轧制润滑与过滤
冷轧钢板中轧制乳化油的选用

冷轧钢板中轧制乳化油的选用1.乳化液的分类通常,乳化液可根据乳化后的稳定性分为稳态乳化液、半稳态乳化液和非稳态乳化液三类。
乳化 液的稳定性是一个极其重要的指标,其测定方法是将油品配制成一定浓度的乳化液,在一个分料漏斗 中静置8分钟,然后将最底下和最上面的四分之一溶液分离出来。
用离心分离法测定两部分的浓度, 然后以最底下部分的油含量对最上面部分的油含量比例构成乳化液的稳定指数,用ESI表示。
1.1 稳态乳化液稳态乳化液,以精炼轻、中质矿物油和合成酯为主要成分,再加入多种添加剂,如脂肪酸、脂肪 油、阴离子和非离子型等表面活性剂,极压添加剂,防锈剂,抗氧剂,抗泡剂等。
此类乳化液可在室 温下将浓缩油直接加入水中形成稳定的乳化液,稳定指数ESI在0.6以上,皂化值小于50,使 用浓度为5%至10%。
配制后的乳化液颗粒大小在1至1.5微米之间,少数可达5微米。
稳态乳 化液具有良好的退火清洁性,可以不经清洗而直接退火。
1.2 半稳态乳化液半稳态乳化液,以精炼脂肪油、合成酯和矿物油的混合油为基油,另加入分散剂,极压添加剂, 防锈剂,抗氧剂等添加剂组成。
此类乳化液需在50至60℃温度下,将油在水中调配成乳化液。
配 制好的乳化液颗粒大部分为1至10微米,比稳态乳化液,因此半稳态乳化液在使用过程中需不断搅 拌并保持一定的温度,防止部分基油从乳化液中析出。
半稳步态乳化液的使用浓度为2%至7%,皂 化值在50至130之间。
半稳态乳化液的润滑性能较稳态乳化液好,但其清洁性较差,故退火前需 经脱脂清洗。
1.3 非稳态乳化液非稳态乳化液的主要成分是动、植物油如牛油、菜仔油等,加入极压添加剂,抗氧剂,防锈剂, 乳化剂等。
这类乳化液对钢板和轧辊的附着性好,可大幅降低摩擦系数,润滑性能特别好。
但残炭多, 退火前必须经过电解脱脂。
非稳态乳化液的皂化值在150至230之间,使用浓度5%至10%。
以上三类乳化液的皂化值,润滑性,冷却性及清净性之间的关系如图1所示。
轧制油

轧制油的特性及润滑机理1、轧制油的主要作用润滑—减小轧辊与铝箔之间的摩擦,提供稳定的摩擦界面,实现稳定轧制,提高表面质量。
冷却—带走金属的变形热和摩擦热,调整轧辊表面温度,控制板形。
清洗—清洗铝箔表面铝粉和机架内的皂化物和铝粉。
2、轧制油的要求轧制油应有良好的润滑性能、冷却性能和高温高压状态下的稳定性能,轧制时不能发生明显的变质;轧制时挥发量要小,退火时易挥发,不形成油斑;无毒,对人体无害。
3、轧制油的组成轧制油由基础油和添加剂组成。
4、基础油的生产方式、质量指标和主要作用4.1 生产方式基础油的生产方式见图1。
4.2 基础油的主要理化指标粘度:油的粘稠程度,主要由取决于碳链的长短。
在其它参数不变的情况下,粘度越高,轧制速度越低。
轧制油随着使用时间的增加,粘度会增加。
馏程(初馏点与终馏点之间的温度差):主要由取决于碳链的长短。
