切削用量的合理选择
合理选择切削用量
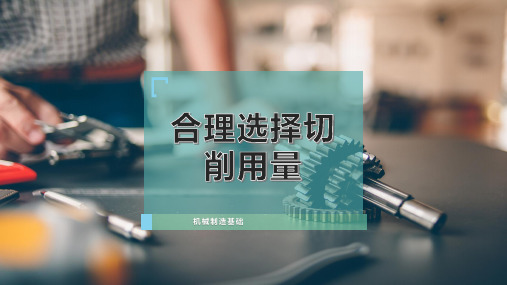
16
课堂实训——选择切削用量
机械制造基础
3)确定切削速度 vc 根据已知条件和已确定的 ap 和 f 值,由P139-140页表得切削速度 vc 130~160 m/min。由于该轴为
细长轴,应选取较小的切削速度,因此切削速度 vc 130 m/min。计算机床转速为
n 1 000vc 1 000 130 1 035 r/min πd 3.14 40
70~80
背吃刀量 ap/(mm)
2~6 进给量 f /(mm/r)
0.3~0.6
切削速度 vc /(m/min)
100~120 90~110 70~90 70~90 50~70 60~80 60~70
6~10
0.6~1
70~90 60~80 50~70 50~70 40~60 50~70 50~60
0.4~0.7 0.6~0.9
0.4~0.6
跳到 P144
5
二、进给量的选择
机械制造基础
续表
铸铁及 铜合金
16×25
20×30 25×25
40
0.4~0.5
60
0.6~0.8
0.5~0.8
0.4~0.6
100
0.8~1.2
0.7~1
0.6~0.8
0.5~0.7
400
1~1.4
1~1.2
0.8~1
0.6~0.8
寸为 46 mm×350 mm,加工尺寸为 39 mm×300 mm。在普通卧式车床CA6140上加工,使用焊接式硬
质合金YT15车刀,刀杆截面尺寸为16 mm×25 mm,刀具几何参数为
o 15,o 8,r 75, s 0,rε 1 mm,br1 0,
第七章 切削用量的选择

在选择合理切削用量时,必须考虑加工性质。 由于粗加工和精加工要完成的加工任务和追求的目 标不同,因而切削用量选择的基本原则也完全不同。
7.7.1
粗加工时切削用量选择的基本原则
粗加工时高生产效率是追求的基本目标。这个目 标常用单件机动时最少或单位时间切除金属体积最多 来表示。下面以外圆纵车为例加以说明(图7-1)。
3.确定切削速度vc 当刀具使用寿命T、背吃刀量ap与进给量f确定 后,即可按式(7.4)计算切削速度vc
(7.4) 式中 k vc——切削速度修正系数,与刀具材料和几 何参数、工件材料等有关。 Cv 、 xv 、yv 、m及K vc值见表7.3.加工其他工件 材料时的系数及指数可查切削用量手册。
由式(6.6)可知,在选择切削用量时:应首先 选择最大的ap,其次要在机床动力和刚度允许的前提 下,选用较大的f,最后再根据式(6.6)选择合理的 vc值。
当刀具使用寿命为一定值用高速钢车刀切钢时,切削用量之间有式(7.3) 关系
(7.3)
式(7.3)表明,为保证刀具合理使用寿命,
不参与优化。因此,切削用量的优化主要是指切削切 削速度vc与进给量f的优化组合。 以单件成本最低为目标的优化目标函数的建 立过程如下: 当ap一定时,由式(7.1)
式中 由式(6.5)得
式中
将tm 、T值代入式(6.14),得 式中
式( 7.9 )即为所建立的单件成本最低的目标函 数。求该函数的极值,得
合理切削用量的选择可按下列方法进行:
1.确定背吃刀量ap
ap一般根据性质与加工余量来确定。
切削加工一般分为粗加工、半精加工和精加工
