旋压机工作原理
旋压机技术之旋压成型的基本方式拉深旋压
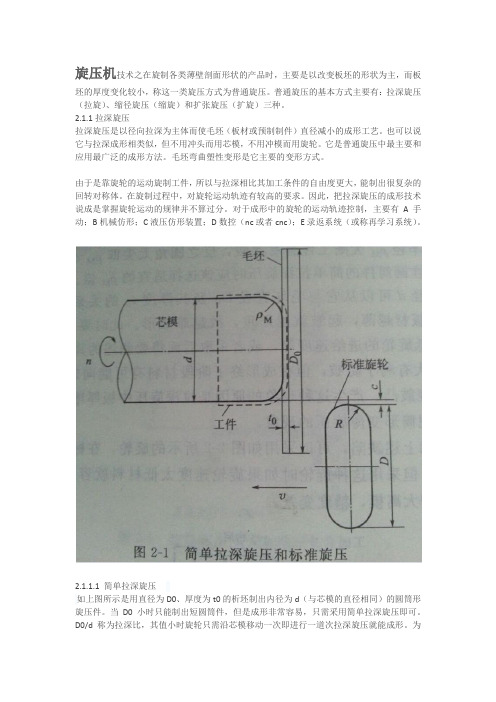
旋压机技术之在旋制各类薄壁剖面形状的产品时,主要是以改变板坯的形状为主,而板坯的厚度变化较小,称这一类旋压方式为普通旋压。
普通旋压的基本方式主要有:拉深旋压(拉旋)、缩径旋压(缩旋)和扩张旋压(扩旋)三种。
2.1.1拉深旋压拉深旋压是以径向拉深为主体而使毛坯(板材或预制制件)直径减小的成形工艺。
也可以说它与拉深成形相类似,但不用冲头而用芯模,不用冲模而用旋轮。
它是普通旋压中最主要和应用最广泛的成形方法。
毛坯弯曲塑性变形是它主要的变形方式。
由于是靠旋轮的运动旋制工件,所以与拉深相比其加工条件的自由度更大,能制出很复杂的回转对称体。
在旋制过程中,对旋轮运动轨迹有较高的要求。
因此,把拉深旋压的成形技术说成是掌握旋轮运动的规律并不算过分。
对于成形中的旋轮的运动轨迹控制,主要有A手动;B机械仿形;C液压仿形装置;D数控(nc或者cnc);E录返系统(或称再学习系统)。
2.1.1.1 简单拉深旋压如上图所示是用直径为D0、厚度为t0的析坯制出内径为d(与芯模的直径相同)的圆筒形旋压件。
当D0小时只能制出短圆筒件,但是成形非常容易,只需采用简单拉深旋压即可。
D0/d称为拉深比,其值小时旋轮只需沿芯模移动一次即进行一道次拉深旋压就能成形。
为区别于多道次拉深旋压而称它为简单拉深旋压。
旋压机旋轮只应沿芯模运动以保证它与芯模的间隙C。
在实际成形中还需考虑下面几个问题。
(1)旋轮的形状通常选用直径为D、顶端圆角半径为R的圆孤状旋轮。
将上图中所示的旋轮称为标准旋轮。
(2)旋轮的进给速度通常用拖板运动的速度u0(m/min)表示,但由于在判断成形的效果时要考虑毛坯的转速,因此毛坯每转的旋轮移动量U的大小是极为重要的因素,称其为旋轮进给量。
例如在进给速度U不变的条件下,如果毛坯转速增加一倍,则旋轮相对毛坯的运动距离变为原来的1/2,这样瞬间成形量就变小了。
(3)芯模的形状在上图中的情况下芯模是圆柱形,其直径为d,端部拐角处的圆角半径为pm。
旋压技术

旋压技术基本概念金属旋压技术的基本原理相似于古代的制陶生产技术。
旋压成型的零件一般为回转体筒形件或碟形件,旋压件毛坯通常为厚壁筒形件或圆形板料。
旋压机的原理与结构类似于金属切削车床。
在车床大拖板的位置,设计成带有有轴向运动动力的旋轮架,固定在旋轮架上的旋轮可作径向移动;与主轴同轴联接的是一芯模(轴),旋压毛坯套在芯模(轴)上;旋轮通过与套在芯模(轴)上的毛坯接触产生的摩擦力反向被动旋转;与此同时,旋轮架在轴向大推力油缸的作用下,作轴向运动。
旋轮架在轴向、旋轮在径向力的共同作用下,对坯料表面实施逐点连续塑性变形。
在车床尾顶支架的位置上,设计成与主轴同一轴线的尾顶液压缸,液压缸对套在芯模(轴)上的坯料端面施加轴向推力。
旋压成型有普通旋压和强力旋压成型两种。
不改变坯料厚度,只改变坯料形状的旋压叫普通旋压成型;即改变坯料厚度,又改变坯料形状的旋压叫强力旋压成型。
