催化裂化催化剂
催化裂化工艺催化剂的发展
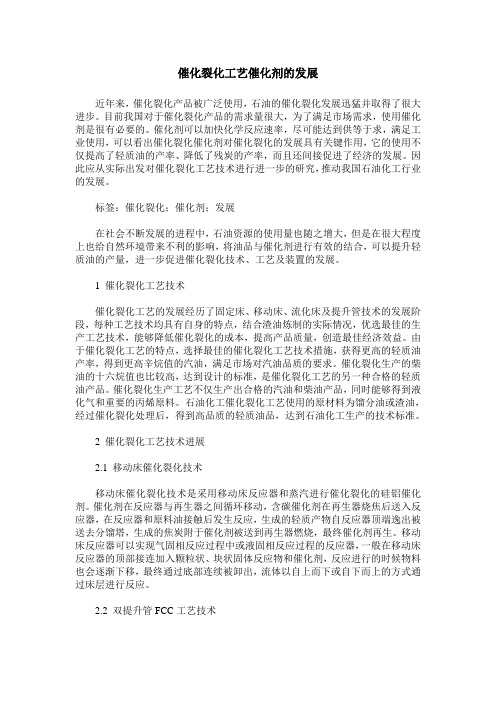
催化裂化工艺催化剂的发展近年来,催化裂化产品被广泛使用,石油的催化裂化发展迅猛并取得了很大进步。
目前我国对于催化裂化产品的需求量很大,为了满足市场需求,使用催化剂是很有必要的。
催化剂可以加快化学反应速率,尽可能达到供等于求,满足工业使用,可以看出催化裂化催化剂对催化裂化的发展具有关键作用,它的使用不仅提高了轻质油的产率、降低了残炭的产率,而且还间接促进了经济的发展。
因此应从实际出发对催化裂化工艺技术进行进一步的研究,推动我国石油化工行业的发展。
标签:催化裂化;催化剂;发展在社会不断发展的进程中,石油资源的使用量也随之增大,但是在很大程度上也给自然环境带来不利的影响,将油品与催化剂进行有效的结合,可以提升轻质油的产量,进一步促进催化裂化技术、工艺及装置的发展。
1 催化裂化工艺技术催化裂化工艺的发展经历了固定床、移动床、流化床及提升管技术的发展阶段,每种工艺技术均具有自身的特点,结合渣油炼制的实际情况,优选最佳的生产工艺技术,能够降低催化裂化的成本,提高产品质量,创造最佳经济效益。
由于催化裂化工艺的特点,选择最佳的催化裂化工艺技术措施,获得更高的轻质油产率,得到更高辛烷值的汽油,满足市场对汽油品质的要求。
催化裂化生产的柴油的十六烷值也比较高,达到设计的标准,是催化裂化工艺的另一种合格的轻质油产品。
催化裂化生产工艺不仅生产出合格的汽油和柴油产品,同时能够得到液化气和重要的丙烯原料。
石油化工催化裂化工艺使用的原材料为馏分油或渣油,经过催化裂化处理后,得到高品质的轻质油品,达到石油化工生产的技术标准。
2 催化裂化工艺技术进展2.1 移动床催化裂化技术移动床催化裂化技术是采用移动床反应器和蒸汽进行催化裂化的硅铝催化剂。
催化剂在反应器与再生器之间循环移动,含碳催化剂在再生器烧焦后送入反应器,在反应器和原料油接触后发生反应,生成的轻质产物自反应器顶端逸出被送去分馏塔,生成的焦炭附于催化剂被送到再生器燃烧,最终催化剂再生。
催化裂化的原料和产品及催化剂

催化裂化的原料和产品及催化剂一、催化裂化的原料催化裂化的原料范围广泛,可分为馏分油和渣油两大类.馏分油主要是直流减压馏分油(VGO),馏程350~500℃,也包括少量的二次加工馏分油如焦化蜡油等;渣油主要是减压渣油、脱沥青的减压渣油、加氢处理重油等。
渣油都是以一定的比例掺入到减压馏分油中进行加工,其掺入的比例主要是受制于原料的金属含量和残炭值.对于一些金属含量很低的石蜡基原油也可以直接用常压重油作为原料。
通常评价催化裂化原料的指标有馏分组成、特性因数K值、相对密度、苯胺点、残炭、含硫量、含氮量、金属含量等。
(一)馏分组成对于饱和烃类为主要成分的直流馏分油来说,馏分越重越容易分裂所需条件越缓和,且残炭产率也越高,对于芳烃含量较高的渣油并不服从此规律。
对于重质原料,密度只要小于0。
92g/cm3 ,对馏程无限制.(二)烃类族组成含环烷烃多的原料容易裂解,液化气和汽油产率高,汽油辛烷值也高是理想的催化裂化原料。
含烷烃多的原料也容易裂化,但气体产率高,汽油产率和辛烷值较低含芳烃多的原料,难裂化,汽油产率更低,液化气产率也低,且生焦多,生焦量与进料的化学组成有关。
烃的生焦能力:芳烃>烯烃>环烷烃>烷烃。
(三)残炭残炭值反映了原料中生焦物质的多少。
残炭值越大,焦产率就越高。
馏分油原料的残炭值一般不大于0.4﹪,而渣油的残炭值较高,一般都在0。
