风机叶片(初稿)070430
风机叶片制作过程--考问讲解

红泥井风电场10月考问讲解11、预弯曲度:叶片逆风方向预弯曲,以防止运转过程中叶片朝向塔架变形。
12、导雷系统:接收和传导雷电的系统13、接收器:装进叶片表面的金属设备来传导电流以使叶片避免电击破坏。
14、叶片扭旋:所有叶片轮廓截面上的叶片扭旋。
四、叶片成型工艺:真空辅助固化成型:铺层完毕之后,进行叶片壳体的真空辅助固化成型,以排除预浸料铺层中多余的树脂及层间夹带的气泡。
1、叶片主要材料目前绝大多数大型风机叶片都采用复合材料,它是以玻璃纤维为增强材料,树脂为基体。
复合材料的优点:(1)拉伸强度高;(2)易成型性好;(3)耐腐蚀性强;(4)维护少、易修补;(5)比重小。
2、叶片轮廓图3、叶片制造过程1)预浸料的制作过程综述将预浸布送到模具混合树脂将混合好的树脂倒入预浸机中预浸机上安干布开始预浸模具准备涂脱模剂贴脱模布上胶衣树脂预浸料铺层、轻木等铺设脱模布、吸胶毡、真空膜开启真空系统及模具加热系统40~50℃预固化6小时胶接面间隙测量筋板高度调整上胶粘剂合模,60℃加热后固化6小时脱模筋板定位安装2)铺层过程详解:1、刷胶衣树脂2、铺设双轴纤维布3、在叶片根部铺设多层三轴纤维布4、铺设轻木(铺设范围距离根部3米到27米处铺设)5、铺设大梁(单轴纤维,铺设范围距离根部从3米多到37米多位置处)6、铺设泡沫7、在叶片根部铺设多层三轴纤维布8、在根部距离1米多到6米处附近铺设轻木9、在根部0米到1.1米处铺设三轴纤维布10、铺设双轴纤维※在根部铺设多层纤维布的原因一是加强叶片根部的受力情况;二是使得叶片根部具有足够的厚度以埋设螺栓。
3)筋板制作:4)避雷系统:避雷系统包括接闪器、电缆、导电记录卡、电缆根部连接。
电缆线在R20.00~R36.70处已在筋板车间预固定在T 筋板上,R20.00以后从T 筋板中间平滑过渡到SS 面筋板底部并一直到法兰区。
筋板制抽真空 固化脱加热后固筋板裁切割、修整5)配重:在两筋板的尖部插入两块玻璃钢板。
风力发电机的叶片设计方法研究(全面)
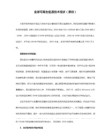
a c c i d e n c e d e s i g n , T h e s e w a y s h a v e o w n t e c h n o l o g y p o i n t s a n d d i s a d v a n t a g e , I n t h i s p a p e r s t e r s s l y d i s c u s s t h e m o m e n t u m - e l e m e n t t h e o yw r a y , t h i s w a y w a s d e v e l o p e d i n t h e b a s i c o f t h e t w o a h e a d w a y s , a n d i t o v e r c o m e t h e i r d e f e c t . I t a l s o u s e e l e m e n t t h e o yt r o d e lw a i t h v a n e d e s i g n . I n t h e v a n e d e s i g n i n g a n d a e r o d y n a m i c lc a h a r a c t e r i s t i c c a l c u l a t i n g t h e y b o t h r e l a t e w i t h i n t e r v e n e g e n e , s o t h e k e y s t o n e i s t o c a r r y t h r o u g h t h e i n t e r v e n e g e n e i n t w o c a s e , t h e r e o u t t o d o t h e v a n e d e s i g n a n d a e r o d y n a m i c a l c h a r a c t e r i s t i c c l a c u l a t i n g .
