加氢装置常见腐蚀
柴油加氢装置铵盐腐蚀机理及工艺防腐对策

柴油加氢装置铵盐腐蚀机理及工艺防腐对策摘要:主要阐述了柴油加氢反应生成的 NH 3、H 2S 和HCl 在反应流出物换热冷却后、相互反应生成NH 4HS 和 NH 4Cl 固体在适当的温度下会结晶析出、在换热器或空冷器等部位结垢造成腐蚀的结盐腐蚀机理,以及结盐腐蚀原因、氯化铵及氯的腐蚀危害,提出了通过限制原料油和重整氢气中的氯含量、采用工艺注水和注剂等手段,可以有效抑制铵盐结晶沉积和腐蚀。
关键词:腐蚀机理 铵盐 氯 工艺防腐近年来,炼油厂柴油加氢装置由于原料和新氢中氯含量偏高,设备结盐积垢、腐蚀造成的非计划停工有增多的趋势,柴油加氢装置能否安全运行,直接影响着全厂的物料平衡和产品质量,因此了解铵盐腐蚀机理及情况,在装置运行中如何减缓腐蚀发生、减少腐蚀事故的发生具有重要意义。
1 结盐腐蚀机理 1.1 主要加氢反应加氢装置主要发生的加氢反应有 4 个,分别为: 加氢脱氯反应:有机氯 + H 2→烃 + HCl 加氢脱氮反应:吡啶 + 5H 2→C 5H 12+ NH 3 加氢脱硫反应:硫醇 + H 2→RH + H 2S 加氢脱氧反应:酚类 + H 2→芳烃 + H 2S从以上反应可以看出在整个工艺系统中存在有 NH3、HCl 、H2S 、H2O 蒸汽等气相物质。
1.2 腐蚀机理加氢反应生成的 NH3,H2S 和 HCl 在反应流出物换热冷却后,由于 NH3、H2S 和 HCl 的分压较高,化学反应生成的NH4HS 和 NH4Cl固体在适当的温度下会结晶析出,在换热器或空冷器及下游流速低的部位结垢浓缩沉积造成垢下腐蚀,形成蚀坑,最终导致穿孔。
由于垢下腐蚀发生导致强烈的金属溶解,产生大量的金属阳离子Fe2+,使溶液中的正电荷过剩,吸引外部的 HS-和Cl-,借电泳作用移动到发生腐蚀的部位,造成了HS-和 Cl-的富集,使该部位溶液的pH值下降。
同时金属表面的 FeS 保护膜由于NH4HS和HCl的存在被破坏,使腐蚀进一步加剧,生成更多的阳离子,吸引更多的阴离子进来。
微晶蜡加氢装置H2S腐蚀问题分析及防治
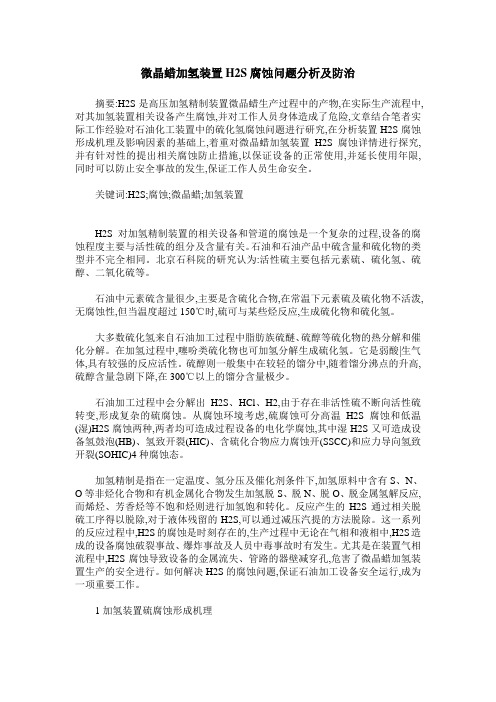
微晶蜡加氢装置H2S腐蚀问题分析及防治摘要:H2S是高压加氢精制装置微晶蜡生产过程中的产物,在实际生产流程中,对其加氢装置相关设备产生腐蚀,并对工作人员身体造成了危险,文章结合笔者实际工作经验对石油化工装置中的硫化氢腐蚀问题进行研究,在分析装置H2S腐蚀形成机理及影响因素的基础上,着重对微晶蜡加氢装置H2S腐蚀详情进行探究,并有针对性的提出相关腐蚀防止措施,以保证设备的正常使用,并延长使用年限,同时可以防止安全事故的发生,保证工作人员生命安全。
关键词:H2S;腐蚀;微晶蜡;加氢装置H2S对加氢精制装置的相关设备和管道的腐蚀是一个复杂的过程,设备的腐蚀程度主要与活性硫的组分及含量有关。
石油和石油产品中硫含量和硫化物的类型并不完全相同。
北京石科院的研究认为:活性硫主要包括元素硫、硫化氢、硫醇、二氧化硫等。
石油中元素硫含量很少,主要是含硫化合物,在常温下元素硫及硫化物不活泼,无腐蚀性,但当温度超过150℃时,硫可与某些烃反应,生成硫化物和硫化氢。
