连铸过程(全)
连铸操作工操作规程(3篇)
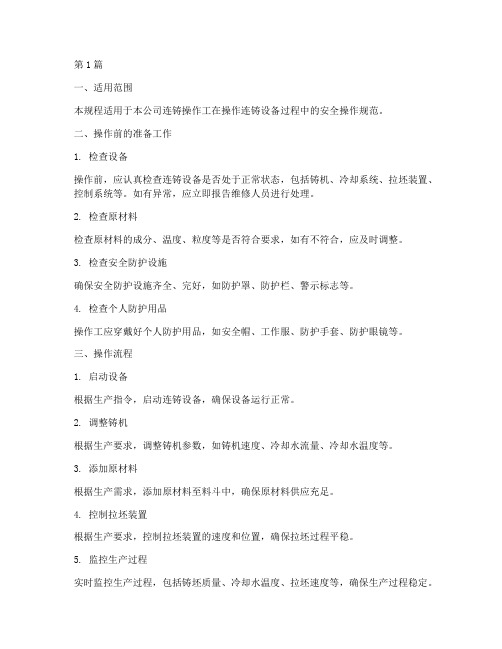
第1篇一、适用范围本规程适用于本公司连铸操作工在操作连铸设备过程中的安全操作规范。
二、操作前的准备工作1. 检查设备操作前,应认真检查连铸设备是否处于正常状态,包括铸机、冷却系统、拉坯装置、控制系统等。
如有异常,应立即报告维修人员进行处理。
2. 检查原材料检查原材料的成分、温度、粒度等是否符合要求,如有不符合,应及时调整。
3. 检查安全防护设施确保安全防护设施齐全、完好,如防护罩、防护栏、警示标志等。
4. 检查个人防护用品操作工应穿戴好个人防护用品,如安全帽、工作服、防护手套、防护眼镜等。
三、操作流程1. 启动设备根据生产指令,启动连铸设备,确保设备运行正常。
2. 调整铸机根据生产要求,调整铸机参数,如铸机速度、冷却水流量、冷却水温度等。
3. 添加原材料根据生产需求,添加原材料至料斗中,确保原材料供应充足。
4. 控制拉坯装置根据生产要求,控制拉坯装置的速度和位置,确保拉坯过程平稳。
5. 监控生产过程实时监控生产过程,包括铸坯质量、冷却水温度、拉坯速度等,确保生产过程稳定。
6. 调整参数根据生产情况,及时调整铸机参数,确保铸坯质量。
7. 停止设备根据生产指令,停止连铸设备,确保设备处于安全状态。
四、安全操作注意事项1. 操作过程中,严禁触摸高温设备、冷却水、铸坯等,防止烫伤、冻伤等事故发生。
2. 严禁在设备运行过程中进行检修、清洁等工作,以免发生安全事故。
3. 严禁在设备附近堆放杂物,确保操作区域安全。
4. 操作过程中,注意观察设备运行状态,发现问题及时处理。
5. 操作过程中,严禁酒后作业,确保操作安全。
6. 严禁在设备附近吸烟、使用明火等,防止火灾事故发生。
五、应急处理1. 发生火灾时,立即切断电源,使用灭火器进行灭火,并迅速撤离现场。
2. 发生设备故障时,立即停止设备运行,报告维修人员进行处理。
3. 发生人身伤害事故时,立即采取急救措施,并报告上级领导。
六、培训与考核1. 新员工在上岗前,必须接受连铸操作规程的培训,考核合格后方可上岗。
连铸工程及监理要点新
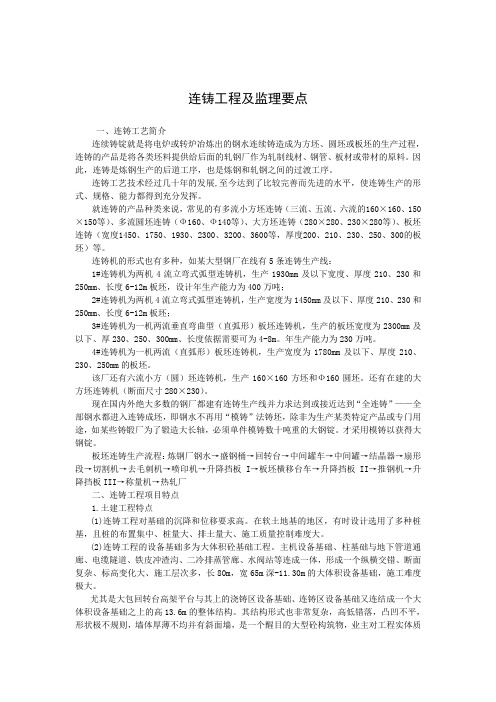
连铸工程及监理要点一、连铸工艺简介连续铸锭就是将电炉或转炉冶炼出的钢水连续铸造成为方坯、圆坯或板坯的生产过程,连铸的产品是将各类坯料提供给后面的轧钢厂作为轧制线材、钢管、板材或带材的原料。
因此,连铸是炼钢生产的后道工序,也是炼钢和轧钢之间的过渡工序。
连铸工艺技术经过几十年的发展,至今达到了比较完善而先进的水平,使连铸生产的形式、规格、能力都得到充分发挥。
就连铸的产品种类来说,常见的有多流小方坯连铸(三流、五流、六流的160×160、150×150等)、多流圆坯连铸(Ф160、Ф140等)、大方坯连铸(280×280、230×280等)、板坯连铸(宽度1450、1750、1930、2300、3200、3600等,厚度200、210、230、250、300的板坯)等。
