热管换热系统的设计方案
汽车冷却系统热管式换热器课设

汽车冷却系统热管式换热器课设
汽车冷却系统热管式换热器课设是一项关于设计和分析汽车冷却系统中热管式换热器的课程设计。
汽车冷却系统是保证发动机及其它汽车组件工作正常的重要系统之一。
而热管式换热器是一种高效的换热器,它利用热管的特性将热量从一个热源传递到另一个热源,从而实现汽车冷却系统中的热量传递和冷却。
在这个课设中,学生需要了解热管的基本原理和工作原理,以及汽车冷却系统的工作原理和要求。
然后,学生需要设计一个适合汽车冷却系统的热管式换热器,并进行性能分析。
具体来说,学生需要进行以下步骤:
1. 研究汽车冷却系统的工作原理和要求,了解发动机的热量产生特点和冷却需求。
2. 研究热管的基本原理和工作原理,了解热管的分类、结构和工作过程。
3. 根据汽车冷却系统的需求和热管的特性,设计一个符合要求的热管式换热器。
这包括选择合适的材料、确定热管的长度和直径,以及设计换热器的结构和尺寸。
4. 使用计算机辅助设计软件(如CAD)进行三维模型设计,并进行热工分析。
这包括模拟热管的工作过程,计算换热器的换热效率和冷却性能。
5. 根据设计结果,进行性能评估和优化。
可以尝试不同的参数,比如热管的长度和直径,以获取最佳的冷却效果。
6. 进行实验验证。
可以利用实验室设备或制作原型进行实验,测试换热器的性能和效果。
7. 撰写课设报告,总结设计过程和结果,并提出改进意见。
通过完成这个课设,学生可以更深入地了解汽车冷却系统和热管式换热器的原理和应用,提高工程设计和分析的能力。
同时,这个课设也可以为未来从事相关领域的工程师提供实际的项目经验和技能培养。
热管与热管换热器设计基础

热管是一种利用液体的湿润性和蒸发冷却原理进行热传导的装置,具有高效、均匀、可控的热传导能力。
热管换热器则是利用热管进行热传导和热交换的换热设备。
以下是热管和热管换热器设计的基础知识:1.热管的工作原理:热管由内外壳体、工作流体和蒸汽管组成。
当热管的工作端加热时,内部的工作流体沸腾产生蒸汽,蒸汽通过蒸汽管传输到另一端,然后在冷却区域重新凝结为液态,液体通过液管回流到工作端。
这样,热量通过蒸汽和液体的相变传导实现了从热源到热汇的传递。
2.热管特性:热管具有高导热性、无需外部能源驱动、传热均匀、尺寸小巧等特点。
它可以将热源与热汇之间的温度差降低到很小的范围,实现高效的热传导。
3.热管换热器设计要点:●热管选择:根据具体应用需求选择合适的热管,考虑工作温度范围、导热性能、流体类型等因素。
●散热需求:确定需要传热的功率和温度差,以便选择合适的热管尺寸和数量。
●热管布局:考虑热源和热汇的位置关系,设计合适的热管布局,使热量能够有效传导到需要的位置。
●换热介质:选择合适的换热介质(如空气、水、液体等),确定流体的流速和换热方式(对流、辐射等)。
●结构设计:考虑热管的结构材料、密封性、耐腐蚀性等因素,确保热管换热器的稳定性和可靠性。
4.热管换热器的应用:热管换热器广泛应用于电子设备散热、航天器热控、工业生产过程中的热回收等领域。
它在提高换热效率、降低设备体积和重量方面具有重要的作用。
总而言之,热管和热管换热器的设计基础包括热管工作原理、热传导特性、热管选择、散热需求、热管布局、换热介质选择以及结构设计等方面。
这些基础知识是设计高效热管换热器的关键。
列管式换热器课程设计(含有CAD格式流程图和换热器图)

