球头铣刀计算直径与切削速度计算
铣床参数公式计算
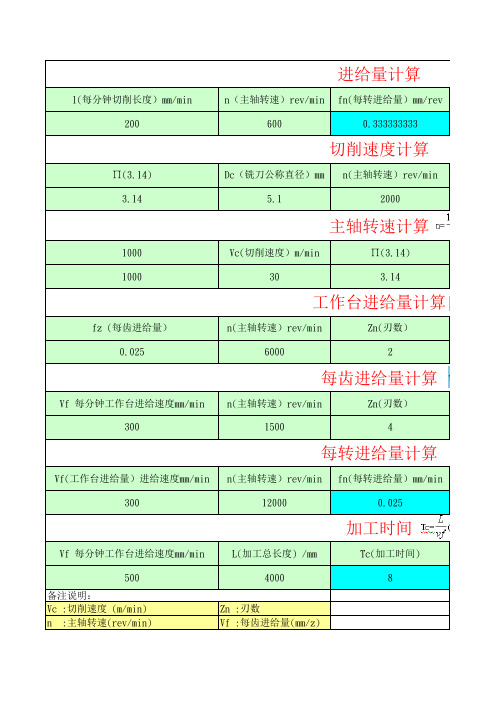
30
3.14
工作台进给量计算
fz (每齿进给量)
Hale Waihona Puke n(主轴转速)rev/min
Zn(刃数)
0.025
6000
2
每齿进给量计算
Vf 每分钟工作台进给速度mm/min 300
n(主轴转速)rev/min
Zn(刃数)
1500
4
每转进给量计算
Vf(工作台进给量)进给速度mm/min n(主轴转速)rev/min fn(每转进给量)mm/min
进给量计算
l(每分钟切削长度)mm/min
n(主轴转速)rev/min fn(每转进给量)mm/rev
200
600
0.333333333
切削速度计算
∏(3.14)
Dc(铣刀公称直径)mm n(主轴转速)rev/min
3.14
5.1
2000
主轴转速计算
1000
Vc(切削速度)m/min
∏(3.14)
1000
Vf(工作台进给量)进给速度 mm/min 300
fz(每齿进给量)mm/min 0.05
Vc(切削速度)m/min 32.028
n(主轴转速)rev/min 955.4140127
间
削速度v、进给量f和切削深度ap,
2.进给量f: 进给量是指工件或刀具每转一周,刀具与工件之间沿进给方向的相对位移。 铣削时,由于铣刀是多齿刀具,所以规定了每齿的进给量af,单位是mm/z。
3.切削深度: 铣削时,这是指待加工表面与已加工表面的垂直距离,单位为mm。
算
计算 计算 量计算
计算 计算
1000 1000
Dc(铣刀公称直径)mm 10
数控机床转速计算公式(一)

数控机床转速计算公式(一)
数控机床转速计算公式
1. 转速计算公式
•转速 (N) = 切削速度 (V) / 刀具直径 (D)
•转速 (N) = 主轴转速 (n) * 主轴倍率
2. 切削速度计算公式
切削速度是指刀具在单位时间内切削加工的路径长度,通常使用单位为 m/min。
切削速度的计算公式如下:
•切削速度(V) = π * 刀具直径 (D) * 主轴转速 (n) / 1000 举例说明:
假设刀具直径为 10mm,主轴转速为 1000 rpm,根据上述公式,可以计算得到切削速度:
切削速度(V) = (π * 10 * 1000) / 1000 = m/min
3. 主轴倍率计算公式
主轴倍率是指主轴转速与转速之间的关系,用于校正转速。
主轴倍率的计算公式如下:
•主轴倍率 = 程序设定转速 / 实际转速
举例说明:
假设程序设定转速为 2000 rpm,实际转速为 1800 rpm,根据上述公式,可以计算得到主轴倍率:
主轴倍率 = 2000 / 1800 =
4. 总结
通过以上的计算公式,可以准确计算数控机床的转速。
首先根据切削速度公式,得到切削速度,然后使用主轴倍率计算实际转速,最终将切削速度除以刀具直径,得到转速。
这些公式是数控机床操作中常用且有效的计算方法,能够帮助创作者准确地控制机床的转速,提高加工效率和质量。
注意:以上公式仅供参考,实际使用中需要根据具体情况进行调整和适配。
刀具切削常用计算公式

N铝=2388rpm vf铝=2865mm/r p铝=9.16kw T铝=36Nm
车削功率和扭矩计算
Vc= 3.14 xD xRPM 1000