4﹪以上,致使焦炭产率高达10﹪(质)左右,热量过剩,因此解决取热问题是实现渣油催化裂化的关键之一。
目前我国已有装置能处理残炭量高达7%~8%的劣质原料。
(四)含硫、含氮化合物含硫量会影响裂化的转化率、产品选择性和产品质量.硫含量增加,转化率下降,汽油产率下降,气体产率产率增加。
原料中的含氮化合物,特别是碱性含氮化合物能强烈的吸附在催化剂表面,中和酸性中心,是催化剂活性下降;中性氮化物进入裂化产物会使油品安定性下降。
(五)金属金属包括碱性金属钠和铁、镍、钒、铜等重金属。
七钼酸铵 催化裂化 催化剂

七钼酸铵催化裂化催化剂
七钼酸铵是一种催化裂化催化剂,它在石油化工工业中扮演着重要的角色。
催化裂化是一种重要的炼油工艺,通过在高温和催化剂的作用下将重质石油馏分转化为轻质产品,比如汽油和液化石油气。
七钼酸铵作为一种催化剂,具有以下特点和作用。
首先,七钼酸铵具有高度的热稳定性和耐腐蚀性,这使得它在高温高压的催化裂化反应条件下能够保持稳定的催化活性,从而提高了反应过程的效率和产物质量。
其次,七钼酸铵催化剂能够在裂化反应中促进碳-碳键和碳-氢键的断裂,从而实现重质石油馏分向轻质产品的转化,提高了汽油和液化石油气的产量,满足了市场需求。
此外,七钼酸铵催化剂还具有良好的选择性,能够在裂化反应中选择性地生成所需的轻质产品,减少了副反应产物的生成,提高了产品的纯度和质量。
综上所述,七钼酸铵作为催化裂化催化剂,在石油化工工业中
具有重要的应用意义,它通过提高反应效率、产品产率和产品质量,为炼油工艺的发展和优化做出了重要贡献。
催化催化裂化技术

催化催化裂化技术催化裂化技术是一种重要的炼油工艺,可以将重质石油馏分转化为高附加值的轻质产品。
本文将从催化裂化技术的原理、应用和发展前景等方面进行探讨,以期为读者提供对该技术的全面了解。
一、催化裂化技术的原理催化裂化技术是通过催化剂的作用将重质石油馏分分解为较轻的产品。
其主要原理是在高温和高压的条件下,将原料油与催化剂接触,使其发生裂化反应。
这种反应可以将长链烃分子裂解成短链烃分子,从而提高汽油和燃料油的产率。
催化裂化反应主要分为两个阶段:热裂化和催化裂化。
在热裂化阶段,原料油在高温下分解成烃气和液体烃。
然后,在催化剂的作用下,烃气和液体烃进一步反应,生成较轻的产品,如汽油、液化气和柴油等。
二、催化裂化技术的应用催化裂化技术在炼油行业中具有广泛的应用。
首先,它可以提高汽油的产率。
由于汽车的普及,对汽油的需求量不断增加。
催化裂化技术可以将重质石油馏分转化为轻质的汽油,从而满足市场需求。
催化裂化技术可以生产出高质量的柴油。
在催化裂化过程中,石油馏分中的硫、氮和金属等杂质可以得到有效去除,从而提高柴油的质量。
这对于减少柴油排放的污染物具有重要意义。
催化裂化技术还可以生产出液化气、石脑油和石化原料等产品。
这些产品在化工、冶金和化肥等行业中具有广泛的应用。
三、催化裂化技术的发展前景随着能源需求的增加和石油资源的日益枯竭,催化裂化技术在未来的发展前景十分广阔。
一方面,随着汽车工业的高速发展,对汽油的需求将持续增加,催化裂化技术将成为满足市场需求的重要手段。
另一方面,随着环境保护意识的提高,对燃料油质量的要求也越来越高。
催化裂化技术可以提高燃料油的质量,减少对环境的污染,因此在未来的发展中具有重要的作用。
随着科技的不断进步,催化剂的研发和改进也将推动催化裂化技术的发展。
新型的催化剂可以提高反应的选择性和活性,从而提高产品的产率和质量。
催化裂化技术作为一种重要的炼油工艺,在提高石油产品产率和质量方面具有重要的作用。
催化裂化