强力旋压成型所需要的旋压力较大,旋压机的结构一般也较复杂。
强力旋压成型又依旋轮移动的方向与金属流动的方向,分为正旋和反旋。
旋轮移动的方向与金属流动的方向相同,叫正旋;反之,称为反旋。
同一种材料,反旋成型所需的旋压力较大。
采用哪种旋压方式成型,要依据零件的形状和工艺要求确定。
旋压机的选型由旋压工艺及多种成型工艺条件要求确定。
旋压机分强力旋压机和普通旋压机二大类型。
强力旋压机又分双旋轮和三旋轮。
还有用于特殊零件旋压的旋压机,如热旋压机、钢球旋压机等。
我国金属旋压成型技术的发展历史近四十年,而在国防工业的应用研究尤为广泛,研究应用水平很高,特别是在旋压成型工艺及装备方面,已经处于国内领先地位。
旋压机的设计和制造能力也很强。
旋压技术简介什么叫旋压技术,也叫金属旋压成形技术,通过旋转使之受力点由点到线由线到面,同时在某个方向给予一定的压力使金属材料沿着这一方向变形和流动而成型某一形状的技术。
这里,金属材料必须具有塑性变形或流动性能,旋压成形不等同塑性变形,它是集塑性变形和流动变形的复杂过程,特别需要指出的是,我们所说的旋压成形技术不是单一的强力旋压和普通旋压,它是两者的结合;强力旋压用于各种筒、锥体异形体的旋压成型壳体的加工技术,是一种比较老的成熟的方法和工艺,也叫滚压法。
螺旋压榨机工作原理
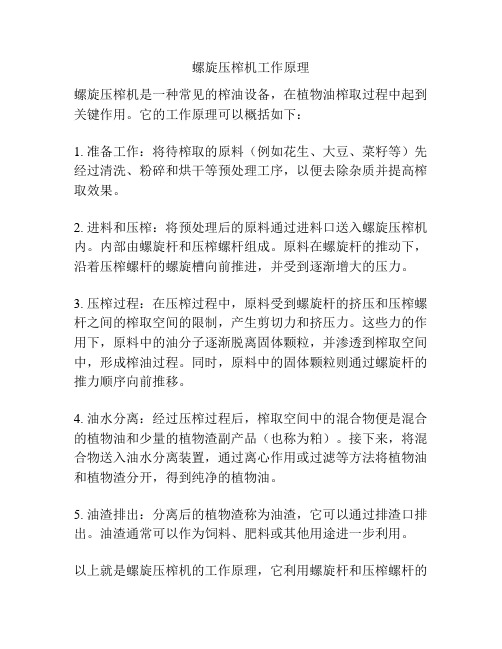
螺旋压榨机工作原理
螺旋压榨机是一种常见的榨油设备,在植物油榨取过程中起到关键作用。
它的工作原理可以概括如下:
1. 准备工作:将待榨取的原料(例如花生、大豆、菜籽等)先经过清洗、粉碎和烘干等预处理工序,以便去除杂质并提高榨取效果。
2. 进料和压榨:将预处理后的原料通过进料口送入螺旋压榨机内。
内部由螺旋杆和压榨螺杆组成。
原料在螺旋杆的推动下,沿着压榨螺杆的螺旋槽向前推进,并受到逐渐增大的压力。
3. 压榨过程:在压榨过程中,原料受到螺旋杆的挤压和压榨螺杆之间的榨取空间的限制,产生剪切力和挤压力。
这些力的作用下,原料中的油分子逐渐脱离固体颗粒,并渗透到榨取空间中,形成榨油过程。
同时,原料中的固体颗粒则通过螺旋杆的推力顺序向前推移。
4. 油水分离:经过压榨过程后,榨取空间中的混合物便是混合的植物油和少量的植物渣副产品(也称为粕)。
接下来,将混合物送入油水分离装置,通过离心作用或过滤等方法将植物油和植物渣分开,得到纯净的植物油。
5. 油渣排出:分离后的植物渣称为油渣,它可以通过排渣口排出。
油渣通常可以作为饲料、肥料或其他用途进一步利用。
以上就是螺旋压榨机的工作原理,它利用螺旋杆和压榨螺杆的
推动和挤压力,对原料进行压榨,实现植物油的榨取,并通过油水分离装置将油和渣分离。
这种工作原理在植物油加工中被广泛应用。
旋压机技术之旋压成形的基本方式缩径旋压
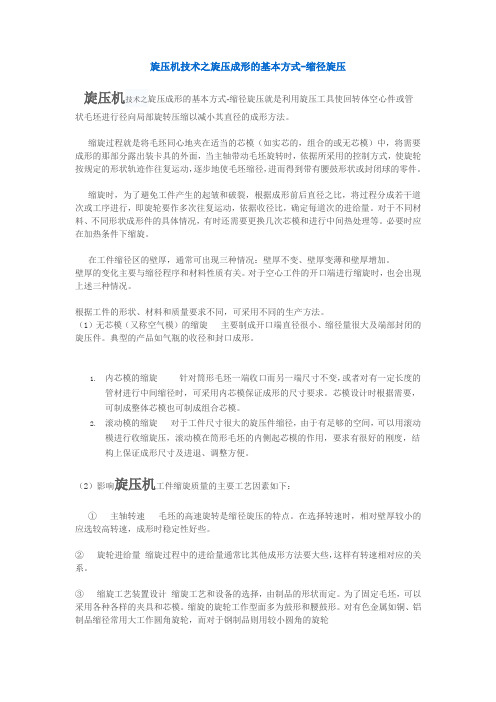
旋压机技术之旋压成形的基本方式-缩径旋压旋压机技术之旋压成形的基本方式-缩径旋压就是利用旋压工具使回转体空心件或管状毛坯进行径向局部旋转压缩以减小其直径的成形方法。