当我们确定了油品的粘度后,馏程宽,就意味着初馏点低,终馏点高,油的挥发大,退火除油困难,使用时粘度动大,速度变化大。
现在粗轧和中精轧基础油的粘度都在30℃以内(粗轧:216~246℃,中精轧:208~238℃)闪点:将油品放在在一个密闭的容器中加热,随着油品温度的升高,油的蒸汽浓度也会增加,能使油品遇见明火发生闪火时对应的最低油品温度点叫闪点。
是衡量油品安全程度的指标。
现在我们三台轧机油的蒸汽浓度均达到了着火的条件,只要有明火或相当于明火的温度,就会发生火灾。
因此,应严格控制明火和机架内的高温。
芳烃:原油中本身存在的一种物质,有一定的香味,也叫芳香烃。
芳烃对人体有害,美国FDA要求轧制油中的芳烃含量应小于1.0%。
现在我们公司使用的基础油芳烃含量小于0.3%,不会对人体产生危害。
硫含量:油品中单质硫和硫化物的总含量。
硫对设备有腐蚀,加速油品的变质。
但硫对润滑有好处(提高极压膜强度)。
硫含量越低越好。
溴价:每100克油品所吸收溴(Br)的毫克数。
溴价的大小反映了油品中双键的多少,包括芳烃中的双键,是衡量油品稳定性的重要指标。
冷轧轧制油使用说明及安全说明书书
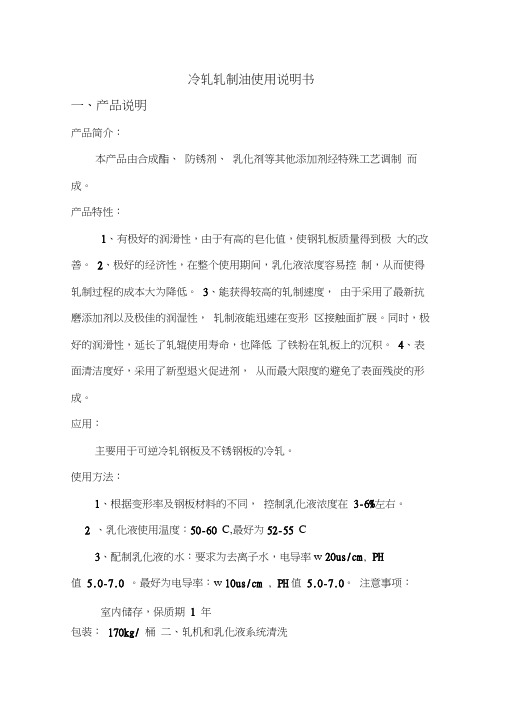
冷轧轧制油使用说明书一、产品说明产品简介:本产品由合成酯、防锈剂、乳化剂等其他添加剂经特殊工艺调制而成。
产品特性:1、有极好的润滑性,由于有高的皂化值,使钢轧板质量得到极大的改善。
2、极好的经济性,在整个使用期间,乳化液浓度容易控制,从而使得轧制过程的成本大为降低。
3、能获得较高的轧制速度,由于采用了最新抗磨添加剂以及极佳的润湿性,轧制液能迅速在变形区接触面扩展。
同时,极好的润滑性,延长了轧辊使用寿命,也降低了铁粉在轧板上的沉积。
4、表面清洁度好,采用了新型退火促进剂,从而最大限度的避免了表面残炭的形成。
应用:主要用于可逆冷轧钢板及不锈钢板的冷轧。
使用方法:1、根据变形率及钢板材料的不同,控制乳化液浓度在3-6%左右。
2 、乳化液使用温度:50-60 C,最好为52-55 C3、配制乳化液的水:要求为去离子水,电导率w 20us/cm, PH值5.0-7.0 。
最好为电导率:w 10us/cm , PH值5.0-7.0。
注意事项:室内储存,保质期1 年包装:170kg/ 桶二、轧机和乳化液系统清洗A设备准备阶段1、检查所有相关设备,包括排液泵,注入泵,溢流口及管道,脱盐水管道等,保证正常使用。
B乳化液切换清洗从一种乳化液切换到另一种乳化液,由于配方的机制不同,不能相互滥用,必须进行清洗,以使乳化液的影响降到最低,保证新乳化液的功能。