连铸机的形式也有多种,如某大型钢厂在线有5条连铸生产线:1#连铸机为两机4流立弯式弧型连铸机,生产1930mm及以下宽度、厚度210、230和250mm、长度6-12m板坯,设计年生产能力为400万吨;2#连铸机为两机4流立弯式弧型连铸机,生产宽度为1450mm及以下、厚度210、230和250mm、长度6-12m板坯;3#连铸机为一机两流垂直弯曲型(直弧形)板坯连铸机,生产的板坯宽度为2300mm及以下、厚230、250、300mm、长度依据需要可为4-8m。
年生产能力为230万吨。
4#连铸机为一机两流(直弧形)板坯连铸机,生产宽度为1780mm及以下、厚度210、230、250mm的板坯。
该厂还有六流小方(圆)坯连铸机,生产160×160方坯和Ф160圆坯。
还有在建的大方坯连铸机(断面尺寸280×230)。
现在国内外绝大多数的钢厂都建有连铸生产线并力求达到或接近达到“全连铸”——全部钢水都进入连铸成坯,即钢水不再用“模铸”法铸坯,除非为生产某类特定产品或专门用途,如某些铸锻厂为了锻造大长轴,必须单件模铸数十吨重的大钢锭。
简述连铸生产工艺流程及主要设备
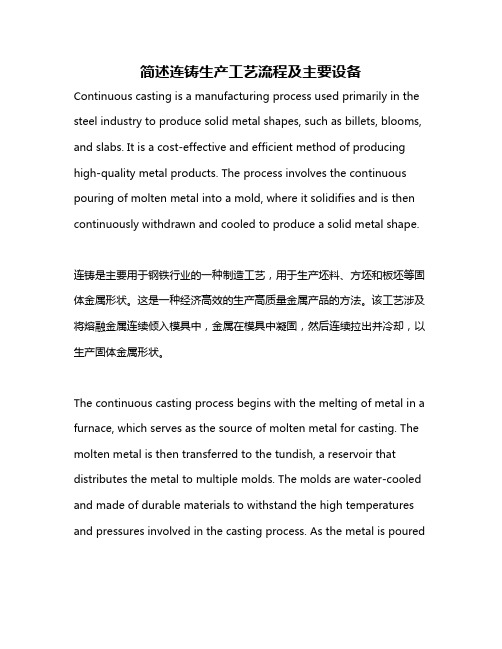
简述连铸生产工艺流程及主要设备Continuous casting is a manufacturing process used primarily in the steel industry to produce solid metal shapes, such as billets, blooms, and slabs. It is a cost-effective and efficient method of producing high-quality metal products. The process involves the continuous pouring of molten metal into a mold, where it solidifies and is then continuously withdrawn and cooled to produce a solid metal shape.连铸是主要用于钢铁行业的一种制造工艺,用于生产坯料、方坯和板坯等固体金属形状。
这是一种经济高效的生产高质量金属产品的方法。
该工艺涉及将熔融金属连续倾入模具中,金属在模具中凝固,然后连续拉出并冷却,以生产固体金属形状。
The continuous casting process begins with the melting of metal in a furnace, which serves as the source of molten metal for casting. The molten metal is then transferred to the tundish, a reservoir that distributes the metal to multiple molds. The molds are water-cooled and made of durable materials to withstand the high temperatures and pressures involved in the casting process. As the metal is pouredinto the molds, it solidifies and forms a shell that is continuously withdrawn to produce the desired metal shape.连铸过程始于熔炉中金属的熔化,熔炉是铸造熔融金属的来源。
