管式裂解炉结构-江西化学工业学校
乙烯裂解炉.
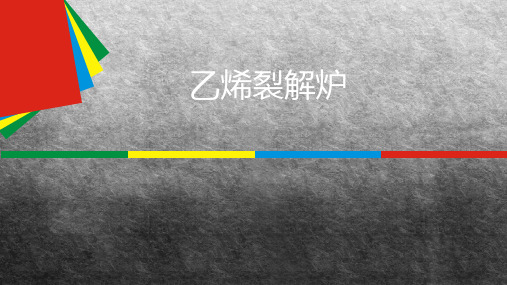
一次反应:原料烃在裂解 过程中首先发生的原料烃 的裂解反应。 ●生成目的产物乙烯、丙 烯(促使其充分进行) 二次反应:一次反应产物 继续发生的后继反应。 ●乙烯、丙烯消失,生成 分子量较大的液体产物以 至结焦生炭(抑制其进行)
(2) 反应机理
烃类裂解的反应机理:自由基机理 1)链引发(活化能高):断裂C—C键,产生一对自由基 2)链增长(活化能不大):自由基夺氢反应,自由基分解反应 3)链终止(活化能一般较低):两个自由基形成稳定分子的过程 自由基夺氢反应:H• + RH → H2 + R• R’• + RH → R’H + R•
种类:
1.乙烯裂解反应器供热方式
直接式供热:蓄热炉裂解、沙子炉裂解、流化床裂解
间接式供热:管式炉裂解 2.其中管式裂解炉分类: 从技术上:(1)双辐射室(2)单辐射室(3)毫秒炉 从炉型上:CBL裂解炉、SRT裂解炉、USC裂解炉、 KTIGK裂解炉、USRT裂解炉、pyrocrack裂解炉、 LSCC裂解炉
对流段顶 部设置烟 道和引风 机
对流段内 设置进料、 稀释蒸汽 和锅炉给 水的预热
烧嘴是工业燃料炉上用的 燃烧装置的俗称。 通常指的是燃烧装置本体 部分,有燃料入口、空气 入口和喷出孔,起到分配 燃料和助燃空气并以一定 方式喷出后燃烧的作用
4.SRT裂解炉优化改进种类
1)炉型:烧嘴 侧壁无焰烧嘴 → 侧壁烧嘴与底部烧嘴联合 2)盘管结构: 炉管的排列、结构、管径、材质 多程 → 双程:减少结焦部位,延长操作周期 光管 → 带内翅片:降低管内热阻,延长清焦周期 等径 → 分支:增大比表面积,传热强度量增加 变径:缓解管内压力的增加 HK-40 → HP-40:提高热强度
2.实施第二次改造的必要性
化工反应设备

• 气液混合物在离桨翼不远处含气量最高, 传质速率也最快,反应器内的传质主要靠 这局部区域。当液层高度与槽直径之比大 于1.2以上时,反应器一般需要两层或多层 桨翼,有时桨翼间还要安置多孔挡板。
• 气体在搅拌槽中的通过能力受液泛限制, 超过液泛的气体不能在液体中分散,它们 只能沿槽壁纵向上升。液体流量由化学反 应时间决定,搅拌槽中的气泡由于浮力关 系,其运动和液体并不完全相同。
• 流化床的下部为浓相段,化学反应主要在 此段进行。在浓相段中装有冷却水管和导 向挡板。冷却水管是为了控制反应温度, 回收反应热。导向挡板是为了改善气固接 触条件。
• 上部为稀相段。在稀相段也装有冷却水管, 目的是将反应温度降至规定的温度以下, 以便中止反应。稀相段之上为扩大段。扩 大段内装有内旋风分离器,以分离并回收 被反应气夹带的催化剂细粒。
• 在反应器内,以原料气为换热介质,通过 管壁与反应物料换热,以维持反应温度的 反应器称之为自身换热式。一般都用于热 效应不太大的高压反应。既能做到热量自 给,又不需另设高压换热设备。
• 主要用于合成氨和甲醇的生产。
• 固定床反应器发展了径向反应器。工业上 甲苯歧化制苯和二甲苯就采用径向反应器。 径向反应器中的流体流动如图10一6所示。
