梅钢去毛刺机液压系统改造的设计和分析
四辊轧机液压压下装置液压系统设计
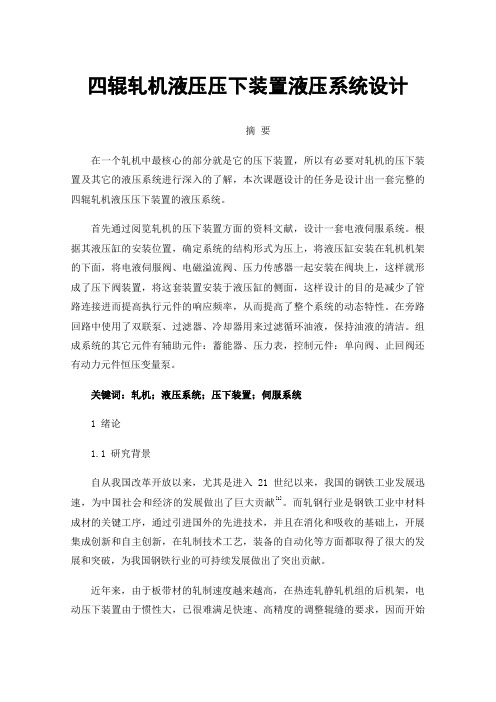
四辊轧机液压压下装置液压系统设计摘要在一个轧机中最核心的部分就是它的压下装置,所以有必要对轧机的压下装置及其它的液压系统进行深入的了解,本次课题设计的任务是设计出一套完整的四辊轧机液压压下装置的液压系统。
首先通过阅览轧机的压下装置方面的资料文献,设计一套电液伺服系统。
根据其液压缸的安装位置,确定系统的结构形式为压上,将液压缸安装在轧机机架的下面,将电液伺服阀、电磁溢流阀、压力传感器一起安装在阀块上,这样就形成了压下阀装置,将这套装置安装于液压缸的侧面,这样设计的目的是减少了管路连接进而提高执行元件的响应频率,从而提高了整个系统的动态特性。
在旁路回路中使用了双联泵、过滤器、冷却器用来过滤循环油液,保持油液的清洁。
组成系统的其它元件有辅助元件:蓄能器、压力表,控制元件:单向阀、止回阀还有动力元件恒压变量泵。
关键词:轧机;液压系统;压下装置;伺服系统1 绪论1.1 研究背景自从我国改革开放以来,尤其是进入21世纪以来,我国的钢铁工业发展迅速,为中国社会和经济的发展做出了巨大贡献[1]。
而轧钢行业是钢铁工业中材料成材的关键工序,通过引进国外的先进技术,并且在消化和吸收的基础上,开展集成创新和自主创新,在轧制技术工艺,装备的自动化等方面都取得了很大的发展和突破,为我国钢铁行业的可持续发展做出了突出贡献。
近年来,由于板带材的轧制速度越来越高,在热连轧静轧机组的后机架,电动压下装置由于惯性大,已很难满足快速、高精度的调整辊缝的要求,因而开始采用电动压下与液压压下相结合的压下方式[2]。
在现代化的冷连轧机组中,几乎已全部采用液压压下装置。
1.3 本课题主要研究内容本课题主要是设计一套四辊轧机压下装置的液压系统,以前冷轧机的压下装置是靠大功率电动机带动牌坊顶部的蜗轮蜗杆和压下螺丝来实现的,自从采用液压技术后,轧制速度提高了10倍以上,精度也大大提高了。
采用液压压下系统的轧机一旦发现误差,能以极短的时间调整辊缝。
所以有必要对轧机液压压下装置进行研究,具体内容如下:(1)首先查阅轧机压下装置液压系统方面的相关资料,了解压下装置的工作原理并对组成压下装置液压系统中的电液伺服阀有一定了解,伺服阀是液压系统中最关键的元件,是液压系统同电气系统的连接元件。
液压机伺服技术改造的实施方案

液压机伺服技术改造实施方案一、需求分析与评估在进行液压机伺服技术改造前,需要深入了解企业的实际需求,如提高生产效率、改善产品质量、降低能耗等。
对现有液压机的工作状况进行全面评估,包括性能、效率、精度、可靠性等方面,找出存在的问题和改进的空间。
根据评估结果,制定改造目标和实施计划。
二、伺服系统选型根据液压机的实际需求和评估结果,选择适合的伺服系统型号。
需要考虑的因素包括:1. 伺服系统的性能参数,如最大输出功率、动态响应、控制精度等;2. 液压机的负载特性和工艺要求;3. 伺服系统的可靠性和稳定性;4. 系统的成本和性价比。
