旋压技术
旋压技术在轮毂加工中的应用

旋压技术在轮毂加工中的应用
旋压技术在轮毂加工中具有重要的应用价值。
旋压技术是利用旋转磨具对工件进行加工、修整和改变形状的一种高效加工技术。
它通过旋转磨具与工件之间的相对运动,实现对轮毂的精密加工和表面质量的提升。
1.表面质量优化:旋压技术可以有效地改善轮毂表面的质量和光洁度。
通过合理选择磨具材料和磨具的形状,可以减少或消除轮毂表面的微观缺陷,同时还能有效地去除轮毂表面的氧化皮和气体腐蚀产物,提高轮毂的光洁度和抗腐蚀能力。
2.尺寸精度提升:旋压技术可以实现对轮毂尺寸的精确控制和调整。
通过旋压过程中的压力和磨具的选择,可以使轮毂的尺寸达到更高的精度要求。
旋压技术还可以实现对轮毂轮胎安装面的平整度和同心度的调整,确保轮毂与轮胎的匹配度达到最佳状态。
3.加工效率提高:旋压技术具有较高的加工效率和生产率。
相比于传统的切削加工方法,旋压技术能够在保证加工质量的前提下,大幅度减少加工时间和工艺复杂度。
这对于轮毂等大型工件的批量生产和加工效率的提升具有重要意义。
4.材料节约:旋压技术可以实现对材料的精简和节约。
由于旋压过程中的磨料由软性材料组成,因此不会对轮毂的材料造成过大的损耗。
相比于传统的切削加工方法,旋压技术能够有效减少材料的浪费,提高材料的利用率。
5.环境友好:旋压技术具有较低的噪音和振动水平,对环境和操作人员的健康没有显著的影响。
同时,旋压技术由于不需要使用冷却液和产生大量的切屑,减少了对环境的污染。
旋压成型工艺

旋压成型工艺
旋压成型工艺是一种常见的金属加工方法,通过旋压机械设备将金属板材弯曲成所需的形状。
这种工艺在制造行业中被广泛应用,可以用于生产各种尺寸和形状的零部件和产品。
本文将介绍旋压成型工艺的原理、优势以及应用领域。
旋压成型工艺的原理是利用旋压机械设备的旋转运动和压力,使金属板材在两个或多个滚轮之间进行弯曲。
通过不断调整滚轮的位置和压力,可以实现对金属板材的精确成型,从而生产出符合设计要求的零部件。
这种工艺可以实现高效、精确的金属加工,适用于各种不同材质的金属板材。
旋压成型工艺具有许多优势。
首先,它可以在不改变金属板材性质的情况下进行加工,确保产品的质量和性能。
其次,旋压成型可以实现对金属板材的多维度成型,满足复杂零部件的生产需求。
此外,与传统的金属加工方法相比,旋压成型具有更高的生产效率和更低的生产成本,可以大大节约制造成本。
旋压成型工艺在许多领域都得到了广泛应用。
在汽车制造行业,旋压成型可以生产车身零部件、排气管等金属零件。
在航空航天领域,旋压成型可以制造飞机机身、发动机外壳等关键部件。
此外,在家电、建筑、能源等领域,旋压成型也有着重要的应用价值,为各行业的发展提供了技术支持。
总的来说,旋压成型工艺是一种高效、精确的金属加工方法,具有广泛的应用前景和市场需求。
随着制造技术的不断进步和发展,旋压成型工艺将在未来得到更广泛的应用,为各行业的发展带来新的机遇和挑战。
希望本文的介绍能够让读者更加了解旋压成型工艺,为相关行业的发展提供参考和借鉴。
旋压工艺技术

旋压工艺技术
旋压工艺技术是一种常用的金属加工方法,主要应用于大量生产各类薄壁金属件的制造工艺。