连铸过程原理及数值模拟

连铸过程原理及数值模拟连铸是一种重要的金属成形工艺,广泛应用于钢铁、铝合金等金属材料的生产和加工中。
连铸过程原理及数值模拟是研究连铸工艺的关键内容,通过对连铸过程的原理分析和数值模拟,可以优化连铸工艺参数,提高产品质量和生产效率。
连铸过程是将熔融金属直接注入到连续运动的铸坯中,通过冷却和凝固过程,将熔融金属转化为固态铸坯。
连铸的基本原理是利用连续运动的铸坯带走热量,使熔融金属迅速凝固,形成连续的固态铸坯。
在连铸过程中,主要包括液相区、液固两相区和固相区三个区域。
在液相区,熔融金属通过连续浇注,填充到铸坯的空腔中。
熔融金属的温度高于固相线,处于液态状态。
随着熔融金属的注入,液相区的长度逐渐增加。
在液固两相区,熔融金属和正在凝固的铸坯同时存在。
由于熔融金属的温度高于固相线,所以熔融金属仍然保持液态。
而铸坯由于受到液相的热量传递,开始逐渐凝固。
在这个区域中,液相区的长度逐渐减小,凝固铸坯的长度逐渐增加。
在固相区,整个铸坯都已经完全凝固。
熔融金属已经完全转化为固态,形成连续的固态铸坯。
在这个区域中,液相区的长度为零,凝固铸坯的长度为整个连铸过程的长度。
为了研究连铸过程的细节和优化连铸工艺参数,数值模拟成为一种重要的方法。
数值模拟是通过数学模型和计算机仿真技术,对连铸过程进行模拟和分析。
数值模拟可以准确地计算连铸过程中的温度场、流场和凝固结构等关键参数,为工艺优化提供科学依据。
在连铸过程的数值模拟中,需要考虑多个物理过程的相互作用。
首先是流体力学过程,包括熔融金属的流动和铸坯带走热量的过程。
其次是热传导过程,包括熔融金属的冷却和凝固过程。
最后是凝固结构演化过程,包括铸坯的晶粒生长和偏析等现象。
为了建立连铸过程的数值模型,需要考虑材料的物理性质、流体力学和热传导方程等方面的参数。
同时,还需要考虑边界条件和初始条件等参数。
通过数值模拟,可以预测连铸过程中的温度分布、流速分布和凝固结构等重要参数,为工艺优化提供指导。
炼钢生产过程及流程图详解(全)

钢铁生产工艺主要包括:炼铁、炼钢、轧钢等流程。
(1)炼铁:就是把烧结矿和块矿中的铁还原出来的过程。
焦炭、烧结矿、块矿连同少量的石灰石、一起送入高炉中冶炼成液态生铁(铁水),然后送往炼钢厂作为炼钢的原料。
炼铁是还原反应。
先是利用氧把矿石中铁及其他物质氧化为三氧化二铁、硫、磷的氧化物等。
硫的氧化物经过处理后排放,磷的氧化物还要加入石灰后转化为矿渣后排出。
主要反应为利用 C 把铁的氧化物还原 2 Fe2O3+ 3 C=4 Fe+ 3 CO2.(2)炼钢:是把原料(铁水和废钢等)里过多的碳及硫、磷等杂质去掉并加入适量的合金成分。
炼钢是氧化反应,是炼铁后的进一步加工。
主要是除去Fe中多余的 C ,因为 C 的含量太高影响钢的韧性。
反应式为: C+O2 = CO2 。
(3)连铸:将钢水经中间罐连续注入用水冷却的结晶器里,凝成坯壳后,从结晶器以稳定的速度拉出,再经喷水冷却,待全部凝固后,切成指定长度的连铸坯。