粗加工时,在保留半精与精加工余量的前提下,若机 床刚度允许,加工余量应尽可能一次切掉,在中等功 率机床上采用硬质合金刀具车外圆时,粗车取ap=2 ~ 6mm,半精车去ap=0.2 ~ 3mm,精车取ap=0.1 ~ 0.3mm。
第二章第六节切削用量的选择方案

• 精加工多采用较高的切削速度,即可提高加工效率, 又要照顾到刀具使用寿命。
二、三要素的选定
1. ap的选定 • 一般根据加工性质与加工余量确定ap。切削加工一
般分为粗加工、半精加工和精加工。 (1)粗加工:考虑机床功率,系统刚度尽可能大
第六节 切削用量的选择
一、切削用量的选择原则
每次切削加工都必须选择切削速度、进给量和背吃刀量,这是 肯定的。
切削用量这三个要素与 生产效率、加工质量和加工成本都有非 常密切的关系。
我们在追求最高的生产效率、最好的加工质量和最低的加工成 本时如何选择切削用量三个要素呢?怎样选择才算合理呢? 下面让我们来分析一下切削用量三要素与生产效率、加工质 量和加工成本的关系。
• (2)工件材料强度、硬度高时,应选较低的vc。 • (3)切削合金钢比切削中碳钢切削速度降低20%~30%;切削
调质状态的钢比切削正火、退火状态钢要降低切削速度 20%~30%;切削有色金属比切削中碳钢的切削速度可提高 100%~300%。
• (4)刀具材料的切削性能愈好,切削速度也选得愈高,如硬质 合金钢的切削速度比高速钢刀具可高几倍,涂层刀具的切削 速度比未涂层刀具要高,陶瓷、金刚石和CBN刀具可采用更 高的切削速度。
f ↑ → 残留面积↑ Ra↑
v c → 通过积屑瘤来影响
2.切削用量与生产率 (1) 生产率
1 w
tw
tw
tm
tct
tm T
tot
tm ( ----- 机动时间)基本工艺时间 tct ----- (安装、调整、换刀)辅助工艺时间 tot ----- 其他辅助时间
刀具几何参数和切削用量的合理选择

加工条件:工艺系统刚性差时,易出现振
动,应选取较小的后角αo;加工表面质量要求 较高时,为减轻刀具与工件之间的摩擦,应选
取较大的后角αo;尺寸精度要求较高时,应选 取较小的后角αo,以减小刀具的径向磨损值NB 值,如下图所示。
硬质合金车刀合理后角的参考值如下表所示。
② 后角αo的选择
切削厚度hD:粗加工时,切削厚度hD较大,要 求切削刃坚固,应选取较小的后角αo。精加工时, 切削厚度hD较小,磨损主要发生在后刀面上,为降 低磨损,应选取较大的后角αo。
工件材料:工件材料强度和硬度较高时,为提
高切削刃强度,应选取较小的后角αo;工件材料软、 塑性大时,后刀面磨损严重,应选取较大的后角αo; 工件材料脆性较大时,载荷集中在切削刃处,为提
负前角双面型:该形式的刀具使刀具的重磨次数 增加,最大程度地减少了前刀面和后刀面的磨损。同 时负前角的倒棱应有足够的宽度,以确保切屑沿该棱 面流出。
(3)倒棱
倒棱是增强切削刃强度的一种措施。在用脆性大 的刀具材料粗加工或断续切削时,磨倒棱能够减小刀 具崩刃,显著提高刀具耐用度(可提高1~5倍)。
倒棱宽度br1不可太大,以便切屑能沿前刀面 流出。br1的取值与进给量f有关,常取br1≈ (0.3~0.8)f。其中,精加工时取小值,粗加工
② 前角γo的选择
工件材料:工件材料的强度、硬度较低,塑
性较好时,应选取较大的前角γo;工件材料脆性较 大时应选取较小的前角γo;工件材料强度、硬度较 高时,应选取较小的前角γo,甚至负前角。
