基于PLC的自动化生产线控制系统软件设计
基于PLC的饮料自动罐装系统毕业设计

基于P L C的饮料自动罐装系统毕业设计The Standardization Office was revised on the afternoon of December 13, 2020毕业设计(论文)题目:自动化生产线中的饮料灌装系统——软件设计学生姓名:学号:专业:班级:指导教师:年月日河北工程大学毕业设计(论文)任务书题目:自动化生产线中的饮料灌装系统——软件设计学生姓名:学号:专业班级:学院:设计起止日期:题目性质一:实际工程目科理论研其他题目性质二:真题模目其他技术要求及原始数据:系统基于PLC-200,主要功能完成饮料灌装生产过程,明确装瓶,传送,盖盖,检测过程,并可以启动,移位,复位按钮进行操作,实现手动,自动全过程。
主要任务: 1、绘制工作流程图或顺序功能图;2、编写全程序T型图或指令表;3、运用程序进行调试;4、编写设计说明书;学生(签字):系主任(签字):指导教师(签字):院长(签字):河北工程大学毕业设计(论文)评语学生姓名专业班级毕业设计(论文)题目自动化生产线中的饮料灌装系统——软件设计1、指导老师评语:指导教师(签字)年月日2、评阅人评语:评阅人(签字)年月日3、答辩组评语:答辩组组长(签字)年月日摘要随着工业自动化水平日益提高,众多工业企业均面临着传统生产线的改造和重新设计问题。
PLC(可编程序控制器)是以微处理器为核心的工业控制装置,它将传统的继电器控制系统与计算机技术结合在一起,近年来在工业自动控制、机电一体化、改造传统产业等方面得到普遍应用。
作为通用工业控制计算机,其实现了工业控制领域接线逻辑到存储逻辑的飞跃,在世界工业控制中发挥着越来越重要的作用。
在饮料行业,自动化生产线的生产方式是推广的最普及的一种生产模式,它促使灌装的速度大幅提升,同时也使得灌装精度更高,给企业带来了不可小觑的生产力。
鉴于此,设计者利用PLC的功能和特点设计出了一款饮料灌装生产流水线控制系统。
毕业设计基于PLC的生产流水线监控系统设计
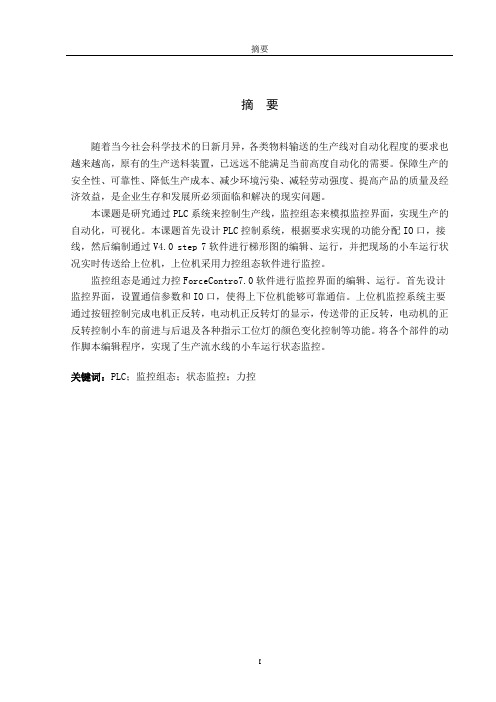
摘要随着当今社会科学技术的日新月异,各类物料输送的生产线对自动化程度的要求也越来越高,原有的生产送料装置,已远远不能满足当前高度自动化的需要。
保障生产的安全性、可靠性、降低生产成本、减少环境污染、减轻劳动强度、提高产品的质量及经济效益,是企业生存和发展所必须面临和解决的现实问题。
本课题是研究通过PLC系统来控制生产线,监控组态来模拟监控界面,实现生产的自动化,可视化。
本课题首先设计PLC控制系统,根据要求实现的功能分配IO口,接线,然后编制通过V4.0 step 7软件进行梯形图的编辑、运行,并把现场的小车运行状况实时传送给上位机,上位机采用力控组态软件进行监控。
监控组态是通过力控ForceContro7.0软件进行监控界面的编辑、运行。
首先设计监控界面,设置通信参数和IO口,使得上下位机能够可靠通信。
上位机监控系统主要通过按钮控制完成电机正反转,电动机正反转灯的显示,传送带的正反转,电动机的正反转控制小车的前进与后退及各种指示工位灯的颜色变化控制等功能。
将各个部件的动作脚本编辑程序,实现了生产流水线的小车运行状态监控。
关键词:PLC;监控组态;状态监控;力控AbstractThis topic is the study of the PLC system to control production lines, monitoring configuration to simulate the monitoring interface, production automation, visualization.Monitoring configuration is controlled through the power of software to monitor interface ForceControl7.0 edit, run. Power Control Power Control 6.0 ForceControl7.0 in adhering to proven technology, based on the historical database, HMI, I / O driver scheduling and