乳化液切换清洗过程如下:1、将轧机收集槽内的乳化液全部打回乳化液箱2、排放乳化液3、清洗乳化液全部循环系统的淤泥(包括轧机周围,收集槽、管道、过滤器、乳化液箱等)4、淤泥清洗完毕后,在乳化液箱中注入足够配制水5、循环2-5 小时,清洗所有设备和附属设备6、排放清洗水7、在乳化液箱中注入足够的配制水,升温至35-45 C8、配制合适0.5%浓度的新乳化液9、循环2-5 小时,充分清洗所有设备和附属设备10、排放乳化液,准备新乳化液的配制C乳化液的配制在完成必要的清洗工作后,可以进行乳化液的配制。
高速线材精轧机润滑系统油液污染控制

具 有 自动 排 气 功 能 。 二 、精 轧 机 润 滑 系统 污 染 物 的产 生及 危 害 经 过 分 析 ,发 现 精 轧 机 润 滑 油 的 主 要 污 染 物 是 固 态 悬
浮微粒及液态水。
运转 速度快 、@ N温度 高和连 续作业 的特点 。 因此 ,对 润 L 滑系 统的性能 、润滑 油的 品质 要求很 高 ,其 油液 清洁度 要 求为N S 级 。如果润 滑油清洁度达 不到要求 ,会影 响到精 A8
染物侵入 。 2 油 液 中水 污 染 产 生 的主 要 原 因: . () 热 交 换 器 的 内 部 泄 漏 。 北 方 地 区 水 质 较 硬 , 由 于 1 工 作 温 度 超 过 10 ,热 交 换 器 内部 液 流 管 道 容 易 结 垢 ,多 0% 次 酸 洗 将 会 使 内 部 密 封 圈 老 化 产 生 泄 漏 ,造 成 油 液 中 水 含 量急剧上升。
3 过 滤 器 ( 备 一 用 ) 过 滤 精 度 1t . 一 0z m,带 压 差 发 信 装 置 ,滤 芯 堵 塞 时 自动 报 警 。 4 压 力 罐 容 量 35 , 设 有 高 、中 和 低 点 液 位 报 警 点 , . . m, 当发 生 断 电 事 故 时 ,压 力 罐 可 作 为 应 急 能 源 供 给 润 滑 系 统
1 固态 污 染 物 侵 入 油 液 的 主 要途 径 : . () 精 轧 机 在 轧 制 过 程 中 ,机 械 传 动 件 会 产 生 大 量 的 1 污 染 物 ,如 齿 轮 、轴 承 等 磨 损 生 成 的 金 属 末 屑 ; 双 唇 密 封
与上 、下滑环 的磨损 颗粒 ;箱 体 内壁 剥落 的油漆碎 片 ;过 滤材 料脱落 的颗粒或 纤维 ;软管及其 他密 封材料 在油 中溶
不锈钢冷轧机反冲洗过滤系统的设计及应用

机组 稳 定 可靠 ,保证 了轧机 的稳 定运 行 。
关 键 词 :反 冲洗 系 统 ;工 艺 润滑 ;不 锈 钢 冷轧 机 中图 分 类号 :T 3 55 文献 标 识 码 :B 文 章编 号 :05 0 5 (0 2 6— 0 3 G 3. 24— 10 2 1 ) 16—
De i n a p i a i n o c wa h Fi e y t m n sg nd Ap lc to f Ba k s l r S s e i t
21 0 2年 6月 第3 7卷 第 6期
润滑与密封
L UBRI CAT1 0N ENGI ERI NE NG
J n 01 u e2 2
Vo . 7 No 6 13 .