• 流化床反应器比较适用于下述过程: • ①热效应很大的放热或吸收过程; • ②要求有均一的催化剂温度和需要精确控制温度
的反应; • ③催化剂寿命比较短,操作较短时间就需要更换
(或活化)的反应; • ④有爆炸危险的反应,某些能够比较安全地在高
浓度下操作的氧化反应,可以提高生产能力,减 少分离和精制的负担。
一段反应 器
绝热型
单层固定 气固液非
床
均相
连续式
工艺流程—裂解炉生产乙烯

利用裂解炉生产乙烯热裂解特点:高温,吸热量大低烃分压,短停留时间,避免二次反应的发生反应产物是复杂的混合物热裂解的供热方式如下所示:直接供热法:工艺复杂,裂解气质量低,成本过高。
其裂解工艺一直没有很大发展!工业上烃类裂解生产乙烯的主要过程为:原料→热裂解→裂解气预处理(包括热量回收、净化、气体压缩等)→裂解气分离→产品乙烯、丙烯及联产物等。
一、原料烃组成对裂解结果的影响影响裂解结果的因素:原料特性;裂解工艺条件;裂解反应器型式;裂解方法等。
原料特性是最重要的影响因素!(一) 原料烃的族组成、含氢量、芳烃指数、特性因数裂解产物分布的影响1. 族组成(简称PONA值)定义:是指原料烃分子中所含各族烃的质量百分比P—烷族烃 N—环烷族烃O—烯族烃A—芳香族烃从表1-7作一比较,在管式裂解炉的裂解条件下,原料愈轻,乙烯收率愈高。
随着烃分子量增大,N+A含量增加,乙烯收率下降,液态裂解产物收率逐渐增加。
*包括乙烷循环裂解原料的PONA值常常被用来判断其是否适宜作裂解原料的重要依据。
表1-8介绍我国几个产地的轻柴油馏分族组成。
表1-8 我国常压轻柴油馏分族组成我国轻柴油作裂解原料是较理想的。
2. 原料氢组成定义:是指原料烃分子中氢原子的质量百分比,不包含溶解的H2烃类裂解过程也是氢在裂解产物中重新分配的过程。
原料含氢量对裂解产物分布的影响规律,大体上和PONA值的影响一致。
表1-9位各种烃和焦的含氢量比较。
表1-9 各种烃和焦的含氢量可以看出,碳原子数相同时,含氢量:烷烃>环烷烃>芳烃。
含氢量高的原料,裂解深度可深一些,产物中乙烯收率也高。
对重质烃类的裂解,按目前的技术水平,原料含氢量控制在大于13%(质量),气态产物的含氢量控制在18%(质量),液态产物含氢量控制在稍高于7~8%(质量)时,就容易结焦,阻塞炉管和急冷换热设备。
图1-3给出了不同含氢量原料裂解时产物收率。
从图中可以看出:含氢量 P>N>A 液体产物收率 P<N<A乙烯收率 P>N>A 容易结焦倾向 P<N<A3. 芳烃指数(BMCI)定义:BMCI=48640/TV+473.7×d15.615.6-456.8TV=(T10+ T30+ T50+ T70+ T90)/5TV—体积平均沸点,KT10、T30…—分别代表恩氏蒸馏馏出体积为10%,30%…时的温度,K基准:n-C6H14的BMCI=0芳烃的BMCI=100因此,BMCI值越小,乙烯收率越高,当BMCI﹤35时,才能做裂解原料。
常用乙烯裂解炉简介

常用乙烯裂解炉简介①鲁姆斯公司的SRT型裂解炉鲁姆斯公司的SRT型裂解炉(短停留时间裂解炉)为单排双辐射立管式裂解炉,已从早期的SRT-I型发展为近期的SRT-Ⅵ型。
