绕管式换热器的结构形式分析及应用前景
螺旋缠绕管式换热器的设计要点

工艺与设备化 工 设 计 通 讯Technology and EquipmentChemical Engineering Design Communications·87·第44卷第7期2018年7月1 螺旋缠绕管式换热器应用分析从装置应用实际情况来说,在煤化工和其他领域中,以不同的结构形式,被广泛的应用。
以LNG 系列螺旋缠绕管式换热器为例,其类型主要如下:①一级制冷四股流缠绕管式换热器;②二级制冷三股流缠绕管式换热器;③三级制冷两股流缠绕管式换热器等。
此类换热器的应用涉及到多个过程,比如低温混合制冷剂、多股流回热换热过程等,设计计算复杂,缺少通用技术标准以及换热工艺设计计算法等,受到工艺流程或者物性参数等因素的影响,因此难以标准化。
2 螺旋缠绕管式换热器的基本结构常规的单股流螺旋缠绕管的基本结构如图1所示,它主要由1-管程壳体;2-管板;3-壳程筒体;4-螺旋管束组成。
它的螺旋管束是由数根外径φ8mm~φ12mm 的换热管根据一定角度正向反向缠绕而成。
1234图1 螺旋缠绕管换热器的基本结构3 螺旋缠绕管式换热器设计要点3.1 做好力学分析在机械设计中,为保证其使用性能,必须要做好力学分析,包括刚性力学分析和弹性力学分析,进而优化设计。
在进行分析的过程中,主要采用的计算方法包括雷诺数计算法以及普朗特数计算等。
基于力学原理,采用对数平均值法以及体积分率法等进行力学分析。
采用单元模型流场数值模拟分析法可确定其在物理参数,简化计算过程获得管束模型以及结构参数。
采用迭代计算法,结合运用数值模拟计算结果,利用计算机进行设计结果优化,进而保证计算的准确性。
3.2 立足于实际在进行螺旋缠绕管式换热器设计时,要考虑到后期加工制作和使用需求。
多数螺旋缠绕管式换热器的换热管和管板的连接采用强度焊的方法。
因为焊接的质量直接影响着换热器使用性能和寿命,所以在设计和制造环节,需要做好壳程部分的优化设计,通过压力试验或者渗漏试验等,检查接头的致密性以及强度。
热管换热器的结构形式

热管换热器的结构形式(三)热管换热器的结构形式以热管为传热单元的热管换热器是一种新型高效换热器,其结构如图片4-50、图片4-51所示,它是由壳体、热管和隔板组成的。
热管作为主要的传热元件,是一种具有高导热性能的传热装置。
它是一种真空容器,其基本组成部件为壳体、吸液芯和工作液。
将壳体抽真空后充入适量的工作液,密闭壳体便构成一只热管。
当热源对其一端供热时,工作液自热源吸收热量而蒸发汽化,携带潜热的蒸汽在压差作用下,高速传输至壳体的另一端,向冷源放出潜热而凝结,冷凝液回至热端,再次沸腾汽化。
如此反复循环,热量乃不断从热端传至冷端。
【图片4-50】热管换热器。
【图片4-51】热管示意图。
热管按冷凝液循环方式分为吸液芯热管、重力热管和离心热管三种。
吸液芯热管的冷凝液依靠毛细管的作用回到热端,这种热管可以在失重情况下工作;重力热管的冷凝液是依靠重力流回热端,它的传热具有单向性,一般为垂直放置离心热管是靠离心力使冷凝液回到热端,通常用于旋转部件的冷却。
热管按工作液的工作温度分为深冷热管、低温热管、中温热管和高温热管四种。