D I 0 3 6 /.s . 2 4— 1 0 2 1 . 6 0 5 O :1 . 9 9 ji n 0 5 0 5 .0 2 0 . 2 s
轧制油介绍(DAStuart)

轧制油介绍招聘(广告)一. 简介1. 轧制润滑的历史第一台冷轧带钢的四辊连轧机在1930年之前开始投产。
在30年代和40年代初期,冷轧机所采用的润滑油的类型主要以棕榈油和水的混合物为基础,而润滑方法则采用直喷式系统向轧机喷油润滑(这种润滑系统类型现在仍然在使用)。
以后,开发了乳化液系统。
用棕榈油配制的粗乳化液以循环的方式向轧机喷乳化液润滑。
这种不稳定的乳化液总要求进行维护,而且不能很好地实现轧机的性能。
在1940年以后,由于棕榈油越来越难找到,而且价格很昂贵,因此,所开发的大部分在美国使用的冷轧油都使用动物油为基础。
随着工业的发展,更新、更高速度的连轧机变得更加盛行,改进轧制油的乳化技术成为更加关键的问题。
由于成本更高、环境保护的要求更加严格,直喷式乳化液润滑系统被逐步淘汰,并且开发了更先进的乳化液润滑技术。
由于每台轧机的乳化液系统的大小、泵的规格、集管喷头的设计、乳化液系统的设计、过滤器的设计、水源的情况、乳化液的配制步骤以及总体乳化液的维护方案等与其它轧机的都不相同,因此,每台轧机的轧制油的配方都与其它轧机的轧制油的配方不同。
在此期间内,极端压力添加剂的使用进一步增强了加到轧制油中的动物油的润滑性能。
由于对乳化液性能的要求越来越高,乳化液系统和添加剂的性能也必须改进和发展。
这些工业上的需求要求在乳化液技术领域内连续进行研究和开发,以便满足不断变化的对冷轧润滑油的要求。
2. 轧制油技术的发展1) 棕榈油直喷式润滑油系统(1940年前)2) 棕榈油加乳化剂循环式润滑系统(1940年前)3) 动物油加乳化剂直喷式和循环式润滑系统(战前)4) 动物油加先进的乳化剂系统(40-50年代)5) 动物油加:(60-70年代)1. 极端压力添加剂2. 先进的乳化剂系统(带油量和粒度概念)6) 动物油加:(当前)1. 各种润滑性添加剂2. 弥散剂(粒度与带油量之间的关系)3. 抗氧化剂4. 杀菌剂5. pH缓冲剂3. 应用轧制油的目的轧制油的功能是在轧辊和带钢的表面形成一个保护膜,由限制金属与金属之间的接触的方法来减小摩擦系数。
不锈钢轧制乳化油
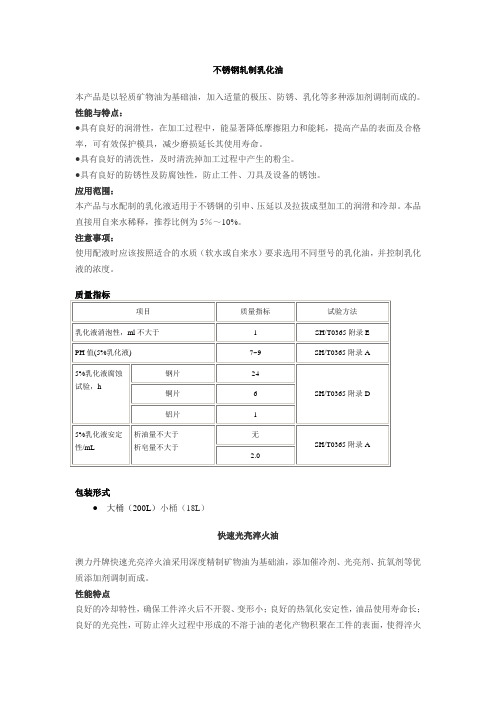
不锈钢轧制乳化油本产品是以轻质矿物油为基础油,加入适量的极压、防锈、乳化等多种添加剂调制而成的。
性能与特点:●具有良好的润滑性,在加工过程中,能显著降低摩擦阻力和能耗,提高产品的表面及合格率,可有效保护模具,减少磨损延长其使用寿命。
●具有良好的清洗性,及时清洗掉加工过程中产生的粉尘。
●具有良好的防锈性及防腐蚀性,防止工件、刀具及设备的锈蚀。
应用范围:本产品与水配制的乳化液适用于不锈钢的引申、压延以及拉拔成型加工的润滑和冷却。