other major core improvements were significantly improved with redesigned one of the core components.Through PLC software ladder editor, run. editing software for Siemens series of industrial products including SIMATIC S7, and -based programming, monitoring and parameter setting, SIMATIC industrial software is an important part. has the following features: hardware configuration and parameter setting, communication configuration, programming, testing, start-up and maintenance, document filing, operation and diagnostics functions. have all the features extensive online help, use the mouse to open or select an object, press F1 to get help for the object.With the rapid changes in science and technology in society today, various types of material handling automation production line of the increasingly high demand, the original production of feeding device, can not meet the current needs of a high degree of automation. Protect the production of security, reliability, lower production costs, reduce environmental pollution, reduce labor intensity and improve product quality and economic benefits, is the enterprise survival and development must face and solve reality.Keys word:PLC;configuration;step;Forcecontrol目录摘要 (I)Abstract ............................................................................................................................. I I1绪论 (1)1.1设计的意义和目的 (1)1.2课题的发展状况 (1)1.3课题需要完成的主要任务 (2)2 PLC的控制系统设计 (3)2.1总体结构图 (3)2.2 PLC软件概述 (3)3力控组态监控设计 (5)3.1力控软件的总体介绍 (5)3.1.1 力控的介绍 (5)3.1.2力控的产品发展史 (6)3.1.3数据文件及应用目录说明 (6)3.1.4力控软件的安装 (6)3.1.5力控软件的基本结构 (8)3.2工程管理器 (9)3.2.1工程管理器的建立 (9)3.2.2建立工程组态画面 (12)3.3 I/O设备 (14)3.3.1I/O设备的介绍 (14)3.3.2I/O设备的步骤 (14)3.4 组态动画 (16)3.4.1组态动画的组建 (16)3.4.2力控的对象类型 (17)3.4.3动画连接的类型 (17)3.4.4动画连接的使用 (18)3.4.5设置变量 (20)4系统运行测试 (21)4.1正转运行 (21)4.2反转运行 (27)4.3移位运行 (28)4.4单周期运行 (29)4.5复位运行 (36)总结 (38)致谢 (39)参考文献 (40)附录 (41)1绪论1.1设计的意义和目的基于PLC控制生产流水线可以减少人员的数量,操作简单,省时省力。