风力机叶片设计及翼型气动性能分析

风力机叶片设计及翼型气动性能分析风力机叶片是风力发电机的核心部件之一,其设计和翼型选择对风力机的发电效率、噪音和寿命等都有着非常重要的影响。
本文将介绍风力机叶片的设计及翼型气动性能分析。
一、叶片设计原理风力机叶片的设计目的是将大气中的风能转换成旋转能,并将其通过转轴传递给发电机,从而产生电能。
因此,叶片的设计主要围绕以下几点展开:1. 创造足够的扭矩:风力机的转子需要达到一定的转速才能发电,而叶片的弯曲和扭矩对于旋转速度的影响至关重要。
设计中需要选择合适的曲线形状和长度来实现理想的扭矩和转速。
2. 保证叶片的强度和稳定性:因叶片在高速旋转状态下会受到巨大的惯性力和风力力矩的作用,因此其材料和结构要足够坚固和稳定,以避免可能的断裂等事故。
3. 提高叶片的气动效率:叶片的气动效率是指其转化风能的能力,通常可以通过优化翼型、减小阻力、降低风阻等方法来提高。
二、叶片设计步骤1. 选定叶片长度:叶片长度通常是根据风力机的规格和性能要求来确定的,也可以根据标准长度来选择。
2. 选择翼型:翼型是叶片的重要组成部分,其形状和性能决定了叶片的阻力和气动效率。
目前,常用的翼型有NACA0012、NACA4415等,根据实际需求来选择。
3. 确定叶片曲线:叶片的曲线是决定扭矩和转速的关键因素,可以通过实验或模拟方法得到合适的曲线形状。
4. 优化叶片的结构:结构设计主要涉及到叶片的强度和稳定性,通常需要进行材料选择、计算等工作以保证叶片的安全性和寿命。
5. 模拟叶片气动特性:叶片的气动特性可以通过流场模拟、试验等方式来获取,可以根据实际需求来对叶片进行调整以达到理想的效果。
三、翼型气动性能分析翼型气动性能是指翼型在气流中运动时产生的力和力矩,其中,升力和阻力是翼型气动力的主要组成部分。
通过分析翼型气动性能,可以选择最优化的翼型来设计叶片。
1. 升力和阻力翼型的升力和阻力是由翼型形状、气流速度、攻角等因素共同决定的。
实际上,翼型的气动性能曲线通常都是非线性的,其升力和阻力特性会随着攻角的变化而不断变化。
风电叶片设计流程

叶片设计流程一.空气动力设计1.确定风轮的几何和空气动力设计参数2.选择翼型3.确定叶片的最佳形状4.计算风轮叶片的功率特性5.如果需要可以对设计进行修改并重复步骤4,以找到制造工艺约束下的最佳风轮设计。
6.计算在所有可遇尖速比下的风轮特性对于每个尖速比可采用上面步骤4 所述的方法,确定每个叶素的空气动力状态,由此确定整个风轮的性能。
7.风力机叶片三维效应分析非定常空气动力现象8.风力机叶片的动态失速9.10.叶片动态入流.风机载荷计算作为风力机设计和认证的重要依据,用于风力机的静强度和疲劳强度分析。
国际电工协会制定的IEC61400-1 标准、德国船级社制定的GL 规范和丹麦制定的DS 472 标准等对风力机的载荷进行了详细的规定。
2.1 IEC61400-1 标准规定的载荷情况2.2 风机载荷计算1 计算模型1 )风模型(1)正常风模型(2)极端风模型(3)三维湍流模型2)风机模型风机模型包括几何模型、空气动力学模型、传动系统动力学模型、控制系统闭环模型和运行状态监控模型等。
2 风力机载荷特性1)叶片上的载荷(1)空气动力载荷包括摆振方向的剪力Q yb和弯矩M xb、挥舞方向的剪力Q xb 和弯矩M yb 以及与变浆距力矩平衡的叶片俯仰力矩M zb。
可根据叶片空气动力设计步骤4 中求得的叶素上法向力系数Cn 和切向力系数Ct, 通过积分求出作用在叶片上的空气动力载荷。
(2)重力载荷作用在叶片上的重力载荷对叶片产生的摆振方向弯矩,随叶片方位角的变化呈周期变化,是叶片的主要疲劳载荷。
