企业产能分析
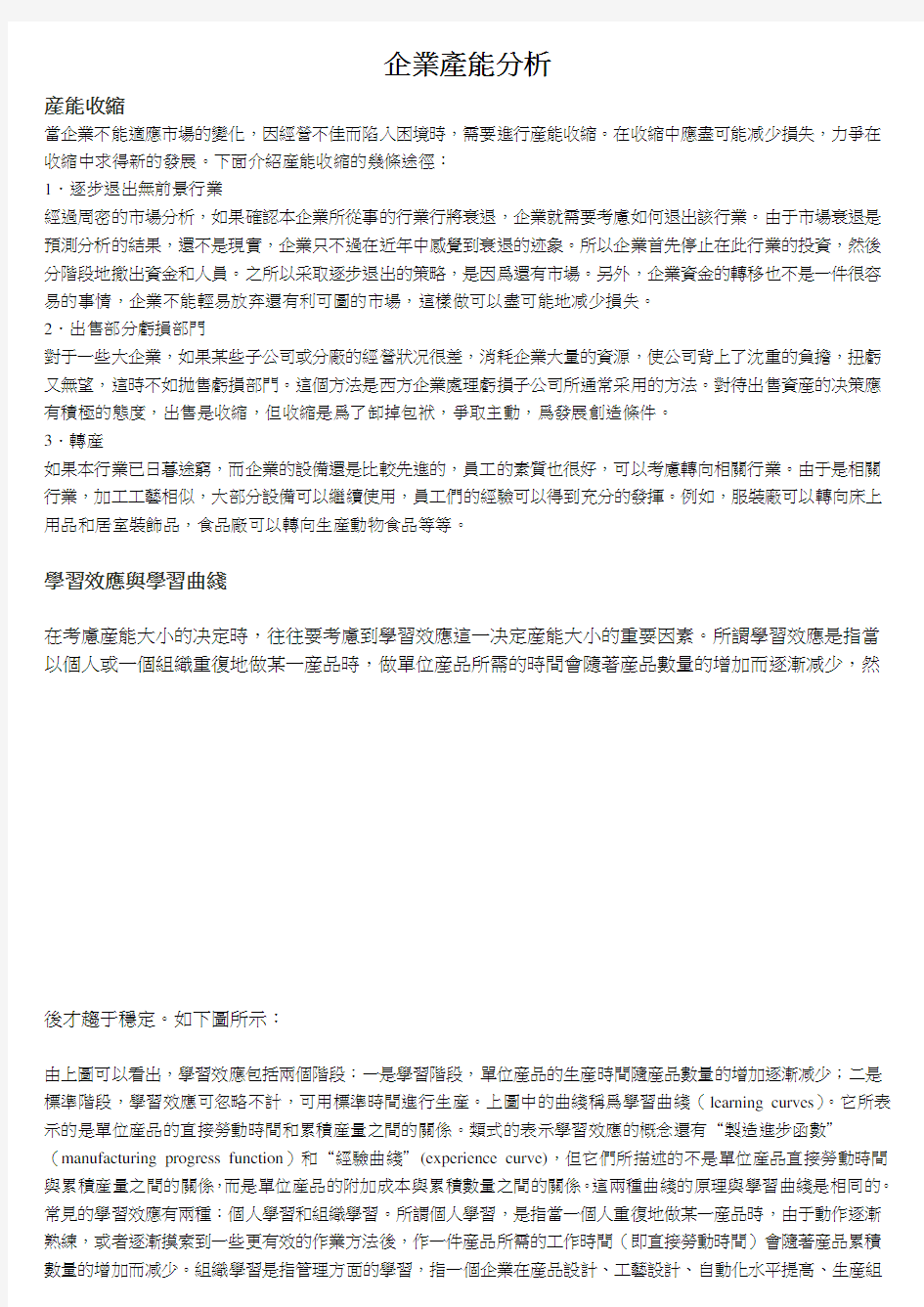

企業產能分析
産能收縮
當企業不能適應市場的變化,因經營不佳而陷入困境時,需要進行産能收縮。在收縮中應盡可能减少損失,力爭在收縮中求得新的發展。下面介紹産能收縮的幾條途徑:
1.逐步退出無前景行業
經過周密的市場分析,如果確認本企業所從事的行業行將衰退,企業就需要考慮如何退出該行業。由于市場衰退是預測分析的結果,還不是現實,企業只不過在近年中感覺到衰退的迹象。所以企業首先停止在此行業的投資,然後分階段地撤出資金和人員。之所以采取逐步退出的策略,是因爲還有市場。另外,企業資金的轉移也不是一件很容易的事情,企業不能輕易放弃還有利可圖的市場,這樣做可以盡可能地减少損失。
2.出售部分虧損部門
對于一些大企業,如果某些子公司或分廠的經營狀况很差,消耗企業大量的資源,使公司背上了沈重的負擔,扭虧又無望,這時不如抛售虧損部門。這個方法是西方企業處理虧損子公司所通常采用的方法。對待出售資産的决策應有積極的態度,出售是收縮,但收縮是爲了卸掉包袱,爭取主動,爲發展創造條件。
3.轉産
如果本行業已日暮途窮,而企業的設備還是比較先進的,員工的素質也很好,可以考慮轉向相關行業。由于是相關行業,加工工藝相似,大部分設備可以繼續使用,員工們的經驗可以得到充分的發揮。例如,服裝廠可以轉向床上用品和居室裝飾品,食品廠可以轉向生産動物食品等等。
學習效應與學習曲綫
在考慮産能大小的决定時,往往要考慮到學習效應這一决定産能大小的重要因素。所謂學習效應是指當以個人或一個組織重復地做某一産品時,做單位産品所需的時間會隨著産品數量的增加而逐漸减少,然
後才趨于穩定。如下圖所示:
由上圖可以看出,學習效應包括兩個階段:一是學習階段,單位産品的生産時間隨産品數量的增加逐漸减少;二是標準階段,學習效應可忽略不計,可用標準時間進行生産。上圖中的曲綫稱爲學習曲綫(learning curves)。它所表示的是單位産品的直接勞動時間和累積産量之間的關係。類式的表示學習效應的概念還有“製造進步函數”(manufacturing progress function)和“經驗曲綫”(experience curve),但它們所描述的不是單位産品直接勞動時間與累積産量之間的關係,而是單位産品的附加成本與累積數量之間的關係。這兩種曲綫的原理與學習曲綫是相同的。常見的學習效應有兩種:個人學習和組織學習。所謂個人學習,是指當一個人重復地做某一産品時,由于動作逐漸熟練,或者逐漸摸索到一些更有效的作業方法後,作一件産品所需的工作時間(即直接勞動時間)會隨著産品累積數量的增加而减少。組織學習是指管理方面的學習,指一個企業在産品設計、工藝設計、自動化水平提高、生産組
織以及其他資本投資等方面的經驗累積過程,也是一個不斷改進管理方法,提高人員作業效率的過程。比如上圖所示的學習曲綫,既可以是組織學習的結果,也可以是個人學習的結果,還可以是兩種學習結果的叠加。
短期産能調整方法
短期産能調整的方法主要有:
1.利用庫存調節生産能力
如果企業的産品具有季節性,銷售旺季與淡季的銷售量相差很大,旺季時,生産能力不足,淡季時,能力過剩,用庫存來平衡能力與需求量之間的缺口是比較常用的方法。這種方法利用了製造業的産品具有可儲存的特點而設計的。例如空調器的旺季是6、7、8三個月份,銷售量占到全年總量的一半以上,而企業的月生産能力遠遠小于旺季時的月需求量。這時企業除了開足馬力加緊生産以外,主要靠淡季多生産一些儲存起來,以彌補旺季時能力的不足。假如産品有保質期限制,如食品廠,應謹慎地采用這種方法。
2.變動勞動時間調節生産能力
生産能力與設備開動時間成正比,有許多企業只開一班,當能力不足時,首選方案便是加班。這時的主要問題是勞動力能否承受較長時期的加班。根據國家法律,我國實行一天8小時工作制,一周40小時工作制,臨時加班是允許的,持續數周加班,員工的生理無法承受,法律也不允許。這時可考慮招收部分臨時工。如果企業是勞動力密集型,除了合理加班以外,只能招收臨時工增加生産能力。
3.利用外部資源增加生産能力
當生産能力短期內不足時,采取臨時性外協的方法,甚至外購的方法也可以解决供需矛盾。現在有許多成品製造企業,能力不足時,大量零部件通過外協解决。需求不足時,又收回外協任務,改爲自製。這樣做固然可以解决一時的供需矛盾,從長遠看會失去企業間的信任,以後沒有企業會與你協作。因此,企業在作能力計劃時也要考慮這些因素。
4.推遲交貨期
如果企業是按照訂貨單來排生産計劃的,那麽在銷售旺季可以采用推遲交貨期的方法來緩解供需矛盾。推遲交貨會影響企業信譽,這也是不得已而爲之。爲了盡可能减少損失,在接受訂貨時就應該準確計算交貨期,或者在價格上做適當的讓步。
由于短期內可動用設備數量基本不變,生産能力的調整與人的主動性、積極性有很大關係,如果員工的積極性能够充分地調動起來,10%的能力缺口是不難平衡的。在西方發達國家,企業已開始注意培養員工的主人翁精神,當生産能力短時不足時,要求員工能够自覺地以生理極限克服短時的能力不足。更進一步講,處于生産第一綫的員工,對生産過程最熟悉,對設備性能最瞭解,對如何提高生産能力他們最有辦法。所以如何通過制度的、企業文化的、教育的手段,培養職工的主人翁精神,對于克服短期能力不足的矛盾是十分有效的。
利用决策樹評價生産方案
决策樹是確定生産能力方案的一條簡捷的途徑。决策樹不僅可以幫助人們理解問題,還可以幫助人們解决問題。决策樹是一種通過圖示羅列解題的有關步驟以及各步驟發生的條件與結果的一種方法。近年來出現的許多專門軟件包可以用來建立和分析决策樹,這樣,利用這些專門軟件包,解决問題就變得更爲簡便了。
决策樹由决策結點、機會結點與結點間的分枝連綫組成。通常,人們用方框表示决策結點,用圓圈表示機會結點,從决策結點引出的分枝連綫表示决策者可作出的選擇,從機會結點引出的分枝連綫表示機會結點所示事件發生的概率。
在利用决策樹解題時,應從决策樹末端起,從後向前,步步推進到决策樹的始端。在向前推進的過程中,應在每一階段計算事件發生的期望值。需特別注意,如果决策樹所處理問題的計劃期較長,計算時應考慮資金的時間價值。計算完畢後,開始對决策樹進行剪枝,在每個决策結點删去除了最高期望值以外的其他所有分枝,最後步步推進到第一個决策結點,這時就找到了問題的最佳方案。
下面以南方醫院供應公司爲例,看一看如何利用决策樹作出合適的生産能力計劃。
南方醫院供應公司是一家製造醫護人員的工裝大褂的公司。該公司正在考慮擴大生産能力。它可以有以下幾個選擇:什麽也不做;建一個小廠;建一個中型廠;建一個大廠。新增加的設備將生産一種新型的大褂,目前該産品的
潜力或市場還是未知數。如果建一個大廠且市場較好就可實現$100,000的利潤。如果市場不好則會導致$90,000的損失。但是,如果市場較好,建中型廠將會獲得$40,000,市場不好則損失$5,000。當然,還有一個選擇就是什麽也不幹。最近的市場研究表明市場好的概率是0.4,也就是說市場不好的概率是0.6。參下圖:
在這些數據的基礎上,能産生最大的預期貨幣價值(EMV)的選擇就可找到。
EMV(建大廠)=(0.4)*($100,000)+(0.6)*(-$90,000)=-$14,000
EMV(中型廠)=(0.4) *($ 600,000))+(0.6)* (-$10,000)=+$18,000
EMV(建小廠)=(0.4)* ($40,000)+(0.6)*(-$5,000)=+$13,000
EMV(不建廠)=$0
根據EMV標準,南方公司應該建一個中型廠。
經驗曲綫
經驗曲綫是一個人們較爲熟知的概念。一家工廠生産某種産品的數量越多,生産者就能更多地瞭解了如何生産該産品,從生産中獲得的經驗也就越來越多。那麽,在以後的生産中,工廠可以有目的地幷且較爲準確地减少該産品的生産成本。每當工廠的累積産量增大一倍時,其生産成本就可以降低一定的百分比(該百分比的具體大小因行業不同而有所差別)。