三、旧设备拆除在安装新伺服系统之前,需要对旧设备进行拆除。
需要拆卸的部件包括:液压泵、液压缸、传动装置等。
在拆除过程中,要保证设备的完整性,以便后续的回收和再利用。
同时,要注意安全问题,采取必要的防护措施,确保操作人员的人身安全。
四、新伺服系统安装按照安装说明书的指引,正确安装新伺服系统。
需要安装的部件包括:伺服电机、控制器、传感器等。
在安装过程中,要确保各部件的连接牢固可靠,避免出现松动或脱落的情况。
同时,要注意电气安全和机械安全,确保设备和操作人员的安全。
五、系统调试与测试完成新伺服系统的安装后,需要进行系统调试与测试。
首先进行电气调试,检查线路连接是否正确,各部件的电源是否正常。
然后进行机械调试,调整各部件的安装位置和间隙,确保设备的运动轨迹和精度符合要求。
最后进行性能测试,检查设备的各项性能指标是否达到预期要求。
六、员工培训为了确保操作人员能够熟练掌握新伺服系统的操作和维护技能,需要进行员工培训。
培训内容包括:新伺服系统的基本原理、操作方法、维护保养等方面。
通过培训,使操作人员能够快速适应新设备,提高工作效率。
同时,也要进行安全培训,加强员工的安全意识,避免发生安全事故。
七、运行监控与优化在新伺服系统投入使用后,需要进行运行监控与优化。
通过实时监测设备的运行状态和性能参数,及时发现和处理异常情况。
YQ32-63型液压机液压系统改造及原理分析

YQ32-63型液压机液压系统改造及原理分析摘要:简述YQ32-63型液压机液压系统改造的设计思路及具体方案,并就改造后的液压系统的特性予以分析。
关键词:液压机液压系统原理分析1概述我学院实训室有一台YQ32-63型液压机,操纵方式为手动操纵,采用的柱塞泵由于使用年限较长而磨损老化严重,故障率高,已满足不了正常教学使用。
在保持其机床主体结构基本不变的基础上,对液压机的液压系统进行改造,采用现代泵阀技术,使之重新达到正常使用的标准。
2改造前液压机液压系统情况分析液压机为立式结构,由机身、两柱塞缸、滑块压头和液压动力和控制部分组成。
主油缸和提升油缸都是柱塞缸,为一体式结构,压头和两主油缸为柱塞杆连接,提升缸起导向和同步作用。
压机上部设有充液池,贮存两个主油缸经充液阀排出的大量油液,机身两旁设有两台悬臂吊供吊装之用,实物如图1所示。
图图1 YQ32-63型液压机实物图上图液压机原液压系统中采用了手动随动结构的径向柱塞泵,油泵的排油量和出口方向通过手柄由随动机构来调整,操纵部分由齿轮泵供油,在两个主油缸油路上各连接有充液阀,控制两个柱塞缸与充液阀的连通和断开。
考虑到该液压压机整体结构比较好,油泵站和压机本体可以分离,充液阀结构合理,经过修理还能继续使用,管路布局良好,油缸密封件经过调换后,油缸使用性能良好,所以采用最新泵阀技术和控制技术。
3改造液压系统分析1.系统主元件功能分析二通插装阀具有液阻小,通流能力大,动作快、泄漏少等一系列优点,因此发展较快,目前已在机械、冶金、汽车、船舶等行业得到广泛地运用。