大多数硫化氢来自石油加工过程中脂肪族硫醚、硫醇等硫化物的热分解和催化分解。
在加氢过程中,噻吩类硫化物也可加氢分解生成硫化氢。
它是弱酸|生气体,具有较强的反应活性。
硫醇则一般集中在较轻的馏分中,随着馏分沸点的升高,硫醇含量急剧下降,在300℃以上的馏分含量极少。
石油加工过程中会分解出H2S、HCl、H2,由于存在非活性硫不断向活性硫转变,形成复杂的硫腐蚀。
从腐蚀环境考虑,硫腐蚀可分高温H2S腐蚀和低温(湿)H2S腐蚀两种,两者均可造成过程设备的电化学腐蚀,其中湿H2S又可造成设备氢鼓泡(HB)、氢致开裂(HIC)、含硫化合物应力腐蚀开(SSCC)和应力导向氢致开裂(SOHIC)4种腐蚀态。
加氢精制是指在一定温度、氢分压及催化剂条件下,加氢原料中含有S、N、O等非烃化合物和有机金属化合物发生加氢脱S、脱N、脱O、脱金属氢解反应,而烯烃、芳香烃等不饱和烃则进行加氢饱和转化。
加氢装置设备铵盐重点腐蚀部位的分析
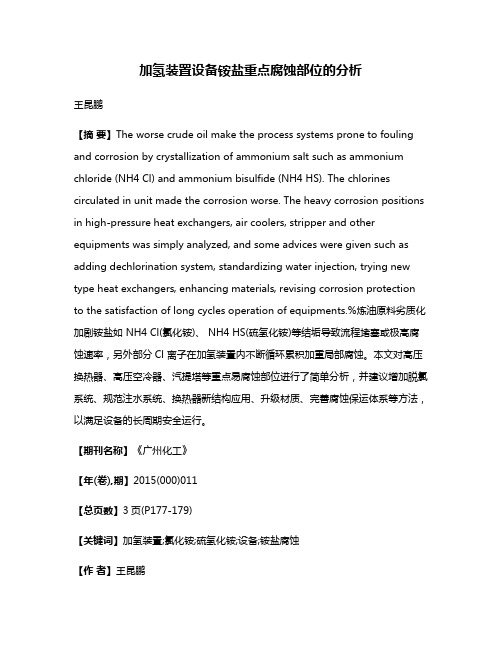
加氢装置设备铵盐重点腐蚀部位的分析王昆鹏【摘要】The worse crude oil make the process systems prone to fouling and corrosion by crystallization of ammonium salt such as ammonium chloride (NH4 Cl) and ammonium bisulfide (NH4 HS). The chlorines circulated in unit made the corrosion worse. The heavy corrosion positions in high-pressure heat exchangers, air coolers, stripper and other equipments was simply analyzed, and some advices were given such as adding dechlorination system, standardizing water injection, trying new type heat exchangers, enhancing materials, revising corrosion protection to the satisfaction of long cycles operation of equipments.%炼油原料劣质化加剧铵盐如 NH4 Cl(氯化铵)、 NH4 HS(硫氢化铵)等结垢导致流程堵塞或极高腐蚀速率,另外部分Cl 离子在加氢装置内不断循环累积加重局部腐蚀。
本文对高压换热器、高压空冷器、汽提塔等重点易腐蚀部位进行了简单分析,并建议增加脱氯系统、规范注水系统、换热器新结构应用、升级材质、完善腐蚀保运体系等方法,以满足设备的长周期安全运行。