刀具材料:刀具材料的强度和韧度高时,如高 速钢,可选取较大的前角γo;反之,刀具材料的强度 和韧度差时,如硬质合金,应选取较小的前角γo。
切削用量的确定

总之,切削用量的具体数值应根机床性 能、相关的手册并结合实际经验用类比方 法确定。同时,使主轴转速、切削深度及 进给速度三者能相互适应,以形成最佳切 削用量。
2.进给速度的确定 进给速度是数控机 床切削用量中的重要参数,主要根据零件 的加工精度和表面粗糙度要求以及刀具、 工件的材料性质选取。最大进给速度受机 床刚度和进给系统的性能限制。确定进给 速度的原则:
1)当工件的质量要求能够得到保证时, 为提高生产效率,可选择较高的进给速度。 一般在100200mm/min范围内选取。
1.主轴转速的确定主轴转速应根据允许的 切削速度和工件(或刀具)直径来选择。 其计算公式为: n=1000v/πD 式中 v---切削速度,单位为m/min,由刀具的耐用 度决定;n-- -主轴转速,单位为 r/min; D----工件直径或刀具直径,单位为mm。 计算的主轴转速n最后要根据机床说明书选 取机床有的或较接近的转速。
2)在切断、加工深孔或用高速钢刀具加 工时,宜选择较低的进给速度,一般在 20~50mm/min范围内选取。
高时,进给速度应选小些,一般在20~ 50mm/min范围内选取。
3)刀具空行程时,特别是远距离“回零” 时,可以设定该机床数控系统设定的最高 进给速度。
3.背吃刀量确定 背吃刀量根据机床、 工件和刀具的刚度来决定,在刚度允许的 条件下,应尽可能使背吃刀量等于工件的
切削用量的确定
数控编程时,编程人员必须确定每道 工序的切削用量,并以指令的形式写入程 序中。切削用量包括主轴转速、背吃刀量 及进给速度等。对于不同的加工方法,需 要选用不同的切削用量。切削用量的选择 原则是:保证零件加工精度和表面粗糙度, 充分发挥刀具切削性能,保证合理的刀具 耐用度;并充分发挥机床的性能,最大限 度提高生产率,降低成本。
切削用量的合理选择

切削用量的合理选择切削用量不仅是在机床调整前必须确定的重要参数,而且其数值合理与否对加工质量、加工效率、生产成本等有着非常重要的影响。
在确定了刀具几何参数后,还需选定合理的切削用量参数才能进行切削加工。
所谓“合理的”切削用量是指充分利用刀具切削性能和机床动力性能(功率、转矩),在保证质量的前提下,获得高的生产率和低的加工成本的切削用量。
选择合理的切削用量时,必须考虑合理的刀具寿命。
切削用量的选择原则切削用量与刀具使用寿命有密切关系。
在制定切削用量时,应首先选择合理的刀具使用寿命,而合理的刀具使用寿命则应根据优化的目标而定。
一般分最高生产率刀具使用寿命和最低成本刀具使用寿命两种,前者根据单件工时最少的目标确定,后者根据工序成本最低的目标确定。
粗车切削用量的选择对于粗加工,在保证刀具一定使用寿命前提下,要尽可能提高在单位时间内的金属切除量。
在切削加工中,金属切除率与切削用量三要素绝保持线性关系,即其中任一参数增大一倍。
都可使生产率提高一倍。
然而由于刀具使用寿命的制约,当任一参数增大时,其他二参数必须减少。
因此,在制定切削用量时,三要素的最佳组合,此时的高生产率才是合理的。
由刀具寿命经验公式知,切削用量各因素对刀具使用寿命的影响程度不同,切削速度对使用寿命的影响最大,进给量次之,被吃刀量影响最小。