由于二通插装阀可以配置不同的先导控制级,就能实现方向、压力和流量的多种控制,集成度很高;二通插装阀采用锥阀结构,内阻小、响应快、泄漏少,适用于高压大流量。
同滑阀相比,它采用微型结构的先导控制,并可不受限制地接受各种形式的开关、模拟和数字信号的控制并进行包括机械、液压参量的反馈和比较,在同一主级上复合压力、流量和方向诸多功能并和比例数字控制兼容,有极佳的“可控性”。
论钢筋切断机液压系统的设计研究

论钢筋切断机液压系统的设计研究摘要:液压式钢筋切断机是目前使用较为广泛的对钢筋现场加工的机器设备。
这种液压机器的在使用中工作效率高、效果好。
本文对液压钢筋切断机的液压系统设计进行研究,从几个关键方面出发已解决应用中的一些问题。
关键词:发展前景工作有点设计要点一、引言建筑行业的发展推动了相关材料加工技术的发展,钢筋是混凝土结构中必不可少的材料之一。
钢筋加工中的重要环节就是对钢筋的切割环节,因为工程所需的钢筋的尺寸差异很大,所以钢筋切割机械也随着需求的增长而发展起来,目前钢筋切割机的主要形式有两种,一种是机械式切割机,一种是液压式切割机,机械式的切割机主要是利用凸轮的运动来切割钢筋,液压式切割机主要是利用液压系统为机器提供动力进行工作。
这两种切割机比较而言,液压式切割机优势较为明显,性能稳定、噪音小、方便移动等,这些给液压切割机的广泛应用创造了条件。
目前的液压切割机已经客服了过去液压切割机的一些缺点,剪切率、速度、误差等方面的性能都有了大幅提高了,但是在高速液压式切割机的使用过程中还会出现“闷车”现象,这种现象使得钢筋和切头都会受到损伤,究其原因主要是液压系统设计中的一些问题造成的影响,如何控制高压流体的压力、流量、流向等问题是高速切割过程中需要平衡的问题,所以技术人员也正在利用先进的技术逐步改进钢筋切割机的液压系统。
二、液压钢筋切断机的发展要求从目前的应用看,我国建筑工程中的钢筋需要主要分为两种,一种是精读需要高的工程,主要是满足预应力混凝土的生产。
另一种是精读要求不高的工程,这样的工程对于机械的可靠性要求占主导,需要保证在钢筋加工中的高效率,即少停机多生产。
前一种的钢筋加工需求主要由锤击式、机械定尺的钢筋调直切割机完成加工。
后一种客户的需求就需要利用液压式切断机机构简单、可靠的性能,缩短其剪切时间,提高生产效率是未来钢筋调直切断机械的发展方向。
另外,国内目前的调直切割机剪切的时间受到一定的限制,在这时间内要完成调直和剪切两项工作,所以在工作中速度受到了一定的影响,所以提高切割机的速度将成为另一个切割机发展的方向。
4MN油压机液压系统改造

利用激 振器给板件施 加持续 的激励信号 ,在线调
整控制参数 ,对板件 的振动进行主动控制 ,压 电传感
器可 以测量到控制前后振动 的典 型时域波形如 图4所
不 。
参 考文 献 :
【】章卫 国, 向忠. 1 杨 模糊控 制理论 与应用 [ . M] 西安 : 西北
工 业 大 学 出版 社 ,9 9 19 .