【期刊名称】《广州化工》【年(卷),期】2015(000)011【总页数】3页(P177-179)【关键词】加氢装置;氯化铵;硫氢化铵;设备;铵盐腐蚀【作者】王昆鹏【作者单位】SEG 中石化洛阳工程有限公司,河南洛阳 471003【正文语种】中文1 加氢装置与铵腐蚀简介国内燃油即将全面达到国Ⅴ标准,加氢装置在炼厂的作用更为重要。
加氢设备腐蚀

一、概述加氢设备由于操作条件的特殊性,常引起一些特殊的损伤现象。
这些特殊的损伤在高温区域以反应器为代表,在低温高压部位以高压空冷器为代表。
据国内外的资料报道,由于强度造成高压设备的破坏例子是极少的,可是由于腐蚀和材料选用不当所引起的损伤例子是较多的。
所以,对于使用在高温高压氢介质中的热壁加氢反应器等设备来说,腐蚀和材料冶金学问题显得更为突出。
因此要求用于制造这类设备的材料要具有令人满意的综合性能。
具体来说至少应满足:(1)材料的致密性、纯洁性和均质性优越,这对于厚(或大断面)钢材尤为重要;(2)严格的化学成分、(3)优越的室温和高温力学性能;(4)能够在苛刻环境下长期使用的抗环境脆化性能。
二、常见的损伤形式与对策(一)高温氢腐蚀1.高温氢腐蚀的特征高温氢腐蚀是在高温高压条件下扩散侵入钢中的氢与不稳定的碳化物发生化学反应,生成甲烷气泡(它包含甲烷的成核过程和成长),即Fe C+2H2一CH4+3Fe,并在晶间空穴和非金属夹杂部位聚集,引起钢的强度、延性和韧性下降与劣化,同时发生晶间断裂。
由于这种脆化现象是发生化学反应的结果,所以它具有不可逆的性质,也称永久脆化现象。
高温氢腐蚀有两种形式:一是表面脱碳;二是内部脱碳。
表面脱碳不产生裂纹,在这点上与钢材暴露在空气、氧气或二氧化碳等一些气体中所产生的脱碳相似,表面脱碳的影响—般很轻,其钢材的强度和硬度局部有所下降而延性提高。
内部脱碳是由于氢扩散侵入到钢中发生反应生成了甲烷,而甲烷又不能扩散出钢外,就聚集于晶界空穴和夹杂物附近,形成了很高的局部应力,使钢产生龟裂、裂纹或鼓包,其力学性能发生显著的劣化。
高温高压氢引起钢的损伤要经过一段时间。
在此段时间内,材料的力学性能没有明显的变化;经过此段时间后,钢材强度、延性和韧性都遭到严重的损伤。
在发生高温氢腐蚀之前的此段时间称为“孕育期”(或称潜伏期)。
“孕育期”的概念对于工程上的应用是非常重要的,它可被用来确定设备所采用钢材的大致安全使用时间。
加氢装置湿硫化氢腐蚀问题浅析

2 0 1 3年 4月
广
州
化
工
V0 l _ 41 No . 7 Apr i l . 2 01 3
Gu a n g z h o u Ch e mi c a l I n d u s t r y
加 氢 装 置 湿 硫 化 氢 腐 蚀 问题 浅 析
潘 晓 斐
t h e l o w t e mp e r a t u r e we t h y d r o g e n s u l i f d e c o r r o s i o n o f h y d r o t r e a t i n g u n i t i n p e t r o c h e mi c a l i n s t a l l a t i o n s .S o me we t hy d r o g e n