该工艺通过将金属材料放在旋压机上,利用旋转压力使材料弯曲、伸展、挤压等形变,从而得到所需形状的金属件。
旋压工艺技术具有以下几个主要特点:
首先,旋压工艺技术可以高效地生产大批量的金属件。
工艺简单,操作方便,一次可完成多道工序。
与传统的冷冲压工艺相比,旋压工艺不需要使用模具,减少了制造成本和设备投资。
因此,在量大、异型、复杂的金属件生产中具有明显的优势。
其次,旋压工艺技术可以制造出高精度的金属件。
旋压时,金属材料在受到旋转压力的作用下,会产生较大的变形,使其逐渐变薄、增长、收缩等,从而得到所需形状和尺寸的金属件。
通过合理设置旋压参数,可以控制变形过程,保证产品的精确度和一致性。
再次,旋压工艺技术可以加工各类金属材料。
无论是常见的铝、铜、不锈钢,还是钛合金、镍合金等高强度材料,都可以通过旋压工艺加工成所需的形状。
而且,旋压工艺对材料的硬度和强度要求相对较低,能够加工出不易变形、耐磨、耐腐蚀的金属件。
此外,旋压工艺技术还具有一定的柔性和创新性。
工艺参数可以根据不同的金属材料及产品要求进行调整,适用于生产各种
规格、型号的金属件。
在制造金属件时,可以根据产品形状的要求,灵活选择旋压的次数、轴向和径向进给量等参数,以获得想要的形状和尺寸。
综上所述,旋压工艺技术是一种高效、高精度的金属加工方法,广泛应用于汽车、航空航天、电子、建筑等行业。
随着科技的不断进步,旋压工艺技术将会进一步发展,为金属制造行业带来更多的机遇和挑战。
对轮无模旋压

对轮无模旋压
对轮无模旋压是一种加工技术,主要应用于金属材料的加工和成型。
它使用无模旋压机,通过旋轮的高速旋转和精确控制,将金属板料或管料加工成各种形状和尺寸的零件。
对轮无模旋压技术的优点包括:
1.无须使用模具,降低了生产成本和周期。
2.可加工各种复杂形状和尺寸的零件,具有很高的灵活性。
3.可通过调整旋轮的参数和加工工艺,实现高精度和高效率的加工。
4.可加工的材料范围广泛,包括金属板料、管料、棒料等。
5.可加工的零件应用领域广泛,如汽车、航空航天、船舶、石油化工等。
对轮无模旋压技术的主要步骤包括:
1.板料或管料的准备:根据零件的尺寸和形状,准备相应的板料或管料。
2.调整旋压机参数:根据加工要求,调整旋轮的参数、主轴转速、进给速度等。
3.安装板料或管料:将准备好的板料或管料安装到旋压机的夹具中。
4.开始加工:启动旋压机,通过旋轮的高速旋转和进给运动,对板料或管料进行加工。
5.检测和质量控制:在加工过程中,进行必要的检测和控制,保证零件的质量和精度。
6.后处理:根据需要,对加工完成的零件进行清洗、涂装等后处理。
总之,对轮无模旋压技术是一种高效、灵活、低成本的金属加工技术,在各行业中得到了广泛的应用。
旋压
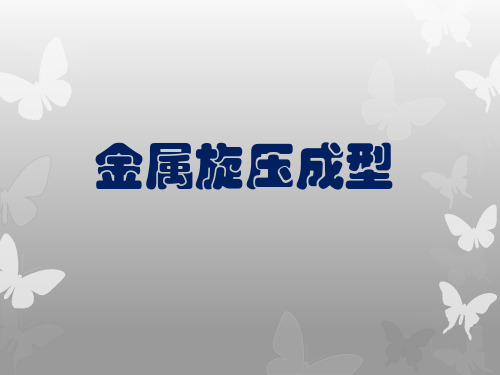
1.2.2强力旋压
1.3旋压的特点
旋压是一种特殊的成形方法。用旋压方法可以完成各种形状旋转体的 拉深、翻边、缩口、胀形和卷边等工艺。金属旋压工艺具有节省原材料、 成本低廉、设备简单和产品质量高等优点;因此,旋压工艺在国防、化工、 冶金、电子、机械等诸方面起到了越来越大的作用,特别在火箭、导弹、 核电、宇航等有关零件的制造方面得到了很好的应用,不仅用于工业上的 锅炉封头、压力容器、储油罐的生产上,而且还用于千家万户的水壶、锅 子、餐杯、洗衣机鼓桶、灯罩等的制造之中。