举例:车削奥氏体不锈钢外圆,工件硬度HB200, 工 件直径75mm,切深3mm,走刀量0.2mm/r, 切削速度 230m/min, 材料单位切削力为2900N/mm2,加工长度
为100mm
V=Vc xap xfr(mm3/min) RPM=(230X1000)/(3.14X75)=976转每分钟
Vc xap xfr xkc P=
60037.2
T= F力 x(D/2) =P x9549/RPM
RPM=(115X1000)/(3.14X75)=488转每分钟 金属去除率V=115x2x0.2=46 立方厘米每分钟 每加工一个零件的时间=100/(0.2x488)=1.02分钟 镗削功率P=(115x3x0.2x2900)/60037.2=3.35千瓦 镗削力=2900 x0.2 x3=1740牛顿=177.5公斤 镗削扭矩T=1740 x37.5=34牛顿米
F力=Kc xfr xap
车削扭矩T=1740 x37.5=65牛顿米
T= F力 x(D/2) =P x9549/RPM
镗削功率和扭矩计算
计算镗削功率时注意Vc减半, 即Vc镗=1/2Vc车
举例:镗削奥氏体不锈钢,工件硬度HB200, 工 件直径75mm,切深3mm,走刀量0.2mm/r, 切削速 度115m/min, 材料单位切削力为2900N/mm2,加 工长度为100mm
hypermill切削参数公式

hypermill切削参数公式Hypermill是一款强大的切削参数计算软件,它能够帮助用户在数控加工中确定最佳的切削参数,提高加工效率和加工质量。
在使用Hypermill时,用户需要根据具体的加工要求和材料特性来设置切削参数,下面将介绍一些常用的切削参数公式。
1. 切削速度公式:切削速度是切削工具在单位时间内与工件接触的次数,通常用m/min表示。
切削速度的选择应根据工件材料和刀具类型来确定。
常用的切削速度公式如下:切削速度(m/min)=π×刀具直径(mm)×转速(r/min)÷10002. 进给速度公式:进给速度是刀具在单位时间内在工件表面的移动距离,通常用mm/min表示。
进给速度的选择应根据切削质量要求、切削力和切削温度等因素来确定。
常用的进给速度公式如下:进给速度(mm/min)=切削宽度(mm)×进给深度(mm)×转速(r/min)3. 切削深度公式:切削深度是切削工具在单次切削过程中与工件接触的最大深度,通常用mm表示。
切削深度的选择应根据工件材料、刀具类型和切削力等因素来确定。
常用的切削深度公式如下:切削深度(mm)=刀具半径(mm)×切削宽度(mm)4. 切削宽度公式:切削宽度是切削工具在单次切削过程中与工件接触的宽度,通常用mm表示。
切削宽度的选择应根据工件形状、切削质量要求和刀具类型等因素来确定。
常用的切削宽度公式如下:切削宽度(mm)=刀具直径(mm)×切削宽度比率5. 转速公式:转速是切削工具在单位时间内旋转的圈数,通常用r/min表示。
转速的选择应根据切削速度、切削深度和切削宽度等因素来确定。
常用的转速公式如下:转速(r/min)=切削速度(m/min)×1000÷(π×刀具直径(mm))6. 铣削时间公式:铣削时间是完成一次铣削过程所需的时间,通常用min表示。
铣削时间的计算应考虑切削路径长度、进给速度和转速等因素。
铣削公式和定义 工程.doc

