铸造铝合金熔炼工艺
6082铝合金生产工艺

6082铝合金生产工艺
6082铝合金是一种广泛应用于航空、航天、交通运输、电子
电器、机械制造、建筑等领域的高强度铝合金。
其生产工艺主要包括原料选择、熔炼、铸造、热处理和加工等步骤。
1. 原料选择:6082铝合金的主要原料是铝、铜、镁、锡等。
这些原料需要经过精确的配比和筛选,以确保最终合金的成分满足相应的要求。
2. 熔炼:原料经过称量后,放入高炉或电炉中进行熔炼。
熔炼过程中需要控制温度和保持适当的通气条件,以确保原料能充分熔化并实现混合。
3. 铸造:熔融的6082铝合金通过喷射铸造、压铸、重力铸造
等方法进行铸造成型。
铸造过程中需要注意保持铸造温度的稳定和操作的准确性,以确保铸件的质量和成型效果。
4. 热处理:铸造完成后,铝合金需要进行热处理,以提高其强度和硬度。
常用的热处理方法包括固溶处理和时效处理。
固溶处理是将铸件加热至高温,使合金中的固溶体完全溶解;时效处理是在固溶处理后,将铸件冷却至室温并保持一定时间,使固溶体重新析出,形成所需的强化相。
5. 加工:经过热处理后的6082铝合金可以进行各种加工操作,如锻造、轧制、挤压、切削等。
这些加工操作可以根据产品的需求,进行不同的形状和尺寸加工,以满足用户的要求。
总结:6082铝合金的生产工艺包括原料选择、熔炼、铸造、热处理和加工等步骤。
这些步骤需要控制好温度、时间、压力等参数,以确保合金的成分和性能达到设计要求。
6082铝合金具有良好的力学性能和耐腐蚀性能,广泛应用于各个领域。
铝合金深井铸造工艺流程
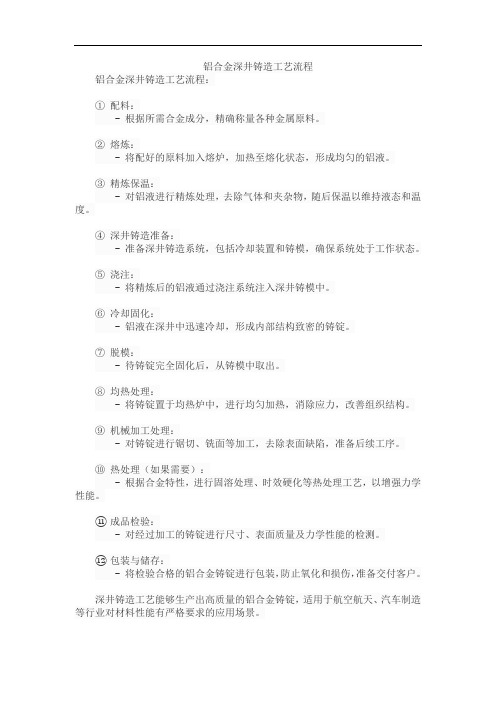
铝合金深井铸造工艺流程
铝合金深井铸造工艺流程:
①配料:
- 根据所需合金成分,精确称量各种金属原料。
②熔炼:
- 将配好的原料加入熔炉,加热至熔化状态,形成均匀的铝液。
③精炼保温:
- 对铝液进行精炼处理,去除气体和夹杂物,随后保温以维持液态和温度。
④深井铸造准备:
- 准备深井铸造系统,包括冷却装置和铸模,确保系统处于工作状态。
⑤浇注:
- 将精炼后的铝液通过浇注系统注入深井铸模中。
⑥冷却固化:
- 铝液在深井中迅速冷却,形成内部结构致密的铸锭。
⑦脱模:
- 待铸锭完全固化后,从铸模中取出。
⑧均热处理:
- 将铸锭置于均热炉中,进行均匀加热,消除应力,改善组织结构。
⑨机械加工处理:
- 对铸锭进行锯切、铣面等加工,去除表面缺陷,准备后续工序。
⑩热处理(如果需要):
- 根据合金特性,进行固溶处理、时效硬化等热处理工艺,以增强力学性能。
⑪成品检验:
- 对经过加工的铸锭进行尺寸、表面质量及力学性能的检测。
⑫包装与储存:
- 将检验合格的铝合金铸锭进行包装,防止氧化和损伤,准备交付客户。
深井铸造工艺能够生产出高质量的铝合金铸锭,适用于航空航天、汽车制造等行业对材料性能有严格要求的应用场景。
铝合金圆铸锭熔铸工艺操作规程

铝合金圆铸锭熔铸工艺操作规程
一、工艺准备
1. 铝合金圆铸锭的熔铸工艺操作规程首先需要准备所需材料,包括铝合金原料和熔炉保温材料。
2. 检查熔炉和相关设备的安全和正常工作状态,确保所有设备都处于良好的工作状态。
3. 确保操作人员具备相关技能和经验,并穿着适当的劳动保护用品。
二、炉前准备
1. 清理熔炉内部的残余物质,确保熔炉干净。