s u l id f e c o ro s i o n s i t u a t i o ns i n h y d r o t r e a t i n g u n i t we r e s u mma r i z e d . At t h e s a me t i me,s o me p r o t e c t i o n c o u n t e r me a s u r e s o f h y d r o t r e a t i ng u n i t i n we t h y d r o g e n s u l id f e c o r r o s i o n we r e i n t r o d u c e d f r o m ma t e r i a l s e l e c t i o n,we l d i n g a n d h e a t t r e a t me n t ,
加氢裂化装置腐蚀与防腐

部 位 腐 蚀 较 重 ,气 液 两 相 转变 部位
( 点部 位 )最 为 严重 。工 艺介 质 中 露
的 HC 、H, 于干 态 时 ,对 金属 没 1 S处 有 腐 蚀性 。 随着 分 馏 塔 顶 冷 却 系统
腐 蚀 的速 率 增 加 。 当 工 艺介 质 的流 速增 大 时 ,高温硫 腐 蚀的 速率增 加 。
需 要 拆 检 的 奥 氏体 不 锈 钢 设 备
压空冷 管束及其 出入 口弯 头区域 。工
艺介质 中的 N、C 、S元 素经过加氢 L
均在 第一 时 间碱 洗 ( aC N NO N ,O+ a 溶 液)阻止连多 硫酸生成 。停 工的过 , 程 中反 应进 料 加 热 炉 炉 管 外壁 喷 碱 液 ,内壁 氮气保持微 正压 。反应器 内 构 件 拆 装 和催 化 剂 装 卸 不 能在 雨 天 进行 , 防止含有氯 离子 的雨水 落入 反 应器 ( P 0L T 3 7 T 3 9 + P 4 堆焊 ) 。空气
等 功 能 。 管道 测厚 数据 导 入 EM 后
将 生 成 以 时 间为 横 坐 标 ,以壁 厚 为
纵 坐 标 的趋 势 图 ,管道ቤተ መጻሕፍቲ ባይዱ腐 蚀 趋 势 一
目了然 。
度、 流速 和设 备材 质 。当介质 温度升
高 时 , S S 蚀 的速率将 增大 , H,+ 腐 而 且高 温将 分解 出更多 的活性 硫 化物 , 提 高 了 活性 硫 化 物 的 浓度 ,导 致 高 温硫 腐 蚀 的速 率 进 一 步 加快 。 当工
冷却 器部 分管 束 内窥镜 检查 。
加氢工艺中设备的腐蚀与防护分析

加氢工艺中设备的腐蚀与防护分析摘要:摘要:随着加氢工艺设备在工业生产中的应用规模不断扩大,其腐蚀防护的途径也逐渐成为业内广泛讨论的问题。
立足于现状,首先结合具体的加氢工艺设备的现状与工艺流程,介绍了加氢工艺设备腐蚀防护的主要内容,其次对加氢工艺装置工艺设备腐蚀成因进行了探讨,最后结合上述内容对加氢工艺设备腐蚀防护的策略进行了解析,希望可以有效提升加氢工艺设备的运行稳定性,取得良好的经济效益与社会效益。
关键词:加氢工艺;设备;腐蚀;防护前言:加氢工艺设备在化工企业等行业中具有广泛的应用,其主要用于处理各种含硫量较高的污水,同时还需要对酸性气体进行预处理。
