聚晶金刚石(PCD)刀具
PCD双刃刀加工参数表

PCD双刃刀加工参数表
1、PCD刀具介绍
金刚石作为一种超硬刀具材料已广泛应用于切削加工,天然金刚石价格昂贵限制了金刚石刀具的发展,20世纪70年代,人们利用高压合成技术合成了聚晶金刚石(PCD),解决了天然金刚石数量稀少、价格昂贵的问题,使金刚石刀具的应用范围扩展到航空、航天、汽车、电子、石材等多个领域。
聚晶金刚石(PCD)刀具主要用于加工有色金属等非黑色金属,
能够刃磨出很锋利的刃口,得到较好的加工表面,而且还是加工非金属新型材料的首选材料,可以切削硬质合金及工业陶瓷等高硬度产品。
2、PCD刀具的性能优势
(1)PCD的硬度可达8000HV,为硬质合金的80~120倍,而且PCD的耐磨性更好。
(2)PCD的导热系数为700W/MK,为硬质合金的1.5~9倍,甚
至高于PCBN和铜。
因此PCD刀具热量传递迅速,良好的传热性在很
大程度上能够延长刀具寿命。
(3)PCD的摩擦系数一般仅为0.1至0.3,而硬质合金的摩擦系数为0.4~1。
因此PCD刀具可显著减小切削力,从而延长了刀具寿命。
(4)PCD的热膨胀系数小,因此PCD刀具热变形小,加工精度高。
刀具热变形越大,加工出的工件表面质量就越差,要想加工出良好加工表面质量的工件就必须严格控制刀具的热变形。
(5)PCD刀具与有色金属和非金属材料的亲和力小,在加工过程中刀尖不易形成积屑瘤。
刀具与被加工材料的亲和力小,那么在加工过程中被加工材料就不容易粘接在刀具表面,也就不容易形成积屑瘤。
(6)PCD刀具的弹性模量大,断裂强度高(比氧化铝高三倍),切削刃钝圆半径值可以磨得很小,不易断裂,能长期保持切削刃的锋利程度。
聚晶金刚石(PCD)刀具在活塞加工中的应用

P D的弹性 模 量 比硬 质 合金 大 得 多 , C 故其 切 削 刃在
切削过程 中不易产生变形 , 能在很大程度上保持刀 刃 的原始几何参数 , 长期保持刃 口 锋利。 () 3 良好 的导热 性和低 热膨 胀系 数 高的导 热系数 和热扩散率使 P D刀具 在切削 C
中切削 热容 易散失 掉 , 这样切 削 区温度会 较低 , 刀具
这样可以使切屑沿前 刀面容易流出, 减小积屑瘤 的
产生 。
2 C P D刀具 ̄ -铝合金材料的优 良性 jr n
P D的优 良特点使 P D刀具广泛应用 于加 工 C C
铝合金 , 尤其 是 高硅 铝 合 金 。高 硅 铝合 金 的硬 度 和
Ke wo d : u i u -i c n a o , p s n y rsa mn l m s io l y l l io , P D ct r t C ut e
1 引言
P D是 指将 金 刚石微粉 ( 度为微 米级 ) C 粒 与少 量 的金属粉 末 ( c ) 如 o等 混合 后 在 高 温 (40C) 压 10  ̄ 高
cs adi plao ah n io . i l , o eav e o o s C u e r t i n es s pctni m c n p t Fn l sm di s nhwt ueP Dctri l i g e . n ta i i n i g sn i ay s o t g y s v h