铣削公式和定义工程公式切削速度 (vc)(m/min)主轴转速 (n)(rpm)每齿进给量 (fz)(mm)金属去除率 (Q)(cm?/min)工作台进给或进给速度 (vf)(mm/min)扭矩 (Mc)(Nm)净功率要求 (Pc) (kW)平均切屑厚度 (hm),侧铣(mm)面铣(mm)在将工件中央对准铣刀放置时。
注意: aros和arcsin用度表示特定切削力 (kc) (N/mm?)如果γ0,使用γ0= 0°,那么公式变为:特定铣刀公式具有直切削刃的刀具在特定深度的最大切削直径(mm)。
面铣 (对中工件) 直切削刃和侧铣 (ae >Dcap/2) mm。
侧铣 (ae >Dcap/2) 直切削刃,mm。
使用圆刀片的刀具在特定深度的最大切削直径(mm)。
面铣圆刀片 (ae >Dcap/2)mm。
侧铣 (ae >Dcap/2) 和圆刀片 (ap球头立铣刀在特定深度的最大切削直径(mm)。
每齿进给量 (mm/齿),刀具对中。
每齿进给量 (mm/齿),侧铣。
内圆坡走铣 (3轴) 或圆弧铣 (2轴) 计算公式周边进给率(mm/min)刀具中心进给率(mm/min)径向切深(mm)对于实体式工件, Dw = 0和 ae eff = Dm/2每齿进给量(mm)当扩孔时每齿进给量(mm)外圆坡走铣 (3轴) 或圆弧铣 (2轴)计算公式周边进给率(mm/min)刀具中心进给率(mm/min)每齿进给量(mm)铣刀主偏角– kr (度)主切削刃角 (kr) 是影响切削力方向和切屑厚度的主要因素。
刀具直径– Dc (mm)刀具直径 (Dc)在PK部位上测量,主切削刃在这里与平行刃带相遇。
Dc 是在大多数情况下出现在订货号的直径,但CoroMill 300除外,它使用D3 。
要考虑的最重要直径是(Dcap) –在实际切削深度 (ap) 处的有效切削直径–用于计算实际切削速度 (ve)。
常用的车削、铣削、钻削加工计算公式全在这里了,随用随查

常用的车削、铣削、钻削加工计算公式全在这里了,随用随查01常用车削加工计算公式●切削线速度Vc(m/min)D m:加工直径,单位(mm)n:主轴转速,单位(rpm)●主轴转速 n (rpm)Vc:切削线速度,单位(m/min)D m:加工直径,单位(mm)●金属去除率 Q (cm3/min)Vc:切削线速度,单位(m/min)a p:切深(吃刀量),单位(mm)f n:每转进给量,单位(mm/r)●净功率 Pc (kW)Vc:切削线速度,单位(m/min)a p:切深(吃刀量),单位(mm)f n:每转进给量,单位(mm/r)●加工时间 Tc (min)I m:加工长度,单位(mm)f n:每转进给量,单位(mm/r)n:主轴转速,单位(rpm)●特定切削力 Kc(N/mm2)k c1:特定切削力,适用于h m= 1 mmh m:平均切屑厚度,单位(mm)m c:实际校正系数h mγ0:切屑前角02常用铣削加工计算公式03常用孔加工计算公式其它一些加工计算公式,也许对你有用。