所以在选择粗加工切削用量时,当确定刀具使用寿命合理数值后,应首先考虑增大被吃刀量,其次增大进给量,然后根据使用寿命、被吃刀量和进给量的值计算出切削速度,这样既能保持刀具使用寿命,发挥刀具切削性能,又能减少切削时间,提高生产率。
被吃刀量应根据加工余量和加工系统的刚性确定。
精加工切削用量的选择选择精加工或半精加工切削用量的原则是在保证加工质量的前提下,兼顾必要的生产率。
进给量根据工件表面粗糙度的要求来确定。
精加工时的切削速度应避开积屑瘤区,一般硬质合金车刀采用高速切削。
大件精加工时,为保证至少完成一次走刀,避免在切削时中途换刀,刀具使用寿命应按零件精度和表面粗糙度来确定。
切削 用量的合理选择
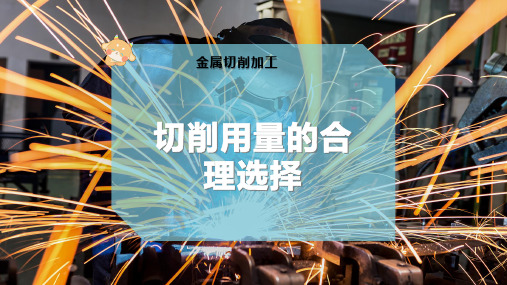
2)根据机床说明书,取机床实际进给量 =0.51mm/r。 3)检验机床进给机构允许的进给量。参考CA6140车床说 明书,查出机床进给机构允许的最大进给抗力为:FMfmax= 3528N。 计算切削时进给力为:
统、工件刚度以及精加工时表面粗糙度要求,确定进给量。
3)根据刀具寿命,确定切削速度。 4)所选定的切削用量应该是机床功率所允许的。
1.2切削用量的合理选择方法
1.背吃刀量的合理选择
背吃刀量一般是根据加工余量来确定。 粗加工(表面粗糙度Ra=50~12.5μm)时,尽可能一 次走刀即切除全部余量,在中等功率的机床上加工,取 ap=8~10mm;加工余量太大或余量不均匀、工艺系统刚性 不足或者断续切削时,可分几次走刀。 半精加工(Ra=6.3~3.2μm)时,取ap=0.5~2mm。 精加工(Ra=1.6~0.8μm)时,取ap=0.1~0.4mm。
1.5切削用量的优化概念
切削用量的优化是指在一定的预定目标及约束条件下, 选择最佳的切削用量。
在实际生产中,由于各种条件(加工零件、机床、刀 具、夹具等)都在变化,很难确定出一组最合理的切削用 量数值。
利用切削用量优化的方法,在确定加工条件下,综合 考虑各个因素,通过计算机辅助设计,能找出满足高效、 低成本、高利润和达到表面质量要求的一组最佳的切削用 量参数。实际切削用量的优化过程就是建立优化目标的数 学模型,用计算机求极值。主要目标函数有三个。
床功率是否允许。 在实际生产中,切削用量的合理选择,既可参照有关 手册的推荐数据,也可凭经验根据选择原则确定。
1.3车削用量的合理选择例题
04-1合理选择切削用量1
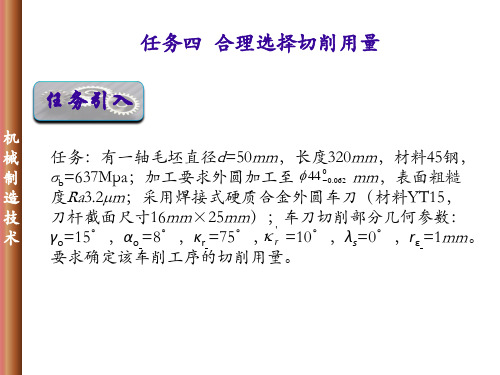
制
造
普通机床
技
术
专门化机床
专用机床
(C)按加工精度分类
普通精度机床(1)、精密机床(0.4)和高精度机床(0.25)。
(D)按自动化程度分类
手动机床、机动机床、半自动机床和自动化机床等。 机 械 制 造 技 术
5.2 机床型号的编制方法 “( )”内容可选,无
5.2.1 普通机床的型号
内容时此项不表示,有 内容则不带括号 “ ”大写汉
5.2.3 组合机床及其自动线的型号 设计单位代号—分类代号 设计顺序号(重大改进顺序号)
组合机床及其自动线的分类代号
机
分类
械 大型组合机床 制 小型组合机床 造 自动换刀数控组合机床
技
术
代号 U H K
分类 大型组合机床自动线 小型组合机床自动线
自动换刀数控组合机床自动线
代号 UX HX KX
任务六 阅读机床传动系统图
机 使执行件与运动源或使两个有关执行件保持确定运动联系的 械 一系列按一定规律排列的传动元件构成传动链。 制 造 技 术