制作:李向波
2
本章目录
概述 催化裂化化学反应原理
催化裂化催化剂
催化裂化工艺流程及主要设备 催化裂化工艺主要操作条件分析 催化裂化反应—再生系统仿真教学 反应—再生系统主要工艺计算简介 本章小结 练习题
3
1.了解催化裂化 工艺的发展,工 艺流程及主要设 备;
2.了解渣油催 化裂化反应存在 的困难及其加工 特点;
53
重催再生器需设取热设备:
a.内取热式
b.外取热式
54
主要要求有: ①再生剂的含炭量较低,一般要求低于0.2%,甚 至低于0.05%; ②有较高的烧碳强度,当以再生器内的有效藏量 为基准时,烧碳强度一般为100~250kg/(t.h);
③催化剂减活及磨损较少; ④易于操作,能耗及投资少;
33
5.筛分组成和机械强度
筛分组成一般要求在20~80μm之间 通常把催化剂粒度分成四个部分:0~20μm,20~40μm,
40~80μm,>80μm
适当的细粉(<40μm)含量可以改善流化质量,降低催化剂
损耗及提高再生效率,细粉在粗颗粒之间起了润滑作用,改
善了催化剂流化性能
采用“磨损指数”来评价微球催化剂的机械强度 通常要求微球催化剂磨损指数≯2
气经旋风分离器分出所夹带的 催化剂后经集气室去分馏系统;
由提升管快速分离器出来的催
化剂靠重力在沉降器中向下沉 降落入汽提段。
46
47
(3)汽提段
汽提段的作用是将待生催化剂携带 的油气汽提出来,增加产品收率,减 小再生器烧焦负荷。 催化剂携带的油气分两部分,一部 分是催化剂颖粒间的油气,另一部分
38
(二)裂化催化剂的再生
第三章催化裂化全

第三章催化裂化全第三章催化裂化第一节概述一. 催化裂化目的少图图3-5(a原油经过常减压蒸馏可以获得到汽油、煤油及柴油等轻质油品,但收率只有10~40%。
而且某些轻质油品的质量也不高,例如直馏汽油的马达法辛烷值一般只有40~60。
随着工业的发展,内燃机不断改进,对轻质油品的数量和质量提出了更高的要求。
这种供需矛盾促使炼油工业向原油二次加工方向发展,进一步提高原油的加工深度,获得更多的轻质油品并提高其质量。
而催化裂化是炼油工业中最重要的一种二次加工过程,在炼油工业中占有重要的地位。
催化裂化过程是原料在催化剂存在时,在470~530℃和0.1~0.3MPa的条件下,发生以裂解反应为主的一系列化学反应,转化成气体、汽油、柴油、重质油(可循环作原料或出澄清油)及焦炭的工艺过程。
其主要目的是将重质油品转化成高质量的汽油和柴油等产品。
由于产品的收率和质量取决于原料性质和相应采用的工艺条件,因此生产过程中就需要对原料油的物化性质有一个全面的了解。
二. 催化裂化原料、产品及特点1. 原料油来源催化裂化原料范围很广。
有350~500℃直馏馏分油、常压渣油及减压渣油。
也有二次加工馏分如焦化蜡油、润滑油脱蜡的蜡膏、蜡下油、脱沥青油等。
1)直馏馏分油一般为常压重馏分和减压馏分。
不同原油的直馏馏分的性质不同,但直馏馏分含烷烃高,芳烃较少,易裂化。
我国几种原油减压馏分油性质及组成见表3.1.1。
表3.1.1 国内几种减压馏出油性质及组成根据我国原油的情况,由表3.1.1可知,直馏馏分催化原料油有以下几个特点:①原油中轻组分少,大都在30%以下,因此催化裂化原料充足;②含硫低,含重金属少,大部分催化裂化原料硫含量在0.1%~0.5%,镍含量一般为0.1~1.0μg/g,只有孤岛原油馏分油硫含量及重金属含量高;③主要原油的催化裂化原料,如大庆、任丘等,含蜡量高,因此特性因数K也高,一般为12.3~12.6。