深冷热管在200K以下工作,工作液有氮、氢、氖、氧、甲烷、乙烷等;低温热管在200~550K 范围内工作,工作液有氟里昂、氨、丙酮、乙醇、水等;中温热管在550~750K范围内工作,工作液有导热姆A、水银、铯、水及钾─钠混合液等;高温热管在750K 以上工作,工作液有液态金属钾、钠、锂、银等。
热管的传热特点是热管中的热量传递通过沸腾汽化、蒸汽流动和蒸汽冷凝三步进行,由于沸腾和冷凝的对流传热强度都很大,而蒸汽流动阻力损失又较小,因此热管两端温度差可以很小,即能在很小的温差下传递很大的热流量。
因此,它特别适用于低温差传热及某些等温性要求较高的场合。
热管换热器具有结构简单、使用寿命长、工作可靠、应用范围广等优点,可用于气─气、气─液和液─液之间的换热过程。
SECESPOL螺旋纹缠绕 换热器
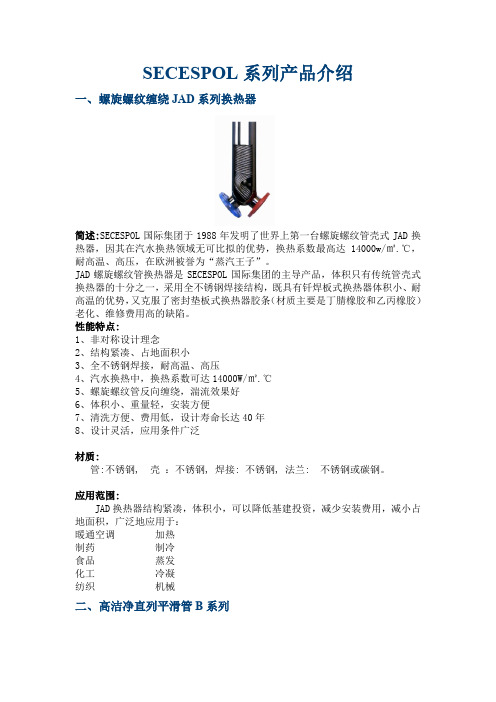
成功应用:
四、H 系列螺旋缠绕管壳式换热器
产品特征: H 系列换热器是由缠绕的特制螺纹管为主要构造。这一构造能够有 效的提高换热效率。而 K 系列以外的换热器,即没有采用螺纹管构造的换热器, 内部采用的均为平滑管。
模块化 CIP: 基于“质量和风险控制体系”的模块化在线清洗设计理念, 完全符合中国新版 GMP 中“可追溯性、可重现性”的规范要求; 便于与现有设备集成对接;支持多模块扩展(硬件、软件); 便于现场移动操作;降低制药质量控制风险;灵活配置,可有效降低采购成本。 系统优势 *为每个单独的车间和生产需要单独定制 *可以将完整的 CIP 功能整合到现有的控制系统中去 *符合 ASME-BPE 标准 *完整的各类文件符合管理机构的验证标准 *完善的数据采集,数据报告输出 *安装过程和售后都有完善的技术支持 。
性能特点: 平滑直列管。 全不锈钢 316L 焊接。 体积小、重量轻,安装方便。 清洗方便、费用低,设计寿命长达 40 年。 设计灵活,应用条件广泛
材质: 管:不锈钢 316L, 壳 :不锈钢 316L。
应用范围: B 系列换热器广泛地应用于:
制药 食品 化工 纺织
制冷 蒸发 冷凝 加热
三、P 系列 高洁净 药用双管板换热器
安装方式:P 系列产品可以竖直或水平安装,其主要基于客户要求,与产品 接触侧均采用快装接口,(Tri-Clamp)设计,方便安装、拆卸、清洗。
ห้องสมุดไป่ตู้
密封垫形式:产品接触侧密封垫 ——改性聚四氟乙烯(铁氟龙)基材料。 ——满足 3A 20-25 和 FDA 要求 ——采用高精密机械加工(保证表面光洁无毛刺)
换热器的结构讲解

换热器的结构管壳式换热器就是具有换热管和壳体的一种换热设备,换热管与管板连接,再用壳体固定。
按其结构型式,主要分为:固定管板式换热器、浮头式换热器、U形管式换热器、填料函式换热器、方形壳体翅片管换热器等。
详细结构如下:固定管板式换热器:固定管板式换热器结构如上图所示,换热器的两端管板采用焊接方法与壳体连接固定。
换热管可为光管或低翅管。
其结构简单,制造成本低,能得到较小的壳体内径,管程可分成多样,壳程也可用纵向隔板分成多程,规格范围广,故在工程中广泛应用。
其缺点是壳侧不便清洗,只能采用化学方法清洗,检修困难,对于较脏或对材料有腐蚀性的介质不能走壳程。