缩旋过程就是将毛坯同心地夹在适当的芯模(如实芯的,组合的或无芯模)中,将需要成形的那部分露出装卡具的外面,当主轴带动毛坯旋转时,依据所采用的控制方式,使旋轮按规定的形状轨迹作往复运动,逐步地使毛坯缩径,进而得到带有腰鼓形状或封闭球的零件。
缩旋时,为了避免工件产生的起皱和破裂,根据成形前后直径之比,将过程分成若干道次或工序进行,即旋轮要作多次往复运动,依据收径比,确定每道次的进给量。
对于不同材料、不同形状成形件的具体情况,有时还需要更换几次芯模和进行中间热处理等。
必要时应在加热条件下缩旋。
在工件缩径区的壁厚,通常可出现三种情况:壁厚不变、壁厚变薄和壁厚增加。
壁厚的变化主要与缩径程序和材料性质有关。
对于空心工件的开口端进行缩旋时,也会出现上述三种情况。
根据工件的形状、材料和质量要求不同,可采用不同的生产方法。
(1)无芯模(又称空气模)的缩旋主要制成开口端直径很小、缩径量很大及端部封闭的旋压件。
典型的产品如气瓶的收径和封口成形。
1.内芯模的缩旋针对筒形毛坯一端收口而另一端尺寸不变,或者对有一定长度的管材进行中间缩径时,可采用内芯模保证成形的尺寸要求。
芯模设计时根据需要,可制成整体芯模也可制成组合芯模。
2.滚动模的缩旋对于工件尺寸很大的旋压件缩径,由于有足够的空间,可以用滚动模进行收缩旋压,滚动模在筒形毛坯的内侧起芯模的作用,要求有很好的刚度,结构上保证成形尺寸及进退、调整方便。
(2)影响旋压机工件缩旋质量的主要工艺因素如下:①主轴转速毛坯的高速旋转是缩径旋压的特点。
在选择转速时,相对壁厚较小的应选较高转速,成形时稳定性好些。
②旋轮进给量缩旋过程中的进给量通常比其他成形方法要大些,这样有转速相对应的关系。
③缩旋工艺装置设计缩旋工艺和设备的选择,由制品的形状而定。
旋压机的工作原理

旋压机的工作原理
旋压机的工作原理是利用机械力和压力的作用将金属材料进行成形。
其基本工作原理如下:
1. 初始状态:在旋压机的工作台上放置待加工的金属材料。
工件应选择具有一定的可塑性和可变形性的金属材料,例如铝合金、钢等。
2. 夹紧工件:工件通过夹具或夹具系统夹紧,以固定在工作台上。
3. 旋转工具:旋压机配备有旋转的工具,如旋转模具或旋转滚轮。
这些工具在操作过程中会施加外力。
4. 施加力量:旋压机启动后,旋转工具开始施加力量到工件上。
压力可以通过液压系统、气压系统或机械传动等方式产生。
5. 成形过程:旋转工具在施加的力的作用下,以旋转或滚动的方式移动在工件表面上。
工具的接触点在金属材料上产生轨迹,使材料受到压力和摩擦力的作用,从而产生塑性变形。
6. 成品产生:随着旋转工具的移动和施加的力逐渐改变金属材料的形状。
通过控制工具的运动轨迹和施加的力的大小,可以实现不同形状的成品。
成品可以是圆柱形、锥形、球形、槽形等。
7. 处理后的工件:一旦成形完成,旋压机停止运动,工件可以
通过夹具松开并取出。
根据要求,工件可能需要进行后续加工或处理,如切割、研磨、清洗等。
以上是旋压机的基本工作原理。