在实际工作过程中,一般需要借助于高温催化的方式来将大量的硫化氢转化,在回收作业过程中也会形成各种不同类型的酸性气体,导致设备出现腐蚀、损坏的问题。
为了进一步探讨加氢工艺设备的腐蚀防护策略,现就加氢工艺设备的工艺现状介绍如下。
1、加氢工艺中设备腐蚀的原因(1)介质原因加氢工艺的介质通常是酸性或碱性催化剂、有机物、气体等,而这些介质可能会对设备产生腐蚀作用。
例如,有机酸或醇等有机物在加氢反应中,会产生酸性物质较多,可能会造成设备腐蚀。
(2)温度原因加氢反应必须在高温高压下进行,而高温会使目标物质与催化剂等材料形成强烈化学反应,造成材料性质发生变化,进而导致材料腐蚀。
(3)压力原因加氢反应在高压环境下进行,压力越高,设备受到的应力越大,容易产生裂纹或失效。
(4)露点腐蚀。
在加氢工艺设备运行过程中,氢气过程气作为重要的介质,其主要的成分包括水蒸气、二氧化硫与二氧化氮,这些成分聚集于尾气低温部分,一旦出现温度低于露点的情况,就很容易出现二氧化硫与水蒸气混合凝结,具有很强的酸性。
比如说急冷水冷却器出现内漏就容易出现亚硫酸腐蚀问题,所以露点腐蚀主要是防护不到位所导致的结果。
2、加氢工艺设备腐蚀防护策略2.1温度调整控制温度调整控制时解决加氢工艺设备腐蚀问题的主要途径。
柴油加氢装置设备系统腐蚀现象分析及防护措施

柴油加氢装置设备系统腐蚀现象分析及防护措施发布时间:2022-07-15T08:27:14.500Z 来源:《科学与技术》2022年第5期3月作者:赵振国韩敏[导读] 腐蚀也是严重危害化学品安全的重要隐患赵振国韩敏中国石化胜利油田分公司石油化工总厂山东东营 257000摘要:腐蚀也是严重危害化学品安全的重要隐患。
它可以减少装置和管道的厚度、裂纹甚至穿孔。
由于氢起始装置是炼油企业的二次工艺处理设备,目前处于高温高压加氢状态。
由于中间存在H2S、NH3、HCl、HCN等组分,腐蚀问题非常复杂。
该设备分析了重要的腐蚀机理和腐蚀失效模式,以解决重要的腐蚀问题。
建议在下一周期从选材、定点厚度、加工工艺等方面采取防腐措施。
因此,建议建立一个腐蚀数据库系统,建立一个高速有效的数据共享平台,将腐蚀监测数据纳入现有的腐蚀数据系统中,对电厂的腐蚀情况进行数据分析和动态评估。
加强腐蚀综合管理和监测,提高装置技术水平,确保装置安全运行。
关键词:柴油;氢化;腐蚀分析;防腐措施加氢精制是利用氢高压催化剂使原油中的烯烃饱和,从而消除硫、氧、硫、有害元素和金属物质的化学过程。
目前,氢起始装置主要系统的腐蚀检测主要集中在加热炉管道、反应排气装置和循环氢脱硫装置[1]。
本文探讨了主要设备及其管道腐蚀的原因和分类,并提供了具体的防锈对策。
1腐蚀原因分析1.1硫化氢腐蚀与高温氢损伤在硫磺精制生产设备中,腐蚀和高氢硫基氢损失主要出现在炉管和反应器、通过生活反应废水处理系统的管道和高温换热器中。
设备表面硫化氢基团的腐蚀主要是由于高温活性硫的腐蚀,以及与H2S和金属直接反应生成FES。
当混合硫原料油在加热炉中逐渐加热到350℃以上时,氢硫基团分解形成游离硫。
由于游离硫比硫化氢强,对炉管和管道的腐蚀更强烈,设备表面会形成铁硫,导致设备表面变薄。
高温氢的损伤可分为表面脱碳和内部脱碳。