以上说明,我国催化裂化原料量大、质优,轻质油收率和总转化率也较高。
催化裂化增产丙烯助剂工业应用

催化裂化增产丙烯助剂工业应用摘要:催化裂化是炼油化工的重要工艺之一,通过提高催化剂的活性、降低烷烃损失和提高原料收率,可提高丙烯产量。
催化裂化催化剂具有较好的抗流行性,能较好地调节催化裂化反应催化剂的流变性质,可使烯烃损失减少、选择性提高或不降。
目前世界上使用和开发新的催化裂化催化剂已经超过了50种,各种新型催化剂在生产过程中往往会产生一系列副作用;开发新的催化剂不但可以提高装置的经济效益,还可以降低丙烯的损失比例。
因此开发具有优异性能的催化剂势在必行!本文以催化裂化装置为例进行介绍催化剂增强剂以其发展现状,希望能为国内的催化裂化催化剂生产企业的发展提供参考。
关键词:丙烯助剂;催化裂化;增产优化引言丙烯是三大合成材料中最主要的原材料之一,它是一种高聚合度的聚合物,可以用它来生产高附加值的聚丙烯。
FCC(催化裂化)技术是一项低投入的生产技术,其生产的产品一般都是弹性的,不需要复杂的工序,既能保证轻油收率,又能高效地将重油进行转换,且原材料的适应性广,可以实现二次处理。
在催化裂化制取丙烯时,通过添加丙烯助剂和工艺操作条件的优化,以达到提高丙烯产率的目的。
1催化裂化增产丙烯助剂简介及应用现状1.1催化裂化增产丙烯助剂简介催化裂化增产丙烯助剂(简称“催化剂增强剂”)主要用于减少丙烯损失、提高丙烯收率,具有很好的效果。
其作用机理为:(1)提高丙烯的转化率,通过增加转化率可以获得更多有用烯烃;(2)提高炼油装置丙烯生产能力,可以提高产品收率。
与传统增强剂相比,催化剂增强剂具有性能优异、成本低、用量少等特点.丙烯助剂优势为:(1)可有效提高选择性和产品收率;(2)提高产品质量和经济效益;(3)减少产品损失;(4)可以实现无污染生产过程;与现有技术相比较,提高产物收率和改善产品质量是更为可靠和可行和高效且经济的方法。
随着国家环保要求日益严格,催化裂化装置需要对催化剂进行升级。
近年来各大炼油厂在催化裂化装置中增加使用了一系列催化剂增强剂,实现了增产丙烯、改善产品质量及生产效率等诸多方面的提升。
第九章 催化裂化

图9-2-1 仲丙基正碳离子结构
典型的正碳离子是含有一个三价碳原子和 带一个正电荷的离子,即三配位正碳离子; 带一个正电荷的离子,即三配位正碳离子; 另外一种为五配位正碳离子, 另外一种为五配位正碳离子,通过配价键 结合,配位数高于通常的价键数。 结合,配位数高于通常的价键数。这些正 碳离子都是非常活泼的活性中间体。 碳离子都是非常活泼的活性中间体。
催化裂化反应是吸热反应, 催化裂化反应是吸热反应,其反应热一般为 吸热反应 400~700 kJ/kg原料,而催化剂再生所放出的热 ~ 原料, 再生所 原料 而催化剂再生 焦炭, 量为34000 kJ/kg焦炭,所以催化剂再生所放出的 焦炭 热量一般能够满足原料反应所需要的热量。 热量一般能够满足原料反应所需要的热量。 RFCC工艺往往还有富余的热量需要取出, 工艺往往还有富余的热量需要取出, 工艺往往还有富余的热量需要取出 再加以利用。催化剂在循环过程有一定的跑损, 再加以利用。催化剂在循环过程有一定的跑损, 跑损 需要不断地进行补充。 需要不断地进行补充。
三、催化裂化技术的发展状况
发展催化裂化技术的缘由: 发展催化裂化技术的缘由: 一方面由于直馏汽油和柴油在数量上不 一方面由于直馏汽油和柴油在数量上不 直馏汽油 能满足需要。 能满足需要。 另一方面直馏汽油的辛烷值太低, 另一方面直馏汽油的辛烷值太低,也不 直馏汽油的辛烷值太低 能直接作为汽油机的燃料。 能直接作为汽油机的燃料。