(3)惯性载荷(4)操纵载荷2 )轮毂上的载荷3)主轴上的载荷4 )机舱上的载荷5) 偏航系统上的载荷6) 塔架上的载荷三.风力机气动弹性当风力机在自然风条件下运行时,作用在风力机上的空气动力、惯性力和弹性力等交变载荷会使结构产生变形和振动,影响风力机的正常运行甚至导致风力机损坏。
因此,在风力机的设计中必须考虑系统的稳定性和在外载作用下的动力响应,主要有①风力机气动弹性稳定性和动力响应②风力机机械传动系统的振动③风力机控制系统(包括偏航系统和变浆距系统等) 的稳定性和动力响应④风力机系统的振动。
风力发电机组叶片设计原理研究

风力发电机组叶片设计原理研究随着对可再生能源的需求日益增长,风力发电作为一种清洁、可持续的能源形式受到了广泛关注。
在风力发电机组中,叶片是转换风能为机械能的核心部件。
因此,叶片的设计和性能对于风力发电机组的有效运行和高效能量转换具有至关重要的作用。
一、风力发电机组叶片的基本结构风力发电机组主要由塔架、转子、发电机以及叶片等组成。
而叶片是最为关键的部件,其主要作用是通过捕获风的能量并将其转换为机械能。
叶片通常由复合材料制成,具有一定的柔韧性和刚性。
叶片的设计需要综合考虑气动性能、结构强度、材料特性以及成本等因素。
二、叶片的气动性能设计原理1. 叶片的气动外形设计叶片的气动外形设计是指通过外形的优化来提高叶片的气动性能。
一般情况下,叶片的外形呈现出弯曲的特点,这有利于增加叶片的面积,并提高叶片对风的捕获效果。
此外,叶片的前缘和后缘也需要进行适当的设计,以减小阻力和噪音。
2. 叶片的空气动力学设计叶片的空气动力学设计是指通过几何参数和气动参数的优化,使其在风力荷载下保持较好的稳定性和动态特性。
在设计过程中,需考虑叶片的扭转角度、截面形状、厚度分布等参数,以及流场的响应和控制。
三、叶片的结构强度设计原理1. 叶片的结构形式设计叶片的结构形式设计是指通过选择合适的材料和结构形式来满足叶片在风力荷载下的结构强度要求。
常见的叶片结构形式有直桨叶片和弯曲叶片两种。
直桨叶片适用于小型和中型风力发电机组,而弯曲叶片适用于大型风力发电机组。
2. 叶片的材料选择和布局设计叶片的材料选择需要考虑材料的强度、耐疲劳性能以及可加工性等因素。
常用的叶片材料有玻璃纤维增强塑料(GRP)、碳纤维复合材料(CFRP)等。
此外,叶片的布局设计也是叶片结构强度设计的重要内容,通过合理的布局设计可以提高叶片的整体强度和稳定性。
四、叶片设计的优化方法1. 数值模拟方法数值模拟方法是一种常用的叶片设计优化方法,通过建立叶片的数学模型,利用计算流体力学(CFD)方法对叶片的气动性能和结构强度进行分析和优化。
第4章_风轮叶片设计

Ø
• • • • • Ø
Ø
l
Ø
• •
其他要求 对叶片设计的要求不仅需要参考和选用设计标准,还 应考虑风电机组的具体安装和使用情况。上述的叶片基本 设计要求,主要参考了IEC 61400—1[2]标准和德国GL的 《风力发电风电机组认证规范》中的有关规定,以下一些 要求仅供设计参考。 极限变形 由于复合材料的优良特性,大型风电机组风轮叶片的 设计首先考虑叶片的刚度是否满足使用要求,然后进行强 度校核。因此对叶片的极限变形要求极为重要: 避免风电机组运行过程中与塔架碰撞,要限制叶片在最大 设计风速时的极限变形; 在叶片变桨距时,应考虑气动弹性载荷对变形的影响。
Ø
Ø
Ø
Ø
l
结构设计要求
结构设计是形成叶片构件的关键设计过程,需要根据叶片所受的 各种载荷,并考虑风电机组实际运行环境因素的影响,使叶片具有足 够的强度和刚度。在规定的使用环境条件下运行时,应保证叶片在使 用寿命期内不发生破坏。另外,要求叶片的设计重量尽可能轻,并考 虑叶片间的相互平衡措施。 叶片的强度通常需要通过静强度和疲劳强度分析校核,受压结构 部分还应进行稳定性校核。强度分析应在足够多的截面上进行,需要 分析校核的横截面数目可根据叶片类型和尺寸确定,但至少应分析4 个以上的截面结构。同时,在叶片几何形状或材料不连续的位置,应 考虑增加必要的附加截面分析。 叶片强度分析可用相应的应变、应力等力学分析校核方法。对于 应力分析,还应额外校验最大载荷点处的应变,以确认设计结构不超 过材料破坏极限。
