碳化钛粒径对碳氮化钛基金属陶瓷微观结构和力学性能的影响
显微组织对金属材料力学性能影响的研究

显微组织对金属材料力学性能影响的研究金属材料是我们日常生活中广泛使用的材料之一,其力学性能的研究对于材料的应用和改进至关重要。
在金属材料的研究中,显微组织是一个非常重要的因素,它对金属材料的力学性能有着直接影响。
1. 显微组织对金属材料硬度的影响硬度是材料的重要力学性能之一,它反映了材料抗压、抗划伤和耐磨损的能力。
显微组织通过晶格结构和晶界分布的形成,对材料的硬度产生直接影响。
一方面,晶粒尺寸是影响金属材料硬度的重要因素之一。
晶粒尺寸越小,其晶体内的晶界面积越大,晶界能对位错的运动产生阻碍,从而增加了材料的硬度。
因此,通过控制材料的热处理或机械加工过程,可以使晶粒尺寸减小,从而提高金属材料的硬度。
另一方面,不同的晶体结构也会对材料的硬度产生影响。
例如,正交晶系的金属材料由于存在较为规则的晶胞结构,其原子排列更加紧密,因此具有较高的硬度。
而体心立方和面心立方结构的金属材料由于晶胞结构的特殊性,会降低其硬度。
通过改变材料的晶体结构,可以调控金属材料的硬度。
2. 显微组织对金属材料韧性的影响韧性是另一个关键的金属材料力学性能指标,它反映了材料在受到外界冲击或加载时的抗拉伸和抗断裂能力。
显微组织可以通过晶界、孔隙和夹杂物等组成部分对金属材料的韧性产生影响。
首先,显微组织中晶界的存在对金属材料的韧性有一定影响。
晶界可以视为晶体之间的边界,其中原子的排列比较无序,容易形成位错、波动和滑移。
晶界能够吸收因外界应力而产生的位错,从而增加材料的塑性变形能力和抗断裂能力,提高材料的韧性。
因此,晶界的存在对金属材料的韧性起到了积极的作用。
此外,显微组织中的孔隙和夹杂物也会对材料的韧性产生影响。
这些缺陷在金属材料中起到了应力集中的作用,使其在受力时容易发生断裂。
控制显微组织中缺陷的分布和形态,可以降低金属材料中的孔隙和夹杂物含量,从而提高材料的韧性。
3. 显微组织对金属材料的强度影响强度是指材料在外力作用下抵抗变形和破坏的能力。
氮化钛

氮化钛氮化钛是一种新型的多功能金属陶瓷材料,它的熔点高、硬度大、摩擦系数小,是热和电的良导体。
首先,氮化钛是用于高强度的金属陶瓷工具、喷汽推进器、以及火箭等优良的结构材料。
另外,氮化钛有较低的摩擦系数,可作为高温润滑剂。
氮化钛合金用作轴承和密封环可显示出优异的效果。
氮化钛有较高的导电性,可用作熔盐电解的电极以及点触头、薄膜电阻等材料。
氮化钛有较高的超导临界温度,是优良的超导材料。
尤其引人注目的是,氮化钛涂层及其烧结体具有令人满意的金黄色,可作为代金装饰材料,具有很好的仿金效果、装饰价值,并具有防腐、延长工艺品的寿命。
镀有氮化钛膜的玻璃还是一种新的“热镜材料”,当薄膜的厚度大于90nm时,红外线的反射率大于75%,提高了玻璃的保温性能。
氮化钛薄膜的颜色还可以随意调整,随氮含量的降低,薄膜将呈现金黄、古铜、粉红等颜色,非常美观。
目前,由于含氮金属陶瓷工具的开发而使氮化钛粉末的需要急剧增加起来;而且国际上代金装饰技术发展相当快,氮化钛在这方面的应用具有十分广阔的前景。
不仅因为氮化钛涂层价格低廉,而且还由于它在耐腐蚀、耐摩擦等性能方面都胜过真空涂层。
因此,对氮化钛的研究具有重要的经济意义。
氮化钛具有典型的NaCl型结构,属面心立方结构点阵。
氮化钛属于“间隙原子”,其中钛原子占据面心立方的角顶。
