1、组对焊接作业指导书
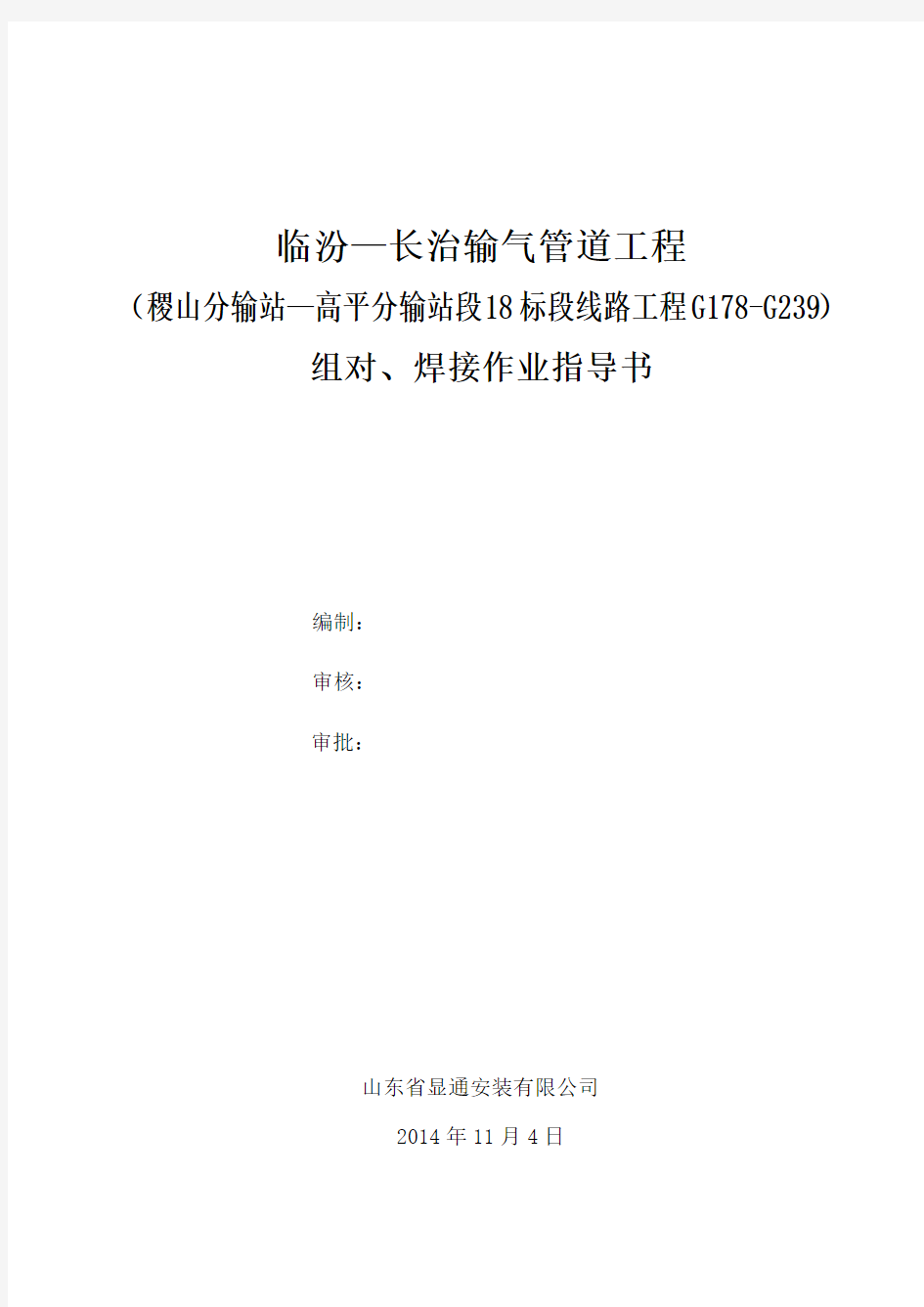
- 1、下载文档前请自行甄别文档内容的完整性,平台不提供额外的编辑、内容补充、找答案等附加服务。
- 2、"仅部分预览"的文档,不可在线预览部分如存在完整性等问题,可反馈申请退款(可完整预览的文档不适用该条件!)。
- 3、如文档侵犯您的权益,请联系客服反馈,我们会尽快为您处理(人工客服工作时间:9:00-18:30)。
临汾—长治输气管道工程
(稷山分输站—高平分输站段18标段线路工程G178-G239)
组对、焊接作业指导书
编制:
审核:
审批:
山东省显通安装有限公司
2014年11月4日
一、管道焊接为特殊过程、焊接质量的好坏直接影响到管线的安全性、使用寿命。因此应重点控制:
1)参加施焊的焊工必须是经过培训取得专业资格证书,同时通过针对当前施工管线
焊接要求考试的合格者,并且只能操作考试所通过的项目;
2)所用焊机须是完好设备,设备性能满足焊接工艺的要求,且电流电压输出性能稳
定,调整时准确到位,严格控制在焊接工艺规程规定的数值内(具体数值见附表);
3)所用焊材与设计要求相符,且通过焊接工艺评定,满足设计要求,焊材使用前有
须经过烘干,施工单位须配备有性能、容量满足设计和施工要求的烘箱、保温箱
等,并且配有专人负责焊条的烘干、收发、回收,并有记录。焊条药皮应无破损、发霉、油污、锈蚀、裂纹、偏心,焊丝无锈蚀、折弯,焊剂无变质现象。每位焊
工须配备保温防潮焊条筒,随用随取随关闭焊条筒,防止焊条受潮。若用气体保
护焊,所用气体的纯度和干燥度应满足焊接规程的要求(焊接材料详见附表);
4)在下列任何一种环境中,如未采取有效防护措施不得进行焊接:
雨天或雪天;
大气相对湿度超过90%;
药皮焊条手工焊时,风速超过8m/s;
气体保护焊,风速超过2m/s;
环境温度低于焊接规程中规定的温度。
二、焊接一般分为根焊、填充焊、盖面焊三个层次,根据壁厚的不同,每个层次的焊道数也有不同,同时每个层次所用焊条型号、电流、电压、焊接速度也有不同,因此焊接时一般采用流水作业方式,可采用两焊工为一组,有几个层次,分几个组,每组焊工在管两侧同时施焊。
三、坡口加工和接头组对
1) 等壁厚管子组焊时,应做到内壁齐平,内壁错边量不超过管壁厚度的10%,
且不大于1mm。
2) 不等壁厚的管段组焊时,壁厚错边量不超过管壁厚度的10%,不等壁厚对焊管
端宜增加过渡段或在管端壁厚较厚的一侧加工内坡口,使其平滑过渡。
3) 当相连管子的屈服强度不同时,则所使用的焊条金属的机械性能至少应与强度
较高的钢管的机械性能相等。
4) 在连接面的焊缝边缘上,不得有尖锐的缺口或划槽。
5) 管子组装前,必须有专人检查管子是否畅通,收工前必须对组焊好的管段的端
头进行封堵,防止杂物进入管内。
6) 管子组对时,两管的螺旋缝错开的距离不得小于100mm,两个环焊缝之间的
直管段长度不应小于600mm。
