环式焙烧炉技术进展
环式焙烧炉

环式焙烧炉 (ring type baking furnace)国内外碳素焙烧炉发展状况环视焙烧炉是生产碳素制品最关键的大型热工炉窑设备,对一个预焙阳极生产厂而言,环式焙烧炉的基建投资占整个碳素厂总投资的50%~60%,而且焙烧炉设计及技术的先进性对产品的质量单位投资的产能、能耗及能源综合利用、炉子寿命、产品生产成本都有很大的影响,焙烧炉火道墙结构的设计,材质的选择和施工工艺是设计焙烧炉最关键的技术。
碳素生产企业环式焙烧炉火道墙采用砖砌结构,由轻质耐火砖、粘土耐火砖、异型耐火砖砌筑而成。
根据焙烧炉火道墙尺寸的不同,每条火道墙重约7~9吨,砖层多打40层。
在生产过程中,依照工艺要求反复地升降温(1250℃~1300℃),降温(20℃~30℃),每次装、出炉时,天车夹具、碳素产品都不可避免地会碰撞到火道墙上,这样火道墙就会发生变形,变形达到一定程度,就必须拆除重砌。
火道墙主要损坏形式:传统工艺采用耐火砖加耐火泥浆砌筑,采用了卧缝打灰、立缝不打灰的砌筑工艺,这样会出现砖缝泥浆脱落,影响了火道墙的整体结构强度。
由于砌砖更多的注重了火道墙的牢固性,但忽视了火焰的流向,不可避免地出现温度死角,对产品的均匀性造成影响。
在生产过程中由于产生不均匀热膨胀以及频繁升降温和装出焙烧品的撞击,造成火道墙变形,继而火焰不走正道→温度死角→温差变大→炉箱变形等恶性循环,能耗增大,降低炉体寿命,出现频繁中小修。
目前国内碳素焙烧炉的设计是50年代从国外引进的技术,火道墙采用砖砌筑结构,经历了半个世纪,并为大多数碳素厂所采用。
随着生产实践的进一步深入,该技术的一些技术问题也逐渐暴露出来。
(1)边火道墙向外突出或整体倾斜,使料箱变窄,装出炉困难;(2)中间火道向内外凹陷,使火道变窄,影响热流气体的流动和燃烧效果;(3)火道墙裂缝严重,导致漏风漏料,影响产品质量,增大热能损耗,破损比较严重的火道墙必须进行中修、大修,由于火道墙是由小块耐火砖砌筑而成,拆除一条火道墙大约需要7~8小时,重新砌筑需24小时左右,拆除并重砌一条火道墙就必须搬运近17吨的材料,这不仅给修炉工作带来困难,而且给车间的正常生产增加难度。
环式焙烧炉讲解

furnace) baking (ring type 环式焙烧炉国内外碳素焙烧炉发展状况环视焙烧炉是生产碳素制品最关键的大型热工炉窑设备,对一个预焙阳极生产厂而言,环式焙烧炉的基建投资占整个碳素厂总投资的50%~60%,而且焙烧炉设计及技术的先进性对产品的质量单位投资的产能、能耗及能源综合利用、炉子寿命、产品生产成本都有很大的影响,焙烧炉火道墙结构的设计,材质的选择和施工工艺是设计焙烧炉最关键的技术。
碳素生产企业环式焙烧炉火道墙采用砖砌结构,由轻质耐火砖、粘土耐火砖、异型耐火砖砌筑而成。
根据焙烧炉火道墙尺寸的不同,每条火道墙重约7~9吨,砖层多打40层。
在生产过程中,依照工艺要求反复地升降温(1250℃~1300℃),降温(20℃~30℃),每次装、出炉时,天车夹具、碳素产品都不可避免地会碰撞到火道墙上,这样火道墙就会发生变形,变形达到一定程度,就必须拆除重砌。
火道墙主要损坏形式:传统工艺采用耐火砖加耐火泥浆砌筑,采用了卧缝打灰、立缝不打灰的砌筑工艺,这样会出现砖缝泥浆脱落,影响了火道墙的整体结构强度。
由于砌砖更多的注重了火道墙的牢固性,但忽视了火焰的流向,不可避免地出现温度死角,对产品的均匀性造成影响。
在生产过程中由于产生不均匀热膨胀以及频繁升降温和装出焙烧品的撞击,造成火道墙变形,继而火焰不走正道→温度死角→温差变大→炉箱变形等恶性循环,能耗增大,降低炉体寿命,出现频繁中小修。
目前国内碳素焙烧炉的设计是50年代从国外引进的技术,火道墙采用砖砌筑结构,经历了半个世纪,并为大多数碳素厂所采用。
随着生产实践的进一步深入,该技术的一些技术问题也逐渐暴露出来。
(1)边火道墙向外突出或整体倾斜,使料箱变窄,装出炉困难;(2)中间火道向内外凹陷,使火道变窄,影响热流气体的流动和燃烧效果;(3)火道墙裂缝严重,导致漏风漏料,影响产品质量,增大热能损耗,破损比较严重的火道墙必须进行中修、大修,由于火道墙是由小块耐火砖砌筑而成,拆除一条火道墙大约需要7~8小时,重新砌筑需24小时左右,拆除并重砌一条火道墙就必须搬运近17吨的材料,这不仅给修炉工作带来困难,而且给车间的正常生产增加难度。
(word完整版)环式焙烧炉