氮化钛是非计量化合物,它的组成为TiN0.6-TiN1.16。
氮的含量可在一定范围内变化而不引起氮化钛的结构发生变化。
由于TiN、TiC、TiO三者晶格参数接近(分别为4.23,4.238,4.15)氮原子常被碳原子、氧原子以任意比例取代形成固溶体,氮原子的变化会引起氮化钛的物理性质发生变化如氮含量减小、碳含量增加、氮化钛的晶格参数增大、显微硬度增大、抗震性降低。
氮化钛粉末一般呈黄褐色,超细氮化钛粉末呈黑色,而氮化钛晶体呈黄色,具有金属光泽。
氮化钛的熔点为3223K,密度为5.43~5.44g/cm3,硬度为8~9,热膨胀系数为 6.81*10-6/℃(室温),热导率为29.31W/(m*K)(室温) ,电阻率为22*10-6Ω*cm(室温)。
碳化钛分子量

碳化钛分子量
碳化钛是一种由钛和碳组成的化合物,化学式为TiC。
它的分子量取决于其中的钛和碳的比例,可以从60到240克/摩尔不等。
下面将详细介绍不同比例下的碳化钛分子量及其物理化学性质。
1. TiC的分子量为60.08克/摩尔,当其化学计量比为Ti:C=1:1时。
此时,碳化钛呈白色粉末状,结晶度高、硬度大、高熔点(约3150℃)、高耐磨性、难溶于大多数酸、碱和盐溶液。
由于这些性质,它常常被用于制造硬质合金、金属陶瓷等材料。
此外,碳化钛还是电炉炉衬、航空航天材料、高温阀门等领域的关键材料。
2. 当Ti:C=1:0.8时,碳化钛分子量为67.73克/摩尔。
此时,碳化钛的颜色开始变为浅灰色,硬度也略有降低,但仍保持较高的熔点、耐磨性和耐腐蚀性。
此种比例的碳化钛通常被用于制造金属陶瓷、热喷涂等材料。
5. 当Ti:C=1:2时,碳化钛分子量为102.52克/摩尔,此时碳化钛呈现出较差的物理化学性质,其硬度已经接近于铁,在一些强酸和强碱中也会有一定的溶解性。
但它仍可以用于制造锻压模具、切削工具等耐磨材料。
总之,碳化钛的分子量与其化学计量比有关,化学计量比不同将导致碳化钛的物理化学性质发生不同程度的变化。
不同比例的碳化钛在工业生产和科学研究中都有广泛的应用。
金属陶瓷
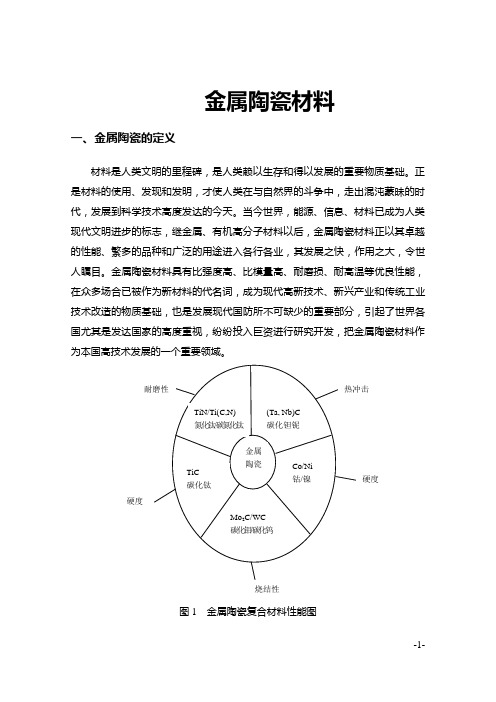
金属陶瓷材料一、金属陶瓷的定义材料是人类文明的里程碑,是人类赖以生存和得以发展的重要物质基础。
正是材料的使用、发现和发明,才使人类在与自然界的斗争中,走出混沌蒙昧的时代,发展到科学技术高度发达的今天。
当今世界,能源、信息、材料已成为人类现代文明进步的标志,继金属、有机高分子材料以后,金属陶瓷材料正以其卓越的性能、繁多的品种和广泛的用途进入各行各业,其发展之快,作用之大,令世人瞩目。
金属陶瓷材料具有比强度高、比模量高、耐磨损、耐高温等优良性能,在众多场合已被作为新材料的代名词,成为现代高新技术、新兴产业和传统工业技术改造的物质基础,也是发展现代国防所不可缺少的重要部分,引起了世界各国尤其是发达国家的高度重视,纷纷投入巨资进行研究开发,把金属陶瓷材料作为本国高技术发展的一个重要领域。
图1 金属陶瓷复合材料性能图1、金属陶瓷的概念金属陶瓷是由陶瓷硬质相与金属或合金粘结相组成的结构材料。
从金属陶瓷英文单词Cermets来,是由Ceramic(陶瓷)和Metal(金属)结合构成的。
金属陶瓷既保持了陶瓷的高强度、高硬度、耐磨损、耐高温、抗氧化和化学稳定性等特性,又具有较好的金属韧性和可塑性。
