球墨铸铁的工艺原理
球墨铸铁板材料-概述说明以及解释
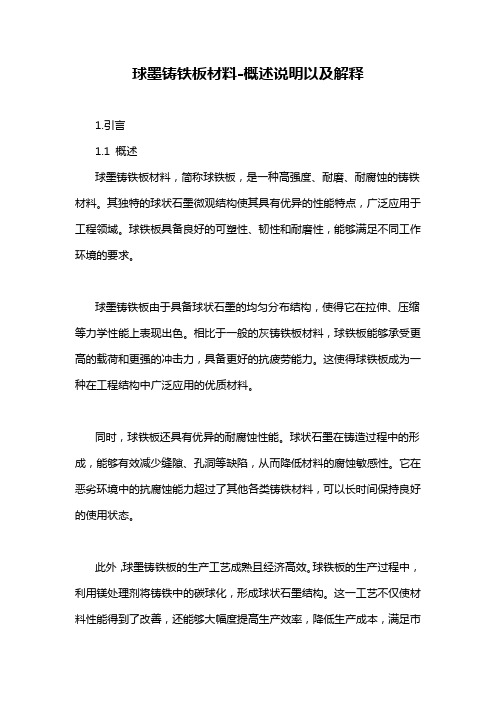
球墨铸铁板材料-概述说明以及解释1.引言1.1 概述球墨铸铁板材料,简称球铁板,是一种高强度、耐磨、耐腐蚀的铸铁材料。
其独特的球状石墨微观结构使其具有优异的性能特点,广泛应用于工程领域。
球铁板具备良好的可塑性、韧性和耐磨性,能够满足不同工作环境的要求。
球墨铸铁板由于具备球状石墨的均匀分布结构,使得它在拉伸、压缩等力学性能上表现出色。
相比于一般的灰铸铁板材料,球铁板能够承受更高的载荷和更强的冲击力,具备更好的抗疲劳能力。
这使得球铁板成为一种在工程结构中广泛应用的优质材料。
同时,球铁板还具有优异的耐腐蚀性能。
球状石墨在铸造过程中的形成,能够有效减少缝隙、孔洞等缺陷,从而降低材料的腐蚀敏感性。
它在恶劣环境中的抗腐蚀能力超过了其他各类铸铁材料,可以长时间保持良好的使用状态。
此外,球墨铸铁板的生产工艺成熟且经济高效。
球铁板的生产过程中,利用镁处理剂将铸铁中的碳球化,形成球状石墨结构。
这一工艺不仅使材料性能得到了改善,还能够大幅度提高生产效率,降低生产成本,满足市场需求。
球墨铸铁板的应用领域广泛多样。
它被广泛应用于汽车制造、机械工业、建筑工程等领域。
在汽车制造中,球铁板常用于发动机铸件、底盘部件等重要组成部分,以提高汽车的安全性和可靠性。
在机械工业中,球铁板常被用于制造齿轮、曲轴等高强度零部件,为机械设备的正常运行起到关键作用。
在建筑工程中,球铁板可用于制造桥梁支座、阀门等被要求具备高强度和耐久性的构件,以确保建筑物的牢固和安全。
总之,球墨铸铁板材料由于其卓越的性能优势,在工程领域得到了广泛应用。
其具备的高强度、耐磨、耐腐蚀等特点,使其成为众多行业的首选材料。
随着科学技术的不断进步和应用范围的扩大,球铁板材料的发展前景将更加广阔,有着充满希望的未来。
1.2文章结构文章结构的安排是为了使读者更好地理解和吸收文章内容。
在本篇文章中,我们将采用以下结构来组织和展示关于球墨铸铁板材料的相关信息。
首先,我们将在引言部分简要介绍球墨铸铁板材料的概况和背景。
QT500—7球墨铸铁熔炼工艺的设计说明

QT500-7球墨铸铁熔炼工艺设计摘要合金熔炼是铸造生产中的重要环节。
当前,铸造生产中的废品约有50% 与熔炼有关,熔炼铁液的成本约占铸件成本的25%~30% ,合金熔炼对铸件质量和成本有着很大的影响。
我们应该针对不同的铸件材质与技术要求选择不同的熔炼方法。
本设计题目为QT500-7球墨铸铁熔炼工艺设计,体现了球墨铸铁熔炼的设计要求、容与方向,有一定的设计意义。
通过对该牌号球墨铸铁的设计,进一步加强了设计者熔炼工艺设计的基础知识,为设计其它牌号铸铁的熔炼做好了铺垫和吸取了更深刻的经验。
本设计运用铸造合金熔炼的基础知识,首先分析了QT500-7球墨铸铁的成分与性能要求,为选取熔炼设备与炉料做好了准备;然后选取熔炼设备,计算炉料的比例用量;最后设定球化、孕育方法,确定浇注温度参数,进行质量检测与分析。
本设计着重点在于使用冲天炉-感应电炉双联熔炼球墨铸铁。
由冲天炉熔化铁液并进行化学成分含量的初步确定;在感应电炉中高温精炼,调整铁液的化学成分至规定的围;进一步清除非金属夹杂物和降低气体含量;提高铁液温度至符合出炉球化要求;最终球化与孕育处理,出炉检测。