本品直接用自来水稀释,推荐比例为5%~10%。
注意事项:使用配液时应该按照适合的水质(软水或自来水)要求选用不同型号的乳化油,并控制乳化液的浓度。
包装形式●大桶(200L)小桶(18L)快速光亮淬火油澳力丹牌快速光亮淬火油采用深度精制矿物油为基础油,添加催冷剂、光亮剂、抗氧剂等优质添加剂调制而成。
性能特点良好的冷却特性,确保工件淬火后不开裂、变形小;良好的热氧化安定性,油品使用寿命长;良好的光亮性,可防止淬火过程中形成的不溶于油的老化产物积聚在工件的表面,使得淬火后的工件表面光亮。
产品符合以下规格SH0564-93应用范围适用于要求高冷速调质、滲碳等零件和大型铸造件、大型齿轮及淬火压床淬火。
注意事项:严禁混入水或其它杂质,密封加盖防止接近热源,避免露天存放,日晒雨淋。
包装规格●170kg/钢桶冷轧薄板轧制油用途:适用于1700mm五机架串联冷轧机组,轧速为25~30m/s,厚度0.3mm以上规格板材。
特性:具有优良的润滑性、冷却性、易冲洗性及防锈性能,显著降低能耗。
注意事项:密封储存,避免混入机械杂质,需用时用水调成所需比例的乳化液。
包装规格●大桶(200L)小桶(18L)或散装不锈钢轧制油Ⅰ不锈钢轧制油是由高度精馏份基础油和精选的多种添加剂调配而成。
性能特点:优异的润滑性和冷却性,在有效防止热擦伤的同时,能及时携带走轧制过程中产生的摩擦热和变形热。
良好的粘压特性,轧材表面光亮。
高线精轧机组润滑系统污染与控制对策

加 强检 修人员 的管 理和培训 工作 ,提高润 滑系统维 护
知 识水平 ,严格执 行检修作 业标准和要 求 ,避 免人为 因素
1完善备件管理 ,防止密封件失效 . 保证双唇密封 、0 型圈等备件的质量。制定双唇密封更 换周 期并定周 期检查 。加 强对密封件 的保管 ,防止在存 放
粒 物排出油箱外 ,在系统含 水较多或发 生乳化无 法排 出时
启 动净油机对油液进行油水分离 。
四 、结 束 语
制定精 轧易损伤设 备检查 标准 ,当发生堆 钢或爆辊 后
及 时检查密封 板 、密封 骨架 、密封 圈 、机架等 。如发 现问
组成 ,每架机架 由一 台锥箱 和一 台辊 箱构成 。锥箱 及辊箱
齿 轮及轴 承采 用稀 油集 中循环 润滑 ,共有 三套 润滑 系 统 。
高 线精轧 、减 定径轧机 辊轴处使 用 的是 双唇骨架 密封 及 抛油环 ,由于轧机 工作时需要 冷却水冷却 ,冷却 水 回水 不畅极 易使 密封及 抛油 环长期 泡在 水里 ,密封 磨损 较快 , 如 不及时更换 ,将导致 大量 的冷却 水涌入轧 机 内部 ,同时 带 入大量 的氧化铁皮等杂质。
直接接触 ,一旦密封 面出现 问题 ,极易造成润滑系统进水 。
3 堆钢造成设备损伤 . 精 轧机辊箱 的密封板为 铜质 ,密封板及 密封 骨架 经过 堆 钢或爆 辊等严重的冲击后 ,变形严重 ,将导致密封不 严 ,
系统进水进渣 。 4 抛油环安装不到位 .