叶片结构设计的基本内容
n l
设计要求 气动设计要求
为了使风电机组有较高的风能利用效率,一般需要通过叶片气动 设计获得相应的设计参数或指标。采用葛劳渥(Glauert)、维尔森 (Wilson)或其他改进的可靠设计方法,通过计算确定叶片的气动外形 (如叶片的翼型、弦长、扭角、剖面厚度沿展向的分布等),并提供相 应的设计条件参数(额定叶尖速比等)。 根据有关设计标准或第2、3章的分析,气动设计过程通常需要确 定以下设计参数或指标: 设计风速 设计风速是叶片设计的重要基础参数,包括额定设计风速、切入 风速、切出风速以及相应的湍流条件等。 气动性能指标 气动设计需要确定叶片的气动功能特性,如风能利用系数CP、推 力系数CQ、转矩系数CT等指标。
风机叶片质量问题分析及监造要点
量薄弱环节,归纳为以下几个方面:
依赖性较大,产品质量均匀性波动较大,产品
(1) 叶片结构风险。叶片设计是依据仿生学 的动静平衡保证性差,废品率较高。工艺生产
图 2 叶片俯视图 图 3 叶片内部结构
图 1 风电机组的部件故障率
1 叶片的结构及制造工艺 1.1 叶片的结构
风机叶片是根据空气动力学特性设计的 叶片外形,叶片长度 30m~60m,单片叶片质 量 6t~18t,叶片后缘厚度较小;叶片结构多 采用壳体——双梁设计型式,叶片壳体较薄, 一般由根部、外壳和加强筋或梁三部分组成 如图 2、图 3 所示,复合材料在整个风机叶片 中的质量一般占到 90% 以上。 1.2 叶片的制造工艺
叶片的最薄弱环节处,通过外部因素作用产生的。
(4) 叶片制作工艺。一些叶片生产厂家为降
最初的小裂纹会随着空气中的颗粒物、风沙的侵 低生产成本采用手糊工艺,主要特点为手工操
入,风机的每次自振、停车等进一步逐渐的加深 作、开模成型、生产效率低以及树脂固化程度
加长。通过总结分析,叶片裂纹的产生原因及质 偏低,且对工人的操作熟练程度及环境条件的
叶 片 出 厂 前, 未 经 过 各 种 复 杂 而变化的环境,由于部分内在应力未 得到释放,故缺陷一般反映在表象, 主要集中表现为以下几个方面:
(1) 褶皱。主要是由于前期纤维 布未铺平、铺设存在搭接、夹杂杂质、 铺设后灌注前纤维布的滑落等因素 造成。
(2) 灌注缺陷。表现为玻璃钢含 胶不足、干纤维、爆聚、气泡等。主 要原因有:导流网铺设不合格 , 真空 测试未达标 , 灌注时模具温度、环境 温湿度未符合工艺要求,树脂混合程 度不达标等。
实务 Practice
风机叶片质量问题分析及监造要点
■ 向国鼎 王宪国 赵天宏 摘要:叶片是风电机组的关键部件。论文基于风电机组叶片的结构特点及生产工艺流程,通过 研究叶片制造环节工艺及质量,分析总结了叶片的常见缺陷及其产生的原因,如褶皱、裂纹等。 从设备监理角度出发,阐述了如何加强风机叶片监造工作,提出相关建议完善叶片质量管控要点, 从而提高叶片产品质量,为风电机组设备的安装与运行提供可靠质量保障。 关键词:叶片 质量 缺陷 裂纹 监造
风力机叶片模态分析及稳定性分析
风力机叶片模态分析及稳定性分析来源:中国玻璃钢综合信息网近年来,“能源危机”越来越引起人们的重视,能源短缺使得可再生能源得到空前发展。
风能作为取之不尽用之不竭的可再生能源在近几年得到了迅速发展,世界上不少国家都把开发利用风能作为一项能源政策。