7)管口如有轻度变形可用专用工具校正,不得用锤直接敲击管壁,校正后的管口
周长差不超过管径的1%,错口误差小于管径的3‰,如有损坏,应将变形部分管段切掉,并重新加工。
四、管线组装焊接
1) 管道组装前,应将管内污物清理干净,并将管端20mm以内的油污、浮锈、熔渣
等清除干净,并不得有裂纹、夹层等缺陷。
2) 管线组焊时,为防止焊接出现裂纹及减少内应力,不得采用任何方式的强行组对。
3) 弹性敷设管道与相邻的反向弹性弯管之间以及弹性弯管和人工弯管之间应用直管
段连接,直管段长度不应小于600mm。
4) 管道焊接应采用多层焊接,严禁一次堆焊。施工时层间熔渣应清除干净,并进行
外观检查,合格后方可进行下一层焊接。
5) 管线焊接时,每道焊口必须连续一次焊完,焊道层与层之间的间隔时间采用下向
焊时应小于或等于3~4min,采用上向焊时应≤5min。
6) 不准在同一焊道上使用不同牌号的焊条。各层间接头必须错开20~30mm,。每
焊完一道焊缝应在气流方向上方距焊口100mm处用塑模打上施焊焊工的代号,并做好记录。管道焊接间断时间两小时以上时,必须用盲板临时封堵管端,防止杂物进入管内。
7) 施焊时,环境温度若低于5℃,L450钢级应在焊口中心的两侧各50mm内的管段
上均匀预热至100~150℃,且焊接过程中的层间温度不应低于预热温度。
8) 根据试焊评价确定焊接工艺方法,需要对异种金属在焊接进行预热时,预热温度
应按可焊性较差一侧的钢材确定。
9) 应采取保护措施防止雨、雪、风沙对焊接质量的影响,在未具备保护措施之前,
不得施焊。
10) 凡是用内对口器组装管道,可不进行点焊。第一遍焊接不低于该焊口总长度的
50%,对口器卸走后,继续完成根焊。而用外对口器或无对口器组装时应进行点焊,点焊应均布4~6处,点焊总长度不小于焊道总长度的50%。
11) 不得在管壁和非施焊处引弧和试验电流,凡是被电弧烧伤造成的管壁伤痕都应
用砂轮磨去,打磨后的管壁厚度不得低于管壁厚度的90%,否则应将该段管子切除。
12)每遍焊完后焊工应认真检查清根,除去表层气孔、夹渣等缺陷,砂轮粉末也应
清除;
13)使用的焊条直径、焊接极性、电流、电压、焊接速度、运条方法等应符合焊接
工艺规程要求(具体数值见附表);
五、焊缝的检查和验收
1)焊缝外观成型均匀一致,焊缝及热影响区表面上不得有裂纹、未熔合、气孔、夹
渣、飞溅、夹具焊点等缺陷;
2)焊缝表面不应低于母材表面,焊缝余高一般不应超过2mm,局部不得超过3mm,余
高超过3mm时,应进行打磨,打磨后应与母材圆滑过渡,但不得伤及母材;
3)焊缝表面宽度每侧应比坡口表面宽0.5mm至2mm;
4)咬边的最大尺寸应符合焊接工艺规程的规定;
5)电弧烧痕应打磨掉,打磨后应不使剩下的管壁厚度减少到小于材料标准允许的最
小厚度。否则,应将含有电弧烧痕的这部分管子整段切除。
六、管道焊接完后,应按规定的方法和焊接要求在焊口附近做出标识,