下圖表明在生産某産品的過程中,90%的經驗曲綫是如何對生産成本産生影響的。
生産能力的步驟確定
在計算生産能力時,必須瞭解每條獨立生產綫的情况、每家獨立工廠的生産水平以及整個生産系統的生産分配狀况,一般可通過以下步驟來進行:
1)運用預測技術預測每條獨立生產綫的産品的銷售情况;
2)計算爲滿足需求所需投入的設備和勞動力數量;
3)合理配置可獲得的設備與勞動力數量。
之後,企業常常還要考慮一個生産能力余量作爲平衡設計生産能力與實際生産能力的緩衝。生産能力餘量是指超過預期需求的生産富餘能力。例如,某産品的預計需求爲1000萬,而設計生産能力爲1200萬。這樣,生産能力餘量爲20%,即企業是以83%的生産能力利用率生産該産品。相反,如果一家企業的設計生産能力低于爲滿足産品需求應達到的生産能力,則說明該企業的生産能力餘量爲負值。比如一家企業的産品年需求量爲1200萬,而其生産能力僅爲1000萬,則該企業的生産能力餘量-20%。
生産能力調節因素
可由企業對生産能力加以調節控制的因素很多。從計劃的觀點看,可將這些因素按取得能力的時間長短,分爲長期、中期和短期三類。
1、長期因素
取得生産能力的時間在一年以上的都可歸入長期因素。它們包括:建設新廠、擴建舊廠、購置安裝大型成套設備、進行技術改造等。這些措施都能從根本上改變生産系統的狀况,大幅度地提高生産能力,但同時也需要大量的資金投入。應用這些因素屬于戰略性决策。
2、中期因素
在半年到一年之內對生産能力發生影響的那些因素爲中期因素。如采用新的工藝裝備、添置一些可隨時買到的通用設備,或對設備進行小規模的改造或革新;增加工人,以及將某些生産任務委托其他工廠生産等,其中,也包括利用庫存來調節生産的作用。這些因素是在現有生産設施的基礎上所作的局部擴充。它們屬于中層管理的决策。一般在年度生産計劃的制定與實施中加以考慮。
3、短期因素
在半年之內以至當月就能對生産能力産生影響的屬于短期因素。這類因素很多,如:
1)加班加點;
2)臨時增加工人,增開班次;
3)采取措施降低廢品率;
4)改善原材料質量;
5)改善設備維修制度。這能减少設備故障時間,提高設備利用率而提高生産能力;
6)采用適當的工資獎勵制度,激發工人的勞動積極性,在短時間內提高生産;
7)合理選擇批量。批量選擇的不同會影響設備調整時間的變化。合理選擇批量能减少不必要的設備調整時間,而提高設備利用率,即提高了設備的生産能力;
生産能力的短期調節因素是對現有生産設施利用的改善,都屬于作業層的决策。
生産能力柔性
生産能力柔性(capacity flexibility)是指(企業)具有迅速提高或降低生産水平,或者迅速地將生産能力從一種産品(服務)轉移到另一種産品(服務)的能力。實現生産能力柔性的途徑主要有:柔性工廠、柔性生産過程和柔性工人。
柔性工廠是實現生産能力柔性的一個途徑。柔性工廠實際上是一種“零時轉換工廠”,在那裏,有可自由移動的機器設備、易拆裝的隔墻以及隨時可以獲得幷且便于重新組合的生産用件,從而實現工廠的零時生産轉換。如同服務機構可以很好地把握顧客口味的變化幷依此變化改變其服務方式一樣,柔性工廠也可以靈活拆卸組裝及移動機器設備,改變生産方式,生産不同産品。
柔性生産過程也是實現生産能力柔性的一種途徑。柔性的生産製造系統再加上易拆裝的機器設備,就構成了柔性生産過程。通過柔性生産過程,工廠可以迅速且低費用地在不同種類的産品間轉換生産。這樣也就實現了人們所說的“範圍經濟性”,範圍經濟性是指多種産品在一起混合生産時耗費的成本低于單獨生産這些産品時的成本。
柔性工人是實現生産能力柔性的另一種途徑。柔性操作工人需要掌握多種技術,以便隨時從一個工種轉換到另一
個工種上。他們不再是某項專業工人,而是經過了多種培訓的工人。同時,柔性操作工人的工作還需要有主管人員和其他職員的靈活配合。
學習率的確定
如果數據齊備且合理,那麽學習率就可利用下式所示的模型來求解:
kn=k1·nb
式中,k1--第一個産品的直接勞動時間;
kn--第n個産品的直接勞動時間;
n--累積的生産數量;
b--等于lgr/lg2;
r--學習率。
求解的步驟包括兩步:
1)計算b的值,其公式爲:b=lg(kn/k1)lgn
2)根據b的定義求解學習率r,其公式爲:r=10(blg2)
如果沒有上述數據,即在某種産品未開始生産之前就想估計學習率,這種估計通常帶有較强的主觀性。在這種情况下有兩種估計方法,一是根據本企業過去生産過的類似産品進行估計。如果工藝等比較類似,就認爲具有相同的學習率。二是把它看作與該産業平均學習率相同。無論采用哪種方法,在實際生産開始、積累了一定數據以後,都需要對最初的估計加以修正。這裏有幾個要注意的問題:
1)盲目地接受産業平均學習率有時是很危險的,因爲對于不同的企業,有時會有相當不同的學習率;
2)影響各企業學習率的主要因素之一是看生産運作是以設備速率爲基礎,還是以人的速率爲基礎,在以設備速率爲基礎的生産運作中,直接勞動時間减少的機會較有限。因爲在這種情况下,産出速度主要取决于設備能力,而不是人的能力。在一個生産運作系統中,以人的速率爲基礎的生産運作所占的比例越大,直接勞動時間中所反映出來的學習效應也就越强;
3)影響學習率的另一個因素是産品的複雜性。簡單産品的學習率不如複雜産品那麽顯著。複雜産品在它的整個壽命周期中通常有更多的機會來改進工作方法,改進材料,改變工藝流程等。也就是說,複雜産品的組織學習率通常更高,特別是在沒有相似産品生産經驗的情况下,學習率更高;
4)資本投入的比率也會影響學習率。這是指自動化程度的提高或設備的改善會使直接勞動時間减少,從而使學習曲綫發生一定變化。因此,當根據過去類似産品的經驗估計學習率時,必須考慮到資本投入比率的影響。
學習曲綫的發現與運用
學習曲綫最早産生于二次世界大戰時的飛機製造業.當時發現生産每架飛機所需的直接勞動時間隨著飛機累積數量的增加很有規律地减少,,這些結果可繪製成一系列的學習曲綫.一項對各主要飛機製造廠所作的調查都表明了類似的結果,無論所製造的飛機是戰鬥機、轟炸機還是其他。另一個獨特的發現是這些曲綫之間也有很大的類型性,即無論生産第一架飛機所用的時間是多少,第8架所需的時間只是第4架的80%,第12架所需的時間只是第6架的80%,等等。也就是說,在任何一種情况下所發生的現象都是,當産量增加一倍時,所需生産時間就减少了20%。由于這種改進的速率非常一致,由此又産生了“學習率”的概念,即在飛機生産中,産量加倍過程中的學習率是80%。不同産品或不同企業,學習率有可能不同。
學習曲綫可以運用與許多領域。首先,在生産運作能力管理中,學習曲綫可以用來幫助企業較精確地估計對生産能力的需求,制定相應的能力計劃;其次,學習曲綫可以用來幫助企業制定産品的成本計劃,因爲根據學習效應,可估計隨著累積産量的增加成本降低的可能性;此外,根據學習效應理論,當一個企業競爭策略的重點放在低成本上時,爲了維持一定的利潤,必須有足够的産量,企業通常總是儘快增加産量,以使得成本降至學習曲綫的低點。學習曲綫這樣一種學習效應對于防止競爭對手進入自己的市場也是很有用的。例如,在電子元器件工業,開發一種集成電路的成本是昂貴的,因此産品最初的價格往往很高,但隨著産品累積生産數量的增加,成本會迅速下降,從而價格也降下來,這對于先開發産品、先進入市場的企業十分有利。而後來的參入這一開始就必須以低價格在市
場上出現,但已開始的生産成本是很高的,這種學習階段的價格低于成本的損失,只能由其自己承擔。
