ISO9001-2015进料检验程序(中英文)
ISO9001:2015文件控制程序英文版

Procedure: [Control of Documents Proc. Title]1.0SUMMARY1.1.This procedure defines the requirements for the creation, review, approval, distribution, useand revision of [Short Client Name] quality management system documents.1.2.This procedure applies only to documents which instruct [Short Client Name] staff on how tocarry out activities and tasks; this includes manuals, procedures, forms and instructional sheetsor posters. Documents outside of this scope do not require control.1.3.The [who?] is responsible for implementation and management of this procedure.2.0REVISION AND APPROVAL3.0CREATION OF DOCUMENTS3.1.Documents are created by an appropriate subject matter expert.3.2.All internal documents are created as soft files (MS Word®, etc.); it is recommended that files ofa similar type follow the format of other documents in that type.3.3.Draft versions must then be sent to the appropriate approver(s) for review and approval.3.4.O riginal releases of documents are given a revision indicator of “0”. ( Revise per preferredrevision indicator method.)4.0REVIEW AND APPROVAL4.1.The [Quality Manual Doc Title] may only be approved by the [who?]. Other documents are to beapproved by the original author, an appropriate area manager or a company executive.4.2.Draft files may be sent to the approver(s) via hardcopy or e-mail.4.3.The reviewer will resolve any issues with the original author to achieve a satisfactory document.4.4.The reviewer will indicate approval of the document by [indicate method.]4.5.The approved document shall then be forwarded to the [Document Controller Title].4.6.[If hardcopy binder will be used] The [Document Controller Title] will maintain a binder of mostcurrent hardcopy versions of documents. Any previous hardcopies in this binder are to bediscarded or filed in an obsolete document file.4.7.The [Document Controller Title] will maintain a computer folder, on the company server, for thelatest soft copy versions of document. This fileset must be on a server subject to data backup.The [Document Controller Title] will place new or revised documents into that folder, settingeach file’s permission to READ ONLY, or converting the released vers ions to a non-editable fileformat.4.8.Any previous soft versions are then moved to a separate folder identified for obsoletedocuments which are kept for historical purposes.4.9.The directory of official released documents shall act as a “master list” of docume nts, indicatingthe current versions of all documents. No other master list is required.5.0DISTRIBUTION OF DOCUMENTS5.1.[If intranet is used] Controlled documents will be available via the intranet for all employees.Employees receive training on the file and folder locations for most current documents.5.2.[If hardcopy document distribution is used] The [Document Controller Title] will maintain a listof where controlled hardcopy documents are to be distributed. The [Document Controller Title]will be responsible for distributing updated copies of such controlled hardcopies to properlocations. Controlled hardcopies shall be stamped CONTROLLED in red ink on the first page, todistinguish them from uncontrolled documents or photocopies.5.3.Controlled hardcopies may not be altered or modified by users, and must remain legible andreadily identifiable. This includes hand mark-ups by unauthorized personnel. The only exceptionto this rule is for Forms (see below.)5.4.Controlled hardcopies may not be photocopied, unless for the purposes of sending to a recipientwho is authorized to receive uncontrolled versions of [Short Client Name] documents (i.e., avendor or customer). The only exception to this rule is for Forms (see below.)6.0RE-EVALUATION6.1.Documents must be reviewed by the original author or another subject matter expert or top6.2.The [Document Controller Title] will ensure re-evaluation is conducted and that documents areupdated if required. The [Document Controller Title] will maintain a record of document re-evaluations, to identify when documents are due for re-evaluation.6.3.If a document is determined to require updating, the changes shall be made and a new versionissued per the rules below.6.4.If a document is determined not to require updating, no action on the document is necessary.7.0REVISING DOCUMENTS7.1.Changes to documents go through the same steps as original issue, except that their revisionlevel is advanced upon approval.7.2.Only authorized personnel may change documents, although any employee can request achange to their Manager, or by filing a [CAR Form Name] [or other document change requestform.]Wherever possible, the document shall include a change history table within its text.[Other methods for identifying changes might be use of Track Changes feature in document,。
ISO9001:2015-English-Version

ISO 9001:2015Quality management systems —RequirementsIntroduction0.1 GeneralThe adoption of a quality management system is a strategic decision for an organization that can help to improve its overall performance and provide a sound basis for sustainable development initiatives. The potential benefits to an organization of implementing a quality management system based on this International Standard are:a) the ability to consistently provide products and services that meet customer and applicable statutory and regulatory requirements;b) facilitating opportunities to enhance customer satisfaction;c) addressing risks and opportunities associated with its context and objectives;d) the ability to demonstrate conformity to specified quality management system requirements.This International Standard can be used by internal and external parties.It is not the intent of this International Standard to imply the need for:—uniformity in the structure of different quality management systems;—alignment of documentation to the clause structure of this International Standard;—the use of the specific terminology of this International Standard within the organization.The quality management system requirements specified in this International Standard are complementary to requirements for products and services.This International Standard employs the process approach, which incorporates the Plan-Do-Check-Act (PDCA) cycle and risk-based thinking.The process approach enables an