壳体与换热管温差应力较大,当温差应力很大时,可以设置单波或多波膨胀节减小温差应力浮头式换热器浮头式换热器结构如图所示,其一端管板与壳体固定,而另一端的管板可以在壳体内自由浮动。
壳体和管束对热膨胀是自由的,故当两种介质的温差较大时,管束与壳体之间不会产生温差应力。
浮头端设计成可拆结构,使管束可以容易地插入或抽出,这样为检修和清洗提供了方便。
这种形式的换热器特别适用于壳体与换热管温差应力较大,而且要求壳程与管程都要进行清洗的工况。
浮头式换热器的缺点是结构复杂,价格较贵,而且浮头端小盖在操作时无法知道泄漏情况, 所以装配时一定要注意密封性能U形管式换热器上图为双壳程U形管式换热器。
U形管式换热器是将换热管弯成U形,管子两端固定在同一块管板上。
由于换热管可以自由伸缩,所以壳体与换热管无温差应力。
因U形管式换热器仅有一块管板,所以结构较简单,管束可从壳体内抽出,壳侧便于清洗,但管内清洗稍困难,所以管内介质必须清洁且不易结垢。
U形管式换热器一般用于高温高压情况下,尤其是壳体与换热管金属壁温差较大时。
壳程可设置纵向隔板,将壳程分为两程(如图中所示)。
填料函式换热器上图为填料函式双管程双壳程换热器,填料函式换热器的换热管束可以自由滑动,壳侧介质靠填料密封。
对于一些壳体与管束温差较大,腐蚀严重而需经常更换管束的换热器,可采用填料函式换热器。
管式换热器工作原理

管式换热器工作原理管式换热器是一种常见的热交换设备,广泛应用于化工、石油、电力等工业领域。
它利用管壁与流体间的对流传热来完成热量的传递,是实现热能转移的重要设备之一。
下面我们将详细介绍管式换热器的工作原理。
首先,管式换热器的工作原理基于热传导和对流传热两种方式。
在管式换热器内部,热源流体和冷却流体分别流过管壁的内外表面,通过对流传热的方式,使得热量从热源流体传递到冷却流体上。
在这个过程中,管壁起到了传热的媒介作用,同时也承受着内外两种流体的压力和温度差。
其次,管式换热器的工作原理还涉及到热传导的过程。
热源流体在管壁内表面传热给管壁,然后通过管壁的热传导作用,将热量传递到管壁的外表面,最终传递给冷却流体。
这种热传导的方式使得管式换热器能够实现高效的热能转移,提高能源利用效率。
另外,管式换热器的工作原理还与流体的流动方式有关。
在管式换热器内部,流体可以采用并行流、逆流或交叉流等不同的流动方式。
不同的流动方式会影响到热量的传递效果,因此在实际应用中需要根据具体的工艺要求选择合适的流动方式。
此外,管式换热器的工作原理还受到管束结构的影响。
管式换热器的管束结构有单通道、多通道、U型管等不同形式,不同的结构形式会对传热效果和压降产生影响。
因此在设计和选择管式换热器时,需要根据具体的工艺条件和要求来确定最合适的管束结构。
总的来说,管式换热器的工作原理是基于热传导和对流传热的方式,通过管壁的传热作用实现热量的传递。
同时,流体的流动方式和管束结构也会对其传热效果产生影响。
在实际应用中,需要根据具体的工艺要求和操作条件来选择合适的管式换热器,以实现最佳的热能转移效果。
套管式换热器实验原理

套管式换热器实验原理套管式换热器是一种常见的换热设备,主要用于实现两种介质之间的热量传递。
它的实验原理是基于传热学的基本原理和换热器的结构特点。
本文将从实验原理、结构特点和应用范围三个方面来介绍套管式换热器。