2.旋压工艺参数的选择
2.2旋轮安装角
芯模轴线和旋轮轴线构成的角称为旋轮安装角。
安装角不能过大,安装角过大会使加工金属流向旋轮前面,从而
导致极粗糙的锉齿形表面。根据加工要求和加工轨迹路线,灯罩旋压 工艺选取了45°安装角。
2.3主轴转速
提高转速,可以改变零件表面的光洁度,并提高生产效率,但主轴转速的 提高也有限制。① 受主轴最高转速和额定转速的限制,批量生产时主轴转速保 持在额定转速以内为宜。② 由于主轴转速的提高会使零件表面的温度升高,从 而改变零件表面的物理特性,所以在提高主轴转速的同时也要兼顾温升的变化, 例如铝制品加工时,主轴转速过高而产生的高温会加大产品表面的粗糙度。灯 罩旋压加工中,根据主轴性能和工艺要求选择了2500r/min。
1.概述
二是,在20世纪60~70年代出现了能单向多道次进给的、电器液压程序 控制的半自动旋压机。三是,由于电子技术的发展,于20世纪60年代后 期,国外在半自动旋压机的基础上,发展了数控和录返式旋压机。这些 设备的快速发展将旋压工艺带进了中、大批量化的生产中。 近20年来,旋压成形技术突飞猛进,高精度数控和录返旋压机不断 出现并迅速推广应用,目前正向着系列化和标准化方向发展。在许多国 家,如美国、俄罗斯、德国、日本和加拿大等国己生产出先进的标准化 程度很高的旋压设备,这些旋压设备己基本定型,旋压工艺稳定,产品 多种多样,应用范围日益广泛。 我国旋压技术的发展状况与国外先进水平相比有较大差距。但近年 来取得了较大发展,许多产品精度和性能都接近或达到了国外较先进水 平。国内许多研究所(如北航现代技术研究所、黑龙江省旋压技术研究 所、长春55所等)已经研制出了性能较好的旋压机。
旋压成型工艺

旋压成型工艺旋压成型工艺是一种常用的金属成型加工技术,它利用旋转的力量将金属板材或管材弯曲成不同形状,通常被应用于制造各种零部件、容器和设备等。
下面将从旋压成型工艺的基本原理、工艺流程、设备和应用等方面进行详细介绍。
一、基本原理旋压成型是利用机械力学和塑性变形原理,通过对金属材料进行旋转变形来实现的。
在旋压过程中,金属板或管材被夹紧在两个滚轮之间,其中一个滚轮固定不动,而另一个滚轮则通过电机带动旋转。
随着滚轮的不断转动,板材或管材逐渐被挤压和拉伸,并沿着滚轮的曲线运动,最终形成所需的几何形状。
二、工艺流程1. 材料准备:首先需要准备好所需要加工的金属板或管材,并根据设计要求切割成相应尺寸。
2. 设计模具:根据所需加工物品的形状和尺寸,设计相应的模具。
3. 夹紧材料:将金属板或管材夹紧在旋压机上,并调整好滚轮的位置和旋转速度。
4. 开始加工:启动旋压机,让滚轮开始旋转,并逐渐调整滚轮的位置和速度,使得金属板或管材逐渐弯曲成所需形状。
5. 检查质量:完成加工后,需要对成品进行检查,确保其符合设计要求和质量标准。
三、设备1. 旋压机:是实现旋压成型的核心设备,主要由底座、夹紧装置、传动系统、滚轮等组成。
根据不同的加工需求和规格,可以选择不同型号的旋压机。