SRT型裂解炉的对流段设置在辐射室上部的一侧,对流段顶部设置烟道和引风机。
对流段设置进料、稀释蒸汽和锅炉给水的预热。
从SRT-Ⅵ型炉开始,对流段还设置高压蒸汽过热,由此取消了高压蒸汽过热炉。
在对流段预热原料和稀释蒸汽过程中,一般采用一次注入蒸汽的方式,当裂解重质原料时,也采用二次注汽。
早期SRT型裂解炉多采用侧壁无焰烧嘴烧燃料气,为适应裂解炉烧油的需要,目前多采用侧壁烧嘴和底部烧嘴联合的布置方案。
底部烧嘴最大供热量可占总热负荷的70%。
SRT-Ⅲ型炉的热效率达93.5%。
图1—21为SRT型裂解炉结构示意图。
图1-21鲁姆斯SRT-Ⅱ型裂解炉结构示意图②斯通-伟伯斯特(S.W)公司的USC型裂解炉S.W的USC裂解炉(超选择性裂解炉)为单排双辐射立管式裂解炉,辐射盘管为W型或U型盘管。
由于采用的炉管管径较小,因而单台裂解炉盘管组数较多(16-48组)。
每2组或4组辐射盘管配一台USX型(套管式)一级废热锅炉,多台USX废热锅炉出口裂解气再汇总送入一台二级废热锅炉。
近期开始采用双程套管式废热锅炉(SLE),将两级废热锅炉合并为一级。
USC型裂解炉对流段设置在辐射室上部一侧,对流段顶部设置烟道和引风机。
对流段设有原料和稀释蒸汽预热、锅炉给水预热及高压蒸汽过热等热量回收段。
大多数USC型裂解炉为一个对流段对应一个辐射室,也有两个辐射室共用一个对流段的情况。
当装置燃料全部为气体燃料时,USC型裂解炉多采用侧壁无焰烧嘴;如装置需要使用部分液体燃料时,则采用侧壁烧嘴和底部烧嘴联合布置的方案。
底部烧嘴可烧气也可烧油,其供热量可占总热负荷的60%-70%。
由于USC型裂解炉辐射盘管为小管径短管长炉管,单管处理能力低,每台裂解炉盘管数较多。
为保证对流段进料能均匀地分配到每根辐射盘管,在辐射盘管入口设置了文丘里喷管。
SHJ_36-91_石油化工管式炉设计规范
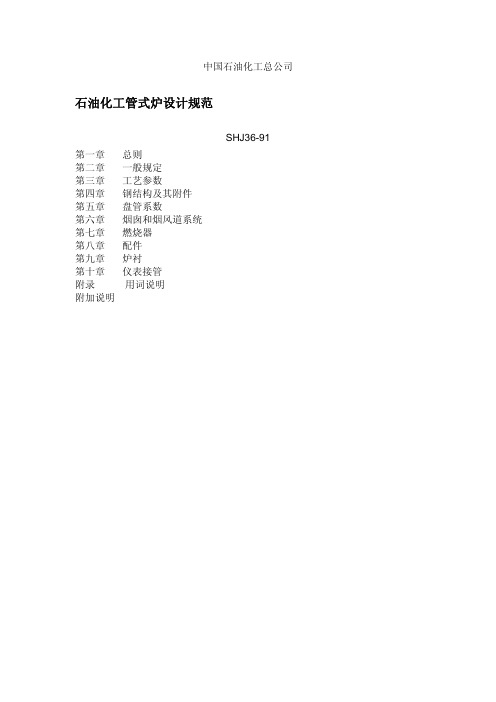
石油化工管式炉设计规范
第一章 总则
第二章 一般规定
第三章 工艺参数
第四章 钢结构及其附件
第五章 盘管系数
第六章 烟囱和烟风道系统
第七章 燃烧器
第八章 配件
第九章 炉衬
第十章 仪表接管
附录
用词说明
附加说明
SHJ36-91
第一章 总则
第1.0.1.条 本规范适用于石油化工新建燃油、燃气管式炉的设计、改建和扩建 的管式炉可参照执行。
六. 采用堵头式回弯头的水平盘管时,回弯头侧的平台应满足安装和检修的要
求。
第4.0.7.条 钢结构及其附件设计的构造要求应符合以下规定:
一. 钢结构在以下部位的钢板最小厚度:
炉壁及弯头箱 4mm
炉顶及炉底
6mm
二. 圆筒炉钢结构:
1. 筒体直径小于 4m 时,可采用无立柱的筒形结构;等于或大于 4m 时,宜采
第4.0.2.条 钢结构的设计荷载应包括永久荷载、活荷载、风荷载、雪荷载、地 震作用和温度作用。
第4.0.3.条 由炉管和弯头产生的所有荷载应由钢结构支承,不应由耐火或保温 材料传递。
第4.0.4.条 钢结构及其附件材料的选用应符合以下规定: 一. 钢结构一般应选用 Q235-A、Q235-A.F 或 16Mn 等钢材制作。当建厂地区