當然,從另一方面來說,學習曲綫如使用不當也是有一定風險的。這是指管理人員往往容易忘記環境動態變化的特性,在這種情况下,環境變化中的不測因素有可能影響學習規律,從而給企業帶來損失。一個著名事例是道格拉斯飛機製造公司被麥克唐納兼幷的事例。道格拉斯飛機曾經根據學習曲綫估計它的某種新型噴氣式飛機成本能够降低,于是對顧客許諾了價格和交貨日期,但是飛機在製造過程中不斷地修改工藝,致使學習曲綫遭破壞,也未能實現成本降低,因此遇到了嚴重的財務危機,不得不被兼幷。總而言之,只有在使用得當的條件下,學習曲綫才是一種强有力的競爭武器。
學習曲綫的建立
學習曲綫的建立基于以下一些基本假設:
生産第n+1個産品所需的直接勞動時間總是少于生産第n個産品所需的直接勞動時間;
當累積生産數量增加時,所需直接勞動時間按照一個遞减的速率减少;
時間的减少服從指數分布;
這些假設實際上就包含了學習曲綫的基本規律,即生産數量每增加一倍,所需直接勞動時間减少了一個固定的百分比。
在這樣的假設下,給定第一個産品的直接勞動時間和學習率,可建立下面這種對數模型:
kn=k1·nb
式中,k1--第一個産品的直接勞動時間;
kn--第n個産品的直接勞動時間;
n--累積的生産數量;
b--等于lgr/lg2;
r--學習率。
用這個模型,即可描繪出學習曲綫。
産能擴張
在生産過程中,企業有時可能需要擴大産能。企業在擴大其生産能力時,應考慮許多方面的問題,其中最重要的幾個方面是維持生産系統的平衡,控制擴大生産能力的頻率以及有效利用外部生産能力。
1.維持生産系統的平衡
在一家生産完全平衡的工廠裏,生産第一階段的輸出恰好完全滿足生産第二階段輸入的要求,生産第二階段的輸出又恰好完全滿足生産第三階段的輸入要求,依次類推。然而,實際生産中達到這樣一個“完美”的設計幾乎是不可能的,而且也是人們不希望的,因爲其一:每一生産階段的最佳生産水平不同,其二:産品需求是會發生變化的,而且由于生産過程本身的一些問題也會導致生産不平衡的現象發生,除非生産完全是在自動化生產綫上進行,因爲一條自動化生產綫就像是一台大機器一樣,是一個整體。
解决生産系統不平衡問題的方法有很多。例如:一,增大瓶頸的生産能力。可采取一些臨時措施,如加班工作、租賃設備、通過轉包合同購買其他廠家的産成品等;二,在生産瓶頸之前留些緩衝庫存,以保證瓶頸環節持續運轉,不會停工;三,如果某一部門的生産依賴于前一部門的生産,那麽就重復設置前一部門的生産設備,可以充足地生産以便供應下一部門的生産所需。
2.擴大生産能力的頻率
在擴大生産能力時,應考慮兩種類型的成本問題:生産能力升級過于頻繁造成的成本與生産能力升級過于滯緩造成的成本。首先,生産能力升級過于頻繁會帶來許多直接成本的投入,如舊設備的拆卸與更換、培訓工人、使用新設備等等。此外,升級時必須購買新設備,新設備的購置費用往往遠大于處理舊設備回收的資金量。最後,在設備更換期間,生産場地或服務場所的閑置也會造成機會成本。
反之,生産能力升級過于滯緩也會有很大的成本支出。由于生産能力升級的間隔期較長,每次升級時,都需要投入大筆資金,大幅度地擴大生産能力。然而,如果當前尚不需要的那些生産能力被閑置,那麽,在這些閑置生産能力
上的投資就將作爲管理費用計入成本,這就造成了資金的占用和投資的浪費。
3.外部生産能力
有些情况下還可以利用一種更爲經濟有效的辦法,那就是不擴大本企業的生産能力,而是利用現有的外部生産能力來增加産量。常用的兩種方式分別是:簽訂轉包合同或共享生産能力。共享生産能力的新途徑還有利用一種企業聯合體間的分時柔性工廠等。
产能分析报告
产能分析报告 一、产能修改记录及主要产品信息 注:产能分析报告——修改记录 1)产能发生变化时以便及时追踪。如进行增产以达到完全生产能力,此时生产线通过一系列步骤可以达到完全生产能力,则应记录下这些变化。填写论证产能时也应同时填写日期。 2)此次产能分析报告均记作初次提交。 注:产品信息 1)完成产能分析报告的首先要明确需要分析的产品的详细信息。包括产品名称、型号、产能概况、客户需求信息等。 2)必要时应完善产品主要零部件供应商信息,以便及时掌握配套商供货情况,平衡零部件供货影响系数。 二、现有设备产能核算 1、预订工作时间标准
注: 1)单班时间:每班总时间-每班的总计可用小时数。 2)班次:表示的是每天每个工艺操作的班次数。 3)作业率:(总工时-无效工时)/总工时。 人员休息-如果在人员休息的时候,机器也停止运转,则输入每班中机器不运转的时间长度。 计划的维修时间-这是计划的每班中机器停机用于维护的时间长度。 4)年出勤时间:年出勤天数-表示的是每年的工艺运作的天数(扣除法定节假日、双休日)。 5)计算举例:每班8小时、每天2班次、作业率80%、年出勤302天,净可用时间=8*2*80%*302=时。 2、代表产品制程/线能力计算
注: 1)代表产品:所谓代表产品指产品制程包含其他所有产品制造过程包含的所有工艺过程;如存在两种以上产品包含不同工艺过程、需分别取各类型产品代表产品制程并进行线能力分析。 2)评价瓶颈工序应排除可用外协、其他生产线可用设备借代等因素影响。 3)每条生产线选取一种或2种产品作为代表说明制程及瓶颈工序即可,其他产品可直接计算毛产能。3、毛产能核算 注: 1)毛产能核算过程没有排除产品合格率、设备故障率、人员负荷等因素对产能的影响,不能作为需求平衡分析的依据,需进一步平衡。 2)其他产品可根据代表产品计算方法计算出出毛产能。
公司产能分析报告模板
公司产能分析报告模板 Revised final draft November 26, 2020
X X公司产能分析报告(模板)产能跟踪分析报告 一、现有设备产能核算 1、预订工作时间标准注: 1)单班时间:每班总时间-每班的总计可用小时数。2)班次:表示的是每天每个工艺操作的班次数。3)作业率:(总工时-无效工时)/总工时。 人员休息-如果在人员休息的时候,机器也停止运转,则输入每班中机器不运转的时间长度。计划的维修时间-这是计划的每班中机器停机用于维护的时间长度。 4)年出勤时间:年出勤天数-表示的是每年的工艺运作的天数(扣除法定节假日、双休日)。 5)计算举例:每班8小时、每天2班次、作业率80%、年出勤302天,净可用时间 =8*2*80%*302=3865.6时。 2、代表产品制程/线能力计算 注: 1)代表产品:所谓代表产品指产品制程包含其他所有产品制造过程包含的所有工艺过程;如存在两种以上产品包含不同工艺过程、需分别取各类型产品代表产品制程并进行线能力分析。 2)评价瓶颈工序应排除可用外协、其他生产线可用设备借代等因素影响。 3)每条生产线选取一种或2种产品作为代表说明制程及瓶颈工序即可,其他产品可直接计算毛产能。 3、毛产能核算 注: 1)毛产能核算过程没有排除产品合格率、设备故障率、人员负荷等因素对产能的影响,不能作为需求平衡分析的依据,需进一步平衡。 2)其他产品可根据代表产品计算方法计算出出毛产能。 4、有效产能(净产能)
注: 1)设备生产包括机器检修、保养、待料等时间,实际的工作时间达不到计划工时,且生产的产品有不良品,因此有效产能必须是以毛产能为基础,减去因停机和良率以及人员缺口等综合因素所造成的产能损失。2)总体设备利用率计算公式:OEE=设备可用性*性能效率*产品合格率。 根据来自生产验证运转的历史数据来计算总体设备利用率的(OEE)。性能效率的计算是通过计划的所需周期时间来的。如果计算单元显示的是100%或者更高,则该单元用红色进行强调。3)人员负荷率=(现有生产人员/人员配置)*100% 反映了以设备为依据的人员配备情况,这一指标在短期内直接对净产能产生影响。 二、产能需求平衡/预警机制 1、产能负荷率计算 注: 1)产能负荷率反映了企业中长期、短期需求计划对目前净产能比值的柔性指标,其作为产能预警的基础数据,对产能提升计划起指导性作用。 2)当负荷率反映3个月以内需求产能状态时,初步方案采取短期产能提升计划;3-6月以上,采取中长期产能提升计划;超过6个月以上,采取长期产能提升计划。2)预警设置采取红黄蓝三色,具体设置见(三、2)产能预警。 2、产能预警 注: 1)坐标轴纵轴表示产能,横轴为时间进度,两条黑色虚线分别表示长期扩能预警、短期扩能预警,红色实线为需求线(变化情况可参照历史数据)。 2)当需求线在短期扩能预警线以下时显示为蓝色椭圆。不设预警,不需扩能;当需求线在短期扩能预警线与长期扩能预警线之间时,设置黄色预警,采取短期产能提升计划;当红色需求线超过长期扩能预警线,并长时间处于短期最大可获得差能之上,采取红色预警,并策划中长期扩能计划。 三、需求平衡/产能提升策略 1、约束产能的解决对策 通过设置产能预警线,提前对可能产生约束的时间点提出产能扩充的对策建议,并针对各类扩充对策预留实施提前期。
