环式焙烧炉
焙烧对石墨电极质量的影响
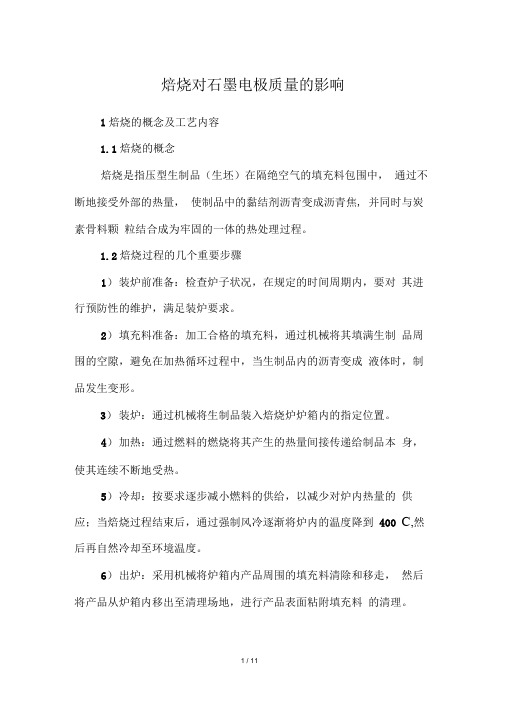
焙烧对石墨电极质量的影响1焙烧的概念及工艺内容1.1焙烧的概念焙烧是指压型生制品(生坯)在隔绝空气的填充料包围中,通过不断地接受外部的热量,使制品中的黏结剂沥青变成沥青焦, 并同时与炭素骨料颗粒结合成为牢固的一体的热处理过程。
1.2焙烧过程的几个重要步骤1)装炉前准备:检查炉子状况,在规定的时间周期内,要对其进行预防性的维护,满足装炉要求。
2)填充料准备:加工合格的填充料,通过机械将其填满生制品周围的空隙,避免在加热循环过程中,当生制品内的沥青变成液体时,制品发生变形。
3)装炉:通过机械将生制品装入焙烧炉炉箱内的指定位置。
4)加热:通过燃料的燃烧将其产生的热量间接传递给制品本身,使其连续不断地受热。
5)冷却:按要求逐步减小燃料的供给,以减少对炉内热量的供应;当焙烧过程结束后,通过强制风冷逐渐将炉内的温度降到400 C,然后再自然冷却至环境温度。
6)出炉:采用机械将炉箱内产品周围的填充料清除和移走,然后将产品从炉箱内移出至清理场地,进行产品表面粘附填充料的清理。
7)检查:用肉眼检查产品表面,并通过锤击回声法判断内部结构缺陷。
2焙烧炉炉型的比较 为适应对不同尺寸及品种的产品进行焙烧,设计了不同类型 的炉子及控制系统, 在提高生产率、降低燃料消耗、控制排放物及提高质量的基础上,开发出了各种各样的焙烧炉。
发展到目前, 焙烧炉的主要炉体型式有:带盖式环式焙烧炉、敞开式环式焙烧 炉、车底式焙烧炉、隧道窑等。
当前,在传统炉型的基础上,敞开式环式焙烧炉又得到了新的改进,即在每个炉箱上增加了一个轻质的保温盖, 并对燃烧喷 嘴结构进行了改进,这不仅有效解决了废气的无组织排放问题, 还实现了燃烧系统的低氮燃烧效果。
以上4种类型是现在主流 的焙烧炉炉型,它们的优缺点如表 1所示。
TaHp Iand ifcmuiunta 时 ddiffeml typ® of 序号(PS1阿壮査例丸炉昶变臥曼戕饨 俯息式时)難阿劇肘的强•则込曲制不1■辄 ■ H 开贰开式卅 林糊K 啊如内眦強側山 8U 上砒%贮尢组即帧耐孵面 种辭札翔氏能炉 焊楠和垂貢方罪畫小用般 能駄•牆九料卿加M 用氐4产用1温(锻締推准飜. 3焙烧升温全过程的机理分析对一次焙烧而言,不论外燃式环式焙烧炉(敞开式环式焙烧2 / 11焙烧炉,都是将燃料燃烧后产生的热量传导给耐火砖或容器焙烧的钢桶,然后再由耐火砖或钢桶传递给填充料,最后由填充料将热量传递给生制品,当生制品自身感受的温度超过黏结剂沥青的软化点时,生坯由玻璃态先软化而后变成熔融状态,恰好在周围填充料的挤压下,使其保持原有的几何形状。
焙烧工艺学

4、生产实际中拖后上盖时间的炉室温度调整方法
如果因某种原因本系统炉室拖后半个上盖的时间 间隔才上盖,这时应根据炉内所装产品及炉室实 际温度等具体情况调整升温任务,以拖后半个上 盖时间的炉室的温度为基准,从低温推到高温, 此时,炉室实际温度比调整后任务高的要进行保 温。另外,上盖时间也需要调整,将两个系统上、 启盖时间顺次对调即可。举例如下:
2 、焙烧曲线由短改长的方法 例如由 320 小时/8室运转改为400小时/8室运转, 这两个曲线差80小时,若直接由320小时/8室运转 改为400小时/8室运转,长曲线相对短曲线拖后上 盖,在实际生产中易出现废气温度过高现象,会 导致烟道着火并危及电除尘装置;另外,即使采 用320小时/8室温度走下限,400小时/8室温度走 上限的方法,调温工不易调整,所以实际生产中 一般也采用过渡曲线的方法,即用360小时/8室运 转曲线过渡的方法。 例如1#盖是320小时/8室已上完的盖,从2#炉盖 采用360小时/8室运转曲线,即1#与 2#炉上盖时 间间隔为45小时,上至4#盖时过渡完,从5#盖开 始运转400小时/8室运转曲线,即 5#盖与 4#炉上 盖时间间隔为50小时,5#以后就是运转400小时 /8室运转曲线。