各 轧机抛 油环 安装 时高 度设 定不 合理 ,如 安装 过高 ,
2 提高安装质量 ,确保结合面安装质量 . 制定 辊箱更换作业 标准 ,保 证各结 合面安装 时要擦 拭 干净 ,并 涂上 防水胶 。在 更换辊 箱时 注意密 封 圈的安 装 。 同时在安装 时确保操作人 员不用手直接 接触结 合面 以免造
- 1、下载文档前请自行甄别文档内容的完整性,平台不提供额外的编辑、内容补充、找答案等附加服务。
- 2、"仅部分预览"的文档,不可在线预览部分如存在完整性等问题,可反馈申请退款(可完整预览的文档不适用该条件!)。
- 3、如文档侵犯您的权益,请联系客服反馈,我们会尽快为您处理(人工客服工作时间:9:00-18:30)。
轧机润滑知识普及一、润滑油轧制基础油由两部分组成——基础油、添加剂1、基础油为轻质矿物油,一般是碳链长度在12~15之间的正构烷烃。
从组成上分为两大类:一类是含芳香烃的基础油,是由直馏煤经分馏切割后获得。
二类是低芳烃的基础油(1%以下),由于加工工艺不同分成两种类型即为正构烷烃和饱和烃。
轧制油的分子式为C6H14——C16H34,是一种混合物,不是单一结构。
铝箔轧机和板带轧机使用的基础油不同。
板带轧机用粘度较高的基础油,箔材用粘度较低的基础油,这种方法既考虑了粗轧绝对压下大,需提高油的承载能力,又兼顾了精轧后消除油斑的要求。
2、对轧制油的要求:1)有良好的润滑性,摩擦系数小。
2)有较高的比热容。
3)容易带走较多的热量。
4)有足够的承载能力,能达到预期压下量。
5)退火时不易形成油斑。
6)有良好的抗氧化稳定性。
7)对设备、铝材无腐蚀作用。
8)无毒、无难闻气味,对人体健康无害。
9)容易净化和过滤,资源丰富,价格低廉。
3、轧制油的理化性能及其评价1)粘度:运动粘度作为润滑油一个重要的性能指标直接影响到成形过程的润滑性能。
此外油的粘度还会影响成形制品退火表面质量,其中有的粘度越高,表面油斑越严重。
另外,油的粘度与闪点、残炭及冷却性能还有一定的关系。
2)密度:一般油的密度都小于1.0g/cm3,而且油品粘度越低,其密度也越小。
大部分油品密度均为0.8~0.9 g/cm3,有些添加剂的密度则大于1.0 g/cm3。
3)闪点:在规定条件下加热油品,当油达到某一温度时,油的蒸汽和周围空气的混合气体,一旦与明火接触即发生闪火现象,此时的最低温度成为闪点。
4)倾点与凝点:油品在标准规定的冷却条件下,能够流动的最低温度成为倾点。
而凝点是在标准规定的实验条件下,将油品冷却到液面不移动时的最高温度。
倾点与凝点都表示油品早低温下流动性能的好坏,同时与油品成分组成中蜡含量有关。
5)馏程:石油产品是多种有机化合物的混合物,在加热蒸馏时没有固定的沸点,只有一定的馏程。
油品的馏程是指从初馏点到终馏点的温度范围。
当油品在规定的条件下,加热蒸出第一滴油品时的温度称为初馏点,而终馏点是指馏出量达到最末一个规定的馏出百分数时的温度。
5)酸值:酸值是表征油品中有机酸总含量多少的指标。
酸值的高低反映了油品生产的精制程度,精制程度越高其酸值越低。
另外酸值的大小还反映了油品中有机酸含量的高低,即对金属腐蚀程度的大小,特别是当油品中含有水分时,这种腐蚀作用可能更加显著。
另外油品被氧化发生变质时常常伴随酸值的升高。
所以酸值也是衡量油品抗氧化性和使用过程中油品老化变质情况的一项重要指标。
6)皂化值:皂化值是指皂化1g油品所需的KOH毫克数,单位为:mgKOH/g。
皂化值在乳化液中具有重要意义,它的高低代表了乳化液润滑性能的好坏,皂化值越高,润滑性能越好,但轧后退火板面清洁性也随之变差。
7)硫含量:硫含量是指油品中硫元素的含量,以质量百分比计。
由于硫对金属具有腐蚀性,故对金属成形油品中硫含量应进行控制。
