时序脉冲燃烧控制系统在北台厂退火炉上的应用
PCS7系统在连退线退火炉的应用

PCS7系统在连退线退火炉的应用许 翔(马钢股份有限公司冷轧总厂, 安徽 马鞍山 243000)摘 要:介绍连续退火热处理工艺及与该工艺相结合的PCS7控制系统,使系统运行和温度控制达到优化,性能达到生产要求,产品质量稳定,又降低生产成本。
关键词:PLC ;PCS7;退火炉;控制系统中图分类号:TG158 文献标识码:A 文章编号:11-5004(2016)7-0108-2某钢铁股份有限公司于2005年从SIEMENS-VAI 公司引进了较为先进的连续立式退火生产线,该立式退火炉由Fives Stein 公司设计,炉型是一个利用全辐射管加热的立式炉[1,2],整个炉内充满氮氢混合气体。
退火炉由以下几个主要部分组成:预热段、加热段、均热段、缓冷段、闪冷段、过时效1、2段、二次冷却段和终冷段。
该退火区域全长143.05m,为立式7层结构,再结晶退火是连退生产线的核心工序。
带钢在炉内随着温度的升高而逐步完成恢复和再结晶过程,在随后的冷却和过时效过程中,通过控制冷却速度和过时效时间获得所需要的组织和性能。
1 退火炉工艺及原理在冷轧带钢生产过程中,带钢经受多道次的冷变形轧制,累积变形高达50%~90%。
如此之大的冷变形量导致冷轧硬化现象使得带钢根本无法进一步加工和使用,所以冷轧后的带钢必须进行再结晶退火。
在再结晶退火过程中,随着带钢的缓慢加热,再结晶过程分为前后衔接的三个阶段:回复――再结晶――晶粒长大。
冷轧带钢的再结晶退火是把冷轧后的带钢加热到再结晶温度以上并保持适当的时间,以控制的冷却速度,达到目标温度的一种热处理工艺。
2 退火炉过程控制系统该立式退火炉的电气控制系统采用SIMENS PCS7过程控制系统,PCS7系统采用分布和数字控制,模块化的硬件与软件,全面集成的现场总线PROFIBUS,开放式系统,自诊断功能[3]。
西门子PCS 7系统是完全无缝集成的自动化解决方案,强大的HMI 人机接口,高可用性和故障安全相结合的形式,集成SIMATIC PDM 软件对智能现场设备进行集中参数化。
蓄热式加热炉换向燃烧系统间歇延时控制工艺的应用

蓄热式加热炉换向燃烧系统间歇延时控制工艺的应用董群;齐晓铭【摘要】唐山国丰钢铁有限公司热轧薄板厂原建一线加热炉使用已达到淘汰年限.该公司通过在设备上应用换向燃烧系统间歇延时控制工艺,实现了燃烧控制自动化,提高了经济效益,保证了产品质量,并有节能环保效果.【期刊名称】《中国设备工程》【年(卷),期】2014(000)003【总页数】3页(P12-14)【关键词】换向燃烧;炉温;节能;经济效益【作者】董群;齐晓铭【作者单位】唐山国丰钢铁有限公司,河北唐山 063300;唐山国丰钢铁有限公司,河北唐山 063300【正文语种】中文【中图分类】TP2782012年7月和2013年9月,唐山国丰钢铁有限公司热轧薄板厂1号线1#、2#加热炉改造重建工程顺利竣工,完成了燃烧系统自动化工程。
在改造前,2座加热炉均已连续使用近7年,炉子的各项指标均不能达到低耗能标准,应淘汰更新。
为了提高热负荷或改善燃烧条件,应当改进燃烧装置,提高炉子生产率。
此项工程已纳入公司2012~2013年年度节能改造规划中。
为节约资金,唐山国丰钢铁有限公司设备部与热轧薄板厂将中冶华天工程技术有限公司研发的换向燃烧系统间歇延时控制工艺专利(国家发明专利号ZL201010250587.3),应用在此次加热炉改造工程中,使用效果良好,产生了明显的经济效益和社会效益。
目前国内大多数双蓄热式加热炉的仪控基本是手动远操控制方式,对操作人员的水平要求很高,影响了炉况的稳定性。
为实现加热炉燃控系统控制自动化,提高炉效率,公司将间歇延时控制方式引入到双蓄热式加热炉的控制系统中,实践证明,效果良好。
1.专利原理通过PLC的计算炉温变化趋势,自动控制情况如下。
(1)当炉温与设定值之间的温差与时间差满足有变大趋势时,说明炉温在上升,供热负荷偏大,此时应将供热负荷减少;(2)当炉温与设定值之间的温差与时间差满足有变大趋势时,说明炉温在下降,供热负荷偏小,此时应将供热负荷增大;(3)当炉温与设定的温度之间的温差与时间差满足没有变大趋势时,说明炉温在控制的范围之内比较恒定,供热负荷适当。