温升阶段 1 2 温度范围(℃) 室温-325 325-600
温升速度 (℃/h)
25 8
累计持续时间 (h)
12 46
3
4
600-800
800保温11小时
13
—
61
72
5
800冷却至250
14.5
110表1-2-4 Fra bibliotek底式炉二次焙烧曲线举例
温升阶段 1 2 3 4 5 6 7 温度范围(℃) 室温-170 170-240 240-430 430-520 520-850 850保温24小时 850冷却至250 温升速度 (℃/h) 5 1 1.4 2.6 3.0 — 12.5 累计持续时间 (h) 24 116 240 275 384 408 456
焙烧炉室冬季施工后烘炉的有效方式
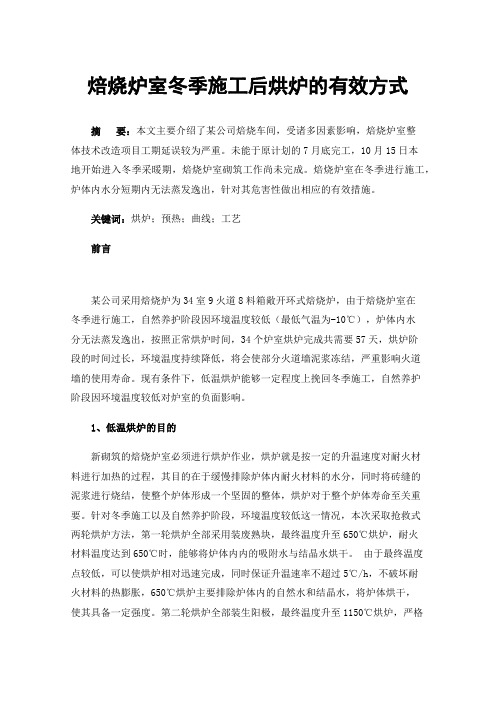
焙烧炉室冬季施工后烘炉的有效方式摘要:本文主要介绍了某公司焙烧车间,受诸多因素影响,焙烧炉室整体技术改造项目工期延误较为严重。
未能于原计划的7月底完工,10月15日本地开始进入冬季采暖期,焙烧炉室砌筑工作尚未完成。
焙烧炉室在冬季进行施工,炉体内水分短期内无法蒸发逸出,针对其危害性做出相应的有效措施。
关键词:烘炉;预热;曲线;工艺前言某公司采用焙烧炉为34室9火道8料箱敞开环式焙烧炉,由于焙烧炉室在冬季进行施工,自然养护阶段因环境温度较低(最低气温为-10℃),炉体内水分无法蒸发逸出,按照正常烘炉时间,34个炉室烘炉完成共需要57天,烘炉阶段的时间过长,环境温度持续降低,将会使部分火道墙泥浆冻结,严重影响火道墙的使用寿命。
现有条件下,低温烘炉能够一定程度上挽回冬季施工,自然养护阶段因环境温度较低对炉室的负面影响。
1、低温烘炉的目的新砌筑的焙烧炉室必须进行烘炉作业,烘炉就是按一定的升温速度对耐火材料进行加热的过程,其目的在于缓慢排除炉体内耐火材料的水分,同时将砖缝的泥浆进行烧结,使整个炉体形成一个坚固的整体,烘炉对于整个炉体寿命至关重要。
针对冬季施工以及自然养护阶段,环境温度较低这一情况,本次采取抢救式两轮烘炉方法,第一轮烘炉全部采用装废熟块,最终温度升至650℃烘炉,耐火材料温度达到650℃时,能够将炉体内内的吸附水与结晶水烘干。
由于最终温度点较低,可以使烘炉相对迅速完成,同时保证升温速率不超过5℃/h,不破坏耐火材料的热膨胀,650℃烘炉主要排除炉体内的自然水和结晶水,将炉体烘干,使其具备一定强度。
第二轮烘炉全部装生阳极,最终温度升至1150℃烘炉,严格控制升温速率使炉墙泥浆烧结,并保证砌炉用砖在热膨胀要求范围内均匀受热,使炉墙有很好的粘接强度。
2、低温烘炉曲线由于吸附水和结晶水在达到650℃维持一段时间以后才能挥发排出,考虑到不破坏耐火材料的热膨胀,确定升温速率不超过5℃/h;低温烘炉起始温度20℃以2.8℃/h升温速率进行升温加热,温度150℃时保温24小时后继续以2.8℃/h升温速率进行升温加热到300℃时保温24小时,300℃开始以5℃/h升温速率到650℃后保温6小时,整个烘炉过程224小时。
车底式焙烧炉

车底式焙烧炉
我公司车底式焙烧炉的技术研发,通过不断的攻坚克难,现已在四川眉山士达新材料有限公司投产应用。
车底式焙烧炉主要用于炭素行业规格较多、对产品的质量要求较高的石墨化产品及精细炭和石墨制品(如石墨化电极、石墨化阴极炭块、核石墨等)的炭素制品的焙烧,与其他常用的炭素焙烧炉窑(主要是环式焙烧炉、隧道窑)比较,具有如下特点:
(1)车底炉焙烧生产运行灵活、焙烧周期短、生产效率高、产品质量好,可实现余热循环利用,几乎适合所有炭素制品,特别是大规格、高质量的炭素制品的焙烧。
与其他常用的炭素焙烧炉窑比较,焙烧周期平均缩短20%,成品率提高1%以上。
(2)按单位产品计,焙烧过程中产生的烟气量小,采用焚烧工艺,使烟气中所含的致癌物3.4苯并芘被焚烧和分解,因而处理后排入大气的废气中不含有致癌物3.4苯并芘,保护了环境。