1、正碳离子的形成 、
裂化催化剂都属于固体酸类物质, 裂化催化剂都属于固体酸类物质,其表面既 固体酸类物质 质子酸( 简称B酸 中心, 有质子酸(Bronsted 酸,简称 酸)中心,又有 非质子酸(Lewis 酸,简称L酸)中心。这些酸中 非质子酸( 简称 酸 中心。这些酸中 心的存在,都会导致正碳离子的形成。 的存在,都会导致正碳离子的形成。
- 1、下载文档前请自行甄别文档内容的完整性,平台不提供额外的编辑、内容补充、找答案等附加服务。
- 2、"仅部分预览"的文档,不可在线预览部分如存在完整性等问题,可反馈申请退款(可完整预览的文档不适用该条件!)。
- 3、如文档侵犯您的权益,请联系客服反馈,我们会尽快为您处理(人工客服工作时间:9:00-18:30)。
催化裂化催化剂在通常的反应条件下,从热力学角度来判断,烃类可以进行分解、异构化、芳构化、氢转移、叠合、烃化等多种反应,但反应速度各异,这样就可以利用催化剂选择性地加速这些反应中所希望的反应,而抑制那些不希望发生的反应,从而达到提高产品质量改善产品分布的目的 ,这是热裂化过程所达不到的。例如为了提高汽油辛烷值,设法使催化剂能选择性加速异构化反应而抑制氢转移反应和不饱和烃进一步脱氢生焦的反应。催化剂基本术语比表面积:单位质量催化剂的内外表面积之和。孔体积:单位质量催化剂所含有的空隙体积。平均孔径:孔体积与比表面积之比。选择性:将进料转化为目的产品的能力。一、催化剂的种类、组成和结构1、分类 工业上所使用的裂化催化剂虽品种繁多,但归纳起来不外乎三大类:天然白土催化剂无定型合成催化剂分子筛催化剂。天然白土催化剂 工业催化裂化装置最初使用的经处理的天然白土,其主要活性组分是硅酸铝。无定型合成催化剂天然白土被人工合成硅酸铝所取代。特点:具有孔径大小不一的许多微孔,一般平均孔径为4—7 nm,比表面积可达500—700m2/g 。 硅酸铝的催化活性来源于其表面的酸性2、硅酸铝催化剂的结构
3、分子筛催化剂特点分子筛催化剂在催化裂化中的应用是催化裂化技术的重大发展。与无定型硅酸铝相比具有的特点: 具有更高的选择性、活性和稳定性,比表面600—800m2/g。分子筛是一种具有晶格结构的硅铝酸盐——又称沸石。重要特点:稳定、均一的微孔结构。有分子大小数量级。按其组成及晶体结构的不同可分为多种类型。分子筛催化剂 分子筛催化剂是60年代发展起来的一种新型的高活性催化剂。它的出现,使流化催化裂化工艺发生了很大变化,装置处理能力显著提高,产品产率及质量都得到改善。 分了筛又名结晶型沸石,是一种具有规则晶体结构的硅铝酸盐,在它的晶格结构中排列者整齐均匀,大小一定的孔穴,只有小于孔径的分子才能进入其中,而直径大于孔径的分子则无法进入。由于它能像筛子一样将直径大小不等的分子分开,因而得名分子筛。 催化裂化催化剂主要有四种Y型分子筛:REY;HY;RE-HY; USY型。一般催化裂化催化剂含分子筛为10—35%。
Y型分子筛的单元晶胞结构Y型分子筛由多个单元晶胞组成,每个单元晶胞由八个削角八面体组成,削角八面体的每个顶端是Si或Al原子,期间由氧原子相连接。由八个削角八面体组成的空洞称为八面沸石笼。人工合成的分子筛是含钠离子的分子筛,这种分子筛本身没有催化活性,分子筛中的钠离子可以用离子交换的方式与其他阳离子交换。以稀土金属离子置换 REY以氢离子置换 HY兼用氢离子和稀土金属离子置换 REHY由HY型分子筛经脱铝得到的更高硅铝比的超稳Y型分子筛。