PLC控制在锅炉燃烧系统中的应用
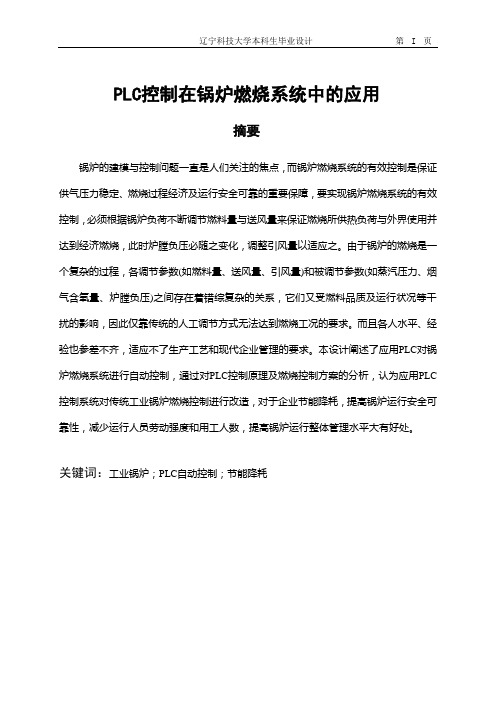
PLC控制在锅炉燃烧系统中的应用摘要锅炉的建模与控制问题一直是人们关注的焦点,而锅炉燃烧系统的有效控制是保证供气压力稳定、燃烧过程经济及运行安全可靠的重要保障,要实现锅炉燃烧系统的有效控制,必须根据锅炉负荷不断调节燃料量与送风量来保证燃烧所供热负荷与外界使用并达到经济燃烧,此时炉膛负压必随之变化,调整引风量以适应之。
由于锅炉的燃烧是一个复杂的过程,各调节参数(如燃料量、送风量、引风量)和被调节参数(如蒸汽压力、烟气含氧量、炉膛负压)之间存在着错综复杂的关系,它们又受燃料品质及运行状况等干扰的影响,因此仅靠传统的人工调节方式无法达到燃烧工况的要求。
而且各人水平、经验也参差不齐,适应不了生产工艺和现代企业管理的要求。
本设计阐述了应用PLC对锅炉燃烧系统进行自动控制,通过对PLC控制原理及燃烧控制方案的分析,认为应用PLC 控制系统对传统工业锅炉燃烧控制进行改造,对于企业节能降耗,提高锅炉运行安全可靠性,减少运行人员劳动强度和用工人数,提高锅炉运行整体管理水平大有好处。
关键词:工业锅炉;PLC自动控制;节能降耗PLC control in the application of boilercombustion systemAbstractThe problem about boiler of modeling and control has been the focus of attention. And the combustion system effective control is to guarantee the supply pressure stability, combustion economic and safe and reliable running. To implement an efficient combustion system control, we must constantly adjusting boiler fuel consumption and air supply under load to ensure that the heating load with the outside world to use and economical combustion. Furnace pressure will change with time, adjusting the air volume to meet the guidelines. As the combustion of boiler is a complex process. And there are a complex relationship between the adjustment parameters (such as fuel consumption, air supply, air flow lead) and the adjustable parameters (such as steam pressure, oxygen content in the flue gas, furnace pressure). They are also affected by fuel quality and the health effects of such interference, so only on the traditional manual adjustment mode does not meet the requirements of the combustio n conditions. And people’s level, experience recognizing, adapt the production process