2. 模具:根据不同加工物品的形状和尺寸设计相应的模具。
一般来说,模具可以分为圆锥形、球形、椭圆形等多种类型。
3. 辅助设备:如切割机、钻孔机等辅助设备可以帮助完成材料准备工作,并提高生产效率。
四、应用1. 容器制造:利用旋压成型技术可以制造各种形状的容器,如锅、盆、罐等。
2. 金属零部件:旋压成型技术可以制造各种形状的金属零部件,如轴承、齿轮、法兰等。
3. 装饰品制造:利用旋压成型技术可以制造各种形状的装饰品,如灯罩、花盆、雕塑等。
4. 工艺品制造:旋压成型技术可以制造各种形状的工艺品,如铜器、铜像等。
总之,旋压成型工艺是一种非常实用和广泛应用的金属加工技术。
旋压成型工艺

旋压成型工艺
旋压成型工艺是一种常见的金属加工技术,通过旋压机将金属板材或管材在一定范围内进行旋转和压缩,从而实现所需形状的加工。
这种工艺在制造行业中被广泛应用,能够高效、精准地生产出各种复杂的金属零部件。
旋压成型工艺的优势在于可以实现金属材料的塑性变形,使得原材料得以充分利用,减少浪费。
与传统的切削加工相比,旋压成型能够减少材料的消耗,提高生产效率,降低生产成本。
同时,旋压成型还可以实现一次成型多道工序,减少人工干预,提高生产精度和稳定性。
在实际应用中,旋压成型工艺可以用于生产各种形状和尺寸的金属零部件,如锥形零件、球形零件、椭圆形零件等。
通过调整旋压机的参数和工艺流程,可以实现对金属材料的精确控制,确保加工出符合设计要求的产品。
除了常规的金属加工,旋压成型工艺还被广泛应用于特种材料的加工,如不锈钢、铝合金、铜合金等。
这些材料通常具有较高的硬度和强度,传统加工方法难以满足其加工要求,而旋压成型能够通过塑性变形实现对特种材料的加工,保证产品的质量和性能。
在实际生产中,旋压成型工艺还可以与其他加工工艺相结合,如冷冲压、焊接、抛光等,实现复合加工,满足不同产品的加工需求。
通过优化工艺流程和设备配备,可以进一步提高生产效率和产品质量,满足市场需求。
总的来说,旋压成型工艺作为一种高效、精准的金属加工技术,在制造行业中具有重要的应用前景。
随着科技的不断进步和工艺的不断完善,相信旋压成型工艺将会在未来发展中发挥越来越重要的作用,为制造业的发展注入新的活力。
旋压技术分类及应用

旋压技术分类及应用:
1.根据变形特征主要可分为两类,普通旋压和强力旋压。
普通旋压包括缩经旋压(文丘里阀),扩经旋压,制梗,分离嗯,焊接旋压。
强力旋压包括筒形流动变薄旋压(多用于军工),锥形剪切变薄旋压(料斗)。
2.根据旋轮与毛坯的相对位置,分为内旋压和外旋压,常见的旋压加工多数为外旋压。
3.根据是否加热。
分为冷态旋压和加热旋压。
冷态旋压,常见一般性金属多为冷态旋压。
加热旋压,加热旋压主要用于一些抗拉强度高,延伸率差的稀有金属,如钼,钛合金,镍等。
- 1、下载文档前请自行甄别文档内容的完整性,平台不提供额外的编辑、内容补充、找答案等附加服务。
- 2、"仅部分预览"的文档,不可在线预览部分如存在完整性等问题,可反馈申请退款(可完整预览的文档不适用该条件!)。
- 3、如文档侵犯您的权益,请联系客服反馈,我们会尽快为您处理(人工客服工作时间:9:00-18:30)。