担体的作用:分子筛催化剂的活性比无定型硅酸铝催化剂的高得多,当用某些单体烃的裂化速度来比较时,某些分子筛的催化活性比硅酸铝高出上万倍,这样高的活性,在工业上无法进行应用,目前在工业上所用的分子筛催化剂中仅含有10%-35%的分子筛,其余的是起稀释作用的担体以及粘结剂。工业上广泛应用的担体是低铝硅铝酸和高铝硅铝酸。担体除了起稀释作用外,还有其他重要作用:在离子交换时,分子筛中的钠不可能完全被置换掉,而钠的存在会影响分子筛的稳定性,担体可以容纳分子筛中未除去的钠,从而提高了分子筛的稳定性。在再生和反应时,担体作为一个宏大的热载体,起到热量储存和传递的作用。适宜的担体可以增强催化剂的机械强度。分子筛的价格较高,使用担体可降低催化剂的生产成本。对于重油催化裂化,担体可以先使难以进入分子筛的大分子先进行裂化,生成小分子再进入分子筛。二、催化剂的使用性能1)物理性质A、密度(真实密度、颗粒密度、堆积密度)B、筛分组成和机械强度C、结构特性(比表面、孔体积、孔径)2)化学性质A、活性B、选择性C、稳定性D、抗金属污染能力(污染指数)催化剂的密度真实密度又称骨架密度:颗粒的质量与骨架实体所占体积之比,一般在2—2.4g/cm3。颗粒密度:把微孔体积计算在内的单个颗粒的密度,一般在0.9—1.2g/cm3 。堆积密度:催化剂堆积时包括微孔体积和颗粒间的孔隙体积的密度,一般在0.5—0.8g/cm 。筛分组成筛分组成 一般催化裂化催化剂的粒径分布范围在:20--100μm。分布是: 40---80 μm 占50%;20---40 μm 占25% 80---100 μm 占25%。<20 μm和>100 μm很少。工业用分子筛裂化催化剂的种类1、REY型分子筛催化剂 酸性中心多、氢转移反应能力强,裂化活性高、水热稳定性好、汽油收率高,但焦炭和干气的产率也高,汽油的辛烷值低。适用于直馏瓦斯油原料。2、USY型分子筛催化剂 硅铝比高、结构稳定性好、耐热和抗化学稳定性增强,酸性中心数目减少,降低了氢转移反应活性,产物中烯烃含量增加,汽油辛烷值提高,焦炭产率减少。3、REHY型催化剂 兼顾了REY和HY分子筛的优点,活性和稳定性低于REY分子筛。RE和H的比例可以根据需要调节。
催化剂的活性催化剂的活性过高对催化裂化不利转化率提高,汽油的选择性下降,气体和焦炭增多。产生气体使气压机,吸收等超负荷运行,有破坏性。焦炭增加会增加再生器的负荷。催化剂的失活 结焦失活 :催化裂化反应生成的焦炭沉积在催化剂的表面,覆盖催化剂的活性中心,使催化剂的活性和选择性下降。随着反应的进行,催化剂上沉积的焦炭增多,失活程度也加大。 工业催化裂化所产生的焦炭可认为包括四类焦炭: ①催化焦——烃类在催化剂活性中心上反应前生成的焦炭。 ②附加焦——原料中的焦炭前身物经缩反应产生的焦; ③可汽提焦——因在汽提段汽提不完全而残留在催化剂 上的重质烃类。 ④污染焦——由于重金属沉积在催化剂表面上促进了脱 氢和缩合反应而产生的焦。水热失活:在高温下,特别是有水存在的条件下,裂化催化剂的表面结构发生变化,比表面积减小、孔容减小,分子筛的晶体结构破坏,导致催化剂的活性和选择性不断下降, 过程比较慢。毒物失活 :对催化裂化催化剂的毒物主要是某些金属和碱性氮化物。几种重金属中,以镍、钒的影响最为重要。而且已老化的重金属的污染作用要比新沉积金属的作用弱得多。由于结焦而丧失活性的催化剂,可以再生。由于结构变化和金属污染的催化剂不能再生。催化剂的活性过高有什么不好?1、催化剂的活性越高,转化率就越高,随着转化率的提高,汽油的选择性急剧下降,而生成了大量的气体和焦炭。