一、挤牙丝攻内孔径计算公式:公式:牙外径-1/2×牙距例1:公式:M3×0.5=3-(1/2×0.5)=2.75mm M6×1.0=6-(1/2×1.0)=5.5mm例2:公式:M3×0.5=3-(0.5÷2)=2.75mm M6×1.0=6-(1.0÷2)=5.5mm二、一般英制丝攻之换算公式:1英寸=25.4mm(代码)例1:(1/4-30)1/4×25.4=6.35(牙径)25.4÷30=0.846(牙距)则1/4-30换算成公制牙应为:M6.35×0.846例2:(3/16-32)3/16×25.4=4.76(牙径)25.4÷32=0.79(牙距)则3/16-32换算成公制牙应为:M4.76×0.79三、一般英制牙换算成公制牙的公式:分子÷分母×25.4=牙外径(同上)例1:(3/8-24)3÷8×25.4=9.525(牙外径)25.4÷24=1.058(公制牙距)则3/8-24换算成公制牙应为:M9.525×1.058四、美制牙换算公制牙公式:例:6-326-32 (0.06+0.013)/代码×6=0.1380.138×25.4=3.505(牙外径)25.4÷32=0.635(牙距)那么6-32换算成公制牙应为:M3.505×0.6351、孔内径计算公式:牙外径-1/2×牙距则应为:M3.505-1/2×0.635=3.19那么6-32他内孔径应为3.192、挤压丝攻内孔算法:下孔径简易计算公式1:牙外径-(牙距×0.4250.475)/代码=下孔径例1:M6×1.0M6-(1.0×0.425)=5.575(最大下孔径)M6-(1.0×0.475)=5.525(最小)例2:切削丝攻下孔内径简易计算公式:M6-(1.0×0.85)=5.15(最大)M6-(1.0×0.95)=5.05(最小)M6-(牙距×0.860.96)/代码=下孔径例3:M6×1.0=6-1.0=5.0+0.05=5.05五、压牙外径计算简易公式:1.直径-0.01×0.645×牙距(需通规通止规止)例1:M3×0.5=3-0.01×0.645×0.5=2.58(外径) 例2:M6×1.0=6-0.1×0.645×1.0=5.25(外径) 六、公制牙滚造径计算公式:(饱牙计算)例1:M3×0.5=3-0.6495×0.5=2.68(车削前外径) 例2:M6×1.0=6-0.6495×1.0=5.35(车削前外径)七、压花外径深度(外径)外径÷25.4×花齿距=压花前外径例:4.1÷25.4×0.8(花距)=0.13 压花深度应为0.13八、多边形材料之对角换算公式:1.四角形:对边径×1.414=对角径2.五角形:对边径×1.2361=对角径3.六角形:对边直径×1.1547=对角直径公式2:1.四角:对边径÷0.71=对角径2.六角:对边径÷0.866=对角径九、刀具厚度(切刀):材料外径÷10+0.7参考值十、锥度的计算公式:公式1:(大头直径-小头直径)÷(2×锥度的总长)=度数等于查三角函数值公式2:简易(大头直径-小头直径)÷28.7÷总长=度数-End-。
金属切削加工速查速算与典型零件加工工艺、操作技术实用手册
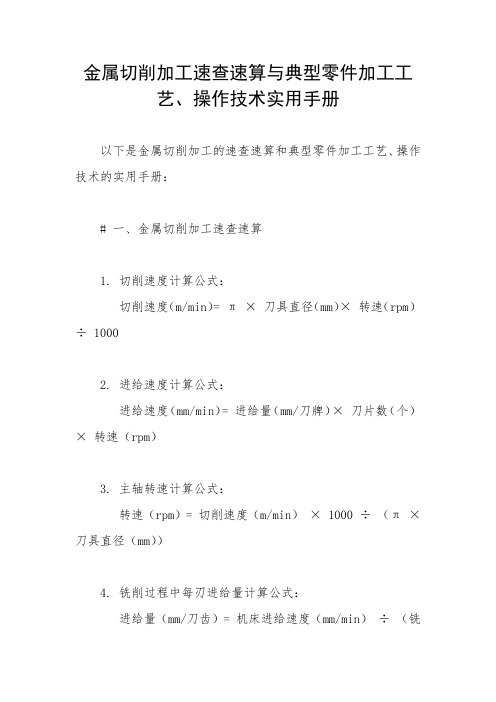
金属切削加工速查速算与典型零件加工工艺、操作技术实用手册以下是金属切削加工的速查速算和典型零件加工工艺、操作技术的实用手册:# 一、金属切削加工速查速算1. 切削速度计算公式:切削速度(m/min)= π×刀具直径(mm)×转速(rpm)÷ 10002. 进给速度计算公式:进给速度(mm/min)= 进给量(mm/刀牌)×刀片数(个)×转速(rpm)3. 主轴转速计算公式:转速(rpm)= 切削速度(m/min)× 1000 ÷(π×刀具直径(mm))4. 铣削过程中每刃进给量计算公式:进给量(mm/刀齿)= 机床进给速度(mm/min)÷(铣刀直径(mm)×刀齿数)5. 铣削切削宽度计算公式:切削宽度(mm)= 铣削进给量(mm/刀齿)×刀齿数# 二、典型零件加工工艺1. 钻孔工艺:- 固定工件,选取合适的钻头。