(A) 外联系传动链
外联系传动链联系动力源和执行件之间的传动链,使执 行件得到运动,且能改变运动的速度和方向,但不要求动 力源和执行件之间有严格的传动比。
机
1
械
制
2
uv
造
3
技
4
B11
工机 工机床 床 床 床 床 机床 床
代号 C Z T M
Y
机
械 读音 车 钻 镗 磨 2磨 3磨 牙
制
造
S X B LG Q 丝 铣 刨 拉割 其
技 术
机
械
制
滚丝机
造
- 1、下载文档前请自行甄别文档内容的完整性,平台不提供额外的编辑、内容补充、找答案等附加服务。
- 2、"仅部分预览"的文档,不可在线预览部分如存在完整性等问题,可反馈申请退款(可完整预览的文档不适用该条件!)。
- 3、如文档侵犯您的权益,请联系客服反馈,我们会尽快为您处理(人工客服工作时间:9:00-18:30)。
切削条件的合理选择
一、刀具几何参数的合理选择
刀具几何参数包含四方面内容: 几何角度、刃形、刃面、刃口型式及参数
(一)前角的选择
1.前角的作用 γ
0
↑→变形程度↓→F↓ q ↓→θ ↓→T↑振动↓质量↑ 刀刃和刀头强度↓散热面积容热体积↓断屑困难 在一定的条件下,存在一个合理值
对于不同的刀具材料和工件材料,
常用T 作中间控制因素把优化指标和切削参数联系起来。
1. 最大生产率刀具使用寿命Tp
根据单件工时最短的原则确定的刀具使用寿命。 单件工时 tw= tm+tct tm/T+ta
tm为切削时间; tct为换一次刀时间;ta为辅助时间
tm=l.Δ/(n f ap)= l.Δπd/(1000v f ap)
= l.Δπd Tm/(1000C0 f ap)=K Tm
tw= K Tm+ tctK Tm-1+tot 取d tw/dT = 0 ∴ T=(1-m) tct/m=Tp vp =C0 / Tp m (2-2) 与此 相应的速度为
分析式(2-2)知:
① tct↑→ Tp↑,即换刀时间长, Tp应取大值,切削 速度应取 较小值;
② m ↑→ Tp↓,即刀材性能较好,速度变化对刀具
量ap,其次在工艺条件允许下选择较大的进给量f ,最后
根据合理的刀具使用寿命,用计算法或查表法确定切削速 度v 。这样使v、f 、ap 的乘积最大,以获得最大的生产率
精加工时则主要按表面粗糙度和加工精度要求确定切削用量。
2.切削用量制订的步骤(以车削为例) (1)背吃刀量ap的选择 粗加工时, ap由加工余量和工艺系统的刚度决定,尽可 能一次走刀切除全部加工余量。 半精加工时, ap可取0.5~2 mm。 精加工时, ap取为0.1~0.4 mm。 在加工余量过大或系统刚性不足情况下,粗加工可分几次 走刀。若分两次走刀,第一次走刀的ap取大些,可占全部 余量的2/3~3/4,而第二次走刀的ap取小些,以使精加工
小值;若刚性差(细长轴),κ r取较大值(90°); ②考虑工件形状、切屑控制、减小冲击等,车台阶轴,取 90 °;镗盲孔>90 °;κ r小切屑成长螺旋屑不易断; 较小κ r,改善刀具切入条件,不易造成刀尖冲击。
(四)副偏角的选择
副偏角的主要作用是形成已加工表面。
副偏角↓→ Ra↓刀尖强度↑散热体积↑
(二)后角的选择
1.后角的作用 α 0↑→rn↓锋利、 lα ↓摩擦F↓→ 质量↑
VB 一定,磨损体积↑→T↑但NB↑