organization to plan its processes and their interactions.The PDCA cycle enables an organization to ensure that its processes are adequately resourced and managed, and that opportunities for improvement are determined and acted on.Risk-based thinking enables an organization to determine the factors that could cause its processes and its quality management system to deviate from the planned results, to put in place preventive controls to minimize negative effects and to make maximum use of opportunities as they arise (see Clause A.4).Consistently meeting requirements and addressing future needs and expectations poses a challenge for organizations in an increasingly dynamic and complex environment. To achieve this objective, the organization might find it necessary to adopt various forms of improvement in addition to correction and continual improvement, such as breakthrough change, innovation and re-organization.In this International Standard, the following verbal forms are used:—“shall” indicates a requirement;—“should” indicates a recommendation;—“may” indicates a permission;—“can” indicates a possibility or a capability.Information marked as “NOTE” is for guidance in understanding or clarifying the associated requirement.0.2 Quality management principlesThis International Standard is based on the quality management principles described in ISO 9000. The descriptions include a statement of each principle, a rationale of why the principle is important for the organization, some examples of benefits associate d with the principle and examples of typical actions to improve the organization’s performance when applying the principle. The quality management principles are:— customer focus;— leadership;— engagement of people;— process approach;— improvement;— evidence-based decision making;— relationship management.0.3 Process approach0.3.1 GeneralThis International Standard promotes the adoption of a process approach when developing, implementing and improving the effectiveness of a quality management system, to enhance customer satisfaction by meeting customer requirements. Specific requirements considered essential to the adoption of a process approach are included in 4.4. Understanding and managing interrelated processes as a system contributes to the organization’s effectiveness and efficiency in achieving its intended results. This approach enables the organization to control the interrelationships and interdependencies among the processes of the system, so that the overall performance of the organization can be enhanced. The process approach involves the systematic definition and management of processes, and their interactions, so as to achieve the intended results in accordance with the quality policy and strategic direction of the organization. Management of the processes and the system as a whole can be achieved using the PDCA cycle (see 0.3.2) with an overall focus on risk-based thinking (see 0.3.3) aimed at taking advantage of opportunities and preventing undesirable results. The application of the process approach in a quality management system enables: a) understanding and consistency in meeting requirements; b) the consideration of processes in terms of added value; c) the achievement of effective process performance; d) improvement of processes based on evaluation of data and information. Figure 1 gives a schematic representation of any process and shows the interaction of its elements. The monitoring and measuring check points, which are necessary for control, are specific to each process and will vary depending on the related risks.0.3.2 Plan-Do-Check-Act cycleThe PDCA cycle can be applied to all processes and to the quality management system as a whole. Figure 2 illustrates how Clauses 4 to 10 can be grouped in relation to the PDCA cycle.The PDCA cycle can be briefly described as follows:—Plan: establish the objectives of the system and its processes, and the resources needed to deliver results in accordance with customers’ requirements and the organization’s policies; and identify and address risks and opportunit ies; — Do: implement what was planned;—Check: monitor and (where applicable) measure processes and the resulting products and services against policies, objectives and requirements and planned activities, and report the results;— Act: take actions to improve performance, as necessary.0.3.3 Risk-based thinkingRisk-based thinking (see Clause A.4) is essential for achieving an effective quality management system. The concept of risk-based thinking has been implicit in previous editions of this International Standard including, for example, carrying out preventive action to eliminate potential nonconformities, analyzing any nonconformities that do occur, and taking action to prevent recurrence that is appropriate for the effects of the nonconformity. To conform to the requirements of this International Standard, an organization needs to plan and implement actions to address risks and opportunities. Addressing both risks and opportunities establishes a basis for increasing the effectiveness of the quality management system, achieving improved results and preventing negative effects. Opportunities can arise as a result of a situation favorable to achieving an intended result, for example, a set of circumstances that allow the organization to attract customers, develop new products and services, reduce waste or improve productivity. Actions to address opportunities can also include consideration of associated risks. Risk is the effect of uncertainty and any such uncertainty can have positive or negative effects. A positive deviation arising from a risk can provide an opportunity, but not all positive effects of risk result in opportunities.0.4 Relationship with other management system standards与其他管理体系标准的关系This International Standard applies the framework developed by ISO to improve alignment among its International Standards for management systems (see Clause A.1). This International Standard enables an organization to use the process approach, coupled with the PDCA cycle and risk-based thinking, to align or integrate its quality management system with the requirements of other management system standards. This International Standard relates to ISO 9000 and ISO 9004 as follows: — ISO 9000 Quality