国内在炭素行业焙烧工序采用的设备主要是生产效率较低和烟气中的有害物不能得到有效治理环式焙烧炉、隧道窑,国外炭素行业焙烧中大多数采用了车底式焙烧炉工艺,因此我们的车底式焙烧炉技术填补了国内的空白,实现碳素的密闭式焙烧,提升产品质量,焙烧产品种类多样化,无有毒气体排放,实现余热循环利用,节能环保,该技术可达到国内领先水平,对整个炭素行业的进步有着重要的意义和作用。
预焙阳极焙烧工艺的优化与实践

预焙阳极焙烧工艺的优化与实践王喜春高翔李东根焦作万方铝业股份有限公司,河南,焦作 454171摘要:本文介绍了焦作万方对预焙阳极焙烧炉控制方法的改进,炉墙缝的合理设置和填充料的正确使用,最终焙烧温度的确定,焙烧曲线的优化,使挥发分能燃烧充分,降低了重油消耗,产品质量、实收率及外观合格率都得到了大幅提高,铝电解使用性能良好。
火焰移动周期可从36h缩短到27h,效益显著。
关键词:预焙阳极;焙烧工艺;优化;挥发分;充分燃烧;质量提高我国的敞开式环式焙烧炉是在消化80年代初引进的日轻焙烧技术的基础上发展起来的,常用的焙烧工艺不能充分利用挥发分燃烧产生的热量,致使焙烧热能消耗一直较高;挥发分燃烧不充分,造成烟气净化负担较重;升温速度控制不理想,产品质量较差。
焦作万方54室敞开式阳极焙烧炉设计产能为4.2万吨/年,由三个火焰系统组成,每个炉室有8条火道7个料箱,分6层卧装;焙烧炉面设备采用机电一体化燃烧架和机电一体化排烟架,DCS自动控制系统;以重油作燃料;所用生阳极为大颗粒配方,沥青用量为17%;于2001年3月投入生产。
经过对焙烧工艺的不断探索和优化,焦作万方在挥发分充分燃烧、燃料消耗降低、实收率增加、阳极内在质量及外观合格率提高等方面取得了较好效果。
1. 控制方法的改进传统升温曲线一般都是控制每个炉室的每条火道的温度,根据温度情况,用人工调节排烟架风门开度和燃料量进行温度控制。
挥发分开始排出时由于炉室温度低基本不能燃烧,到次高温炉室,炭块挥发分大量排出导致炉室温度超高时,则打开看火孔透入冷空气降温,所以挥发分燃烧产生的热量,没有得到充分利用。
一种方法是只控制燃烧架加热的高温炉室温度,负压控制完全凭人工经验,保证高温炉室不带正压就行了,低温炉室温度不控制。
结果是预热炉室温度跟不上升温曲线,挥发分基本没有燃烧就排入了烟道,燃料消耗高,产品实收率低。
焦作万方阳极焙烧加热设备采用脉冲式燃烧控制器,DCS自动控制系统,可精确对每条火道的温度和负压进行自动调节,控温精度为:预热段±20℃;加热段±2℃。
日产1600t/d氧化铝循环流态化焙烧

日产1600t/d氧化铝循环流态化焙烧摘要现今世界成功地应用于工业生产的流态化焙烧炉有三种,原西德鲁奇公司的循环流态焙(C.F.C). 美国铝业公司的流态闪速焙烧炉(F.F.C)。
丹麦史密斯公司的气体悬浮焙烧炉(G.s.c)。
关于普遍应用于氧化铝工业生产的三种流态化焙烧炉进行了分析和比较,指出了三种炉型各自的特点和不足。
流态闪速焙烧炉和循环流态焙烧技术体会成熟,生产稳固性较强,气体悬浮焙烧炉能耗指标先进。
并指出了引进应以流态化闪速焙烧炉优先,消化创新以气体悬浮焙烧炉为基础。
最后指出我国铝工业应以气体悬浮焙烧炉为基础,在消化吸收流态化焙烧技术的前提下进展创新,形成适合我国氧化铝工业特点的流态化焙烧炉。
关键词:闪速流态化焙烧循环流态化焙烧焙烧炉氢氧化铝Cycling fluidiztion calcinations calcinerof producing alumminum oxide 1600t/dAbstractIn today's world successfully applied to industrial production for the three fluidized roaster, the company Xideluqi the cycle of flow-baking (CFC). Alcoa