关键词 : 铝硅合金 , 活塞 , P D刀具 C Ap l fPCD ti g To li M a h n n it n py o Cu tn o n c i i g P so
Zh n o u L u Zh n in z a gi e l a g Ba g o i a qa g h n l ta
pcd不能加工黑色金属的原因

pcd不能加工黑色金属的原因
在现代制造业中,PCD(聚晶金刚石)作为一种超硬材料,广泛应用于各类切削工具的制造。
然而,尽管其性能优越,PCD却无法加工黑色金属。
本文将深入探讨PCD无法加工黑色金属的原因。
首先,我们需要了解PCD的物理和化学性质。
PCD是一种由金刚石微粉聚集体烧结而成的超硬材料,其硬度仅次于天然钻石,具有极高的耐磨性和耐热性。
然而,PCD的化学稳定性相对较差,容易与某些化学物质发生反应。
接下来,我们来分析黑色金属的特性。
黑色金属主要是指铁、铬、锰及其合金,这些金属在常温下容易与空气中的氧气和水蒸气发生反应,形成一层紧密的氧化膜。
这层氧化膜的硬度极高,接近于PCD 本身的硬度,因此使用PCD进行加工时,刀具很容易被这层氧化膜磨损。
此外,黑色金属中的合金元素,如铬和锰,也容易与PCD发生化学反应,导致刀具迅速钝化或严重磨损。
这种化学反应不仅会影响PCD的切削性能,还会产生大量的热,进一步加剧刀具的磨损。
综上所述,PCD无法加工黑色金属的主要原因是其化学稳定性较差,容易与黑色金属中的合金元素发生化学反应,导致刀具迅速钝化或严重磨损。
因此,在选择切削工具时,应充分考虑材料之间的相容性,以最大限度地提高切削效率和延长刀具使用寿命。
金刚石(PCD)铰刀的产品介绍及应用

量,是对金刚石铰刀寿命有很大的影响。 ⑥ 前导向部:前导部是考虑与加工前的孔,其中最小间隙为10--20米欧。
同时还需要注意冷却槽的设计 金刚石铰刀铰孔时,若热量和切屑来不及排出,刀体将发热膨胀,孔的加工质量会明显降低,严重时还会发生“咬死”刀现象。
内镀法
金刚石铰刀内镀的方法: 采用稳定材料制造一个与铰刀外形相反的
高精度内孔胎模,将金刚石磨粒电镀在胎模内表 面,加厚形成电镀层,再将镀层与刀杆粘结在一 起。
金刚石颗粒的顶端整齐,规则地排列在模具 的内表面上,等高性和均匀性较好;
无需修磨,微刃锋利;
所加工孔的尺寸精度和几何精度较高,表面 粗糙度较小,使用寿命较长。
2 PCD铰刀
PCD铰刀的定义及优势
PCD铰刀,一般根据直径大小,采用合金基体或者钢制基体。刃数为2刃或2刃以上。此类刀具主要用于加工公 差要求比较严格,光洁度要求比较高的孔,通孔盲孔均可加工。此类刀具加工的孔,光洁度最高可达Ra0.1以内。
PCD铰刀的优势
具有超高硬度和耐磨性; 具有超长刀具使用寿命; 切削性能稳定,加工效率高; 提高尺寸精度和工艺可靠性。
备注:一般直径15mm左右的可以做成可调式金刚石铰刀,但由于国内市场,可调式金刚石铰刀精度没有固定时金刚 石铰刀好,如果要求精度较高的情况下, 建议选择固定式金刚石铰刀
金刚石铰刀的组成结构及优势
金刚石铰刀的优势