基于PLC的装配流水线控制系统设计
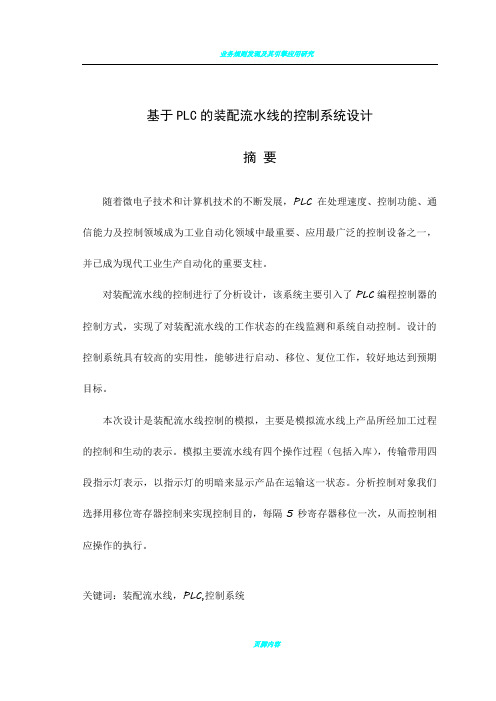
基于PLC的装配流水线的控制系统设计摘要随着微电子技术和计算机技术的不断发展,PLC在处理速度、控制功能、通信能力及控制领域成为工业自动化领域中最重要、应用最广泛的控制设备之一,并已成为现代工业生产自动化的重要支柱。
对装配流水线的控制进行了分析设计,该系统主要引入了PLC编程控制器的控制方式,实现了对装配流水线的工作状态的在线监测和系统自动控制。
设计的控制系统具有较高的实用性,能够进行启动、移位、复位工作,较好地达到预期目标。
本次设计是装配流水线控制的模拟,主要是模拟流水线上产品所经加工过程的控制和生动的表示。
模拟主要流水线有四个操作过程(包括入库),传输带用四段指示灯表示,以指示灯的明暗来显示产品在运输这一状态。
分析控制对象我们选择用移位寄存器控制来实现控制目的,每隔5秒寄存器移位一次,从而控制相应操作的执行。
关键词:装配流水线,PLC,控制系统DESIGN OF CONTROL SYSTEM OF ASSEMBLY LINEBASED ON PLCABSTRACTWith the development of the microelectronics technology and computer technology, PLC in processing speed, control function, communication ability and control fields have new breakthrough. Become one of the most important control equipment in the field of industrial automation, the most widely used, and has become an important pillar of the modern industrial production automation.Control of the assembly line are analyzed and designed, the system is mainly introduced PLC control programming controller, realized the on-line monitoring system of assembly line and the working state of automatic control. Practical design of the control system has high, can start, shift work, reset, can reach the expected goal.The design is simulated assembly line controle, simulation is the main line of products through the control of process and the vivid representation.Simulation of main line is four operations (including storage), transmission belt with four indicates, to display the products in the transportation of this state to light shade. Analysis of the control object we choose to use the shift register control to achieve the control objective, every 5 seconds of shift register once, so as to control the corresponding operations.KEY WORDS: assembling line, plc, the control system目录前言 (1)第1章绪论 (3)1.1 