pattern flash roaster (FFC). Denmark Smith's suspension of gas roaster (Gsc). In this paper three kinds of fluidization calciners, which have widely used in alumina production , are analyzed and compared . And their characteristics and shortcoming are pointed out .The author thinks that fluidzation flash calciner and circulation fluidization calciner have ripe experience and stable production , but gas suspension calciner has advanced index for energy consumption . The author also puts forward that import should give priority to fluidization flash calciner and innovation should base on gas suspension calciner. Finally, China's aluminum industry should be suspended gas roaster based in the digestion and absorption fluidization technology roasting under the premise of the development of innovative form suitable for the characteristics of China's alumina industry fluidization roaster.Key words: Flash fluidization calcinations, baking cycle fluidized calcinations, caliner, aluminum hydroxide,目录第一章:概述…………………………………………………………1-一、流态化焙烧新技术在国内外进展状况………………1-二、我国氧化铝焙烧技术和装置现状……………………1-3、氧化铝循环焙烧炉工艺特性、能耗状况……………1-4、氧化铝循环焙烧炉工作原理…………………………第二章:氧化铝循环焙烧炉热工艺性能………………………2-一、氧化铝循环焙烧炉工艺流程介绍 (16)2~二、氢氧化铝的干燥和预热的工艺流程、热工特点 (16)2-3、氢氧化铝的焙烧的工艺流程、热工特点 (17)2-4、氢氧化铝的冷却的工艺流程、热工特点 (18)2-五、氧化铝循环焙烧炉工艺特点、热工特点、热效能 (19)2-六、氧化铝循环焙烧炉工艺性能与气态悬浮焙烧炉工艺性能、热工特点比较(列表格比较) (20)2-7、氧化铝循环焙烧炉工艺性能与回转窑工艺性能及热工特点比较(列表格比较) (23)第三章:氧化铝循环焙烧炉热工计算…………………………3-一、氧化铝循环焙烧炉工艺计算的原始数据及条件 (24)3-二、氧化铝循环焙烧炉工艺进程的物料平稳及物料平稳表 (25)3-3、燃料的燃烧计算及结果表 (26)3-4、氧化铝循环焙烧炉工艺进程的热平稳计算 (28)3-五、氧化铝循环焙烧炉工艺进程的热平稳计算表 (33)3-六、氧化铝循环焙烧炉工艺进程的热平稳与气态悬浮焙烧炉的热平稳比较 (33)第四章、氧化铝选换焙烧炉设计热耗与实际热耗的效能分析………………………………………………………4-1、计算误差分析 (37)4-二、氧化铝循环焙烧炉计算中存在的不可幸免的因素 (39)4-3、两种流态化炉型综合性能比较……………………………39终止语 (40)参考资料 (40)日产1600t/d氧化铝循环流态化焙烧第一章概述1.1 流态化焙烧新技术在国内外进展状况近四十年以来我国一直采纳回转窑炉来焙烧氢氧化铝。