和计算,或根据经验和相关数据图表等确定旋压道次数k。当道次。大于20~22, 则必。大于20~22,则必须用一个或几个中间芯模进行多工序旋压。 ④ 画出实体芯棒的一半,再沿其端面画出毛坯的一半,然后按夹角a分别为10°、 20° 、30°、40 °、50 °、 60°、70 °的各射线的交点,以及DT/2的数值 近似地画出锥形件半成品直径连续变化的曲线。 DT/2是根据毛坯变形部分面积 相等的原则。
4)表面质量:
① 工件外表面粗糙度是由旋轮的工作型面和旋压工艺参数形成的。具有较长的 压光带和较大工作圆角半径的轮旋轮,减少进给率,提高模具转速,均可以提高 旋压件外表面质量。 ① 旋轮圆角半径和进给率是影响工件外表面粗糙度的主要工艺因素;提高外表 面质量还考虑如下措施: 1、防止机床振动和爬行; 2、以上旋轮前产生隆起失稳妥 3、加强润滑及减小旋轮成形角(工作角)
六、旋压件的质量控制
1)金相组织
• 变薄旋压件的坯料在旋轮压力作用下产生塑性变形时,晶粒内部 在一定的滑移面上沿一定的方向产生滑移,由此引起晶粒形状的 畸形变,旋压变形或经热处理使金相组织均匀致密。
• 室温变薄旋压时,晶粒被压扁毛拉长,在旋压方向形成纤维组织。 旋压工件壁厚变形不是均匀的压缩,而是由外向内逐渐加强,当 旋压减薄率大于40%时,壁厚变形组织的均匀性基本一致。随着 减薄率的增加,工件晶粒细化加剧,同时材料中的夹杂物形态被 破碎或拉长,减轻了对材料强度的不良影响。
5)残余应力:
旋压变形伴随一定的切向扭曲。由于组织性能、旋压温度、各层金属变形量的不 一致,以及工件内外摩擦的影响,旋压形是不均匀的。
材料在塑性变形时,受旋轮和模具的摩擦作用而改变流动状况,使旋压件沿壁厚 方向产生速度梯度,引起工件内层附加应力,即残余应力。摩擦力越大则残 余应力越大。
七、旋压件的缺陷、产生原因和防止措施
民用制造:炊具,照明器材,通风设备,汽车零件,消防, 医疗等器械。
二、金属旋压工艺
1.旋压工艺方案和选择
1)旋压方式的选择
主要是从成型件的形状、毛坯尺寸、工艺特点等方面加以考虑。对于筒 形件,一般指采用正旋压或反旋压。对于锥形件和曲母线形件,一般指 剪切旋压或普通旋压,或指剪切旋压和普通旋压联合方式。此外,无论 强力旋压还是普通旋压都有内旋压和外旋压之分。
6)旋压温度
在加热条件下的强力旋压,会使其工艺过程复杂化,但热旋压已作为强力化旋压 工艺应用范围和解决难成形材料加工的有效措施。强力旋压时的加热温度与普通 冲压时采用的加热温度略同。毛坯越厚加热温度越高,但不要高于材料的再结晶 温度,以防止发生再结晶。
五、旋压道次规范和旋轮运动轨迹
1)影响旋压道次规范因素
变薄旋压
• 坯料形状与壁厚同时改变的旋压成形过程称为变薄旋压,又称为 强力旋压。变薄旋压与普通旋压的区别是变薄旋压属于体积成形 范畴,在变形过程中主要使壁厚减薄而坯料体积不变,成品形状 完全由芯模尺寸决定,成品尺寸精确度取决于工艺参数的合理匹 配。
3.应用领域:
国防建设:航天航空,导弹,火箭,飞机零件,子弹。
• 2)对毛坯的要求
• 1)对毛坯内外层的要求:
① 毛坯内部不得有隔层、夹杂、裂纹和疏松等。 ② 毛坯表面不得有斑痕、加工印记、裂纹和毛刺等缺陷。 ③ 毛坯表面的污垢和鳞皮应除掉,以免压伤制件和弄脏润滑剂。