8)芳烃含量:由于芳烃,特别是稠环芳烃在医学上被怀疑具有致癌性,所以在轧制食品和药品包装用金属薄板、箔材时,轧制油中的芳烃含量受限。
4、1)粘度与压力的关系随着所受压力的增加,润滑油分子间距减小,分子间作用力增大,因而粘度增加。
通常矿物油所受压力超过20MPa时,粘度随压力的变化开始显著。
压力继续增加,粘度变化增大。
2)粘度与温度的关系压力的增加使粘度急剧增加,而温度增加却使粘度急剧减小。
二、添加剂1、添加剂就是能够改善油品某种性能的有极性的化合物或聚化物,它是提高矿物油润滑性能的最经济、最有效的途径之一。
为了保证金属成形润滑剂的各种功能,添加剂是必不可少的。
铝合金轧制油常用的添加剂有三类:醇、酯、脂肪酸添加剂对轧制油性能的影响:2、对添加剂的要求1)提高工艺润滑油润滑性能,增加变形区内油膜强度,降低摩擦系数。
2)成分和性能稳定。
3)退火无污染。
4)对金属和设备无腐蚀。
5)无毒性。
无刺激性气味。
6)与基础油互溶性好。
7)使用经济,资源丰富,适于广泛应用。
8)添加方便。
3、作用机理1)添加剂可以改善润滑油的润滑性能,是一种带有极性分子的有机物质,它与金属具有很强的亲和能力,在变形区中添加剂牢固地吸附在金属表面。
通过与基础油之间的碳链缠绕是润滑油滞留在变形区中,形成薄而强的油膜,该油膜可承受很高的径向应力和剪切应力。
当该应力超过金属的屈服极限时,金属将发生塑性变形,这时加工过程可稳定正常进行从而是所生产出的产品表面质量好且设备能耗低。
2)温度影响。
由于添加剂是通过与金属表面发生物理或化学吸附来达到起作用效果,因此对温度特别敏感。
一些诸如载荷、速度等工艺条件对添加剂作用效果都可归结于温度变化对添加剂的影响。
三、硅藻土与活性白土1、硅藻土,是被称之为硅藻的单细胞植物死亡后经过1至2万年左右的堆积期,形成的一种化石性的硅藻堆积土矿床。
硅藻是最早在地球上出现的原生生物之一,生存在海水或者湖水中。
正是这种硅藻,通过光合作用向地球提供氧,促进了人类和动植物的诞生。
这种硅藻土是由单细胞水生植物硅藻的遗骸沉积所形成,这种硅藻的独特性能在于能吸收水中的游离硅形成其骨骸,当其生命结束后沉积,在一定的地质条件下形成硅藻土矿床。
它具有一些独特的性能,如:多孔性、较低的浓度、较大的比表面积、相对的不可压缩性及化学稳定性,在通过对原土的粉碎、分选、煅烧、气流分级、去杂等加工工序改变其粒度的分布状态及表面性质后,可适用于涂料油漆添加剂等多种工业要求。
2、组成3、铝加工在轧制铝板带、箔工艺过程中,对过滤轧制污油的助滤剂,一般有以下基本要求:1)由于现代化轧机上轧制油,每一个工作循环都要求全流过滤,助滤剂必须满足流量要求。
即在全流过滤时,在规定的时间内流量基本保持不变。
这一特性在过滤器上用入口压力来衡量,在定时连续运转时,进口压力达4kg/cm2,过早达到规定压力,不利于设备保持正常运转。
(严格讲是入口和出口的压力差,因出口压力很小,可忽略不计,一般用入口压力来表示)2)在满足流量要求的前提下,重要的是保证过滤效果,过滤后净油中最大杂质颗粒不大于0.5μm,净油中的灰分含量为0.05~0.005%。
3)助滤剂应有一定的极性,它不但能载留滤液中较大颗粒的杂质,而且能靠极性作用吸附颗粒极小的胶质。
4)过滤后的净油应清澈,当污油透光率不低于80%时,滤后净油的透光率应不低于90%,提高10个百分点。
5)污油过滤后灰分含量不应增加,经2小时沉淀,不应有可见沉淀物。
6)在过滤过程中,助滤剂不能截留轧制油中的添加剂。
7)不能含有有害健康的成分。
8)不能混有影响运行的杂质。
9)质量稳定均一。
4、硅藻土助滤剂在过滤中的作用及工作原理硅藻土助滤剂主要通过下列三种作用将悬浮在液体中的固体杂质粒子截留在介质的表面及沟道当中,从而达到固液分离的目的:一、筛分作用:这是一种表面过滤作用,当流体流经硅藻土时,硅藻土的孔隙小于杂质粒子的粒径,这样杂质粒子不能通过而被截留下来,这种作用被称之为筛分作用。