E —m al ly a hu @ wu t d .c i : iu n i s.e u n。
第1 0期
邢峰 等 :模糊 PD控制仿 真与实验研究 I
・1 9 ・ 4
约 3 % ,板件 振动 明显 减弱 。证 明所 建立 的控 制 系 0 统 ,对 于时变 、不确定 的持续激振 ,仍然可以达到很
2 液压 系统 改进
原液压系统 的工作原理 图如图 1 所示 。系统要完
成的主要功能是 :油缸 活塞 快速下 降 ( 快进 ) ;油缸 活塞慢 速下降 ( 工进 ) ,即开始压制工 件 ;油缸活塞 停止动作 ,处 于压制工件 的保压状态 ;油缸活塞快速
上升 。根据该油压机压制工件的工 序要求 ,对液压系
21 0 2年 5月 第4 0卷 第 1 0期
机床与液压
MACHI NE TOOL & HYDRAULI CS
M a 01 v2 2 Vo . 0 No 0 1 4 .1
D :1 . 9 9 jis. 0 1—3 8 . 0 2 1 . 5 OI 0 3 6 /.sn 10 8 12 1.0 0 2
【】韦巍. 2 智能控制技术[ 张恩勤, 施颂椒. 一类基于 PD控制的新型模糊控制方 I
法 [ ] 上海交通大学学报 ,0 0 3 ( ) 60— 3 . J. 20 ,4 5 :3 64
液压与气动系统的改造

上一页 下一页 返回
6.2 气动系统的改造
6.2.3参考方案
1.故障现象分析 (1)框架在升降过程中动作缓慢或不动作。造成这个问题的
直接原因就是气动比例阀动作失灵。气动比例阀内安装的模 板和其他电器元件发生故障,或者气动比例阀内的控制气路 通气不畅,则气动比例阀就不能按照PLC的要求对有杆腔的 压力进行调节,而无杠腔进气由2YA控制继续充压,有杆腔 的背压不断增高,当背压不能及时从比例阀释放时,就会出 现升降框架下降速度慢,甚至不动的现象。 (2)气动比例阀故障频繁、使用寿命短。为了保证在气动比 例阀的响应速度,系统的控制阀箱装在了火焰切割机上靠近 气缸的位置。
开裂现象也大为减少。其合格率大大提高。通过调节压制速 度可以实现更多品种的工件压制和拉延工艺的要求。系统压 力稳定性改善了很多,压力调节精度比改造前提高了很多。 这次改造是在原系统的基础上进行的,尽量利用原有元件, 花费少、周期短、效果好。
上一页
返回
6.2 气动系统的改造
6.2.1板坯二次火焰切割机气动系统的改 造
时的冲击。 2.参考改造方案 (1)将气缸有杆腔进气的减压阀改为节流阀。 (2)将气缸无杆腔进气的气动比例阀改为减压阀。 (3)不改变PLC的控制程序,将有杆腔排气控制阀的控制线
连铸出坯系统改造液压设计1

方坯连铸出坯系统液压改造朱绪征皇埔雅志(安阳钢铁集团有限责任公司)摘要本文介绍了安钢第一炼轧厂连铸出坯系统改造中液压部分的设计,根据各部位不同的情况,做了相应的改进和设计,并利用了原有液压站。
以最少的投资,获得较好的效益。
关键词液压系统液压缸流量REDESIGN HYDRALIC SYSTEM ON RECONSTRUCTION OF CONTIUOUS CASTINGZHU XUZHENG WANG RONGHUI(Anyang Iron & Steel Group Co.,Ltd)SUMMARY This article mainly introduces the rebuild of hydraulic system on reconstruction of continuous casting machine. It gives out the hydraulic system design through the change of rebuild technology, it uses the capacity of the original hydraulic station completely, calculates out the total flux ,and meets the requirement. This design can save investment and bring good effect indeed.KEY WORD hydraulic system hydraulic cylinder flux安阳钢铁公司第一炼轧厂原有100吨电炉一台,方坯连铸和板坯连铸机各一套。