镀层结合力,金刚石粘结牢度,金刚石颗粒分布均匀,外观质量高; 金刚石铰刀前后导向外圆度达到0.005mm,圆柱度为0.005mm/100mm,前导向外圆粗糙度Ra0.63微米, 后导向外圆粗糙度Ra0.16um,刀柄与前后导向部分的同轴度达到0.015mm; 被铰孔工件圆柱度小于0.003,粗糙度可达Ra0.4-0.2,精度高,效率高,使用寿命长; “量体裁衣”式服务,规范化流程,为客服创造的价值超越契约。
如何正确合理使用PCD和PCBN

如何正确合理使用PCD和PCBNPCD(聚晶金刚石)和PCBN(立方氮化硼)是现代切削工具中非常重要的两种超硬材料。
它们在加工高硬度材料、高温合金和难加工材料方面具有重要的应用价值。
正确和合理利用PCD和PCBN材料,可以显著提高加工效率、降低成本和改善加工表面质量。
本文从选择合适的材料、优化工艺参数和正确维护刀具等方面介绍如何正确合理使用PCD和PCBN。
一、选择合适的材料正确选择PCD和PCBN材料是使用的关键。
在选择时需要考虑工件材料、切削条件、切削耐力和加工表面质量要求等因素。
1.工件材料PCD材料适合用于加工铝合金、铜合金、铸铁等非铁系金属材料,而PCBN材料主要应用于加工高硬度材料、高温合金和铸铁等铁系材料。
2.切削条件根据切削条件选择合适的PCD和PCBN材料。
例如,在高速切削(速度大于500 m/min)和干切削条件下,PCD材料能够更好地发挥其优势。
而在低速切削和液冷切削条件下,PCBN材料更为适用。
3.切削耐力根据工件材料的硬度和切削耐力要求选择合适的PCD和PCBN材料。
一般来说,若要加工硬度较低的材料,选择PCD材料;若要加工硬度较高的材料,选择PCBN材料。
4.加工表面质量要求根据加工表面质量要求选择合适的PCD和PCBN材料。
例如,若要求加工表面精度高、光洁度好,选择PCD材料。
若要求加工表面耐磨性好、使用寿命长,选择PCBN材料。
二、优化工艺参数正确调整工艺参数可以提高切削效率、延长刀具寿命和改善加工表面质量。
1.切削速度根据材料的硬度选择合适的切削速度。
一般来说,PCD和PCBN材料的切削速度较高。
但需要注意切削速度过高会导致刀具受热过度,影响刀具寿命。
2.进给量根据材料的硬度选择合适的进给量。
一般来说,对于硬度较低的材料,可以适当增大进给量,提高切削效率。
对于硬度较高的材料,应适当降低进给量,保证加工质量。
3.切削深度根据材料的硬度选择合适的切削深度。
一般来说,对于硬度较低的材料,可以适当增大切削深度,提高切削效率。
PCD刀具应用与发展
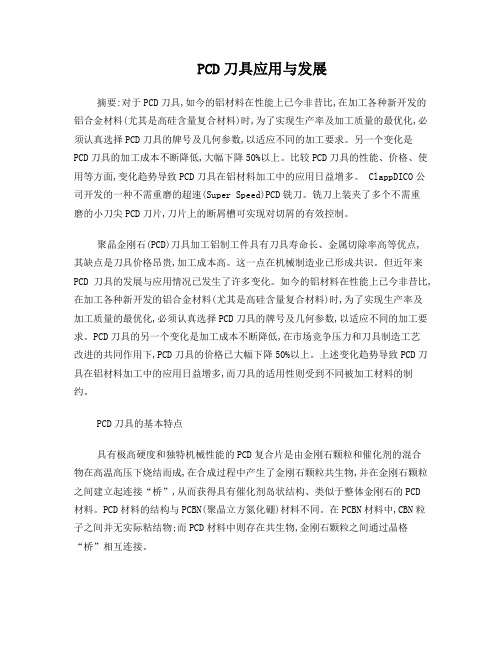
PCD刀具应用与发展摘要:对于PCD刀具,如今的铝材料在性能上已今非昔比,在加工各种新开发的铝合金材料(尤其是高硅含量复合材料)时,为了实现生产率及加工质量的最优化,必须认真选择PCD刀具的牌号及几何参数,以适应不同的加工要求。
另一个变化是PCD刀具的加工成本不断降低,大幅下降50%以上。
比较PCD刀具的性能、价格、使用等方面,变化趋势导致PCD刀具在铝材料加工中的应用日益增多。
ClappDICO公司开发的一种不需重磨的超速(Super Speed)PCD铣刀。
铣刀上装夹了多个不需重磨的小刀尖PCD刀片,刀片上的断屑槽可实现对切屑的有效控制。
聚晶金刚石(PCD)刀具加工铝制工件具有刀具寿命长、金属切除率高等优点,其缺点是刀具价格昂贵,加工成本高。
这一点在机械制造业已形成共识。