X X X X 大学《材料工程原理B》课程设计设计题目: 5.5×104t/y热水冷却换热器设计专业: -----------------------------班级: -------------学号: ----------- 姓名: ---- 日期: ---------------指导教师: ----------设计成绩:日期:换热器设计任务书目录1.设计方案简介2.工艺流程简介3.工艺计算和主体设备设计4.设计结果概要5.附图6.参考文献1.设计方案简介1.1列管式换热器的类型根据列管式换热器的结构特点,主要分为以下四种。
以下根据本次的设计要求,介绍几种常见的列管式换热器。
(1)固定管板式换热器这类换热器如图1-1所示。
固定管板式换热器的两端和壳体连为一体,管子则固定于管板上,它的结余构简单;在相同的壳体直径内,排管最多,比较紧凑;由于这种结构式壳测清洗困难,所以壳程宜用于不易结垢和清洁的流体。
当管束和壳体之间的温差太大而产生不同的热膨胀时,用使用管子于管板的接口脱开,从而发生介质的泄漏。
(2)U型管换热器U型管换热器结构特点是只有一块管板,换热管为U型,管子的两端固定在同一块管板上,其管程至少为两程。
管束可以自由伸缩,当壳体与U型环热管由温差时,不会产生温差应力。
U型管式换热器的优点是结构简单,只有一块管板,密封面少,运行可靠;管束可以抽出,管间清洗方便。
其缺点是管内清洗困难;哟由于管子需要一定的弯曲半径,故管板的利用率较低;管束最内程管间距大,壳程易短路;内程管子坏了不能更换,因而报废率较高。
此外,其造价比管定管板式高10%左右。
(3)浮头式换热器浮头式换热器的结构如下图1-3所示。
其结构特点是两端管板之一不与外科固定连接,可在壳体内沿轴向自由伸缩,该端称为浮头。
浮头式换热器的优点是党环热管与壳体间有温差存在,壳体或环热管膨胀时,互不约束,不会产生温差应力;管束可以从壳体内抽搐,便与管内管间的清洗。
影响热管换热的因素研究及优化设计

e ce tk a d h a aa c ro a l e o ti e t i e e tlv l b s g te o h g n x e me t i f i n e tb n e er r 8 c r b ba n d a f r n e es y u i  ̄ o o a e p r n n l d n h l i me o o c a g h e e f e p r n a a t r. T e r n e a ay i o a iu a tr f c n e t h t d t h n e t e lv l o x e me t f co s h a g l ss f v r s fco s a e t g h a i l n o i
2 1 4月 第 1 00年 3卷 第 4期
21 0 0,Vo ,1 l 3,No 4 .
贵州电力技术
GU ZHOU I ELECTRI P C OW ER TECHNOLOGY
专题 研讨
S c ̄ Re ts pe i po
文章编 号 :0 8— 8 X( 0 0 0 0 8 0 1 0 0 3 2 1 )4— 0 1— 3
Z a g Y uo g W a gJa g h n o rn , n in
( o eeo l tcl nier g G i o nvr t, uyn 5 0 3 G i o , hn ) C H g f e r a g ei , uz u U ie i G i g5 0 0 uz u C ia E ci E n n h sy a h
中图分 类号 :K 2 T 2