management systems —Fundamentals and vocabulary provides essential background for the proper understanding and implementation of this International Standard; — ISO 9004 Managing for the sustained success of an organization — A quality management approach provides guidance for organizations that choose to progress beyond the requirements of this International Standard. Annex B provides details of other International Standards on quality management and quality management systems that have been developed by ISO/TC 176. This International Standarddoes not include requirements specific to other management systems, such as those for environmental management, occupational health and safety management, or financial management. Sector-specific quality management system standards based on the requirements of this International Standard have been developed for a number of sectors. Some of these standards specify additional quality management system requirements, while others are limited to providing guidance to the application of this International Standard within the particular sector.A matrix showing the correlation between the clauses of this edition of this International Standard and the previous edition (ISO 9001:2008) can be found on the ISO/TC 176/SC 2 open access web site at: /tc176/sc02/public.1 ScopeThis International Standard specifies requirements for a quality management system when an organization: a) needs to demonstrate its ability to consistently provide products and services that meet customer and applicable statutory and regulatory requirements, and b) aims to enhance customer satisfaction through the effective application of the system, including processes for improvement of the system and the assurance of conformity to customer and applicable statutory and regulatory requirements. All the requirements of this International Standard are generic and are intended to be applicable to any organization, regardless of its type or size, or the products and services it provides. NOTE 1 In this International Standard, the terms “product” or “service” only apply to products and services intended for, or required by, a customer. NOTE 2 Statutory and regulatory requirements can be expressed as legal requirements.2 Normative referencesThe following documents, in whole or in part, are normatively referenced in this document and are indispensable for its application. For dated references, only the edition cited applies. For undated references, the latest edition of the referenced document (including any amendments) applies. ISO 9000:2015, Quality management systems —Fundamentals and vocabulary3 Terms and definitionsFor the purposes of this document, the terms and definitions given in ISO 9000:2015 apply.4 Context of the organization4.1 Understanding the organization and its contextThe organization shall determine external and internal issues that are relevant to its purpose and its strategic direction and that affect its ability to achieve the intended result(s) of its quality management system. The organization shall monitor and review information about these external and internal issues.NOTE 1 Issues can include positive and negative factors or conditions for consideration.NOTE 2 Understanding the external context can be facilitated by considering issues arising from legal, technological, competitive, market, cultural, social and economic environments, whether international, national, regional or local. NOTE 3 Understanding the internal context can be facilitated by considering issues related to values, culture, knowledge and performance of the organization.4.2 Understanding the needs and expectations of interested partiesDue to their effect or potential effect on the organization’s ability to consistently provide products and services that meet customer and applicable statutory and regulatory requirements, the organization shall determine: a) the interested parties that are relevant to the quality management system; b) the requirements of these interested parties that are relevant to the quality management system. The organization shall monitor and review information about these interested parties and their relevant requirements.4.3 Determining the scope of the quality management systemThe organization shall determine the boundaries and applicability of the quality management system to establish its scope. When determining this scope, the organization shall consider: a) the external and internal issues referred to in 4.1; b) the requirements of relevant interested parties referred to in 4.2; c) the products and services of the organization. The organization shall apply all the requirements of this International Standard if they are applicable within the determined scope of its quality management system. The scope of the organization’s quality management system shall be available and be maintained as documented information. The scope shall state the types of products and services covered, and provide justification for any requirement of this International Standard that the organization determines is not applicable to the scope of its quality management system. Conformity to this International Standard may only be claimed if the requirements determined as not being applicable do not affect the organization’s ability or responsibility to ensure the conformity of its products and services and the enhancement of customer satisfaction.4.4 Quality management system and its processes4.4.1 The organization shall establish, implement, maintain and continually improve a quality management system, including the processes needed and their interactions, in accordance with the requirements of this International Standard. The organization shall determine the processes needed for the quality management system and their application throughout the organization, and shall:a) determine the inputs required and the outputs expected from these processes;b) determine the sequence and interaction of these processes;c) determine and apply the criteria and methods (including monitoring, measurements and related performance indicators) needed to ensure the effective operation and control of these processes;d) determine the resources needed for these processes and ensure their availability;e) assign the responsibilities and authorities for