环式焙烧炉 (ring type baking furnace)国内外碳素焙烧炉发展状况环视焙烧炉是生产碳素制品最关键的大型热工炉窑设备,对一个预焙阳极生产厂而言,环式焙烧炉的基建投资占整个碳素厂总投资的50%~60%,而且焙烧炉设计及技术的先进性对产品的质量单位投资的产能、能耗及能源综合利用、炉子寿命、产品生产成本都有很大的影响,焙烧炉火道墙结构的设计,材质的选择和施工工艺是设计焙烧炉最关键的技术。
碳素生产企业环式焙烧炉火道墙采用砖砌结构,由轻质耐火砖、粘土耐火砖、异型耐火砖砌筑而成.根据焙烧炉火道墙尺寸的不同,每条火道墙重约7~9吨,砖层多打40层。
在生产过程中,依照工艺要求反复地升降温(1250℃~1300℃),降温(20℃~30℃),每次装、出炉时,天车夹具、碳素产品都不可避免地会碰撞到火道墙上,这样火道墙就会发生变形,变形达到一定程度,就必须拆除重砌。
火道墙主要损坏形式:传统工艺采用耐火砖加耐火泥浆砌筑,采用了卧缝打灰、立缝不打灰的砌筑工艺,这样会出现砖缝泥浆脱落,影响了火道墙的整体结构强度。
由于砌砖更多的注重了火道墙的牢固性,但忽视了火焰的流向,不可避免地出现温度死角,对产品的均匀性造成影响。
在生产过程中由于产生不均匀热膨胀以及频繁升降温和装出焙烧品的撞击,造成火道墙变形,继而火焰不走正道→温度死角→温差变大→炉箱变形等恶性循环,能耗增大,降低炉体寿命,出现频繁中小修。
目前国内碳素焙烧炉的设计是50年代从国外引进的技术,火道墙采用砖砌筑结构,经历了半个世纪,并为大多数碳素厂所采用。
随着生产实践的进一步深入,该技术的一些技术问题也逐渐暴露出来。
(1)边火道墙向外突出或整体倾斜,使料箱变窄,装出炉困难;(2)中间火道向内外凹陷,使火道变窄,影响热流气体的流动和燃烧效果;(3)火道墙裂缝严重,导致漏风漏料,影响产品质量,增大热能损耗,破损比较严重的火道墙必须进行中修、大修,由于火道墙是由小块耐火砖砌筑而成,拆除一条火道墙大约需要7~8小时,重新砌筑需24小时左右,拆除并重砌一条火道墙就必须搬运近17吨的材料,这不仅给修炉工作带来困难,而且给车间的正常生产增加难度。
多孔环式炭素焙烧炉砌筑施工工法

多孔环式炭素焙烧炉砌筑施工工法多孔环式炭素焙烧炉砌筑施工工法一、前言多孔环式炭素焙烧炉砌筑施工工法是指在建造炭素焙烧炉时所采用的一种施工方法。
这种施工工法具有许多特点,适用范围广泛,能够确保施工质量,同时也需要注意安全措施。
本文将详细介绍多孔环式炭素焙烧炉砌筑施工工法的工艺原理、施工工艺、劳动组织、机具设备、质量控制、安全措施、经济技术分析等内容,并附上一个工程实例。
二、工法特点多孔环式炭素焙烧炉砌筑施工工法的特点如下:1. 炭素焙烧炉采用多孔环式结构,能够提高炉内物料的利用率和烧结效果。
2. 工法施工简单,操作方便,能够提高施工效率和质量。
3. 多孔环式炭素焙烧炉砌筑具有较好的耐火性能和导热性能,能够保证炉体使用寿命和热效率。
4. 炭素焙烧炉采用多孔环式结构,能够方便进行炉内物料的装卸和烧结过程的控制。
5. 工法具有良好的环保效果,能够减少对环境的污染和资源的浪费。
三、适应范围多孔环式炭素焙烧炉砌筑施工工法适用于以下范围:1. 钢铁工业:可用于炼铁、钢铁冶炼等工艺中的焙烧炉建造。
2. 碳素工业:可用于炭素制品生产中的炼焦、煅烧等过程中的炭素焙烧炉建设。
3. 化工工业:可用于化工生产中的石油焙烧等工艺过程中的焙烧炉建造。
4. 粉末冶金工业:可用于粉末冶金中的烧结炉建设。
四、工艺原理:多孔环式炭素焙烧炉砌筑施工工法的核心在于利用多孔环式结构提高炉内物料的利用率和烧结效果。
其工艺原理主要有以下几点:1. 通过设定合理的炉体结构和烟道布置,保证炉内物料在焙烧过程中得到充分的接触和反应。
2. 通过选择适当的耐火材料和炉体材料,提高炉内物料的热传导性和耐高温性能。
3. 通过控制炉内温度、气氛和气流,实现物料的热解、烧结和冶炼等过程。
五、施工工艺多孔环式炭素焙烧炉砌筑施工工法的施工工艺包括以下几个阶段:1. 基础施工:包括基础开挖、基础搅拌、基础浇筑等工序。
2. 砌筑施工:包括炉壁砌筑、炉顶砌筑、烟道砌筑等工序。
一种环式焙烧炉的烘炉方法