文 献标 识码 : B
影 响 热 管换 热 的 因素研 究及 优 化 设 计
张友荣 , 王 江
换热器的设计(1)

换热器的设计姓名:学号:目录1.设计方案简介 (1)1.1固定管板式换热器 (2)1.2浮头式换热器 (2)1.3U型管式换热器 (2)1.4填料函式换热器 (3)2.设计任务 (3)3.设计方案的确定 (3)3.1选择换热器的类型 (3)3.2流程安排 (4)3.3确定物性参数 (4)3.4估算传热面积 (4)3.4.1热流量 (4)3.4.2对数平均传热温度差 (4)3.4.3平均传热温差校正及壳程数 (5)3.4.4传热面积 (5)3.4.5冷却水的用量 (5)3.5工艺结构设计 (5)3.5.1管径和管内流速 (5)3.5.2管程数与换热管数 (5)3.5.3换热管排列原则 (6)3.5.4计算换热面积 (7)3.5.5壳程折流板选择 (7)3.5.6折流板间距 (8)3.5.7折流挡板数 (8)4.总传热系数K的计算 (8)4.1对流传热膜系数 (9)4.1.1管内传热膜系数 (9)4.1.2管外传热膜系数 (10)5. 换热管的核算 (11)5.1核算压强 (11)5.1.1管程压强 (11)5.1.2壳程压强降 (12)6.主体构建的设计与连接 (14)6.1管板 (14)6.1.1管板厚度 (14)6.2壳体管箱壳体和封头的设计 (14)6.2.1壁厚的确定 (15)6.2.2 壳程接管位置的最小尺寸 (15)6.2.3管箱接管位置的最小尺寸 (15)6.3折流板 (15)6.3.1折流板的作用 (15)6.4其他主要构件 (16)6.4.1膨胀节 (16)6.4.2拉杆和定距管 (17)6.4.3支承板 (17)6.4.4旁通挡板 (19)6.5换热器主要连接 (20)6.5.1管子与管板的连接 (20)6.5.2管板与壳体的连接结构 (20)6.5.3管板与分程隔板的连接 (21)6.5.4拉杆与管板的连接 (21)6.6支座 ................................................... 21i P1.设计方案简介换热器是广泛应用于化工、石油化工、动力、医药、冶金、制冷、轻工等行业的种通用设备。
轮机热管理系统的设计与优化方法

轮机热管理系统的设计与优化方法在现代船舶和工业领域,轮机热管理系统扮演着至关重要的角色。
它不仅关乎着设备的正常运行和可靠性,还直接影响着能源的利用效率和环境保护。
一个精心设计和优化的轮机热管理系统能够有效地降低能耗、减少排放,并延长设备的使用寿命。
轮机热管理系统的基本原理是通过对热量的产生、传递和散发进行有效的控制和管理,以维持轮机设备在适宜的温度范围内工作。
这涉及到对冷却介质(如水、油等)的流动、传热过程以及热交换器等关键部件的设计和布局。
在设计轮机热管理系统时,首先需要对轮机设备的热负荷进行准确的评估。
这包括考虑发动机的燃烧过程、摩擦损失、功率输出等因素所产生的热量。
通过详细的热力学分析和计算,可以确定热负荷的大小和分布情况,为后续的系统设计提供基础数据。
冷却介质的选择也是一个关键环节。
水具有良好的传热性能和比热容,但在一些特殊环境下可能会出现腐蚀和结冰等问题。
而油则具有较好的润滑性能和稳定性,但传热效率相对较低。
因此,需要根据具体的应用场景和要求,综合考虑各种因素来选择合适的冷却介质。
热交换器是轮机热管理系统中的核心部件之一。
其设计的优劣直接影响着热量传递的效率。
常见的热交换器类型包括管壳式、板式和翅片式等。