由于“金属陶瓷”和“硬质合金”两个学科术语没有明确的分界,所以具体材料也很难划分界线,从材料的组元看,“硬质合金”应该归入“金属陶瓷”,IE. Campbell就将“硬质合金”归入到“金属陶瓷”。
2、金属陶瓷的历史WC-Co基金属陶瓷作为研究最早的金属陶瓷,由于具有很高的硬度(HRA80~92),极高的抗压强度6000MPa(600kg/mm2),已经应用于许多领域。
但是由于W和Co资源短缺,促使了无钨金属陶瓷的研制与开发,迄今已历经三代:第一代是“二战”期间,德国以Ni粘结TiC生产金属陶瓷;第二代是20世纪60年代美国福特汽车公司添加Mo到Ni粘结相中改善TiC和其他碳化物的润湿性,从而提高材料的韧性;第三代金属陶瓷则将氮化物引入合金的硬质相,改单一相为复合相。
Y_2O_3添加剂对SiC复相多孔陶瓷烧结性能和力学性能的影响
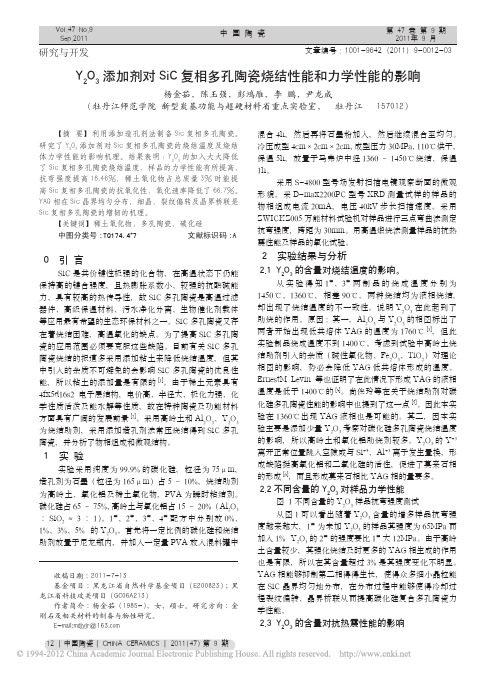
【摘 要】利用添加造孔剂法制备SiC 复相多孔陶瓷。
研究了Y 2O 3添加剂对SiC 复相多孔陶瓷的烧结温度及烧结体力学性能的影响机理。
结果表明:Y 2O 3的加入大大降低了SiC 复相多孔陶瓷烧结温度,样品的力学性能有所提高,抗弯强度提高18.46%,稀土氧化物占总质量3%时能提高SiC 复相多孔陶瓷的抗氧化性,氧化速率降低了66.7%。
YAG 相在SiC 晶界均匀分布,细晶,裂纹偏转及晶界桥联是SiC 复相多孔陶瓷的增韧的机理。
【关键词】稀土氧化物,多孔陶瓷,碳化硅中图分类号:TQ174.4+7 文献标识码:A0 引 言SiC 是共价键性极强的化合物,在高温状态下仍能保持高的键合强度,且热膨胀系数小、较强的抗酸碱能力、具有较高的热传导性,故SiC 多孔陶瓷是高温过滤器件、高级保温材料、污水净化分离、生物催化剂载体等应用最有希望的生态环保材料之一。
SiC 多孔陶瓷又存在着烧结困难,高温氧化的缺点。
为了提高SiC 多孔陶瓷的应用范围必须要克服这些缺陷。
目前有关SiC 多孔陶瓷烧结的报道多采用添加粘土来降低烧结温度,但其中引入的杂质不可避免的会影响SiC 多孔陶瓷的优良性能,所以粘土的添加量是有限的[1]。
由于稀土元素具有4fx5d16s2 电子层结构,电价高、半径大、极化力强、化学性质活泼及能水解等性质,故在特种陶瓷及功能材料方面具有广阔的发展前景[2]。
采用高岭土和Al 2O 3、Y 2O 3为烧结助剂,采用添加造孔剂法常压烧结得到SiC 多孔陶瓷,并分析了物相组成和微观结构。
1 实 验实验采用纯度为99.9%的碳化硅,粒径为75μm,造孔剂为石墨(粒径为165μm)占5~10%,烧结助剂为高岭土、氧化铝及稀土氧化物,PVA 为瞬时粘结剂。
碳化硅占65~75%,高岭土与氧化铝占15~20%(Al 2O 3 ∶SiO 2≈3∶1)。
1#、2#、3#、4#配方中分别放0%、1%、3%、5% 的Y 2O 3。
氮化钛杨氏模量
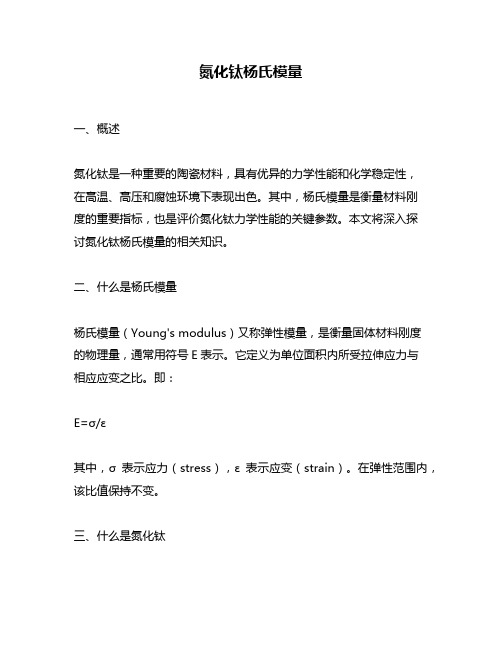
氮化钛杨氏模量一、概述氮化钛是一种重要的陶瓷材料,具有优异的力学性能和化学稳定性,在高温、高压和腐蚀环境下表现出色。
其中,杨氏模量是衡量材料刚度的重要指标,也是评价氮化钛力学性能的关键参数。
本文将深入探讨氮化钛杨氏模量的相关知识。
二、什么是杨氏模量杨氏模量(Young's modulus)又称弹性模量,是衡量固体材料刚度的物理量,通常用符号E表示。
它定义为单位面积内所受拉伸应力与相应应变之比。