(4)轧钢:连铸出来的钢锭和连铸坯以热轧方式在不同的轧钢机轧制成各类 钢材,形成产品。
炼钢工艺总流程图炼焦生产流程:炼焦作业是将焦煤经混合,破碎后加入炼焦炉内经干馏后产生热焦碳及粗焦炉气之制程。
烧结生产流程:烧结作业系将粉铁矿,各类助熔剂及细焦炭经由混拌、造粒后,经由布料系统加入烧结机,由点火炉点燃细焦炭,经由抽气风车抽风完成烧结反应,高热之烧结矿经破碎冷却、筛选后,送往高炉作为冶炼铁水之主要原料。
还原气体,还原铁矿石,产生熔融铁水与熔渣之炼铁制程。
转炉生产流程:炼钢厂先将熔铣送前处理站作脱硫脱磷处理,经转炉吹炼后,再依订单钢种特性及品质需求,送二次精炼处理站(RH真空脱气处理站、Ladle Injection盛桶吹射处理站、VOD真空吹氧脱碳处理站、STN搅拌站等)进行各种处理,调整钢液成份,最后送大钢胚及扁钢胚连续铸造机,浇铸成红热钢胚半成品,经检验、研磨或烧除表面缺陷,或直接送下游轧制成条钢、线材、钢板、钢卷及钢片等成品。
连铸工艺知识点总结

连铸工艺知识点总结一、概述连铸是指在一台设备上同时进行浇铸和凝固过程的一种工艺。
它可以大幅度提高生产效率,减少材料浪费,提高产品质量。
在现代工业中,连铸工艺已经被广泛应用于钢铁、铝、铜等金属的生产中,成为了重要的生产工艺之一。
二、连铸的原理连铸的基本原理是利用连铸机,在一个连续的过程中,将金属液直接浇注至坯料模具中,然后通过顺序凝固、切割、堆垛等工序,最终产生坯料产品。
整个连铸过程中,金属液会先经过结晶器的处理,实现坯料的凝固,在这个过程中,还会进行一系列的拉伸、抽拉和冷却等操作,使得坯料的形状和尺寸得以控制和稳定。
三、连铸的优势1. 提高生产效率:相对于传统浇铸工艺,连铸可以大幅度提高生产效率。
因为它可以在同一个设备上连续进行浇铸和凝固过程,减少了生产过程中的空闲时间,从而实现了生产效率的提升。
2. 减少材料浪费:连铸工艺可以减少金属的二次加工过程,大大减少了金属的浪费,减少了材料的消耗,同时也减少了对环境的污染。
3. 提高产品质量:由于连铸工艺可以控制金属的凝固过程,使得坯料的材料结构更加均匀,从而提高了产品的质量。
4. 节省能源:相对于传统的浇铸工艺,连铸工艺可以在生产过程中更好地利用能源,降低能源的消耗。
四、连铸的工艺流程1. 铸坯模具的准备:连铸的第一步是准备好适用于连铸工艺的铸坯模具,通常采用的是一种特殊的铸坯模具,可以确保坯料的形状和尺寸的准确度。
2. 结晶器处理:在连铸的过程中,金属液会通过结晶器进行处理,实现坯料的凝固。
3. 拉伸、抽拉和冷却:在结晶器处理完后,金属液会经过一系列的拉伸、抽拉和冷却等操作,以控制坯料的形状和尺寸。
4. 切割和堆垛:最后,坯料会被切割为所需的尺寸,然后进行堆垛,完成整个连铸工艺的过程。
五、连铸的应用领域1. 钢铁生产:连铸工艺在钢铁生产中得到了广泛的应用,可以高效地生产出各种规格的钢铁坯料。
2. 铝合金生产:在铝合金生产中,连铸工艺可以提高产品质量,降低生产成本。
3连铸坯的凝固
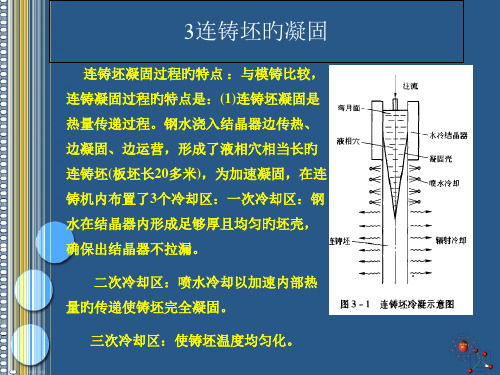
结晶器设计参数对传热旳影响
• A 结晶器锥度旳影响 • 为了使坯壳与结晶器铜壁保持良好旳接触,以减小