课题研究的背景 (3)1.2 课题研究的现状 (3)1.2.1 可编程控制器简介 (3)1.2.2 装配流水线简介 (6)1.3 课题研究的目的和意义 (8)1.4 方案设计与介绍 (10)第2章可编程控制器 (13)2.1 PLC的基本结构和各部分的作用 (13)2.2 PLC的工作原理 (15)2.2.1 输入刷新阶段 (15)2.2.2 程序执行阶段 (15)2.2.3 输出刷新阶段 (15)第3章硬件设计 (17)3.1 整体要求 (17)3.2 PLC机型选择 (18)3.2.1 S7-200 PLC特性 (18)3.2.2 S7-200主要功能模块介绍 (19)3.3 I/O接线图及地址分配 (20)3.4 主电路的设计 (22)第4章软件设计 (24)4.1 软件的组成及作用 (24)4.1.1 软件的分类 (24)4.1.2 应用软件的编辑语言 (24)4.2 工作流程图 (25)4.3 梯形图 (27)结论 (35)谢辞 (36)参考文献 (37)附录 (39)前言本设计的目的是通过对装配流水线的PLC控制设计,进一步熟悉PLC 的概念、特点和控制原理。
基于自动供料系统顺序控制的PLC程序设计

输入地址输出输出顶料到位开关顶料复位开关推料到位开关I0.0I0.1I0.2顶料推料Q0.0Q0.1表1I/O地址分配表图1自动供料系统结构图将初始步预置为活动步。
根据以上分析,绘制顺序功根据顺序功能图,利用SCR指令的方法[6]编写该控制的梯形图程序,如图4所示。
在SCR段中用的常开触点驱动该步中为ON的输出点的线圈,利用转换条件对应的触点(或者电路)来驱动转换到后续步图3顺序功能图程序调试该控制过程的软件设计以及硬件连接完成后,查程序是否有误,各执行机构动作是否发生冲突。
检查无误后下载运行程序。
经过实验表明,程序编写无误,可以满足控制要求。
进行自动供料系统的程序设计,程序设计方法简单易被接受,易于掌握,不仅避免了传统的继电器控制电路设计中对设计人员经验要求高的问题,的稳定性和控制过程的可靠性也得到显著提高。
应用于实际生产,提高工作效率。
参考文献:[1]覃娟.基于PLC和MCGS的自动供料单元控制系统设计[J].装备制造技术,2016(2):119-122.[2]于成龙.基于PLC控制的高炉自动化上料系统的应用与分析[J].自动化应用,2020,3:27-29.[3]祁伟.PLC技术视角下锰铁高炉自动上料控制系统研究[J].工业加热,2019,48(9):33-36.[4]王晓燕.基于PLC的液晶玻璃基板自动上料控制系统[J].兵器装备工程学报,2019,2:33-36.[5]戴冠秀,刘太湖,巩敦卫,等.PLC在运料小车自动控制系统中的应用[J].工矿自动化,2005(6):57-59.图2PLC外部接线图图4梯形图程序。
基于PLC的自动化烘焙设备控制系统毕业设计

基于PLC的自动化烘焙设备控制系统毕业设计1. 项目背景随着现代社会生活节奏的加快,自动化技术在食品工业中的应用日益广泛。
烘焙行业作为食品工业的重要组成部分,对生产效率和产品质量的要求越来越高。
为满足这一需求,利用可编程逻辑控制器(Programmable Logic Controller,PLC)设计一套自动化烘焙设备控制系统成为必然趋势。
2. 系统概述本设计旨在实现自动化烘焙设备的控制,通过PLC作为控制核心,结合传感器、执行机构及相关控制软件,实现对烘焙过程的自动化控制。
主要包括原料投料、和面、分割、烘焙、冷却和包装等环节。
3. 系统设计3.1 硬件设计- PLC选型:选用某品牌可编程逻辑控制器作为控制核心,具备足够的输入输出点,满足系统需求。
PLC选型:选用某品牌可编程逻辑控制器作为控制核心,具备足够的输入输出点,满足系统需求。
- 传感器:包括温度传感器、压力传感器、光电传感器等,用于实时监测烘焙过程的各项参数。
传感器:包括温度传感器、压力传感器、光电传感器等,用于实时监测烘焙过程的各项参数。
- 执行机构:包括电机、气缸、电磁阀等,用于实现具体的控制动作。
执行机构:包括电机、气缸、电磁阀等,用于实现具体的控制动作。
- 人机界面:选用触摸屏作为操作界面,便于操作人员监控和控制设备。
人机界面:选用触摸屏作为操作界面,便于操作人员监控和控制设备。
3.2 软件设计- 控制程序:采用梯形图编程,实现对各执行机构的控制逻辑。
控制程序:采用梯形图编程,实现对各执行机构的控制逻辑。