- 设置合适的切削速度和进给速度。
- 开始钻孔,保持合适的冷却液供给。
2. 车削工艺:- 固定工件,选择合适的车刀。
- 设置合适的主轴转速、进给速度和切削速度。
- 开始车削,保持合适的切削液供给。
3. 镗削工艺:- 固定工件,选择合适的镗刀。
- 设置合适的主轴转速、进给速度和切削速度。
- 开始镗削,保持合适的切削液供给。
4. 铣削工艺:- 固定工件,选择合适的铣刀。
- 设置合适的主轴转速、进给速度和切削速度。
- 开始铣削,保持合适的切削液供给。
5. 磨削工艺:- 固定工件,选择合适的砂轮或砂带。
- 设置合适的主轴转速、进给速度和切削速度。
- 开始磨削,保持合适的冷却液供给。
# 三、操作技术实用手册1. 切削液使用技巧:- 选择合适的切削液种类和浓度。
- 保持切削液的清洁度和稳定性。
- 定期更换和补充切削液。
2. 刀具维护技巧:- 定期检查刀具磨损情况。
- 及时更换磨损严重的刀具。
铣床加工

铣削加工铣床加工是以铣刀回转作主运动、工件或铣刀作进给运动的切削加工方法。
铣床除能铣削平面、沟槽、轮齿、螺纹和花键轴外,还能加工比较复杂的型面,效率较刨床高,在机械制造和修理部门得到广泛应用。
第一节铣床一、铣床的的功用和运动铣床通常以铣刀的回转和工件的移动作为它的表面成形运动。
使用分度头和回转工作台等铣床附件装夹工件时,还可以实现工件的圆周进给。
因此铣床的工作范围很广。
二、铣床分类铣床种类很多,一般是按布局形式和适用范围加以区分,主要的有升降台铣床、龙门铣床、单柱铣床和单臂铣床、仪表铣床、工具铣床等。
升降台铣床有万能式、卧式和立式几种,主要用于加工中小型零件,应用最广;龙门铣床包括龙门铣镗床、龙门铣刨床和双柱铣床,均用于加工大型零件;单柱铣床的水平铣头可沿立柱导轨移动,工作台作纵向进给;单臂铣床的立铣头可沿悬臂导轨水平移动,悬臂也可沿立柱导轨调整高度。
单柱铣床和单臂铣床均用于加工大型零件。
仪表铣床是一种小型的升降台铣床,用于加工仪器仪表和其他小型零件;工具铣床主要用于模具和工具制造,配有立铣头、万能角度工作台和插头等多种附件,还可进行钻削、镗削和插削等加工。
其他铣床还有键槽铣床、凸轮铣床、曲轴铣床、轧辊轴颈铣床和方钢锭铣床等,它们都是为加工相应的工件而制造的专用铣床。
另外,按控制方式,铣床又可分为仿形铣床、程序控制铣床和数控铣床等。
三、工件在铣床上的装夹铣床工作台台面上有几条T形槽,较大的工件可靠可靠可以使用螺钉和压板直接装夹在工作台上。
中、小型工件常通过机床用平口虎钳、回转工作台和分度头等铣床附件装夹在工作台上。
第二节铣削加工一、铣刀刀具是机械制造中用于切削加工的工具,又称切削工具。
广义的切削工具既包括刀具,还包括磨具。
绝大多数的刀具是机用的,但也有手用的。
由于机械制造中使用的刀具基本上都用于切削金属材料,所以“刀具”一词一般就理解为金属切削刀具。
切削木材用的刀具则称为木工刀具。
在采用合金工具钢时,刀具的切削速度提高到约8米/分,采用高速钢时,又提高两倍以上,到采用硬质合金时,又比用高速钢提高两倍以上,切削加工出的工件表面质量和尺寸精度也大大提高。