these processes;f) address the risks and opportunities as determined in accordance with the requirements of 6.1;g) evaluate these processes and implement any changes needed to ensure that these processes achieve their intended results;h) improve the processes and the quality management system.4.4.2 To the extent necessary, the organization shall:a) maintain documented information to support the operation of its processes;b) retain documented information to have confidence that the processes are being carried out as planned.5 Leadership5.1 Leadership and commitment5.1.1 GeneralTop management shall demonstrate leadership and commitment with respect to the quality management system by:a) taking accountability for the effectiveness of the quality management system;b) ensuring that the quality policy and quality objectives are established for the quality management system and are compatible with the context and strategic direction of the organization;c) ensuring the integration of the quality management system requirements into the organization’s business processes;d) promoting the use of the process approach and risk-based thinking;e) ensuring that the resources needed for the quality management system are available;f) communicating the importance of effective quality management and of conforming to the quality management systemrequirements;g) ensuring that the quality management system achieves its intended results;h) engaging, directing and supporting persons to contribute to the effectiveness of the quality management system;i) promoting improvement;j) supporting other relevant management roles to demonstrate their leadership as it applies to their areas of responsibility. NOTE Reference to “business” in this International Standard can be interpreted broadly to mean those activities that are core to the purposes of the organization’s existence, whether the organization is public, private, for profit or not for prof it.5.1.2 Customer focusTop management shall demonstrate leadership and commitment with respect to customer focus by ensuring that:a) customer and applicable statutory and regulatory requirements are determined, understood and consistently met;b) the risks and opportunities that can affect conformity of products and services and the ability to enhance customer satisfaction are determined and addressed;c) the focus on enhancing customer satisfaction is maintained.5.2 Policy5.2.1 Establishing the quality policyTop management shall establish, implement and maintain a quality policy that:a) is appropriate to the purpose and context of the organization and supports its strategic direction;b) provides a framework for setting quality objectives;c) includes a commitment to satisfy applicable requirements;d) includes a commitment to continual improvement of the quality management system.5.2.2 Communicating the quality policyThe quality policy shall:a) be available and be maintained as documented information;b) be communicated, understood and applied within the organization;c) be available to relevant interested parties, as appropriate.5.3 Organizational roles, responsibilities and authoritiesTop management shall ensure that the responsibilities and authorities for relevant roles are assigned, communicated and understood within the organization. Top management shall assign the responsibility and authority for:a) ensuring that the quality management system conforms to the requirements of this International Standard;b) ensuring that the processes are delivering their intended outputs;c) reporting on the performance of the quality management system and on opportunities for improvement (see 10.1), in particular to top management;d) ensuring the promotion of customer focus throughout the organization;e) ensuring that the integrity of the quality management system is maintained when changes to the quality management system are planned and implemented.6 Planning6.1 Actions to address risks and opportunities6.1.1 When planning for the quality management system, the organization shall consider the issues referred to in 4.1 and the requirements referred to in 4.2 and determine the risks and opportunities that need to be addressed to:a) give assurance that the quality management system can achieve its intended result(s);b) enhance desirable effects;c) prevent, or reduce, undesired effects;d) achieve improvement.6.1.2 The organization shall plan:a) actions to address these risks and opportunities;b) how to:1) integrate and implement the actions into its quality management system processes (see 4.4);2) evaluate the effectiveness of these actions.Actions taken to address risks and opportunities shall be proportionate to the potential impact on the conformity of products and services.NOTE 1 Options to address risks can include avoiding risk, taking risk in order to pursue an opportunity, eliminating the risk source, changing the likelihood or consequences, sharing the risk, or retaining risk by informed decision.NOTE 2 Opportunities can lead to the adoption of new practices, launching new products, opening new markets, addressing new customers, building partnerships, using new technology and other desirable and viable possibilities to address the organization’s or its customers’ needs.6.2 Quality objectives and planning to achieve them6.2.1 The organization shall establish quality objectives at relevant functions, levels and processes needed for the quality management system.The quality objectives shall:a) be consistent with the quality policy;b) be measurable;c) take into account applicable requirements;d) be relevant to conformity of products and services and to enhancement of customer satisfaction;e) be monitored;f) be communicated;g) be updated as appropriate.The organization shall maintain documented information on the quality objectives.6.2.2 When planning how to achieve its quality objectives, the organization shall determine:a) what will be done;b) what resources will be required;c) who will be responsible;d) when it will be completed;e) how the results will be evaluated6.3 Planning of changesWhen the organization determines the need for changes to the quality management system, the changes shall be carried out in a planned manner (see 4.4).The organization shall consider:a) the purpose of the changes and their potential