在设计热交换器时,需要考虑换热面积、流体流速、温差等因素,以确保足够的传热能力和较小的压力损失。
此外,管路系统的设计也不容忽视。
合理的管径和布局能够减少流动阻力,提高冷却介质的流量和流速,从而增强散热效果。
同时,还要考虑管路的密封性能和防震措施,以防止泄漏和损坏。
在优化轮机热管理系统方面,可以采用多种方法。
其中,数值模拟技术是一种非常有效的手段。
通过建立数学模型和使用专业的软件,可以对系统中的流体流动、传热过程进行仿真分析,预测不同设计方案下的性能表现,并进行优化改进。
智能控制策略也是当前的研究热点之一。
利用传感器实时监测轮机设备的温度、压力等参数,通过控制器自动调整冷却介质的流量、温度等,实现对热管理系统的精确控制,从而提高系统的适应性和节能效果。
热管设计

一、设计任务
利用烟气预热空气,完成换热器的设计,提交说明书,画出设计总图和部件图。技术要 求如下: 烟气:进口温度 545℃,出口温度 150℃,压力 1.18 kgf cm 2 ,流量 9 kg s 空气:进口温度 27℃,压力 1.54 kgf cm 2 ,流量 14 kg s
二、问题分析
设计任务所给的流体是烟气和空气, 于是首先可以排除间壁式中的喷淋式换热器和蒸发 冷却器。同时由于两者不能混合,且烟气具有一定的腐蚀性与灰尘,所以排除混合式、蓄热 式及板式换热器。两种流体的流量均比较大,而压力不是很大,选择套管式和微型换热器是 不合理的。烟气进出口温差近 400℃,故应选择传热系数大的换热器,于是排除沉浸式。烟 气的平均温度较高,故不应选择板翅式换热器。还剩下管壳式、管翅式和热管换热器,由于 我对热管这个相对比较新型的高效换热器比较感兴趣,于是便选择了热管换热器。 热管是一种依靠管内工质的蒸发、凝 结和循环流动而传递热量的部件。热管型 式可分为吸液芯热管、两相热虹吸管和旋 转热管。工程中烟气预热空气大多使用两 相闭式热虹吸管(也叫重力热管) ,其工作 原理图如图 1 所示。管子为真空密封,当 管子的下端被高温流体加热时,下端的液 体蒸发并以高速向上部移动,在与温度较 低的上端管壁接触后,冷凝成液体,然后 在重力作用下沿管内壁流回下端蒸发段, 从而完成高低温流体的换热循环。热管换 热器传热效率高,管内没有运动部件,运 行可靠。热管外表面常加翅片,单位体积 的换热面积大,结构紧凑,通道简单,管 外流动压力损失小,是个不错的选择。 图 1 两相闭式热虹吸管及工作原理图
NT
B 14 支 S1
(4)元件加热段外光管面积 Fo ,e
Fo ,e d ole 0.343m2
热管的换热基本知识及其换热计算
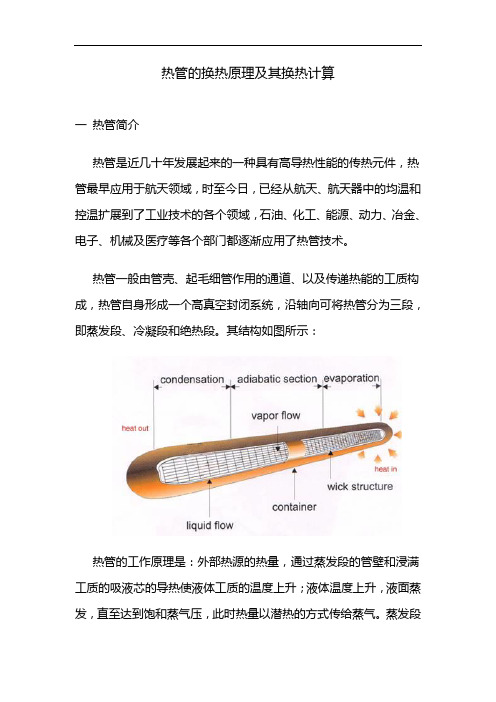
热管的换热原理及其换热计算一热管简介热管是近几十年发展起来的一种具有高导热性能的传热元件,热管最早应用于航天领域,时至今日,已经从航天、航天器中的均温和控温扩展到了工业技术的各个领域,石油、化工、能源、动力、冶金、电子、机械及医疗等各个部门都逐渐应用了热管技术。
热管一般由管壳、起毛细管作用的通道、以及传递热能的工质构成,热管自身形成一个高真空封闭系统,沿轴向可将热管分为三段,即蒸发段、冷凝段和绝热段。
其结构如图所示:热管的工作原理是:外部热源的热量,通过蒸发段的管壁和浸满工质的吸液芯的导热使液体工质的温度上升;液体温度上升,液面蒸发,直至达到饱和蒸气压,此时热量以潜热的方式传给蒸气。
蒸发段的饱和蒸汽压随着液体温度上升而升高。