风机叶片是风力机的关键部件之一,目前大型风机叶片的材料主要是轻质高强、耐腐蚀性好、具有可设计性的复合材料,由于叶片采用复合材料铺层设计,结构异常复杂,单纯的经典理论解析计算已难以精确计算出叶片的强度和刚度,为此需要进行有限元的仿真模拟。
本文采用ANSYS的参数化语言APDL直接建模,然后赋材料属性、划分网格,进行叶片模态分析,较好地模拟了叶片的真实结构,计算了叶片在自由状态下的固有频率和在20RPM下的预应力频率。
最后加载极限载荷校核了叶片各截面稳定性。
1叶片模型的建立1.1建立几何模型叶片截面的翼型数据通过CA TIA导出,结合弦长和扭转角计算出实际叶片截面的坐标。
在AN-SYS的程序中形成如下格式:k,,838.309405,-83.92648,0k,,771.63901,-338.19972,0根据1MW叶片翼型的特点,将叶片分为45个截面,每个截面上有86个关键点。
通过Bspline命令将每个翼型上的关键点连成18条曲线,然后将叶片翼型上的曲线通过纵向直线连接。
最后通过Askin命令建立曲面,每两个翼型截面之间就有18个曲面,建完所有曲面就生成了叶片蒙皮的几何模型。
如图1(a)所示,再布置上主梁、腹板,形成整体叶片的几何模型。
1.2建立有限元模型在单元类型的选择上,根据叶片特点,主要采用shell91和shell99单元,其中shell91单元用于模拟夹芯结构。
在定义材料性能参数时,主要采用定义实常数的方式来模拟材料的性能、铺层角和铺层厚度。
之后选择合适的单元尺寸进行网格划分,最终形成叶片的有限元模型。
该模型共有21295个节点,共划分了7414个高精度的壳单元。
文献综述 风机叶片发展研究
复合材料风机叶片发展研究综述高振宇华北电力大学科技学院 07k5[摘要]本文综述了风机叶片材料的发展历程,并介绍了其相关结构设计及成型工艺,最后对风机的发展趋势作了展望。
[关键字]风机叶片复合材料结构设计成型工艺引言随着我国国民经济持续发展,尤其是高能耗行业快速增长带动了我国能源需求特别是电力需求的快速增长,而如今煤炭等常规资源的严重紧缺和环境污染问题影响着电力和经济的发展。
因此开发和发展新能源和可再生资源以优化电力结构已成当务之急。
针对这种情况,风能无疑成了备受关注的焦点,用风力发电可减少常规能源的消耗,对保护环境、改善能源结构具有重要意义。
如今风电产业的迅猛发展带动了风电机组产业的快速发展,其中叶片是风电机组的最关键和最基础的部件之一,其良好的设计、优越的性能是保证机组正常稳定运行的决定因素。
其中,长期不停的运转和恶劣的环境需要叶片具有最佳的机械性能和疲劳强度。
故研究其材料、结构设计和成型工艺非常必要并且具有深远意义。
一、风机叶片应用材料我国最初的风电叶片以木材为原料,可谓是第一代叶片材料。
随后发展为钢材、铝合金等金属,但由于钢质叶片重量太重、铝质叶片的抗疲劳强度不佳,都遭到淘汰。
后来,玻璃钢叶片材料因为重量轻、强度高、可设计性强、价格比较便宜等因素,成为大中型风机叶片材料的首选。
然而,随着风机叶片朝着超大型化和轻量化的方向发展,玻璃钢复合材料开始达到其使用性能的极限,碳纤维复合材料(CFRP)逐渐开始应用到超大型风机叶片中去。
目前商品化的大型风力机叶片大多采用玻璃纤维复合材料(GRP)。
这种复合材料主要有以下优点:1、具有极佳的疲劳强度和机械性能,能经受住极端恶劣条件和随机负荷的考验。
2、容易成型。
由于叶片具有复杂的外形,用金属制造相当困难,而用复合材料则容易的多并且能进行批量生产。
3、耐腐蚀、抗紫外线性能好。
风力机安装在户外,如今又大力发展海上风电,叶片要受到各种环境的影响,要具有耐酸碱、抗氧化和风沙的性能。
- 1、下载文档前请自行甄别文档内容的完整性,平台不提供额外的编辑、内容补充、找答案等附加服务。