consequences;b) the integrity of the quality management system; c) the availability of resources;d) the allocation or reallocation of responsibilities and authorities.7 Support7.1 Resources7.1.1 GeneralThe organization shall determine and provide the resources needed for the establishment, implementation, maintenance and continual improvement of the quality management system. The organization shall consider:a) the capabilities of, and constraints on, existing internal resources;b) what needs to be obtained from external providers.7.1.2 PeopleThe organization shall determine and provide the persons necessary for the effective implementation of its quality management system and for the operation and control of its processes.7.1.3 InfrastructureThe organization shall determine, provide and maintain the infrastructure necessary for the operation of its processes and to achieve conformity of products and services. NOTE Infrastructure can include: a) buildings and associated utilities; b) equipment, including hardware and software; c) transportation resources; d) information and communication technology.7.1.4 Environment for the operation of processesThe organization shall determine, provide and maintain the environment necessary for the operation of its processes and to achieve conformity of products and services.NOTE :A suitable environment can be a combination of human and physical factors, such as:a) social (e.g. non-discriminatory, calm, non-confrontational);b) psychological (e.g. stress-reducing, burnout prevention, emotionally protective);c) physical (e.g. temperature, heat, humidity, light, airflow, hygiene, noise).These factors can differ substantially depending on the products and services provided.7.1.5 Monitoring and measuring resources7.1.5.1 GeneralThe organization shall determine and provide the resources needed to ensure valid and reliable results when monitoring or measuring is used to verify the conformity of products and services to requirements. The organization shall ensure that the resources provided:a) are suitable for the specific type of monitoring and measurement activities being undertaken;b) are maintained to ensure their continuing fitness for their purpose.The organization shall retain appropriate documented information as evidence of fitness for purpose of the monitoring and measurement resources.7.1.5.2 Measurement traceabilityWhen measurement traceability is a requirement, or is considered by the organization to be an essential part of providing confidence in the validity of measurement results, measuring equipment shall be:a) calibrated or verified, or both, at specified intervals, or prior to use, against measurement standards traceable to international or national measurement standards; when no such standards exist, the basis used for calibration or verification shall be retained as documented information;b) identified in order to determine their status;c) safeguarded from adjustments, damage or deterioration that would invalidate the calibration status and subsequent measurement results.The organization shall determine if the validity of previous measurement results has been adversely affected when measuring equipment is found to be unfit for its intended purpose, and shall take appropriate action as necessary.7.1.6 Organizational knowledgeThe organization shall determine the knowledge necessary for the operation of its processes and to achieve conformity of products and services.This knowledge shall be maintained and be made available to the extent necessary.When addressing changing needs and trends, the organization shall consider its current knowledge and determine how to acquire or access any necessary additional knowledge and required updates.NOTE 1 Organizational knowledge is knowledge specific to the organization; it is gained by experience. It is information that is used and shared to achieve the organization’s objectives.NOTE 2 Organizational knowledge can be based on:a) internal sources (e.g. intellectual property; knowledge gained from experience; lessons learned from failures and successful projects; capturing and sharing undocumented knowledge and experience; the results of improvements in processes, products and services);b) external sources (e.g. standards; academia; conferences; gathering knowledge from customers or external providers).7.2 CompetenceThe organization shall:a) determine the necessary competence of person(s) doing work under its control that affects the performance and effectiveness of the quality management system;.b) ensure that these persons are competent on the basis of appropriate education, training, or experience;c) where applicable, take actions to acquire the necessary competence, and evaluate the effectiveness of the actions taken;d) retain appropriate documented information as evidence of competence.NOTE Applicable actions can include, for example, the provision of training to, the mentoring of, or the reassignment of currently employed persons; or the hiring or contracting of competent persons.7.3 AwarenessThe organization shall ensure that persons doing work under the organization’s control are aware of:a) the quality policy;b) relevant quality objectives;c) their contribution to the effectiveness of the quality management system, including the benefits of improved performance;d) the implications of not conforming with the quality management system requirements.7.4 CommunicationThe organization shall determine the internal and external communications relevant to the quality management system, including:a) on what it will communicate;b) when to communicate;c) with whom to communicate;d) how to communicate;e) who communicates.7.5 Documented information7.5.1 GeneralThe organization’s quality management system shall include:a) documented information required by this International Standard;b) documented information determined by the organization as being necessary for the effectiveness of the quality management system.NOTE The extent of documented information for a quality management system can differ from one organization to another due to:— the size of organization and its type of activities, processes, products and services;— the complexity of processes and their interactions;— the competence of persons.7.5.2 Creating and updatingWhen creating and updating documented information, the organization shall ensure appropriate:a) identification and description (e.g. a title, date, author, or reference number);b) format (e.g. language, software version, graphics) and media (e.g. paper, electronic);c) review and approval for suitability and adequacy.7.5.3 Control of documented Information7.5.3.1 Documented information required by the quality management system and by this International Standard shall be controlled to ensure:a) it is available and suitable for use, where and when it is needed;b) it is adequately protected (e.g. from loss of confidentiality, improper use, or loss of integrity).7.5.3.2 For the control of documented information, the organization shall address the following activities, as applicable:。