一、实验原理套管式换热器的实验原理基于传热学的基本原理,主要包括传热方式、传热系数和传热面积等方面。
1. 传热方式套管式换热器的传热方式主要有对流传热和传导传热两种。
对流传热是指通过介质流动而实现热量传递,而传导传热是指通过固体材料的直接接触而实现热量传递。
在套管式换热器中,冷却介质和被冷却介质分别通过内管和外管流动,通过对流传热方式实现热量的传递。
2. 传热系数传热系数是描述热量传递能力的指标,它决定了套管式换热器的传热效果。
传热系数受到多种因素的影响,包括介质的性质、流速、内外管之间的传热面积等。
实验中可以通过改变流速、控制温度差等方式来调节传热系数,进而研究其对传热效果的影响。
3. 传热面积传热面积是套管式换热器的重要参数,它直接影响着换热器的传热效果。
传热面积的大小取决于内外管的长度和直径,同时也受到套管式换热器结构的限制。
在实验中,可以通过改变内外管的长度和直径来调节传热面积,进而研究其对传热效果的影响。
二、结构特点套管式换热器的结构特点主要包括内外管的布置方式、流体流动形式和换热面积的设计等方面。
1. 内外管布置方式套管式换热器的内外管可以采用不同的布置方式,常见的有并列式和串联式两种。
并列式布置方式适用于两种介质流速较大且温差较小的情况,可以提高换热效率。
串联式布置方式适用于两种介质流速较小且温差较大的情况,可以实现更大的温差。
2. 流体流动形式套管式换热器的流体流动形式可以分为顺流和逆流两种。
顺流是指冷却介质和被冷却介质在内外管中的流动方向相同,逆流是指冷却介质和被冷却介质在内外管中的流动方向相反。
顺流方式适用于温差较小的情况,可以减小传热面积;逆流方式适用于温差较大的情况,可以提高传热效果。
u型管式换热器的结构特点
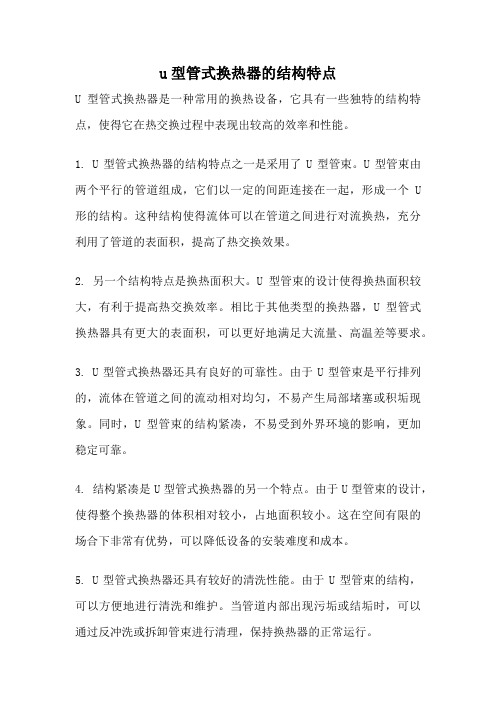
u型管式换热器的结构特点U型管式换热器是一种常用的换热设备,它具有一些独特的结构特点,使得它在热交换过程中表现出较高的效率和性能。
1. U型管式换热器的结构特点之一是采用了U型管束。
U型管束由两个平行的管道组成,它们以一定的间距连接在一起,形成一个U 形的结构。
这种结构使得流体可以在管道之间进行对流换热,充分利用了管道的表面积,提高了热交换效果。
2. 另一个结构特点是换热面积大。
U型管束的设计使得换热面积较大,有利于提高热交换效率。
相比于其他类型的换热器,U型管式换热器具有更大的表面积,可以更好地满足大流量、高温差等要求。
3. U型管式换热器还具有良好的可靠性。
由于U型管束是平行排列的,流体在管道之间的流动相对均匀,不易产生局部堵塞或积垢现象。
同时,U型管束的结构紧凑,不易受到外界环境的影响,更加稳定可靠。
4. 结构紧凑是U型管式换热器的另一个特点。
由于U型管束的设计,使得整个换热器的体积相对较小,占地面积较小。
这在空间有限的场合下非常有优势,可以降低设备的安装难度和成本。
5. U型管式换热器还具有较好的清洗性能。
由于U型管束的结构,可以方便地进行清洗和维护。
当管道内部出现污垢或结垢时,可以通过反冲洗或拆卸管束进行清理,保持换热器的正常运行。
6. 最后,U型管式换热器的结构特点还包括耐压性能好。
由于管道是平行排列的,内外压力均匀分布,不易产生应力集中,从而提高了整个换热器的耐压性能。