炭素焙烧炉横墙开裂原因与对策分析
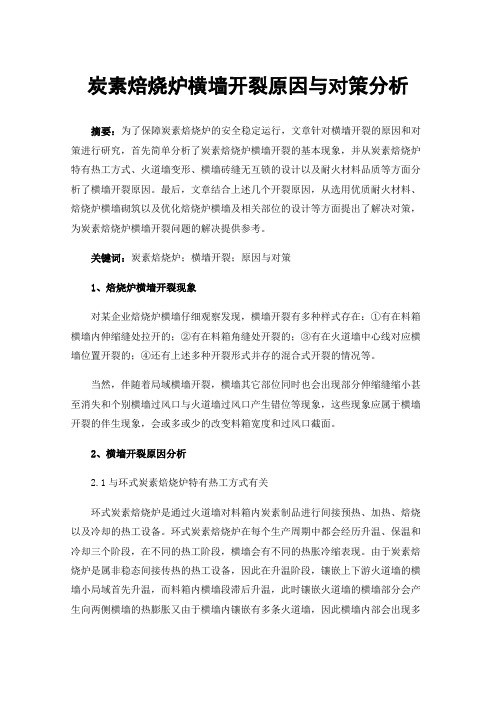
炭素焙烧炉横墙开裂原因与对策分析摘要:为了保障炭素焙烧炉的安全稳定运行,文章针对横墙开裂的原因和对策进行研究,首先简单分析了炭素焙烧炉横墙开裂的基本现象,并从炭素焙烧炉特有热工方式、火道墙变形、横墙砖缝无互锁的设计以及耐火材料品质等方面分析了横墙开裂原因。
最后,文章结合上述几个开裂原因,从选用优质耐火材料、焙烧炉横墙砌筑以及优化焙烧炉横墙及相关部位的设计等方面提出了解决对策,为炭素焙烧炉横墙开裂问题的解决提供参考。
关键词:炭素焙烧炉;横墙开裂;原因与对策1、焙烧炉横墙开裂现象对某企业焙烧炉横墙仔细观察发现,横墙开裂有多种样式存在:①有在料箱横墙内伸缩缝处拉开的;②有在料箱角缝处开裂的;③有在火道墙中心线对应横墙位置开裂的;④还有上述多种开裂形式并存的混合式开裂的情况等。
当然,伴随着局域横墙开裂,横墙其它部位同时也会出现部分伸缩缝缩小甚至消失和个别横墙过风口与火道墙过风口产生错位等现象,这些现象应属于横墙开裂的伴生现象,会或多或少的改变料箱宽度和过风口截面。
2、横墙开裂原因分析2.1与环式炭素焙烧炉特有热工方式有关环式炭素焙烧炉是通过火道墙对料箱内炭素制品进行间接预热、加热、焙烧以及冷却的热工设备。
环式炭素焙烧炉在每个生产周期中都会经历升温、保温和冷却三个阶段,在不同的热工阶段,横墙会有不同的热胀冷缩表现。
由于炭素焙烧炉是属非稳态间接传热的热工设备,因此在升温阶段,镶嵌上下游火道墙的横墙小局域首先升温,而料箱内横墙段滞后升温,此时镶嵌火道墙的横墙部分会产生向两侧横墙的热膨胀又由于横墙内镶嵌有多条火道墙,因此横墙内部会出现多个小局域的方向不同的热膨胀。
边料箱温度低于中间料箱的温度。
因此,中部横墙要向两侧低温区横墙产生热膨胀及热应力,最终形成横墙的位移。
焙烧炉在保温和冷却阶段,无论鼓风架还是冷却架鼓入的冷空气,会使火道对应的横墙段降温相对较快,而料箱对应的横墙段降温较慢(因料箱物料多,热焓大,且有填充料密封,散热差),这样在每个火道对应横墙段与相邻料箱对应的横墙段的小局域范围都会出现温差,料箱处横墙因温度高有向火道处横墙冷缩的热力学运动,会引起料箱处横墙伸缩缝加大的趋势。
焙烧工考试:炭素焙烧工考试学习资料.doc
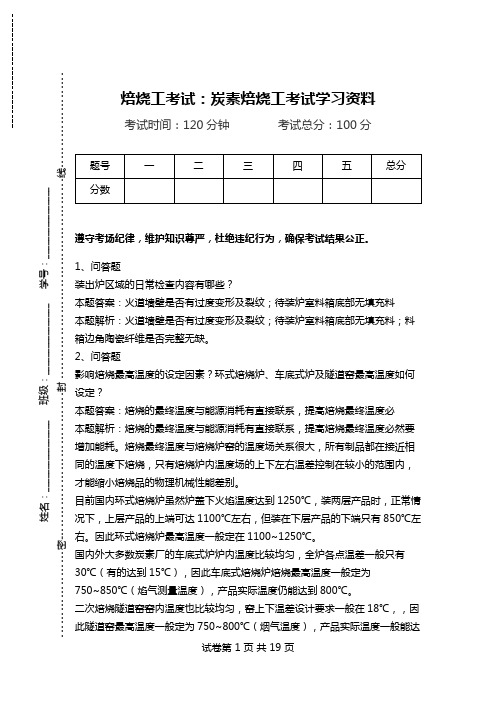
焙烧工考试:炭素焙烧工考试学习资料 考试时间:120分钟 考试总分:100分遵守考场纪律,维护知识尊严,杜绝违纪行为,确保考试结果公正。
1、问答题 装出炉区域的日常检查内容有哪些? 本题答案:火道墙壁是否有过度变形及裂纹;待装炉室料箱底部无填充料 本题解析:火道墙壁是否有过度变形及裂纹;待装炉室料箱底部无填充料;料箱边角陶瓷纤维是否完整无缺。
2、问答题 影响焙烧最高温度的设定因素?环式焙烧炉、车底式炉及隧道窑最高温度如何设定? 本题答案:焙烧的最终温度与能源消耗有直接联系,提高焙烧最终温度必 本题解析:焙烧的最终温度与能源消耗有直接联系,提高焙烧最终温度必然要增加能耗。
焙烧最终温度与焙烧炉窑的温度场关系很大,所有制品都在接近相同的温度下焙烧,只有焙烧炉内温度场的上下左右温差控制在较小的范围内,才能缩小焙烧品的物理机械性能差别。
目前国内环式焙烧炉虽然炉盖下火焰温度达到1250℃,装两层产品时,正常情况下,上层产品的上端可达1100℃左右,但装在下层产品的下端只有850℃左右。
因此环式焙烧炉最高温度一般定在1100~1250℃。