多孔环式焙烧炉施工工艺

表2 回填 陆域边坡抗滑稳定计算成果表
量的测点作为永久监测点 。 [ 4 ] 王 强. 塑料排 水预压 法加 固软基机 理及 沉降计 算方 法研
4 . 2
水 平 位 移 监 测
究[ D] . 南京 : 河海大学硕 士论 文, 2 0 0 1 .
5 ] 邓礼久 , 金 亮星 , 罗嘉金 . 塑料排 水堆栽预 压 法处理软基 的 在 回填土过程 中设置水平位移 观测 点进行监 测 , 回填至高程 [ 固结效果[ J ] . 铁道科 学与工程 学报 , 2 0 1 3 , l O ( 3 ) : 6 9 - 7 3 . 1 2 . 0 m 可按 2 4 h水平位移大 于 1 0 mm作为停止加载控制标准 ; 后 6 ] 黎 玉, 王齐福 . 塑料排 水板堆栽预 压法软基加 固监测分析 期 回填时以 2 4 h的水平位 移大于 5 m m作为 停止加 载控制标 准。 [ 填筑速率应 以水平位移控制为主 , 如超过此限应立即停止填筑。
实, 并 向湖 区方 向设 置 0 . 5 %的排水坡 面 。回填 速度 根据要 求进
工程 区场地起伏较 大 , 土层分 布变化 也 比较大 , 软 基分 布不 行控制 , 在 回填 过程 中对 侧 向变形进 行观 测 , 一 旦发 现侧 向变形 均匀 , 为节省工程投 资并确保 工程 的安全 性 , 首 先要 确定 软基 的 过大 , 则要减小加载 速度 或停 止加载 , 休止一段时间后再回填。 分布范围 , 有针对性 的采用 不同 的地基处 理方法 , 并 在施 工期及
多孔环式炭素焙烧炉砌筑
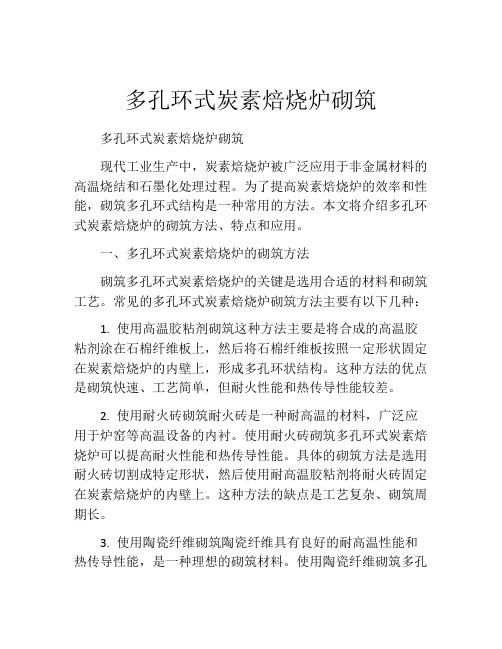
多孔环式炭素焙烧炉砌筑多孔环式炭素焙烧炉砌筑现代工业生产中,炭素焙烧炉被广泛应用于非金属材料的高温烧结和石墨化处理过程。
为了提高炭素焙烧炉的效率和性能,砌筑多孔环式结构是一种常用的方法。
本文将介绍多孔环式炭素焙烧炉的砌筑方法、特点和应用。
一、多孔环式炭素焙烧炉的砌筑方法砌筑多孔环式炭素焙烧炉的关键是选用合适的材料和砌筑工艺。
常见的多孔环式炭素焙烧炉砌筑方法主要有以下几种:1. 使用高温胶粘剂砌筑这种方法主要是将合成的高温胶粘剂涂在石棉纤维板上,然后将石棉纤维板按照一定形状固定在炭素焙烧炉的内壁上,形成多孔环状结构。
这种方法的优点是砌筑快速、工艺简单,但耐火性能和热传导性能较差。
2. 使用耐火砖砌筑耐火砖是一种耐高温的材料,广泛应用于炉窑等高温设备的内衬。
使用耐火砖砌筑多孔环式炭素焙烧炉可以提高耐火性能和热传导性能。
具体的砌筑方法是选用耐火砖切割成特定形状,然后使用耐高温胶粘剂将耐火砖固定在炭素焙烧炉的内壁上。
这种方法的缺点是工艺复杂、砌筑周期长。
3. 使用陶瓷纤维砌筑陶瓷纤维具有良好的耐高温性能和热传导性能,是一种理想的砌筑材料。
使用陶瓷纤维砌筑多孔环式炭素焙烧炉的方法是将陶瓷纤维按照一定形状固定在炭素焙烧炉的内壁上,然后使用高温胶粘剂进行固定。
这种方法的优点是砌筑周期短、砌筑简单,但陶瓷纤维的耐火性能稍逊于耐火砖。
二、多孔环式炭素焙烧炉的特点多孔环式炭素焙烧炉相比传统的炭素焙烧炉具有以下几个特点:1. 高温均匀多孔环式炭素焙烧炉砌筑多孔结构,可以提供更好的热传导性能,从而使燃烧更加均匀,提高炭素焙烧炉的高温效率。
2. 耐火性能优异多孔环式炭素焙烧炉使用耐火材料进行砌筑,耐高温性能优异,能够承受高温环境下的烧结和石墨化过程,延长炭素焙烧炉的使用寿命。
3. 操作方便多孔环式炭素焙烧炉具有砌筑周期短、操作方便的特点,降低了生产成本,提高了生产效率。
三、多孔环式炭素焙烧炉的应用多孔环式炭素焙烧炉广泛应用于非金属材料的高温烧结和石墨化处理过程。
科技成果——炭素环式焙烧炉燃烧系统优化技术