刀头强度↓散热体积↓重磨体积↑ 在一定的条件下,存在一个合理值
2.合理后角的选择原则 ①粗加工、断续切削、工材强度硬度高, 选较小后角, 已用大负前角应↑α 0 ; ②精加工取较大后角,保证表面质量;
切削速度v可按下式计算求得 Cv
v=
T
m a xv f yv p
Kv
(3-36)
式中各系数和指数可查阅切削用量手册。
切削速度值也可查表3-8来选定。
生产中选择切削速度的一般原则是: 1)粗车时, ap和f 均较大,故选择较低的切削速度v ; 精车时, ap和f 均较小,故选择较高的切削速度v 。
2)工件材料强度、硬度高时,应选较低的切削速度v ;
3. 切削液的合理选用
(1)从加工要求考虑 粗加工,选用水溶液或低浓度乳化液;
精加工,选用极压切削油或高浓度乳化液;
(2)从刀具材料考虑 高速钢,需用切削液;Y合金等,可不用或充分连续用; (3)从工件材料考虑 钢等塑性材料,需用切削液;铸铁等脆材,可不用; 高强度钢等难加工材料,宜用极压切削油或乳化液 (4)从加工方法考虑 钻孔铰孔、攻螺纹和拉削等,宜用极压乳化液或切削油; 成形刀具齿轮刀具等用极压切削油;磨削宜用乳化液。
四、切削液的合理选用
1.切削液的分类 水溶液 水+添加剂 冷却 粗加工
乳化液
切削油
乳化油+水
矿物油+添加剂 润滑 精加工
2. 切削液的作用机理
① 冷却 ↓摩擦↓热的产生;将热量带走。本身导热系数、 比热、汽化热及流量、流速、冷却方式等。
② 润滑 切削液的渗透性、形成润滑膜能力、润滑膜强度
③ 排屑、清洗 ④ 防锈 防锈添加剂
工序具有较高的刀具寿命和加工质量。
切削有硬皮的铸、锻件或不锈钢等加工硬化严重的材料时, 应尽量使ap超过硬皮或冷硬层厚度,以避免刀尖过早磨损。
(2)进给量f 的选择
粗加工时,f 的大小主要受机床进给机构强度、刀具的强度 与刚性、工件的装夹刚度等因素的限制。 精加工时,f 的大小主要受加工精度和表面粗糙度的限制。
Tpr=(1-m)( tct+ta Ct /S)/m+ Ct K Tpr m/mS 与此 相应的速度为 vpr= C0 / Tpr m
当销售价≥生产成本时, 有如下关系: Tc ≥Tpr >Tp 通常根据优化指标来 选择刀具使用寿命: 1.产品销路不畅或产品初创阶段,宜采用经济使用寿命Tc; 2.产品销路通畅甚至供不应求情况下,宜采用最大利润率使 用寿命Tpr ; 3.产品急需的情况下(如战时或救灾),宜采用最大生产率
2.刃倾角的选择原则
①粗加工、有冲击、刀材脆、工材强度硬度高,λ s取负值;
②精加工、系统刚性差(细长轴),λ s取正值; ③微量极薄切削,取大正刃倾角。
二、刀具使用寿命的合理选择
生产目标:加工质量、加工效率、经济性 优化指标:单件生产时间、单件加工成本、利润率
切削参数:切削用量、刀具材料、几何参数、机床等
T 随γ
0
的变化趋势为驼峰形。
高速钢的合理前角比Y合金的大。 加工塑材的合理前角比脆材的大
2.合理前角的选择原则 ①粗加工、断续切削、刀材强度韧性低 工材强度硬度高,选较小的前角; ②工材塑韧性大、系统刚性差,易振动 或机床功率不足,选较大的前角; ③成形刀具、自动线刀具取小前角; ④Aγ 磨损增大前角, Aα 磨损减小前角
反之,选较高的切削速度v 。 3)刀具材料性能越好,切削速度v选得越高。
4)精加工时应尽量避免积屑瘤和鳞刺产生的区域;