• 2)对毛坯尺寸精度要求:
① 毛坯壁厚偏差的影响; ② 对毛坯内径偏差; ③ 预制毛坯的椭圆度和毛坯不同部位的不同轴度; ④ 毛坯底部与其轴线不垂直度; ⑤ 毛坯与其芯模间的偏差;
2)毛坯的处理
毛坯的原始状态对旋压件的质量影响很大。
3)旋压设备的选用
为了实施所选定的工艺方案和旋压工艺规范,必须选用适合的旋压机, 并选配合理的工艺装备,以便生产优质产品,获得较高的技术经济效果。
2.毛坯的种类及要求
• 1)毛坯种类:
① 平板坯; ② 由平板坯预成型的毛坯; ③ 经车削的锻造毛坯; ④ 焊接的毛坯; ⑤ 经车削的铸造毛坯; ⑥ 轧制或挤压的管坯; ⑦ 用粉末金法生产的毛坯; ⑧ 用圆锭作为毛坯;
⑧ 旋压硬材料时可以使用硬质合金旋轮。 ⑨ 旋轮和芯模的偏摆小,因为它影响表面精整。 ⑩ 使用平面旋轮消除预旋轮的旋压痕迹。
⑪ 为了降低工件内表面的粗糙度,与它相接触的芯模部分最好不进行润滑, 让毛坯与芯模直接接触而得到精整并强制压光。
4)工件扭转的影响及其防止的方法:
① 旋轮圆角半径小则扭转角小。
旋压技术
一、旋压技术的发展与概述
1.发展简介
• 金属旋压是一种金属塑性成型的加工工艺。 • 旋压成型过程是一个复杂的弹性变形过程,边界接触条件的非线性,使得旋
压成型机理更为复杂。
• 由于旋压机理的复杂性、旋压工件个点的应力,应变分布很不均匀;受诸多 工艺参数的影响、旋压成型工艺也较为复杂。
• 对旋压过程进行数值模拟,定性地分析减薄率、旋轮成型角、 料与磨具间的 摩擦系数对旋压结果的影响;
③ 应该从材料性能方面分析是否容易开裂。延伸率小的材料不适 于拉深旋压。
④ 芯模与旋轮的间隙过大则工件内表面呈现梨皮状,有时还导致 壁部断裂,所以间隙应留得适当。
3)表面精整的质量的控制和处理:
① 工件表面出现的旋轮压痕是与旋轮圆角半径和旋轮进给速度有关系的。旋 轮圆角半径大而进给速度小一般能使表面光洁。
2)防止壁部断裂的措施:
① 多道次拉深旋压时每一道次的间距p要取得小。 ② 拉深旋压时旋轮进给速度取得太小,否则旋轮就会在毛坯同时
一处施旋多次,从而容易拉薄壁部。
① 变薄施压时旋压进给速度取得太大反而容易断裂,所以必须选 取合适的进给速度。
② 旋轮圆角半径R不要过小。如果t0/ R太大,则在拉深旋压时会 加大旋轮前面形成的环节的阻力而使壁部断裂。
4)进给速度
芯模每转一圈时旋轮芯模母线移动的距离称为进给量。与零件的尺寸精度、旋压 力的大小和毛坯的减薄率都有密切关系。进给量较大,有利于旋压件贴膜;其值 较小,有利于提高表面光洁度。
5)旋轮安装角
芯模轴线和旋轮轴线构成的角称为旋轮安装角B。 B值可在0<B<a+(π /2)的范围 内任意选择。通常可取B=a或B=(π / 2)安装角不能过大,以免旋轮前沿过深压入 毛坯和零件过渡区内,是金属流向旋轮前面,从而造成极粗糙的锉齿形表面。消 除这种现象,增加大旋轮圆角半径或减小进给量和减薄率。
3)尺寸精度:
• 旋压件的直径精度有内径与外径之分,壁厚精度有壁厚差之别。 壁厚偏差是壁厚的实际尺寸相对于基本尺寸的差别,壁厚差是壁 厚实际尺寸之间的差值,它与壁厚的基本尺寸无直接关系。