and the requirements of modern business management. The article gives the PLC on system for automatic control. Through the PLC control principles and combustion control methods, we argue that the transform of PLC control system on the traditional industrial combustion is good at heating energy enterprises, improving the boiler operation safety and reliability, reducing our labor and employment for the operating personnel, increasing the number of overall management of the boiler operation.Key words:industrial boiler, PLC automatic control, energy conservation目录摘要 (I)Abstract (I)目录 (II)1 绪论 (1)1.1 课题研究背景及意义 (1)1.2 锅炉燃烧控制系统的国内外发展现 (1)1.2.1 锅炉燃烧控制系统发展简介 (1)1.2.2 锅炉燃烧控制策略研究现状 (2)1.3 PLC控制在国内外的发展近况 (2)1.4 本课题研究内容 (3)2 锅炉燃烧系统设计 (4)2.1 锅炉的工作过程简介 (4)2.2 锅炉燃烧系统简介 (5)2.2.1 锅炉燃烧系统工艺 (5)2.2.2 锅炉燃烧控制系统要求 (6)2.3 锅炉燃烧控制系统设计 (6)2.3.1 锅炉燃烧控制系统结构 (6)2.3.2 锅炉燃烧控制总体框架 (7)2.3.3 燃料子系统设计 (7)2.3.4 送风子系统设计 (8)2.3.5 引风子系统设计 (8)3 锅炉燃烧控制系统硬件部分设计 (10)3.1 可编程控制器(PLC)简介 (10)3.1.1 可编程控制器(PLC)工作原理 (10)3.1.2 可编程控制器的主要特点 (11)3.2 可编程控制器(PLC)选型 (11)3.2.1 可编程控制器CPU选择 (11)3.2.2 模拟量输入/输出扩展模块 (12)3.3 PLC及其扩展模块接线 (12)3.3.1 PLC I/O地址分配表 (12)3.3.2 PLC及其模块接线 (12)3.4 变频器 (13)3.4.1 变频器基本结构 (14)3.4.2 变频器驱动风机原理 (15)3.4.3 变频器选择 (16)4 锅炉燃烧控制系统软件部分设计 (17)4.1 Step7软件简介 (17)4.2 PLC系统的软件设计 (18)4.2.1 控制算法流程 (18)4.2.2 梯形图 (19)结论 (24)致谢 (25)参考文献 (26)附录梯形图 (27)1绪论1.1课题研究背景及意义锅炉是工业生产中普遍使用的动力设备,是能源转换的重要工具。
锅炉燃烧时序控制系统PLC设计与改造

锅炉燃烧时序控制系统PLC设计与改造管成程【期刊名称】《《船电技术》》【年(卷),期】2019(039)008【总页数】4页(P40-43)【关键词】可编程控制器(PLC); 锅炉燃烧时序控制; 设计与改造【作者】管成程【作者单位】青岛港湾职业技术学院山东青岛 266404【正文语种】中文【中图分类】G712锅炉作为船舶动力装置之一,是船上较早实现自动控制的设备。
在蒸汽动力装置中,它产生的蒸汽可以用来驱动船舶主机;在内燃机动力装置中,作为辅助锅炉产生的蒸汽可以加热货油;在柴油机货船中锅炉产生的蒸汽可以加热燃油、滑油,还可以为船员生活提供热力[1]。
如何成功点火和燃烧是使用锅炉的前提,本文重点介绍利用西门子可编程控制器(PLC)实现锅炉的燃烧时序控制。