根据实际需要和技术要求,旋压机的结构和工作过程可能有所不同,但基本的原理是相似的。
旋压
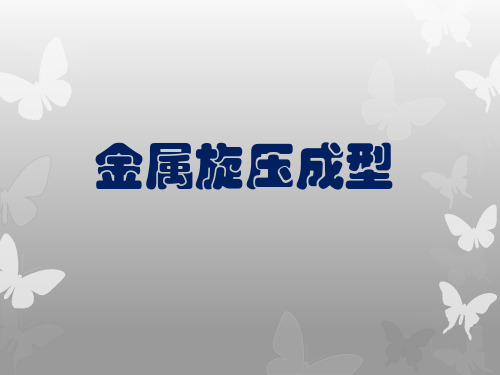
1.2.2强力旋压
1.3旋压的特点
旋压是一种特殊的成形方法。用旋压方法可以完成各种形状旋转体的 拉深、翻边、缩口、胀形和卷边等工艺。金属旋压工艺具有节省原材料、 成本低廉、设备简单和产品质量高等优点;因此,旋压工艺在国防、化工、 冶金、电子、机械等诸方面起到了越来越大的作用,特别在火箭、导弹、 核电、宇航等有关零件的制造方面得到了很好的应用,不仅用于工业上的 锅炉封头、压力容器、储油罐的生产上,而且还用于千家万户的水壶、锅 子、餐杯、洗衣机鼓桶、灯罩等的制造之中。
2.旋压工艺参数的选择
2.2旋轮安装角
芯模轴线和旋轮轴线构成的角称为旋轮安装角。
安装角不能过大,安装角过大会使加工金属流向旋轮前面,从而
导致极粗糙的锉齿形表面。根据加工要求和加工轨迹路线,灯罩旋压 工艺选取了45°安装角。
2.3主轴转速
提高转速,可以改变零件表面的光洁度,并提高生产效率,但主轴转速的 提高也有限制。① 受主轴最高转速和额定转速的限制,批量生产时主轴转速保 持在额定转速以内为宜。② 由于主轴转速的提高会使零件表面的温度升高,从 而改变零件表面的物理特性,所以在提高主轴转速的同时也要兼顾温升的变化, 例如铝制品加工时,主轴转速过高而产生的高温会加大产品表面的粗糙度。灯 罩旋压加工中,根据主轴性能和工艺要求选择了2500r/min。
1.概述
二是,在20世纪60~70年代出现了能单向多道次进给的、电器液压程序 控制的半自动旋压机。三是,由于电子技术的发展,于20世纪60年代后 期,国外在半自动旋压机的基础上,发展了数控和录返式旋压机。这些 设备的快速发展将旋压工艺带进了中、大批量化的生产中。 近20年来,旋压成形技术突飞猛进,高精度数控和录返旋压机不断 出现并迅速推广应用,目前正向着系列化和标准化方向发展。在许多国 家,如美国、俄罗斯、德国、日本和加拿大等国己生产出先进的标准化 程度很高的旋压设备,这些旋压设备己基本定型,旋压工艺稳定,产品 多种多样,应用范围日益广泛。 我国旋压技术的发展状况与国外先进水平相比有较大差距。但近年 来取得了较大发展,许多产品精度和性能都接近或达到了国外较先进水 平。国内许多研究所(如北航现代技术研究所、黑龙江省旋压技术研究 所、长春55所等)已经研制出了性能较好的旋压机。
一块铁板高速旋转,压一下就变成了半圆球,这就是金属旋压工艺
一块铁板高速旋转,压一下就变成了半圆球,这就是金属旋压
工艺
导读
金属旋压成型,是一门针对钣金的对称旋转成型工艺,常常被应用在家具,灯具,餐具,航天等行业。
金属旋压成型,原理是由主轴带动坯料与模芯旋转,然后用旋轮对旋转的坯料施加压力。
由于旋压机的主轴的回转运动及工具的纵、横向进给运动,这一局部塑性变形便逐渐地扩展到整个坯料,从而获得各种形状的空心旋转体零件。
视频时长3分22秒,建议WiFi观看