- 1、下载文档前请自行甄别文档内容的完整性,平台不提供额外的编辑、内容补充、找答案等附加服务。
- 2、"仅部分预览"的文档,不可在线预览部分如存在完整性等问题,可反馈申请退款(可完整预览的文档不适用该条件!)。
- 3、如文档侵犯您的权益,请联系客服反馈,我们会尽快为您处理(人工客服工作时间:9:00-18:30)。
球头铣刀计算直径与切削速度计算
Click:99 Date:7/12/2011 5:23:34 AM
球头铣刀的计算直径Deff一般要小于铣刀直径Dc,故其实际转速不应按铣刀直径Dc计算,而应按计算直径Deff计算。
Deff=(Dc²-(Dc-2×ap)²)0.5
为铣刀直径,ap为切削深度。
而:
n=Vc×1000/(π×Deff)
公式:
3.14*d*n
切削速度Vc=-------- (m/s)
1000
Vc*1000
主轴转速n=--------- (r/m)
d*n
进给量f= fz*Z (fz-每次进给量,Z-刀齿数)
进给速度Vf=n*fz*Z
球头铣刀Deff
铣刀直径Dc
切削深度ap
2 2
Deff={Dc-(Dc-2*ap) }*0.5
Vc*1000
n=---------- (mm/min)
p* Deff
切削宽度L:(又称步距)一步切削宽度L与刀具直径 d成
正比,与切削深度成反比。
d=D-2r(r圆角半径)
平底刀:L=(0.6-0.9)d
圆鼻刀:L=(0.8-0.9)d
用球头刀进行平面或斜面的残余高度控制:
I‘前一球刀中心与后一球刀中心的距离’
R‘球刀半径’
h‘残余高度’
......(平面)I=2 R*R-(h-R)..........
(斜面)I`=I(sin@)
. ......h`=R- .............
UG 编程要点知识:
轮廓切削方法通常用于零件的侧壁或者外形轮廓的精加工,外形可以事封闭的或者敞开的,可以是连续的或者非连续的,具体的应用有内壁和外形的加工、陡、壁的介层加工等。
常用的方式是在精加工中使用轮廓切削方式,在粗加工中使用跟随工件切削方式。
球头铣刀计算直径与切削速度计算
Click:99 Date:7/12/2011 5:23:34 AM 球头铣刀的计算直径Deff一般要小于铣刀直径Dc,故其实际转速不应按铣刀直径Dc计
算,而应按计算直径Deff计算。
Deff=(Dc²-(Dc-2×ap)²)0.5
为铣刀直径,ap为切削深度。
而:
n=Vc×1000/(π×De ff)
公式:
3.14*d*n
切削速度Vc=-------- (m/s)
1000
Vc*1000
主轴转速n=--------- (r/m)
d*n
进给量f= fz*Z (fz-每次进给量,Z-刀齿数)
进给速度Vf=n*fz*Z
球头铣刀Deff
铣刀直径Dc
切削深度ap
2 2
Deff={Dc-(Dc-2*ap) }*0.5
Vc*1000
n=---------- (mm/min)
p* Deff
切削宽度L:(又称步距)一步切削宽度L与刀具直径d成正比,与切削深度成反比。
d=D-2r(r圆角半径)
平底刀:L=(0.6-0.9)d
圆鼻刀:L=(0.8-0.9)d
用球头刀进行平面或斜面的残余高度控制:
I‘前一球刀中心与后一球刀中心的距离’
R‘球刀半径’。