锅炉的自动控制并非孤立存在,它和多方面有关联,比如:水位的自动控制、蒸汽压力的自动控制、锅炉点火及燃烧的时序控制和自动安全保护。
锅炉燃烧时序控制系统按照时间顺序的先后,完成预扫风、预点火、点火、燃烧、以及停炉。
如图1,启动锅炉前先检查是否满足条件,条件满足就按下启动按钮,进入预扫风阶段,燃油泵开启,但是燃油电磁阀关闭,让油路进入外循环;鼓风机开启,风门挡板先不开启,利用大风进行预扫风,把炉腔内残存的油气排出,防止在点火时出现“冷爆”。
预扫风时间根据锅炉结构不同持续时间不同,一般持续几十秒时间。
预扫风结束后进入预点火状态[2]。
在保持鼓风机开启状态,接通风门挡板的电磁阀,关小风门,输出少量风;油泵和燃油电磁阀保持不变,接通点火变压器,点火电极打火,进行预点火,时间几秒钟。
然后进入正式点火,保持点火电极持续打出火花,保持小风门,打开燃油电磁阀,开大回油阀,利用小风量和少喷油进行点火。
点火成功后维持一段时间的底火燃烧,让锅炉的温度缓慢上升,进行预热。
然后进入负荷控制燃烧,开大风门和关小回油阀,提供大风量和多油量,按照一定比例进行充分燃烧。
在点火和燃烧过程中,出现任何异常情况都要进行保护,不管是点火失败还是中间熄火,都要保持扫风一段时间后,关断各个输出。
基于双交叉限幅的连续退火炉燃烧控制系统分析

并结合使 用高速煤气烧 嘴 , 借 助高 速煤气烧 嘴的燃 烧效 率 , 采
取直接燃 烧的方式加 热 , 能够对钢 带等金属 物质进 行均 匀 、 无 氧化的加热 , 因此提高 了加热的效率 , 缩短 了加热所需 的时 间, 同时也缩短了炉子 的长度 。炉 喉的作用 主要是 控制相 关 的燃
控制 温度的过程 中显现 出了 自身 的不 足 , 在 数学模 型方 面 无
空气的进入 , 完成进 口密封 的功能 。在 预热段 , 能够利 用烟气
的物理热 、 气 体 的燃烧 热等 热量 来完 成金 属 设备 的预热 。同 时, 在预热时 , 需要 配 置相关 的补燃 烧嘴 , 并 供 给补燃 烧 嘴空 气, 而不必供给煤气 。在加热炉 阶段 , 采用焦 炉煤气作 为燃料 ,
降低 了操作程序 的运 行效率 。另外 , 在整 个 D O S的操作模 式 中, 人 为因素成 为 非 常重 要 的 一个 方 面 , 由于过 多 的人 工 干 预, 造成各 个工作组 的实 际操 作水平不 一 , 无法对其 进行 系统 化、 标 准化管理 , 因此 不利 于实 行大 规模 的机 械作 业 , 无 法提
中的变化 , 适应不断变化的生产 线工作流程 。
连 续 退 火 炉燃 烧 控 制 系 统 基 本 能 满 足 生 产 工 艺 的 需 要 ,
选取 。连续退火炉燃烧控制系统能够控制生产 线中的压力 , 使
其保持为定值 , 以适应 生产线 主机负荷 的变化 , 确保 生产 线的
正 常运 转 与 作 业 。
基 于 双 交 叉 限幅 的连 续 退 火炉 燃烧 控 制 系 统 分析
孙云 鹏
( 中冶南 方工 程技术 有 限公司 , 湖北 武 汉 4 3 0 2 2 3 ) 摘 要: 从连 续退火 炉燃 烧控 制技 术 的发展现 状及 问题 、 基于 双交叉 限 幅的连 续退 火炉退 火工 艺与燃 烧控 制 概述 、 燃 烧控 制 系统 设计
PLC自动控制技术在电热退火炉中的应用

2019年 第5期热加工45PLC 自动控制技术在电热退火炉中的应用■ 胡振庐,王志斌,白永胜,任紫亭摘要:通过对电阻炉电控系统解析,加装了一套自动控时电路系统,通过PLC 程序编程,能够智能截取工艺保温起点和终点,并按工艺要求计时后自动切断加热电路,然后在炉冷工艺段完毕声光提示出炉空冷,最后自动关闭程序。
该系统与原手动电路互不干扰,生产中可以根据需要,自主切换“手动/自动”控制系统。
关键词:电阻炉;PLC ;自动控时电路;退火炉我公司的一台额定功率500kW 的电阻退火炉,额定温度为650℃,适用于液压支架结构件焊后低温去应力退火作业。
高耗能的退火炉实行间歇作业,通常选在夜间用电低峰时开启,夜间员工作业疲乏,人工计时常出现保温时间过长的情况,一个月累计的无谓耗能很大,并且长时间退火保温对焊缝性能及结构件母材性能有降低的风险。