U型管式换热器具有U型管束、换热面积大、可靠性高、结构紧凑、清洗性能好和耐压性能好等结构特点。
这些特点使得U型管式换热器在工业生产和能源领域得到了广泛的应用,为热交换过程提供了高效、可靠的解决方案。
换热器的结构与性能特点
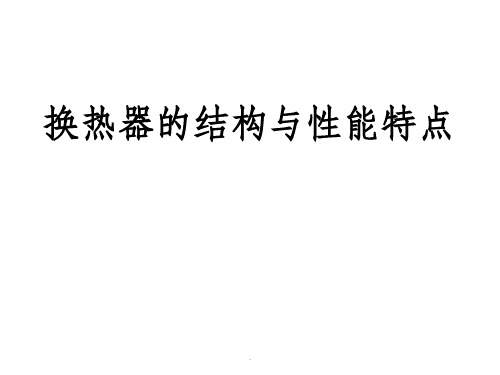
(1)沉浸式蛇管换热器
多以金属管弯绕而成,制成适应容器的形状,沉浸在容器内的液体中。两种 流体分别在管内、管外进行换热。
.
蛇管的形状主要取决于容器的形 状和生产队要求。如化工生产中 的反应器内的加热或冷却管,多 做成圆盘形或螺旋形的;氨冷的 冷冻盐水槽中的换热管,则多用 长的蛇形管构成。实际上,蛇管 可以制成任意需要的形状。如图 所示。 蛇管可以由钢管,铜管,银管或 其它有色金属和非金属材料如玻 璃,陶瓷,石墨和塑料等制成。
.
一、夹套式换热器
夹套式换热器是最简单的板式换热器, 它是在容器外壁安装夹套制成,夹套 与容器之间形成的空间为加热介质或 冷却介质的通路。这种换热器主要用 于反应过程的加热或冷却。在用蒸汽 进行加热时,蒸汽由上部接管进入夹 套,冷凝水由下部接管流出。作为冷 却器时,冷却介质(如冷却水)由夹 套下部接管进入,由上部接管流出。 特点:
几种常用的蛇管形状
沉浸式蛇管换热器的优点:结构简单、价格低廉、便于防腐蚀、能承受高压。 缺点:由于容器的体积较蛇管的体积大得多,管外流体的传热膜系数较小, 故常需加搅拌装置,以提高其传热效率. 。 多应用于小型容器内的液体换热。
(2)喷淋式蛇管换热器
喷淋式换热器也为蛇管式换热器,多用作冷却 器。这种换热器是将蛇管成行地固定在钢架上, 热流体在管内流动,自最下管进入,由最上管 流出。冷水由最上面的淋水管流下,均匀地分 布在蛇管上,并沿其两侧逐排流经下面的管子 表面,最后流入水槽而排出,冷水在各排管表 面上流过时,与管内流体进行热交换。这种换 热器的管外形成一层湍动程度较高的液膜,因 而管外对流传热系数较大。另外,喷淋式换热 器常放置在室外空气流通处,冷却水在空气中 汽化时也带走一部分热量,提高了冷却效果。
- 1、下载文档前请自行甄别文档内容的完整性,平台不提供额外的编辑、内容补充、找答案等附加服务。
- 2、"仅部分预览"的文档,不可在线预览部分如存在完整性等问题,可反馈申请退款(可完整预览的文档不适用该条件!)。
- 3、如文档侵犯您的权益,请联系客服反馈,我们会尽快为您处理(人工客服工作时间:9:00-18:30)。
绕管式换热器的结构形式分析及应用前景
摘要:随着绕管式换热器应用要求的不断提高,研究其结构形式分析及应用前
景凸显出重要意义。本文首先介绍了绕管式换热器的结构形式特点,提出了提高
绕管式换热器设备工作效率的可行性措施,并结合相关实践经验,分别从大型化、
高温化,以及高压化等多方面,就绕管式换热器的应用前景展开了研究,阐述了
个人对此的几点看法与认识。
关键词:绕管式换热器;结构形式;应用前景
一、前言
作为换热器最为主要的种类之一,绕管式换热器的应用优势不言而喻。该项课题的研究,
将会更好地提升对绕管式换热器的结构形式的分析与掌控力度,从而通过合理化的措施与途
径,进一步优化其在实际应用中的整体效果。
二、绕管式换热器的结构形式特点
1.结构构成原理