表面脱碳是指钢铁设备和管道的表面材料在高温下暴露在氢气中,碳浓度迅速降低,钢的强度和硬度也随之降低。
- 1、下载文档前请自行甄别文档内容的完整性,平台不提供额外的编辑、内容补充、找答案等附加服务。
- 2、"仅部分预览"的文档,不可在线预览部分如存在完整性等问题,可反馈申请退款(可完整预览的文档不适用该条件!)。
- 3、如文档侵犯您的权益,请联系客服反馈,我们会尽快为您处理(人工客服工作时间:9:00-18:30)。
1 加氢装置常见的腐蚀 1. 氢腐蚀 氢腐蚀是在高温高压条件下,分子氢发生部分分解而变成原子氢或离子氢,并通过金属晶格和晶界向钢中扩散,扩散侵入钢中的氢与不稳定的碳化物发生化学反应,生成甲烷气泡(它包含甲烷的成核过程和成长),即Fe3C+2H2→CH4+Fe,并在晶间空穴和非金属夹杂部位聚集,而甲烷在钢中的扩散能力很小,聚积在晶界原有的微观孔隙(或亚微观孔隙)内,形成局部高压,造成应力集中,使晶界变宽,并发展成为裂纹,开始时是很微小的,但到后期,无数裂纹相连,引起钢的强度、延性和韧性下降与同时发生晶间断裂。由于这种脆化现象是发生化学反应的结果,所以他具有不可逆的性质,也称永久脆化现象。 在高温高压氢气中操作的设备所发生的氢腐蚀有两种形式:一是表面脱碳,二是内部脱碳。 表面脱碳不产生裂纹,这点与钢材暴露在空气、氧气或二氧化碳等一些气体所产生的脱碳相似,表面脱碳的影响一般很清,其钢材的强度和硬度局部有所下降而延性有所提高。 内部脱碳是由于氢扩散侵入到钢中发生反应生成甲烷,而甲烷又不能扩散到钢外,就聚集于晶界或夹杂物附近。形成了很高的局部应力,使钢产生龟裂、裂纹或鼓包,其力学性能发生了显化。 造成氢腐蚀的因素: ① 操作温度、氢的分压和接触时间。温度越高或者压力越大发生 2
高温氢腐蚀的起始时间越早。氢分压8.0MPa是个分界线,低于此值影响比较缓和,高于此值影响比较明显,操作温度200℃是个临界点,高于此温度钢材氢腐蚀程度随介质的温度升高而逐渐加重。氢在钢中的话浓度可以用下面公式表示: C=134.9P1/2exp(-3280/T) 式中: C-氢浓度 P——氢分压,MPa T-温度,K 从式中可看出,温度对钢中氢浓度的影响比系统氢分压更显著。 ② 钢材中合金元素的添加情况。在钢中不能形成稳定碳化物的元素(如镍、铜)对改善钢的抗氢腐蚀的性能毫无作用;而在钢中添加形成很稳定碳化物的元素(入铬、钼、钒、钛、钨等),就可以使碳的活性降低,从而提高钢材抗氢腐蚀的能力。关于杂质的影响,在针对2.25Cr-1Mo刚的研究已发现,锡、锑会增加甲烷气泡的密度、大小和生成速率。 ③ 加工过程。钢的抗氢腐蚀性能与钢的显微组织也有密切关系。回火过程对钢的氢腐蚀性能也有影响。对于淬火状态,只需很短时间加热就出现了氢腐蚀。但是一施行回火,且回火温度越高,由于可形成稳定的碳化物,抗氢腐蚀性能就得到改善,另外对于在氢环境下使用的铬钼钢设备,施行焊后热处理同样具有提高抗氢腐蚀能力的效果。曾有试试验证明,2.25Cr-1Mo钢焊缝若不进行热处理的话,则 3