2. 检查炉体和炉底的温度计和热电偶的准确性,并进行必要的校准。
3. 加入足够的熔炉保温材料,确保熔炉保持在适宜的温度范围内。
三、熔铸操作
1. 将铝合金原料切割成合适的尺寸,并清理表面的杂质和氧化物。
2. 将切割好的铝合金原料放入熔炉中,根据需要加入合适的熔剂和合金元素。
3. 打开燃烧器,调整火焰大小和位置,使炉内的温度逐渐升高。
4. 根据工艺要求,控制熔炉的温度和时间,确保铝合金原料充分熔化。
5. 检查炉内的熔体温度和化学成分,确保满足产品质量要求。
6. 打开炉底的出铅口,将熔化好的铝合金熔体倒入铸造模具中。
7. 等待熔体冷却凝固,取出铝合金圆铸锭,并进行必要的检验和质量控制。
四、清理和维护
1. 关闭燃烧器和熔炉的出气口,待炉温降至安全温度后进行清理。
2. 清理熔炉内的残余物质和灰尘,保持熔炉的清洁。
3. 定期维护和检修熔炉和相关设备,确保其正常工作和安全性。
以上就是铝合金圆铸锭熔铸工艺操作规程的基本内容,具体操作时要根据实际情况进行调整,并遵守相关的安全操作规定。
铝合金熔炼工艺

铝合金熔炼工艺(总18页)--本页仅作为文档封面,使用时请直接删除即可----内页可以根据需求调整合适字体及大小--铝合金熔炼工艺1、性能特征目前压铸件数量最多的就是铝合金,它具有重量轻、比强度高,有较高的力学性能和耐腐蚀性能等。
但与锌合金相比,它的铸造性能相对要差,有粘模倾向,在熔炼中更易产生氧化、吸气、偏析、夹渣、结晶粒大等缺陷,铁是铝合金中的有害元素,但铝合金中的含铁量低于%时,在生产过程中容易产生粘模,高于1%时,会使合金中力学性能降低。
铝合金"增铁"的原因主要来自三个方面:1)熔炼过程中,铁和合金接触机会较多,如坩埚、铁勺、浇包、熔炼工具等,它们的表面均应涂上涂料。
2)铁在铝合金熔液中溶解速度随温度升高而增大,铝合金熔炼温度高于750℃时,即称为"铝合金过烧",这时候铁的溶解速度增大很快。
3)铝合金中的增铁除了温度因素外,还与时间有关,即保温时间越长,增铁量越多,吸气量也增加,因此尽量减少保温时间对合金增铁,吸气的减少都是有利的。
2、铸铁坩埚及熔炼工具、涂料的使用方法铸铁坩埚及工具预热至120~200℃后,在其表面涂上或喷上涂料,可重复喷涂2~3次,以获得致密、均匀的涂层,随后徐徐加热到200~300℃,以烘干排除水分。
3、熔炼坩埚铸铁坩埚也用于铝合金的保温炉中,因铝合金的熔化温度高,易损坏坩埚,其损坏原因有以下因素:1)表面涂料喷涂不好,造成坩埚腐蚀严重。
2)在正常情况下,采用铸铁坩埚保温时,其溶液温度为620~680℃(按不同合金牌号的铸件的要求而异),如将铸铁坩埚作熔化兼保温时,则埚壁最高温度可达800℃以下;当合金过热时,埚壁温度可达850℃以上,如此温度下,铸铁的抗拉强度很低,稍受载荷或冲击,极可能出现裂纹。
3)由于铝合金熔液对铁的侵蚀使铸铁埚壁的内部和外表同时受到侵蚀和烧损,就会加剧裂纹出现的可能。
从安全和维护合金质量出发,在连续使用时,应经常清除残渣,涂上涂料,转换坩埚方向使用。
铝合金熔铸流程和特征

铝合金熔铸流程和特征铸造铝合金是以熔融金属充填铸型,获得各种形状零件毛坯的铝合金。
具有低密度,比强度较高,抗蚀性和铸造工艺性好,受零件结构设计限制小等优点。
分为Al-Si和Al-Si-Mg-Cu为基的中等强度合金;Al-Cu为基的高强度合金;Al-Mg为基的耐蚀合金;Al-Re为基的热强合金。