2、大量的气体将使原设计的气压机、吸收稳定系统以及气体处理装置超负荷运行,甚至严重破坏平衡操作,损坏设备。3、大量的焦炭将增加再生器的焦炭负荷,这样就会受到主风机功率和再生温度的限制。由于主风机的限制,就必须降低进料量,虽然提高了转化率,但降低了汽油的净产量。怎样控制催化剂的活性?控制催化剂活性的过高的最简单的方法就是降低再生器的燃烧强度,使再生催化剂炭含量增加,再生催化剂炭含量增加会造成以下影响:1、选择性降低,生焦率增高,汽油产率下降。2、如用降低氧含量的方法,则烟气中CO含量增高,使环保出现问题。3、对于某些独特的催化剂,将大幅度降低其抗金属污染能力。催化剂流态化基本原理固定床:固体粒子处于堆紧状态,颗粒静止不动的床层,叫做固定床。床层的压降随流体流速的增加而增加。移动床:流体和固体颗粒同时进入反应器,他们互相接触,一面进行反应,一面颗粒移动这种反应床层叫做移动床。流化床:床层颗粒之间脱离接触,颗粒悬浮在流体中,往各个方向运动的床层叫做流化床。床层高度和空隙率随流速增大而增大,但床层压降基本不随流速而变。散式流化床: 固体颗粒脱离接触,但颗粒分布均匀,颗粒间充满流体,无颗粒与流体的聚集状态,此时已具有一些流体性能。鼓泡床: 随着气速增加,固体颗粒脱离接触,但流化介质气体出现集聚相,称为气泡。此时由于气泡在床层表面处破裂,将部分颗粒带到表面稀相空间的稀相区,此时稀相区内含颗粒量较少。湍动床: 气速增大到一定限度时,由于气泡不稳定性,而使气泡分裂产生更多小气泡,床层内循环加剧,气泡分布较前为均匀,床层由气泡引起的压力波动减小,表面夹带颗粒量大增。工业上流化床再生器属于这种。快速床: 气速uf再增大,气体夹带固体量已达到饱和夹带量,密相床已不能继续维持而要被气流带走, 使密相床层要靠固体循环量来维持。催化裂化装置中的烧焦罐操作属于这种。输送床: 靠循环量也无法维持床层,已达到气力输送状态,提升管反应器属于输送床流化。流化床反应器的特点1、由于流化床的传热速率高和返混,床层各部分的温度比较均匀,避免了局部高温现象,因此对强放热反应,例如再生反应,可以采用较高的再生温度以提高烧碳速率。2、流化床中气泡的长大、气节和沟流的发生,使气体与固体颗粒接触不充分对反应不利。3、流态化使固体具有像流体那样的流动性,装卸、输送都较为灵活方便,这对需要大量固体颗粒循环的反应系统很有利。4、有一些固体被带入稀相,进而带出反应器。5、固体颗粒的激烈运动加剧了对设备的磨损,也使催化剂的粉碎率增大,加大了催化剂的损耗临界流化速度和终端速度
平均粒径 提升管中的气一固流动(垂直管中的稀相输送)提升管中的气速比流化床高得多,工业装置一般采用油气进口处的线速为4.5~7.5m/s。由于在向上流动的过程中反应生成的小分子油气增加,气体体积增大,因此在提升管出口处的气体线速增达到8~18m/s,催化剂也由比较低的初速度逐渐加快到接近油气的速度。催化剂颗粒是被油气携带上去的,它的上升速度总是要比气体的速度低些,这种现象称作催化剂的滑落。 而气体线速uf与催化剂线速us之比则称为滑落系数。在催化剂被加速之后,催化剂的速度应等于uf与催化剂的自由降落速度ut之差,因此,
滑落系数 当ut增大时,滑落系数减小,当uf很大 时,滑落系数趋近于1,也就是us趋近于uf,此时催化剂的返混现象减小至最低程度。催化剂的循环 流化催化裂化装置的催化剂循环采用密相输送的办法,在Ⅳ型催化裂化装置采用U形管输送,而在提升管催化裂化装置则采用斜管或立管输送。在输送管内,固体浓度约400~600kg/m3,故称为密相输送。