在压差的作用下,蒸气通过蒸气通道流向低压且温度也较低的冷凝段,并在冷凝段的气液界面上冷凝,放出潜热。
放出的热量从气液界面通过充满工质的吸液芯和管壁的导热,传给热管外冷源。
冷凝的液体通过吸液芯回流到蒸发段,完成一个循环。
如此往复,不断地将热量从蒸发段传至冷凝段。
绝热段的作用除了为流体提供通道外,还起着把蒸气段和冷凝段隔开的作用,并使管内工质不与外界进行热量传递。
在热管真空度达到要求的情况下,热管的传热能力主要取决于热管吸液芯的设计。
根据热管的不同应用场合,我公司设计有多种不同的热管吸液芯,包括:轴向槽道吸液芯、丝网吸液芯和烧结芯等。
基于热管技术的相变传热原理、热管结构的合理设计以及专业可靠的品质保证,多年实践证明,我公司生产的热管及热管组件正逐渐迈向越来越广阔的市场。
(1) 产品展示(2) 产品参数说明项目技术参数热管长度> 100mm主体材料铜管毛细结构槽沟/烧结芯/丝网管工作介质冷媒设计工作温度30~200℃设计使用倾角> 5°传热功率50~1000w (根据实际产品规格型号) 热阻系数< 0.08℃/W (参考值)传热功率测试原理测试总体要求1)加热功率有功率调节仪控制输入;2)热管保持与水平台面α角度(根据具体应用定);3)管壁上监测点的温度变化在5min内小于0.5℃认为传热达到稳定状态,记录此时传热功率为最大传热功率。
- 1、下载文档前请自行甄别文档内容的完整性,平台不提供额外的编辑、内容补充、找答案等附加服务。
- 2、"仅部分预览"的文档,不可在线预览部分如存在完整性等问题,可反馈申请退款(可完整预览的文档不适用该条件!)。
- 3、如文档侵犯您的权益,请联系客服反馈,我们会尽快为您处理(人工客服工作时间:9:00-18:30)。
1
热管散热器设计方案
热管散热器工作原理
热管技术的原理和普通的散热器不同,热管主要是利用工质的蒸发与冷凝来
传递热量。热管一般是由管壳、吸液芯和工质三个部分组成。将管内抽至较高的
真空度后充以适量的工质,使得紧贴管内壁的吸液芯毛细多孔材料中充满液体后
加以密封。热管有两端,分别为蒸发端(加热端)和冷凝端(散热端),两端之间
需要采取绝热措施。当热管的一端受热时(即两端出现温差时),毛细芯中的液体
蒸发汽化,蒸汽在压差之下流向另一端放出热量并凝结成液体,液体再沿多孔材
料依靠毛细作用流回蒸发端。
热管散热器的分类和特点
按照工作温度,热管可以分为:
(1)深冷热管:工作温度范围为(100~200)K,工质可选用氦、氩、氮、氧等。
(2)低温热管:工作温度范围为(200~250)K,工质可选用水、氟利昂、氨、酒精、
丙酮等有机物质。
(3)中温热管:工作温度范围为(550~750)K,工质可选用导热姆A、水银、硫、
铯等物质。
(4)高温热管:工作温度范围大于750K,工质可选用钾、锂、铝、银等高熔点
液态金属。
热管散热器的特点:
(1)利用工质的相变传热,传热能力高。
(2)热管内蒸汽处于饱和状态,均温特性好。
(3)具有可变换热流密度特性。
(4)具有良好的恒温特性。
电子设备热管散热器的设计
1.热管的设计要求
(1)工作温度:根据电子设备、电子器件及整机的温度控制要求,热管的工作温
度一般为-50℃~200℃。
(2)发热量:根据器件的发热功率和工作环境条件确定热管所需传递的功率。
2
(3)热特性:按照电子器件发热功率的大小和温度控制的要求(均温、恒温或控
温)来设计蒸发端、冷凝端、吸液芯和管壳的几何形状、尺寸。
(4)工作环境:根据电子设备的工作环境条件(如陆地、海面或高空等)来估计