大多数需要进行热处理以达到强化合金、消除铸件内应力、稳定组织和零件尺寸等目的。
用于制造梁、燃汽轮叶片、泵体、挂架、轮毂、进气唇口和发动机的机匣等。
还用于制造汽车的气缸盖、变速箱和活塞,仪器仪表的壳体和增压器泵体等零件。
铸造铝合金具有良好的铸造性能,可以制成形状复杂的零件;不需要庞大的附加设备;具有节约金属、降低成本、减少工时等优点,在航空工业和民用工业得到广泛应用。
用于制造梁、燃汽轮叶片、泵体、挂架、轮毂、进气唇口和发动机的机匣等。
还用于制造汽车的气缸盖、变速箱和活塞,仪器仪表的壳体和增压器泵体等零件。
铝合金型材生产包括熔铸、挤压和氧化三个过程。
1.熔铸是铝材生产的首道工序。
主要过程为:(1)配料:根据需要生产的具体合金牌号,计算出各种合金成分的添加量,合理搭配各种原材料。
(2)熔炼:将配好的原材料按工艺要求加入熔炼炉内熔化,并通过除气、除渣精炼手段将熔体内的杂渣、气体有效除去。
(3)铸造:熔炼好的铝液在一定的铸造工艺条件下,通过深井铸造系统,冷却铸造成各种规格的圆铸棒。
2、挤压:挤压是型材成形的手段。
先根据型材产品断面设计、制造出模具,利用挤压机将加热好的圆铸棒从模具中挤出成形。
常用的牌号6063合金,在挤压时还用一个风冷淬火过程及其后的人工时效过程,以完成热处理强化。
不同牌号的可热处理强化合金,其热处理制度不同。
3、氧化:挤压好的铝合金型材,其表面耐蚀性不强,须通过阳极氧化进行表面处理以增加铝材的抗蚀性、耐磨性及外表的美观度。
其主要过程为:(1)表面预处理:用化学或物理的方法对型材表面进行清洗,裸露出纯净的基体,以利于获得完整、致密的人工氧化膜。
铸造铝合金的熔炼(一)

铸造铝合金的熔炼(一)铝合金熔炼的内容包括配料计算,炉料处理,熔炼设备选用,熔炼工具处理及熔炼工艺过程控制。
熔炼工艺过程控制的内容包括正确的加料次序。
严格控制熔炼温度和时间、实现快速熔炼、效果显著的铝液净化处理和变质处理及掌握可靠的铝液炉前质量检测手段等。
熔炼工艺过程控制的目的是获得高质量的能满足下列要求的铝液:1)化学成分符合国家标准,合金液成分均匀;2)合金液纯净,气体、氧化夹杂、熔剂夹杂含量低。
3)需要变质处理的合金液,变质良好。
据统计因熔炼工艺过程控制不严而产生的废品中,如渗漏、气孔、夹渣等,主要原因是合金液中的气体、氧化夹渣、熔剂夹渣未清除所引起。
因此在确保化学成分合格的前提下,熔炼工艺过程控制的主要任务是提高合金液的纯净度和变质效果。
1.铝合金的炉料1.1炉料组成炉料由新金属、中间合金、回炉料及重熔回炉料组成。
1.1.1 新金属国标中可查到新金属的牌号、等级、纯度及用途,是炉料的主要组成,纯度高,可用来稀释回炉料中带入的杂质含量。
1.1.2 中间合金为便于加入某些难熔合金元素,如铜、锰、硅等,或成分严格控制的元素如锑、锶、稀土等,需预先与纯铝制成中间合金。
对中间合金的要求是:熔点和铝掖温度接近,合金元素比例尽可能高,化学成分均匀,冶金质量好,易于破碎,配料称重等。
熔制中间合金的方法有直接熔化法和铝热法。
1.1.3 回炉料回炉料可分成三类。
第一类包括成分合格的报废铸件、浇冒口等,可直接使用;第二类包括小毛边、浇口杯中剩余的金属、冲压车间的边角料等,需重熔成再生合金锭,方能使用;第三类包括熔渣、切屑、炉底残渣及化学成分不合格又无法调整的废金属,如铁含量较高,需经专业化的冶金厂重熔成再生合金锭。