国内外大多数炭素厂的车底式炉炉内温度比较均匀,全炉各点温差一般只有30℃(有的达到15℃),因此车底式焙烧炉焙烧最高温度一般定为750~850℃(焰气测量温度),产品实际温度仍能达到800℃。
二次焙烧隧道窑窑内温度也比较均匀,窑上下温差设计要求一般在18℃,,因此隧道窑最高温度一般定为750~800℃(烟气温度),产品实际温度一般能达姓名:________________ 班级:________________ 学号:________________--------------------密----------------------------------封 ----------------------------------------------线----------------------到700℃以上。
- 1、下载文档前请自行甄别文档内容的完整性,平台不提供额外的编辑、内容补充、找答案等附加服务。
- 2、"仅部分预览"的文档,不可在线预览部分如存在完整性等问题,可反馈申请退款(可完整预览的文档不适用该条件!)。
- 3、如文档侵犯您的权益,请联系客服反馈,我们会尽快为您处理(人工客服工作时间:9:00-18:30)。
环式焙烧炉 (ring type baking furnace)一种由若干个结构相同的炉室呈双排布置,按移动的火焰系统运转,对压型生制品进行焙烧热处理的热工设备。
概况组成环式焙烧炉炉子的各炉室之间既可连通,也可切断。
生产时,把几个炉室串连起来组成一个火焰系统。
(见彩图插页第l5页)其运行情况见图1。
燃料从l3号炉室给入并燃烧,这里成为温度最高的炉室,完成对生制品焙烧后,高温废烟气并不立即排人烟道,而是在负压抽力的作用下依次流经14、15、16、1、2号炉室,利用其余热对生制品进行焙烧前的预热,在这一过程中,烟气温度逐渐降低,从2号炉室流出后,已无再利用的价值,便经连通罩排入烟道。
于是从l3号至2号炉室便构成一个火焰系统。
l3号炉室是加热室,l4号至2号炉室是预热室。
7号至l2号炉室是焙烧完的制品通行冷却的炉室,冷却制品的空气或者是靠12号炉室的负压从大气中吸进,或者是靠鼓风机强制鼓人。
冷却用空气在流经7号至l2号炉室时,与进入冷却温度高达1000℃的制品发生热交换,既冷却了制品,又加热了自身(一般可达800℃以上)。
然后进入13号炉室供烧料燃烧。
起到提高热利用率和焙烧温度的目的。
6号至3号炉室则分别处于出炉、修炉、装炉,待加热作业阶段,是预备炉室。
炉子运行一定的间隔时间后,l3号炉室的制品焙烧结束,停止向其供热,将燃烧装置移至14号炉室,l3号炉室进入冷却阶段,l4号炉室变成加热室,由于火焰系统少了一个炉室需要增加一个炉室,所以在移动燃烧装置的同时将连通烟道的连通罩从2号炉室移至3号炉室,使3号炉室进入火焰系统,形成15号至3号炉室为预热室,8号至l3号炉室为冷却室,其余4号至7号炉室则为预备室,环式炉的运行就是火焰系统按一定的作业周期这样周而复始的循环。
火焰系统一个一个炉室地沿环形路线移动,所包含的炉室号逐渐在变换。
对于火焰系统中的每一个炉室都依次经历烟气预热、焙烧和冷却阶段,然后进行预备作业。
由上可见,对于环式焙烧炉的火焰系统而言是连续作业,而对于单个炉室来说则是间断式周期性作业。
一个火焰系统所辖的炉室数可按生产的具体情况加以调整,一台炉可有一个或几个火焰系统,根据炉子的产能决定。
几个火焰系统同时运行,焙烧的作业周期应协调一致。
带盖炉在加热期间(包括加热和焙烧)以及冷却阶段初期要用炉盖把炉室盖严,使炉室密闭。
无盖炉则没有盖,炉室在运行期间都是敞开的。
带盖炉炉盖和炉室之间的空间是走烟气的通道,有时燃料也在这里燃烧。
所以不盖上炉盖,炉子就无法运行,而无盖炉燃料燃烧和烟气流动都在密闭的火道内进行,所以炉子在运行时不加盖,是敞开的。
带盖炉还可分有火井式和无火井式两种。
火井是燃料的燃烧室和烟气的通道。
无火井炉没有火井,燃料是在炉盖下面的空间燃烧,而以中间隔墙内的上升火道来替代火井的通道作用。