但近年来PCD刀具的发展与应用情况已发生了许多变化。
如今的铝材料在性能上已今非昔比,在加工各种新开发的铝合金材料(尤其是高硅含量复合材料)时,为了实现生产率及加工质量的最优化,必须认真选择PCD刀具的牌号及几何参数,以适应不同的加工要求。
PCD刀具的另一个变化是加工成本不断降低,在市场竞争压力和刀具制造工艺改进的共同作用下,PCD刀具的价格已大幅下降50%以上。
上述变化趋势导致PCD刀具在铝材料加工中的应用日益增多,而刀具的适用性则受到不同被加工材料的制约。
PCD刀具的基本特点具有极高硬度和独特机械性能的PCD复合片是由金刚石颗粒和催化剂的混合物在高温高压下烧结而成,在合成过程中产生了金刚石颗粒共生物,并在金刚石颗粒之间建立起连接“桥”,从而获得具有催化剂岛状结构、类似于整体金刚石的PCD材料。
PCD材料的结构与PCBN(聚晶立方氮化硼)材料不同。
在PCBN材料中,CBN粒子之间并无实际粘结物;而PCD材料中则存在共生物,金刚石颗粒之间通过晶格“桥”相互连接。
PCD刀具牌号是以金刚石颗粒的粒度进行分类。
根据制造商的标准,细颗粒、中等颗粒和粗颗粒PCD牌号所对应的金刚石粒度大致分别为2μm、10μm和25μm。
pcd刀具的设计原则

PCD刀具的设计原则一、合理选择PCD粒度PC D粒度的选择与刀具加工条件有关,如设计用于精加工或超精加工的刀具时,应选用强度高、韧性好、抗冲击性能好、细晶粒的P C D。
粗晶粒PC D刀具则可用于一般的粗加工。
PC D材料的粒度对于刀具的磨损和破损性能影响显著。
研究表明:P C D粒度号越大,刀具的抗磨损性能越强。
采用DeBeers 公司S YN DITE 002和S YN DITE025两种PC D材料的刀具加工S iC基复合材料时的刀具磨损试验结果表明,粒度为2μm的S YN DITE002PC D材料较易磨损。
二、合理选择PCD刀片厚度通常情况下,PC D复合片的层厚约为0.3~1.0mm,加上硬质合金层后的总厚度约为2~8mm。
较薄的PC D层厚有利于刀片的电火花加工。
DeBeers公司推出的0.3mm厚P CD复合片可降低磨削力,提高电火花的切割速度。
PC D复合片与刀体材料焊接时,硬质合金层的厚度不能太小,以避免因两种材料结合面间的应力差而引起分层。
三、几何参数与结构设计PC D刀具的几何参数取决于工件状况、刀具材料与结构等具体加工条件。
由于P CD刀具常用于工件的精加工,切削厚度较小(有时甚至等于刀具的刃口半径),属于微量切削,因此其后角及后刀面对加工质量有明显影响,较小的后角、较高的后刀面质量对于提高P C D 刀具的加工质量可起到重要作用。
P C D复合片与刀杆的连接方式包括机械夹固、焊接、可转位等多种方式。
四、PCD复合片与刀杆连接方式的特点与应用连接方式-特点-应用范围机械夹固-由标准刀体及可做成各种集合角度的可换刀片组成,具有快换和便于重磨的优点-中小型机床整体焊接-结构紧凑、制作方便,可制成小尺寸刀具-专用刀具或难于机夹的刀具,用于小型机床机夹焊接-刀片焊接于刀头上,可使用标准刀杆,便于刃磨及调整刀头位置-自动机床、数控机床可转位-结构紧凑,夹紧可靠,不需重磨和焊接,可节省辅助时间,提高刀具寿命-普通通用机床五、PCD刀具的切削参数与失效机理PC D刀具切削参数对切削性能的影响①切削速度PC D刀具可在极高的主轴转速下进行切削加工,但切削速度的变化对加工质量的影响不容忽视。