回炉料具有遗传性。
遗传的内容包括有“纯度遗传”和“组织遗传”两种。
纯度高、晶粒细的炉料遗传质量高,熔制的合金质量也会高,有时比等级较低的新金属熔制的合金质量更好。
1.2 配料计算配料计算的任务是按照指定的合金牌号,计算出每一炉次的炉料组成及各种熔剂的用量。
第二章 铸造铝合金熔炼.pdf

4、变质效果评定 (1) 测定共晶反应温度
铝合金熔炼
变质正常,断口银白色丝绒状,晶粒很细,看不到硅亮点; 变质不足,晶粒粗大,断口暗灰色,发亮的硅晶粒明显可见; 变质过度,断口呈青灰色,晶粒粗大;
铝合金熔炼 电阻炉
铝合金熔炼 感应炉
铝合金熔炼 反射炉
铝合金熔炼 高效反射炉
铝合金熔炼
铝合金熔炼
2、变质剂
磷复合变质剂: 10%P+90%C2Cl2,加入量0.25%; 20%P+70%KCl+10%K2TiF6;加入量0.5%-0.8%; 15%P+40%C2Cl2+38%KCl+7%K2TiF6;加入量0.5%-0.8%;
(1) 压入法
1.钠盐变质剂预热,300-400℃,20 -30min; 2.精炼后,除去熔渣和氧化皮;
m 3
Al4C3
n 2
H2
铝合金熔炼
2、影响铝合金液吸气的因素
(1) 合金液氢溶解度与氢的或水蒸汽的分压的影响
(2) 铝合金的蒸气压的影响: 铝的蒸气压较低。
(3) (4) (5)
氧化膜的影响: Al2O3氧化膜致密的。 Al2O3等夹杂物的影响: Al2O3吸氢,核心。 合金元素的影响:加Mg容易吸氢,Si和Cu降低吸氢量。
(2) 脱水氯化锌精炼法
2Al 3ZnCl2 3Zn AlCl3 (gas)
ZnCl2 H2 Zn HCl(gas)
(3) 无毒精炼剂精炼法
无毒精炼剂精炼法原理
NaNO3 C NaCO3 N2 CO2
NaNO3 Na2O NO
氟硅酸钠和冰晶石粉的作用――精炼和缓冲作用; 食盐的作用---------缓冲作用; 耐火砖屑的作用-------精炼剂残留物烧结成团上浮。
铝合金铸造工艺(3篇)

第1篇摘要:铝合金因其具有轻质、高强度、耐腐蚀等优点,在航空航天、汽车制造、建筑等领域得到了广泛的应用。
铝合金铸造是将熔融的铝合金液注入铸模中,经过凝固、冷却和脱模等过程,最终获得具有一定形状和尺寸的铝合金铸件。
本文介绍了铝合金铸造工艺的基本原理、分类、特点以及在实际应用中的注意事项。
一、铝合金铸造工艺的基本原理铝合金铸造工艺是将熔融的铝合金液注入铸模中,使其在铸模内冷却、凝固、结晶,最终形成具有一定形状和尺寸的铝合金铸件。
其基本原理如下:1. 熔融:将铝合金原料在熔炉中加热至熔点,使其熔化成液态。
2. 注入:将熔融的铝合金液通过注管注入铸模中。
3. 冷却:铸模内的铝合金液在冷却介质(如水、空气等)的作用下逐渐凝固。
4. 结晶:凝固过程中,铝合金液中的溶质和杂质逐渐析出,形成晶体。
5. 脱模:铸件凝固、冷却至室温后,从铸模中取出。
6. 后处理:对铸件进行清理、去毛刺、热处理等工序,以提高其性能。
二、铝合金铸造工艺的分类1. 按照铸模材料分类:(1)金属模铸造:铸模由金属制成,如铸铁、钢等。
(2)非金属模铸造:铸模由非金属材料制成,如石墨、砂等。
