,从Fix-Des输出装配图后,重要的夹具还要对其性能进行评价,有加工精度、刚度和变形、各夹紧点夹紧力作用下的工件稳定性等。如薄壁工件在加工时,如夹紧点的数量和位置不合适,容易产生较大的变形,因此夹具设计完成后要作评价。