产能分析报告模板及指标明细
产能分析报告模板及指标明细 一、产能修改记录及主要产品信息 注:产Array能分析 报告— —修改 记录 1) 产能发 生变化 时以便 及时追踪。如进行增产以达到完全生产能力,此时生产线通过一系列步骤可以达到完全生 产能力,则应记录下这些变化。填写论证产能时也应同时填写日期。 2)此次产能分析报告均记作初次提交。 注:产品信息 1)完成产能分析报告的首先要明确需要分析的产品的详细信息。包括产品名称、型号、产能概况、客户需求信息等。 2)必要时应完善产品主要零部件供应商信息,以便及时掌握配套商供货情况,平衡零部件供货影响系数。
二、现有设备产能核算 1、预订工作时间标准 注:Array 1)单班时 间:每班 总时间- 每班的总 计可用小 时数。 2)班次: 表示的是 每天每个 工艺操作的班次数。 3)作业率:(总工时-无效工时)/总工时。 人员休息-如果在人员休息的时候,机器也停止运转,则输入每班中机器不运转的时间长度。计划的维修时间-这是计划的每班中机器停机用于维护的时间长度。 4)年出勤时间:年出勤天数-表示的是每年的工艺运作的天数(扣除法定节假日、双休日)。5)计算举例:每班8小时、每天2班次、作业率80%、年出勤302天,净可用时间 =8*2*80%*302=3865.6时。 2、代表产品制程/线能力计算
1)代表 产品: 所谓代 表产品 指产品 制程包 含其他 所有产 品制造 过程包 含的所 有工艺 过程; 如存在 两种以上产品包含不同工艺过程、需分别取各类型产品代表产品制程并进行线能力分析。 2)评价瓶颈工序应排除可用外协、其他生产线可用设备借代等因素影响。 3)每条生产线选取一种或2种产品作为代表说明制程及瓶颈工序即可,其他产品可直接计算毛产能。 3、毛产能核算
公司产能分析报告范文
2014公司产能分析报告模板 一、产能修改记录及主要产品信息 注:产能 分析报告—— 修改记录 1)产能发生变化时以便及时追踪。如进行增产以达到完全生产能力,此时生产线通过一系列步骤可以达到完全生产能力,则应记录下这些变化。填写论证产能时也应同时填写日期。 2)此次产能分析报告均记作初次提交。 注:产品信息 1)完成产能分析报告的首先要明确需要分析的产品的详细信息。包括产品名称、型号、产能概况、客户需求信息等。 2)必要时应完善产品主要零部件供应商信息,以便及时掌握配套商供货情况,平衡零部件供货影响系数。 二、现有设备产能核算 1、预订工作时间标准
注: 1)单班时间:每班总时间- 每班的总计可用小时数。 2)班次:表示的是每天每个工艺操作的班次数。 3)作业率:(总工时-无效工时)/总工时。 人员休息-如果在人员休息的时候,机器也停止运转,则输入每班中机器不运转的时间长度。 计划的维修时间-这是计划的每班中机器停机用于维护的时间长度。 4)年出勤时间:年出勤天数-表示的是每年的工艺运作的天数(扣除法定节假日、双休日)。 5)计算举例:每班8小时、每天2班次、作业率80%、年出勤302天, 净可用时间=8*2*80%*302=时。 2、代表产品制程/线能力计算 注: 1)代表产品:所谓代表产品指产品制程包含其 他所有产品制造过程包含的所有工艺过程;如存在两种以上产品包含不同工艺过程、需分别取各类型产品代表产品制程并进行线能力分析。 2)评价瓶颈工序应排除可用外协、其他生产线可用设备借代等因素影响。
3)每条生产线选取一种或2种产品作为代表说明制程及瓶颈工序即可,其他产品可直接计算毛产能。 3、毛产能核算 注: 1)毛产能核算过程没有排除产品合格率、设备故障率、人员负荷等因素对产能的影响,不能作为需求平衡分析的依据,需进一步平衡。 2)其他产品可根据代表产品计算方法计算出出毛产能。 3、有效产能(净产能) 注: 1)设备生产包括机器检修、保养、待料等时间,实际的工作时间达不到计划工时,且生产的产品有不良品,因此有效产能必须是以毛产能为基础,减去因停机和良率以及人员缺口等综合因素所造成的产能损失。 2)总体设备利用率计算公式:OEE=设备可用性*性能效率*产品合格率。 根据来自生产验证运转的历史数据来计算总体设备利用率的(OEE)。性能效率的计算是通过计划的所需周期时间来的。如果计算单元显示的是100%或者更高,则该单元用红色进行强调。 3)人员负荷率=(现有生产人员/人员配置)*100%
公司产能分析报告模板
公司产能分析报告模板 、产能修改记录及主要产品信息 注:产能分析报告一一修改记录 1)产能发生变化时以便及时追踪。如进行增产以达到完全生产能力,此时生产线通过一系列步骤可以达到完全生产能力,则应记录下这些变化。填写论证产能时也应同时填写日期。 2)此次产能分析报告均记作初次提交。 注:产品信息 1)完成产能分析报告的首先要明确需要分析的产品的详细信息。包括产品名 称、型号、产能概况、客户需求信息等。 2)必要时应完善产品主要零部件供应商信息,以便及时掌握配套商供货情况,平
衡零部件供货影响系数。 、现有设备产能核算 注: 1)单班时间:每班总时间-每班的总计可用小时数。 2)班次:表示的是每天每个工艺操作的班次数。 3)作业率:(总工时-无效工时)/总工时。 人员休息-如果在人员休息的时候,机器也停止运转,则输入每班中机器不运转的时间长度。 计划的维修时间-这是计划的每班中机器停机用于维护的时间长度。 4)年出勤时间:年出勤天数-表示的是每年的工艺运作的天数(扣除法定节假日、双休日)
5)计算举例:每班8小时、每天2班次、作业率80%年出勤302天,净 可用时间=8*2*80%*302=3865.6 时。 2、代表产品制程/线能力计算 注: 1)代表产品:所谓代表产品指产品制程包含其他所有产品制造过程包含的所有工艺过程;如存在两种以上产品包含不同工艺过程、需分别取各类型产品代表产品制程并进行线能力分析。
2)评价瓶颈工序应排除可用外协、其他生产线可用设备借代等因素影响。 3)每条生产线选取一种或2种产品作为代表说明制程及瓶颈工序即可,其他产品可直接计算毛产能。 3、毛产能核算 注: 1)毛产能核算过程没有排除产品合格率、设备故障率、人员负荷等因素对产能的影响,不能作为需求平衡分析的依据,需进一步平衡。 2)其他产品可根据代表产品计算方法计算出出毛产能。 3、有效产能(净产能)
设备产能调查分析表.doc