上面这种属于最普通的旋压,一般也就是加工成弧形或者圆形,尖端的科技技术一都是军工技术,而军工技术都是严格封锁保密的更不要说出口了,而军工技术一旦运用到民用行业,可能产生巨大的影响。
军工领域严禁出口的旋压技术民用,助力变速箱国产化。
视频2分32秒,建议WiFi观看
可能有金粉会问,金属旋压这样的工艺看起来也不是很难,为什么上文却提到需要“严格保密”?小编提供一个思路:
2018年德国某次内阁会议上宣布将禁止德国机械工具公司莱费尔德金属旋压公司出售给中国投资者的决定。
图为德国机械工具公司莱费尔德金属旋压公司产品。
金属塑性加工方法——旋压(一)
金属塑性加工方法——旋压(一)
金属塑性加工是一种通过施加力和应变来改变金属形状和结构
的方法。
旋压是金属塑性加工的一种常见方法,它使用旋压机将金
属材料塑性变形成所需的形状。
旋压原理
旋压的原理是通过旋转金属材料来施加力和应变。
旋压机由一
个圆筒形的工件和一个将工件固定在轴上并施加旋转力的夹具组成。
在旋转的同时,夹具还会向工件施加一定的径向力。
这样,金属材
料就会在旋转和径向力的作用下发生塑性变形。
旋压过程
旋压过程可以分为以下几个步骤:
1. 原料准备:选择适合旋压的金属材料,并根据所需形状和尺
寸切割成合适的工件。
2. 夹具调整:将工件固定在旋压机的夹具上,并根据需要调整夹具的径向力。
3. 旋压加工:启动旋压机,使工件开始旋转。
同时,夹具会施加一定的径向力,使金属材料开始塑性变形。
4. 修整和检验:完成旋压加工后,对成品进行修整和检验,确保其达到质量要求。
旋压应用
旋压方法适用于许多金属材料,如铝、铜、不锈钢等。
它常用于制造圆形或柱状的工件,如轴承套、奖杯底座等。
旋压有许多优点,包括:
- 简单而高效的加工过程。
- 较低的材料浪费。
- 产生的工件表面质量高。
结论
旋压是一种常见的金属塑性加工方法,适用于制造圆形或柱状的工件。
它通过旋转金属材料和施加径向力来改变其形状和结构。
旋压具有简单高效、材料浪费少和工件表面质量高的优点。
在实际应用中,我们可以根据需要选择合适的金属材料和夹具参数来进行旋压加工。
旋压详细资料
旋压的基本原理和加工工艺详解利用旋压工具(旋轮或擀棒)和芯模使毛坯边旋转边成形,生产金属空心回转体件的一种回转成形工艺。
旋压时,金属毛坯随芯模旋转或旋压工具绕毛坯和芯模旋转,旋压工具相对芯模作进给运动,从而使毛坯受压并产生连续局部变形以获得空心回转体零件,如图所示。
旋压时,旋压工具与毛坯接触面积小,毛坯只局部产生塑性变形,所需变形力小,可用小吨位的设备加工大型空心回转体制品。
旋压产品具有较高的尺寸精度和较低的表面粗糙度,力学性能好。
旋压工具制造简单,更换容易。
但旋压产量较低,品种受到一定限制,多适用于小批量多品种的产品。
旋压是一种古老的加工方法。
早在10世纪初,中谚藤:国就使用旋压方法把银锡等金属板旋压成各种器皿。
20世纪以来,旋压工艺在工业上得到广泛应用。
目前旋压工艺不仅用于加工铝、铜及其合金,而且越来越多地用于加工钢铁和稀有金属。
旋压的产品有日常生活用具、化工容器、各种形状的机器零件,航天器、航空器和火箭导弹的各种壳体部件等。