ISO9001-2015进料检验管理办法

进料检验管理办法(ISO9001:2015)1.目的为使进料产品之质量能符合本公司之要求,使有关部门及供货商有法可依,特制订此管理办法,针对IQC的作业内容、抽样计划、AQL水准、不良处理等进行明确定义。
2.范围所有提供本公司之原材料、零件、半成品的供应厂商均适用之。
3.权责工程部:负责提供标准之Sample及相关零配件或产品之工程规格及HSF标准。
资材部:负责采购之安排,材料之供应,提供新厂商及送验通知。
品保部:负责进料之检验、检验规范之制定。
4.定义4.1.严重缺点( CRITICAL DEFECT )可能导致产品对用户之安全造成伤害之缺点,亦即违反安全规定,谓之严重缺点(CR)。
4.2.主要缺点( MAJOR DEFECT )使材料功能丧失或对制程造成不易排除之影响,致该材料不堪使用,数量不符及混料者,谓之主要缺点(MA)。
4.3.次要缺点( MINOR DEFECT )与承认书、工程规格书要求有差异,但不影响材料使用功能或该缺点易于排除者、外观不良及包装不良者,其缺点谓之次要缺点(MI)。
4.4.重工(REWORK)系指所生产原材料、半成品,因有瑕疪或不良,且超出允收水平被判拒收,针对此一批退原因而做相关之处理动作,谓之重工。
4.5.拒收(REJECT)系指所生产之原材料、半成品,有瑕疪或不良,且超出允收水平被判批退。
4.6.质量异常反应供货商生产之半成品、成品在进料检验发现有重大不良时,品管应开立【质量异常单】,同时知会采购及生管,SQE提出【矫正措施报告】至厂商,并追踪改善结果。
4.7. AVL:Approved Vender List 合格厂商名册4.8. MRB:Material Review Board 物料监审委员会4.9. FAI:First Article Inspection新产品首件检验表4.10. MRS:Material Recognition Standard 零件检验标准书4.11. HSF:Hazardous Substances Free 不含有有害物质4.12. HSF左证资料:包含“ICP测试报告、MSDS、材质证明书、不使用保证书(承认用)、环境物质不使用证明书(承认用、量产用)”4.13.MSDS:Material Safety Data Sheet 物质安全数据表5.作业内容5.1.仓储单位收料后,依《仓储管理作业程序》将货物搬至待验区,再由仓库填写《收料单》,《收料单》后需附有相关产品检验报告交至IQC检验。
iso9001:2015标识和可追溯性控制程序英文版

Procedure: [Identification & Traceability Proc. Title]1. SUMMARY1.1. This procedure defines the methods used to identify and (where applicable) provide uniquetraceability for [Short Client Name] products. This procedure includes methods:1.1.1. To define the methods for identifying products (what they are)1.1.2. To define the methods for identifying products as to their current inspection or teststatus1.1.3. To define the methods for segregating and discriminating between product andtooling when their appearance is similar1.1.4. To define the methods for providing traceability, including unique serialization, orproduct as applicable1.2. The [who?] is responsible for implementation and management of this procedure.2. REVISION AND APPROVALRev. Date Nature of Changes Approved By[Rev Number] [Date ofIssue]Original issue.[ProcedureApproverName]3. APPLICATION3.1. This procedure applies to all departments which use, handle, transport, store, inspect ormanufacture product, raw materials and tooling, at all [Short Client Name] facilities.3.2. This procedure not only applies to typical product, but also deliverables from services, such asreports, schedules, etc.3.3. Non-critical materials or supplies, which are not incorporated into final product or which serveonly to support facilities or operations, are not subject to this procedure.4. DEFINITIONS4.1. Product4.1.1. “Product” includesany of the following:Any part, assembly or item ordered by the customerDeliverable reports or documentsProduct may refer to finished product, or work in process (WIP)4.2. Raw Materials4.2.1. “Raw materials” include any of the following:Any materials or items (metals, plastics, components, pre-built assemblies, smallparts) which become part of the finished product’s physical construction; some ofthese items may sometimes be referred to as “consumables”.Coatings, paint, plating, adhesives, chemicals or materials which will be incorporatedinto (or onto) the final product.4.3. Tooling4.3.1. “Tooling” can include any of the following:Devices used by manufacturing for setup or production, including fixtures and jigs.Devices used by inspection for determining acceptance of product, including testfixtures.Shop aids, which are simple devices (blocks, spacers, shapes) used to assist inproduction or development, but which are not precision tools and which can be usedfor a variety of applications.4.3.2. Tooling does not include:Cutting tools, drill bits, etc.Hand toolsMachining equipment5. PRODUCT5.1. There are many ways to identify product; this procedure presents the most typical, acceptablemethods. Additional product identification methods may be called out in the design or productiondocumentation.5.2. Identification typically includes the part number, revision, Work Order # and unique serialnumber (if applicable).5.3. Identification is done through any of the following methods:5.3.1. Part marking, by way of ink marking, etching or some other method.5.3.2. Bag-and-tag methods, especially for small parts.5.3.3. Placement of parts on shelves or in containers that are properly marked, withsignage or other methods.5.3.4. Placement of parts near associated paperwork, for the purpose of identification andtraceability, may be used if the paperwork can clearly be identified as relating to theparts in question, typically by way of the inclusion of a drawing which can becompared to the product.5.3.5. Segregating entire areas of the production floor with belt stanchions and attachedsignage, indicating what type of items are allowed, or disallowed, within the enclosedarea.。
iso9001:2015采购控制程序英文版
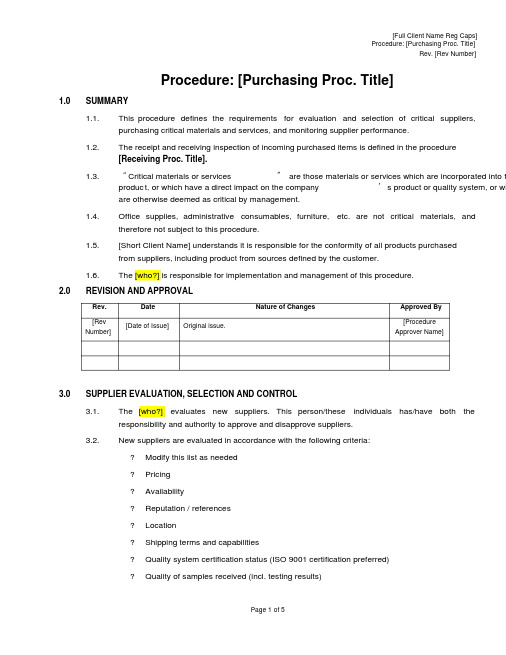