即:E=σ/ε其中,σ表示应力(stress),ε表示应变(strain)。
在弹性范围内,该比值保持不变。
三、什么是氮化钛1. 氮化钛的结构与特点氮化钛(TiN)属于金属陶瓷材料,具有典型的离子型晶体结构。
其晶胞结构为面心立方格子,每个Ti原子被6个N原子包围着形成八面体配位结构。
由于Ti-N键长相对较短,键能较高,使得氮化钛具有优异的硬度和弹性模量。
此外,氮化钛还具有较好的耐腐蚀性、高温稳定性和导电性能。
2. 氮化钛的制备方法目前,常用的氮化钛制备方法主要包括物理气相沉积(PVD)、化学气相沉积(CVD)和热反应法等。
其中,PVD是一种将金属或合金靶材在真空环境下加热蒸发,使其沉积在基底表面形成薄膜的方法。
CVD则是通过将金属有机物或卤化物等气体与反应气体在高温下反应生成氮化物沉积在基底表面上。
热反应法则是利用Ti粉末与NH3等反应生成TiN粉末。
四、影响氮化钛杨氏模量的因素1. 晶格结构晶格结构是影响杨氏模量的重要因素之一。
由于TiN具有典型的离子型晶体结构,在其晶胞中存在着大量共价键和离子键,因此其刚度较高。
此外,晶格结构还会影响材料的热膨胀系数和热导率等性能。
2. 成分和杂质氮化钛的成分和杂质也会对其杨氏模量产生影响。
例如,当TiN中含有过量的氮或碳等元素时,会导致晶格结构发生变化,从而影响材料的力学性能。
此外,杂质也可能引入缺陷,从而降低材料的强度和刚度。
3. 制备工艺制备工艺也是影响氮化钛杨氏模量的重要因素之一。
搪瓷用含钛热轧高强钢板的显微组织和力学性能研究

( .R & D C n r B oh nI nadS e C . t. S aga 2 10 ,C ia 1 e t , asa o n t l o ,Ld , h nhi 09 0 hn ; e r e
S u y o ir sr cu e a d M e h n c lPr p ris t d n M c o t u t r n c a ia o e t e
o t n u - Co a n n g ・ S r ng h f Tia i m - nt i i g Hi h — t e t - - H o —Ro ld S e l o a el g t- — l t es f r En m l n e i
3 C l g f t i s c nea dE g er g D nh aU i ri , h nhi 00 1 C ia . ol eo e a i c n ni e n , ogH n esy S aga 2 0 5 , h ) e Ma r l S e n i v t n
Ab ta t T e e a l d tn sh v e n w d l sd frw trh aest e lc tils te ,HDG sr c : h n mel a k a eb e ieyu e o ae e tr orpa es nesse 1 e a s e n ls ctn sd et sln evc ie,n n —txca d hg orso eitn e ost f t la d pa t a k u oi gs riel e i t o v o o i n ih c r in rs a c .T ai y o s s te rq i me t o omig wedn n n mel g o ne a k, te tes h ud b f hg h e