- 监控软件:开发上位机监控软件,实现对烘焙过程的实时监控和数据记录。
监控软件:开发上位机监控软件,实现对烘焙过程的实时监控和数据记录。
4. 系统实现4.1 控制逻辑详细描述PLC控制程序的梯形图,包括启动、停止、故障处理等逻辑。
4.2 系统调试对系统进行分模块调试,确保各环节控制功能的正确实现。
5. 系统测试对完成的自动化烘焙设备控制系统进行全面测试,包括功能测试、性能测试和安全测试,确保系统稳定可靠。
基于plc的自控成型机控制系统设计

基于plc的自控成型机控制系统设计1. 引言自动化技术的发展使得工业生产过程更加高效和可靠。
自控成型机作为一种重要的生产设备,在制造业中得到广泛应用。
基于PLC的自控成型机控制系统设计是一种常见的解决方案,它能够实现对成型机的精确控制和监测。
本文将对基于PLC的自控成型机控制系统设计进行深入研究,以期为工程实践提供参考和指导。
2. 成型机工作原理成型机是一种用于将原材料加工成所需形状的设备。
它通常包括供料系统、加热系统、冷却系统和模具等组件。
在工作过程中,原材料通过供料系统进入模具中,在加热和冷却过程中完成形状变化,并最终通过出料系统排出。
3. 基于PLC的自控成型机控制系统设计要求基于PLC的自控成型机控制系统设计需要满足以下要求:3.1 精确可靠性:能够精确地对成型过程进行监测和调节,以保证最终产品质量。
3.2 灵活性:能够适应不同形状和尺寸的产品加工需求,具备一定的可扩展性和可调节性。
3.3 安全性:能够实现对成型机各个部件的安全监控和控制,防止意外事故的发生。
3.4 可视化:能够实现对成型机工作状态和参数的实时监测和显示,方便操作人员进行调试和维护。
4. 基于PLC的自控成型机控制系统设计方案4.1 PLC选择:根据成型机的工作需求和控制要求选择合适的PLC型号。
常见的PLC品牌有西门子、施耐德等,根据具体情况选择合适品牌与型号。
4.2 硬件设计:根据成型机结构和工作原理设计硬件电路,包括供电系统、传感器接口、执行器接口等。
确保硬件电路与PLC之间能够正常通信,并保证信号传输稳定可靠。
4.3 软件设计:根据成型机工作流程编写PLC程序。
程序应包括供料系统、加热系统、冷却系统等各个部分的控制逻辑,并考虑安全监测与故障处理等功能。
编写人员应熟悉PLC编程语言和相应的开发环境。
4.4 人机界面设计:设计成型机的人机界面,包括触摸屏、按钮等操作界面,以方便操作人员进行设备的监控和控制。
界面应具备直观、简洁、易操作等特点,提供实时监测和报警功能。
基于PLC的食品加工设备控制系统设计-控制方案
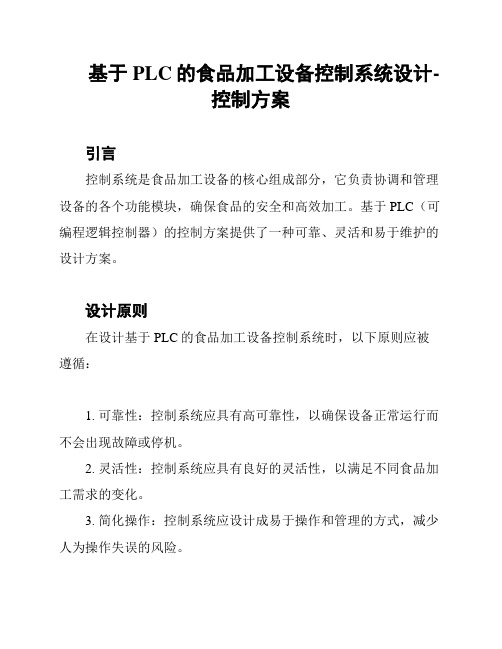
基于PLC的食品加工设备控制系统设计-控制方案引言控制系统是食品加工设备的核心组成部分,它负责协调和管理设备的各个功能模块,确保食品的安全和高效加工。
基于PLC(可编程逻辑控制器)的控制方案提供了一种可靠、灵活和易于维护的设计方案。
设计原则在设计基于PLC的食品加工设备控制系统时,以下原则应被遵循:1. 可靠性:控制系统应具有高可靠性,以确保设备正常运行而不会出现故障或停机。
2. 灵活性:控制系统应具有良好的灵活性,以满足不同食品加工需求的变化。
3. 简化操作:控制系统应设计成易于操作和管理的方式,减少人为操作失误的风险。
4. 安全性:控制系统应具备完善的安全机制,以保障操作人员和食品安全。
控制方案设计基于上述原则,以下是一个基本的基于PLC的食品加工设备控制系统设计方案:1. 输入模块1.1 传感器模块:安装适当的传感器来检测食品加工设备的状态,如温度、压力、液位等。
2. 输出模块2.1 执行器模块:控制执行器(如马达、阀门等)来控制设备的运行状态和工作参数。
3. PLC控制逻辑3.1 状态监测与控制:PLC通过读取传感器模块的数据,监测设备状态,并根据预设的逻辑和算法进行控制。
3.2 软件编程:使用适当的PLC编程语言,编写控制逻辑和算法,以实现设备的自动化运行,并根据需要进行调整。
4. 人机界面4.1 触摸屏界面:为操作人员提供直观的操作界面,以便监控设备状态、更改参数和报警信息。
4.2 警报系统:当设备发生异常情况时,通过警报系统及时通知操作人员,以便采取必要的措施。
总结基于PLC的食品加工设备控制系统设计方案是一个可靠、灵活和易于操作的方案,它可以满足食品加工设备的各种需求,并提供高效和安全的加工过程。