保护渣在结晶器内预防钢液二次氧化旳作用,主要靠保护渣液渣层来 实现。一般结晶器内液渣层厚度在8~15mm范围内,在液面稳定,水 口插入深度合理旳情况下,均能起到很好隔绝空气旳作用。
3、吸收溶解从钢水中上浮到钢渣界面旳夹杂物,净化钢液
要求保护渣具有良好旳吸收熔解夹杂物旳能力。经过以为,粘度低 夹杂物熔解速度增长,液渣旳高碱度、低SiO2、Al2O3、高Na2O、 CaF2有利于提升夹杂物旳熔解度。
3连铸坯旳凝固
连铸坯凝固过程旳特点 :与模铸比较, 连铸凝固过程旳特点是:(1)连铸坯凝固是 热量传递过程。钢水浇入结晶器边传热、 边凝固、边运营,形成了液相穴相当长旳 连铸坯(板坯长20多米),为加速凝固,在连 铸机内布置了3个冷却区:一次冷却区:钢 水在结晶器内形成足够厚且均匀旳坯壳, 确保出结晶器不拉漏。
• 在结晶器旳角部 旳传热为二维, 开始凝固最快, 最早收缩,最早 形成气隙。角部 区域坯壳最薄, 这也是产生角部 裂纹和发生漏钢 旳单薄环节。
5
4
3
2
1
结晶器旳散热
主冷却水
背板
1500
1000 °C
500 200
0铸坯壳铜板Fra bibliotek缝隙钢液
25
50
mm
结晶器壁温度分布
坯壳旳生长规律
• 被拉出结晶器旳铸坯其坯壳必须有足够 旳厚度,以防在失去铜壁支撑后变形或 漏钢。一般而言,小方坯要求出结晶器 下口处坯壳厚度应不小于8-15mm,板 坯要求厚度应为15-20mm。坯壳厚度旳 生长规律服从凝固平方根定律:
炼钢精炼连铸过程钢水演示文稿
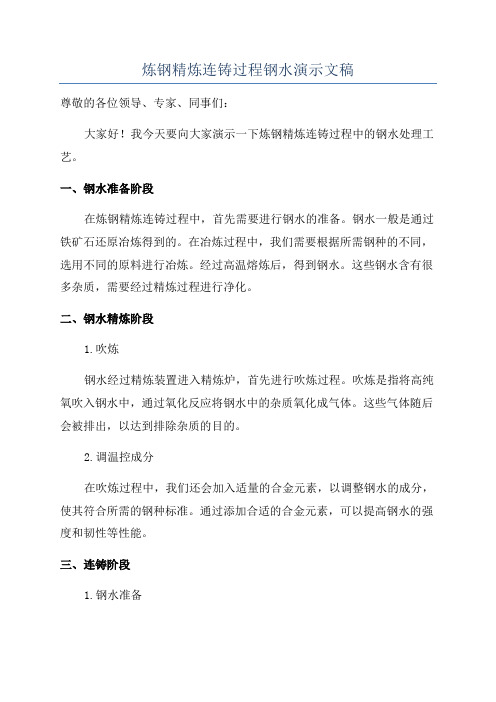
炼钢精炼连铸过程钢水演示文稿尊敬的各位领导、专家、同事们:大家好!我今天要向大家演示一下炼钢精炼连铸过程中的钢水处理工艺。
一、钢水准备阶段在炼钢精炼连铸过程中,首先需要进行钢水的准备。
钢水一般是通过铁矿石还原冶炼得到的。
在冶炼过程中,我们需要根据所需钢种的不同,选用不同的原料进行冶炼。
经过高温熔炼后,得到钢水。
这些钢水含有很多杂质,需要经过精炼过程进行净化。
二、钢水精炼阶段1.吹炼钢水经过精炼装置进入精炼炉,首先进行吹炼过程。
吹炼是指将高纯氧吹入钢水中,通过氧化反应将钢水中的杂质氧化成气体。
这些气体随后会被排出,以达到排除杂质的目的。
2.调温控成分在吹炼过程中,我们还会加入适量的合金元素,以调整钢水的成分,使其符合所需的钢种标准。
通过添加合适的合金元素,可以提高钢水的强度和韧性等性能。
三、连铸阶段1.钢水准备在精炼完成后,钢水会被送至连铸机的铸包中,待进入连铸机进行连铸。
2.结晶器冷却在连铸过程中,我们会通过结晶器对钢水进行冷却。
结晶器是由一系列水冷铜管组成的,通过水的循环,将钢水的温度降低,从而使其逐渐凝固。
结晶器的冷却速度和冷却方式可以根据钢水的要求进行调整。
3.拉速控制在连铸过程中,我们还需要通过控制拉速来控制钢坯的形态和质量。
拉速过快会导致钢水的不均匀凝固,从而产生缺陷。
而拉速过慢则会使连铸生产效率降低。
4.喷流冷却在连铸过程中,我们还会通过喷流冷却来进一步降低钢水的温度,以促进钢水的凝固。
喷流冷却可以减少钢水的表面温度,提高钢坯的质量。
四、总结通过以上的介绍,我们可以看到,在炼钢精炼连铸过程中,钢水的质量得到了极大的提高。
通过吹炼和精炼过程,钢水中的杂质被有效去除,同时钢水的成分也得到了调整。