旋压按加工温度分为冷旋压、温旋压和热旋压。
一般多采用冷旋压。
旋压按金属变形特征分为普通旋压和强力旋压。
普通旋压改变毛坯的形状,扩大或缩小直径而基本不改变厚度的旋压方法。
这种旋压多用于成形各种薄壁的铝、铜、不锈钢等生活用具,如灯罩、炊具及手工艺品等。
普通旋压包括缩径旋压(缩旋)和扩径旋压(扩旋)。
此外,还可以完成一些切割、搭接等工作。
普通旋压有手工旋压、半自动旋压和自动旋压等。
缩径旋压使毛坯产生径向收缩的一种普通旋压。
缩旋除在旋压工具作用下使整体旋压成形外,还可以进行收口、收颈、压槽和收边等局部变形。
扩径旋压使毛坯产生径向胀大的一种普通旋压。
它除了整体扩旋成形外,还可以翻边、扩颈、扩口和压槽等局部成形。
扩颈旋压采用芯模在毛坯之外而旋轮在毛坯之内的内旋压法。
普通旋压工艺参数主要考虑坯料的尺寸和性能、旋轮进给量、仿形板的型面、道次间距及旋轮形状等。
普通旋压坯料一般用板坯。
旋轮进给量厂是芯模每转一圈时,旋压工具沿芯模母线移动的距离;常选,f=0.3~3m/r,f过大时制品易起皱,过小时制品易拉薄。
普通旋压——第三组
四、普通旋压工艺特点
• 与冲压相比,金属旋压能大大简化工艺所用的装 备,一些需6~7次冲压的制件,旋压一次即可做 出,旋压机床比相同能力的冲床价格便宜一半。 • 旋压过程中,被旋压坯料近似逐点变形,任何夹 渣、裂纹、砂眼等缺陷都容易暴露出来,起到制 品检验作用。 • 坯料来源广。
旋压件
四、普通旋压工艺特点
缺点: 除圆筒件、圆锥件、椭圆件等薄壁回转体零 件外,其他复杂形状的零件用旋压法生产往往是 不经济或难加工的,而且旋压的坯料厚度不能太 大,极限尺寸可查表。 金属旋压工艺的批量有一定限制,过大过小 都不合算,以中小批量为宜。批量在1000件以下 时,旋压件较冲压件的成本便宜;超过1000件, 旋压件比冲压件贵。
The end,thank • 翻边 卷边 压沟 滚筋
三、普通旋压工艺 a) 旋压力 b) 成形极限
c) 影响因素
旋压力
计算原理采用叶山假设(参课本P123-125), 计算值受μa影响较大。 工程上采用如下公式: P=(0.2~0.4)бb 其中,P为普旋的单位塑流压力, бb为所旋压材料 的抗拉强度。
(二)缩径旋压
利用旋压工具使回转体空心件或管状毛坯进行 径向局部旋转压缩以减小其直径的成形方法。 缩旋过程是将毛坯同心地夹在适当的芯模中, 将需要成形的那部分露出装夹具的外面,当主轴带 动毛坯旋转时,依据所采用的控制方式,使旋轮按 规定的形状轨迹作往复运动,逐步地使毛坯缩径。
(三)扩径旋压
• 利用旋压工具使回转体空心件或管状毛坯进行局 部直径增大的成形方法。根据芯模形式,分为: 用外芯模的扩旋法 用支承滚轮扩径法
多道次拉深旋压
用于拉深比大的深圆筒件或其他形状复杂的工 件,通过旋轮的多循环移动将毛坯逐次旋成成品, 而旋轮借靠模仿形装置按指定方式自动往复直到旋 出零件。
- 1、下载文档前请自行甄别文档内容的完整性,平台不提供额外的编辑、内容补充、找答案等附加服务。