通过合理的输入、输出模块设计和PLC 编程,我们可以实现设备的自动化运行和远程监控,提高生产效率和质量。
同时,适当的人机界面和警报系统可以帮助操作人员及时发现并处理异常情况,保障食品加工的安全性和稳定性。
毕业论文基于PLC的车间生产流水线运输控制设计

毕业设计说明书(论文) 基于PLC的车间生产流水线产品运输控制毕业设计说明书(论文)中文摘要毕业设计说明书(论文)外文摘要1 绪论1.1 课题的背景和意义当前企业现代化生产规模不断扩大和深化,使得生产物的输送成为生产物流系统中的一个重要环节。
车间生产流水线产品运输控制是企业现代化生产的重要组成部分,80年代以来,面对激烈的市场竞争,人们在车间生产运输工作中所惯用的那种人工方式,已不能适应快速增长的工作需要。
在现代化工业生产中,为了提高劳动生产率,降低成本,减轻工人的劳动负担,要求整个工艺生产过程全盘自动化,这就离不开车间生产流水线产品运输控制系统。
在自动化生产线上,有些生产机械的工作台需要按一定的顺序实现自动往返运动,并且有的还要求在某些位置有一定的时间停留,以满足生产工艺要求。
传统的生产流水线产品运输大多是继电器控制,而继电器控制有着接线繁多,故障率高的缺点,且维护维修不易等缺点。
用PLC程序实现车间生产流水线产品运输控制,不仅具有程序设计简易、方便、可靠性高等特点,而且程序设计方法多样。
目前,PLC在工业控制中获得了巨大的成功,因此可以预见,基于PLC的车间生产流水线产品运输控制系统具有广阔的应用前景。
1.2 课题国内外发展的状况由于自动化的不断发展,使得车间生产线的产品运输控制得到不断的改善,生产效率也不断提高,国内外车间生产流水线产品运输控制系统经历了以下几个阶段:a) 手动控制:在20世纪60年代末70年代初期,便有一些工业生产采用PLC 来实现产品运输控制,但是由于当时的技术还不够成熟,只能够用手动的方式来控制机器,而且早期运输控制系统多为继电器—接触器组成的复杂系统,这种系统存在设计周期长、体积大、成本高等缺陷,几乎无数据处理和通信功能,必须有专人负责操作。
b) 自动控制:在20世纪80年代,随着计算机的价格下降,这时的大型工控企业将PLC充分地与计算机相结合,自动化设备终于实现了PLC在车间产品运输控制系统方面的应用。
- 1、下载文档前请自行甄别文档内容的完整性,平台不提供额外的编辑、内容补充、找答案等附加服务。
- 2、"仅部分预览"的文档,不可在线预览部分如存在完整性等问题,可反馈申请退款(可完整预览的文档不适用该条件!)。
- 3、如文档侵犯您的权益,请联系客服反馈,我们会尽快为您处理(人工客服工作时间:9:00-18:30)。
基于PLC的自动化生产线控制系统软件设计摘要:自动化生产线由送料单元、加工单元、装配单元、输送单元和分拣单元5个单元组成。
每个单元都有控制本单元工作过程的PLC。
控制系统要求,每个都要上电时先复位,然后才能工作;按了停止按钮后,每个单元都要把本单元的流程进行完,然后停止;按下急停按钮,立即停止工作,急停按钮回复,寻找断点继续工作。
研究以上控制要求的编程思路,并且以自动线供料单元为例,研究复位、停止、急停等控制要求编程的方法。
关键词:PLC;自动线;控制;软件设计1.自动化生产线概述自动化生产线是在流水线的基础上逐渐发展起来的,它不仅要求线体上各种机械加工装置能自动地完成预定的各道工序及工艺过程,使产品成为合格的制品;而且要求在装卸工件、定位夹紧、工件在工序间的输送、工件的分拣甚至包装等都能自动地进行。
按照规定的程序自动地进行工作,这种自动工作的机械电气一体化系统就是自动生产线(简称自动线)。
自动线一般由送料、加工、装配、输送和分拣五个单元组成。
工作目标是将供料单元料仓内的工件送往加工单元的物料台,完成加工操作后,把加工好的工件送往装配单元的物料台,然后把装配单元料仓内不同颜色的小圆柱工件嵌入物料台上的工件中,完成装配后的成品送往分拣单元分拣输出,分拣站根据工件的材质、颜色进行分拣。
文中研究的自动线由送料单元、加工单元、装配单元、输送单元和分拣单元5个单元组成。
工作目标是将供料单元料仓内的工件送往加工单元的物料台,完成加工操作后,把加工好的工件送往装配单元的物料台,然后把装配单元料仓内不同颜色的小园柱工件嵌入到物料台上的工件中完成装配后的成品送往分拣单元分拣输出,分拣站根据工件的材质、颜色进行分拣。