发生氢腐蚀的温度将比纳尔逊(Nelson)曲线表示的温度低100℃以上。 ④ 钢材受的热应力。在高温氢气中蠕变强度会下降,特别是由于二次应力(如热应力或由冷加工所引起的应力)的存在会加速高温氢腐蚀。当没有变形时,钢材具有较长的“孕育期”,随着冷变形量增大,“孕育期”逐渐缩短,当变形量达到39%时,则在任何试验条件下都无“孕育期”,只要暴露在此条件的氢气中,裂纹立刻就发生。因此对于临氢压力容器的受压元件,应重视采用热处理消除残余应力; ⑤ 不锈钢复合层和堆焊层的影响,由于氢在奥氏体不锈钢以及铁素体钢中的溶解度和扩散系数不同,因此完整冶金结合的奥氏体不锈钢复合层和堆焊层能降低作用在目材中的氢分压。 如何防止氢腐蚀: ① 采用内保温、降低筒壁温度; ② 采用耐氢腐蚀的钢板做反应器筒体; ③ 采用抗氢腐蚀的衬里(如0Cr13、1Cr18Ni9Ti等) ④ 采用多层式结构,可在壁上开排气孔及特殊的集气层,将内筒渗过来的氢气集中起来排走。 ⑤ 采用催化剂内衬筒式反应器,新氢走环形空间,使筒壁降温。 ⑥ 在实际应用中,对于一台设备来说,焊缝部位的氢腐蚀更不可忽视。因为通常焊接接头的抗氢腐蚀性能不如目材,特别是热影响区的粗晶区附近更显薄弱应引起重视。 4
2. 氢腐蚀潜伏期 在高温高压氢的作用下,钢材的破坏往往不是突出发生的,而是经历一个过程,在这个过程中,钢材的机械性能并无明显变化,这一过程就称为潜伏期或孕育期。潜伏期的长短与钢材的类型和暴露条件有关.条件苛刻,潜伏期就短,甚至几小时就破坏.在高温压力比较低的条件下,潜伏期可能就长一些.知道钢材的氢腐蚀潜伏期后,对掌握设备的安全运转时间有很重要的意义。 3. 氢致裂纹 氢致裂纹也称诱导裂纹。这是由于反应器在高温高压的氢气中操作时氢气扩散侵入钢中,当反应器在停工冷却过程中,由于冷却速度太快,氢来不及从钢中向外释放,钢内就会吸藏了一定的氢,严重的拉伸延性损失就会导致裂纹引发。 在操作中,当装置停工时,宜采用能使氢较彻底释放出的停工方案。例如停工时降温速度不能过大,并在较高的温度下(大于350℃)保持一段较长的时间。 4. 氢脆 所谓氢脆,就是由于氢残留在钢中所引起的脆化现象。产生了氢脆的钢材,其延伸率和断面收缩率显著下降。这是由于侵入钢中的原子氢,使结晶的原子结合力变弱,或者作为分子状态在晶体或杂物周边上析出的结果。但是,在一定的条件下,若能使氢较彻底释放出来,钢材的力学性能仍可得恢复。这一特性与氢蚀截然不同,所以氢脆是 5
可逆的,也称作一次性脆化现象。对于操作在高温高压环境下的时设备,在操作状态下,器壁会吸收一定量的氢。在停工过程中,冷却速度太快,使在温度低于150℃引起亚临界裂纹扩展,对设备的安全使用带来威胁。 防止氢脆的对策: ① 尽量减少应变幅度,这对于改善使用寿命很有帮助。采取降低热应力和避免应力集中等措施都是有效的。 ② 尽量保持堆焊金属有较高的延性。 ③ 装置在停工时降温速度不宜过快,且停工过程中应有使钢材中吸收的氢尽量释放出来的过程(分阶段恒温脱氢,一般在260~427℃之间),以减少器壁中的残留氢含量。另外,尽量避免非计划停工(紧急放空)也是非常重要的。因为此情况下器壁中的残留氢浓度会很高。 5. 应力腐蚀 所谓应力就是作用在单位面积上的内力值,垂直于横截面上的应力称为正应力,平行于横截面的应力称为剪应力。金属材料在静拉应力和腐蚀介质同时作用下,所引起的破坏作用,称为应力腐蚀。 产生腐蚀应力的原因,首先是由于内应力使钢材增加了内能,处于应力状态下的钢材的钢材稳定性必然会下降,从而降低了电极电位,内应力愈大,化学稳定性愈差,电极电位愈低。所以,应力大的区域成为阳极,其次应力(特别是表示拉应力)破坏了金属表面的保护膜,保护膜破坏后形成裂缝,裂缝就成为阳极,其他无应力区域成 6