关键词:球墨铸铁双联熔炼球化处理孕育处理QT500-7 Ductile Iron Smelting Process DesignAbstractAlloy melting is an important part in casting production. At present,about 50% of the waste in the foundry production is related to the smelting. The cost of the molten iron is about 25% - 30% of the cost of the casting.We should choose different smelting methods for different casting materials and technical requirements.This design topic is QT500-7 nodular cast iron smelting process design,reflects the design requirements, content and direction of ductile iron smelting, there is a certain design significance. Through the design of this type of ductile iron, further strengthen the designers of the basic knowledge of smelting process design for the design of other grades of cast iron to pave the way and draw a more profound experience.The design and use of casting alloy melting of basic knowledge, the first analysis of the QT500-7 nodular cast iron composition and performance requirements for the selection of smelting equipment and charge ready;then select smelting equipment, calculation burden ratio; finally set the ball, inoculation method, to determine the parameters of casting temperature, quality detection and analysis.This design is focused on the use of cupola induction furnace duplex melting of nodular cast iron. By cupola melting iron liquid and preliminary identification of chemical components; in the induction furnace high temperature refining, adjustment of the liquid metal chemical composition to the specified range; further clear non metallic inclusions and reduce the gas content; improve the temperature of molten metal to meet released the ball of the requirements; and eventually the ball and inoculation treatment, detection of released.Key words:Ductile iron,Tecastiron,Spheroidize,Inoculation treatment目录摘要IAbstractI1 绪论11.1球墨铸铁的出现11.2国外球墨铸铁的发展11.3球墨铸铁的应用21.4熔炼工艺与发展31.5课题来源与意义32 熔炼工艺方案的确定42.1熔炼技术要求与分析42.1.1技术要求42.1.2材料性能与分析42.2工艺方案53 冲天炉熔炼工艺设计63.1冲天炉熔炼特性与原理63.1.1冲天炉熔炼概述73.1.2冲天炉熔炼的技术要求73.1.3冲天炉的燃烧过程原理93.2炉料的计算113.2.1球墨铸铁原铁液的配比要求113.2.2QT500-7原始资料的确定123.2.3确定元素增减率与增减后成分123.2.4确定配料比并校核133.2.5炉料计算143.3熔炼工艺与参数143.3.1装炉143.3.2炉前控制143.3.3铁液出炉153.3.4脱硫处理153.4熔炼过程的化学反应164电炉熔炼工艺设计174.1感应电炉的熔炼特点174.1.1感应电炉构造与工作原理174.1.2感应电炉熔炼的优缺点与其应用184.2熔炼工艺与参数184.2.1二次脱硫184.2.2脱磷处理194.2.3精炼调整194.3球化工艺194.3.1球化剂194.3.2QT500-7球化剂的选用214.3.3 QT500-7的球化处理工艺214.3.4球化剂加入量的确定234.4孕育工艺244.4.1孕育剂244.4.2孕育处理工艺254.5出液浇注264.5.1浇注温度对性能的影响264.5.2球铁的浇注温度265质量检验与分析275.1质量检测275.1.1炉前三角试片检验法275.1.2火苗判断法275.1.3炉前快速金相法275.1.4炉前光谱分析法275.2缺陷分析275.2.1球化不良285.2.2球化衰退295.2.3石墨漂浮296 结论30致32参考文献321 绪论铸造是机电装备制造业中铸件生产的工艺过程。
球墨铸铁管的生产工艺

球墨铸铁管的生产工艺
1. 材料准备:球墨铸铁管的原料是铸铁和球墨铸铁毛坯,需要进行配料和熔炼。
配料需要按照一定比例和质量要求将铸铁和球墨铸铁毛坯混合。
2. 熔炼:将配好的原料放入炉中加热熔化,熔炼过程需要加入一定量的稀土镁等元素来提高球墨铸铁的性能。
3. 球化处理:将熔化的铁水倒入球化炉中,通过加入球化剂,将熔体中的碳素球化,生成球墨铸铁毛坯。
4. 浇铸:将球墨铸铁毛坯倒入模型中进行铸造,这个过程需要注意保持炉温、模型温度等因素的控制。
5. 除毛刺:球墨铸铁管铸造完毕后,需要进行质量控制,包括对漏铁、毛刺等进行处理。
6. 机械加工和热处理:球墨铸铁管进行机械加工,包括车、铣、钻、打磨等工艺,并经过热处理使其获得一定的力学性能和耐腐蚀性。
7. 涂层处理:球墨铸铁管可以进行涂层处理,如环氧、沥青、聚氨酯等处理,提高其使用寿命和防腐能力。