为解决这一问题,对原设备进行了电控改造,加装一套自动控时电路,通过PLC 编程来控制各加热温区的通断,准确截取保温起点和终点,保证保温时长。
1. 技术要求退火工艺曲线如图1所示,室温装炉加热到520℃时开始保温,工艺要求保温90~120min ,而后炉冷到300℃出炉空冷。
该退火炉分为4个温区,由并排的两个电控柜进行操作控制,改造要求用一个PLC 控制器控制4个温区的通断,并智能截取升温阶段终点,即保温阶段起点,在适当考虑均温时间的情况下,计时保温2h 后断开加热回路,程序在炉冷阶段继续运行,炉冷到300℃时声光提示出炉空冷,程序自动关闭,达到与工艺曲线相契合的节能保质效果。
2. 电控改造方案电阻炉原电路分为4条加热回路,4条温控回路,风扇、炉门升降及超温报警回路。
采用的改造方式是控制加热回路的开关,温控回路仍由其温控仪表控制,只采集或共享其中一个热电偶的温度值,其他电路不动。
这样可以把PLC 控时电路对原电路的影响程度降到最低,达到PLC电路与原电路互不干扰的效果。
改造电路如图2所示。
连续退火炉节能减排降耗的控制措施
(上接第215页)摘要:我国的连续退火炉建设还处在初级阶段,为了能够更好地促进这一技术的可持续发展,业内人士一直在探索影响连续退火炉能耗的主要因素,并不断致力于钻研提高产品质量和生产效率、减排降耗的各种方法。
通过不懈的努力,终于探索出连续退火炉从设计、生产到投入使用、保养、维修等各个环节中息息相关的联系,从而得出了一些有效控制能耗、减排环保的基本措施。
关键词:连续退火炉燃烧控制余热回收节能降耗对于大型的连续退火炉,影响到成品质量和给环境带来的伤害的主要因素是炉内压力、露点以及氧含量,从生产制造、安装至运行均应当按照节能降耗的标准来操作。
除此之外,各种加热和冷却技术也是连续退火炉减排降耗的重要指标。
而对于一些小型的机器设备,提高产品竞争力的最佳选择就是利用低压换热器来回收余热。
传统的退火炉作业在加热、燃烧控制和后期余热处理等方面都存在粗放浪费的缺陷,因此,新型数字化的控制技术很好地给连续退火炉的应用和发展指明了方向。
1影响连续退火炉能耗的主要指标炉压主要是由分布在炉子底部大量保护气体注入而形成的压力室,是为了防止外界气体进入炉内,从而保证炉内微正压稳定,生产安全和质量合格。
而为了达到这一目的,往往需要通过注入大量保护气体,为了确保炉内温度,需要大大增加燃气量,这也就增加了排气量和能源消耗。
露点是指在炉内气压固定的条件下,空气中的气态水达到饱和状态凝结为液态水所需的温度,它是衡量连续退火炉内环境干燥程度的重要指标,受炉内原材料所含的氧化物和其表面残留水分的影响。
在实际操作中,存放时间较长的铝带原料表面容易产生氧化铝,一旦进入炉内,遇到氢气,二者发生化学反应生成水,炉内的露点便会增高。
为了给退火炉减压,稳定其温度,就必须增加保护气体的注入量和排放量,另一方面,此举也大大增加了辐射管的燃烧功率。
允许氧含量是因为炉内气体流动非常复杂,各处的压强正负不一,再加上机器外壁焊接工艺粗糙、封闭性差等原因,均有可能导致炉内含氧量增加,而保护气体中的氢气与之发生反应会生成水,继而影响了露点。
连续退火炉烧嘴ON-OFF点火控制的应用
“ N—O F 脉 冲点火 , 种 方式 控 制 的灵 活性 提 O F” 这
高 , 少助 燃空 气过 剩 量 并 使其 部 首加 热 功率 调 减
整 的影响 。
当煤气 的热 值发 生变 化 时 , 烧 状 况将 会 发 燃
生 很 大 的变 化 , 温度将 会急 剧增 加 , 而采用 这种 控
8个 部分 。 Βιβλιοθήκη 1 加 热段 辐射 管分 布
退 火 炉加 热 区域 主要 由加 热 段 和 均 热 段 组
成 。加 热 段 带 钢 行 程 有 1 5个 道 次 , 程 约 3 0 全 0
m。加 热 段 布置 了 1 7列共 10个 辐 射 管 , 8 每一 个 辐 射管 都有 一 套控 制单 元 , 含 点火 系统 、 立 的 包 独 助 燃空 气/ 气 气 开 关 阀 、 焰 检 测器 等 设 备 , 煤 火 炉