科技成果——炭素环式焙烧炉燃烧系统优化技术适用范围钢铁行业炭素环式焙烧炉燃烧系统及炉盖节能改造行业现状目前我国大部分炭素企业采用环式炉进行生制品的一次焙烧。
由于燃料由火井上部的煤气入口水平喷入,煤气和炉内产生的沥青烟燃烧不充分,沥青烟产生量大,炉盖漏风,保温性差,能耗高,废气净化难度大。
据统计,目前国内炭素企业的平均焙烧能耗约340kgce/t。
目前该技术可实现节能量7万tce/a,减排约18万tCO2/a。
成果简介1、技术原理该技术采用新型的燃烧器,煤气自上而下进入火井,与自下而上的烟气及助燃空气混合,使燃烧更加充分,提高了燃烧效率;根据炉室温度和升温曲线自动调节煤气流量,使炉子温控更精确,减少燃料浪费;通过使更多的沥青烟参与燃烧,最大限度地节省燃料,减少沥青烟的产生和排放量;通过新型联通罩的自动调节,降低炉室负压,减少烟气量,降低烟气流速,提高传热效率,减少热损失;通过提高炉盖的密闭性和保温效果,减少热损失。
2、关键技术(1)采用先进的煤气燃烧器、可移动式燃烧架和烟气联通罩,通过采集炉室温度和系统压力参数,自动调节煤气用量和烟气量,实现对炉室温度的精确控制,提高煤气及沥青烟的燃烧效率,提高产品(2)通过改变炉盖的部分结构及耐火材料,减轻了炉盖重量、提高保温和密封效果,延长使用寿命。
3、工艺流程炭素环式焙烧炉燃烧系统优化工艺流程图主要技术指标焙烧品单位能耗(包括新增的蒸气及电力消耗)可降低约39%。
技术水平该技术于2010年通过中国炭素行业协会组织的科技成果鉴定,目前已在国内30多台炭素环式焙烧炉上使用,能耗平均下降30%以上,节能效果显著。
典型案例典型用户:中钢集团吉林炭素股份有限公司、河北联冠电极股份典型案例1建设规模:年产1.32万t石墨电极焙烧品的新型炭素焙烧炉,建设条件为煤气热值大于1200kcal/Nm3,煤气中粉尘、焦油含量小于800mg/m3(粉尘、焦油含量为合测值),需蒸汽1t/h。