5)断续切削时为减小冲击和热应力,宜适当降低v ; 6)在易发生振动的情况下, v 应避开自激振动的临界速度;
7)加工大件、细长件和薄壁件或加工带外皮的工件时,应
适当较低v 。 切削用量三要素选定之后,还应校核机床功率。
使用寿命影响小, Tp应取小值,切削速度取 较大值
2. 最低成本使用寿命Tc 根据单件成本最低的原则确定的刀具使用寿命。 单件成本 C= tmM+tct (tm/T)M+ (tm/T) Ct+totM M 为工时费用率; Ct为刀具每用一次分摊的成本,刀具总成本/刃磨次数; 将tm=K Tm代入上式, ∴ T=(1-m)( tct+ Ct /M)/m=Tc 与此 相应的速度为 分析式(2-2)知: ① tct↑→ Tc↑; ② m ↑→ Tc↓; vc= C0 / Tc m 令d C /dT = 0 得 (2-3)
三、切削用量的合理选择
1.切削用量的选择原则
粗加工时,应在保证必要的刀具使用寿命的前提下,以
尽可能提高生产率和降低成本为目的。根据刀具使用寿
命与切削用量的关系式,切削用量↑, T ↓,其中速度
v 对T 影响最大,进给量f 次之,背吃刀量ap影响最小。
粗加工中选择切削用量时,应首先选择尽可能大的背吃刀
副刃工作长度↑→ 摩擦↑Fp↑易振动→Ra↑,T↓ 在一定条件下,存在一合理值。系统刚性好,。
(五)刃倾角的选择
1.刃倾角的作用 ①影响刀刃锋利性.λ s↑→γ
0e
↑、rn ↓→ ↑锋利性
②负刃倾角→刀头强度↑散热体积↑
③负刃倾角→ Fp↑→变形↑,易振动→Ra↑ ④正λ s切屑流向待加工表面,负λ s切屑流向已加工表面 在一定条件下, 存在一合理值
③成形、复杂、尺寸刀具取小后角; ④系统刚性差,易振动,取较小后角;
⑤工材塑性大取较大后角,脆材↓α
0
(三)主偏角的选择
1.主偏角的作用 κ r↓→ac↓aw↑→单位刃长负荷↓→ T↑
刀尖强度↑散热体积↑,Ra↓
Fp↑→变形↑加工精度↓,易振动→Ra↑,T↓
在一定的条件下,存在一个合理值 2.合理主偏角的选择原则 ①主要看系统刚性。若刚性好,不易变形和振动,κ r取较
③M ↑→ Tc↓;即Tc应取小值,vc取大值以降低成本;
④ Ct↑→ Tc↑;即刀具成本高,Tc应取大值, vc取小值
3. 最大利润使用寿命Tpr 根据单件利润最高的原则确定的刀具使用寿命。
单件利润率
pr= (S – C) / tw
S 为单件创造的产值 将C 、tw代入上式, 令d pr /dT = 0 得 (2-4)
刀具使用寿命 T
使用寿命Tp 。
选择刀具使用寿命应从以下几方面考虑:
1. 制造和刃磨较简单、成本不高的刀具,使用寿命选得低
些,反之高些。
硬合金车刀T为60~90min,钻头T为80~120min,硬质 合金端铣刀T为90~180min,齿轮刀具为200~300min。 2. 装卡调整复杂的刀具,使用寿命选得高些,仿形车床、组 合钻床上刀具为通用机床上的200~400%。 3. 切削大型工件为避免中途换刀,使用寿命选得高些,一般 为中小件加工时的200~300%。
生产实际中常根据经验或查表法确定f 。
粗加工时根据工件材料、车刀刀杆尺寸、工件直径及以确定 的背吃刀量按表3-6来选择f 。 在半精加工和精加工时,则按加工表面粗糙度要求,根据工 件材料、刀尖圆弧半径、切削速度按表3-7来选择f 。
(3)切削速度的确定
根据已经选定的背吃刀量ap 、进给量f及刀具使用寿命T,