自动化生产线主要完成的是顺序动作,其控制器多选用可编程控制器。
可编程控制器根据检测传感部分送来的信号,按照预先设计好的控制程序,控制执行机构完成相应的动作。
文中主要研究自动线控制软件设计。
自动化生产线由以下系统组成:(1)自动加工系统,这个系统是指生产线的基础系统,是整个生产线的框架。
(2)物流系统,这个系统是指生产线上的传送装置,例如轨道、输送带、转盘等,主要是负责产品的运输。
(3)信息系统,这个系统是对生产线传输进行负责,例如生产线的信息、控制等,同时还对计算机与其它控制系统进行信息传输,相当于人体的血液。
(4)软件系统,这个是生产线最重要的部分,他就像人体的大脑,它包括控制软件、生产系统软件、运输软件、监控软件等。
自动化生产线是一个复杂的综合体,是解决机械硬件实现柔性化的关键技术,而它的优点有设备领用率高,可以将生产线上的设备柔性的连接;生产能力稳定;产品质量高,由于产品生产不间断,这样会使产品的质量得到保证;运行灵活,生产、检验、维护方便。
未来自动化生产线应该向着高速、精度高、效率高、智能化的方向发展,实现用户界面的图像化,将机器与人直接对话,现在的生产线只能行程简单的图形,实现的是图形的仿真与动态模拟,所以可视化是未来发展的重要方向。
2.自动化生产线的研究背景及意义近年来,无线通信、传感器、组网等技术的进步使信息系统得到了前所未有的发展,然而,在经济建设的各主要领域,生产线基础设施和信息基础设施的建设往往是分开进行的。
一方面,人们不断地建设和完善周围的生产线;另一方面,人们也不遗余力地发展数据中心、个人电脑和宽带网络等信息世界,但将信息世界和生产线世界割裂开来。
而国民经济的发展对信息系统早已提出了更高的要求,现代科技的发展要求将计算技术拓展到整个人类活动的空间,将人类的生产线世界计算化、网络化、信息化,使信息系统和生产线系统整合统一成为自动化生产线分布式控制系统【1】。
自动化生产线分布式控制系统的重要特性与生产线环境紧密交互,其应用任务的临界性通常对自动化生产线分布式控制系统的精度、能耗、实时性、组网可靠性、安全性、服务质量等性能指标有着严格的要求。
然而,也正是由于同生产线环境的紧密结合,环境因素不可避免地会影响传感/执行子系统的采样数据并且不断产生变化,生产线环境的不确定性和系统自身的误差给整个系统的性能造成极大的影响。
另一方面,由于市场和推广的原因,自动化生产线分布式控制系统通常采用大量低成本的非定制器件搭建和设计,系统资源非常有限。
因此系统的性能保障问题正在成为自动化生产线分布式控制系统设计和应用的瓶颈,阻碍其大规模发展的步伐。
3.自动线控制要求自动化生产线,是指以计算机程序设计运用模式,取代传统人工跟踪加工处理的生产过程,它具有高效率、一体化等特征,与传统的生产线加工方式相比,它主要通过执行自动编程命令,操控生产对象进行自主性生产,其速率更高、质量保障性也更大。
由于自动化生产线控制结构,主要是以程序生产为主导,各部分生产操作均是按照“命令”进行操作,由此,它要求各个部分在生产过程中,均要保持在同一运转速率上,才能够实现流畅性生产;同时,自动化生产线控制系统,着重突出的是“控制”的自动化,确保机械与人能够协调运作,而不是要求人跟随机械的变化而变化,由此,自动化生产控制系统,必须有较为综合的人机对话平台,才能够彰显“自动化控制”的这一优势。
我们在进行系统升级、全面性设计的过程中,应注重对这两点问题进行把握。
本控制系统以可编程控制器为整个控制系统的核心,各单元均设置一台西门子S7-200PLC承担其控制任务,各PLC之间通过PPI通信实现互连,构成分布式的控制系统。
系统硬件如图1所示。
自动线各单元流程不同,但其控制要求相同。
自动线各单元控制要求如下:3.1每个单元上电后先要复位;3.2每个单元按流程完成生产过程;3.3按下停止按钮,每个单元要完成一个控制流程,然后停止;3.4按下急停按钮,每个单元立即停止工作,当急停按钮复位后,再从断点开始动作。
图1 系统硬件结构图4.控制系统软件设计4.1总体编程思路自动线各单元生产过程基本相似,故每个单元的编程思路相同。
由于自动化生产线中主要完成的流水动作,因此编程主要用西门子的顺控指令完成。
程序结构主要包括主程序和子程序,主程序主要完成复位、通讯和调用子程序,子程序主要完成具体动作过程和显示。
常规编程这里不做过多研究,本文主要研究复位、顺控指令、停止和复位编程的方法。