Procedure: [Purchasing Proc. Title]1.0SUMMARY1.1.This procedure defines the requirements for evaluation and selection of critical suppliers,purchasing critical materials and services, and monitoring supplier performance.1.2.The receipt and receiving inspection of incoming purchased items is defined in the procedure[Receiving Proc. Title].1.3.“Critical materials or services” are those materials or services which are incorporated into fproduc t, or which have a direct impact on the company’s product or quality system, or whare otherwise deemed as critical by management.1.4.Office supplies, administrative consumables, furniture, etc. are not critical materials, andtherefore not subject to this procedure.1.5.[Short Client Name] understands it is responsible for the conformity of all products purchasedfrom suppliers, including product from sources defined by the customer.1.6.The [who?] is responsible for implementation and management of this procedure.2.0REVISION AND APPROVALRev. Date Nature of Changes Approved By[Rev Number] [Date of Issue] Original issue.[ProcedureApprover Name]3.0SUPPLIER EVALUATION, SELECTION AND CONTROL3.1.The [who?] evaluates new suppliers. This person/these individuals has/have both theresponsibility and authority to approve and disapprove suppliers.3.2.New suppliers are evaluated in accordance with the following criteria:?Modify this list as needed?Pricing?Availability?Reputation / references?Location?Shipping terms and capabilities?Quality system certification status (ISO 9001 certification preferred)?Quality of samples received (incl. testing results)?On-site audit results?Telephone interview results?Written survey results?Customer mandate?Sole source / OEM status3.3.Where a customer mandates a special process source, both [Short Client Name] and anysuppliers must use the required supplier; this usage may override [Short Client Name]status rules.3.4.In some cases a formal risk assessment may be conducted as part of the evaluation andselection of a potential supplier, or in order to determine if a problematic supplier should be retained; see [Risk Management Proc. Title].[Use this next section if the ASL is a spreadsheet, database or document – NOT if the ASL is part of an ERP system.]3.5.The [who?] will maintain an Approved Supplier List (modify name if needed) which lists allevaluated and approved suppliers, and their approval status.3.6.Suppliers who meet any of the evaluation criteria, in the judgment of the person conducting theevaluation, may then be entered into the purchasing system and items may be purchased.However, the supplier is entered into the Approved Supplier List (ASL) on a CONDITIONAL basis, pending inspection or review of products or services rendered.3.7.Upon successful receipt or review of products or services, the manager may then advance thesupplier’s status to APPROVED.3.8.If the results of review of product or service received are insufficient or otherwise lacking, thestatus to DISAPPROVED, or to leave it at buyer may then elect to change the supplier’sCONDITIONAL until further orders are received and reviewed.3.9. A supplier may also be listed as RESTRICTED, where certain purchasing restrictions are placed onthe supplier. This may be useful to limit what products may be purchased from a supplier, or toplace other conditions.3.10.The Approved Supplier List indicates the supplier, location, approval status (Approved,Conditional, Disapproved, Restricted), and the scope of approval (typically commodity type orproduct family). Re-approval of suppliers is continual and ongoing based on the suppliers abilityto meet the criteria of paragraph 3.2. For Restricted status, a note of the restriction must alsobe included.3.11.Suppliers used for at least six months prior to [Date of Issue], have been grandfathered into thesystem as Approved, provided they have no outstanding quality issues on record, and only uponthe decision by [who?] to do so.[Use this next section if the ASL is part of the ERP system]。
ISO9001-2015中文版

ISO9001-2015中文版ISO 9001:2015 质量管理体系要求中国XXXXX编发2017年9月1日目录前言 (I)引言 (II)0.1 总则 (II)0.2 质量管理原则 (II)0.3 过程方法 (III)0.4 与其他管理体系标准的关系 (V)1. 范围 (1)2 规范性引用文件 (1)3 术语和定义 (1)4 组织环境 (1)4.1 理解组织及其环境 (1)4.2 理解相关方的需求和期望 (1)4.3 确定质量管理体系的范围 (1)4.4 质量管理体系及其过程 (2)5 领导作用 (2)5.1 领导作用和承诺 (2)5.1.1 总则 (2)5.1.2 以顾客为关注焦点 (2)5.2 方针 (3)5.2.1 制定质量方针 (3)5.2.2 沟通质量方针 (3)5.3 组织的岗位、职责和权限 (3)6 策划 (3)6.1 应对风险和机遇的措施 (3)6.2 质量目标及其实现的策划 (4)6.3 变更的策划 (4)7 支持 (4)7.1 资源 (4)7.2 能力 (6)7.3 意识 (6)7.4 沟通 (6)7.5 形成文件的信息 (6)8 运行 (7)8.1 运行策划和控制 (7)8.2 产品和服务的要求 (7)8.2.1 顾客沟通 (7)8.2.2 与产品和服务的要求的确定 ..... .. (7) 8.2.3 产品和服务的要求的评审 (8)8.2.4 产品和服务要求的更改 (8)8.3 产品和服务的设计和开发 (8)8.3.1 总则 (8)8.3.2 设计和开发策划 (8)8.3.3 设计和开发输入 (8)8.3.4 设计和开发控制 (9)8.3.5 设计和开发输出 (9)8.3.6 设计和开发更改 (9)8.4 外部提供过程、产品和服务的控制 (9) 8.4.1总则 (9)8.4.2 控制类型和程度 (10)8.5 生产和服务提供 (10)8.6 产品和服务的放行 (11)8.7不合格输出的控制 (12)9 绩效评价 (12)9.1 监视、测量、分析和评价 (12)9.2 内部审核 (13)9.3 管理评审 (13)10 持续改进 (14)10.1总则 (14)10.2 不合格和纠正措施 (14)10.3 持续改进 (15)附录A(资料性附录) (16)附录B(资料性附录) (19)参考文献 (22)国际标准化组织(ISO)是由各国标准化团体(ISO成员团体)组成的世界性的联合会。
ISO9001-2015进料检验不合格品处理程序

进料检验不合格品处理程序(ISO9001:2015)1目的制定组件进料检验发现的不合格品的处理办法,确保材料出现不合格时能有效及时的处理。
2范围本办法适用于公司IQC检验范围内所有不合格物料的处理。
3相关文件3.1不合格品控制程序4定义4.1不合格品:所有来料检验发现的不符合质量标准的原物料。
4.2退/换货:将不合格物料全部退回供应商或部分与供应商更换。
4.3特采:不合格物料因客户、生产需求急迫,客户或销售部代表客户同意授权,或投入后不影响产品功能、构造机能、特殊外观要求及应用功能性,不造成人身安全,可满足最终客户使用品质的不合格品做特殊接收的状态,等同让步接收。
4.4厂内挑选:经过协商,由公司相关部门代为厂商全检不合格品,挑选合格品投入生产,不合格品由采购部负责办理退/换货,并由厂商赔偿工时损失。
4.5供应商挑选:由供应商负责按照我司要求对不合格品进行全检(可派人员来我司进行挑选等)。
5职责5.1质量部(IQC):物料的检验及物料不合格的及时反馈。
5.2质量部(PQC):针对特采物料上线使用情况进行跟踪及数据统计。
5.3SQE:不合格物料的评审,联系供应商对已发现的不合格物料进行确认及推动改善。
5.4采购部:不合格物料的评审,联系供应商对不合格物料进行处理。
5.5PMC:物料安全库存的确认;及特采物料上线使用前的信息发布。
5.6工程部:负责对材料的安全性、功能性使用的影响进行评审判定,必要时实施相关实验。
5.7生产部:不合格物料的评审,在线不合格物料的及时提报,配合做好厂内挑选工作,确保合格品投入生产。
5.8仓库:不合格物料的分类存放。
5.9质量部:负责对不合格材料作出最终判定;6环境满足客户要求,符合行业标准7职业健康安全满足客户要求,符合行业标准8管理内容8.1特采原则8.1.1对产品的使用,确定安全性、公害性及功能性的顾虑原则,不致产生客户抱怨事件发生时。
8.1.2对产品功能及产品价值的影响很微小时。
ISO9001-2015产品检验程序

产品检验程序1.目的保证进厂的原材料、辅料等符合规定要求,不致影响产品质量和生产效率。
为对产品生产过程中的检验工作进行管理,防止不合格品非预期流转。
对产品的特性进行检测,以验证产品是否满足要求,特制定本程序。
2.范围本程序适用于公司外购来料、内部生产和服务全过程中的配件及产品检验。
3.定义3.1 入料批:同一厂商同一次交货的同一物料同一型号可视为一个入料批。
3.2 检验批:一个入料批可视为一个检验批。
同一厂商的同一型号物料一周之内交货的不同入料批也可合并为一个检验批,条件是检验时间不可影响生产进度。
4.权责4.1检验人员负责实施过程检验:首件检验(确认),巡检,最终检验的确认。
4.2 生产部门4.2.1负责实施各工序间的自检及巡查工作;4.2.2对所发现的质量问题的记录及反馈。
5.程序5.1进料检验5.1.1仓库收料仓管人员根据公司采购单和供应商的送货单接收来料,核实无误后放于收料待检区,然后通知检验人员进行检验。
5.1.2 品质检验检验人员按照检验指导书对进料进行检验,将检验结果填写到“进料检验记录”中;同时填写“进料质量反馈报告”,送达采购处备案。
5.1.3检验结果处理5.1.3.1如果各项检验均合格,检验人员将合格标签贴于来料包装上,由仓管人员办理入库手续。
5.1.3.2如果某项检验不合格,检验员将此批料标识待处理,填写“品质异常报告单”,同时通知生产部门进行评审,或通知采购与供应商进行沟通。
a.若结果为特采使用,检验员贴“特采”标签,放行入库,置于合格区。
b.若结果为退货,检验员贴“不合格”标贴 ,由采购安排退回供应商。
具体参照《进料检验作业指导书》执行。
5.1.3.3 本公司进料产品不允许紧急放行。
5.1.4供应商品质改善5.1.4.1当来料判定为不合格时,品质工程师应向供应商发出“品质异常报告单”,要求供应商进行原因分析和纠正措施并回传本公司。
5.1.4.2 检验人员负责对供应商的纠正措施进行验证,在供应商纠正行动阶段,若连续3批进料经检验合格,即判改善有效;若连续3批进料有一批经检验不合格,即重发投诉,转入新的纠正预防行动,重新跟进。
- 1、下载文档前请自行甄别文档内容的完整性,平台不提供额外的编辑、内容补充、找答案等附加服务。
- 2、"仅部分预览"的文档,不可在线预览部分如存在完整性等问题,可反馈申请退款(可完整预览的文档不适用该条件!)。
- 3、如文档侵犯您的权益,请联系客服反馈,我们会尽快为您处理(人工客服工作时间:9:00-18:30)。
IQC进料检验作业程序
Incoming inspection procedure
(ISO9001:2015)
1.0 目 的:本程序旨在建立适切之进料检验作业管制,以确保外购的生产性材料材
质符合环境要求,质量符合本公司的设计要求.