pcd材料

pcd材料PCD (Polycrystalline Diamond) 是一种具有高硬度和优异耐磨性的材料,由多个小晶体颗粒组成。
PCD材料在工业领域具有广泛的应用,尤其是在切削和磨削工具领域,其独特的性能使其成为一种非常受欢迎的选择。
PCD材料的主要成分是人工合成的金刚石微粉和硬质合金基体。
通过高温高压的工艺,在合适的温度和压力条件下,将金刚石微粉和金属粉末进行烧结,最终形成了坚硬且具有优异耐磨性的PCD材料。
PCD材料具有几个显著的特点。
首先,PCD材料具有极高的硬度,比普通刚玉和硬质合金要高。
其硬度可达到5800-10000HV,使得PCD材料具有出色的切削性能,可以用于切割各种高硬度材料,如铸铁、铝合金、镍合金等。
其次,PCD材料具有出色的耐磨性。
其耐磨性能比一般刚玉和硬质合金高5-10倍,可以大大延长刀具的使用寿命。
这使得PCD材料成为高效率切削工具的理想选择,在高速加工和大批量生产中发挥了重要的作用。
此外,PCD材料还具有良好的导热性能和化学稳定性。
它的导热系数很高,能够迅速将切削过程中产生的热量分散,从而减少切削温度,保护切削刀具不易被热疲劳破坏。
同时,PCD 材料对酸、碱和大部分有机溶剂具有较高的耐腐蚀性,适用于多种工作环境。
在实际应用中,PCD材料可用于制造各种切削工具,如刀具、钻头、车刀和铣刀等。
这些工具广泛用于机械加工、汽车制造、航空航天、电子、模具制造等领域。
虽然PCD材料具有众多优点,但也存在一些限制。
首先,由于其高硬度和脆性,PCD材料容易受到冲击和碰撞而破裂。
因此,在使用过程中需要注意避免过大的冲击力。
其次,PCD 材料的制造成本较高,导致其价格相对较高。
这也限制了其在某些领域的应用。
总之,PCD材料以其高硬度、优异耐磨性和良好的导热性能而受到广泛关注。
在工业领域,PCD材料被广泛应用于切削和磨削工具制造中,并发挥了重要的作用。
随着科学技术的不断进步,相信PCD材料将在更多领域发挥其优势,为人们的生产和生活带来更多便利和效益。
- 1、下载文档前请自行甄别文档内容的完整性,平台不提供额外的编辑、内容补充、找答案等附加服务。
- 2、"仅部分预览"的文档,不可在线预览部分如存在完整性等问题,可反馈申请退款(可完整预览的文档不适用该条件!)。
- 3、如文档侵犯您的权益,请联系客服反馈,我们会尽快为您处理(人工客服工作时间:9:00-18:30)。
PCD的定义,PCD是英文Polycrystalline diamond的简称,中文直译过来是聚晶金刚石的意思.它与单晶金刚石相对应.摘自:中国机械资讯网聚晶金刚石(PCD)刀具发展1.概述1.1 PCD刀具的发展金刚石作为一种超硬刀具材料应用于切削加工已有数百年历史。
在刀具发展历程中,从十九世纪末到二十世纪中期,刀具材料以高速钢为主要代表;1927年德国首先研制出硬质合金刀具材料并获得广泛应用;二十世纪五十年代,瑞典和美国分别合成出人造金刚石,切削刀具从此步入以超硬材料为代表的时期。