缠绕管式换热器(Spiral Wounded Heat Exchanger)相对于普通的列管式换热器具有不可
比拟的优势,其适用的温度范围广,适应热冲击,能够自身消除热应力,紧凑度非常高,由
于自身具有特殊的构造,使得其流场充分发展,不存在流动死区,其中最特别的是,通过设
置多股管程(壳程单股),能够在一台设备内满足多股流体的同时换热。绕管式换热器是在
芯筒与外筒之间的空间内将传热管按螺旋线形式交替缠绕而成的,相邻两层螺旋状传热管的
螺旋方向是相反的,并采用具有特殊形状的定距件,使之能够保持一定的间距。
缠绕管可以采用单根绕制而成,也可采用两根或者多根组焊后一起然后绕制而成。管内
可以通过一种的称为单通道型绕管式换热器;也可分别通过几种不同的介质,而每种介质所
通过的传热管最后均汇集在各自的管板上,构成的换热器称为多通道型缠绕管式换热器。区
别于平常所用的直管式换热器,绕管式换热器的优势是,不仅仅换热管加长了,有足够的流
程使物料在其中流通和热交换,同时保持流体在壳程内的压力平衡,平均了热能分布,这样
在实际的使用中,大大地提高了换热效率与传热能力。
2.技术特色绕管式换热器的三大技术特色
技术特色绕管式换热器的三大技术特色或者说是技术精髓为:精准的换热管间距、合理
的管层数量以及层间距、全自动化的机器人焊接流程。
(一)精准的换热管间距不锈钢管材因为其材质的特殊性而导致了在弯曲或者缠绕的时
候很难具有塑性,为实现所有换热管的间距都是统一的这一技术要求带来了很大的困难,这
就要求我们在加工时需要完备的技术和丰富的经验,而正是原装进口的高精度设备和顶尖的
缠绕工艺为我们机械的生产提供了基础。
(二)合理的管层数量以及层间距在换热管束缠绕时,每层相对的管径都在发生着变化,
盘绕角度又要保持一致,要保证每根换热管的长度基本相同确实是很难做到的。而设计师设
计出了每层换热管不同数量,以及合理的层间距就完美地攻克了这一难题,同时也解决了复
杂换热条件下的流道要求。
(三全自动化的机器人焊接流程在设备生产的过程当中,采用全自动化的机器人焊接,
以保证所有焊点尤其是在管板焊接都实现了标准统一,安全性能极高。
3.绕管式换热器应用于工程的主要优点
(一)结构紧凑,单位容积具有较大的传热面积。对管径8~12mm的传热管,每立方
米容积的传热面积可达100~170平方米。
(二)可同时进行多种介质的传热。
(三)管内的操作压力高,目前国外最高操作压力可达2000多MPa。
(四)传热管的热膨胀可自行进行补偿。
(五)换热器容易实现大型化发展。
三、提高绕管式换热器设备工作效率的可行性措施
1.使用复合材料显著缓解机器发热热量
绕管式设备使用复合材料可以显著缓解机器发热对于内部构件的损伤。根据复合材料缠
绕技术中,缠绕容器散热效率的实验中得到了测试结果表明,一般的气-气型管壳形式的换热
器传染系数约为80-380w/(m2-k),并且,绕管式换热器的总传热系数在峰值运行期间,可
以达到590w/(m2-k)以上。由此可见,在一般的散热操作零构件中,使用绕管式换热器设
备开展机器换热,效果最为显著,单位时间的散热效率也最高。
2.采用纤维缠绕圆柱形结构提高散热效果
对于一般的绕管式换热器中的固定管板部分,通常会在换热的过程中由于“热胀冷缩”物