2. 按照冷却方式分类:(1)水冷铸造:铸模表面涂有水冷材料,冷却速度快。
(2)风冷铸造:铸模表面涂有风冷材料,冷却速度较慢。
3. 按照铸件结构分类:(1)砂型铸造:适用于形状复杂、尺寸较大的铸件。
(2)金属型铸造:适用于形状简单、尺寸较小的铸件。
(3)压铸:适用于形状复杂、尺寸精度要求高的铸件。
三、铝合金铸造工艺的特点1. 生产效率高:铝合金铸造工艺可实现大批量生产,提高生产效率。
2. 成本低:铝合金铸造工艺设备简单,操作方便,生产成本低。
3. 适用范围广:铝合金铸造工艺可适用于各种形状、尺寸和性能要求的铸件。
4. 节能环保:铝合金铸造工艺在生产和应用过程中,具有较好的节能环保性能。
四、铝合金铸造工艺在实际应用中的注意事项1. 铝合金熔融温度:铝合金熔融温度过高或过低都会影响铸件质量,应严格控制熔融温度。
- 1、下载文档前请自行甄别文档内容的完整性,平台不提供额外的编辑、内容补充、找答案等附加服务。
- 2、"仅部分预览"的文档,不可在线预览部分如存在完整性等问题,可反馈申请退款(可完整预览的文档不适用该条件!)。
- 3、如文档侵犯您的权益,请联系客服反馈,我们会尽快为您处理(人工客服工作时间:9:00-18:30)。
1
铸造铝合金熔炼工艺
1 工艺适用范围
本熔炼工艺适用于砂型和金属型铸造ZL101A合金的熔炼,可针
对于重力铸造、低压铸造、倾转浇注、调压铸造等成型工艺使用。
本工艺可作为ZL101A合金熔炼的母工艺,针对某一特定的成型
工艺,如需特殊指出,可在此工艺基础上形成相应熔炼工艺,但不允
许与母工艺相互冲突。
2 工艺文件的抄报与保存
工艺文件抄报、抄送范围:总师、副总师、技术部、质量部。
工艺文件保存范围:电子文件备份和纸质文件送档案室保存,技
术部、质量部各存一份使用文件。
3 工艺详细内容
3.1熔炼设备、工具的选择及对后续熔炼质量的影响
3.1.1 铝合金料熔化设备
规定使用熔炼设备范围为:坩埚电阻炉,燃气连续熔化炉。
对于金属型铸造可采用两种熔炼设备,使用燃气连续熔化炉熔化
铝液,然后转包到坩埚电阻炉进行后续处理(精炼及变质);也可使
用坩埚电阻炉熔化铝液及进行后续处理(精炼及变质)。
如采用金属型低压铸造、调压铸造成型工艺,可使用侧面开口注
入铝液的机下炉进行连续生产。
采用坩埚电阻炉熔化铝液,铝液温度控制750℃以下,熔化过程
的铝液吸气较少;采用燃气连续熔化炉熔化铝液,铝液温度控制容易
2
超750℃,熔化过程的铝液吸气倾向较大。
3.1.2熔炼工具的选择及准备
熔炼前熔炼工具的准备对铝液熔炼质量影响较大,坩埚采用石墨
及SiC材质,使用前需进行预热烘干,烘干工艺如图1;如采用金属
材质坩埚,最好选用不锈钢材质,如选用铸铁材质坩埚,以合金球墨
铸铁为好。常用的浇包、浇勺等多采用不锈钢制作。
图1 新坩埚使用前烘干工艺
上述所选择的工具,使用前均需涂刷涂料,涂刷涂料前要对坩埚
及工具进行喷砂处理,去除表面的铁锈及污物,然后预热到120~
180 ℃,逐层喷涂,浇包、浇勺的涂料厚度0.3~0.8mm为宜,坩埚
涂料可稍厚一些。涂料最好选用专用的金属型非水基涂料,也可自行
配制,基本配方如表1所示,使用前涂料需预热到50~90 ℃。
表1 涂料配方
成分 氧化锌或铝矾土 水玻璃 表面活性剂 水
配比 占水量10~20% 占水量8~15% 占水量1% 100%