• 影响旋压件尺寸精度的主要因素:
①简单的小规格工件尺寸精度容易提高,反之则降低。 ②坯料椭圆度与壁厚差小,则有利于保证尺寸精度。 ③芯模与旋轮加工尺寸精确,是旋压高精度产品的基础。 ④有效控制合理工艺参数,工件收径贴模可获取高精度产品。 ⑤主轴偏摆小和导轨间隙小,设备的精度与状态良好,旋压产品精度高。 ⑥芯模与主轴良好配合,旋轮轴间隙合理,有助于旋压件尺寸精度的提高。
1)旋压件的缺陷、产生原因
旋压制品产生缺陷的原因和影响精度的因素有如下几个方面: 1、毛坯,包括材料、热处理和硬化程度等条件; 2、旋轮的形状,包括外径D、成形角a和顶端圆角半径等; 3、旋轮的进给比、壁厚减薄率、道次程序以及润滑条件等; 4、成形方式,包括正旋和反旋。
2)成形时采用的措施和注意事项 1)防止起皱的措施:
② 若允许使用黏度系数大的润滑油则表面均匀发暗。 ③ 旋轮的工件面最好经过研磨。 ④ 要使工件内表面美观就应将芯模表面加工的光洁,最好是镀硬烙。
⑤ 采用从压预制件时需注意预制形状,尤其是角部圆角大小,因为这影响旋 压表面的质量。
⑥ 旋压铝件或铜件时,用硬质合金压头轻轻推压,这样进行精整是很有效的。
⑦ 以变薄旋压为主成形铝制件时,使用塑料旋轮很有效。但用在多道次拉深 旋压时,需注意表面会留下多道次旋压的痕迹。
① 对板坯进行旋压时,应放慢旋轮的进给速度和拖板的进给速度。 ② 加大毛坯转速。 ③ 在旋轮的反面加反推辊,使其和旋轮一起夹住毛坯,从而减缓 每转的弯曲变形。 ① 旋压之前可以使用卷边装置将毛坯的边缘卷边,以提高其抗皱 能力。 ① 减小旋轮的圆角半径。 ② 在可能的情况下,一般采用较厚的板坯。因为起皱的容易度与 板厚的平方成反比。 ① 多道次拉深旋压时,旋轮都不要旋到毛坯的外缘为止,而应在 中途转移到下一道次。凸缘宽度小时容易起皱,因此若不妨碍最好 在每一道次都留一点凸缘的情况下进行成形。
• 加热变薄旋压时,温度高于合金再结晶温度,在变形过程中将发 生再结晶现象,使材料趋向于恢复原组织状态,材料旋后的组织 变化不显著。
2)力学性能:
① 旋压件金相组织变化的同时,其力学性能也相应地变化。金 属材料变薄旋压后,强度指标提高,由于加工硬化,塑性指 标降低。此外,材料的电阻率增大,热导率和磁导率降低, 内应力使材料抗腐蚀性降低。
5)工件的形状和尺寸精度
① 在球形、抛物面形以及凸形壳体件成形中,旋压终了处的芯模与工件之间 可能出现间隙,致使工件产生若干形状误差。
② 为了获得准确的形状,必须事先考虑卸件后的弹量,并把它估算搭配芯模 中去,即修正芯模的结构尺寸。
③ 旋轮进给速度选择和调整得适当就能获得高的形状精度。
⑦ 由于工件的形状和成形条件的多样性,对于扭转还不能从定量 上予以说明,只能从成形情况来判断。一种观点是旋轮与毛坯 的接触面积增大,尤其是因为变薄而增加了总接触面积时就增 大了扭转角,旋轮进给速度小时瞬时接触面积小,但总接触面 积增大,所以扭转角增大,当旋轮圆角半径小时则接触面积小, 所以减小了扭转角。
3.毛坯的设计计算
一般的锥形件的毛坯计算
强力旋压锥形件,工件减薄量要严格遵守正旋律
计算:t= t0Sina 圆板毛坯的直径D0计算: D0=D理+ ∆