根据安钢发展需要,新增100吨转炉一台及附属设备,为适应扩大规模后的生产(100万吨/年的生产规模),需对连铸系统进行改造。
改造的重点是方坯连铸机出坯系统,包括六流辊道延长,增加一部快速横移冷床,供热送,增加活动升降挡板,改造翻转冷床、翻钢机等等。
连铸板坯去毛刺机的使用及优化

18囱魁科技2020年•第10期直藩扳毘工壬删肌前随田Utt化◊马钢股份公司第四钢轧总厂徐伟■本文介绍了锯齿型去毛刺机的工艺特点,基本机构和工作原理,以及使用过程中的优化情况。
铸机生产过程中,成型后定尺切割时由于割缝处切割氧的吹扫,大量氧化铁和金属夹杂物流动至板坯割缝底部的两侧,冷却成型后运输时被辐道压实成为块状钢渣。
这些毛刺的硬度往往比较大,如果不能及时有效地去除,在后续的轧制工艺中极有可能会形成钢板的表面缺陷,造成质量事故。
降低公司效益,影响品牌打造。
因此,去毛刺机的去毛刺效率成为影响板坯表面质量的重要因素,如何快速,完全的将板坯的毛刺去除,保证铸坯表面质量是连铸工艺中一直在研究的课题。
马钢四钢轧3#连铸生产线通过技术改造,上线了辽宁某公司设计制造的锯齿形毛刺机,相比之前使用的锤刀式毛刺机和圆盘刮刀式毛刺机,该毛刺机设计简单,不需要频繁补充锤刀,维护成本低,同时刀座设计合理,不会因工况条件影响导致活塞杆无法弹起造成缺齿,出现不能完全去除条状毛刺的情况。
1去毛刺机的基本结构锯齿形板坯去毛刺机由主机、液压系统、电气控制系统、細系统和毛刺濟軽等组成。
图1锯齿形去毛刺机结构图活动机体采用箱式结构,整体密闭,水冷却,通过连杆与液压马达连接,在液压马达驱动下,带动锯齿形刮刀在横梁箱体内横向往复运动,为锯齿形刮刀提供横向锯切力。
两侧箱体底部有提升油缸,主机瓦座上有翻转油缸,由活塞油缸传动齿条带动横梁箱体旋转90。
,起到清除残留在刮刀上毛刺和氧化皮的作用。
电气控制系统主要包括PLC可编程控制柜、远程操作HMI、本地操作箱、终端接线箱、去毛刺设备位置检测接近开关及板坯运动位置检测光电开关等,其作用是完成对毛刺机的手动和自动运行控制。
冷却系统主要包括各种冷却水配管、阀、接头等,冷却方式为内循环开路水冷却,其功能是为整机进行冷却。
毛刺收集装置利用原有毛刺收集斗,其作用是去除的毛刺通过收集斗收集后,由吊车将收集斗吊离排渣沟对去除的毛刺进行集中处理。
- 1、下载文档前请自行甄别文档内容的完整性,平台不提供额外的编辑、内容补充、找答案等附加服务。
- 2、"仅部分预览"的文档,不可在线预览部分如存在完整性等问题,可反馈申请退款(可完整预览的文档不适用该条件!)。
- 3、如文档侵犯您的权益,请联系客服反馈,我们会尽快为您处理(人工客服工作时间:9:00-18:30)。
2011年第1期 梅山科技 ・49・ 梅钢去毛刺机液压系统改造的设计和分析 李艳 (梅山钢铁公司炼钢厂 南京210039)
摘要:通过对梅钢2号连铸机原气动去毛刺系统的故障分析,根据现场条件以及对液压 系统的计算,得出增加去毛刺机液压系统的可行性改造方案,最优化地实现了项目改造。 关键词:去毛刺机;流量;绝热状态
Design and Analysis of Hydraulic System Reconstruction of Deburring Machine at Meigang
y0n (Steelmaking Plant of Meishan Iron&Steel Co.,Nanjing 210039) Key words:deburring machine;flow rate;thermal insulation state