2 1 第 4期 0 2年
梅 山科 技
・ 3・ 3
连 续退 火 炉 烧 嘴 O — F N O F点 火 控 制 的应 用
李 丹
( 山钢铁 公 司冷 轧厂 生产技 术 室 南京 梅
203 ) 10 9
摘
要: 主要 分 析 了连 续退 火 炉烧嘴 O .F N O F控制 的 特点 和在 点 火控 制 方 面的应 用情 况 。
K e o d b r r i n t n; a ee to y w r s: u ne ;g ii f me d t ci n o l
梅 钢 冷 轧 厂 新 建 连 续 退 火 机 组 是 由 法 国
动 进行 热量 分配 控 制 。
表 1 加 热段各 列 辐射 管功 率分布 / W k
燃烧优化控制系统在链条炉上的应用
行状态 , 缩短 了锅炉正常运行 周期 ,烟 囱经常 冒黑烟 ,即浪
费了能源 ,又严 重污染了环境 ,同时 由于燃烧不充 分 ,使燃 烧 成本大大增加 。 目前 ,在我国锅炉控制还存在 以下 问题 :
【 收稿 日期】 2 0 1 3 — 0 7 — 1 8
1 ) 基 础 自动化仪 表配 置水平 低 ,只安装 一些 简单 的测
6 ) 技术很成熟 ; 7 ) 各种投入成本不 高 ;
8 )效益很 明显 。
2 B CS 技术在 中小燃煤链条炉上的应用分析
5 0 万 台左右 。针对我 国 中小企业 中 占主体的多种规 格的链条 炉 的现 状 ,在现有 的条件下进行技术 改造还是很 有潜力 的。
在本文 中将 重点介绍 B C S 技术 应用于链条炉的情况 。
本世纪 前3 0 年甚至更长 时间 ,在我 国一次性能源构 成 中,煤 炭仍将 占主体地位 。 目前 ,我国对煤 炭的主要 利用方式仍然
1 . 1“ 通用优 化控 制技 术 ( B C S) ” 的核心技 术包 括 以下四
方面:
1 )软测量技术 ;
2 ) 有 限条件下 的燃烧优化技术 ;
3 ) 运行安全稳定可靠 ;
4 )维护工作量很小 ; 5 )操作非常简单 ;
制水平 低的原 因主要 和锅炉的燃烧方 式及控制特 点有关 ,输 入输 出变量多 ,特 别是各变量之 间互相关联互相 影响 ,十分
复杂 。 目前我 国 中小 型燃 煤 锅 炉主 要 以链 条 炉为 主 ,数 量在
仍 是两大难题 ,这些 问题 的存 在导 致锅炉长期处于 不稳定运
“ 通 用优化 控制技术 ( B C S)”的 目的是 完善各 类锅炉
- 1、下载文档前请自行甄别文档内容的完整性,平台不提供额外的编辑、内容补充、找答案等附加服务。
- 2、"仅部分预览"的文档,不可在线预览部分如存在完整性等问题,可反馈申请退款(可完整预览的文档不适用该条件!)。
- 3、如文档侵犯您的权益,请联系客服反馈,我们会尽快为您处理(人工客服工作时间:9:00-18:30)。
时序脉冲燃烧控制系统在北台厂退火炉上的应用 2005-12-12 10:37:23 有祥武 荣莉 马庆云 柴天佑 供稿 摘要:主要介绍了北台球墨铸铁管厂退火炉时序脉冲燃烧控制系统的组成、控制原理和动态性能,指出时序脉冲燃烧控制方式的优点以及在引进应用中应注意的问题。 关键词:时序脉冲燃烧控制流量退火炉燃烧控制器烧嘴
Application of time series pulse combustion control system to annealing furnace in Beitai Ductile Cast Iron Pipe Plant
You Xiangwu (Beitai Ductile Cast Iron Pipe Plant Benxi 117017) Rong Li Ma Qingyun Chai Tianyou (Automation Research Center of Northeastern University)