实际上可以把滤饼的表面看成是一个具有等效平均孔径的筛面,当固体粒子的直径不小于(或略小于)硅藻土孔隙直径时,固体粒子便会从悬浮液中“筛分”出来,起到表面过滤的作用。
二、深度效应:深度效应是深层过滤的阻留作用。
在深层过滤时,分离过程只发生在介质的“内部”,部分穿过滤饼表面的比较小的杂质粒子,被硅藻土内部而曲折的微孔沟道和滤饼内部更细小的孔隙所阻留,这种微粒往往小于硅藻土的微孔,当微粒撞到通道的壁上时,这就有可能脱离液流,但它是否能达到这一点,决定于微粒受到的惯性力和阻力的平衡,这种截留与筛分作用在性质上是类似的,都属于机械作用。
滤除固体粒子的能力基本上仅与固体粒子和孔隙的相对大小及形状有关。
三、吸附作用:吸附作用与以上两种过滤机理截然不同,这一作用实际上也可以看成是动电吸引作用,它主要取决于固体粒子与硅藻土本身的表面性质。
当那些硅藻土内部孔隙还小的颗粒碰撞在多孔硅藻土内部表面上时,被相反电荷所吸引,还有一种是粒子间的相互吸引形成链团而粘附在硅藻土上,这些都属于吸附作用,吸附作用比前两种作用复杂,一般认为,比孔隙直径小的固体微粒之所以被截留,主要是由于:(1)分子间力(也叫做范德华吸引力),包括永久偶极作用、诱导偶极作用和瞬间偶极作用;(2)Zeta电位的存在;(3)离子交换过程从以上三种作用看,在悬浮液的净压过滤过程中,采用松散颗粒状的硅藻土助滤剂作为过滤介质,主要是为过滤介质层即滤饼提供尽可能多的孔隙,以及形成的孔的间隔层,使悬浮液由此隔阂层的小孔中通过,将悬浮在液体中的固体杂质粒子截留在此介质的表面及沟道之中,从而使固液达到分离的目的。
硅藻土助滤剂一般分为两个步骤进行:1、在过滤前先用清液(已澄清的滤液或前一次已过滤好的滤液)或清水在过滤介质(滤网、滤布或滤纸)表面上涂敷一层硅藻土肋滤剂,然后进行过滤操作,这就是预涂过滤,这一涂层称作预涂层。
2、少量的助滤剂按一定的比例均匀分散到被滤液体中,被送入滤机的过程称作添加,这样助滤剂与原液中的悬浮固体杂质粒子混合并沉积到预涂上,新的过滤面不断形成,细小硅藻土助滤剂颗粒,拥有数不清的细小通道,可以阻塞杂质的通过。
予涂量是0.5~1kg/m2,予涂厚度是1~2mm,予涂浓度为6~12%,予涂时间为10分钟左右。
轧制油滤前存在杂质直径0.1~2mm的铝屑,0.1~1μm的氧化物和其他几微米的尘埃,由于轧制时间延续,小于10μm的颗粒逐渐增加而使轧制油黑化,如不及时去除会影响制品的表面质量,所以要选用优质的既能保证过滤速度、流量,又能去除造成油质黑化微粒的合适的硅藻土助滤剂。
硅藻土不带有极性,只是机械的过滤杂质,小一些的胶质需要用带有极性的活性白土过滤。
但是活性白土加入太少,不能全部吸取超细颗粒,轧制油过滤不净,逐渐变黑。
加入太多会带走轧制油中的极性物质——添加剂。
为防止添加剂被带走,保持良好的过滤效果,每天要根据灰分和透光率来确定活性白土的添加量。
通常采用75%的硅藻土和25%的活性白土组成过滤介质,这个比例运转时间是最长的,假如需要更高的清洁度,可增加活性白土的比例。
为了减少轧制油的残留物、微量水分和氧化物,添加活性白土的量是有效的,但势必增加添加剂的消耗量并缩短过滤周期。
四、润滑剂的毒性与防护由于工艺润滑剂是由有机和无机化合物组成,特别是添加剂如抗氧剂、防腐杀菌剂等可能会对人身造成一些危害,由于每个人对润滑剂中的一些化学成分敏感性不同,因此对引起的症状也不尽相同。
一般长期接触工艺润滑油的人,可能引起下列疾病:1)接触性皮炎。
水、溶剂、乳化剂、洗涤剂都可能使皮肤脱脂,导致干裂,引发接触性皮炎。
另外如果皮肤被润滑剂中的金属碎屑划伤也可能引发皮炎。