在梅钢炼钢厂2号连铸机2流项目建设中, 其去毛刺机采用了气动刮板式结构,自项目投产 以来,该设备使用效果良好,但故障较多,存在气 动阀件及气缸损坏频繁等问题,导致板坯的去毛 刺率达不到生产需要,不能符合板坯质量标准,一 定程度上影响了热轧板厂和冷轧厂的设备及生产 质量,进而影响了生产节奏。 1 设备改造的可行性分析 在现场应用过程中,2号连铸机2流去毛刺 机去毛刺效果良好,毛刺去除比较干净,但相对1 流去毛刺机(锤刀式)存在较多故障,经常出现阀 件及气缸损坏频繁等问题,导致去毛刺率无法提 高,不能达到制造部的板坯质量标准。考虑到热 轧板厂和冷轧厂对板坯质量有严格的要求,板坯 如果有毛刺,一定程度上会影响热轧板厂和冷轧 厂的设备及生产质量,进而影响生产节奏,所以现 拟对2流去毛刺机进行改造。 1.1 刮板式去毛刺机工作原理 去毛刺机的刀片是长条形,两面有刃,以便去 除铸坯两端的毛刺。1台去毛刺机用两把刮刀覆 盖铸坯最大宽度。为减小切削阻力,刮刀与铸坯的 宽度方向成4。~6。的夹角,两把刮刀互相平行,每 把刮刀的两端分别支撑在1组碟形弹簧上,保证两 端都能紧压铸坯表面。当铸坯到达去毛刺工位时 停止运动,去毛刺机处于待机位置,升降气缸将铸 坯压紧在去毛刺辊道上,升降气缸将刀台升起,刀 片的刃面紧压在铸坯下表面上,其压紧力的大小取 决于弹簧的压紧力。刀架升降依靠导板为其导向, 之后横移气缸推动横移机构在轨道上行走,带动横 移机构上的所有机构运动进行去毛刺作业。因为 铸坯宽度为900~1 350 lq,lm,故在铸坯的两侧各有 1套去毛刺机构,在推动刀架去毛刺时依靠齿轮一 齿条机构使2套机构强制同步,刀具平移进行去毛 刺作业,毛刺去除后刀台下降退回到待机位置,前 端去毛刺以后再去除后端的毛刺,刮刀去毛刺时的 移动方向总是从铸坯里面向着切割端面。 1.2锤刀式去毛刺机工作原理 锤刀式去毛刺机的机构见图1。在去毛刺辊 全长上车出圆盘,圆盘上沿圆周方向钻8个通孔, 穿装8根长销,长销上悬挂锤刀。去毛刺辊的轴 承座由油缸带动升降,其滑动导轨在机架的滑动 导板上滑动,轴承座的升降位置由接近开关来调 整和限制。去毛刺过程的控制信号来自光电开 关。铸坯前端到达去毛刺机第1位置时去毛刺辊 启动,沿铸坯前进方向转动,到达去毛刺机第2位 置时(光电开关控制)液压缸动作,将去毛刺辊升 起到限定位置,飞转的锤刀依靠动能将毛刺打掉, 之后去毛刺辊回到待机状态。待铸坯后端到达去 毛刺机第1位置时去毛刺辊启动,逆铸坯前进方 ・50・ 梅山科技 2011年第1期 向转动,到达去毛刺机第2位置时液压缸动作,将 去毛刺辊升起到限定位置,飞转的锤刀依靠动能 将毛刺打掉,去毛刺机回到待机状态。 【 } 。 铸坯 。 锤 图1锤刀式去毛刺机机构简图 1.3两种去毛刺机使用对比 通过对两个流的去毛刺机使用对比发现:刮 刀式去毛刺机靠碟形弹簧,将长度为1 200 mrll左 右的刀片压紧在铸坯下表面上,当铸坯表面有鼓 肚或突起时,凹处就会有一部分毛刺不能去除,刀 片的进退是机械强制进行的,所以刀片在去毛刺 过程中,难以保持调整好的切削状态,而且其毛刺 机结构显得复杂,刀片及刀架、刀架升降机构、横 移机构、齿轮及齿条同步机构、去毛刺辊道的安装 以及相应的气压回路,都必须精心调整才能达到良 好的去毛刺工况,8个气缸必须全部保持良好的状 态,任何1个气缸损坏,都将使去毛刺机无法完成 正常的动作,由于去毛刺的时候每个气缸要动作4 次,频繁的压力冲击使得气缸的密封圈很容易损 坏,气缸一旦漏气将影响去毛刺机的功能。而锤刀 式去毛刺机的传动系统属于常规机械传动设备,除 油缸的升降速度要求较快外没有特别的调整要求。 设备的功能和精度都很容易达到使用要求,维护也 很方便。目前2号连铸机1流的去毛刺机设备运 行正常,毛刺的去除率在98%以上,满足了生产和 设备维护的要求。根据以上分析以及梅钢自身的 工艺和设备特性,锤刀式去毛刺机更加适合该铸机 的工况,最终决定对2号连铸机2流气动去毛刺系 统实施现场改造。 2去毛刺机的液压系统改造 根据梅钢炼钢厂现场的既有条件,目前就近 有1套切割辊道液压站,用于控制2号连铸机1 流的切割摆动辊道液压缸、去毛刺机液压缸和2 流的切割摆动辊道液压缸。为节约项目改造费 用,避免增加原铸机液压站的数量和相关电气装 机容量,拟利用该泵站作为泵源,新增1个控制阀 台以实现改造设备的液压缸控制。