供应商Supplier 供应商 A Supplier A 设备名称 Description of equipment 60T 压力机 设备产能调查表 Questionary of production capacity of the equipments 单台设备产能 Production capacity of single equipment 设备数量 设备占用率 年产量Quantity 生产产品Occupancy Annual of Product H/天天/年 良品率 节拍( S/ 产品单台产能rate of output equipme 开动率 Rate of Production equipments nts Days/ye Operatio 件) acceptabl capacity of H/day ar n rate s/piece e products single product 产品A 73500 95% 60 161595 0.45 Product A 产品B 42000 90% 50 183708 0.23 Product B 产品C 56000 2 12 315 75% 90% 60 153090 0.37 Product C 产品D 71400 90% 70 131220 0.54 Product D 开发产品60000 95% 50 193914 0.31 Developed product 产能是否满足生产 需求 Production 富余产能 capacity can Redundant capacity meet the production demand? 78848OK 填写说明: Description of completion: 1、黄色区域部分为技术担当在现场调查后进行填写部分,其余部分会自动生成。 1. Yellow zone shall be completed by the technical director after investigation on the site. The other parts may be automatically generated. 2、“生产产品”中的产品 A、B、C、D 为供应商设备现行生产的产品,开发产品为现在需要开发的产品 2.The product A, B, C and D in "in-process products" refer to the products manufactured by the supplier's equipments currently. The developed products refer to the products required to develop. 3、关于“设备数量”的填写说明如下: 3. Description of completion of "quantity of equipments" is as follows: 如果是针对单台设备调查,就直接填写设备数量。In the event of single equipment, please fill in the quantity of equpments directly. 如果是针对生产线调查,就填写生产线中的瓶紧工序的设备数量,相应的“节拍”也必须填写为该设备的生产节拍。如果有必要也可针对生产线每台设备进行单独调查。In the event of production line, please fill in the quantity of equipments for critical procedures. The corresponding "s/piece" shall also be filled in production time of the equipment. If it is unnecessary, it is also possible to singly investigate each equipment for production line. “OK”为满足生产需求, "NG" 为不满足生产需求。 4. Red zone is the investigated conclusion."OK" refers to that it can meet the production demand. "NG" refers to that it can not 4、红色区域部分为调查结论。 meet the production demand.
XX公司产能分析报告(模板).doc
产能跟踪分析报告
一、现有设备产能核算 1、预订工作时间标准 注: 1)单班时间:每班总时间-每班的总计可用小时数。 2)班次:表示的是每天每个工艺操作的班次数。 3)作业率:(总工时-无效工时)/总工时。 人员休息-如果在人员休息的时候,机器也停止运转,则输入每班中机器不运转的时间长度。 计划的维修时间-这是计划的每班中机器停机用于维护的时间长度。 4)年出勤时间:年出勤天数-表示的是每年的工艺运作的天数(扣除法定节假日、双休日)。 5)计算举例:每班8小时、每天2班次、作业率80%、年出勤302天,净可用时间=8*2*80%*302=3865.6时。 2、代表产品制程/线能力计算 注: 1)代表产品:所谓代表产品指产品制程包含其他所有产品制造过程包含的所有工艺过程;如存在两种以上产品包含不同工艺过程、需分别取各类型产品代表产品制程并进行线能力分析。
2)评价瓶颈工序应排除可用外协、其他生产线可用设备借代等因素影响。 3)每条生产线选取一种或2种产品作为代表说明制程及瓶颈工序即可,其他产品可直接计算毛产能。3、毛产能核算 注: 1)毛产能核算过程没有排除产品合格率、设备故障率、人员负荷等因素对产能的影响,不能作为需求平衡分析的依据,需进一步平衡。 2)其他产品可根据代表产品计算方法计算出出毛产能。 4、有效产能(净产能) 注: 1)设备生产包括机器检修、保养、待料等时间,实际的工作时间达不到计划工时,且生产的产品有不良品,因此有效产能必须是以毛产能为基础,减去因停机和良率以及人员缺口等综合因素所造成的产能损失。2)总体设备利用率计算公式:OEE=设备可用性*性能效率*产品合格率。 根据来自生产验证运转的历史数据来计算总体设备利用率的(OEE)。性能效率的计算是通过计划的所需周期时间来的。如果计算单元显示的是100%或者更高,则该单元用红色进行强调。 3)人员负荷率=(现有生产人员/人员配置)*100% 反映了以设备为依据的人员配备情况,这一指标在短期内直接对净产能产生影响。 二、产能需求平衡/预警机制 1、产能负荷率计算
企业生产运营分析报告
企业生产运营分析报告 一.生产计划的制定 从总体来说,我公司刚刚接手生产厂缺乏生产经验,没有从一开始就做好合理的生产规划,未能充分考虑到产品研发时间与生产线建设时间的因素,加之起初p1 在本地市场还是占很大市场份额的,生产部门便直接投入生产产品p1,希望在第一年内能拿到大的订单,获得较多收入。由于第一年未能充当当地的标王,所以没有拿到大订单, 导致很多p1 作为库存剩余,从第二年才开始研发p2,p3。 第二年我们积累了一定的经验,并且认识到本地市场目前对p1 仍然有较大的市场,但是需求在不久的将来会逐渐减少,所以在第一季度着手开发p2,p3,希望能尽早获得p2,p3 的订单。在研发p2,p3的过程中,继续生产p1,希望在当年能拿到较大的订单,并且能够及时收回资金,投入生产。但是受到第一年销售额的影响,所以 未能争取到大的p1 订单,而p2,p3 又在研发中,导致第二年依然保持相同的销售量, 一方面p1 积压,另一方面还需要继续购进生产原料继续生产不至于使生产线闲置。 表一 我们预计在第三、第四年p1的订单依旧保持与前期相等,p2 已研发成功,可以生产接到订单。到第三年年末,公司由于大量的贷款即将到期,用于投入生产的资金不足加之预计订单量持平,所以降低了生产。因为总共要求经营四年,在第四年第一季度完成少量订单后,CEO便决定变卖厂房生产线以偿还之前的银行贷款和高利贷,提前结束生产活动。 生产线投资决策 公司在接受老厂长移交时拥有三条手工生产线, 还有一条半自动生产线, 从生产线产能一览表可知,全自动、柔性生产线生产周期短,生产效率高,但是安装周期都需要4Q,时间相对较长。 表二 生产线购买价格安装周期生产周期出售残值 手工线5M 无3Q 1M 半自动8M 2Q 2Q 2M 全自动16M 4Q 1Q 4M 柔性线24M 4Q 1Q 6M 为了提高生产效率,接到更多的订单,增加销售收入,我们从第二年开始投入新型生产线的建设,但是时间较晚,从第三期才开始引入柔性生产线,第四期引入全自动生