4.2复位编程自动化生产线每个单元在上电后都要求先复位,复位完成才能进行下一步工作,否则系统报警。
系统五个单元的复位编程思路相同,都是在PLC上电的第一个周期给复位标记置位,在复位标记闭合情况下,检查各个元件的初始状态,若各个元件都在初始状态则给置位标记复位,在复位情况下才能完成下面的动作,并且将此信息传给主机,否则报警。
4.3顺控指令编程自动化生产线主要完成的是顺序动作,因此动作顺序的实现都是用顺序控制指令编写成子程序,在需要时调用。
编程时都是在主程序中给起始步置位,在条件合适时调用子程序,完成本单元动作,然后再返回起始步等待。
4.4停止编程自动化生产线要求每个单元在按了停止按钮后,要把本单元的工作流程进行完,然后停止。
要完成这个要求,需要在主程序中添加相应的指令来。
编程时是在按下停止按钮时,给顺控子程序的起始步复位,这样动作子程序在执行完一个流程后返回起始步,因为起始步复位而停止动作。
4.5急停编程当遇到紧急情况时,可以按下单元的急停按钮,这时系统立即停止动作;当紧急情况处理完时,拔出急停按钮,要求能自动找到原来的断点,继续执行原来中断的动作。
编程思路是在按下急停按钮时,立即停止调用动作子程序,这时单元动作停止,当急停恢复时,恢复调用子程序,这样子程序可以接着原来中断的步继续执行动作。
5.应用实例5.1供料单元简介本文所介绍的自动化生产线5个单元编程思路都是相似的,只是动作过程不一样。
下面以供料单元为例,研究编程的技巧。
供料单元结构如图2所示,它主要用于向系统中其他单元提供原料。
具体动作过程如下:在需要将工件退出到物料台时,首先使加紧气缸的活塞杆伸出,压住次下层工件;推到物料台。
在推料气缸返回后,再使加紧气缸返回,松开次下层工件。
图3 供料单元复位程序5.2供料单元复位编程供料单元初始是在顶料气缸和推料气缸均处于缩回位置时,为复位状态。
在程序开始运行时,用SM0.1给初态检查标记M5.0置位,当M5.0闭合时检查单元是否处于初始状态,若在初始状态,给M5.0复位,如图3所示。
其他单元编程思路相同,只是复位的内容不一样。
5.3供料单元顺控动作编程若设备准备好,按下启动按钮,给起始步S0.0置位,开始供料控制子程序执行。
如图4所示。
如果出货台上没有工件,则应把工件推到出货台上。
若货台上的工件被取走,并且没有停止信号,则进行下一步推出工件操作。
启动顺控指令各单元编程方法相同。
图4 供料单元顺控动作启动程序5.4供料单元停止编程若在运行中按下停止按钮,停止标记M1.1置位,在M1.1闭合时给S0.0复位,这样在供料控制子程序执行完一个流程返回S0.0时,停止工作,如图5所示。
这样的编程思路可以保证每个单元在完成本单元动作后停止【2】。
5.5供料单元急停编程若在运行中遇到紧急情况,需要立即按下急停按钮,应该立即停止动作;当急停恢复后,应该寻找急停前的断点,接着前面的断点继续工作。
在供料单元的运行过程中按下急停按钮,I1.4断开,停止调用子程序,则供料单元停止工作。
当急停回复后,I1.4闭合,供料控制子程序回复调用,即可接着原来的断点工作,如图6所示。
自动线5个单元急停编程思路完全相同。
图6 供料单元急停程序结论自动化生产线可以自动完成生产过程,大幅度提高生产效率,改变生产流程,只需改变控制程序,控制程序的设计是自动运作的关键。
以上是以自动化生产线供料单元为例研究复位、停止和急停的编程方法,这种编程方法虽然只是针对自动线的一个单元,但可以应用到自动化生产线的其他单元。
自动线实现的功能可以有多种,但其基本编程的思路相同。
这种编程的思路可以用到更多的PLC控制的自动化生产线编程中,完成系统控制。
参考文献:[1]张宋文.PLC技术在自动化生产线中的应用探讨[J].电子技术与软件工程,2014(07):264.[2]贾浩然.PLC在生产线自动化改造中的应用[J].山东工业技术,2017(03):134.[3]任婷婷.自动化生产线的安装与调试[J].电子技术与软件工程,2018(03):145.[4]樊晓晨.冲压自动化生产线中的工业机器人应用[J].科技创新导报,2016,13(01):65-66.[5]熊才高.计算机控制技术在自动化生产线上的应用探讨[J].信息与电脑(理论版),2016(10):58-59.[6]喻洪流.对自动化生产线设备维修体制的探讨[J].设备管理&;维修,1999(05):7-9.。