高温度的限制、介质在管内停留时间、注水或注汽、烧焦、检查口等); 四. 燃料的种类、液体燃料的元素组成、气体燃料的气体组成、温度、压力、
密度、粘度及液体燃料雾化剂的种类、温度和压力等;混烧时,液体燃料 和气体燃料的比例; 五. 自动控制水平; 六. 建厂地区的基本风压、地震烈度、场地土类别、雪荷载及最冷月月平均最 低温度等; 七. 环境保护、职业安全卫生及其他要求。 第2.0.2.条 管式炉炉型应根据工艺操作要求、长周期运转、便于检修、投资少
裂化反应

催化裂化反应
• 裂化反应。裂化反应是C-C键断裂反应,反 应速度较快。2)异构化反应。它是在分子 量大小不变的情况下,烃类分子发生结构 和空间位置的变化。3)氢转移反应。即某 一烃分子上的氢脱下来,立即加到另一烯 烃分子上,使这一烯烃得到饱和的反应。4) 芳构化反应。芳构化反应是烷烃、烯烃环 化后进一步氢转移反应,反应过程不断放 出氢原子,最后生成芳烃。
• 1、原料范围加宽,单程乙烯收率高,炉 子热效率不断提高。 • 2、工艺条件:停留时间不断缩短,反应 温度逐渐提高;催化裂解(KTI)。 • 3、技术要求: • ①研究、制造抗高温管材。 • ②研究、制造性能更优的保温耐火材料。 • ③提高自动控制水平。 • 4、生产规模大型化;单套装值大型化; 公用工程岛。
本次主要讲烃类热裂化
• 热裂化原理: • 烃类(乙烷、石脑油、轻柴油等) 乙烯、丙烯。 • 反应类型:脱氢、断链、异构化、叠合, 焦化。 • 一次反应:由烃类裂化生成乙烯和丙烯的 反应。(有利) • 二次反应:乙烯、丙烯继续反应生成炔烃、 二 烯烃、芳烃直至 生成焦或碳的反应。 (不利)
烃类热裂化的一次反应包括:
(二)管式裂解炉
• • • • • • • 1、鲁姆斯SRT-X型炉 2、凯洛格毫秒裂解炉(MSF) 3、斯通-韦勃斯特超选择裂解炉(USC) 4、倒梯台下吹式裂解炉(M-TCF) 5、顺梯台裂解炉(IFP) 6、荷兰KTI裂解炉(GK) 7、德国Linde裂解炉(LSCC)
(三)裂解气的急冷
• 1、目的:①回收高温热能,产生高压蒸 汽 • ②终止二次反应 • 2、方法:①直接急冷(用油或水) • ②间接急冷 • 3、急冷换热器:双套管式 • USX式 • 是裂解装置五大关键设备之一
烷烃热裂化的一次反应;
石油化工工艺

一、填空题1、化工生产过程一般可概括为原料预处理、化学反应和产品分离及精制三大步骤。
2、间歇式制取半水煤气的工作循环一般包括吹风阶段、一次上吹制气阶段、下吹制气阶段、二次上吹阶段、空气吹净阶段五个阶段。
其工艺流程是由煤气发生炉、余热回收装置、煤气的除尘、降温、储存设备所组成。
3、尿素的分子式为Co(NH2)2,纯净的尿素为白色,无味,针/棱柱状晶体。
易溶于水、液氨、醇,稍溶于乙醚及脂,溶解度随温度的升高而增加。
实现工业化合成尿素的方法有氰氨基钙法和氨与二氧化碳合成法两种。
4、工业上烃类热裂解制乙烯的主要生产过程是:原料、热裂解、裂解气预处理、裂解气分离、产品及联产品。