- 2、"仅部分预览"的文档,不可在线预览部分如存在完整性等问题,可反馈申请退款(可完整预览的文档不适用该条件!)。
- 3、如文档侵犯您的权益,请联系客服反馈,我们会尽快为您处理(人工客服工作时间:9:00-18:30)。
旋压机工作原理
旋压机是一种广泛使用于金属加工行业的机器设备。
它可以将扁平金属材料,通过旋转和挤压的方式,加工成复杂的圆形和曲线形状。
旋压机的工作原理是基于金属的塑性变形原理,通过施加强大的压制力,使金属发生变形而完成加工。
本文将详细介绍旋压机的工作原理,以及它在金属加工中的应用。
一、旋压机的结构与工作原理
旋压机由机架、立柱、工作台、滑块、挤出轮、定位杆、主轴、传动机构等部分组成。
机架是机器底部的结构,支撑着所有的机械部件。
立柱是机架上竖立的立柱,其作用是支撑滑块。
工作台则是旋压机的工作平台,可以让操作者方便地操作和观察加工过程。
滑块是放置在立柱上的移动部件,可以左右移动以及上下移动。
挤出轮是旋压机的核心部分,它是旋转的轮轴,可以将材料挤压变形。
定位杆是用于定位材料的,主轴是用于支撑挤出轮的轴承。
传动机构则是用于将电机的转速传递给挤出轮,使其可以旋转。
而加工过程中,施力杆通过挤压作用使金属材料发生变形,从而得到加工后的圆形的产品。
旋压机最重要的组件是挤出轮,它的工作原理是通过将已经切割好的金属条材送入挤出轮,挤出轮进行旋转,
同时也要施以强大的压力,其作用是将金属材料逐步变形,从而得到所需要的圆形、椭圆形甚至自定义形状的金属产品。
二、旋压机的应用
旋压机在业界的应用十分广泛,其能够加工的金属种类涵盖了包括铜、铁、铝、钛等等在内的所有基础金属。
旋压机目前主要应用于生产具有圆形、椭圆形或者带有凸起的曲线形状的轧花铺贴、装饰品、灯饰零件、家居装饰、电子产品外壳等等。
特别是在铜雕和艺术制品领域,旋压机应用广泛。
其通常用于制作盘状和球状的古典铜雕装饰、桥梁、钟表零件、人物头像等。
因为旋压机形状的灵活性,加工出来的金属产品可以达到非常复杂的曲线形态,特别适合于需要细腻表现的艺术制品。
三、旋压机的优缺点
旋压机的优点是具有较高的加工速度、加工质量高、精度高,表面光滑、易处理等特点。
特别适合于加工规模较小,但品质要求较高的产品。
旋压机的缺点主要在于制造成本较高,同时由于加工过程太过繁琐复杂,高要求的技术和操作技能也是必须的。
因此,使用旋压机进行生产产品的生产成本较高。
此外,旋压机加工过程中的废料比较多,废品率比较高,不
仅浪费了材料,也加大了成本。
一些金属材料很贵且不易加工时,旋压机加工的成本会更高,另外用旋压机加工的产品无法完全保证各个部位的厚度一致,如果需要更高更均匀的厚度控制,还需要通过其它加工工艺进行处理。
四、总结
在整个金属加工行业中,旋压机的应用具有广泛性和重要性,通过上述介绍,我们可以清晰地了解到旋压机的工作原理、在金属加工领域中所发挥的重要的作用以及在实际使用中存在的缺点和优点。
虽然这样的机器造价较高,但其与其他机器加工方法相比,能够为需要高品质、多变形的生产环节提供更好的加工解决方案。