理原理会产生一定的管线膨胀。
20世纪末期,美国著名的热力材料科学家MattTriplett、Neer-AAS等科学家,针对不同
工质的材料开展绕管散热技术的探讨,对于纤维缠绕圆柱形的散热效果进行了一系列具体试
验。对于绕管式换热器的壳程传热效率和压降模式来说,随着制热能量在等量梯级增加的情
况下,散热容器的裂纹长度随之变长,负荷效能呈现出过高的现状。并且,当外界的供热能
量增加到一定的数值时,压力容器上的迟到区域冲击区域与薄膜区域的冲击,对于散热容器
产生的等量降低效果基本呈现出正相关的受损趋势。
3.加强对于绕管式本体的探伤,提高管体材料使用寿命
在散热体的管控过程中,使用目视法是检测散热容器抗损伤的最简单和直接有效的方法。
机械设计师通过肉眼对换热器内部的绕管部分进行检查,或者借助放大镜对容器外表面的壁
衬进行检测,可以发现在受热情况下,复合缠绕材料表面纤维的具体受损伤的情况。
四、绕管式换热器的应用前景探讨
1.绕管式换热器的大型化趋势
由于绕管式换热器结构的特殊性,它的封头虽然很小,但是管子可以长达数百米,目前
已开发制造了一些大型的绕管式换热器。随着装置的大型化趋势不断发展,要求绕管换热器
也要不断增大。但是目前普通列管式换热器由于管子的限制,是无法把换热器做大的。
2.绕管换热器的高温化趋势
绕管式换热器必备的性能就是高效的换热性能,但其目前基本上只应用于深冷装置。从
2001年开始,合肥通用所等企业开始专注研究能够应用于高温场合的绕管式换热器,并且,
于2002年在镇海炼化投入使用,这种换热器所采用的是CrMo钢耐高温材料。经过几年运行,
该换热器的性能能够完全达到使用要求,而且质量也很可靠。这种产品的成功应用大大拓宽
了绕管式换热器的应用领域,使其可以从低温应用领域转向高温应用领域。如果介质允许,
在炼油行业也是可以应用绕管式换热器的。
3.绕管式换热器的高压化趋势
目前,绕管式换热器多应用于壳程压力高而管程压力低的地方,一般壳程压力能够达到
15.0MPa,但是管程压力普遍小于5.0MPa。由于绕管式换热器的结构特点为:管板小,壳程
压力大,两端入口封头较小,所以该结构能克服一般的高压换热器的缺点。普通高压换热器
一般都是采用浮头式或者U形管式,当压力提高时,不仅加大了壳体厚度,而且还会大幅度
提高法兰的强度等级。而绕管式换热器却可以利用其加长的长度来增大面积,而且两端的小
管板也使得连接的法兰减小,这样会将制作工艺简单化。目前,国内某些单位正在研究用绕
管式换热器逐步替代炼油行业中的一些高压换热器,如,加氢裂化和重整装置等。
五、结束语
通过对绕管式换热器结构形式分析及应用前景的研究,我们可以发现,绕管式换热器的
诸多优势特点,决定了其在实际应用中的地位,有关人员应该从绕管式换热器应用的客观实
际需求出发,研究制定最为符合实际的应用实施策略。
参考文献:
[1] 吴金星,李亚飞,张灿灿等.绕管式换热器的结构形式分析及应用前景[J].压力容器.2014
(12):138-142.
[2] 贾金才.几何参数对绕管式换热器传热特性影响的数值研究[J].流体机械.2014(08):33-
307,173.
[3] 吴志勇,陈杰,浦晖等.LNG绕管式换热器壳侧过热态流动的数值模拟[J].煤气与热力.2014
(08):148-153.