Abstract The composition, control principle and dynamic characteristics of time- series pulse combustion control system applied to the annealing furnace in Beitai Ductile Cast Iron Pipe Plant are introduced. The advantages of the above mentioned control system are described. And finally, some problems to be paid attention to when that technique is imported or applied are pointed out. Key words time- series pulse combustion control; flowrate; annealing furnace; burning controller; burner nozzle
近年来,随着燃烧控制技术的不断发展,一些热值较高的燃料(如:天然气、重油等)被逐步应用于热处理工艺中。在传统的燃烧控制方式中,给加热炉加热一般是通过调节燃料和空气的流量使之充分混合、燃烧来完成的,即在加热的过程中,燃料和空气的流量是连续变化的。但在燃料热值较高的情况下,使用少量的燃料就可以满足热处理工艺的要求,因此燃料和空气的流量都比较小,输送燃料的管路截面也比较小,如果采用连续燃烧的方式进行控制,控制燃料流量的碟阀就要做得很小,而控制系统的响应能力无法满足流量变化的需要,因此控制温度的误差是很大的。为了解决这个问题,国外一些专家自80年代初即开始对时序脉冲燃烧控制系统进行了研究和应用。这种控制系统是通过控制烧嘴的燃烧时序和燃烧时间来控制炉子的温度。由于它具有动态性能好、控制温度波动小、节约燃料等优点,因而得到了广泛的重视和应用。我国自90年代初开始引进这项新技术,经实际应用验证,效果良好,具有较大的推广价值。下面以北台球墨铸铁管厂退火炉时序脉冲燃烧控制系统为例,介绍这种控制系统的组成和控制原理。 1 工艺简介 北台球墨铸铁管厂退火炉是1994年从德国IOB公司引进的,具有世界先进水平。该退火炉使用混合煤气作燃料,采用直火加热的方式对球墨铸铁管进行退火。炉子的结构为卧式,共有6个区,其中1区为加热区,温度控制在1010℃;2、3区为保温区,温度控制在970℃;4区为冷却区;5、6区为低温区,温度控制在700℃。管子在炉内运输链的带动下,以一定的速度由1区进入,从6区输出。按照设计要求,北台球墨铸铁管厂所用煤气热值为9200kJ/m3,压力为8000Pa。由于管子在1、2、3区进行了加热处理,到达5区时温度仍然在500℃以上,因此5、6区的热负荷较低,所用煤气的流量较小。5区共有4个烧嘴,全部燃烧时煤气总流量为250m3/h左右。6区共有6个烧嘴,全部燃烧时煤气总流量为350m3/h左右。5区煤气管路直径为100mm,6区煤气管路直径为120mm。为了满足工艺要求,5、6区采用了时序脉冲燃烧控制系统。由于5、6区控制系统在设计上基本是一样的,为此,本文仅以5区为例介绍时序脉冲燃烧控制系统的组成和控制原理。 2 控制系统 2.1 组成及工作原理 控制系统的硬件结构简图如图1所示。
其工作原理如下。炉子的温度是通过PI调节器设定的。PI调节器对设定的温度与热电偶检测到的炉子实际温度进行采样,并按照PI算法(即比例、积分算法)计算出偏差值,由偏差值的大小输出一个4~20mA的电流信号。这个电流信号经过A/D转换器转换成数字量以后,送给S5-115UPLC控制系统。S5-115U产生一系列时序脉冲信号,并根据输入数字量的大小控制不同的燃烧控制器和烧嘴,使它们按照一定的时序点燃或熄灭,进而控制退火炉的温度。图1中,PI调节器采用PHILIPS公司的KS4290系列数字式调节器。这种调节器是PHILIPS公司于90年代初生产的新型智能化调节器,可以实现正偏差和负偏差两种调节方式,即当PI算法计算出的偏差值为正时,调节器工作在正偏差调节方式,输出电流在12~20mA之间变化。当PI算法计算出的偏差值为负时,调节器工作在负偏差调节方式,输出电流在4~12mA之间变化。