设备产能分析报告
设备产能分析报告 一.公司概况 公司拥有16000㎡现代化的标准厂房、另有超过20000m3有效仓储空间;专业化的研究中心、企业配备先进的现代化国家研发中心及全自动生产检测设备,从来料检验、生产管理、物料管理到设备管理,都实现了资源配置的最优化,科王电器十分注重技术研发与产品创新,安装了连续配气装置,配置了综合测试系统、能效测试台、寿命测试台、恒温恒湿试验机、高温试验箱、热电偶耐久性试验台、盐雾试验机、色谱分析仪、湿式流量计、安全性能综合测试仪等业内先进的生产设备和检测设备,是一间集新产品开发、生产制造为一体的技术主导型生产企业。 二.现有生产设备状况 三.现有设备产能核算 1.预订工作时间标准
注: 1)单班时间:每班总时间-每班的总计可用小时数。 2)班次:表示的是每天每个工艺操作的班次数。 3)作业率:(总工时-无效工时)/总工时。 人员休息-如果在人员休息的时候,机器也停止运转,则输入每班中机器不运转的时间长度。计划的维修时间-这是计划的每班中机器停机用于维护的时间长度。 4)年出勤时间:年出勤天数-表示的是每年的工艺运作的天数(扣除法定节假日、星期天)。 2.代表产品制程/线能力计算
注: 1)代表产品:所谓代表产品指产品制程包含其他所有产品制造过程包含的所有工艺过程;如存在两种以上产品包含不同工艺过程、需分别取各类型产品代表产品制程并进行线能力分析。 2)评价瓶颈工序应排除可用外协、其他生产线可用设备借代等因素影响。 3)每条生产线选取一种或2种产品作为代表说明制程及瓶颈工序即可,其他产品可直接计算毛产能。 四.产能需求平衡/预警机制
XX公司产能分析报告(模板)
产能跟踪分析报告 一、现有设备产能核算 1、预订工作时间标准 注: 1)单班时间:每班总时间-每班的总计可用小时数。 2)班次:表示的是每天每个工艺操作的班次数。 3)作业率:(总工时-无效工时)/总工时。 人员休息-如果在人员休息的时候,机器也停止运转,则输入每班中机器不运转的时间长度。 计划的维修时间-这是计划的每班中机器停机用于维护的时间长度。 4)年出勤时间:年出勤天数-表示的是每年的工艺运作的天数(扣除法定节假日、双休日)。 5)计算举例:每班8小时、每天2班次、作业率80% 年出勤302天,净可用时间=8*2*80%*302=3865.6 时。 2、代表产品制程/线能力计算 注: 1)代表产品:所谓代表产品指产品制程包含其他所有产品制造过程包含的所有工艺过程;如存在两种以上产品包含不同工艺过程、需分别取各类型产品代表产品制程并进行线能力分析。 2)评价瓶颈工序应排除可用外协、其他生产线可用设备借代等因素影响。 3)每条生产线选取一种或2种产品作为代表说明制程及瓶颈工序即可,其他产品可直接计算毛产能。 3、毛产能核算
注: 1)毛产能核算过程没有排除产品合格率、设备故障率、人员负荷等因素对产能的影响,不能作为需求平衡分析的依据,需进一步平衡。 2)其他产品可根据代表产品计算方法计算出出毛产能。 4、有效产能(净产能) 注: 1)设备生产包括机器检修、保养、待料等时间,实际的工作时间达不到计划工时,且生产的产品有不良品,因此有效产能必须是以毛产能为基础,减去因停机和良率以及人员缺口等综合因素所造成的产能损失。 2)总体设备利用率计算公式:OEE设备可用性*性能效率*产品合格率。 根据来自生产验证运转的历史数据来计算总体设备利用率的(OEE。性能效率的计算是通过计划的所需周期时间来的。如果计算单元显示的是100%或者更高,则该单元用红色进行强调。 3)人员负荷率二(现有生产人员/人员配置)*100% 反映了以设备为依据的人员配备情况,这一指标在短期内直接对净产能产生影响。 二、产能需求平衡/预警机制 1、产能负荷率计算 注: 1)产能负荷率反映了企业中长期、短期需求计划对目前净产能比值的柔性指标,其作为产能预警的基础数据,对产能提升计划起指导性作用。 2)当负荷率反映3个月以内需求产能状态时,初步方案采取短期产能提升计划;3-6月以上,采取中长期产能提升计划;超过6个月以上,采取长期产能提升计划。
公司产能分析报告模板
告报析分踪跟能产. 一、现有设备产能核算 1、预订工作时间标准 注: )单班时间:1)计划工时A-每班总时间每班的总计可 e=a*b*c*d 说明计算公式:净可用工时用小时数。表示)班次:2根据自身工时计划安排填写8 a 单班时间/时的是每天每个工艺操作的b根据自身工时计划安排填2班次次数根据自身工时计划安排填c80作业率)(总)作业率: 3无效工工时根据自身工时计划安排填d302 年出勤天/ /总工时。时如人员休息净可用时e 果在人员休息的时候,机器也停止运转,则输入每班中机器不运转的时间长度。这是计划的每班中机器停机用于维护的时间长度。-计划的维修时间表示的是每年的工艺运作的天数(扣除法定节假日、双休日)。4)年出勤时间:年出勤天数- 时。净可用时间=8*2*80%*302=3865.62班次、作业率80%、年出勤302天,5)计算举例:每班8小时、每天线能力计算2、代表产品制程/注: =产品年产能瓶颈工序总加工时间净可用时间(年)/)代表产1品:所谓代人员日加工总加工辅助工时加工工时设备工序设备设备表产品指产备注配置min/ 名称名称编号台数件 min/件时间能力品 制程包含其他所有产 品制造过程 包含的所有工艺过程;如存在两种以上产品包生产线瓶颈工序设备产能描述:含不同工艺)其他1)瓶颈工序、设备产能,2过程、需分别取各类型产品代表产品制 程并进行线能力分析。)评价瓶颈工序应排除可用外协、其他生产线可用设备借代等因素影响。2 种产品作为代表说明制程及瓶颈工序即可,其他产品可直接计算毛产能。)每条生产线选取一种或23 3、毛产能核算产品年度毛产能= 产品定额系数代表产品/产品系产品名工时定产品定额系注备实际产能所占比例线产能数额称列. 注 毛产能核)1 算过程没有 排除产品格率、设备 故障率、人 员负荷等因 素对产能的
产能分析报告详解
产能规划 产能规划的步骤 1.估计未来能力需求 在进行产能规划时,首先要进行需求预测。 由于能力需求的长期计划不仅与未来的市场需求有关,海域技术变化,竞争关系以及生产率提高等多种因素有关,因此必须综合考虑。所预测的时间段越长,预测的误差可能性就越大。 在制造业企业中,企业能力经常是可以利用的设备数来表示的,在这种情况下,管理人员必须把市场需求(通常是产品产量)转变为所需的设备数。 将这些设备信息输入APS,通过APS可快速实现未来能力的评估。 2.计算需求与现有能力之间的差 当预测需求与现有能力之间的差为正数时,就需要扩大产能,当一个生产运作系统包括多个环节或多个工序时,能力扩大必须考虑到各个工序能力的平衡。当企业的生产环节很多,设备多种多样时,各个环节的所拥有的生产能力往往不一致,既有富余有瓶颈的环节。而富余的和瓶颈的环节又随着产品品种和制造工艺的改变而变化。从这个意义上来说,企业的整体生产能力是由瓶颈环节的能力所决定的,这个制定能力计划时必须注意的一个关键问题。否则的话,就会形成一种恶性循环,即,某瓶颈工序能力紧张——增加该工序能力——未增加能力的其他工序又变为瓶颈工序。 利用APS可快速发现瓶颈环节,方便企业管理者决策。 3.制定候选方案 处理能力与需求之差的方法可有多种。最简单的一种是:不考虑能力扩大,任由这部分顾客或订单失去。其他方法包括能力扩大规模和时间的多种方案,包括积极策略,消极策略或者中间策略的选择,也包括新设施地点的选择,还包括是否考虑使用加班,外包等临时措施,等等。这些都是制定能力计划方案所要考虑到内容。所考虑的重点不同,就会形成不同的候选方案。一般来说,至少应给出3-5个候选方案。 利用APS模拟排程,制定多种可供选择方案。 4.评价每个方案 评价包括两个方面:定量评价和定性评价。定量评价主要是从财务的角度,以所要进行的投资为基准,比较各种方案给企业带来的收益以及投资回收清况。这里,可使用净现值法,盈亏平衡分析法,投资回收率法等不同方法。定性评价主要是考虑不能用财务分析来判断的其他因素,例如,是否与企业的整体战略相符,与竞争策略的关系,技术变化因素,人员成本等等,这些因素的考虑,有些实际