ur e ns ffr n , lig a d e a ln f itr tn i h s l e so l e o ih s e gh,e c l n o a i t tnt r x el tfr bly,wed bly a d e a l bly,ep cal ih srn h atrf n . e m i la it n n mel it i a i s e il hg t g f r g y et e i i T ers l h w ta u otef ea d ds es et a im p e ii tsteta im —c nan n ih h e ut s o h td et h n n i ri i nu rcpt e h i nu — o tiighg s i p v t a t
TiAl基合金的工艺-显微组织-力学性能关系

1.1台金元素对强度和延性的影响‘”乱
TiAl基合金的强度和延性受化学成分及显微 组织控制,对Ti一(43~55)Al(摩尔分数,%)成分合 金,在Ti.51 Al成分附近合金的强度最低。室温延 性受铝含量控制,最大值出现在两相Ti一48舢成分 附近。对Ti一48~合金而言,含5%~15%(体积分 数)的。t2/y层片组织时延性最好。含量太低,晶粒 容易长大;含量太高,则脆性的a:将削弱细晶显微 组织的韧化作用。
室温延性差和延性随温度提高而增加反映在断 裂方式上。由拉伸和蠕变试验来看,在低温下的变 形模式主要是由位错堆垛造成的解理,而在脆一韧 转变点上主要为沿晶断裂[33·3“。
在脆—韧转变温度以下。双态组织或层片组织 中层片晶团的断裂均为穿晶断裂。a:相在晶团中 起强化作用,位错运动很慢。两相之间位错的传递 很困难,经塑性变形后材料具有很高的相界位错密 度。在脆一韧转变温度以上,延性大幅度提高的原因 可归结为孪生、滑移及攀移的加剧。该温度随着成 分、组织及应变速度可在600--820℃之间变化,断 裂模式由脆性穿晶断裂或沿晶断裂转变为延性韧窝 断裂。在单相y晶粒中,这种转变比在层片晶团中 发生较早,表明层片组分较多的材料脆一韧转变温 度较高“-3j。
113%。
为了获得所需性能,加工态制品、近型成形零
万方数据
第ll卷第4期
彭超群.等:TiA]基合金的工艺—显徽组织一力学性能关系
-529
件及其它制品(如板材和箔材)都必须在适当的条件 下进行热处理。尽管有许多不同种类的后加工热处 理,但可归结为3类,如图1所示【3…。第1类和第 Ⅱ类包含退火及随后的时效处理,第Ⅲ类仅包含时 效处理。具体的热处理温度、时间、加热和冷却速 度及最终性能随各具体合金而定,并根据所需的显 微组织来选择。方案I中对材料通常进行0.5~5 h 高温退火处理,然后以30~150℃/rain的冷却速度 冷至室温,再重新加热.时效4~100 h;在方案Ⅱ 中,材料直接从退火温度炉冷至时效温度,或者把 试样从退火炉转入另一时效炉中。为了获得细小、 均匀的晶粒尺寸,需要采用相对较快的加热速度; 为了避免产生裂纹和把最终相的过饱和度减至最 小,宜采用相对较慢的冷却速度。两步热处理(I 类和Ⅱ类)用于具备非层片组织的热加工材料,第 Ⅲ类热处理用于不要改变加工态组织的情况或者显 微组织十分稳定(例如全层片组织)而不能用时效来 控制的情况。根据原始组织及热处理工艺,可以获 得4种不同类型的Ti~基合金组织,即近y组织、 双态组织、近全层片组织和全层片组织。