重力场对热管工作的影响,同时确定冷凝端与冷却介质的连接方式。
(5)结构尺寸:根据用户提供的热管外形尺寸、重量等要求进行结构设计。
2.工质选择
(1)选择要求
工质的工作温度范围在工质的凝固点与临界温度之间,以接近工质的沸点为
宜;选用的工质无毒、不易爆、使用安全;工质与管壳材料及吸液芯应相容,对
热管的安全工作和可靠性不产生有害的影响;工质的品质因素高;重力场条件下
的热管,工质的选用应考虑毛细力的提升高度。
(2)适合电子设备用的热管工质有甲烷、氨、氟利昂、丙酮、甲醇、乙醇、庚烷、
水和导热姆A 等。
3.吸液芯的选择
吸液芯的结构和性能是决定热管性能的关键因素。吸液芯的类型主要有均匀吸
液芯和组合式吸液芯。对吸液芯的主要要求是起到一个有效的毛细泵作用,在流
体和吸液芯结构之间产生的表面张力必须大到能克服管内的全部粘滞压降和其他
压降,还要维持所要求的流体循环。因为热管常常要在蒸发段比冷凝段高的重力
场中工作,所以吸液芯把工质提升的高度应等于或大于在蒸发段和冷凝段之间的
最大高度差。这个高度具有矛盾性,一方面为了使吸液芯内粘滞损失最小,希望
毛细孔尺寸大;而另一方面为了提供足够的毛细力和最大提升高度,又希望毛细
尺寸小,应采取毛细尺寸最佳化的处理方法。
除上述工作特性外,还必须考虑以下几方面的要求:
(1)与工质和管壁材料应相容;(2)具有较高的渗透率且传热性能好;(3)应具
有足够的刚性,以保证吸液芯和管壁紧密接触;(4)便于加工,性能可靠,经济
性好。
4.管壳设计
(1)材料
电子设备热管用的管壳材料主要有紫铜、无氧铜、铝合金、不锈钢等。管壳材料
3
应与工质相容;湿润性良好;导热系数高;具有足够的机械强度和良好的机加工
性能。
(2)管壳结构
a.壁厚:由于管壳需要承受工质蒸发时所产生的蒸汽压力,因此需对管壳的强度
进行校核,以保证热管安全工作。对于壁厚的要求是传热欲其薄,强度欲其厚。
两者虽有矛盾,但都需考虑,在保证强度的条件下用最薄的。
b.外壁结构:外壁结构可以是光滑的,或者是翅片的,根据需要和可能来决定,
翅片形式可以参考一般散热器的外翅片结构。
c.管壳:管壳多数为圆柱体,封头多数为平板深直口型。管筒和封头之间的连接
用焊接,焊口常用对接。在工以上,氩弧焊和氢保护焊可保证焊接质量。
d.热管的接长:利用环箍热管连接法。将两根被连接的热管的端部,分别插入一
个环箍热管的两端。这样,热管便可通过环箍这个中间热管而传递过去。被连接
热管与环箍热管之间的接触情况和接触面积是影响其热量传递的重要因素。
结束语
电子设备热管散热器的设计首先应根据设计技术要求,选择合适的工质、吸
液芯、管壳,然后进行传热量校核,最后通过试验验证热管散热器设计的合理性。
分离式液—气热管换热器的设计与应用
1前言
分离式热管换热器以其传热效率高、远程传热、现场布置灵活而具特色。其
最大的特点是加热段与冷凝段可以相互独立。以往大部分的分离式热管换热器都
是采用一种热流体同时加热两种或两种以上的冷流体,冷、热流体间多为气—气换
热形式,然而,将二种或两种以上的热流体(液体) 来加热冷流体(气体) ,目前还不
多见。在结构上加热段完全采用普通管板式列管换热器,热流体走壳程;冷凝段为
带有翅片管束的换热器,其翅片管外流经被加热气体,管内通过上升管、下降管与
列管换热器管程构成回路,将其抽成真空状态,充装工质。这样壳程内热流体通过
对流换热将热量传输给管程内的液态工质,工质吸收热量在真空状态下蒸发,蒸汽
沿上升管流至冷段凝结放出汽化潜热将流经翅片管外的气体加热。