带盖炉装备在炭素厂或铝厂里,既可焙烧电极,又可焙烧铝用阳极和阴极,适用多品种、多规格产品的生产。
无盖炉则主要装备在铝厂,生产铝用阳极,而且要求阳极规格单一。
带盖炉中国的带盖炉由l~2个火焰系统组成。
一个火焰系统的炉子有l6~20个炉室,两个火焰系统的则有30~36个炉室。
其他国家有更大型的炉子,含3~5个火焰系统。
有火井和无火井的带盖炉其结构示于图2、图3。
加热时炉室都盖上炉盖。
对有火井炉燃料在火井内燃烧,对燃烧后的高温烟气流至炉盖下的空间,而无火井炉燃料直接在已充分利用了热量并且温度降至l50℃左右的烟气经中间隔墙内的斜坡烟道进入侧部烟道,炉子排出的烟气在净化系统中除去粉尘和焦油后,最后经排烟机从烟囱排人大气。
有的炉子还设置旁通烟道,以便在排烟机和净化系统出现故障以及焚烧烟道时,烟气直接经旁通烟道进入烟囱。
下面对炉子的主要构造及组成分别做介绍。
炉底及大墙位于炉室的底部及四周,直接砌筑于炉子混凝土基础上,按炉体所处的位置有地下式和地上式两种结构。
一般为方便操作和减少散热,采用地下式结构,把整个炉子砌在深达5m多的地下。
但当地下水位较高时,为防水则采用地上式结构。
要求炉子基础下面的土壤必须坚实而质地均匀。
炉底和大墙中设保温层,以减少散热损失并保护基础。
炉盖下的空间燃烧,之后烟气通过格子砖孔垂直向下到达炉底,经砖墩再流至下一个串联的炉室,在这里炉气经火井或上升火道又到达炉盖下面,然后再经格子砖,炉底流至第三个炉室,依次烟气流经串联在一起的每一个炉室,完成对生制品的焙烧作业。
料箱及火道用格子砖墙把炉室分隔成4~8个等面积的长方形或长条形料箱,料箱内装制品及填充料,格子砖墙上的孔即为火道。
料箱和火道的底部是坑面砖。
坑面砖靠砖墩支撑,砖墩之间的间隙可以走烟气。
热烟气就是在这一流动过程中完成对料箱中的制品的热交换。
火井及中间隔墙火井位于炉室的前端。
只有火井式炉才有火井。
送入炉内的燃料,先在火井中与预热空气混合进行燃烧,生成的热烟气再进入炉室,达到温度均匀的目的。
无火井式炉,燃料直接在炉盖下面的空间燃烧。
中间隔墙位于相邻两个炉室之间,内中有连通两个炉室的烟道,从前一个炉室炉底流来的烟气,对有火井式炉要经过火井才能到达炉室上部;对无火井式炉,是通过中间隔墙中的上升火道直接到达炉室上部。
当烟气不需引入下一个炉室时,还可通过中间隔墙中的斜坡烟道与侧部烟道接通。
燃烧系统中国多数带盖炉以发生炉煤气为燃料,煤气管铺设在炉两侧的地沟内,对应每个炉室设支管,并以煤气连通罩与炉室接通,送入炉内的煤气经埋砌在砖里的小煤气管从烧嘴砖送入并燃烧,有火井式炉烧嘴砖砌在火井出口处,煤气在火井上部燃烧,无火井式炉烧嘴砖砌在大墙里,煤气在炉盖下面的空间燃烧。
少数炉子以固定在燃烧架上的煤气烧嘴或重油喷嘴直接从炉盖插入进行燃烧。
对于有火井式炉,这种燃烧方式可以使燃烧和空气混合充分燃烧完全。
煤气和重油管道应设吹洗清扫装置,重油管道还应有加热保温设施。
连通火道在炉子的两个端头,使两排炉室彼此串连起来,烟气能够相通。
因为连通火道较长,为防止烟气温度降低太多,有的炉子在连通火道上还设有补充热量的辅助燃烧装置。
侧部烟道位于炉子两侧。
有砖烟道和钢烟道两种结构,钢烟道的气密性较好。
在侧烟道上对应每个炉室设有竖烟道,需要排烟时采用烟气连通罩使炉室和竖烟道接通,这样,炉室的烟气经斜坡烟道、烟气连通罩、竖烟道而进入侧部烟道。
从炉室排出的烟气温度在150℃左右。
烟气中含有的焦油会沉积下来,为便于汇集,烟道宜带有坡度。
烟道应定期清扫和焚烧,以免断面减小导致炉子产生负压。
回收的焦油可用做燃料供人炉内。
炉盖炉室上炉盖后,其上部的敞开部分即为密闭的空间。
进入火焰系统的炉室都要加盖,完成焙烧进入冷却的炉室也暂不取盖,这一方面可以减缓冷却,另外还可以提高进入高温炉室作为助燃的预热空气的温度。
一个火焰系统需ll~13个炉盖。
炉盖由骨架和耐火材料构成,重约l0~15t,使用天车吊运。