8. 包装:球墨铸铁管加工完毕后,进行包装,直至出厂。
球墨铸铁的化学成分

锰可以部分替代硅的作用,并改善球墨铸铁的铸造 性能和耐腐蚀性。
03
锰含量的增加还可以提高球墨铸铁的淬透性和回火 稳定性。
磷(P)和硫(S)的影响
磷和硫是有害元素,会导致球 墨铸铁脆化,降低其韧性和耐 腐蚀性。
控制磷和硫的含量是生产高质 量球墨铸铁的关键之一。
通过合理的熔炼技术和合金化 处理,可以降低磷和硫的含量, 提高球墨铸铁的性能。
VS
智能制造领域
智能制造的发展对球墨铸铁提出了更高的 要求,需要不断优化材料性能和生产工艺 ,以满足智能制造领域的需求。
感谢您的观看
THANKS
生产与应用
生产
通过高温熔炼、球化和孕育处理、浇 注和冷却等工艺过程制备而成。
应用
广泛应用于汽车、机械、化工、电力 、建筑等工业领域,用于制造各种承 受重载和复杂应力的零部件可以追溯到20世纪初,经过多年的研究和发展,其生产工艺和 应用领域不断拓展。
发展
随着科技的进步和应用需求的不断提高,球墨铸铁在成分优化、工艺改进、性 能提升等方面仍有很大的发展空间。
02
球墨铸铁的化学成分
碳(C)
01
碳是球墨铸铁的主要元素,通常 含量在3.0-3.8%之间。碳有助于 提高铸铁的强度和耐磨性,同时 对韧性也有一定影响。
02
碳含量的增加可以提高铸铁的硬 度和强度,但也会降低韧性。因 此,在选择碳含量时,需要根据 具体的应用需求进行平衡。
硅(Si)
硅是球墨铸铁中常见的元素,通常含 量在1.8-3.0%之间。硅有助于提高 铸铁的强度和耐磨性,同时也有助于 提高铸铁的热稳定性和抗氧化性。
硫含量的增加会降低铸铁的韧性和耐腐蚀性。因此,在选 择硫含量时,应尽量控制其含量在较低水平。
球墨铸铁的等温淬火工艺
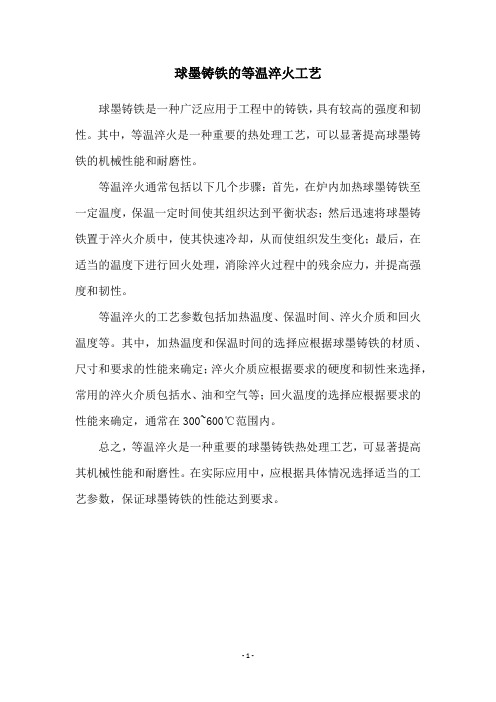
球墨铸铁的等温淬火工艺
球墨铸铁是一种广泛应用于工程中的铸铁,具有较高的强度和韧性。
其中,等温淬火是一种重要的热处理工艺,可以显著提高球墨铸铁的机械性能和耐磨性。
等温淬火通常包括以下几个步骤:首先,在炉内加热球墨铸铁至一定温度,保温一定时间使其组织达到平衡状态;然后迅速将球墨铸铁置于淬火介质中,使其快速冷却,从而使组织发生变化;最后,在适当的温度下进行回火处理,消除淬火过程中的残余应力,并提高强度和韧性。
等温淬火的工艺参数包括加热温度、保温时间、淬火介质和回火温度等。
其中,加热温度和保温时间的选择应根据球墨铸铁的材质、尺寸和要求的性能来确定;淬火介质应根据要求的硬度和韧性来选择,常用的淬火介质包括水、油和空气等;回火温度的选择应根据要求的性能来确定,通常在300~600℃范围内。
总之,等温淬火是一种重要的球墨铸铁热处理工艺,可显著提高其机械性能和耐磨性。
在实际应用中,应根据具体情况选择适当的工艺参数,保证球墨铸铁的性能达到要求。
- 1 -。
第三章球墨铸铁
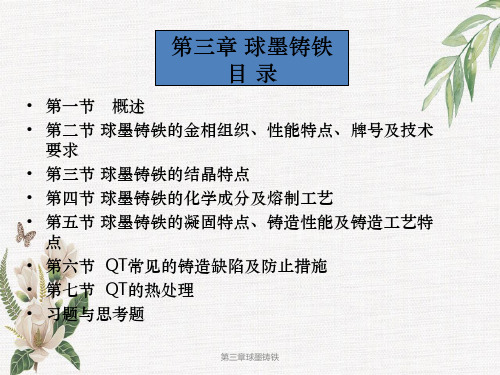
• 2、力学性能的检验 • 本技术要求适用于砂型或导热性与砂型相当的铸型中
铸造的普通和低合金球墨铸铁件,不适用于球铁管件 和连续铸造的QT件。 • QT的力学性能以抗拉强度及伸长率为验收依据,对于 屈服点及硬度有要求时,共需双方协商决定,可作为 验收依据。QT检验用试块形状见图3-7所示,尺寸分 别见表3-9和表3-10。