二十世纪七十年代,人们利用高压合成技术合成了聚晶金刚石(PCD),解决了天然金刚石数量稀少、价格昂贵的问题,使金刚石刀具的应用范围扩展到航空、航天、汽车、电子、石材等多个领域。
1.2 PCD刀具的性能特点金刚石刀具具有硬度高、抗压强度高、导热性及耐磨性好等特性,可在高速切削中获得很高的加工精度和加工效率。
金刚石刀具的上述特性是由金刚石晶体状态决定的。
在金刚石晶体中,碳原子的四个价电子按四面体结构成键,每个碳原子与四个相邻原子形成共价键,进而组成金刚石结构,该结构的结合力和方向性很强,从而使金刚石具有极高硬度。
由于聚晶金刚石(PCD)的结构是取向不一的细晶粒金刚石烧结体,虽然加入了结合剂,其硬度及耐磨性仍低于单晶金刚石。
但由于PCD烧结体表现为各向同性,因此不易沿单一解理面裂开。
PCD刀具材料的主要性能指标:①PCD的硬度可达8000HV,为硬质合金的80~120倍;②PCD的导热系数为700W/mK,为硬质合金的1.5~9倍,甚至高于PCBN和铜,因此PCD刀具热量传递迅速;③PCD的摩擦系数一般仅为0.1~0.3(硬质合金的摩擦系数为0.4~1),因此PCD刀具可显著减小切削力;④PCD的热膨胀系数仅为0.9×10 -6~1.18×10 -6,仅相当于硬质合金的1/5,因此PCD刀具热变形小,加工精度高;⑤PCD刀具与有色金属和非金属材料间的亲和力很小,在加工过程中切屑不易粘结在刀尖上形成积屑瘤。
1.3 PCD刀具的应用工业发达国家对PCD刀具的研究开展较早,其应用已比较成熟。
自1953年在瑞典首次合成人造金刚石以来,对PCD刀具切削性能的研究获得了大量成果,PCD刀具的应用范围及使用量迅速扩大。
目前,国际上著名的人造金刚石复合片生产商主要有英国De Beers公司、美国GE公司、日本住友电工株式会社等。
据报道,1995年一季度仅日本的PCD刀具产量即达10.7万把。
PCD刀具的应用范围已由初期的车削加工向钻削、铣削加工扩展。
由日本一家组织进行的关于超硬刀具的调查表明:人们选用PCD刀具的主要考虑因素是基于PCD 刀具加工后的表面精度、尺寸精度及刀具寿命等优势。
金刚石复合片合成技术也得到了较大发展,DeBeers公司已推出了直径74mm、层厚0.3mm的聚晶金刚石复合片。
国内PCD刀具市场随着刀具技术水平的发展也不断扩大。
目前中国第一汽车集团已有一百多个PCD车刀使用点,许多人造板企业也采用PCD刀具进行木制品加工。
PCD刀具的应用也进一步推动了对其设计与制造技术的研究。
国内的清华大学、大连理工大学、华中理工大学、吉林工业大学、哈尔滨工业大学等均在积极开展这方面的研究。
国内从事PCD刀具研发、生产的有上海舒伯哈特、郑州新亚、南京蓝帜、深圳润祥、成都工具研究所等几十家单位。
目前,PCD刀具的加工范围已从传统的金属切削加工扩展到石材加工、木材加工、金属基复合材料、玻璃、工程陶瓷等材料的加工。
通过对近年来PCD刀具应用的分析可见,PCD刀具主要应用于以下两方面:①难加工有色金属材料的加工:用普通刀具加工难加工有色金属材料时,往往产生刀具易磨损、加工效率低等缺陷,而PCD刀具则可表现出良好的加工性能。
如用PCD刀具可有效加工新型发动机活塞材料——过共晶硅铝合金(对该材料加工机理的研究已取得突破)。
②难加工非金属材料的加工:PCD刀具非常适合对石材、硬质碳、碳纤维增强塑料(CFRP)、人造板材等难加工非金属材料的加工。