在连铸过程中,钢水经过结晶器的冷却和拉速的控制,得到了均匀凝固和理想的形态。
喷流冷却进一步降低了钢水的温度,确保钢坯的质量。
这就是炼钢精炼连铸过程中钢水的处理工艺,通过这样的工艺流程,我们可以生产出质量优良的钢材。
- 1、下载文档前请自行甄别文档内容的完整性,平台不提供额外的编辑、内容补充、找答案等附加服务。
- 2、"仅部分预览"的文档,不可在线预览部分如存在完整性等问题,可反馈申请退款(可完整预览的文档不适用该条件!)。
- 3、如文档侵犯您的权益,请联系客服反馈,我们会尽快为您处理(人工客服工作时间:9:00-18:30)。
1 (2 3 cos cos 3 ) 。由(4-10)式可知 4
—
0 , cos0 1 液体中质点已是一个晶核,不需任何过冷度就可形核;
,依附于外来质点形成晶核。
— 0 180
结论是非均质形核有效性决定于润湿角 。越小 ,形核功就越小,就易形核 ,形核速率比较如图4-4。非均质形核的过冷度比均质形核大为减少。在实际生 产中主要是非均质形核,除模壁表面作为“依托”形成晶核外,液体金属中需含 有两类小质点:一类叫活性质点,如金属氧化物(Al2O3),其晶体结构与金属 晶体结构相似,它们之间界面张力小,可作为“依托”而形成核心。另一类是难 熔物质的质点,它们的结构虽然与金属晶体结构相差较远,但这些难熔质点表面 往往存在细微凹坑和裂纹,其中尚未熔化的金属,可作为“依托”而形成晶体核 心。因此,可以在钢液中加入形核剂以细化晶粒。
前言
1
凝固理论
·钢液的结晶
·晶体的长大 ·凝固结构
1.1 钢液结晶与凝固结构
·凝固结构控制
1.2 凝固偏析 ·凝固显微偏析
·凝固宏观偏析
1.3 凝固收缩 1.4 钢的高温力学性能 1.5 凝固过程中气体和非金属夹杂物
2
连铸工艺与设备
2.1 连铸机机型及特点 2.2 连铸工艺与设备
-钢包
-中间包 -结晶器 -二次冷却区 -拉坯矫直机 -切割机 2.3 连铸新技术
( 2)
1974年-1989年:
技术特点:全连铸工艺,以连铸机为核心。
( 3)
1989年-现在:
连轧为代表,钢厂向紧凑化发展。
技术特点:连铸-连轧工艺,以薄板坯,连铸-
2. 21世纪钢铁工业发展趋势
(1) 产品更加纯洁化
(2) 生产工艺更加高效低耗
(3) 生产过程对环境更加友好
3 连续铸钢的特点
O O
O O
O O
钢 坯 清 理 O
加 热
轧 制
轧 钢 燃 料 消 耗 ×109J/t
2.01 0.92
O
O O
3 4 5
O O O
O O O
O
O O O
O O O
1.34 0.878 0.334
6
连铸坯直接轧 制CC-DR
O
O
角 部 补 热
O
4 连铸技术的发展历史
(1)19世纪中叶H.Bessemer提出了连续浇注金属的构想; (2)1933年,现代连铸的奠基人S.Junghans提出并发展 了结晶器振动装置,奠定了连铸的工业应用的基础; (3)本世纪30年代,连铸成功应用于有色金属; (4)1950年, S.Junghans和Mannesmann公司合作,建成 世界上第一台工业连铸机; (5)50年代,工业应用时期; 到50年代末,有连铸机30台,产量110t,连铸比0.34%. (6)60年代,稳步发展时期; 到60年代末,有连铸机200余台,产量4000万t. (7)70年代,迅猛发展时期; 1981年连铸比33.8%. (8)80年代,完全成熟时期; 1990年连铸比64.1%; (9)90年代,近终型连铸技术时代