强度最高、其次是B上、S体、P体、F体。 • QT静载荷性能的一其个突出的特点是屈服点。σ0.2高,超
过正火45钢,比强度σ0.2/σb也高于钢(据测 试:QTσ0.2/σb=0.7—0.8,钢的 σ0.2/σb= 0.3-0.57)。QT可 以代替钢制造静态承力大、材料强度要求较高的件。 • QT硬度比同基体的钢和灰铸铁要高,所以耐磨性能好。 球墨铸铁的弹性模量在159000~172000MPa,而且随球 化率的降低而降低。
第三章球墨铸铁
第三章球墨铸铁
第三章球墨铸铁
• 浇注单铸试块时应与所测铸件同包铁液在干型或湿型 内浇注。若需热处理时,试块应与铸铁同炉热处理。 当铸件质量大于2000kg,且壁厚在30~200mm时, 一般采用附铸试块,热处理后从铸件上切取,其形状 及尺寸如图3-8和表3-11所示。
第三章球墨铸铁
• 三、本章的重点知识
• 本章主要介绍铁素体、珠光体及贝氏体球墨铸铁的金 相组织、性能特点及技术要求,化学成分确定及熔制 工艺,球墨铸铁的热处理、铸造性能及铸造工艺特点, 常见缺陷及其防止措施等。
第三章球墨铸铁
第二节 球墨铸铁的金相组织、性能特点、牌 号及技术要求
• 一、球墨铸铁的金相组织特点 • 1、石墨 • 2、金相基体 • 二、QT的性能特点 • 1、力学性能 • 2、使用性能 • 3、工艺性能 • 三、球墨铸铁的牌号及技术要求 • 1、球墨铸铁的牌号 • 2、力学性能的检验
球墨铸铁的名词解释
球墨铸铁的名词解释球墨铸铁(Ductile Iron),也称球墨铸造铁、球墨球铸铁、球墨铸铁等,是一种铸铁中的一种特殊种类。
它以其优异的机械性能和高强度而被广泛应用于各个领域,从汽车工业到建筑工程,都有着重要的作用。
球墨铸铁是在铸铁基体中添加一定量的镁合金元素(通常为硫酸镁或硫酸镁盐溶解沉淀)后铸造而成。
这种特殊的合金化处理赋予了球墨铸铁既具有铸铁的良好流动性和铸造性能,又具有钢铁的高强度和高韧性。
首先,球墨铸铁的名字来自其外观,它铸造后的铁皮表面呈现出许多球状的石墨颗粒。
这些石墨球形态的存在是由于镁在铁水中与硫形成的镁硫化合物与石墨晶体反应,造成晶体失稳并生成球状石墨颗粒。
这些球状石墨颗粒在弯曲和扭曲应力下具有更好的断裂性能,从而提高了球墨铸铁的韧性和延展性。
其次,球墨铸铁具有出色的机械性能。
相对于灰口铸铁和普通铸铁,球墨铸铁的抗拉强度和抗压强度更高。
这是由于镁在铁水中的作用,能够阻碍石墨晶体的成长,增加铁素体晶格的不规则度,从而提高合金的强度,降低矩阵组织间的应力集中程度。
此外,球墨铸铁还具有良好的耐磨性、耐热性和耐冲击性能,能够适应复杂的工作环境和高强度的使用要求。
此外,球墨铸铁还具有优良的切削加工性能和耐蚀性。
球墨铸铁较硬度低,易于切削和加工,大大降低了模具制造和加工的困难度。
同时,球墨铸铁的耐腐蚀性也较好,对酸、碱和盐等介质有良好的抗腐蚀能力,使其在化工、食品加工等行业中得到广泛应用。
然而,球墨铸铁也存在一些不足之处。
例如,其冷却收缩系数相对较大,易引起内部晶间缩孔和表面缺陷。
此外,球墨铸铁在高温下容易发生奥氏体再生,导致性能下降。
因此,在生产过程中需要严格控制降温速度和冷却条件,以保证球墨铸铁的质量。
综上所述,球墨铸铁是一种通过镁合金化处理铸铁而成,具有石墨球颗粒分布、优良的机械性能、良好的切削加工性能和耐腐蚀性能的特殊合金材料。
它在汽车、机械、建筑、化工等各个领域具有广泛的应用前景。
球墨铸铁铸造工艺流程
球墨铸铁铸造工艺流程