Attempt: The procedure is to establish unanimous incoming inspect
operations, in order to make sure those purchasing stuff can
manage environment requirement and the quality can come up to
design .
2.0 范 围:适用于本公司所有外购的生产性物料的进料检验.
Range: Apply to all incoming inspection of purchasing stuff.
3.0 定 义: Definition
3.1 IQC: 进料检验单位(Incoming Quality Control).
3.2 SQE :供货商质量工程(Supplier Quality Engineer).
3.3 客供配件:由客户提供,代为出货包装用之配件,并不参与成品组立、加工作业流
程.(此种配件不纳入零件承认规范内,仅作资材面处理).
Customer supplied parts: Customer supplied parts are used to delivery
package parts, not participate in final-products、operation procedure.(the
parts are not bring into parts recognition rules, only be regarded as stuff
management)
4.0 权 责: Rights and responsibility
4.1 品保部负责物料的检验、判定、检验后的标识及不合格品的改善追踪工作.
QA Dep. manage stuff inspection、judgment、mark and rejects improving or
德信诚培训网
ISO9001-2015内审员升级培训(100元) ISO9001-2015内审员培训(200元) :http://www.55top.com
tracking after inspection.
4.2 资材部采购员负责与供货商联络,并协助来料质量异常的处理及改善追踪.
Material purchaser manage and communicate with suppliers, then support
dealing and tracking anomaly.
5.0 作业内容: Contents
5.1 检验规划:Inspection planning
5.1.1 抽样计划:IQC依MIL-STD-105E(II)对进料实施抽样检验.
Sampling scheme: IQC refer to MIL-STD-105E(II)to execute sampling
action.
5.1.2 正常检验:IQC依MIL-STD-105E(II)对进料实施抽样检验.
Regular inspection: IQC refer to MIL-STD-105E(II)to execute sampling
action.
5.1.3 抽样时机:IQC依照MIL-STD-105E(II)对物料进行抽验检验,取样需平均抽
样,在仓库平均取样后,在IQC室依照该物料之承认书与图纸执行检验。例
如:来料5000PCS,500PCS/箱 50PCS/盒 IQC依照AQL抽样200PCS.
Sampling scheme : IQC refer to MIL-STD-105E(II)to execute sampling
action, after average sampling in warehouse, IQC refer to
specification and drawings to inspect, for example: 5000PCS
incomings,500PCS/carton,50PCS /box, IQC will select 200PCS.
5.1.4 加严检验:当正常检验进行中,连续5批进料有3批NG时,则转为加严检
验,则依MIL-STD-105E加严抽样计划表进行抽样检验,连续5批允收时,转
为正常检验.
Tightened inspection: When do regular inspection,3 in 5 batches
incomings are NG, then refer to MIL-STD-105E to perform tightened
德信诚培训网
ISO9001-2015内审员升级培训(100元) ISO9001-2015内审员培训(200元) :http://www.55top.com
inspection, execute regular inspection if 5 batches are received
continuously.
5.1.5 减量检验:当正常检验进行中,连续10批允收且无制程反应该材料异常时,
转为减量检验,减量检验执行中,若有一批NG或制程反馈来料异常时则转为
正常检验.
Reduced inspection: When do regular inspection,10 batches are
accepted and have no process abnormality, then turn to reduced
inspection, if one batch is NG or have process abnormality, then turn
to regular inspection.
5.1.6 免检:Exemption
5.1.6.1 客供配件,IQC除对产品作料号核对,包装验收等常规检验外,对其产品
性能实施免检.
About customer-supplied accessories, IQC check its number,
package ,do exemption about its property.
5.1.6.2 当受限于设备、技术等因素无法执行检验时,由品保部拟定<<免检物料
清单>>,并由供货商提供相对应的检验报告及质量保证书,该物料IQC
则实施免检
When we can’t execute inspect for lacking equipment、technology,
QA Dep. draft <
report and guaranteed certificate, so IQC can execute exemption.
5.1.6.3 对于免检物料,IQC对其料号、包装、保质期等做常规检验.
For exemption materials, IQC make regular inspection about its part
number、package、quality guarantee period.
5.1.6.4 对于免检物料,品保单位加严跟踪投线质量.