3.1.3炉料的存放与处理,
3
熔炼所使用的炉料需存放在干燥、不易混淆和污染的地方,铝锭
按炉号分批次摆放,中间合金及其它炉料应分隔摆放,相应的炉料成
分化验单库房要上交技术部或档案室备案。
炉料在使用前需进行相应处理,表面有污物的要进行去除,再加
入熔化炉之前,对炉料进行烘干处理(大于100℃、超过2h)。
对于所使用的盐类变质剂和除气剂,塑料密封包装在使用前不允
许打开,在潮湿季节,使用前最好进行烘干处理。
3.2熔炼合金的配制工艺
3.2.1 炉料的选择
铝锭选用双零85铝,硅选用一、二级硅,镁选用工业纯镁。
钛选用中间合金形式,以Ф10mm的铝钛硼丝为宜,质量一级,
主成分为钛:5%,硼:1%,杂质含量小于0.5%,余为铝。
3.2.2 配制熔炼工艺
将铝锭(或回炉料)在坩埚内熔化(坩埚容量的1/3),熔化温度
小于730℃,然后将规定重量的硅(块度适宜)加入到已熔化的铝合
金液中,加完以后,用铝锭将硅块压入铝合金液内部,不允许硅块裸
露在空气中,加热熔化,待全部熔化后,搅拌均匀,将温度调整到
680—700℃,用钟罩将镁压入到铝合金液中的,移动钟罩,待镁全部
熔化后,将钟罩从铝合金液中提出,铝钛硼丝在精炼前加入。
3.3 精炼处理
铸造铝合金的精炼的目的: 去除铝合金中的气体,非金属夹杂物
和其它有害元素。
4
3.3.1 盐类除气
钟罩压入式,钟罩大小根据精炼剂使用量确定,钟罩上的出气
孔以Φ3—Φ5mm为宜。处理温度710—750℃,总加入量分为两次加
入较为合理。操作时,钟罩一般要求压入到坩埚底部,并在熔池内缓
慢移动(不要刮碰坩埚底部和坩埚壁),直至反应完成。熔炉上排风
罩不小于坩埚直径。
3.3.2 氩气旋转喷吹精炼
推荐使用旋转喷吹氩气精炼装置,不推荐使用单管吹气方式,
总的原则为,铝合金液表面在处理时,无明显大气泡产生。一般工艺
参数随不同设备的而定,变量参数有:吹头转速、进气压力、进气量、
精炼时间、铝液温度,吹头在坩埚中的工作位置。
3.4 变质处理
铸造铝硅合金变质的目的: 细化合金组织,改变共晶硅形态,提
高铸件的力学性能。
3.4.1 钠盐变质
对于变质后的铝合金液,如在1小时内浇注完成,建议使用钠盐
变质。其工艺过程为:预热三元变质剂,在735—750℃均匀撒在铝
合金液表面,切盐,使之产生分散的桔黄色火苗,时间3—8min。如
采用氩气旋转喷吹精炼,建议二者复合使用。钠盐加入量为
1.5—2.5%。
3.4.2 锶变质
对于变质后的铝合金液,如在1小时内不能浇注完成,使用锶变
5
质,建议使用铝锶合金(10%Sr)作为变质剂,不建议采用锶盐变质。
其工艺过程为:在铝合金熔化见铝水后,尽快加入铝锶合金,而且要
保证在加锶1h后进行浇注。一般要求加入锶后进行精炼处理。锶的
加入量0.01—0.03%。
3.5 铝合金液质量检测
3.5.1精炼效果的检测
建议采用铝合金液真空试样密度检测方法,对于砂型铸造密度
大于2.64g/㎝3;对于金属型铸造密度大于2.60g/㎝3。
3.5.2变质效果检测
建议使用热分析检测仪,变质温度低4—8℃;如无热分析检测
仪,需观察断口分析,并结合金相进行判断。
3.6铝合金液浇注
控制浇注温度;注意挡渣;控制浇注速度。
4 工艺的变更
如需变更工艺,需技术部、质检部、生产部等共同制定试制工
艺,待小批量生产验证后,确定为正式工艺。