- 2、"仅部分预览"的文档,不可在线预览部分如存在完整性等问题,可反馈申请退款(可完整预览的文档不适用该条件!)。
- 3、如文档侵犯您的权益,请联系客服反馈,我们会尽快为您处理(人工客服工作时间:9:00-18:30)。
风力机翼型
风力机翼型的特点: • 风电机组叶片是在低雷诺数下运行,一般在0.7×106~ 10×106 范围,这时翼型的边界层特性变得很异常; • 风电机组叶片是在大迎角下运行,叶片各剖面处的入流角 (迎角)可以在0~90°范围内变化。这时翼型的深失速特 性显得十分重要; • 风电机组在偏航运行时,叶片各剖面处的入流角(迎角)是 周期性变化,必须考虑翼型的动态失速特性。 • 风电机组叶片在大气中运行,沙石、碎石、雨滴、油污等会 使叶片表面的粗糙度增加,影响翼型气动特性; • 从制造技术考虑,风电机组叶片的后缘不是尖的,而是钝的, 作了加厚处理; • 从结构强度和刚度考虑,风电机组叶片翼型的相对厚度大, 在叶片根部处一般可达30%左右。
m / adm 106
主材
辅材
常规 • 常规 – Polyester – 玻璃纤维GF – Epoxy – 碳纤维CF 创新 – 木集成材 – ?? • 创新 其他思路 – 竹材 – 多种选择 • 其他思路 – 混合Hybrid,合金
材料生态性能
材料 Description 密度 kg/cum 2700 能量 强度 kWh/kg MPa 60 0.33 290 30 单位载荷耗能 kWh/N 559 24 Aluminium Concrete Extrusions
The blades have to carry a large bending moment because of the wind loads. when it is gusty this load fluctuates badly because the control system cannot predict the gusts correctly all the time. This causes the blades to fatigue.
Walls (compressive 2200 loads only) 2400 700
Reinforced Concrete Beams Wood Steel GRP CFRP
Source: Chris Hornzee-Jones
0.7 1.33 11.5 26.4 60
30 80 275 150 600
4.2 初步设计
• 确定主参数 – 风轮直径 – 设计(额定)风速下的额定功率 – 叶尖速度 – 额定转速,转速范围 – 控制策略
4.3 细节设计-形状设计
• 翼型设计: – 叶型族,厚弦比,弦长, 叶根到叶尖的弦长变化, 扭角 • 优化目标: – Max Cp额定值 – =>max Cp均值 – =>Max AEP年发电量 • 设计的耦合 – 风资源统计特性 – 整机功率传递模型 – 控制策略
0.3
0.2
0.1
0.0
-0.1
-0.2
-0.3
-0.4 -200 -150 -100 -50 0 50 100 150 200
迎角α/(°)
风力机翼型
CL
流动迟滞现象
风力机翼型
动态失速现象
CD
α/(°)
CL
α/(°)
阻力特性
升力特性
The aerodynamics of the blade can be used to avoid this. When the airfoil stalls the air looses its grip on the blade and this can be used to control the power before it hurts the blade.