目前生产乙烯较成熟的工艺技术是管式炉裂解工艺,管式裂解炉的结构包括对流段和辐射段组成的炉体,炉体内由耐高温合金钢制成的炉管,燃烧器三个主要部分。
5、从石油中制取芳烃的两种主要加工工艺是石脑油重整工艺和烃类裂解工艺。
6、烃类热裂解制乙烯的生产工艺主要由【裂解】和【分离】两部组成。
裂解气的深冷分离流程主要分为【顺序分离流程】【前脱乙烷分离流程】【前脱丙烷分离流程】三种,典型的分离流程是【前脱丙烷分离流程】7、原料气脱硫的方法很多,按脱硫剂的状态来分,脱硫方法可分为干法和湿法两大类。
干法脱硫分为【吸附法】和【催化转化法】两种。
湿法脱硫按其脱硫机理不同又可分为【物理吸收法】【化学吸收法】【物-化吸收法】和【氧化法】四种。
8、催化加氢反应在邮寄化工生产中的应用一方面是【合成有机化工产品】另一方面是【加氢精制】加氢催化剂的种类很多,若按其形态来区分,常用的加氢精制催化剂主要由【金属催化剂】【骨架催化剂】【金属氧化物催化剂】【金属硫化物催化剂】【金属络合物催化剂】五大类。
9、一氧化碳与水蒸气反应生成【CO2】和【H2】的过程,称为CO变化或水煤气变换;目前工业上采用的变换催化剂有【中变催化剂】【低变催化剂】【钴钼系耐硫催化剂】三大类。
10、生产能力是指【一个设备】【一套装置】或【一个工厂】在单位时间内生产的【产品量】或在单位时间内处理的【原料量】;生产强度是指设备的单位特征【几何量】的生产能力,即设备的【单位体积或面积】的生产能力。
烃类热裂解的过程组织
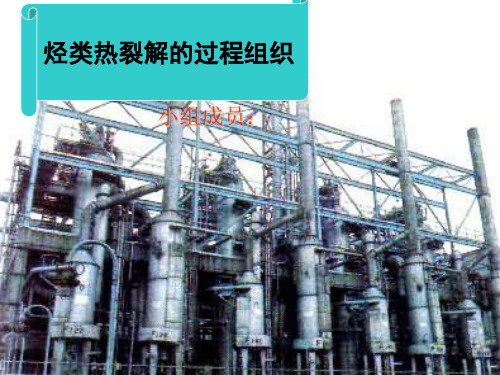
裂解的工艺流程
裂解工艺流程包括原料供给和预热系统、裂解和高压水蒸汽系统、急 冷油和燃料油系统、急冷水和稀释水蒸汽系统。
图1-4轻柴油裂解工艺流程
裂解气的净化与分离 轻柴油裂解气组成
组分
H2 CO CH4 C2H2 C2H4 C2H6 丙二烯+丙炔 C3H6 C3H8 1,3-丁二烯 异丁烯 正丁烷 苯 甲苯 二甲苯+乙苯 苯乙烯 C9~200度馏分 CO2 硫化物 H2O
烃类热裂解的过程组织
小组成员:
裂解原料
气态烃 轻质烃
C 2H 6 C 3H 煤油
重油 重质烃 渣油 闪蒸馏分油 原油 用于裂解,技经指标不理想
环烷烃
环烯烃
中等分子烯烃
叠合烯烃
二烯烃
较大分子的烯烃
乙烯、丙烯
芳烃
稠环烃
焦
中等分子烷烃
甲烷
乙炔
碳
烃类热裂解的操作条件
一般当温度低于750℃时,生成乙烯的可能性较小,者说乙烯收率 较低;在750℃以上生成乙烯可能性增大,温度越高,反应的可能 性越大,乙烯的收率越高。但当反应温度太高,特别是超过900℃ 时,甚至达到1100℃时,对结焦和生碳反应极为有利,同时生成 的乙烯又会经历乙炔间阶段生成碳,这样原料的转化率虽有增加, 产品的收率却大大降低。 下表为温度对乙烷转化率及乙烯收率的关系
裂解的化学反应
3.芳烃的断侧链反应
芳烃的热稳定性很高,一般情况下,芳香不易发生断裂。所 以由苯裂解生成乙烯的可性极小。但烷基芳烃可以断侧链生 成低级烷烃、烯烃和苯。
4.烯烃的断链反应
常减压车间的直馏馏份中一般不含烯烃,但二次加工的馏份 油中可能含有烯烃。大分子烯烃在热裂解温度下能发生断链 反应,生成小分子的烯烃。