公司现状分析报告
XX公司现状分析报告
1.2016年经典案例客户(年度交易额前5名或单笔交易超过30万的客户) 是1.精艺2.智诚3.海亮集团4.皓月5.建大. 2.目前在交易客户总数410家,历史累计客户总数370家,客户流失率9.7%。 其中战略客户(年交易200万以上)6家。 3.2014年总业绩0.8亿,2015年总业绩1亿,2016年总业绩1.2亿,年 均增长率20%。 五、管理现状: 1、财务管理: (1)没有年度预算机制。 (2)现金支出审批没有设定明确的把关标准及节点 (3)没有根据管理岗位的职责大小设定报销审批权限及标准。 (4)缺乏“通过精确的财务管理,预防系统性风险”的意识,没有资产、负债整体情况的盘点。对现金流进出规律及未来预测、利润分析,成 本分析等有基础,但没有比例上的分析,也没有从过去的变化中发现 规律,预判未来,导致公司领导无法做精准决策。 2、事务管理: (1)部门之间协作不够,衔接有零散的、约定俗成的规则,但没有清晰界定的工作内容、标准、时限、权责划分。出现不配合现象需要高层亲 自干预。 (2)干部关注业务,不关注管理。注重部门利益,不关注整体利益。
(3)中层执行不力,乱执行,执行方向不明确,有矫枉过正的现象。 3、质量管理现状: (1)主要检测设备名称及数量? (2)我们的质量检测人员总人数5 个,工程师3 个。 (3)我们的品质在主要原料入厂检测、在研发以及小试阶段、新产品试生产阶段、常规生产的中间过程控制和最终产品检测在发挥品质管理和检测功能?(4)我们目前运用了ISO9001管理体系进行精细化工生产和质量科学化管控,哪些质量管理工具?或者我们的质量管理方法GB、HG、SH等标准是 4、销售管理: 1、公司已经向制造型企业转移,但销售重心布局单一,未能形成可复制 于其他区域的销售管理模式,未能形成以镇江为中心的多重心布局, 影响了公司的纵深发展。 2、公司目前长三角的销售团队人员过于紧凑。人均销售业绩不高。公司 业绩增长幅度受制于区域市场总容量,短期内区域业绩增长幅度难以 超过50%。 3、销售团队负责人缺乏市场营销策划能力。缺乏大客户管理能力。 4、没有对销售数据进行系统的、深入的数据分析,从总监到销售员普遍 存在依赖经验、感觉和片面的信息进行判断,在充分激励竞争的市场 环境下缺乏持续有效的业绩增长能力。 5、销售团队负责人的管理责任意识不够。仅关注业绩本身,但对于人员 的能力培养,纪律意识及文化引导方面存在不足。 六、企业文化及导向: 1.企业标识LOGO非常好,目前公司上下一致认知度高。 2.企业使命不明确 3.企业经营理念不明确 4.企业核心价值观不明确 5.企业经营方针不清晰 6.用人理念没有明确 七、公司未来发展方向及策略。 问题: 1、请参考上述资料,并结合对公司实际调研情况,从公司管理、技术、人 力资源、市场及文化方面给出评价,并给与建议 2、请结合分析,制定公司未来发展发向,及1年目标,3年目标,5年目 标,并给出阶段性相应措施。
产能分析报告格式.docx
CAFR06-006 I. J68CC II. 特 专用或共享工艺( 通过共享工艺,仅显示特殊零件的操作模 式 ) A.班次数 /天 B.总计小时数 /班 C人员休息:午餐和休息(分钟数/班) 计划维护时间(分钟数/班) D天数 / 星期 E净可用时间 ( 生产小时数 /星期 ) [A*(B-(C/60))*D] 预 计 停 机 时 间 F工具 / 变体 /易耗工具切换(分钟数) G每班切换数 H每班的设备检查(分钟数) I每班中断时间 ( 非计划停机时间 ) (分钟数 ) J总计计划停机时间/星期(小时数)[ (FxG+H)/60xAxD] K设备可用性[(E-J)/E] B)X顾客顾需客求量生产/星期(不 C)产能修改记录(例 如按节拍生产) 地址Y包括顾售客后/件应)商的工作天供2400 供应商代码Z数/顾星客期每天需求量5 生产日期(DPV ) 型号 批次售后件年需求量0 工艺 1工艺 2工艺 3工艺 4工艺 5工艺 6工艺 7 1111111 0.000.000.000.000.000.000.00 0.000.000.000.000.000.000.00 ------- 预 预计报废和返工零件百分比 对于相关工艺,请参见培训材料 L预计合格率(%)-------计 划 周 期 时 间/ 产 能 正好满足顾客需求量所需的周期时间(秒/零件)[E*3600*K/-------X*L] M计划的理想周期时间(用秒表测量)( 秒 /零件 ) 对于一个工具上有多个模腔的情况,请参见培训材料。 计划的生产量 / 星期[(E-J)*3600/M*L] 计划的生产量 / 天[ (E-J)*3600/M*L/D] III 生 产 生产运转的总计持续时间(分钟) N O1总计计划停机时间( 午餐、休息及维护)( 分钟 ) O2(切换和检查 )( 分钟 ) P非计划停机时间总计( 即中断、非预计调整和非预计设定等) (分钟 ) - - 按节拍生产产能其他例如试运转(阶段 0)验证(阶段3) 10、 中断的原因 生 Q总计运转零件 R拒收零件总计 S下线后返工、再测试或着维修的零件总计 T合格零件总计 ( 仅首次通过——不包括被拒收的、再处理的或着返工的零件 ) 零件拒收原因 U工艺实际周期时间总计(秒 /零件 ) [(N-O1-O2-P) x 60 / Q] IV V每周可运零件数[E*3600 / ((N-O)*60/T)] W每天可运零件数[ V/Y] Z DPV AA高于 / 低于 DPV 的百分比[ W/Z] V. 总 体 设 备 利 用 率 设备可用率[(N-O1-O2-P)/(N-O1)] 性能效率[(M*Q)/(N-O1)] 合格率[T/Q] OEE DE SHARED ------- ------- --------------0000000 ------- ---------------------------- VI. 制造瓶颈 工艺编号 高于 DPV 的 % : 0.00% VII. 供仅顾客使用STA 评估结果 :按节拍生产(阶段 0)电话号码传产能验证(阶段 3)头衔真号码 顾客姓名 批准 供应 商名 拒绝 供应 商授日期顾客签字日期
公司产能分析报告
厦门奥特乐电子有限公司 Xiamen Aottler Electronics CO.,LTD 产能分析报告 一、主要产品信息 产能分析报告 产能分析报告简述日期备注 T73-2 继电器生产线产能2011.11 4100 继电器生产线产能2011.11 产品名称型号设计年产能2012 年需求计划备注T73-2T73-2A/B/C型6000000 只4000000单班 41004100A/B/C 型8000000 只5000000单班 二、现有设备产能核算 1、预订工作时间标准 计划工时 计算公式:净可用工时 e=a*b*c*d说明a单班时间 / 时10 b班次/班1 c作业率( %)95% d年出勤天数 / 天300 e净可用时间 / 时2850 2、生产线能力计算 设备名设备生产产总加日加工人员备工序名称设备编号 品只 /工时能力配置注称台数