4
2 结构形式与设计计算方法
根据热管加热段的换热,结构上采用普通管板式列管换热器,热流体流经壳程
管程为热管工质,换热器管程由若干根换热管组成一个单元,每个单元相互独立,
热管的冷凝段则为翅片管换热器,管外流经需要被加热的空气,管内通过若干根上
升管、下降管与列管换热器每个单元管程内构成回路,将其抽成真空状态,充装工
质。其结构如图1。
首先进行热力计算,热流体在壳程被冷却,放出热量Q ,为强化传热壳程布置了一定
数量的折流板,其壳程流体的换热系统可根据公式:
Nu = 0136 Re0.55 Pr1/ 3 (μf μw) 0.14
求出。管程流体的换热系数可通过传热因子jh 导出:
jh = Nu·Pr - 1/ 3·(μf μw) - 0114 (2)
式中μf ———流体粘度;
μw ———流体在壁温下的粘度;
因此,热管热段列管式换热器的总传热系数可以求出,传热面积也可求得,换热管
根数可以确定。壳程液体所放出的热量与管内工质进行换热,工质吸收热量蒸发,
蒸汽沿管内上升,通过上升管输送到热管冷凝段, 在冷凝段管内蒸汽与管外气体
换热,其管外换热系数可根据:
5
Nu = 01137 Re016338 Pr1/ 3 (3)
求出,冷凝段总传热系数也随之求得。这样,冷凝段翅片管换热器的传热面积可以
得出, 翅片管数量可以确定。
在结构上,热管加热段为典型的普通管壳式换热器,采用了固定管板形式,壳
体、封头、法兰、支座等均属于压力容器设备的零件,设计、制造按压力容器规程
执行。管板、折流板则按规程要求根据具体情况考虑,管板的厚度选取应考虑到材
料的强度、介质的压力、温度、以及管子的固定方式和受力状况等因素,管壳式换
热器在设计中必须考虑由温差引起的热应力,作出必要的热补偿措施。
6
为了使分离式热管换热器正常循环工作,必须克服上升管和下降管中蒸汽及
冷凝液流动所产生的压力损失,该能量来源于冷、热两端换热器之间的高度差和
上升管与下降管内工质的密度差。在系统中,循环工作图见图2 ,其运动压头Syd :
Syd = (ρι - ρe ) gH1 + (ρι - ρv ) gH2 + (ρc - ρv )gH3 (4)
式中ρι———饱和水密度;ρe 蒸发段汽液两相密度;ρc ———冷凝段汽液两
相密度;ρv ———蒸汽密度;
阻力:
ΣΔP = ΔPc + ΔPι+ ΔPe + ΔPv (5)
在稳定流动状态下, 运动压头是和循环回路的总阻力相等的,即达到平衡点:
Syd = ΣΔP (6)
换热器位差愈大, 水循环速度增加, 循环强烈, 流体的速度随之增加,阻力也增大,
重新达到新的平衡:
S′yd = ΣΔP′ (7)
由此可得到换热器之间的最低高差,合理布置换热设备。
工作计划
1) 2012年7月–2012年9月:进一步资料收集、整理、分析、确定热管换热
系统整机技术方案;
2) 2012年10月–2013年2月:完成热管换热装置的模拟计算分析和优化设计,
确定最优的结构参数,加工制作原理样机,并搭建完善实验测试台架;
3) 2013年3月 - 2013年7月:开展原理样机性能测试,与模拟计算结果对比,
分析进一步的优化方案;
4) 2013年8月 - 2013年11月: 确定实验样机的最终方案,包括工艺路线,
工艺材料的选取,加工制作实验样机;
5) 2013年12月 - 2014年3月:实验样机综合性能测试,确定型号;
6) 2014年4月 - 2014年6月:实验样机可靠性、稳定性测试;
7) 2014年7月 课题总结