以下为对现有 利旧系统的能力核算和改进以及新增控制系统的 设计。 2.1 既有液压系统泵源能力的核算 现有切割辊道液压系统控制2流共10个切 割油缸,以实现切割辊道的上升和下降。主要技 术参数如下:切割油缸型号03125 ram/70 lqclm× 400 mm,速度要求为0.1 rrt/s,切割辊道重10 t。 油缸在摆上时有杆腔进油,摆下时(靠自重)无杆 腔进油,则切割油缸运动所需最大流量可通过以 下步骤得出。 辊道下降时流量为: Q下降=3.14 X 0.125 ×0.1 X 60×1 000/4 =74 L/rain 辊道上升时,切割油缸动作所需的最低压 力为: P切割油缸=F/A=10 X 10 X 9.8×4/7r(0.125
一0.07 )=11.63 MPa 此时切割油缸的流量为: Q 升=3.14×(0.125 一0.07 )X 0.1 X 60× l 000/4=50.5 L/rain 由于Q下降>Q上升,因此Q…取74 L/min,切割 油缸运动所需最大流量为74 L/min。 改造实施后,每流去毛刺液压系统由2个去 毛刺油缸控制去毛刺辊道的上升和下降。主要技 术参数如下:去毛刺机油缸型号0380 mm/45 mm ×100 mm,速度要求为0.1m/s,去毛刺辊道重约 2 t。 去毛刺油缸运动所需最大流量为: Q去毛刺油缸=3.14 X0.08 ×0.1 X 60 X 1 000/4 =30 L/min, 去毛刺油缸动作所需的最低压力为: P去毛刺油缸=F/A=2×10 X 9.8 X 4/7r(0.08 一0.045。)=5.7 MPa。 切后辊道液压系统主泵使用的是恒压变量柱 塞泵,1用1备,型号为A10V071DR/31RP.PA 12N00,额定压力为280 bar,排量v…=71 em , 李艳梅钢去毛刺机液压系统改造的设计和分析 ・51. 电机为三相异步电机,型号为Y225M一4 B35,转 速1 450 r/min。 泵的流量为:Q=71×1 450/1 000=102.95 L/min。考虑到会有去毛刺机和切割辊道同时动 作的情况,泵的流量小于油缸的总流量Q 缸.= 74+30×2=134 L/rain或Q总油缸2=74+74=148 L/rain。所以2流切割辊道和去毛刺系统增加了 蓄能器组。其液压系统简图见图2。 1流去毛刺阀台l l 1流切割辊道 2流去毛刺阀台(新增)I l 2流切割辊道 切后辊道液压站 l流切割阀台 2流切割阀台 新增去毛刺蓄能器组 减压阀型号为ZDRK 10 VP5一IO/210YMV,控制 阀采用叠加板式连接。 2)蓄能器的选择皮囊式蓄能器(见图4)的 特点是气体与油隔离,油不易氧化,尺寸小,重量 轻,反应灵敏,充气方便。其工作示意图见图5。
图2 液压系统简图 图4皮囊式蓄能器结构图 初步拟定2流去毛刺系统的液压原理图见
图3。
图3 2流去毛刺系统的液压原理图 2.2改造控制系统的设计 1)液压控制阀的选择根据液压控制阀所 在油路的工作压力和通过该阀的最大流量来确定 阀的规格型号。通过以上计算,去毛刺机油缸动 作的工作压力为5.7 MPa,流量为30 L/min。对 照样本选型,电磁换向阀型号为4WE10D3X/ CG24N9K4,节流阀型号为Z2FS10—5—3X/315,
P0 充 气 压 力
预压充气时 蓄压充气时 压力油放出时 图5 皮囊式蓄能器工作示意图 根据玻义耳气体定律的工作原理,蓄能器的 容量可用公式(1)计算得出 : 1 1 1 1 I =△V/P。÷[( 1)i一(寺) ] (1)
2 式(1)中:n为状态指数(等温状态n=1,绝热状
态n=1.4),一般来说,蓄能器压力的释放可以看 为绝热状态;P。为蓄能器注油前充气压力;Vo为 压力为 时的气室容积;尸 为使用蓄能器所需 维持的最低工作压力;P 为系统的最高工作压 力;△V:V。一 ,V。为最低压力下的气体体积; 为最高压力下的气体体积。 蓄能器皮囊的充气压力也应根据不同的使用 情况来确定,用作辅助动力源时,P。一般按P 的