间 T73 组装 T73 组 13 1800 10 18000 7 T73-2SCX 装线 动簧组成 动簧带 1 2000 10 20000 无 型 T73-2DHDL-014 料 铆动点 铆动点 1 1600 10 16000 1 T73-2MDD-015 机 铆静点 A 铆静触 1 2000 10 20000 T73-2MJD-016A 机 铆静点 B 铆静触 1 2000 10 20000 T73-2MJD-017B 1 机 轭铁整 轭铁整 1 2000 10 20000 形 T73-2EZX-018 形机 插引线 插引线 1 2500 10 25000 脚 T73-2CYXJ-019 脚 绕磁路 饶线机T73-2RXJ-020 1 1000 16 16000 12 班 3、毛产能核算 产品系 产品名 工时定额 型号比例 线产能 实际产能 备 注 列 称 A 型 65% 18000 11700 T73-2 B 型 10 小时 10% 18000 1800 C 型 25% 18000 4500 合 计 10 小时 18000 3、有效产能 产品 /生 毛产能 设备可 稼动率 合格率 作业 人员配 现有人 净产能 产线 用性 率 置 员 T73-2 18000 100% 95% 99.5% 95% 10 10 16100 三、产能提升策略 1) 人力资源: A) 增加班次,采取两班制或三班制( 1 小时- 1 星期) B) 加班,适当延长工作时间( 1 小时- 1 星期) C)内部支援,其他线暂时借调( 1 小时- 1 星期) ; 2) 设备资源
生产产能分析
产能分析 产能分析即对生产能力的分析,一般指分析一个公司或者集团一年或者一个月的总生产能力,是评估改企业产值的一个标准,即分析制作流程,装备负荷能力,人才负荷才能,场地符合才能,等等进行分析归纳。 一产能剖析重要针对哪几个方面? 产能的分析重要针对以下几个方面: 1、做何种机型以及此机型的制作流程。 2、制程中使用的机器装备的OEE(装备负荷能力)。 3、产品的总标准时间,每个制程的尺度时间(人力负荷才能)。 4、资料的筹备前置时光。 5、生产线及仓库所须要的场合大小(场地负荷才能)。 二生产排期应注意什么原则? 生产计划排程的部署应注意以下原则: 1、交货期先后原则:交期越短,交货光阴越紧迫,越应部署在最早时间生产。 2、客户分类原则:客户有重点客户,一般客户之分,越重点的客户,其排程应越受到器重。如有 的公司依据销售额按ABC法对客户进行分类,A类客户应受到最优先的待遇,B类次之。C类更次。 3、产能平衡原则:各生产线生产应顺畅,半成品生产线与成品生产线的生产速度应雷同,机器负 荷应斟酌,不能发生生产瓶颈,呈现停线待料事件。 4、工艺流程原则:工序越多的产品,制作光阴愈长,应重点予以关注。 三PMC管理做得差,容易造成什么现象? PMC的筹划能力、节制才能及沟通调和能力做得差,容易造成以下现象: 1、经常性的停工待料:因为生产无计划或物料无计划,造成物料进度经常跟不上,以致经常性的 停工待料 2、生产上的顿饱来一顿饥:因为经常停工待料,等到一来物料,交期自然变短,生产光阴不足, 只有加班加点赶货,结果有时饿死,有时撑死。 3、物料计划的不准或物料控制的不良,半成品或原资料不能连接上,该来的不来,不该来的一大 堆,造成货仓大批堆积资料和半成品,生产自然不顺畅。 4、生产计划表仅起情势上的作用,生产计划与实际生产脱节,计划是一套,生产又是
企业产能分析
企業產能分析 産能收縮 當企業不能適應市場的變化,因經營不佳而陷入困境時,需要進行産能收縮。在收縮中應盡可能减少損失,力爭在收縮中求得新的發展。下面介紹産能收縮的幾條途徑: 1.逐步退出無前景行業 經過周密的市場分析,如果確認本企業所從事的行業行將衰退,企業就需要考慮如何退出該行業。由于市場衰退是預測分析的結果,還不是現實,企業只不過在近年中感覺到衰退的迹象。所以企業首先停止在此行業的投資,然後分階段地撤出資金和人員。之所以采取逐步退出的策略,是因爲還有市場。另外,企業資金的轉移也不是一件很容易的事情,企業不能輕易放弃還有利可圖的市場,這樣做可以盡可能地减少損失。 2.出售部分虧損部門 對于一些大企業,如果某些子公司或分廠的經營狀况很差,消耗企業大量的資源,使公司背上了沈重的負擔,扭虧又無望,這時不如抛售虧損部門。這個方法是西方企業處理虧損子公司所通常采用的方法。對待出售資産的决策應有積極的態度,出售是收縮,但收縮是爲了卸掉包袱,爭取主動,爲發展創造條件。 3.轉産 如果本行業已日暮途窮,而企業的設備還是比較先進的,員工的素質也很好,可以考慮轉向相關行業。由于是相關行業,加工工藝相似,大部分設備可以繼續使用,員工們的經驗可以得到充分的發揮。例如,服裝廠可以轉向床上用品和居室裝飾品,食品廠可以轉向生産動物食品等等。 學習效應與學習曲綫 在考慮産能大小的决定時,往往要考慮到學習效應這一决定産能大小的重要因素。所謂學習效應是指當以個人或一個組織重復地做某一産品時,做單位産品所需的時間會隨著産品數量的增加而逐漸减少,然 後才趨于穩定。如下圖所示: 由上圖可以看出,學習效應包括兩個階段:一是學習階段,單位産品的生産時間隨産品數量的增加逐漸减少;二是標準階段,學習效應可忽略不計,可用標準時間進行生産。上圖中的曲綫稱爲學習曲綫(learning curves)。它所表示的是單位産品的直接勞動時間和累積産量之間的關係。類式的表示學習效應的概念還有“製造進步函數”(manufacturing progress function)和“經驗曲綫”(experience curve),但它們所描述的不是單位産品直接勞動時間與累積産量之間的關係,而是單位産品的附加成本與累積數量之間的關係。這兩種曲綫的原理與學習曲綫是相同的。常見的學習效應有兩種:個人學習和組織學習。所謂個人學習,是指當一個人重復地做某一産品時,由于動作逐漸熟練,或者逐漸摸索到一些更有效的作業方法後,作一件産品所需的工作時間(即直接勞動時間)會隨著産品累積數量的增加而减少。組織學習是指管理方面的學習,指一個企業在産品設計、工藝設計、自動化水平提高、生産組
产能分析报告及指标明细
产能分析报告及指标明细 The document was prepared on January 2, 2021
产能分析报告模板及指标明细 一、产能修改记录及主要产品信息 注:产Array能分析 报告— —修改 记录 1) 产能发 生变化 时以便 及时追踪。如进行增产以达到完全生产能力,此时生产线通过一系列步骤可以达到完全生 产能力,则应记录下这些变化。填写论证产能时也应同时填写日期。 2)此次产能分析报告均记作初次提交。 注:产品信息 1)完成产能分析报告的首先要明确需要分析的产品的详细信息。包括产品名称、型号、产能概况、客户需求信息等。 2)必要时应完善产品主要零部件供应商信息,以便及时掌握配套商供货情况,平衡零部件供货影响系数。 二、现有设备产能核算
1、预订工作时间标准 注:Array 1)单班 时间:每 班总时间 -每班的 总计可用 小时数。 2)班 次:表示 的是每天 每个工艺操作的班次数。 3)作业率:(总工时-无效工时)/总工时。 人员休息-如果在人员休息的时候,机器也停止运转,则输入每班中机器不运转的时间长度。 计划的维修时间-这是计划的每班中机器停机用于维护的时间长度。 4)年出勤时间:年出勤天数-表示的是每年的工艺运作的天数(扣除法定节假日、双休日)。 5)计算举例:每班8小时、每天2班次、作业率80%、年出勤302天,净可用时间 =8*2*80%*302=时。 2、代表产品制程/线能力计算
1)代 表产 品:所 谓代表 产品指 产品制 程包含 其他所 有产品 制造过 程包含 的所有 工艺过 程;如 存在两种以上产品包含不同工艺过程、需分别取各类型产品代表产品制程并进行线能力分析。2)评价瓶颈工序应排除可用外协、其他生产线可用设备借代等因素影响。 3)每条生产线选取一种或2种产品作为代表说明制程及瓶颈工序即可,其他产品可直接计算毛产能。 3、毛产能核算