如华中理工大学1990年实现了用PCD刀具加工玻璃;目前强化复合地板及其它木基板材(如MDF)的应用日趋广泛,用PCD刀具加工这些材料可有效避免刀具易磨损等缺陷。
2.PCD刀具的制造技术2.1 PCD刀具的制造过程PCD刀具的制造过程主要包括两个阶段:①PCD复合片的制造:PCD复合片是由天然或人工合成的金刚石粉末与结合剂(其中含钴、镍等金属)按一定比例在高温(1000~2000℃)、高压(5~10万个大气压)下烧结而成。
在烧结过程中,由于结合剂的加入,使金刚石晶体间形成以TiC、SiC、Fe、Co、Ni等为主要成分的结合桥,金刚石晶体以共价键形式镶嵌于结合桥的骨架中。
通常将复合片制成固定直径和厚度的圆盘,还需对烧结成的复合片进行研磨抛光及其它相应的物理、化学处理。
②PCD刀片的加工:PCD刀片的加工主要包括复合片的切割、刀片的焊接、刀片刃磨等步骤。
2.2 PCD复合片的切割工艺由于PCD复合片具有很高的硬度及耐磨性,因此必须采用特殊的加工工艺。
目前,加工PCD 复合片主要采用电火花线切割、激光加工、超声波加工、高压水射流等几种工艺方法,其工艺特点的比较见表1。
表1 PCD复合片切割工艺的比较工艺方法-工艺特点电火花加工-高度集中的脉冲放电能量、强大的放电爆炸力使PCD材料中的金属融化,部分金刚石石墨化和氧化,部分金刚石脱落,工艺性好、效率高超声波加工-加工效率低,金刚石微粉消耗大,粉尘污染大激光加工-非接触加工,效率高、加工变形小、工艺性差在上述加工方法中,电火花加工效果较佳。
PCD中结合桥的存在使电火花加工复合片成为可能。
在有工作液的条件下,利用脉冲电压使靠近电极金属处的工作液形成放电通道,并在局部产生放电火花,瞬间高温可使聚晶金刚石熔化、脱落,从而形成所要求的三角形、长方形或正方形的刀头毛坯。
电火花加工PCD复合片的效率及表面质量受到切削速度、PCD粒度、层厚和电极质量等因素的影响,其中切削速度的合理选择十分关键,实验表明,增大切削速度会降低加工表面质量,而切削速度过低则会产生“拱丝”现象,并降低切割效率。
增加PCD刀片厚度也会降低切割速度。
2.3 PCD刀片的焊接工艺PCD复合片与刀体的结合方式除采用机械夹固和粘接方法外,大多是通过钎焊方式将PCD 复合片压制在硬质合金基体上。
焊接方法主要有激光焊接、真空扩散焊接、真空钎焊、高频感应钎焊等。
目前,投资少、成本低的高频感应加热钎焊在PCD刀片焊接中得到广泛应用。
在刀片焊接过程中,焊接温度、焊剂和焊接合金的选择将直接影响焊后刀具的性能。
在焊接过程中,焊接温度的控制十分重要,如焊接温度过低,则焊接强度不够;如焊接温度过高,PCD容易石墨化,并可能导致“过烧”,影响PCD复合片与硬质合金基体的结合。
在实际加工过程中,可根据保温时间和PCD变红的深浅程度来控制焊接温度(一般应低于700℃)。
国外的高频焊接多采用自动焊接工艺,焊接效率高、质量好,可实现连续生产;国内则多采用手工焊接,生产效率较低,质量也不够理想。
2.4 PCD刀片的刃磨工艺PCD的高硬度使其材料去除率极低(甚至只有硬质合金去除率的万分之一)。
目前,PCD刀具刃磨工艺主要采用树脂结合剂金刚石砂轮进行磨削。