小于临界半径晶核趋向消失。
表4-1纯液体金属结晶过冷度
金属
Sn Pb Al Cu Mn Fe Ni Co
熔点
f ( K )
过冷度
ΔT(k)
103 80 130 130 308 295 319 330
T T f
0.208 0.133 0.110 0.174 0.206 0.161 0.186 0.181
由图4-1可知,当ΔGΣ达到最大值时的晶核大小叫临界半径,在 r r 时,求:
由(4-4)式可知,临界晶核半径是与过冷度成反比。由图(4-1)可知: — 晶核长大导致系统自由能增加,新相不稳定; — 晶核长大导致系统自由能减少,新相能稳定生长; — 形核和晶核溶解处于平衡。 结论是:在一定温度下,任何大于临界半径的晶核趋向于长大,
实验测定:
实验研究指出,树枝晶间距 l 与凝固速度 R 和温度梯度有关。
l CR m G n
雅可比试验不同温度梯度和凝固速度对树枝形态的影响,并测定 了 l 和 l 与 R 和 G 关系,如图4-13所示。由图可得出: 上述两经验式中,对一次晶间距,指数m、n值相差较大;对二次 晶间距,m、n值近似相等。不同作者得到的m、n值相差较大。 试验指出,二次枝晶间距与区域凝固时间 们的经验关系式:
参考书目
(1) 炼钢学原理 冶金工业出版社,曲英主编。 (2) 浇注与凝固 冶金工业出版社,蔡开科主编。 (3) 连续铸钢 科学出版社,蔡开科主编。
(4) 钢铁冶金学(炼钢部分)
冶金工业出版社, 陈家祥主编。
前 言
1 现代炼钢技术的发展(连铸技术的作用)
( 1)
1947年-1974年:
技术特点:转炉、高炉的大型化;以模铸-初轧 为核心,生产外延扩大。
(3)成分过冷与结构
·当固液交界面前沿出现成分过冷时, 交界面就不
稳定了,不再保持平面结构。 ·按过冷度的大小,开始形成晶胞、晶胞树枝晶、树 枝晶结构。 ·随成分过冷度的增加,结构形貌由晶胞发展为树枝
晶。
1.1.3.3 树枝晶凝固
图4-8为晶体长大成树枝晶示意图。铁为立方晶格,成 正六面体结晶,由于结晶总是在结晶面溶质偏析小的地 方和结晶潜热散出最快的地方优先生长,在晶核长大过 程中,棱角比其他方向导热性好,而且棱角离未被溶质 富集的液体最近。因此棱角方向长大速度比其他方向要 快,从八个角成长为菱锥体的尖端,其生长方向几乎平 行于热流,构成树枝晶主轴,称之为一次树枝臂。垂直 于一次枝晶臂而长出分叉的枝晶叫二次枝晶臂。冷却速 度继续增加时,在二次枝晶臂上垂直长出三次枝晶臂, 这些枝晶彼此交错在一起宛如茂密的树枝。从而使结晶 潜热从液体中可以很容易的通过彼此连接的枝晶而传导 出来,直到完全凝固为止
(2)产生新相界表面自由能
GF lc 2r 2 (1 cos ) ( cs ls )r 2 (1 cos2 ) r 2 lc (2 3 cos cos3 )
(3)总自由能变化 G :
Gr
:
1 G r 3 (2 3 cos cos 2 )G r 2 lc (2 3 cos cos 3 ) 3
1 凝固理论
1 凝固理论