- 1、下载文档前请自行甄别文档内容的完整性,平台不提供额外的编辑、内容补充、找答案等附加服务。
- 2、"仅部分预览"的文档,不可在线预览部分如存在完整性等问题,可反馈申请退款(可完整预览的文档不适用该条件!)。
- 3、如文档侵犯您的权益,请联系客服反馈,我们会尽快为您处理(人工客服工作时间:9:00-18:30)。
单元 管式裂解炉的结构与特点
【任务指导】
三、管式裂解炉中炉管的性能及布置方式
1.管式裂解炉中炉管的性能 (1)对炉管的要求 能承受900℃左右的高温、各种介质的腐蚀以及一定的压力和荷载, 具有好的导热性能、高传热强度、内外表面光滑和材料成分均匀等特点。 (2)管子规格 Φ3~7 in(1in=2.54cm)。 (3)管子材质 国外材质型号有HK-40等,国内材质型号ZG40Cr25Ni35Nb、 ZG40Cr35Ni45Nb等。管子用离心浇铸法制成,内部经机械加工平整以减少反应过程的 结焦。 2.管式裂解炉中布管方式 管式裂解炉中,工艺物料(原料气或裂解气)涉及的管路分为对流段和辐射段,对流段 为工艺物料管路在对流室的部分,辐射段为工艺物料管路在辐射室的部分。原料气先经 对流段由烟道气预热,再到辐射段由火焰辐射传热产生高温而裂解,裂解气离开辐射段 后立即进入急冷锅炉。 对流段,工艺物料涉及管路的管子采用水平放置。辐射段,工艺物料涉及管路的管子有 水平放置和垂直放置两种。早年使用的裂解炉为方箱炉,辐射段的炉管采用水平放置, 但由于传热强度低、炉管受热弯曲、耐热吊装件安装不易等原因已被淘汰,而SRT炉, 辐射段的炉管采用方式
单元 管式裂解炉的结构与特点
【任务指导】
三、管式裂解炉优缺点 (1)优点 炉型结构简单;操作容易;便于控制;能连续生产;乙 烯、丙烯收率高;裂解气质量好;动力消耗小;热效率高;原料 的使用范围日渐扩大;便于实现大型化。 (2)缺点 重质原料的适应性还有一定限制;原料利用不高、燃料 油增加、公用工程费大、耐高温合金钢耗量大、反应过程的结焦 等。 SRT炉的主要工艺特性,如表6-1所示。
单元 管式裂解炉的结构与特点 【任务指导】 一、管式裂解炉结构
管式裂解炉既是一个管式 反应器,又是一个高传热 强度的传热设备。
图6-1 SRT管式裂解炉结构
单元 管式裂解炉的结构与特点
【任务指导】
二、管式裂解炉的传热方式
辐射室中燃料燃烧产生的火焰,主要以辐射方式将热量传给炉管的外表面, 同时传给炉墙。炉管外表面接受了火焰的辐射热量,以导热的方式将热量 从炉管外表面传到内内表面,炉管内表面以对流的方式将热量传递给管内 原料气,管内原料气受热呈现高温而发生裂解反应。 裂解炉中大部分的热量传递是在辐射室内进行。热源向炉管表面给热途径 主要是辐射传热方式。 原料气在进入辐射室之前,先在对流室进行预热。在对流室高温烟道气以 对流传热方式将热量传给管内的原料气。
单元 管式裂解炉的结构与特点
【任务指导】
三、管式裂解炉中炉管的性能及布置 方式