《球墨铸铁铸造工艺流程》
球墨铸铁是一种高性能铸铁材料,具有很高的强度和耐磨性,常用于制造汽车发动机缸体、机床床身等重要零部件。
球墨铸铁的制造工艺流程具有一定的复杂性,需要经过多道工序才能得到优质的铸件。
首先,球墨铸铁铸造的原料主要包括融化铁水、球化剂和稀土镁合金。
在铸造过程中,首先将合格的铁水装入球墨铸铁模具中,然后加入球化剂和稀土镁合金。
球化剂的作用是使铁水中的石墨颗粒球化,提高铸件的韧性和强度;而稀土镁合金则可以进一步改善铁水的流动性和润湿性,提高铸件的表面质量。
随后,通过震动、振动或压力等方法,让铁水在模具中充分填充并冷却固化,形成球墨铸铁铸件。
在这个过程中,需要控制好铁水的温度、流动速度和填充压力,确保铸件的密实性和表面质量。
最后,还需要对球墨铸铁铸件进行去毛刺、修磨、热处理等后续工艺处理,以提高铸件的机械性能和表面光洁度。
整个球墨铸铁铸造工艺流程是一个相当复杂的过程,需要严格控制各道工序的参数和质量,才能保证最终铸件的质量。
同时,还需要使用先进的铸造设备和工艺技术,以确保球墨铸铁铸件具有均匀的组织结构和优异的性能。
球墨铸铁生产工艺流程
球墨铸铁生产工艺流程球墨铸铁是一种具有优异性能和广泛应用领域的铸造材料,其生产工艺流程经过多年的发展和改进,逐渐形成了一套较为成熟和稳定的生产流程。
在球墨铸铁的生产过程中,各道工序的执行严格按照规程进行,确保了最终产品的质量和性能稳定。
本文将详细介绍球墨铸铁的生产工艺流程,包括原料选取、熔炼、浇铸、热处理和表面处理等工艺环节,以期能够对相关领域的研究和生产实践提供一定的参考和借鉴。
首先,在球墨铸铁的生产过程中,原料的选取至关重要。
球铁基体是球墨铸铁的主要结构组织,其质量对最终产品的性能有着直接的影响。
因此,在生产中,通常会选择高质量的生铁和废钢作为原料,经过熔炼、脱硫、合金等工艺处理后,得到具有一定化学成分的熔融铁水。
同时,添加适量的球化剂和脱渣剂,能够有效改善熔铁的流动性和净化度,为后续工艺操作奠定基础。
其次,熔炼阶段是球墨铸铁生产中的关键环节。
在高温环境下,将原料中的生铁和废钢等材料完全熔化并混合均匀,以保证最终产品的化学成分符合标准要求。
同时,熔炼过程中需要不断监测和调整炉温、时间、搅拌速度等参数,确保合金元素的均匀分布和条件的达到。
通过严格控制熔铁的质量和温度,可以有效降低气体和夹杂物的含量,从而提高球墨铸铁的密度和力学性能。
在熔炼完成后,即进入了浇铸工艺环节。
浇注过程需要根据铸件的设计要求和结构特点,选择合适的浇注系统和浇注方式,确保熔铁在模具中充分充实并不产生气孔和缺陷。
此外,在浇铸过程中还需要注意铸件的冷却速度和温度分布,通过控制冷却条件可以调节铸件的晶粒大小和组织结构,进而影响其力学性能和耐磨性。
热处理是球墨铸铁生产过程中一个不可忽视的环节。
通过热处理工艺对球墨铸铁进行退火、淬火等处理,可以有效改善其晶粒结构和强度硬度等性能。
退火处理能够消除内应力和提高材料的韧性,适用于一些要求强度和韧性均衡的应用场合;而淬火则是通过快速冷却使材料产生马氏体变换,提高其硬度和耐磨性,广泛用于一些需要强度和硬度的部件制造。
球墨铸铁QT600--3表面激光多道淬火工艺的研究