1.1 钢液结晶与凝固结构
1.1.1 均质形核
(1)新核的形成引起系统的自由能的变化: · 体积自由能的下降: ΔGv=-(4/3)(πγ3 (GA-GB)) 式中:γ:球形晶核的半径;GA:A相体积自由能; GB:A相体积自由能 · 表面自由能的增加: ΔGF=4πγ2σ 式中:σ:A、B两相界面自由能 (2) 均质形核的条件: ΔGΣ=ΔGv+ΔGF=-(4/3)(πγ3 (GA-GB))+4πγ2σ
1.1.4.2 凝固时晶体长大方式
(1)定向生长
(2) 等轴晶长大 · 爆发形核理论 ·固体质点理论 ·成分过冷理论 ·树枝晶熔断理论
·结晶雨理论
·晶体游离理论
1.1.4.3 连铸坯凝固结构
(1)表皮细小等轴晶 · 厚度一般2~5mm (2)柱状晶区 · 穿晶结构 · 上倾一定角度: 例如10度 (3)中心等轴晶 · 伴随疏松、缩孔和 偏析
1.1.4.4 凝固结构对产品性能的影响
(1)柱状晶的枝干较纯,而枝晶间偏析
(3)连铸产品的均一性好,质量好;
(4)易于实现机械化和自动化。
表:炼钢-轧钢不同生产流程的轧钢能耗比较
工艺过程 炼 钢 铸 锭 均 热 初 轧 开 坯 O
O
连 铸
1 2
模铸钢锭冷装 轧制IC-CCR 模铸钢锭开坯 后 直 接 轧 制 IC -DR 连铸坯冷装炉 轧制CC-CCR 连铸坯热送轧 制CC-HCR 连铸坯直接热 装炉轧制 CC - DHCR
1.1.3 晶体的长大
1.1.3.1 晶体的长大的能量消耗
- 原子的扩散
- 晶体的缺陷
- 原子的粘附
- 结晶潜热的导出
1.1.3.2 晶核长大的驱动力-成分过冷理论
(1)成分过冷的产生 ·纯金属凝固:过冷是靠模壁向外传热控制 ·合金凝固:
选分结晶
溶质元素在固相和液相的再分配 溶质浓度的不同使液相线温度不同
0.5
t c 关系如图4-14。它
l 0.00716 tc (1.5%C,1.1%Mn)
l 0.0518 tc
0.44
(0.6%C,1.1%Mn)
树枝晶间距对钢锭结构、显微偏析有重要影响。实际钢锭凝固时 凝固速度与温度梯度不可能彼此独立变化,而通过凝固时放出热 量来影响整个凝固过程。这样就可用冷却速度来控制树枝晶间距 ,以得到细的树枝结构。而影响冷却速度最重要的因素是凝固方 法。图
4-15表示了不同凝固方法的冷却速度与树枝晶间距关系。由 于冷却速度的差异,故连铸坯的树枝晶结构比钢锭的要细。加 大冷却速度,可以得到较细的树枝晶结构。 文献中对二次枝晶间距与冷却速度还有不同的经验式。铃木等 人提出 C 0.88% 的炭钢中:
l 709 0.395 ( : C 分,l : )
钢的凝固与连续铸造
•教学目的:
本部分课程从钢的凝固原理出发, 结 合钢的连铸工艺,使学生从理论上和实践上 掌握浇注和凝固过程中发生的主要的物理化 学现象,初步掌握连铸工艺与设备及其最新 发展,为将来从事冶金工程领域的工作,为 生产高质量的连铸坯,以及解决连铸生产中 的实际问题奠定理论基础。
课程大纲
1.1.4 凝固结构
1.1.4.1 钢水凝固过程的冶金特点
(1)δ -γ相的转变 · 稳定的δ相(或γ相)凝固 例如: 铁素体的Cr钢 · δ相凝固后转变为奥氏体 例如:Ni-Cr奥氏体不锈钢 · δ相凝固后转变为γ,再转变为α相 例如:低碳钢