SRT炉在布管方式方面也不断改进,前后发展Ⅰ 型、Ⅱ型、Ⅲ型等三种炉型,如图6-2所示。Ⅰ型 炉中有8根立管,从原料气进口到裂解气出口在辐 射段有8程,造成在辐射段的停留时间长;Ⅱ型炉 中也有8根立管,但从原料气进口到裂解气出口在 辐射段有4程(第1程4根炉管细,第2程2根炉管较 细,第3、4程2根炉管较粗),因而在辐射段的停 留时间短;Ⅲ型炉中也有10根立管,但从原料气 进口到裂解气出口在辐射段有6程,因而在辐射段 的停留时间介于Ⅰ型炉的停留时间与Ⅱ型炉的停 留时间之间。 立管式裂解炉的辐射盘管大多采用单排管,以此 保证辐射盘管受热均匀。也有采用双排盘管的, 可在较低投资前提下获得较大的单炉乙烯生产能 力,综合单排盘管和双排盘管的优缺点,也有采 用混排辐射盘管的。
单元 管式裂解炉的结构与特点
【任务指导】
一、管式裂解炉结构
管式裂解炉主要由炉体和裂解管两大部分组成。炉体用钢构体和耐火材料 砌筑,分为对流室和辐射室。原料预热管及蒸汽加热管安装在对流室内, 裂解管布置在辐射室内。在辐射室的炉侧壁和炉顶或炉底安装了一定数量 的烧嘴(燃料喷嘴、火嘴等)。 SRT炉是最典型的一种管式裂解炉,其结构如图6-1所示。对流室内设有水 平放置的数组换热管以预热原料、工艺稀释用蒸汽,预热急冷锅炉进水以 及产生过热高压蒸汽等,在布置对流段管排时,应按烟气余热能位高低合 理安排换热管。辐射室由耐火砖(里层)、隔热砖(外层)砌成。新型炉也有 的使用可塑耐火水泥作为耐火材料。管式裂解炉的核心部分是辐射室,预 热后的原料气在辐射室的炉管中完成裂解反应。裂解炉的炉管悬吊在辐射 室中央,炉管的尺寸及布管方式随炉型而变。炉膛的侧壁和底部安装有燃 烧器,燃料燃烧主要以辐射传热方式加热炉管和管中的原料气。原料气在 炉管中获高温而裂解,裂解产生的裂解气离开辐射室后立即进入急冷锅炉, 被高压水骤冷以终止反应。高压水受热生产 10~12MPa的高压蒸汽,并回 收热能。急冷锅炉随裂解炉的炉型不同而有所不同。
化学反应器与操作
单元 管式裂解炉的结构与特点
江西省化学工业学校精品课程
单元 管式裂解炉的结构与特点
【任务目标】
●掌握管式裂解炉结构 ●掌握管式裂解炉的传热方式 ●掌握管式裂解炉中炉管的性能及布置方式 ●了解管式裂解炉优缺点
【任务指导】
一、管式裂解炉结构
裂解炉是石油烃裂解的主要设备。 1.管式裂解炉炉型 目前应用较广的管式裂解炉有短停留时间炉(简称SRT炉)、超选择性炉(简称USC 炉)、林德-西拉斯炉(简称LSCC炉)、超短停留时间炉(简称USRT炉,或称毫秒裂 解炉)。 美国鲁姆斯公司短停留时间裂解炉(SRT炉)是立管式裂解炉的典型装置。现在世界上 大型乙烯装置多采用立式裂解反应管。中国的燕山石油化工公司,扬子石油化工公司和 齐鲁石油化工公司的 300kt乙烯生产装置均采用此种裂解炉。 超选择性炉(简称USC炉)、超短停留时间炉(USC炉)也常被石化企业采用。例如, 中国大庆石油化工总厂以及世界上一些石油化工厂采用USC炉来生产乙烯等产品,中国 兰州石油化学公司将采用USRT炉生产乙烯。而LSCC裂解炉在工业上也得到一定的应 用,单台炉的乙烯年产量可达70kt。 管式裂解炉按外形分,有方箱炉、立式炉、门式炉、梯台式炉等,以立式炉为主流。按 燃烧方式分,有直焰式、无焰辐射式和附墙火焰式。按烧嘴位置分,有底部燃烧、侧壁 燃烧、顶部燃烧和底部侧壁联合燃烧等。