由于砂轮磨料与PCD之间的磨削是两种硬度相近的材料间的相互作用,因此其磨削规律比较复杂。
对于高粒度、低转速砂轮,采用水溶性冷却液可提高PCD的磨削效率和磨削精度。
砂轮结合剂的选择应视磨床类型和加工条件而定。
由于电火花磨削(EDG)技术几乎不受被磨削工件硬度的影响,因此采用EDG技术磨削PCD具有较大优势。
某些复杂形状PCD刀具(如木工刀具)的磨削也对这种灵活的磨削工艺具有巨大需求。
随着电火花磨削技术的不断发展,EDG技术将成为PCD 磨削的一个主要发展方向。
3.PCD刀具的设计原则3.1 刀具材料的选择(1)合理选择PCD粒度PCD粒度的选择与刀具加工条件有关,如设计用于精加工或超精加工的刀具时,应选用强度高、韧性好、抗冲击性能好、细晶粒的PCD。
粗晶粒PCD刀具则可用于一般的粗加工。
PCD材料的粒度对于刀具的磨损和破损性能影响显著。
研究表明:PCD粒度号越大,刀具的抗磨损性能越强。
采用De Beers 公司SYNDITE 002和SYNDITE 025两种PCD材料的刀具加工SiC基复合材料时的刀具磨损试验结果表明,粒度为2μm的SYNDITE 002PCD 材料较易磨损。
2)合理选择PCD刀片厚度通常情况下,PCD复合片的层厚约为0.3~1.0mm,加上硬质合金层后的总厚度约为2~8mm。
较薄的PCD层厚有利于刀片的电火花加工。
De Beers公司推出的0.3mm厚PCD 复合片可降低磨削力,提高电火花的切割速度。
PCD复合片与刀体材料焊接时,硬质合金层的厚度不能太小,以避免因两种材料结合面间的应力差而引起分层。
3.2 刀具几何参数与结构设计PCD刀具的几何参数取决于工件状况、刀具材料与结构等具体加工条件。
由于PCD刀具常用于工件的精加工,切削厚度较小(有时甚至等于刀具的刃口半径),属于微量切削,因此其后角及后刀面对加工质量有明显影响,较小的后角、较高的后刀面质量对于提高PCD刀具的加工质量可起到重要作用。
PCD复合片与刀杆的连接方式包括机械夹固、焊接、可转位等多种方式,其特点与应用范围见表2。
表2 PCD复合片与刀杆连接方式的特点与应用连接方式-特点-应用范围机械夹固-由标准刀体及可做成各种集合角度的可换刀片组成,具有快换和便于重磨的优点-中小型机床整体焊接-结构紧凑、制作方便,可制成小尺寸刀具-专用刀具或难于机夹的刀具,用于小型机床机夹焊接-刀片焊接于刀头上,可使用标准刀杆,便于刃磨及调整刀头位置-自动机床、数控机床可转位-结构紧凑,夹紧可靠,不需重磨和焊接,可节省辅助时间,提高刀具寿命-普通通用机床4.PCD刀具的切削参数与失效机理4.1 PCD刀具切削参数对切削性能的影响(1)切削速度PCD刀具可在极高的主轴转速下进行切削加工,但切削速度的变化对加工质量的影响不容忽视。
虽然高速切削可提高加工效率,但在高速切削状态下,切削温度和切削力的增加可使刀尖发生破损,并使机床产生振动。
加工不同工件材料时,PCD刀具的合理切削速度也有所不同,如铣削Al2O3强化地板的合理切削速度为110~120m/min;车削SiC颗粒增强铝基复合材料及氧化硅基工程陶瓷的合理切削速度为30~40m/min。
(2)进给量如PCD刀具的进给量过大,将使工件上残余几何面积增加,导致表面粗糙度增大;如进给量过小,则会使切削温度上升,切削寿命降低。