改进的转轮气动模型与诱导速度的计算
图4. 转轮旋涡气动模型
An airfoil works because of suction on the top.
The pressure is thought of as lift and drag forces, which increase as the angle of attack increases.
风力机翼型
翼型几何参数
t
相对厚度:t c 100%
风力机翼型
翼型升力特性
升力系数CL
迎角α/(°)
Байду номын сангаас
风力机翼型
翼型阻力特性
1.5
阻力系数CD
1.0
0.5
0.0 -200 -150 -100 -50 0 50 100 150 200
迎角α/(°)
风力机翼型
翼型俯仰力矩特性
0.4
俯仰力矩系数CM
4、叶片设计/制造/测试过程
• 叶片设计 – 概念设计 – 初步设计 – 细节设计 叶片制造 测试过程
• •
4.1 概念设计
The best blades are made of wood Veneers, glass-cloth and epoxy.
美国NREL提出的叶片基本翼型
(美国NREL)叶片铺层基本构造
ENERCON E112风力发电机组
3、 叶片空气动力学
• • BEM 动量叶素理论 CFD 计算流体力学
现有的转轮气动模型
图1. 风力机示意图
图2. 叶片某断面处的速度图
As the blades sweep the disk of air, the blade tip speed Is typically 6 to 10 times the wind speed.
对风机重量也是决定成本的重要因素
The wood is more than 50% of the blade weight and is the primary structural material. It makes these blades 5 times less energy intensive to make then their next nearest competitors. Where the blade fastens to the hub, metal studs have to be bonded in to make a bolted joint possible
4
5
triaxial fabric
1.27 mm
Aircraft designs are driven by performance to weight. 飞机设计是由性能重量比驱动 Wind turbine designs are driven by performance to cost. 风机设计由性能成本比驱动
If we look along a blade towards the tip, the combination of rotation speed and wind speed gives an angle of attack which means there is a forward power force, which drives the machine.
Aircraft do not go near the stall point, because they fall out of the sky if the wing stalls.
The aerodynamics can now be used to design the power cu
风机叶片介绍
明向军整理 2006年5月
目录
• • • • • • 1、风电叶片产业 2、叶片发展趋势 3、空气动力学 4、叶片设计、制造、测试 5、好叶片是怎样的? 6、未来的研究
1、风电叶片产业
叶片产业发展
• • • • • • • • • • • • • • In the beginning, the turbine was designed around an “off the shelf ” blade: – 90% of blades were out-sourced – Built in Western Europe and the U.S. • Today, turbines are specifically designed…driven by loads, site conditions, control strategies, and COE targets: – 50% of blades are out-sourced – Built in Western Europe and U.S….and Brazil, India, & China • In the future: – Majority of blades will be designed in-house – Built in low-cost countries
In high winds, the blade is rotated to reduce the angle of attack.
风力机翼型
风力机叶片的剖面形状称之为风力机翼型, 它对于风力机性能有很大的影响。目前风力机 叶片使用的翼型有NACA系列,FX系列,SERI 系列,FFA-W系列和DU系列等。
风电产业
风电产业
风电产业
风电产业
风电产业
叶片维护
2.叶片发展趋势
风轮叶片发展趋势
最大风轮叶片尺寸发展趋势
国外风轮叶片发展趋势
额定功率与叶轮直径的关系
单个叶片重量与叶轮直径的关系
Blade Mass Scaling – All Sources
NOI ATV Polymarin Euros LM
2.05 3.07 2.76 2.92 2.30
叶片 与转轮 共振图
国外风轮叶片发展趋势
国外风轮叶片发展趋势
风吹过叶轮后
叶片位移图
蓝色-负 红色-正
叶片设计与整机设计的关系