S5-115U可以根据A/D转换器输出的数字量的大小来识别调节器工作在哪一种调节方式。当调节器工作在负偏差调节方式,并且炉子的温度高于工艺要求的温度范围时(5区的温度范围为690~710℃,高于温度范围是指高于710℃),S5-115U熄灭所有的烧嘴,并打开冷却装置对退火炉实施冷却。 2.2 软件设计 在时序脉冲燃烧控制系统中,烧嘴何时点燃是由时序脉冲信号控制的,而烧嘴的燃烧时间是由设定温度和炉子实际温度的偏差值决定的。因此如何产生时序脉冲信号以及如何控制烧嘴的燃烧时间是时序脉冲燃烧控制系统需要解决的关键性技术问题。为了确保系统的可靠性,该控制系统采用S5-115UPLC控制系统来生成时序脉冲信号和控制烧嘴的燃烧时间。 5区共有4个烧嘴,对称分布在炉内两侧。S5-115U使用4个扩展脉冲计时器T0、T1、T2、T3分别控制1#、2#、3#、4#4个烧嘴。计时器的计时值是通过A/D转换器转换以后得到的数值。计时器是通过S5-115U的一个中间标志字节FY29的4个标志位的信号状态来启动的,即当标志位FY29.3的信号状态为1时,启动计时器T3,点燃4#烧嘴;当标志位FY29.2的信号状态为1时,启动计时器T2,点燃3#烧嘴;依此类推,当标志位FY29.0信号状态为1时,启动计时器T0,点燃1#烧嘴。为了使标志位的信号状态能依次被置位和复位,进而产生时序脉冲信号,图2为一个循环的程序流程框图。
图2中,占空比为0.1s∶5s的脉冲信号,指脉冲信号为1时的时间值为0.1s,脉冲信号为0时的时间值为5s。当脉冲1到来时,执行第1个判断Y以后的程序,FY29.3置位为1,FY29.2、FY29.1、FY29.0为0。第1个脉冲过去后,执行第1个判断N以后的程序,各标志位的状态将维持5s。第2个脉冲到来时,信号状态为1的位,将由FY29.3移至FY29.2,FY29.3将由0补充。同时,由于执行了第2个判断N以后的程序,将不再置位FY29.3。FY29.1、FY29.0仍为0。第2个脉冲过去后,这个状态仍将维持5s,……当第5个脉冲到来时,将执行两个判断Y以后的程序,重新置位FY29.3,开始下一个循环。由程序流程图产生的各个标志位及各个计时器的信号状态如图3所示。
图3中各标志位置位的时序即是各烧嘴被依次点燃的时序,计时器的信号状态即是烧嘴的工作状态。每个烧嘴经过20s被循环点燃一次。时间t即是烧嘴的燃烧时间,是由PI调节器计算出的温度偏差值控制的。 2.3 燃烧控制器及烧嘴的工作原理 由于在时序脉冲燃烧控制系统中,烧嘴要被频繁地点燃和熄灭,这就要求燃烧控制器和烧嘴要有快速的响应能力,这是决定该控制系统是否可靠和实用的一个重要因素。北台球墨铸铁管厂退火炉采用德国KROMSCHRODER公司于90年代初研制生产的IFS110IM型燃烧控制器。烧嘴采用该公司同期生产的ZKIH20/10型点火烧嘴以及与之配套使用的LBY70型燃烧烧嘴。点火烧嘴安装在燃烧烧嘴的内部,它使用的煤气和空气是由辅助煤气管路和辅助空气管路提供的。辅助煤气管路和辅助空气管路上分别安装着辅助煤气阀和辅助空气阀,其中辅助空气阀是一个手动控制阀,一般情况下始终是打开的。燃烧烧嘴使用的煤气和空气是由主煤气管路和主空气管路提供的。主煤气管路和主空气管路上分别安装着主煤气阀和主空气阀。每个烧嘴由一个燃烧控制器控制,其控制系统线路原理如图4所示。
YL1、YL2、YL3—电磁阀线圈;Y1、Y2、Y3—电磁阀;KL1、KL2、KL3—中间继电器线圈;K1、K2、K3—中间继电器辅助接点; S—起动按钮;A—烧嘴;T—高压线圈;Y4—手动控制器
工作原理如下。首次点燃烧嘴时,按动启动按钮S,燃烧控制器首先打开辅助煤气阀Y1,同时燃烧控制器在高压线圈T上产生的高电压通过点火烧嘴A放电,点燃辅助煤气管路。燃烧控制器通过检测回路在3s内检测点火烧嘴是否被点燃,如未被点燃,则切断辅助煤气阀;如已被点燃,则给中间继电器K3送电,使K3吸合。K3的辅助接点接在S5-115U的输入接口上,S5-115U根据K3是吸合的还是断开的来判断点火烧嘴是点燃的还是熄灭的,