炉盖所用的耐火材料有耐火砖与浇注料两种。
炉盖砖为特异型,制作困难,砌筑要求高,但是使用寿命可长达8~10年。
浇注料炉盖施工简便,造价低,有一定的推广价值。
炉盖的骨架是铸铁或铸钢结构,可以保证结构强度的要求。
此外,炉盖还应加强保温、防止漏气,以减少散热损失和控制烟气量。
强制冷却装置中国大部分带盖炉都采取自然冷却方式,只有在炎热地区或炉子的炉室数较少时才对焙烧后的制品进行强制冷却。
这里在炉子四周设强制冷却风管,并配置风机。
工作时将外部空气鼓人炉内冷却制品,被加热了的空气经风管和风机排至车间,风管和炉室的连接也是采用连通罩。
无盖炉中国的无盖炉由34~90个炉室组成,分为2~5个火焰系统。
每个系统中有5~6个炉室加热,9~10个炉室冷却,其余4个炉室用于装出炉和检修。
无盖炉的结构见图4。
无盖炉没有炉盖,燃料直接在密闭的火道内或横墙的上部通道燃烧。
火道内设有折流墙,使燃烧生成的高温烟气在火道里迂回流动,并经横墙的上部通道流人串连的下一个炉室的火道,在这里再经过一次或两次折流,翻过横墙又进入第三个炉室的火道。
依次,烟气流经串连在一起的火焰系统中每一个炉室的火道,完成对料箱内的生制品的加热和焙烧后,温度已降至350℃以下,最后经安装在横墙上的烟道排至环形烟道。
无盖炉炉后也设有烟气净化系统,也采用机械排烟。
经过净化的烟气由烟囱排人大气。
炉底、侧墙和挡墙无盖炉也有地上和地下两种配置方式。
砌在炉基础上的炉底由轻质浇注料,保温砖和耐火砖组成。
侧墙为保温砖,挡墙为耐火砖,这两部分相当于有盖炉的大墙。
炉底和侧墙的保温砖可防止炉内热量的散失,并使}昆凝土基础表面不超过允许的温度。
横墙位于炉室之间,相当于有盖炉的中间隔墙。
横墙上部有与前后火道相对应的通道,其顶部有方孔安全铸铁座和盖。
从这里既可供入燃料燃烧,又可以通过烟道抽出废烟气,还可以向冷却炉室送风或抽风,以进行制品的冷却。
火道及料箱横墙之间的部分是炉室,由几条平行的纵向道把炉室分为(n~1)个大小相同的料箱。
一般,每个炉室有5~7个料箱,6~8条火道。
火道内设有折流墙,使烟气在火道内按v形或w形做上下曲折的流动。
这种流动方式有利于火道内的温度均匀。
火道壁的部分砖缝砌筑时做得能够透气,以使料箱内的制品逸出的挥发分能够透过这些砖缝进入火道内燃烧。
火道顶部开有2~4个孔,便于供人燃料,测温测压及观察等操作。
有把火道做成整体装配式的,便于检修火道时用天车进行整体吊装。
这样既不会影响炉子运转,又便于检修的作业环境得到改善,从而可获得更好的修炉质量。
火焰系统内串连炉室的前后火道是彼此相通的,但横向的各条火道则是彼此独立的。
只有在进人烟道后,各条火道的烟气才混合。
连通火道位于炉子端部把两排炉室的火道连接起来的通道。
连通火道的结构应尽量使烟气重新分配至各条火道时能够均匀。
环形烟道安装在炉子周围炉子排烟的通道。
环形烟道一般为钢烟道,内衬耐火材料,对应于每个横墙设铸铁的烟气接口,平时加盖,排烟时用烟斗连接横墙上对应每条火道的方孔和环形烟道上相应的烟气接口,废烟气就从火道导入环形烟道。
环形烟道的出口接烟气净化系统。
燃烧装置无盖炉一般以发生炉煤气或重油为燃料。
无论采用何种燃料,都是以便于移动的燃烧架实现对炉子的供热。
燃烧架用软管和安装于炉两侧的燃料管连接,通过横墙口的方孔或火道上的燃烧口向炉子送人燃料。
燃烧架的煤气和重油管道应设吹洗清扫装置。
重油管道还应有加热保温措施。
对燃料量的控制有手动和自动两种方式,自动的方式可以达到准确控制火道温度,节约燃料的目的。
一个炉室用1~2个燃烧架加热。
用2个燃烧架可以缩小炉室的前后温差。
也可以把2个燃烧架做成一体,即所谓双火焰燃烧架。
烟斗用于炉室排烟的可以移动的装置。
用烟斗把要排烟的炉室和环形烟道连接起来,就能将炉室的废气引导至环形烟道内,烟斗上设有测温测压装置,根据炉室调温的要求,用手动或自动的方式调节烟斗总管或支管上的蝶阀,就能控制火道的负压。