为阴极,成为腐蚀电池,加速腐蚀。奥氏体不锈钢对应力腐蚀是比较敏感的,较易发生,这可能是和他比较容易产生滑移即孪晶有关。由于滑移带和孪晶界应力集中,易遭受腐蚀破坏,裂纹一般都是穿晶的,也有在晶间发生的,由于这种应力腐蚀所产生的裂纹呈刀口状,所以成为“刀口腐蚀”。奥氏体不锈钢形成刀口腐蚀的原因,除了焊缝有不均匀的的应力外,还由于焊缝在焊接后的冷却过程中,从奥氏体中析出了铬的碳化物,使晶界贫铬,刀口腐蚀就发生在焊缝区或热影响区里,而热影响区内的某一段的温度很可能就是奥氏体的贫铬的碳化物出的敏化温度(450~850℃),这样就使得晶界贫铬,发生晶界裂纹。 防止应力腐蚀的方法: ① 利用热处理消除焊接和冷加工的残余应力,以及进行稳定化和固溶处理; ② 采用超低碳(小于0.03%)不锈钢或用含铌、钛稳定的不锈钢,焊接时用超低碳或含铌的焊条进行焊接。 6. 奥氏体不锈钢的连多硫酸腐蚀机理
连多硫酸应力腐蚀开裂的特征应力腐蚀开裂是某一金属(钢材)在拉应力和特定的腐蚀介质共同作用下所发生的脆性开裂现象。奥氏体不锈钢对于硫化物应力腐蚀开裂是比较敏感的。连多硫酸(H2SxO6,x=3~6)引起的应力腐蚀开裂也属于硫化物应力腐蚀开裂,一般为晶间裂纹。当炼油装置停工过程中,系统降温降压后,有水气被冷凝下来或打开设备检修时,设备和管线内部与湿空气接触。铁/铬硫化物 7
于氺和氧发生化学反应,就有亚硫酸和连多硫酸生产,从而产生腐蚀。在石化工业装置中,奥氏体不锈钢或管道发生硫化物应力腐蚀开裂多有见到。连多硫酸应力腐蚀开裂在加氢装置中也都发生过。
防止奥氏体不锈钢产生连多硫酸腐蚀最好采取以下几点措施: ① 材质一般采用超低碳型(C≦0.03%)或稳定性的不锈钢(SUS321,SUS347),采用奥氏体+铁素体双相不锈钢也有较好的效果,它对连多硫酸应力发生开裂不敏感。制造上要尽量消除或减轻由于冷加工或焊接引起的残余应力,并注意加工成不形成应力集中或尽可能小的结构。
② 使奥氏体不锈钢设备或管线的金属表面保持干燥,即不与空气和水基础或处于热状态下。即装置停工后,对不需检修的奥氏体不锈钢设备或管线用阀门或盲板封闭起来,内充氮气保持正压,使其隔绝空气。如果温度低于38℃会生产液态水时,则要将无水氨注入系统内,浓度大约5000PPm,特别是加热炉管,在停工检修时,保持其温度在149℃以上,使其干燥。
③ 对于需要检修的奥氏体不锈钢设备,管线和不能保持149℃以上的加热炉管,应用1.5~2%的碳酸钠或氢氧化钠溶液进行中和冲洗。冲洗后,务必用不含氯化物的除盐水冲洗,以防止残留碱留在表面上造成碱脆和在开工时被带到催化剂上,影响活性。在溶液中增加0.5%的硝酸钠,可以减少不锈钢发生氯化物应力腐蚀开裂的可能性,但必须防止溶液中加入过量的硝酸钠(不大于0.5%),它有引起碳