学校代号:10532学号:¥1102W244密级:公开湖南大学工程硕士学位论文球墨铸铁QT600.3表面激光多道淬火工艺的研究导师姓名及职称:刘继常教授桂林高级工程师论文提交日期:2013年5月20日StudyontheprocessesofmultichannellasersurfacequenchingofductilecastironQT600-3byLUODanB.E.(nunanUniversityofArtandScience)2011AthesissubmittedinpartialsatisfactionoftheRequirementsforthedegreeofMasterofEngineeringVehicleEngineeringintheGraduateSchoolofHunanUniversitySupervisorProfessorLIUJichangSeniorEngineerGUILinMay,2013湖南大学学位论文原创性声明本人郑重声明:所呈交的论文是本人在导师的指导下独立进行研究所取得的研究成果。
除了文中特别加以标注引用的内容外,本文不包含任何其他个人或集体已经发表或撰写的成果作品。
对本文的研究做出重要贡献的个人和集体,均已在文中以明确方式标明。
本人完全意识到本声明的法律后果由本人承担。
…名:产日期:邳年6月6日学位论文版权使用授权书本学位论文作者完全了解学校有关保留、使用学位论文的规定,同意学校保留并向国家有关部门或机构送交论文的复印件和电子版,允许论文被查阅和借阅。
本人授权湖南大学可以将本学位论文的全部或部分内容编入有关数据库进行检索,可以采用影印、缩印或扫描等复制手段保存和汇编本学位论文。
本学位论文属于1、保密口,在一年解密后适用本授权书。
2、不保密团。
(请在以上相应方框内打“√”)日期:Zof乡年6月6日作者签名:日期:加侈年6月6日导师签名:球墨铸铁QT600·3表面激光多道淬火工艺的研究摘要球墨铸铁材料因其较高的强度、良好的塑性和韧性,以及便于生产,成本比钢低廉等优良的性能而被广泛应用在工业生产中的各个领域。
- 1、下载文档前请自行甄别文档内容的完整性,平台不提供额外的编辑、内容补充、找答案等附加服务。
- 2、"仅部分预览"的文档,不可在线预览部分如存在完整性等问题,可反馈申请退款(可完整预览的文档不适用该条件!)。
- 3、如文档侵犯您的权益,请联系客服反馈,我们会尽快为您处理(人工客服工作时间:9:00-18:30)。
球墨铸铁的工艺原理
球墨铸铁(Ductile Iron)是一种重要的铸铁材料,具有高强度、良好的韧性和耐用性。
其工艺原理主要包括球化处理和铸造工艺两个方面。
1. 球化处理:球墨铸铁的主要特点就是球状石墨(球墨)的存在,球墨可以增加材料的韧性和塑性,使其具有较高的拉伸强度和冲击韧性。
球状石墨的形成是通过在铸造过程中添加球化剂(一般为钆或镧等稀土元素)来达到的。
球化剂的作用是在铸造过程中形成碳化物核,在高温下将镁中的氧原子还原为氧化镁(MgO),释放出活泼的镁原子,与碳原子结合形成石墨球。
球化剂的添加量和方式会影响球墨铸铁的球状石墨形态和数量,因此需要精确控制球化剂的添加。
2. 铸造工艺:球墨铸铁的铸造工艺与普通铸铁类似,但需要更高的浇注温度和降温速率。
在铸造过程中,为了防止铁水中的氧气和其他杂质对球化剂的妨碍,通常会采用滑进式浇注法,即先浇注一部分铁水,再通过浇注剂将剩余的铁水顺滑地倒入模型中。
这样可以保持较高的浇注温度和较快的浇注速度,有利于球化剂发挥作用。
总体而言,球墨铸铁的工艺原理是通过控制球化剂的添加量和方式,以及优化铸造工艺参数,实现球状石墨的形成和分布,从而提高球墨铸铁的力学性能和耐用性。